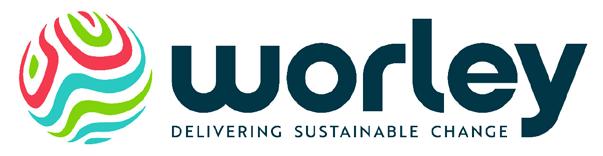
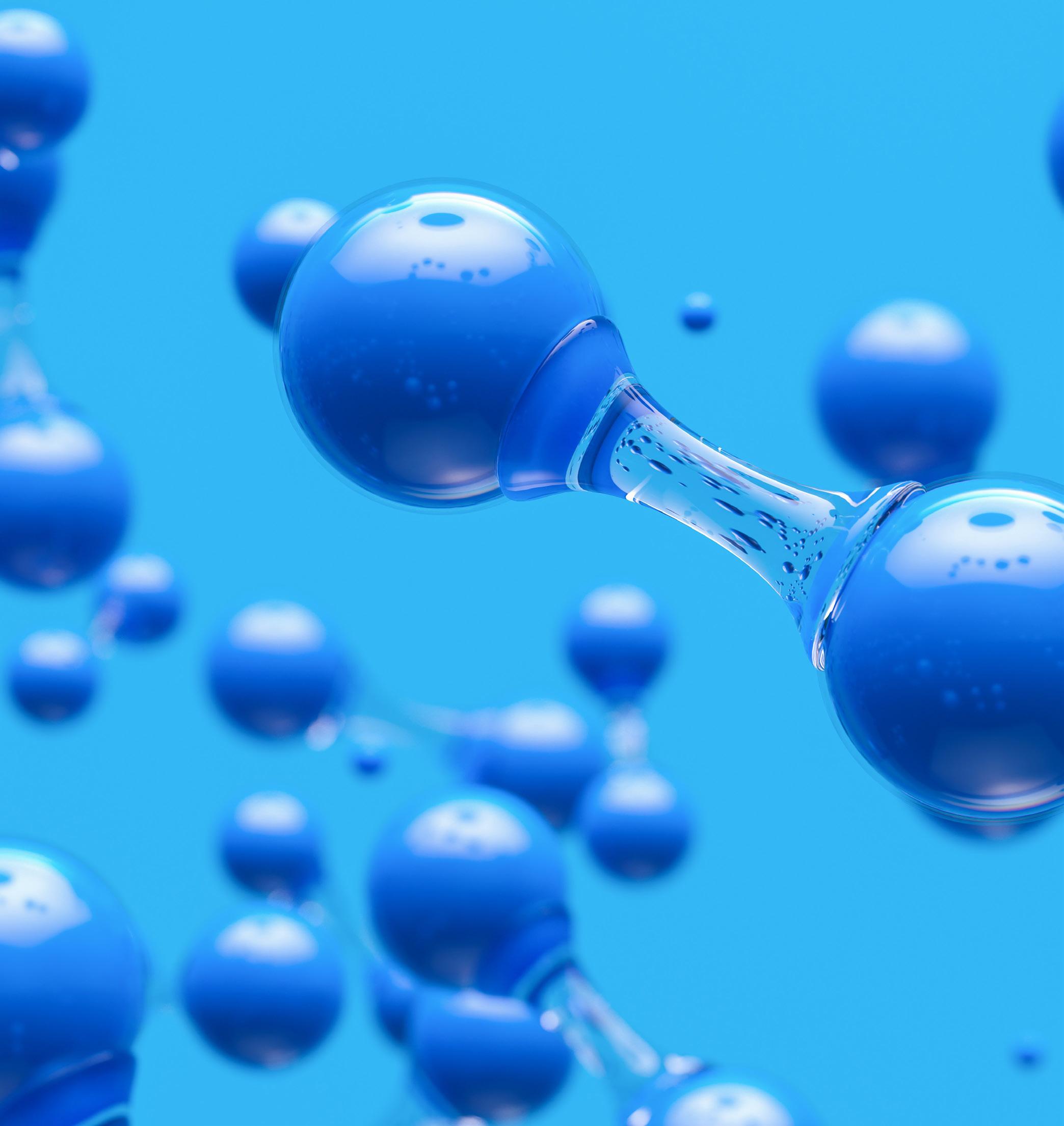
Developing World Leading Standardised Hydrogen Production Plants WORLEY

Developing World Leading Standardised Hydrogen Production Plants WORLEY
PRODUCTION: David Hill
By standardising the design and process around hydrogen production plants, Worley is looking to cement its position as a world leader in EPC for the growing hydrogen industry. As more projects move from concept to FEED, pre-FID and beyond, the need for a programme approach to drive down cost is essential. SVP Global Hydrogen, Chris Gill explains more for Energy Focus.
//Europe’s largest renewable hydrogen production plant is emerging from the ground. Shell announced a Final Investment Decision (FID) in 2022, expecting hydrogen production to begin in 2025. The 200MW electrolyser will be located on the Tweede Maasvlakte in the Port of Rotterdam and will produce around 60,000 kg of renewable hydrogen per day. The plan is to take green electricity produced through an offshore wind farm to power the electrolyser before distributing hydrogen via a new hydrogen pipeline to partially decarbonise activity at the Shell Energy and Chemicals Park Rotterdam. Named Holland Hydrogen 1 (HH1), the project is one of just a few globally to progress to implementation. Hydrogen is the fuel of the future and, because of its green potential, many plans are in development. But
because the industry remains in infant stages, costs are still prohibitive.
Worley, a global professional services company of energy, chemicals and resources experts, is supporting the delivery of the HH1 project and is looking to lead the way in the design and construction of hydrogen production plants around the world.
According to the International Energy Agency (IEA), challenging economic conditions combined with mixed government policies and lacking sight of returns for investors has slowed the progress of low carbon hydrogen rollout, even with interest in the industry remaining strong.
Worley is aiming to add value to driving standardisation across projects, removing complexities from processes, and taking a programme approach where levelized costs can be reduced for international players
looking to deploy across multiple sites.
“It’s nascent, it’s expensive, in most cases the business cases don’t hang together very well, and people are struggling to commit to long-term offtake agreements because of the price of the molecule,” says Chris Gill, SVP Global Hydrogen at Worley.
“Without long-term offtake agreements, you can’t finance the project. Nearly all projects are reliant on subsidies and the subsidy money is not flowing all that freely – someone has to pay a green premium in all of this.”
Shell’s HH1 is important as it paves the way for others to follow. It demonstrates that what has been designed can be built and will work, and it shows that value can move through the chain. In Saudi Arabia, the NEOM Green Hydrogen project – the world’s
largest - has also received a FID and will produce 600 tonnes of carbon-free hydrogen per day by the end of 2026. A 30-year offtake agreement is in place and major companies are involved.
For Worley, seeing ground broken is significant and gives confidence that the hydrogen economy has certainty.
“There is a general agreement that this is the direction of travel, and it is what needs to happen,” explains Gill of attitude in the industry. “But there is always reticence and people want to see something that has been built first. We have been working with several customers to assist with innovative plans. Proof of concept is still required for customers, but we do have a number of customers who are already excited about moving forward.”
While only a few standardised, renewable projects have progressed significantly on a global scale, Worley is extraordinarily busy. The company boasts skills in abundance and is laden with engineering and project capability from its historic involvement across energy, oil and gas, chemical, and other process industries. At the same time, the Worley team is expert in attracting finance and implementing highly successful projects that achieve goals.
We’ve advanced several projects and have independently undertaken efforts to introduce our inaugural product to the market,” says Gill. “While we don’t have a full range of ‘products’ readily available, we’re actively working on it and are progressing in pre-FID phases on a number of standardised projects.
“As we grow in the market, we’ll achieve more volume in the supply
// THERE IS A GENERAL AGREEMENT THAT THIS IS THE DIRECTION OF TRAVEL, AND IT IS WHAT NEEDS TO HAPPEN //
chain and that will iterate. We expect the product development cycle to then reduce costs while improving efficiency.”
Competitors are also busy with more than 40 countries around the world making it clear publicly that hydrogen is part of the longer-term energy mix. Thanks to Worley’s long history working in tandem with downstream and chemical and integrated energy companies, there is a clear advantage. “I think we are a little further ahead than most because of the traditional work we have been doing in the hydrogen space with a number of our traditional customers,” says Gill.
Currently, significant project details remain closed in terms of media coverage, but Gill confirms that Worley is active with global organisations in traditional energy, power and utility, and private equity to develop, with more than 470 hydrogen projects at various stages.
“We’re engaged in multiple
hydrogen projects for a global customer, showcasing how customers adopting a programmatic approach facilitate faster standardisation. These projects are backed by solid balance sheets and secured offtake agreements. It’s essential for project economics to align for approvals, and customers like these are pivotal in propelling the industry forward.
“We are working with a number of utility customers –those with renewable portfolios looking to convert electrons into molecules – who have programme approaches and we are active across a number of different scopes.”
As the industry advances, Worley sees its value add as a unique ability to drive down cost by offering standardisation solutions across. To achieve this, the company is actively engaging the supply chain to create simple and
Honeywell solutions cover the entire value chain when it comes to the reduction of carbon dioxide through the use of hydrogen.
Worley and other contractors around the world are busy developing the future of energy, investing in hydrogen to fuel the progressive energy transition. It’s a challenging but exciting adventure and requires innovation at every stage to pave the way for the low-carbon foundations of tomorrow.
Partnering with Honeywell to develop advanced control and automation systems, Worley is focused on delivery and cost-efficiency for the industry.
Together, the companies have developed the Worley Repeatable Accelerated Package (WRAP) scope, focused on green hydrogen production.
“It is now starting to move from predesign into project sourcing and execution,” says Tim Cook, EMEA EPC Sales Director at Honeywell.
Currently, both companies are looking at providing an ‘off-the-shelf’ solution for a major international energy business keen on green hydrogen usage in the production of sustainable aviation fuel.
“We are busy across multiple sites, at various stages, and we are in the middle of design before Final Investment Decisions happen later in the year,” says Cook. “Worley do the process design first and then they look at the control and automation systems, and that is where we get involved. We work across renewable energy, through the electrolysers to purification and compression – that is where our WRAP is successful. We provide control and safety systems, and we are looking at temperature, pressure, flow, and various other parameters. We take in a lot of data and control the process based on that data.”
Honeywell has set up a demo station at Worley HQ in the Hague. From here, where more than a year of engineering and design has gone into a concept without commitment from an official customer, Honeywell is displaying how standardisation is key in driving down the prohibitive cost of green hydrogen.
“We are putting remote input/output in the field instead of having cabinets dotted around a site. Also, CCTV, alarm systems, fire and gas systems, building protection systems – we can bring all of that together.
We can offer a fully integrated, standardized solution resulting in significant cost reduction. Applied over multiple installations for large multi-site programs, this can offer further increased savings,” explains Cook.
Investing now offers Honeywell first mover advantage in an industry expected to boom over the next decade. Longer-term, the company is already planning systems that could allow for centralised control over a global network of hydrogen production sites, expected to come from current energy majors.
“Between Worley and Honeywell, we believe we can make these projects attractive and investible.
“Hydrogen is not new, but green hydrogen is novel. It’s all about making it cost effective against grey hydrogen. Budgets are tight, everything must be efficient – no waste, no spare capacity, no contingency. Solutions must be perfect and that is why we have spent so much time working these things out,” concludes Cook.
“It has been great working with Honeywell as our Main Automation Contractor partner over the last year as part of the Worley solution helping to reduce the levelized cost of hydrogen production. I am looking forward to all that hard work maturing into projects soon,” says Chris Gill, Worley VP of Hydrogen.
Learn more about Honeywell’s enablement of the hydrogen economy today
minimal solutions around their area of expertise, while working within a functional Worley brief. Gill says that this must be done across Capex and Opex if the hydrogen economy is to reach a self-sustaining position.
“In Capex, we are trying to standardise the asset and remove complexity. An important part of that
is to make it supply chain led.” He gives the electrical example, where Worley has a key strategic supply chain partner. “Rather than us designing several different motors or electrical drivers, we are asking the supply chain to come up with the easiest way to do things so that you have the simplest electrical arrangement. We think that
will lead to more economical assets.”
For Opex efficiency, the embedding of digital solutions is vital. Utilising digital solutions across appropriate digital platforms allows for operators to get better outcomes from assets over the asset lifecycle. “This challenges
Continues on page 8
INDUSTRIAL CYBER SECURITY
RENEWABLE HYDROGEN LOOP
HONEYWELL EXPERION® PKS
Infinitely Scalable, Fault Predictive, HIVE®
INTEGRATED DIGITAL TWIN
Grid to Gate Power and Process Digital Twin
INTELLIGENT OPERATOR COCKPIT
AI Enabled Suite for Future Ready Operation
SAFETY & SECURITY
Fire and Gas Detectors Gas Cloud Imaging
PLANTWIDE OPTIMIZATION
Optimizing LCH and Derivatives in Realtime
WORKFORCE COMPETENCY
Competency, Safety and Productivity
HYDROGEN PASSPORT
Realtime Carbon Intensity Management
ADVANCED ALARM MANAGEMENT
Operations and Worker Safety
EQUIPMENT EFFECTIVENESS
Predictive Asset Performance Management
LEAN&MODULAR EXECUTION
Design, Integration, Implementation, Construction, Testing & Commissioning Modular, Flexible and Scalable Deployment
assumptions in the business case to enable it to take off,” Gill adds. With standardisation across the planning and implementation process, positive relationships with suppliers are essential. There must be shared vision and there must be a willingness to advance the industry and not simply a quest for short-term profit. The company works closely with most manufacturers of electrolysers
and has invested R&D capability in creation of solutions at industrial scale to fit around electrolyser OEM scope.
Honeywell is one of Worley’s control and automation partner, using its unmatched global presence to develop simplified, but above all safe, solutions in hydrogen production facilities.
“We work very well together, they get our vision, and they share that vision. We have a number of common
customers and so collaboration makes a lot of sense,” states Gill. “Ultimately, standardisation will reduce the levelized cost of the product. If we get this right the pie will be bigger because projects will go through FID and get to implementation, and we will hopefully get a bigger share of the pie.”
Gill is keen on involvement in projects far and wide, but stresses that producing green hydrogen for use in the energy industry is by no means easy. The level of funding and skill required to bring about progress is significant. “The challenge of how to put projects together and the challenge of standardisation and commercials, combined with process experience, is where the common middle ground is,” he says, adding that the company has some of the best minds in the industry working on solutions every day.
“If it was easy, everyone would do it. We have a number of industry gurus and people who really know
their stuff. Our teams attract different, younger talent. We appeal to people who want to be in clean energy, and they feel good about being in clean energy. It’s a magnet for talent and requires a different way of thinking and a different way of doing things, and that is great. From a development and retention point of view, it’s a real positive. When we started moving in this direction, I was quite surprised by the number of people who came and asked to be part of it.”
Part of the industrial gas space for 16 years, Gill started out with BOC, looking after operations in Korea. He then ran his own business for four years before joining Worley, responsible for downstream chemicals. He became MD for Spain, Sweden and Belgium in 2019 and then demonstrated a good understanding of traditional customers and knowledge of how industrial gas companies work before taking over the hydrogen business. “The hydrogen molecule has been used for a long time and industrial gas companies are front a centre in that. They went
through a process of standardising assets 20 years ago,” he says.
Through his career, he is confident that the hydrogen space has certainly seen progress, but more needs to be done to advance hydrogen as part of a strategy to achieve net zero by 2050 and reduce emissions by 45% by 2030, according to the Paris Agreement
“Have we seen progress? Yes, absolutely. I have been in this role for four years and when I started, 20MW was a big green hydrogen project. 500MW or 1GW is now a big project. The scale of the projects has increased, and we have seen projects develop to the point where the business cases work. We are seeing projects get through FID and HH1 is a good example – we are building it now. Is it enough to meet 2030 targets in which hydrogen is part of the solution? No.”
As more projects advance through the challenging stages with the help of Worley, and the hydrogen economy makes material progress, the company’s standardisation efforts will continue to drive down cost and improve
efficiency, allowing more countries, companies, and people to take advantage of carbon-free, clean, safe, and innovative hydrogen production to fuel the world of the future.
“We want to be one of the key market leaders in the space. It’s in the sweet spot in terms of what we do and we want to be a go-to provider of solutions in the hydrogen space,” says Gill.
In the short term, Worley is busy in Rotterdam with Shell HH1. And in the medium term, teams around the world are continuing to pioneer in the industry, bringing thought leadership and engineering excellence to solve problems that others cannot. Gill is embracing the challenge and enjoying the collaboration.
“It really is very exciting,” he concludes.