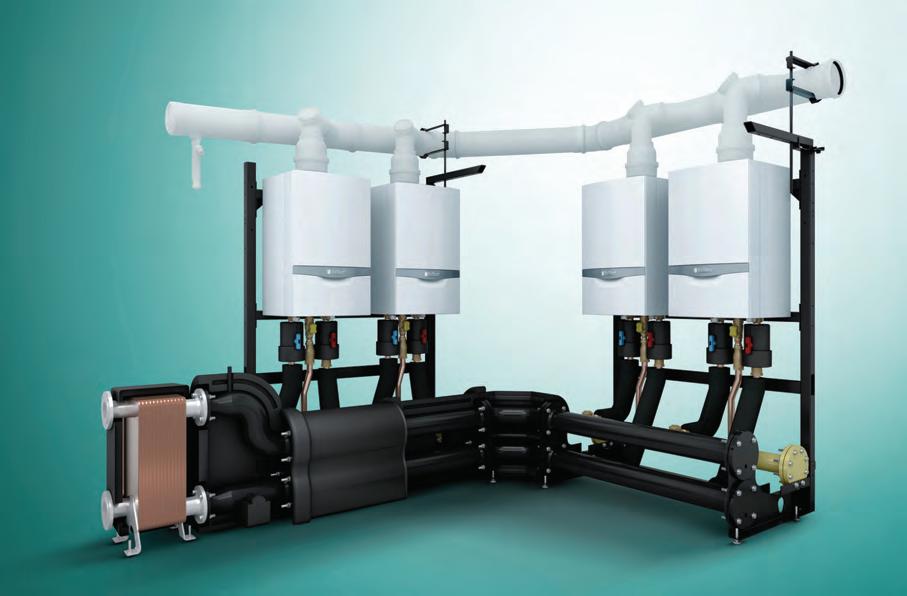
20 minute read
Boilers & Burners
Mark Wilkins is technologies and training director at
Vaillant
Advertisement
Why oversizing is essential
Mark Wilkins explains why redundancy is essential for many commercial applications, how it is implemented and why oversizing is unavoidable in these cases
versizing a heating
Osystem accidentally should never happen. However, implementing a redundancy contingency in certain plant rooms is not only wise, but the deliberate over-sizing by adding additional back-up boilers in cascade can offer a range of benefits.
By controlling and designing such systems in the right way, heating systems can be used efficiently, alternating the heat between boilers so that they are effectively being used less, therefore improving the lifespan of the product while providing essential and comfort conditions.
There is a wide range of nondomestic buildings where the provision of heat is critical to an organisation’s operations. To ensure heat security, redundancy is built into the heating system using ‘spare’ boilers. Without this back up to deliver heating and hot water, lives could be put at risk, businesses could incur significant losses, and occupants could suffer disruption to important aspects of their daily lives.
Protected services such as hospitals and nursing homes need hot water and heating to keep vulnerable patients safe, comfortable, and ensure maximum hygiene on the premises. Thermal comfort is also essential in educational establishments and childcare settings, as set out in the requirements of Building Bulletin (BB) 101. Adherence to the guidelines not only contributes to occupants’ physical health, but also the ability of both staff and pupils to concentrate. Loss of heating and hot water could lead to building closures and disruptions to their education. The Health and Safety Executive also places constraints on employers to provide basic comfort and care to their employees, so there is a legal framework in all workspaces, even in office environments.
Heat is not only needed to keep people safe and comfortable. Many industries require heat and hot water for manufacturing processes. Without these, production would grind to a halt, resulting in significant losses to businesses. In museums, humidity levels and temperatures must be kept constant to preserve valuable artefacts. If their condition is not maintained, this could result in damage to irreplaceable objects which have historical and cultural significance to a country.
Installing a system with cascaded boilers is advantageous in that it operates at its maximum capacity during the highest heat demand. At the same time, it can guarantee heat security if a failure occurs or during essential maintenance.
Meeting heating demand
For example, in a nursing home with a 600kW heating demand, six or seven Vaillant ecoTEC plus 120kW boilers could be set up as a cascade. This ensures that the heating demand can be met with five units fired up, with one or two spare units as back-up. Should a fault occur, for instance if one boiler doesn’t fire up as needed, the Vaillant VRC 700 controller, which can be used in a cascade set up with
The units in a cascade are not idle, they are operational under normal circumstances
Contrary to myths, a system where the boilers are cascaded does not waste energy
up to seven boilers, would recognise this and simply use one of the others to continue delivering heating and hot water.
The backup units in a cascade system do not sit idle, they are fully operational under normal circumstances. This is because the operator can programme the controls so that all units, including the spare ones, work on a rotational basis and manage changeovers. There are two important advantages to this set-up. By spreading the load, the risk of breakdowns in all units can be reduced, and their life can be prolonged. Using the back-up equipment regularly also ensures that they would operate when needed.
There are other circumstances where the inclusion of back-up boilers could result in even greater oversizing. For example, in a commercial building with a heat demand of say, 280kW, while a 280kW ecoCRAFT may be able to support the heat demand, for increased system flexibility and heat security, it’s often more effective to install three 120kW boilers, oversizing by a total of 80kW. In this case, the system would be oversized by 30 per cent. But if usage is rotated equally between the three units, at any given time two of the boilers would be covering more than 90 per cent of the heat demand, so a product such as a Vaillant commercial boiler could operate well beyond the 15-year industry-expected lifespan.
Contrary to myths, a system where the boilers are cascaded does not waste energy. They are controlled so that only some of them are fired up to provide the amount of heat required at any particular time. Vaillant’s VRC 700 can automatically manage this process for cascade installations with up to seven Vaillant boilers, and integrate with any BMS via additional accessories. If there are more than seven Vaillant units, they can integrate directly with the BMS via additional accessories, so that building operators can manage their heating in the most energy-efficient way.
Plant sizing shouldn’t be exceeded, and system diversity factors should be used correctly. However, plant rooms must be capable of all the challenges it is designed for. Having redundancy in a heating system not only prepares a building in the event of breakdowns but can also extend the lifetime of the system when designed and controlled wisely.
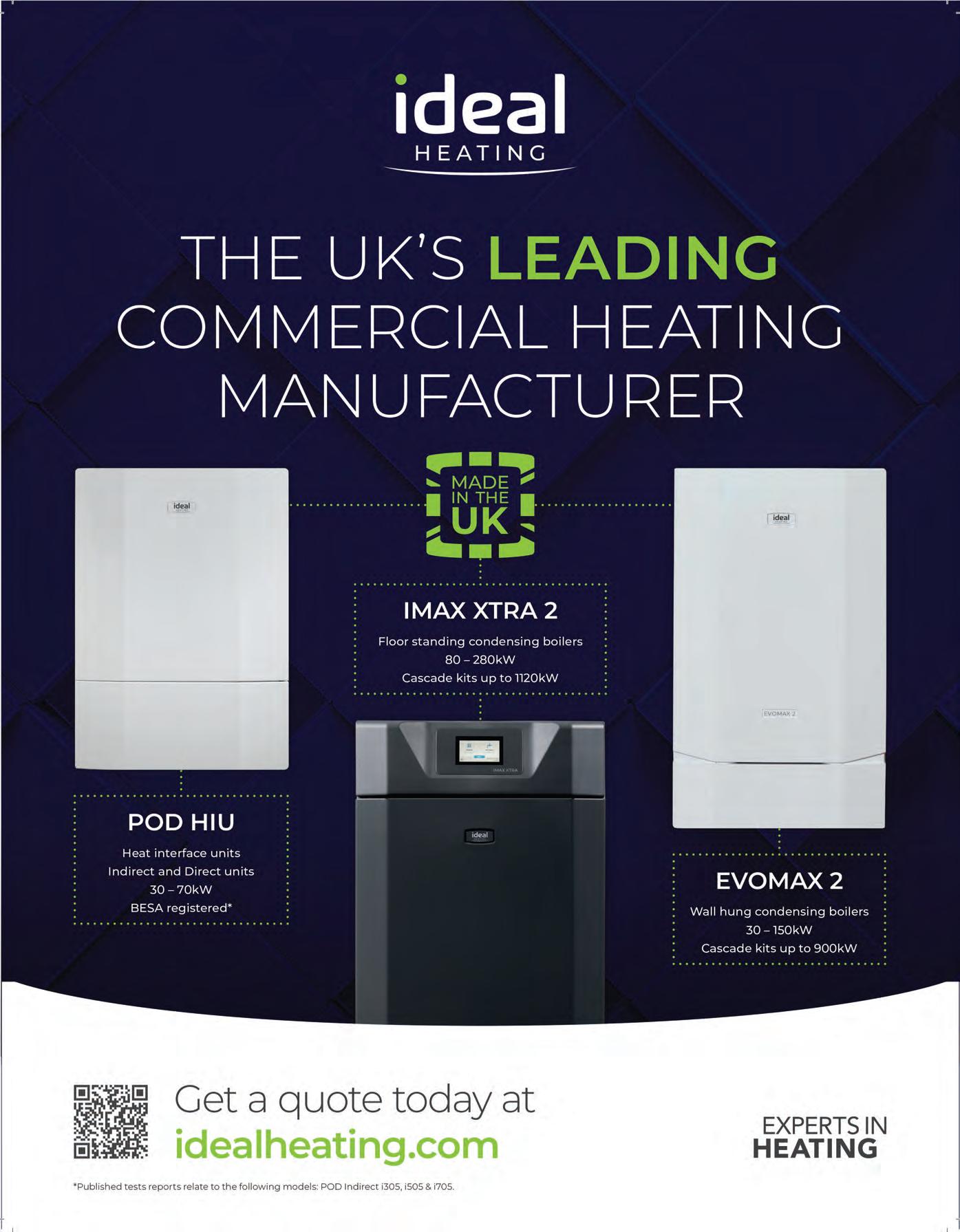
Boilers & Burners
Jeff House is head of external affairs at Baxi

Hydrogen-ready boilers could be mandated from 2026
The time is ripe for hydrogen
Jeff House discusses the critical role of hydrogen in protecting UK energy resilience, decarbonising heat and achieving the nation’s net zero ambition
t the time of writing, the UK
Agovernment is preparing to unveil a new energy strategy to improve Britain’s energy independence and protect households and businesses from volatile global energy markets.
Renewables such as wind and solar power are rightly expected to be part of the new strategy to free the UK from dependence on imported gas and oil. However, the speeding up the introduction of hydrogen – thereby diversifying gas supply – could play a critical role in protecting national energy security while supporting our 2050 net zero ambition.
And we’re not alone. Increasing the profile of green hydrogen is a key focus of the European Commission’s REPowerEU plan to provide the bloc with energy independence before 2030. It proposes producing an additional 15m tonnes of green hydrogen on top of its original 2030 target of 5.6m tonnes, together with a boost in deployment of wind and solar power.
We have long espoused the view that, along with electrification and heat networks, hydrogen has an exciting part to play in the future energy mix – particularly in poorly insulated, harder to treat buildings where the technically and financially viable options can be restricted. Here are some of the reasons.
Hydrogen boilers produce zero carbon emissions at the point of use as the main by-product of burning hydrogen is water. This will help businesses and organisations to achieve their net-zero emissions target.
Businesses and homes will be able to use heating and hot water in the same way as today, without major changes to their heating systems. This makes it a low disruption option.
Hydrogen can be produced domestically and used effectively to store energy over longer periods of time, providing intersessional flexibility and offsetting the intermittent nature of renewable generation. As such, it has the ability to improve energy resilience and security.
Hydrogen into the mix
Is the infrastructure in place? It is expected that the first step will be to introduce a blend of up to 20 per cent hydrogen into the natural gas mix, which could save six million tonnes of carbon dioxide a year nationally – equivalent to taking 2.5m combustion engine cars off the road (Source: HyDeploy).
Energy Networks Association has confirmed that all five of Britain’s gas network companies are ready to start blending hydrogen from next year. This will also mean that Britain’s gasfired power plants will be able to use blended hydrogen to generate cleaner electricity.
Is the blend safe? As a leader in hydrogen boiler technology, we have been working closely with government on a number of projects to trial hydrogen for heat. 20 per cent hydrogen blends have been successfully demonstrated using our natural gas boilers at the HyDeploy project at Keele University, proving that blending hydrogen with natural gas is feasible and safe – and a greener alternative to the gas we use now. Phase 2 of the HyDeploy project is now live in Gateshead, supplying a blend of up to 20 per cent hydrogen to over 600 existing homes.
According to this work on the HyDeploy project and the Gas Safe Bulletin TB159, current domestic natural gas boilers and other appliances are compatible with hydrogen blends of up to 20 per cent. In other words, no changes to heating products, guidance or measures are needed.
Although, for customer peace of mind of a future-ready installation, we have secured independent certification that our Remeha Quinta Ace and Gas 320/620 Ace condensing boiler ranges are 20 per cent hydrogen blend compatible.
When will we switch to hydrogen boilers? Demand for pure hydrogen boilers will be dictated by the gas distribution networks as their deployment will coincide with local area network conversions and larger scale pilot projects.
The next phase will be the introduction of ‘Hydrogen Ready’ boilers – which could be mandated from 2026 according to current plans – which we see as the bridging solution to the energy transition.
These boilers initially use natural gas but can be easily converted to hydrogen at the point of a local network switch over. As of today, the standards and certification framework to enable a product to be classified as ‘Hydrogen Ready’ are not yet in place so watch this space.
The final evolution is 100 per cent hydrogen boilers, appliances that are designed specifically to operate on hydrogen at the point of installation.
We are now demonstrating a 100 per cent hydrogen boiler as part of the government’s Hy4Heat programme in Low Thornley near Gateshead. Our hydrogen boiler produces no greenhouse gases at the point of use.
Next year the first approved trial of a hydrogen village involving around 300 occupied homes will take place in Fife, Scotland. Following on from this, a hydrogen village is planned for 2025, with OFGEM set to give the go ahead to successful bidders shortly. A further commitment in the UK Hydrogen Strategy and Heat & Buildings Strategy is a hydrogen town scale deployment that could be supported with a hydrogen grid by 2030.
But while progress with hydrogen is moving in the right direction, the supply infrastructure needs to accelerate to support diversification of national energy supply.
The UK government’s current ambition is for 5GW of low carbon hydrogen production capacity by 2030. We would like more ambitious targets introduced for hydrogen deployment to support our climate goals and a ramping up of domestic production to drive greater national energy independence.
On every level – commercial, sustainable and political – it would seem that the time is now ripe for hydrogen.
Networked control system 'promises to cut energy consumption'
The latest networked control system from compressed air specialist BOGE promises to reduce energy consumption and improve maintenance efficiency in manufacturing operations.
BOGE Airtelligence Provis 3 is an intelligent management solution which takes remote control, monitoring and auditing of compressed air systems to a new level. Unlike previous networked control products, Provis 3 is limitless in its scope and scale. It has been developed for larger and more complex plants with multiple compressors and equipment. Importantly, it can securely integrate and upgrade new and old components from different manufacturers.
Provis maximises energy efficiency by intelligently and proactively matching fluctuations in compressed air demand with flow from the optimum combination of compressors and other components. Further energy-saving benefits result from Provis energy auditing, reporting, costing and performance testing functions, whose clear insights enhance budgeting, decision-making and planning.
In addition, Provis enables monitoring of equipment condition and activity, so maintenance interventions are timed optimally to minimise costs and downtime. Authorised users can access intuitively displayed information and check, control or adjust equipment via the inbuilt Provis 3 display, or remotely on their PCs, tablets or smartphones.
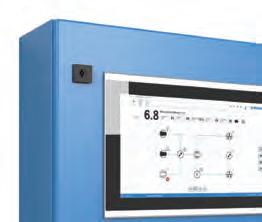
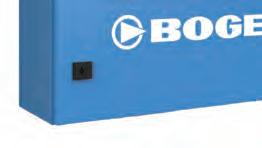
Three-strong range of heat pumps joins heating, hot water solutions
REMEHA has added a range of air source heat pumps (ASHPs) to its portfolio of sustainable commercial heating and hot water solutions.
The E-HP heat pump range is available in three outputs with individual heat capacities of 44kW, 88kW and 168kW and cascade options that dovetail with current commercial customer heat demands. The 44kW unit is eligible for capital grants under the government’s Boiler Upgrade Scheme (BUS) to support the installation of heat pumps in domestic and smaller non-domestic buildings. The BUS opened for grant applications from 1 April 2022.
The monobloc design is a self-contained heat generator, extracting renewable heat from the atmosphere and amplifying it using refrigerant compression. Specifically manufactured for northern Europe climate conditions, the Remeha E-HP AW can deliver a high supply temperature of up to 65°C and operate down to ambient temperatures of -20°C, providing a sustainable solution for all UK buildings.
Quiet, smart and energy efficient, the new Remeha E-HP AW heat pumps can be seamlessly integrated with other Remeha products and heat sources to provide sustainable heating and hot water solutions for new build and retrofit applications.


Boilers & Burners
Christian Engelke is technical director at
Viessmann
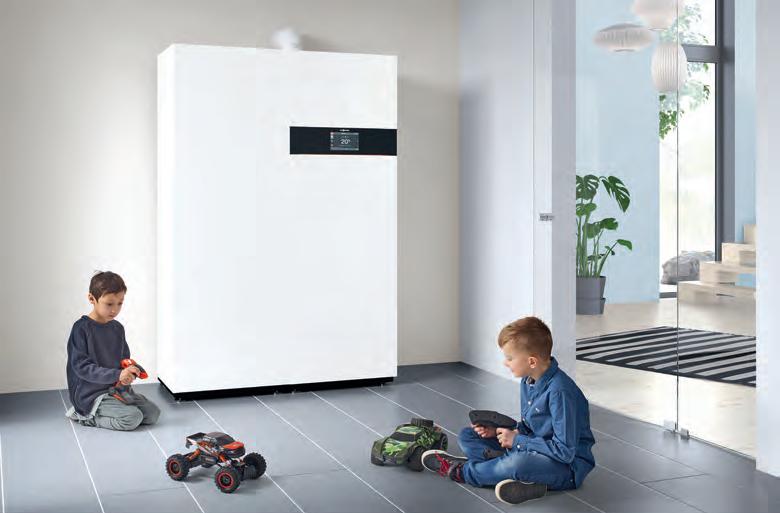
The right funding packages have to be in place for fuel cell microCHPs to be viable for most homeowners
What future for fuel cells?
With energy prices skyrocketing, environmental pressures intensifying, Christian Engelke discusses whether hydrogen fuel cell technology is set to enter the mainstream this year
ydrogen fuel cell systems
Hthat generate heat and power in domestic and commercial buildings are
not new.
While fuel cells are a successful and proven technology, it’s one that many installers and consumers still consider to be too big, costly, or too far a leap into the future. However, that could now be changing.
Fuel cell micro-CHPs suit a diverse range of properties and circumstances, from high-end new builds and renovations to more regular boiler replacements where homeowners are looking for an environmentally friendly solution, but where heat pumps aren’t feasible. They work by converting natural gas to hydrogen, which is then used to generate both power and heat through an electrochemical reaction known as cold combustion. In an exceptionally clean and efficient process, hydrogen is used as both a fuel source and energy store, while the carbon-producing combustion that takes place in conventional condensing boilers doesn’t happen, saving around two tonnes of CO2 per year. Viessmann’s Vitovalor’s fuel cell generates as much power as 30m2 of photovoltaic cells, but, unlike solar panels, it does it day and night, in all weathers.
As energy prices continue to spiral, the appeal of such efficiency is growing. For an average property, the combined gas and electricity savings now equate to around £1,500-£2,000 per year, up from £900 a year ago, based on Ofgem data, and this is set to increase further. Maintenance costs, too, are minimal; the Vitovalor fuel cell requires servicing only every five years.
In a fuel cell micro-CHP gas is converted to hydrogen which is used to generate both power and heat
However, the up-front cost of the technology can be a barrier. PACE funding is only available until mid 2022 to mitigate this issue, but that is no longer the case, and, when the government’s Feed-in Tariff (FiT) was replaced by the Smart Export Guarantee (SEG) in 2019, the financial case for fuel cells weakened. While a homeowner can still sell excess electricity to their energy supplier through the SEG, and while its value will grow as fuel prices continue to rise, the current best SEG rate offered is around 20 times lower than FiT payments were initially.
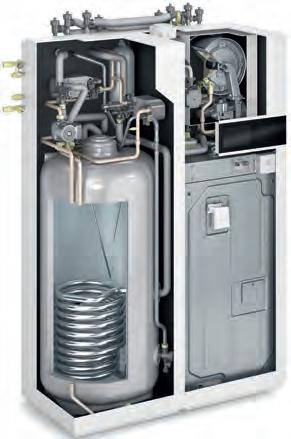
Viability for home owner
So, with large and growing energybill savings on one side but a sizeable up-front cost and low SEG payments on the other, is fuel cell technology financially viable for the average property owner today?
The short answer is yes - provided the right funding packages are in place. With units costing slightly more than ASHPs, financial support is critical to put this technology within reach of most people.
The good news is that grants available via the Ogfem-run Energy Company Obligation (ECO) scheme for low income, fuel-poor and vulnerable households are set to dramatically increase in size for many homeowners, making new fuel cell systems cheap – or even free – to install in many cases.
Launched in 2013, ECO runs in three-to-four-year cycles. During the third cycle, which is now concluding, customers were entitled to claim several thousand pounds towards their purchase costs, based on their anticipated fuel savings. However, if ECO4 is approved to begin in April 2022, funding will be allocated according to the difference a new system will make to the Energy Performance Certificate (EPC) rating of a property. As a fuel cell micro-CHP can thrust a building up several EPC bands in one go, that equates to a very substantial level of ECO funding – potentially enough to cover the entire cost.
This is especially important to landlords, as the Minimum Energy Performance of Buildings (No. 2) Bill currently working its way through parliament proposes that all rental properties should have a minimum EPC-rating of C by 2025.
Viessmann is working with energy conservation and renewables specialist Happy Energy Solutions Ltd to simplify access to grants for customers and installers. Happy Energy liaises with EDF to organise funding on behalf of installers, so that installers can concentrate on winning the business and fitting the technology. Happy Energy recently coordinated a package of funding for a couple in Hackney, east London, that covered the entire cost of a new Vitovalor fuel cell boiler (and solar panels). This reduced their energy bills by around 40 per cent, slashed their carbon emissions and moved their three-bedroom, end-of-terrace, Edwardian home from EPC rating D up to A. They’re now exporting electricity to the grid and receiving payments from their energy company.
But what about higher-income households that are not eligible for ECO funding? How does the financial case for a Vitovalor fuel cell mCHP stack up for them?
If electricity prices continue to rise as predicted, then homeowners could save in the region of £800900 per year based on an average of 4,500kWh/pa. In this scenario, the cost to generate a kWh of electricity for self-consumption is half the cost of purchasing from the grid.
As the technology becomes more commonplace, we could well see a momentum building that carries it into the mainstream during the next year, especially given the recent Spring Statement that micro combined heat and power products are included in the zero VAT technologies from April 1st 2022 to 31st March 2027.

ELCO Burners has developed a wide range of products that feature FGR (Flue Gas Recirculation) Technology. This system has been specifically designed to reduce NOx emissions to less than 30mg/kWh, even when burners are matched to boilers with a low thermal load, or on high flue temperature applications, such as oil thermal heaters.
ELCO has recently completed an impressive project in Seoul, South Korea, which included the installation of four ELCO Burners at the country’s largest hospital complex. Three of the new units were Ultra Low NOx Gas Burners with FGR technology – each delivering a powerful output of 16MW with NOx emissions less than 30mg/ kWh, while contributing to a combined system output of 80MW. These now provide highly efficient and low NOx heating and hot water services to the hospital building.
For monobloc burners, FGR consists of delivering a mixture of air and flue gas to the combustion head of the burner. This results in a significant reduction in NOx emissions from the unit.
To achieve these reductions, a new pipeline is installed to connect the flue gas outlet of the boiler to the burner fan inlet. This is sized to minimise any pressure drop and provide an adequate rate of flue gas to deliver reduced NOx emissions. Generally, the extraction point is at the base of the flue pipe, where the pressure is close to zero, resulting in a suction being generated in the burner intake box, which is a function of the fan curve and the air damper position.
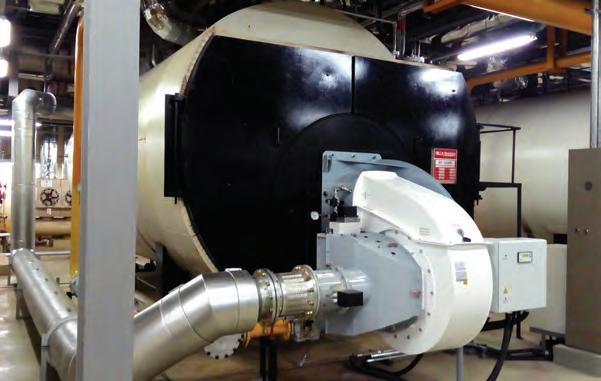
Vegetarian food producer looks to drive down its carbon intensity
Protium, the UK‐based green hydrogen energy services company, and its consortium partner, Petrofac, are to explore the deployment of green hydrogen technology with meat-free pioneer Quorn. Quorn’s production facility, Belasis, in Billingham continues to expand its production capacity to support the company’s growth. Protium and Petrofac will assess how the introduction of dual-fuel boilers (combusting both hydrogen and natural gas blend) can meet their expanding production capacity. Located close to Quorn’s Belasis production facility, Protium and Petrofac will explore the feasibility of supplying green hydrogen via a pipeline as part of Protium’s green hydrogen project in Teesside. Following a string of recent updates demonstrating Protium’s project velocity and expanding CAPEX pipeline, this project represents a wider strategic move from Protium who recently announced a planned hydrogen hub, in Teesside, located one mile from Belasis. Here, the team will be utilising Wilton Engineering’s site to deploy up to 40MW of electrolysis, which will produce over nine tonnes of green hydrogen per day. Initially, Protium would look to displace part of Quorn’s natural gas demand with green hydrogen which could save as much as 13,200 tonnes of CO₂ emissions per year. This would be equivalent to removing 7,600 cars from the road. Mark C Taylor, chief engineering officer at Quorn, said: “Quorn Foods is committed to being net-positive by 2030. We are also aiming for net-zero emissions within our operations by the same date. “To achieve this, we are considering all options to drive down the carbon intensity of our process heat and electricity consumption. The transformational opportunity which green hydrogen potentially presents is one we are taking very seriously.” The project could serve as a blueprint for other manufacturing companies looking to decarbonise their manufacturing processes, not only in the vegan protein space but across the broader food and beverage manufacturing sector. According to a 2021 report by the Waste & Resources Action Programme (WRAP), the UK food and beverage industry contributes to 35 per cent of the UK’s total GHG emissions, meaning the industry plays an integral role in tackling climate change and
achieving net zero.
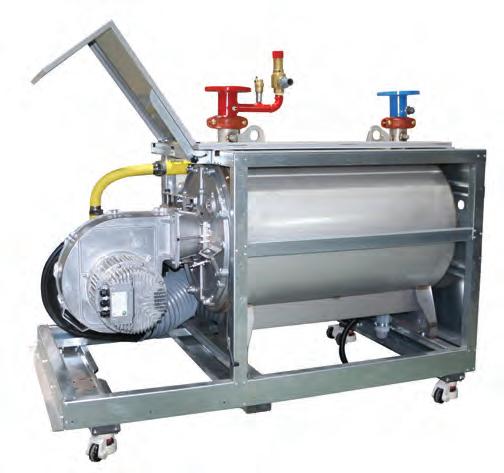
Schools and offices the targets for new range of floor-standing boilers
Modutherm has introduced the Genesis FS ULTRA range of floorstanding gas condensing boilers. Ideally suited to larger commercial heating applications, including schools, offices, retail outlets, hotels or heat networks, the flagship FS ULTRA is available in eight models with outputs ranging from 334kW to 2,666kW from a single unit, or cascade installations up to 16 boilers.
All models can operate at a ΔT up to 30ºC and a 6 bar pressure, while offering turndown ratios up to 30:1. The boiler range also delivers excellent durability and efficiencies up to 109 per cent, thanks to a NHEXT stainless steel heat exchanger, while an integral BLUEJET premix burner provides high flame retention and stability. NOx emissions are also kept below 36mg/ kWh (Class 6), easily exceeding the requirements for the best BREEAM NOx rating to provide two credits.
To further improve efficiencies, the FS ULTRA range has a low water content design, which facilitates rapid heat up times, as well as reduced fuel consumption. The design also keeps unit weights and dimensions to a minimum, making them perfect for roof top plant room installation and for applications where space is at a premium.
Ian Bradley, managing director of Modutherm, said: “Commercial boilers are still essential products for many of the UK’s buildings, especially in larger properties, or when retrofitting old and inefficient units. In such cases, opting for a highly efficient and low emission boiler, such as the FS ULTRA, is a great choice and can dramatically improve efficiencies and running costs.”
