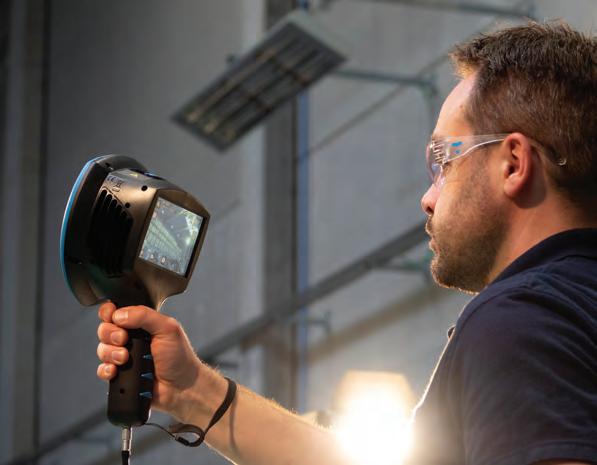
23 minute read
Compressed Air
Paul Clark is business line manager - CTS
Sales at Atlas Copco Compressors
Advertisement
Time for a full health check
Paul Clark explains how compressed air system health checks and energy audits carried out in an industrial environment can reduce costs and help deliver energy efficiency improvements
ven the most conservative
Eanalyses estimate that compressed air systems account for 10 per cent of all energy used in global industry, and of that, between 10 – 30 per cent is wasted on leaks. This wastage is expensive; even a 3mm leak could cost around £2,000 a year, with a loss equivalent to 16 tonnes of CO₂ emission. So, any optimisation of compressed air systems – no matter how small – impacts performance and efficiency significantly, lowering fuel bills and reducing carbon footprints.
The simple and most effective means of achieving optimisation is to carry out a health check and energy audit. These assessments can be performed quickly and accurately, and in some cases at no cost, and with zero disruption to the users’ production operations. Just one important aspect of these checks is identifying and eliminating leaks.
Leaks can be caused by many issues including corrosion, poor pipe connections and bad seals. And without investigation, these problems can add up to a significant amount of wasted energy over time, resulting in higher bills.
There is a variety of techniques that can be employed to locate, log, quantify and rectify air leaks. Initial steps involve little or no technology. In fact, some leaks can be found simply by listening and their location can be identified by the elementary technique of applying a soapy water solution to potential leak points such as joints, flanges, and valves, with bubbling indicating the source.
A more precise approach employs advanced technology. The use of ultrasonic leak detection equipment, which operates without interrupting plant production, reaches system areas that are hard to access, and locates all air leaks.
Leaks clearly marked
Once inspection has been completed, leaks can be marked on-site with weatherproof tags, along with a supporting written report that can provide more details on leak locations, photographic evidence of holes, leak severity in litres/minute, energy costs, positions, and costs to repair.
It is often not possible to know that leaks exist unless surveys are carried out
With the technology in place to provide fast, accurate and cost-effective leak detection, compressor technology specialists have developed three levels of health checks and energy audits for compressed air installation. Some of these services are offered freeof-charge, while others require an upfront investment which is quickly recouped through energy efficiency improvements, and the subsequent cost savings they bring:
• Level 1 – free visual inspection and energy potential calculations
(EPC). A visual assessment covers information such as compressor room environment, determining any air quality issues, and a visual inspection of all compressed air equipment on site, including appropriate capacity, ISO compliance, unproductive running, and pressure levels.
EPC calculations can also be carried out, focussing on the power usage of the compressors, load v. unload hours, and average leak assessment.
• Level 2 - Energy assessment and recommendations through
data logging. While EPC delivers an estimation of potential energy savings, this next level service provides a realworld assessment based upon the findings of data logging equipment fitted to each compressor. The data
Even modern systems are likely to have some leakage after six months
logging devices record and then map the energy consumed over a full week period, showing the actual running hours and calculated air usage.
Based on this data, engineer specialists can then calculate a realistic energy savings potential,
Many air audit services offered by compressor suppliers are free of charge
make simulations, and provide recommendations to achieve optimal energy efficiency. This service can also be free of charge.
• Level 3 - Full audit to ISO
11011:2013 standard. The full audit service provides a premium assessment of a range of parameters, such as flow testing, air leak detection, air quality testing, measurement and analysis of pressure and dewpoint throughout the wider system, from compressor room to production processes. Included in the audit are reporting and discussions of the most suitable methods to reduce energy costs and CO₂ emissions.
Even the most modern compressed air system is likely to have some level of leakage within six months of installation. Manufacturing facilities are often harsh operational environments. Over time, leaks can occur due to factors such as human error, sub-standard welding or pipe connections and damaged valves and seals. Often, it is not possible to know that leaks exist unless they are looked for, which is why leak detection surveys are crucial.
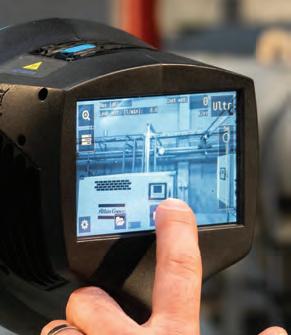
Easy health checks
It is wrong to assume that health checks and energy audits will disrupt production lines. The initial steps, such as a health check, couldn’t be easier and involve a visual assessment that can be conducted in as little as ten minutes, with no downtime whatsoever. Even more sophisticated data logging and ultrasonic testing, and the fitting of flow meters, can be performed in a completely unobtrusive manner.
Many of the air audit services offered by compressor equipment suppliers are free of charge. Even when there is an upfront cost the efficiency savings discovered always amount to more than the initial outlay.
There is little doubt that compressed air health checks, energy audits and leak detection can have a transformative effect on business operations. There are experts on hand to help tailor the various levels of service to operators’ needs, resulting in a unique set of findings that will relate to the specific requirements of an organisation.
Vanda Jones is executive director at the Briitsh
Compressed Air Society
Compressed Air
Energy going up in thin air
Vanda Jones discusses the key factors to consider when embarking on a compressed air energy reduction programme – and why now is the time to act
ften referred to as the fourth
Outility, industry relies on compressed air to keep plants performing profitably and efficiently.
However, it is not a free resource. Generating compressed air can be very energy intensive, representing between 5-30 per cent plus of a site’s total electricity bill.
Coupled with this significant overhead, poor practices and housekeeping can also contribute to unnecessary wastage. In fact, according to a report entitled ‘Compressed Air Systems in the European Union’, when looking at the most important energy saving techniques available to compressed air users, ‘the energy savings amount to 32.9 per cent, achievable over a 15-year period.’1
Using figures from the recent UK Energy-related products policy study, conducted by ICF in May 2021, BCAS calculated the combined energy usage for the mid-point of all industrial compressor technologies over their lifetime at 11.71TWh.2
Based on the current UK average non-domestic electrical unit cost of £0.1249/kWh3, the figures are substantial - equating to £1.475bn being spent by UK companies to generate the compressed air their businesses rely on.
Add to this the fact that over 30 per cent of this energy is being wasted through inefficient practices – equivalent to £485.43m in wasted electricity spend - and there is much that businesses can do to cut this figure significantly.
Yet, compressed air energy consumption is often overlooked, when, as we have already learnt, the potential for wastage is substantial and represents a considerable overhead, not to mention carbon footprint that could be reduced.
Take full system approach
A compressed air system is just that; a system, and every element of it impacts on its energy consumption. Therefore, when exploring the potential savings that could be realised, it is important to take a full, system approach – from generation to air treatment to distribution and finally, the point of use.
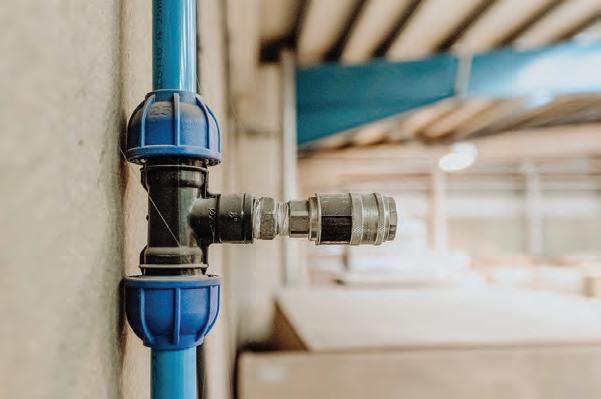
UK companies spend £1.475bn generating compressed air - over 30 per cent is wasted
Many actions will require elements of maintenance or equipment/system upgrade, but the human element should not be overlooked. Substantial efficiency improvements can be made by implementing new processes and encouraging staff to use compressed air more efficiently and safely. For example, not allowing benches or equipment to be cleaned down with compressed air will save a significant amount of air being vented into the atmosphere.
BCAS members can advise on the best equipment and system for a particular application. This could include incorporating fixed and variable-speed drives or a combination of both as well as efficient downstream equipment. For example, if a site installs the most efficient compressor available, but connects it to a system with a 30 per cent leak rate, then all the benefits are lost. Operators should aim to improve the overall system
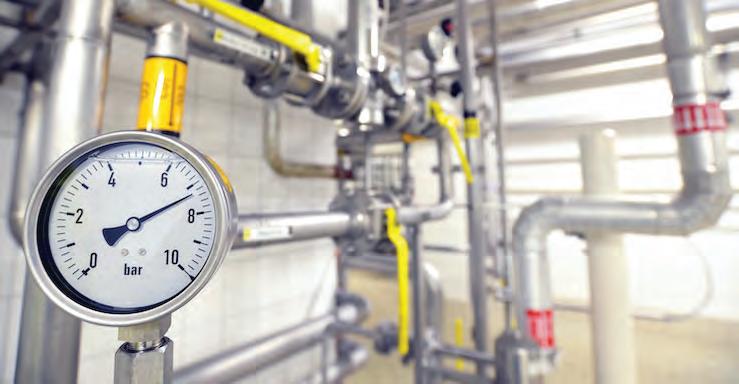
Taskforce urges users to aim for 10% cut
The British Compressed Air Society (BCAS) has launched its 10 per cent Taskforce initiative to encourage compressed air users to cut their energy consumption from compressed air by up to 10 per cent. BCAS is calling for UK businesses to take simple steps, many of which can be achieved at little or no cost.
Working together the industry could save over £147.5m in wasted electricity costs.
efficiency. Efficiency in the generation of compressed air is one aspect but targeting avoidable waste in the system is even more important.
Even when off-load, compressors can consume up to 70 per cent of their full load power, so units should be switched off overnight where there is no demand for air and running hours optimised to reduce costs.
Reducing air leaks can have the biggest impact on overall system efficiency. Leak rates in industrial systems are typically between 20 and 40 per cent, meaning the compressor must work harder, and therefore consume more energy, to compensate for the pressure loss. A tiny leak of just 3mm can cost more than £700 a year in wasted energy, but an out-of-hours survey can identify leaks easily.
Huge amount of wasted heat
As much as 95 per cent of the energy consumed by a compressor is converted to heat and, unless captured, will be wasted to the atmosphere. Many manufacturers offer heat recovery systems, which can often be retrofitted.
Treating air to remove dirt, water and oil is necessary but can use a lot of energy. The process is likely to only need a proportion of the compressed air to be treated to a very high purity. In these cases, excellent savings are achievable by treating all the generated air to the minimum acceptable level and improving the purity (quality) to the desired level at the usage point.
Low-cost, regular maintenance will help retain low leak rates and reliability of equipment. Operators should consider a policy that specifies that energy efficient options are purchased when replacing all equipment – whether it is a basic drain valve through to the actual compressor unit itself.
Finally, the manufacturer’s genuine spare parts should be used, instead of cheaper alternatives. These can enable significant savings in excess of 25 per cent.
References
1) Compressed Air Systems in the European
Union. Energy, Emissions, Savings
Potential and Policy Actions. Peter Radgen and Edgar Blaustein 2) Data obtained from the UK Energy-related products policy study. Conducted for the Department for Business, Energy, & Industrial Strategy by ICF Consulting
Services Ltd 3) https://www.gov.uk/government/ statistical-data-sets/gas-and-electricityprices-in-the-non-domestic-sector
Compressed Air
Waste to energy with compressed air
Cobalt Energy has relied on BOGE Compressors to supply compressed air systems in the construction of two separate facilities to convert clinical waste into energy
hen consultancy Cobalt
WEnergy won a contract to build a new energyfrom-waste plant, it knew that a reliable compressed air system would play a central role in its success. The company specialises in thermal renewable, solar and energy-storage technologies in the UK. In 2019, as an engineering, procurement and construction management (EPCM) contractor, it began constructing Haylers End Energy Recovery Plant in Malvern, for its client Waste Energy Power Partners. The plant began operating in 2020.
Haylers End – which was previously a derelict waste-incineration facility – uses a reciprocating grate system to process 8,000 tonnes/year of clinical waste, received from the National Health Service (NHS) and private medical companies. The plant scavenges power using a modern waste heat-recovery boiler. This raises steam that can generate electricity and provide hot water to clean the clinical-waste receptacles. In full operation, it operates self-sufficiently in terms of electricity consumption. Any excess is fed into the distribution network.
To operate successfully, the facility needs a reliable supply of compressed air. This is necessary for the flue-gas clean-up system, and to operate components such as valves in ancillary systems. The flue-gas clean-up system can work with lower-quality compressed air – but the ancillaries needs air certified as Class 2 according to ISO 85731:2010. During the commissioning phase, Cobalt Energy produced a specification for a suitable compressed-air system and put it out to tender.
“We invited several companies to Malvern to outline their systems,” says Wade Pritchard, senior project manager at Cobalt Energy.
BOGE won the tender and in compliance with strict planning regulations, BOGE designed, supplied, installed and commissioned an integrated compressed-air system
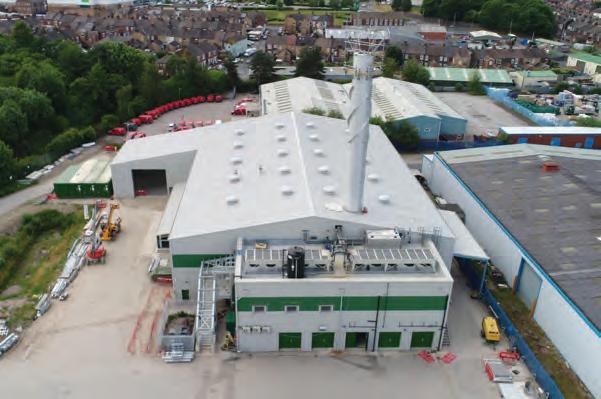
Two 30kW screw compressors are operating at the Stoke clinical waste processing site
that met Cobalt’s specifications. It included duty and stand-by screw compressors, refrigerant dryers, absorption dryers and auto drains.
Planning restrictions
One project complication was the presence of planning restrictions. These specified that Haylers End had to be re-built in the image of the original site, which added significant complications. For instance, the air compressors had to be fitted in the basement. Getting air to and from them – and keeping them cool – required a complex arrangement. However, BOGE project manager Neil Gibson managed to navigate these issues – such as by helping to design an appropriate ventilation route.
In addition, the space available for the compressed-air system was limited. This was overcome, however, by the bespoke, designed layout of the equipment for system flow, to suit the tight space, thanks to the relatively small footprint of BOGE’s compressors. For the duty and stand-by systems, it recommended its 15.14-kw C 20 F/S screw compressors. These, like all models in the C series, are designed to fit into small spaces. They are also reliable and easy to maintain – because they use a minimal number of pipes and connections. They were combined with BOGE’s DS26-2 refrigerant dryers, which feature an energyefficient aluminium heat exchanger. This reduces performance losses in the refrigeration cycle while using less refrigerant than comparable models.
The systems are completed with DAZ absorption dryers – which have active carbon towers – and Beko 13 auto drains.
“The installation work carried out by BOGE went very smoothly,” says Pritchard. “It makes my job much easier when contractors are reliable and professional – and abide by all health and safety regulations.”
Pritchard was suitably impressed by BOGE when a similar contract came in. Cobalt had been asked to build a larger energy-from-clinical-waste facility – this time in Stoke on Trent, Staffordshire. Pritchard asked BOGE to supply the compressed air system directly, rather than through tender.
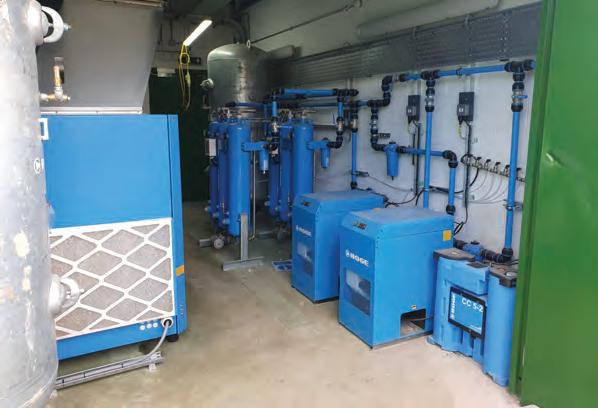
Ease of maintenance
The Stoke facility will be capable of processing 16,000 tonnes/year of clinical waste, and works on the same principles as the Malvern plant. For the new project, BOGE recommended larger duty and stand-by systems than those in Malvern. It proposed a pair of its 30kW S 40 screw compressors, which are designed for energy efficiency, reliability and ease of maintenance. These operate with two DS 40-2 refrigerant dryers which have energy-efficient aluminium heat exchangers and two DAZ 36-2 adsorption dryers with active carbon towers. As with the Malvern installation, the systems also feature a pair of BEKO 13 auto drains.
“The Stoke project was more straightforward than Malvern,” says Pritchard. “There’s more room, and it’s all on one level. In terms of footprint, it is probably 50 per cent larger than Malvern – but the compactness of BOGE’s machines has still been highly beneficial.”
The strong working relationship built up between the two companies has also developed further. At one point, complications in the planning of the facility forced Cobalt to put its order with BOGE on hold for several months.
“Neil bailed us out of that one,” says Pritchard. “Fortunately, it worked out – and we still received the compressors in plenty of time.”
The Haylers End plant is now up and running – while the Stoke facility is on the verge of completion. Cobalt Energy plans to approach BOGE directly for compressed-air systems for future construction projects.
ESTA VIEWPOINT
For further information on ESTA visit www.estaenergy.org.uk
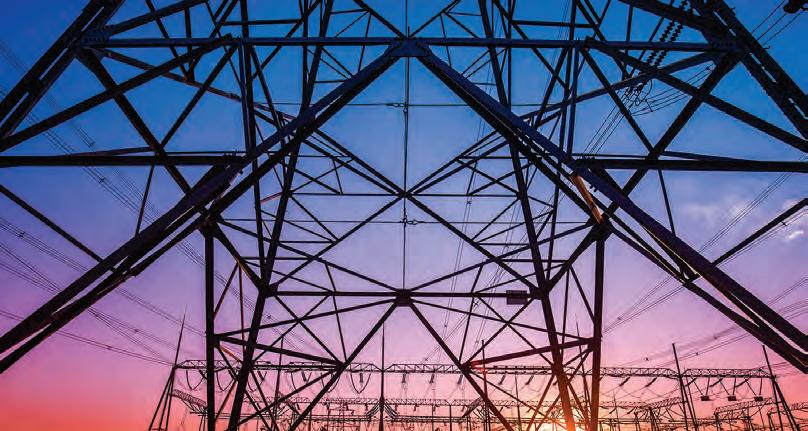
When will the first fuel come first?
Mervyn Pilley reflects on the Government’s obsession with energy supply and hopes that efficiency becomes a core part of its forthcoming energy strategy
am coming up to the end of my first
Ithree years at ESTA and I could never have imagined what an extraordinary three years they have been. Long, drawn-out negotiations to get a Brexit agreement over the line greeted my arrival. Then we had an election where a different result could have potentially turned energy policy on its head yet produced a Government that steadfastly does not seem to want to engage with lobbying activity no matter how well reasoned. Then along came a pandemic that decimated the face-toface activity on which ESTA had forged its reputation, and now a horrendous war. Add in turmoil in the energy markets where all of the focus has been on supply and its security together with an unexpected change to the certifying body for our major training programme, and I feel as though I have been on one long roller coaster ride. The good news is that while I have never enjoyed roller coaster rides for real, I love what I do and remain totally convinced that an effective membership organisation can really contribute to solving many of the problems facing us.
The irony for me is that I was brought into ESTA to effect change and that, despite the circumstances outside of my control, I have continued to do. Not all of the projects have moved as quickly as I would have liked but our then energy efficiency does indeed become a supply side issue. The energy strategy arising from the market chaos and sanctions has been delayed so I can only hope that when it finally does arrive, with or without nuclear power stations, it will contain energy efficiency. The lack of willingness of the chancellor to fund the nuclear investment coupled with the limited support offered to energy users, especially business users, in the spring statement worries me and reinforces my big concern that the Government is expecting far too much from the private sector in financing the various strategies published last year. £90bn of private sector in the current situation seems to be incredibly optimistic.
40th anniversary is proving to be a spur to push forward with ambitious plans for this year. Ironically, as I have looked to return us to that face-toface meeting and networking activity, I have discovered a knock-on effect of the rapid energy prices increases. All venues have put their prices up considerably and as they scrabble to recover lost revenue from the pandemic availability of sensibly priced meeting places around the UK has dropped.
However, in addition to a return to trade show activity this year with an energy efficiency zone at the Installer/ Elemental trade show at the NEC between the 21st and 23rd June 2022 and a return to the Smart Buildings show at ExCel in October, we are also planning a number of road show type events where members can showcase their wares to existing and potential customers. We even have some ambition to return to the days when we had our own exhibition but that will not happen for a year or two.
One big frustration remains the fact that the Government’s focus is still very much on supply – where is it coming from and how secure are our existing supplies with very few giving any attention at all to demand side. My view remains that if you agree with the view in the IEA report that energy efficiency should be regarded as the first fuel Mervyn Pilley is executive director of
ESTA (Energy Services and Technology Association)
One big frustration remains that Government focus is still very much on the supply side
Roll out of EV chargers
Following on from my colleague George Barnes’ article in last month’s edition I also remain concerned about how effective the Government’s plans are to roll out EV chargers. Time is short and local authorities are cash strapped so it is unlikely that they on their own can deliver the number of charging points needed especially in rural areas and the north of England. This is really part of the levelling up strategy although it is not always linked to that.
On the ESTA front we are refreshing our energy efficiency in buildings research group run jointly with BESA. While we have good expertise in the group already the turmoil caused by the pandemic has meant we have lost some members. We are open to nonmember experts having a part to play in the group as thought leadership is an important aim.
You also will not be too surprised that a large amount of my focus is currently on recruiting new members from sectors that would not have been traditional markets for us – facilities management companies, building services engineering companies, M&E divisions, retrofit professionals, architects and designers. These are all areas where commercial energy efficiency is especially important. Irrespective of the apparent lack of interest from so many people on the importance of energy efficiency we will continue to shout the message aloud.
• If any reader is interested in joining ESTA, please get in touch at mervyn@estaenergy.org.uk. Join us to drive the energy efficiency movement forward.
TALKING HEADS
Mehmet Olgun
Mehmet Olgun is head of net zero compliance with EQUANS
n 2019, the UK became the first
Imajor economy in the world to pass laws to end its contribution to global warming by 2050 – setting a target to bring all greenhouse gas emissions to net zero by that date. This went beyond the target set in 2008 to reduce carbon emissions by 80 per cent below 1990 levels. To help achieve this target, the government has introduced a raft of mandatory compliance schemes that require businesses to measure, report and reduce their greenhouse gas emissions.
For organisations, ensuring full compliance with these schemes – which include Streamlined Energy &
Carbon Reporting (SECR), The Energy
Savings Opportunity Scheme (ESOS), and UK Emissions Trading Scheme (UK ETS) – can be a complex process that demands considerable time and resources. Given the administrative burden of mandatory compliance, many organisations regard compliance with any additional voluntary standards as beyond their capabilities and resources. But adopting internationally recognised standards for energy management or carbon footprinting – such as ISO 50001 and ISO 14001 – not only simplifies and supports compliance with mandatory legislation, it also unlocks greater environmental, financial and reputational benefits for the business.
It’s also increasingly clear that mandatory schemes alone will not deliver the government’s new net zero targets. The latest Intergovernmental
Panel on Climate Change (IPCC) report suggests that current efforts to decarbonise will not be sufficient to keep global temperature rises within 1.5°C above pre-industrial levels. In light of these findings, governments and businesses will need to go beyond current legislative measures to meet their net zero commitments.
Tightening up of regulations
The government has already announced a tightening up of schemes like ESOS, which are set to become more stringent to better support the drive towards net zero. At the recent UN Climate Change Conference of the Parties (COP26), Chancellor Rishi Sunak announced that all large, listed firms would have to introduce not just climate-related risk disclosures, but
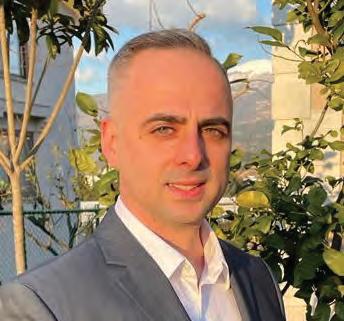
Voluntary schemes can cut carbon
Businesses will need to go far beyond current legislative measures to meet net zero commitments. Voluntary compliance schemes have a vital role to play, as Mehmet Olgun explains
comprehensive net zero strategies. A new taskforce is to be created to develop a robust compliance standard for these strategies. It’s a strong signal that regulatory pressures are set to increase on large businesses, meaning now is the time to get ahead by implementing effective net zero strategies to tackle carbon emissions effectively and sustainably.
Adopting the processes and behaviours required to comply with voluntary accreditations, such as ISO 50001, establishes best practice and creates the baseline of data needed to fulfil many regulatory obligations. It also sets the groundwork for developing a net zero carbon roadmap, which every business will need as regulations tighten up and the global deadline for reaching net zero approaches.
ISO 50001 is the internationally recognised standard for Energy Management Systems (EnMS). It gives businesses the most robust and effective framework for improving energy efficiency over the longterm. By complying with ISO 50001, businesses will automatically meet the reporting and auditing requirements for mandatory regulations, including
It can be confusing for businesses to select the right schemes for their net zero ambitions
Olgun: 'it's important for organisations to avoid duplication of effort in complying with different schemes'
ESOS, and will find it significantly easier to achieve their CCA carbon reductions
There are a number of other worthwhile voluntary schemes that businesses can opt to comply with, including ISO 14064 for validating and verifying greenhouse gas emissions, and PAS 2050 for quantifying the carbon footprint of specific products or services. There are also schemes, such as Global Real Estate Sustainability Benchmark (GRESB), Global Reporting Initiative (GRI) and Carbon Disclosure Project (CDP) which may be appropriate for different businesses, depending on their size, sector and location.
Compliance confusion
The plethora of voluntary compliance schemes available can be confusing. It can be difficult for businesses to select the right schemes or combination of schemes to fulfil their specific net zero ambitions in the most efficient and cost-effective way. It’s important to avoid duplication of effort in complying with different schemes, and to ensure that the data-gathering, operational processes and behavioural changes required for any scheme are appropriate to the size and nature of the business.
That’s why it’s helpful to get expert advice at the outset, to identify the right voluntary accreditation schemes for each business – ones that will deliver lasting operational, cost and efficiency benefits, while simplifying compliance with all relevant mandatory schemes.
EQUANS has developed Certify, a service that combines compliance and carbon-reduction expertise into one simple partnership arrangement. Our experts help to support compliance with both voluntary accreditations and mandatory regulations, while easing administrative burdens and improving efficiencies. The aim is to give businesses the peace of mind that they are tackling the challenges of decarbonisation and compliance in the optimum way, while maximising opportunities to improve energy and operational efficiency, reduce costs and achieve challenging net zero targets.
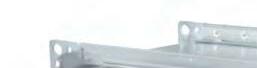
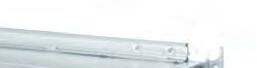
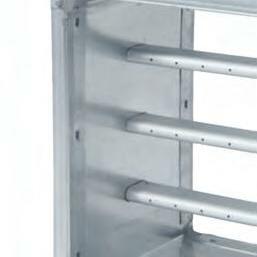
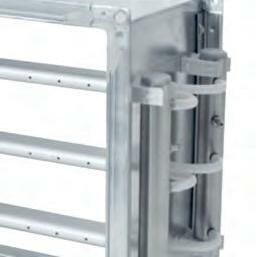
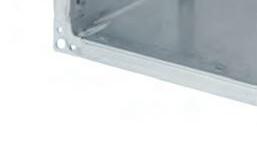
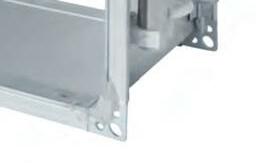