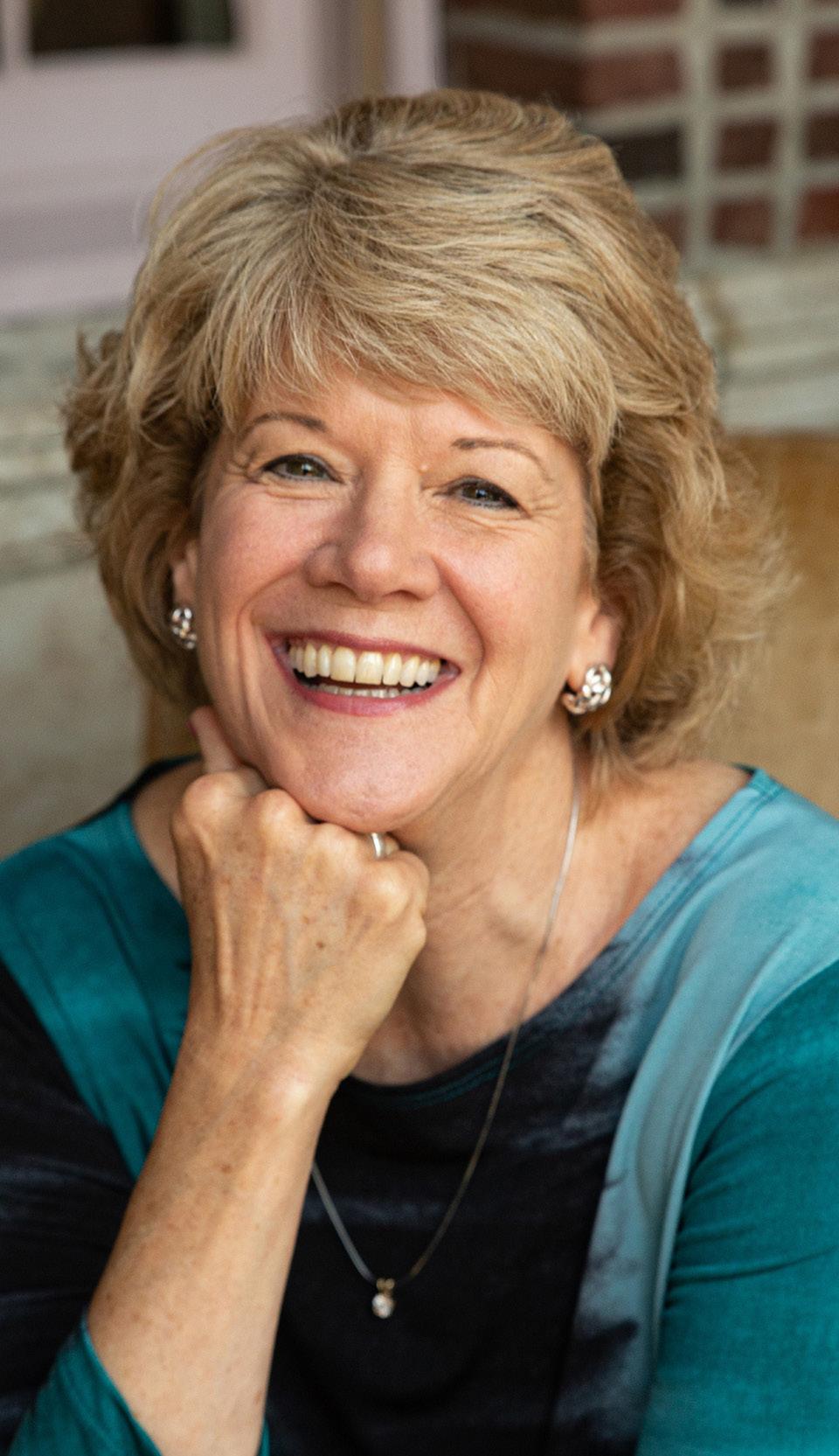
2 minute read
Bridging the GAP
In tiny rural towns, in the heart of the Twin Cities, and sprinkled throughout the suburbs and the small cities across the state, you can almost hear the hum as Minnesota’s manufacturers produce everything from luxury saunas and high-performance cycling products to industrial springs and roasted coffee. Since the legislature established Enterprise Minnesota as a non-profit consultancy in 1987, our mission has been to help small- and medium-sized manufacturers grow profitably and provide great careers for every Minnesotan. There are plenty of manufacturing jobs out there for hire!
We pursue those goals using many tools, none more critical than the one-onone assistance provided by our business developers and consulting experts. Since 2008, the Growth Acceleration Program (GAP) has made this expertise more accessible to the manufacturers who need it most through a dollar-for-dollar matching program available to those with fewer than 250 employees.
Advertisement
Our consultants provide services in many areas, but the current demand is high in employee retention, continuous improvement/lean, ISO certification, and strategy/succession planning. Smaller companies benefit greatly when our experts help navigate them through these particular challenges.
Low unemployment and steady growth in manufacturing jobs mean that attracting and retaining employees challenges all manufacturers. Our advisers work with companies to assess their needs and develop strategies to help them recruit, train, and retain the best employees.
Aagard, an Alexandria engineering company that builds custom packaging and automation systems, worked with Enterprise Minnesota business growth consultant Michele Neale on employee development and retention programs. First she helped the company develop a curriculum for employees, and later she helped build the company’s successful mentoring program, creating presentations to give new hires a sense of Aagard’s culture while improving employee engagement and retention in the process. Many companies respond to the persistent worker shortage by implementing continuous improvement or lean initiatives. Homecrest Outdoor Living in Wadena faced a COVID-related demand surge as consumers spent more time outside. Homecrest staffed up, but also knew it needed to do more with the employees already on its team. Enterprise Minnesota business developer Bill Martinson suggested they work with us to implement lean manufacturing techniques and refine welder training and operations, helping the company produce more with its existing team.
H&S Specialties, Inc is a custom plastic injection and mold building company in Glenwood. Company leaders understood that achieving ISO certification could improve their process documentation, secure their client base, and ensure the viability of the company with a proven business management system. Enterprise Minnesota ISO expert Keith Gadacz conducted a quality assessment, helped address process and documentation gaps, and communicated the process to all 12 of H&S’s employees. With Gadacz’s assistance, H&S created a business management system that was simple and easy to use, and the company passed the certification, helping it retain those 12 jobs and $1.4 million in sales. Through the process, H&S invested $85,000 and generated $30,000 in cost savings.
GAP can be a real game changer for these kinds of companies. It’s also an outstanding investment for taxpayers. Since its creation, GAP has documented returns of at least 25:1. GAP has helped more than 418 manufacturers invest $583 million in plant, equipment, technology and employee skill development, while increasing or retaining sales by $1.46 billion.
Minnesota’s manufacturers employ 325,000 workers, with employees earning an average of $76,181 annually. That’s 16% higher than the state’s average salary. And the economy-wide ripple effect is tremendous: Experts estimate that for every $1 spent in manufacturing, there is a total impact of $2.60 to the overall economy.
Maintaining manufacturing’s strength is essential to Minnesota’s future. As the legislature considers funding for GAP again this session, we hope policymakers will recognize the important role this program plays in keeping manufacturing strong, particularly in small cities where manufacturing may employ most residents, and in underserved communities throughout the state. These companies provide outstanding career opportunities for Minnesotans of ALL backgrounds.