
25 minute read
The Warren Report
Andrew Warren is chairman of the British Energy Efficiency Federation
03.21
Advertisement
Vague and vacuous – the Government’s latest proposal on fuel poverty
Sustainable Warmth is the latest fuel poverty strategy. Launched without fanfare, it does little to inspire confidence that this scourge on our homes will be eliminated any time soon
Environmental Justice. That is one key policy that US President Joe Biden has adopted. He has set up a large high-powered team in his administration the sole objective of which is to ensure that policies being adopted to deliver a zero-carbon society do not damage further the least advantaged and the poorest.
This philosophy is echoed in the title of the UK Government’s long awaited new fuel poverty strategy. It is called “Sustainable Warmth.” You will be forgiven for not having heard about it before today.
Last month it was quietly placed upon the Government website, just 48 hours after the energy minister Martin Callanan had assured the former buildings minister, Don Foster, in the House of Lords that “we plan to publish in due course…the updated fuel poverty strategy.” Not, please note, publish “imminently” or even “shortly”, the standard ministerial fob-offs to importunate questioners.
I can find no evidence of any departmental press release, or even a staged Parliamentary answer announcing it. So, why the sudden release of a strategy intended to cover policy for the rest of the decade? After all, given the need to get the text signed off by all relevant government ministers and departments, it must largely have been written many weeks before.
I suspect, when it was prepared, there were great hopes that England would be witnessing an enormous increase in the number of homes being made more energy efficient. Something Callanan stressed is “the best long-term solution to tackle fuel poverty.” This was because back in July the Chancellor had announced £2bn to improve the energy efficiency of English homes, to be spent by the end of March. And the main programme, the Green Homes Grant scheme, was offering grants of £10,000 towards installing measures for low-income householders, twice the size of that more generally available.
Consequently, “Sustainable Warmth” is littered with references to this scheme - I counted five separate occasions when this July statement from the Chancellor was cited in this relatively short document.
But during last month there was a growing crescendo of highly publicised Parliamentary interventions, led by the powerful Environmental Audit Committee and its no-nonsense chair, Philip Dunne, pointing out what a tiny proportion of that £2bn had yet been spent. This was answered by confirmation that the Treasury intends, at the end of this month, taking back at least £1bn of the money announced for the scheme just eight months ago.
The rest of “Sustainable Warmth” is both tendentious in many of its claims, and vacuous in many of its various proposals. The Government website leads with the bold claim that 1.2m fewer households are in fuel poverty than was the case in 2010. But in the document itself, unlike most other such statements, there is no cross-reference or source provided, which makes me suspicious. And certainly no absolute figures given between the number of English households in fuel poverty in 2010, and then in 2020.
Even if such a statement could be justified, I suspect it must largely be due to the initial years of the decade. That was when the government was still funding the successful Warm Front programme exclusively aimed at improving low-income housing. Equivalent programmes have significantly continued, indeed grown in size, in each of the devolved nations. But since 2012, there has been a vacuum in England.
Statutory basis behind fuel poverty policy
The Warm Homes & Energy Conservation Act 2000 is acknowledged to be the statutory basis behind fuel poverty policy. But there is no mention of its original target of abolishing fuel poverty by 2016 - indeed there is even a strange footnote referencing it as “requiring Government to set up interim milestones to reach the 2030 target, with dates for achieving them.”
And nowhere is it stated that abolition is the objective, just
“driving down levels.” But how far? The answer is that weasel phrase “as far as is reasonably practical.” Ostensibly, to ensure everybody is in an energy performance certificate C rated home by 2030. Unless it is a listed building. Or unless they raise objections. Or unless it is all too difficult.
There is a welcome recognition that the there is “real potential benefit in increasing homes to band C in one renovation”- followed immediately by crowing that the fuel bill payer-funded Energy Company Obligation (ECO) has delivered 2.8m measures into 2.1m homes. In other words, just over a single measure per home. Precisely the opposite to that “real potential benefit.”
To be fair, there are a few useful nuggets included for the future. There is formal confirmation that ECO’s budget will be restored for four years to £1bn a year- the rate it was back in 2013, but welcome, nonetheless.
The Business Department has obviously at last got agreement with the Housing Ministry to provide better guidance for private landlords, particularly those of homes in multiple occupation, as to when they must provide an energy certificate: it is amazing how few comply.
The Homes Upgrade Grant, that the Prime Minister announced last year won’t start until early (April?) 2022, but will be targeted at low-income, off-grid homes.
The assumption is still that removing such homes from oil-heating to heat pumps will offer lower running costs in future. But maybe they know something about future prices per barrel of oil that we don’t.
Whether installing heat pumps in the 80 per cent of homes currently enjoying gas-fired heating will lower many fuel bills remains to be seen. Biden’s Environmental Justice would surely require that to be a guarantee.
Heating Technology
For further information on Sabien Technology visitwww.eibi.co.uk/enquiriesand enter ENQUIRY No. 125
Tony Willis is technical director at Sabien Technology
Go beyond boiler control
Don’t assume your boiler is operating at maximum efficiency. Tony Willis examines how the problem of dry cycling can be easily be overlooked – and quickly rectified
The availability of affordable microprocessors which began in the 1980s allowed some huge advances in “intelligent heating technologies” over the last few decades. These enabled boiler and burner manufacturers to adopt a higher level of precise control, previously not possible with simple electro-mechanical methods.
Some of these technologies include: electronic fuel-air ratio controls for modulating burner systems, intelligent boiler sequencing, weather compensation, building and climate controls, building optimisers and building management systems (BMS).
For many years now, it has been standard procedure to control a building’s services through a building management system (BMS) or building energy management system (BEMS). When they are correctly commissioned and maintained, a BMS or BEMS will help to maintain the overall building efficiency and prevent energy from being wasted.
Consequently, it is quite natural to assume that a building with an existing BMS/BEMS is operating to maximum efficiency in all areas with no need for additional ‘fine’ control. However, many of these systems are not typically programmed to control each individual item of plant, particularly boilers, down to the finest detail. Their primary role is to optimise a building’s energy requirements rather than the individual items of plant that make up a building’s energy-consuming services. Consequently, there will be cases where a building’s energy performance can benefit from this ‘fine’ level of control thus enhancing the operation and optimising the boiler plant. This can be achieved by retrofitting additional controls that address specific areas of wasted energy consumption if they were omitted during initial plant commissioning.
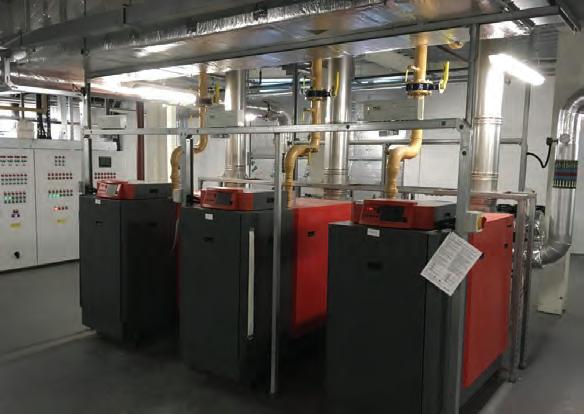
Boiler load optimisation carries out a real-time analysis of each boiler’s flow and return temperatures
Like many aspects of our lives, buildings and their heating demands evolve over time, often shifting from the original design for load requirements. This is further compounded by an increase in building efficiency as a result of insulation, glazing and other energy efficiency solutions. This results in boiler plant being operated for extended periods, far below intended boiler kW output capacity. These conditions can lead to boilers operating inefficiently at ‘part load’ conditions which in turn will cause the boilers to dry and short cycle - an inherent problem that is not always recognised or considered.
Therefore, further savings can be achieved by optimising each individual boiler to eliminate boiler dry cycling. These are savings that can be achieved over and above those of existing control strategies, without conflicts. So when it comes to ‘fine tuning’ energy performance, boiler load optimisation is the next logical step.
To look in more detail we can consider the boiler ‘dry cycling’ phenomenon. This aspect of inefficiency offers the largest energy saving on your boiler plant. Unless measures are taken to control it, boiler dry cycling happens with the majority of boilers under part-load conditions. It occurs when a boiler loses heat to its surroundings (acting like a radiator) so that the water temperature in the boiler falls below the current set-point of the boiler’s internal thermostat / load control. When this happens, the boiler may fire simply to recover the boiler’s standing losses/temperature of the wasted heat – even though this energy is not currently being used to meet demand for heat to the building.
Recognised perennial problem
Dry cycling has been a recognised problem for many years, and early attempts at retrofit solutions were an abject failure. These ‘failures’ either delayed the boilers firing, or artificially reduced the boiler set points, both of which allowed temperatures to fall in the spaces being heated. In addition, they can cause direct conflicts with the BMS strategy by artificially changing the boiler’s set point temperatures.
An alternative, using boiler load optimisation technology developed in the last few years, is to carry out real-time analysis of each boiler’s flow and return temperatures every ten seconds and measure the decay of the flow and return temperatures every second. This provides a true load profile for each boiler and can therefore differentiate between a genuine call for heat and one that is simply firing to recover heat caused by the standing losses.
The advantage of this approach is that it recalculates the values every time the boiler reaches its required set point temperature, so it adapts to variable set-points and does nothing to conflict with the BMS/ BEMS operation or other controls such as weather compensation or sequencing. It also helps to mitigate the energy wastage caused by shortcircuiting and short-cycling.
In this way, retrofitted intelligent boiler load optimisation is an example of how the right additional controls can work in harmony with other controls and increase the energy savings that can be achieved.
So if you are considering retrofitting additional controls, the key is to understand how they work (don’t be fooled by manufacturers’ jargon), talk to others that have used them and be absolutely certain they won’t compromise comfort or your existing BMS control strategy.
With any energy reduction initiative, it is vital that the client can realise the savings and has the visibility and confirmation that the control is delivering, and expectations are met. With the recent availability of low-cost IoT cloud-based monitoring, boiler load optimisation controls can be fully monitored with the energy saving and reduced CO2 displayed. This data can also be used for full analysis of the existing boiler plant performance and validate existing controls such as BMS etc.
Heating Technology
For further information on products and services visit www.eibi.co.uk/ enquiries and enter the appropriate online enquiry number
Temperature sensors for home heat recovery systems

Whole house heat recovery ventilation systems are just one of the many ways in which consumers are looking to become more energy conscious, while maintaining their comfortable living environment.
As MVHR (Mechanical Ventilation Heat Recovery) systems are often hidden away in loft spaces, it is imperative that they should be low maintenance, demand the minimum level of servicing and therefore use highly reliable parts
ATC Semitec is now stocking a wide range of IP67 and IP68 temperature sensors with long-term reliability which are ideally suited for use in MVHR systems.
ATC Semitec’s 103AT-11, are single-insulated, fully encapsulated IP67 rated temperature sensors, offering fast response times, and high accuracy (±0.3°C at 25°C). The sensor tip is moulded directly onto the cable ensuring the interface is completely sealed, whilst its small sensor tip responds quickly to temperature change. The flexible leads enable easy installation and the AT-11 offers industry standard resistance values such as the 10k /B3435K (103AT-11).
These sensors are widely used across a diverse range of industries, and within the HVAC market they are a popular choice for use within underfloor heating, heat pumps, solar panels and batteries.
They are readily available from stock in lengths from 600mm to 3m long. The range of even higher integrity IP68 sensors are stocked with various R25 and B values and sensor lengths from 500mm to 5m long.
ONLINE ENQUIRY 140
Heating Technology
For further information on Klima-Therm visitwww.eibi.co.uk/enquiriesand enter ENQUIRY No. 126
Tim Mitchell is sales director of Klima-Therm
The hidden cost of heat pumps
Heat pumps have a vital role to play in the energy mix of the future but end users must ensure that natural refrigerants are part of the mix to mitigate global warming, says Tim Mitchell
Emissions of fluorinated gases (F gases) – including hydrofluorocarbons (HFCs) – commonly used as refrigerants for air conditioning systems more than doubled in Europe between 1990 to 2014. Thankfully, however, the F-Gas
Regulation stopped this trend in its tracks and then began to reverse it.
Despite Brexit, the UK will, according to REFCOM (the Register of Companies Competent to
Manage Refrigerants), continue to follow the step-down programme established by the F-Gas Regulation to reduce the nett amount of global warming gas on the market. We are also expected to adopt further revisions likely to come into force at the start of 2023.
The market for HFC gases such as R410A has shrunk significantly, in terms of CO2 equivalence, to just 45 per cent of what was available in 2015 as a direct result of the
F-Gas Regulation. This undoubtedly represents massive progress in the campaign to reduce the industry’s impact on the environment.
But further progress is still needed on reducing the global warming potential (GWP) of refrigerants and that is where so-called ‘natural’ refrigerant gases come in, because their GWPs are so much lower than those of the common F-gases.
The natural options in air conditioning applications include propane, ammonia and carbon dioxide (CO2). The GWP of these is 3, 0 and 1, respectively. This compares with a GWP of 2,088 for R410A, a commonly used F-gas refrigerant in air conditioning applications.
The standard classifications for refrigerants revolve around toxicity (A or B – in simple terms, non-toxic or toxic) and flammability (from 1, 2L, 2 or 3 – in simple terms, nonflammable to highly flammable), as defined in ISO 817.
CO2 is an A1 refrigerant, so it is neither toxic nor flammable.
Ammonia (B2L) is toxic but exhibits low flammability. Propane (A3) is
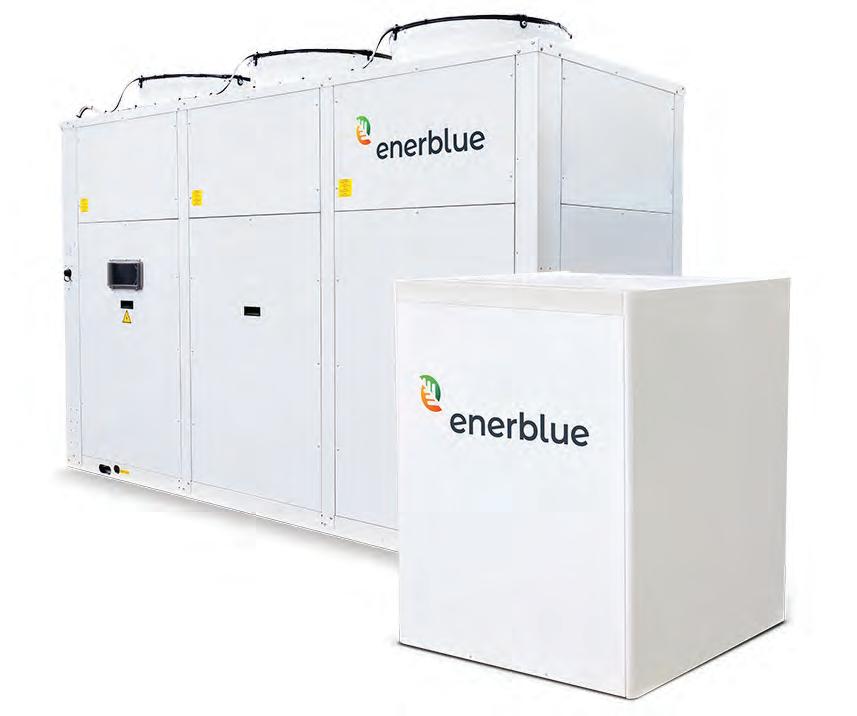
Natural refrigerants offer a less harmful option when used in heat pumps
non-toxic but highly flammable.
Truly environmentally responsible temperature control, where nonmechanical means are impossible, involves using natural refrigerants in combination with energy-efficient appliances. As a result, heat pumps have come into their own for heating and cooling.
Rolling out heat pumps
As heat pumps are rolled-out on a larger scale – the current government is targeting over 600,000 installations every year by 2028 – natural refrigerants offer a less harmful option.
CO2 is arguably the best refrigerant option for heat pump applications where hot water is consumed, such as hospitals, hotels, leisure centres and in communal domestic hot water loops, because it can deliver hot water at boiler-like temperatures at far greater efficiencies than the other natural alternatives or HFCs.
F-gases and how to control them
F-gases have been a clear and present danger to the environment since they were first developed in the 1990s to replace even more environmentally damaging chlorofluorocarbons (CFCs) and hydrochlorofluorocarbons (HCFCs).
The most common F-gas refrigerants used in heat pumps are hydrofluorocarbons (HFCs), all of which have a high global warming potential (GWP) compared with natural refrigerants.
To control emissions from fluorinated greenhouse gases the European Union published the first F-Gas Regulation in 2007 which only really involved actions like leak testing, monitoring and servicing systems.
The second F-Gas Regulation, which came into force in 2015, introduced a phase-down mechanism involving a gradually declining cap on the total placement of bulk HFCs on the market.
Under UK and EU legislation, a ban came into force on 1 January 2020 to prevent refrigerants with a global warming potential greater than 2500 being used to service or refill refrigeration or freezer systems, with a refrigerant charge size of 40 tonnes of CO2 equivalent or more.
Indeed, CO2 is in a class of its own with an operating envelope that lends itself exceptionally well to domestic hot water temperatures. A typical air-source CO2 heat pump, for example, could comfortably deliver hot water at 75oC from air at -4oC with a coefficient of performance (CoP) of around 2.53, whereas an HFC using the same criteria would give a CoP of around 1.78 while working at the very top of its operating range.
Among “traditional” refrigerants, the main low GWP alternatives are hydrofluoro-olefins (HFOs) or blends which use them. HFOs are organic compounds which still use hydrogen, fluorine and carbon, like traditional F-gases, but their chemical structure is such that they are unstable in air, breaking down very much more quickly than traditional F-gases. With the normal GWP metric being based on a 100-year impact assessment, this instability is what makes the HFO GWPs so low.
As well as GWP, there is another environmental issue with refrigerants: ‘embodied’ carbon. This measures the ‘cradle to grave’ greenhouse gas equivalence throughout the supply chain from manufacture to end-of-life disposal. The metric that takes this – as well as other environmental factors such as GWP and energy efficiency – into account is called Life Cycle Climate Performance.
LCCP is more inclusive than previous metrics such as Total Equivalent Warming Impact, which looks at direct and indirect greenhouse gas emissions but fails to account for embodied emissions, and Life Cycle Warming Impact, which considers direct, indirect and refrigerant manufacturing emissions but overlooks appliance manufacturing, materials, transport installation and recycling.
This feeds into the latest thinking around embodied and whole life carbon in the built environment, such as CIBSE TM65 covering mechanical, electrical and public health systems.
Daniel Burton is chief executive officer at Wondrwall Group
Heating Technology
For further information on Wondrwall Group visitwww.eibi.co.uk/enquiriesand enter ENQUIRY No. 127
Finding a flexible solution
Heat pumps and hydrogen might play their part but Daniel Burton believes a smart and agile approach to decarbonising heating may be called for
Heating is one of the UK’s biggest sources of carbon emissions. Space heating is estimated to contribute around 17 per cent of carbon dioxide emissions and hot water about 4 per cent. Currently, only about 5 per cent of homes currently have any form of low-carbon heating while natural gas dominates the domestic market where it is used to heat around 85 per cent of homes.
Meeting the UK’s net zero carbon targets by 2050 will require a range of low-carbon alternatives.
According to Energy Systems
Catapult there is no ‘silver bullet’ solution, and proposals for blanket solutions are expected to cost far more than a bottom-up approach that chooses the best low-carbon heating solution on a place-byplace basis.
The established view is that the best way to decarbonise domestic heating is to invest heavily in insulation, and then install a heat pump. While this approach can work in many situations, it will not always be the most cost-effective way to achieve the end goal. In some cases, it is not even practical or possible to retrofit homes in this way.
For many years, gas has been the go-to solution for domestic heating and hot water. However, as part of its commitment to decarbonising energy, the UK government has declared that from 2025, no new homes should be connected to the gas grid. While some hold out hopes that clean hydrogen gas may be available by then, many experts doubt that we won’t be able to produce anywhere near sufficient clean hydrogen to meet the needs of the gas grid.
With gas being so much part of the current mindset, it’s hardly surprising that heat pumps – which rely on a familiar set up of pipes, thermostats and radiators – are currently the most popular way to electrify domestic heating and hot water.
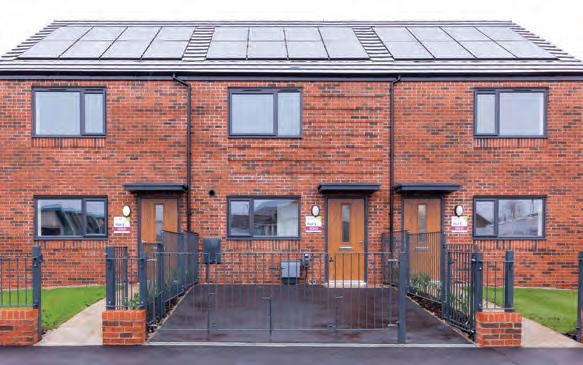
Manchester City Council is exploring a new, technology-led approach to cutting bills for tenants
While heat pumps do have a lot to recommend them, they are not the best option in every case. Heat pumps rely on a ‘low and slow’ approach – drawing heat from the environment to gently but steadily heat homes. This can work well if homes are extremely well insulated and the outside temperatures are not too low. Otherwise, either the heat is lost too quickly, or the system needs to operate well outside its margins of efficiency.
Pushing up overall costs
Heat pumps can be unsuitable for retrofit, as upgrading insulation to sufficient levels pushes the overall costs up significantly. On top of the cost of extra insulation, the old central heating system needs to be completely replaced with an external compressor unit, a new central hot water immersion tank, heating water clusters and more. The radiators also need to be bigger to compensate for the lower running temperature. There are also some situations where fitting a heat pump externally is simply not viable – for example in high-rise buildings.
There is another option, however, that takes a technologyled approach.
Manchester City Council recently explored a different approach to electrifying domestic heating in a new-build development in West Gorton, Greater Manchester. The affordable houses were equipped with modern digital and renewable energy solutions that can deliver reductions to energy bills of up to 90 per cent for tenants.
The mews-style, three-bedroom homes, built in partnership with Manchester City Council, are fitted with solar PV and battery storage. But what makes them unique is the intelligent solution that ties these elements together. The self-learning system, designed by Wondrwall, automatically adapts heating, lighting, security and energy consumption according to the behaviour of the occupants, environmental conditions and wholesale energy costs.
Combining electric underfloor heating and infrared panels can quickly provide warmth when needed, and the intelligent, partitioned, hot-water cylinder heats water only when needed. A system comprising solar panels, inverter and battery storage provides free electricity from the sun and enables the tenants to take advantage of hourly fluctuations in energy costs. For new and old properties, the cost of installing this ‘smart and agile’ solution compares favourably with wet heating systems, heat pumps and high levels of insulation.
The key to the effectiveness of the system, is its ability to learn and adapt to the information in real time. The system will begin a typical day by checking the weather forecast shortly after midnight. Combining this information with what it knows about the behaviour of the occupants and the performance of the solar panels, it will predict how much electricity it needs to draw from the grid to meet the family’s needs for the day.
The system then analyses time-of-use tariffs for the day and determines the most cost-effective time to charge the domestic batteries. If there is an unexpected energy requirement during the day, the system might respond by supplying energy from the battery and importing energy from the grid. Conversely, if there is a spike in energy from the PV solar panels, the system will export energy back to the grid. During the evening, when energy prices are at their peak the system powers the house entirely from energy stored in the battery. After midnight, the system processes the day’s data, adjusts its algorithm accordingly, and the cycle begins again.
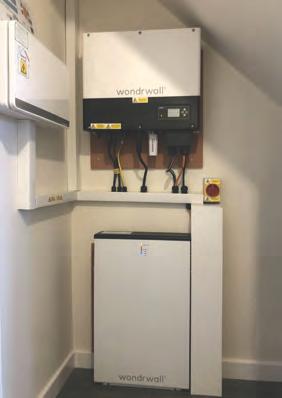
Heating Technology
For further information on Zehnder UK visitwww.eibi.co.uk/enquiriesand enter ENQUIRY No. 128
Rupert Kazlauciunas is technical product manager, MVHR, Zehnder UK
Can we achieve zero-carbon homes?
Hitting a target of zero-carbon homes is a huge challenge. Rupert Kazlauciunas looks at the obstacles to be overcome and its implications for the heating industry
In its report on the ‘Route to zero carbon’, the Passivhaus Trust (PHT) outlines the pressing need to adopt a zero-carbon target for all new-build UK homes.
As it does so, it emphasises the difficulties in defining exactly what this would actually look like and how it could be achieved.
The report opens with a grave indictment of where we are on our route to zero carbon: “There are clear imperatives to reduce the carbon emissions resulting from the built environment. However, we are currently not achieving any significant year-on-year reductions and, unless new policies embodying new standards, incentives and penalties are put in place, we are unlikely to do so.”
Much of the stalling of progress can be attributed to a failure of political will: a super-green standard for new homes was first announced many years ago. This policy was set to ensure that all new-builds did not result in the net release of carbon dioxide during their day-to-day use.
It set out requirements for all new housing developments to focus on energy efficiency and to offset any emissions by generating their own energy through renewable sources.
But, in July 2015, just a few months before it was scheduled to pass into law, the initiative was abandoned by the Treasury, in a knee-jerk reaction to heightened publicity over the endemic UK housing shortage.
The solution to achieving zero carbon homes, however, goes well beyond providing political backbone.
PHT prefaces its report with this observation: “Setting a zero-carbon target for our new housing would be a clear and bold step to achieve genuine emissions reductions.
However, understanding what this actually means and how to achieve it is far from clear.”

Decarbonising the grid will make electricity an increasingly attractive option for home heating
There are three main obstacles to adopting a true zero-carbon approach: • the clear performance gap that exists between predicted heating energy demand and actual energy use; • the gap in available supply and seasonal energy demand for winter heating will require inter-seasonal renewable energy storage. This will inevitably result in losses; and • the national grid is limited in its ability to manage renewable energy.
Elimination of performance gap
Due to these current obstacles, PHT calculates that a notionally zero carbon home is actually responsible for 18kg of CO2/m2 each year. To offset this, an average UK home would need to install 28 solar panels – and that is far greater than the roof space it has available.
Yet, the energy efficiency of a Passive House – and the elimination of a performance gap between design and usage – would require only 14 solar panels. This dramatically reduces the requirement for grid and storage enhancements and halves the amount of renewable generation for offsetting required.
“Reducing the heating energy demand through a fabric first approach is therefore the only practical way to achieve zero-carbon homes in reality,” states the report. Passive House recognises that a fabric-first approach alone won’t solve the problem: there will be many sites not suitable for solar or other renewable energy generation.
It is proposed that any achievable zero-carbon initiative must use off-site generation. The sort of scheme envisaged is one where a contribution is paid by all newbuild developments towards the construction of national renewable energy projects.
Another area that is highlighted as contributing significantly to reducing emissions is energy-efficient heating in homes.
The UK’s national strategy of ‘decarbonising’ the electricity grid has already had a significant impact on emission levels. This is already starting to have a massive disruptive effect on the heating industry. Electricity is an increasingly attractive choice for energy efficient and eco-friendly heat pumps. The next few years will see a switch from gas to electric pumps for heating and hot water in homes. Indeed, in March, the Chancellor vowed that gas heating for new houses will be banned by 2025, to be replaced by heat pumps and best-in-class insulation solutions.
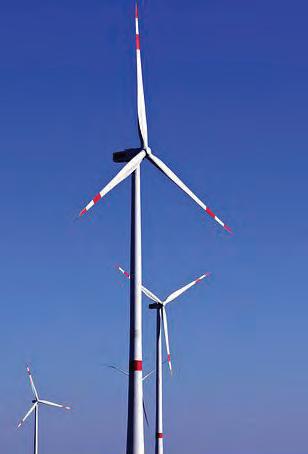
Greater electricity need
The reduction in carbon emissions for heat pumps is marked. Comparing an average house (built to Building Regulations standards) using a gas boiler to the same house using an air source heat pump applying 2020 emissions factors the total energy demand reduces from around 7,000kWh/year to 4,300kWh/ year.
The report adds: “As the grid is decarbonised, there is an increasing case to use more electricity for heating purposes. This is particularly compelling when using heat pumps, as the running costs can become comparable to gas.”
To fully take advantage of this switch to electricity for heating – and not overburden the limited capacity of the national grid’s renewable energy supply – we need to focus our building designs on reducing thermal loss. This can be achieved by improving the fabric of our buildings and using ventilation for heat recovery. Houses that implement this can reduce their energy demand further to 3,700kWh/year.
Issues of comfortable, healthy homes dovetail neatly with concerns over carbon emissions and energy efficiency. Developments in heating and ventilation are central to achieving both zero carbon and maximum comfort.
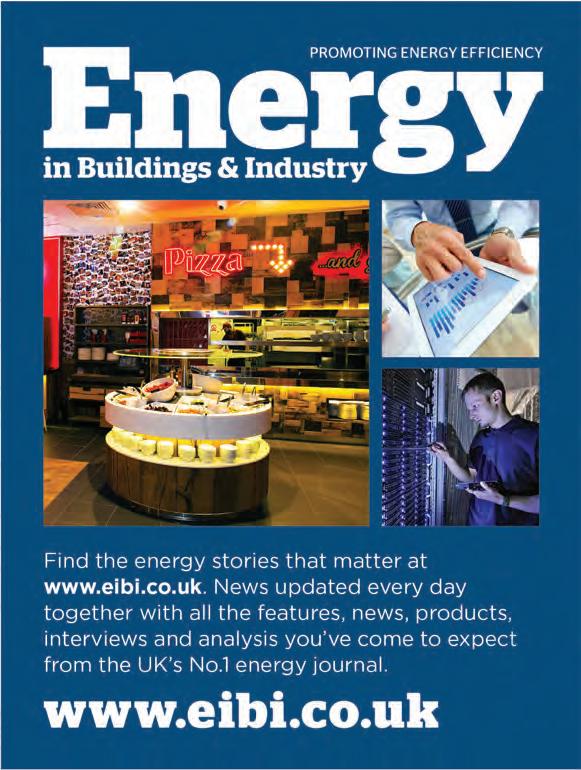
eibi.co.uk/enquiries Enter 5 eibi.co.uk/enquiries Enter 6
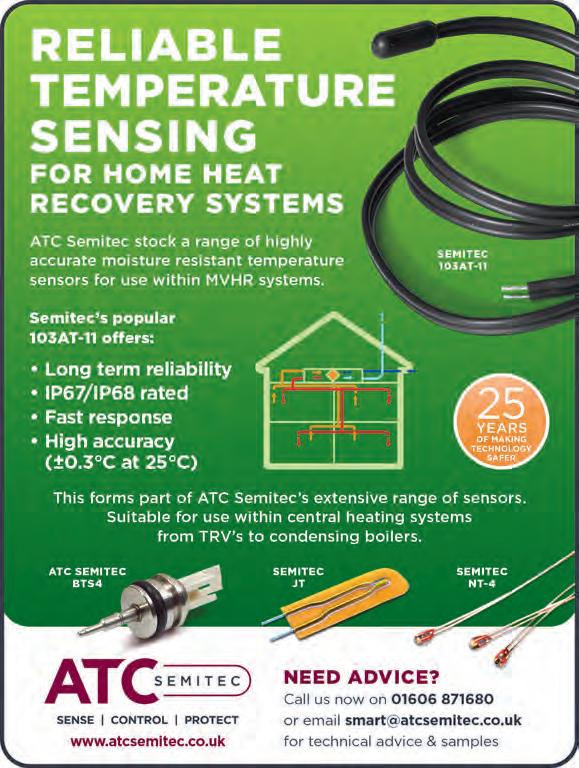
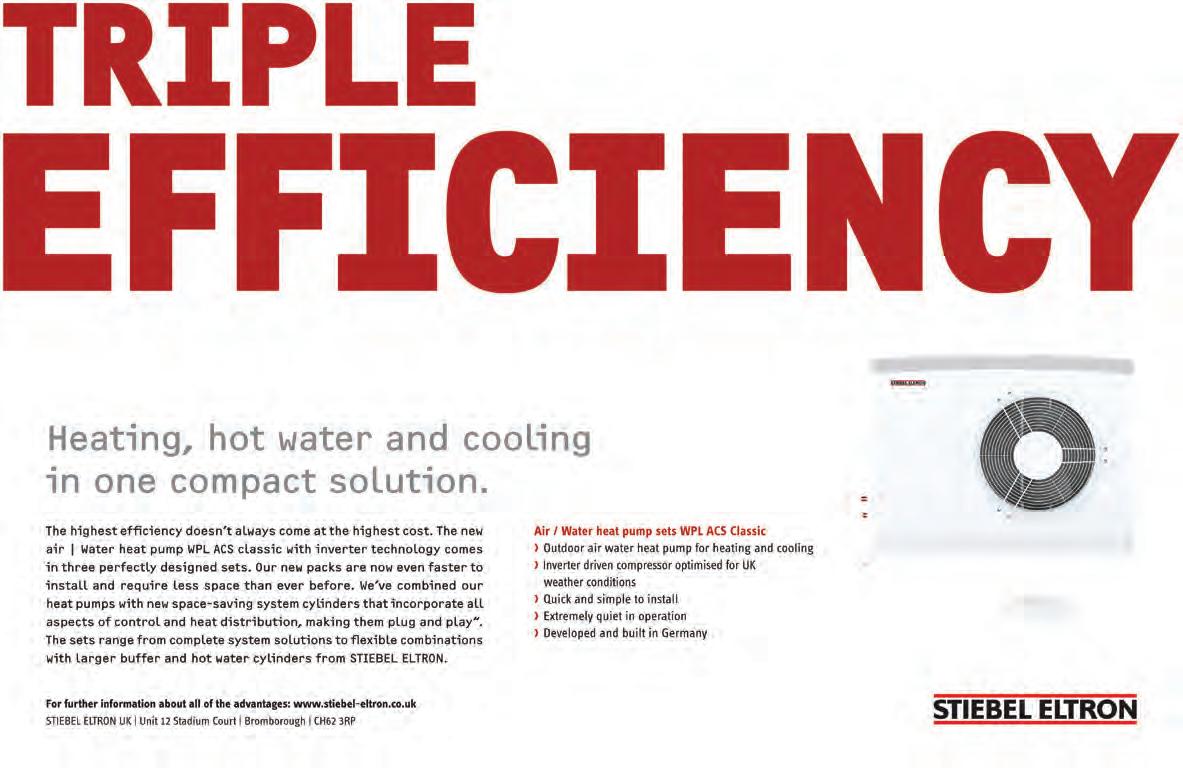