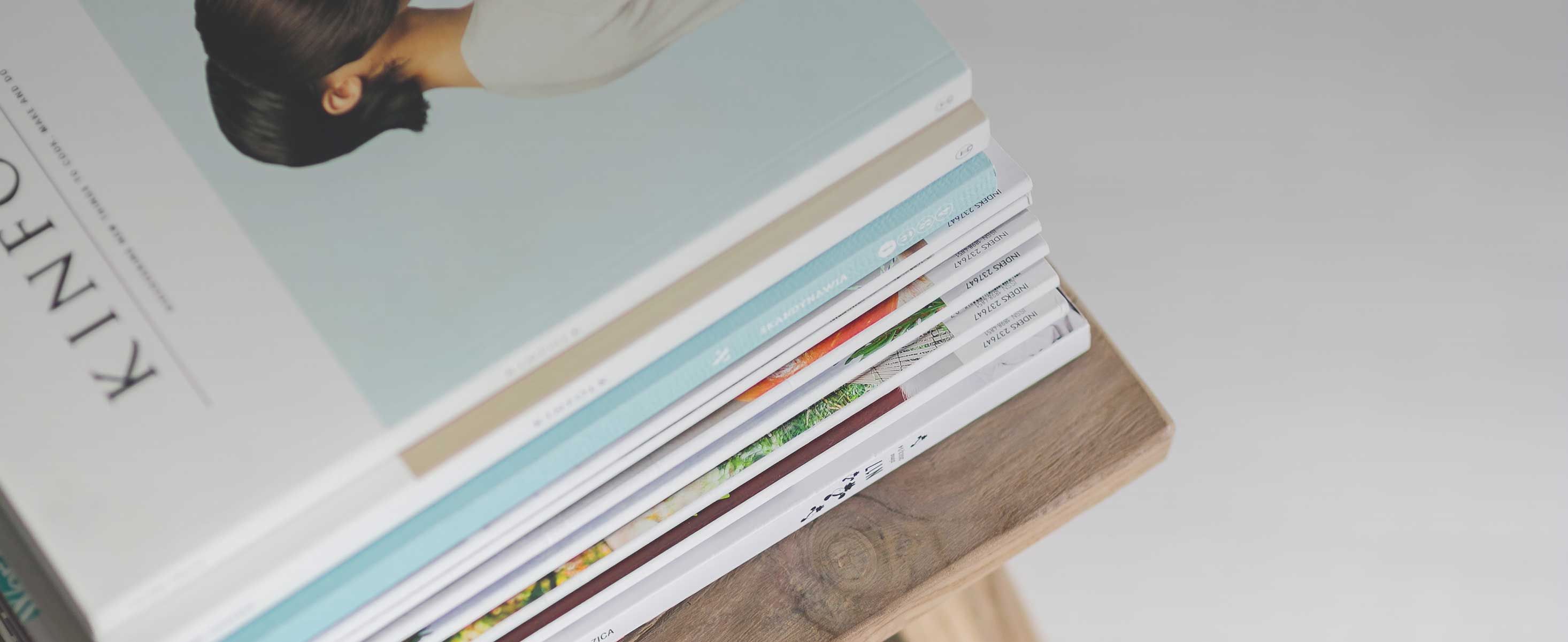
3 minute read
How Both Sides Win
When new owners purchased Integrated Manufacturing Solutions (IMS) of Shakopee in 2014, it was a typical early-stage company focused on getting its business off the ground and fostering consistent growth. Developing a culture of employee support and advancement just hadn’t been a top priority.
Full-time and contract employees worked on sheet metal manufacturing, powder coating, laser cutting, and welding, but they didn’t really have insight into how their efforts helped customers. Opportunities to learn and grow at IMS were limited, as were employee benefits. It was more of a punch-the-clock operation, says Kevin May, president and CEO of St. Paul-based CT Holdings, which owns IMS.
Advertisement
CT Holdings provides its portfolio of small businesses with shared services, including finance, operations, and human resources. Its leaders sought to transform IMS into the well-oiled manufacturing company they envisioned by changing how it approaches its most important asset: its people.
“We’re really in the people business,”
May says. “Our goal is to build sustainable businesses around people who happen to do industrial wireless communication, software development, or fabrication, and build a foundation of perpetuating growth and stability. It’s about leaving things better than
Kevin May, president and CEO
May and team found that the best way to improve IMS was to change the way it provides opportunities for advancement while bolstering its benefits. The company started in 2019 with offering health care insurance to employees and their families, later adding a 401(k) and short-term disability while aligning pay to the market.
“IMS didn’t create stability or opportunity for growth for its people,” May says. “When we came on board, we really wanted to improve conditions for employees. It’s about ensuring that you have a safe place to work and that you are delivering value — and you should get something for that.”
Transformed training
Another key change involved the way IMS handles training. Leaders developed a progression plan for employees who are interested in learning new skills. Generally, new hires come in as contract workers, giving both sides time to get to know each other. When IMS hires people full-time, they can begin training in departments like press brake operations, laser cutting, and powder coating, says Charlie Pehrson, vice president of operations.
Participation is voluntary. Those who sign up follow a four-level progression under the direction of a lead employee in the department. They work at their own pace to master a range of skills at each level, Pehrson says. If they want to reach level one or two and stop, no problem. And if they want to continue until they complete all four levels, even better. As employees finish each level, IMS adjusts their wages to reflect their new capabilities.
“It’s very unique and it’s been a success,” Pehrson adds. “Employees look at it as a value-add or a hidden perk. They are able to expand their knowledge, and they are grateful to be given the opportunity. Everyone needs an opportunity to move into a new role.”
The training program also helps IMS build resilience in its operations. If one area of the business is slow and another slammed with work, employees with cross training can shift gears to work in another department instead of being sent home, May says.
These changes — and many more — have put IMS on a strong growth path. When CT Holdings purchased IMS, it had $2 million in sales. In 2022, IMS brought in $10 million and is on track to hit $11.3 million in 2023. IMS now has 70 total employees, including 46 full-timers.
Another key contributor involved leaders’ efforts to build a worker-friendly culture.
To increase staff members’ connection to their work, IMS started holding employee appreciation events and inviting customers. While celebrating with food trucks and games, employees also see the final result of their manufacturing work. At one recent gathering, employees were excited to watch a part that they painted or welded in action on a customer’s security product.
“They saw what it’s doing and the value it’s bringing to the world,” May says. “It’s a big deal for me personally to show employees why they matter to each other, why they matter to their customers, and why their work has value beyond IMS.”
Change management
Instituting all of this change wasn’t easy, especially as IMS had to fight through the upheaval of the pandemic, too. It took time to build trust and get buy-in with staff, prompting the company to call on Enterprise Minnesota consultants for help with leadership development. Together, they built a cohort of employees in key departments who champion the changes across IMS.
The company’s improved training and benefits has bettered its ability to retain employees in a tough hiring market. It also helped fuel a shift from being more of a job shop with significant churn in work and pricing to one that builds deeper relationships with customers and provides more stability to all.
IMS’s combined efforts to enhance the employee experience are paying off. At their core, the changes send the message to staff that they are an important part of IMS, with pathways to continue building skills and opportunities, May says.
This transformation has confirmed May’s view of how to grow profitably and sustain that growth at any company. “Employees are the most important asset in your business,” he adds. “If you can’t connect the value you’re bringing to them with the value they’re bringing to you and that both sides are wining, then both sides lose.”
Suzy Frisch