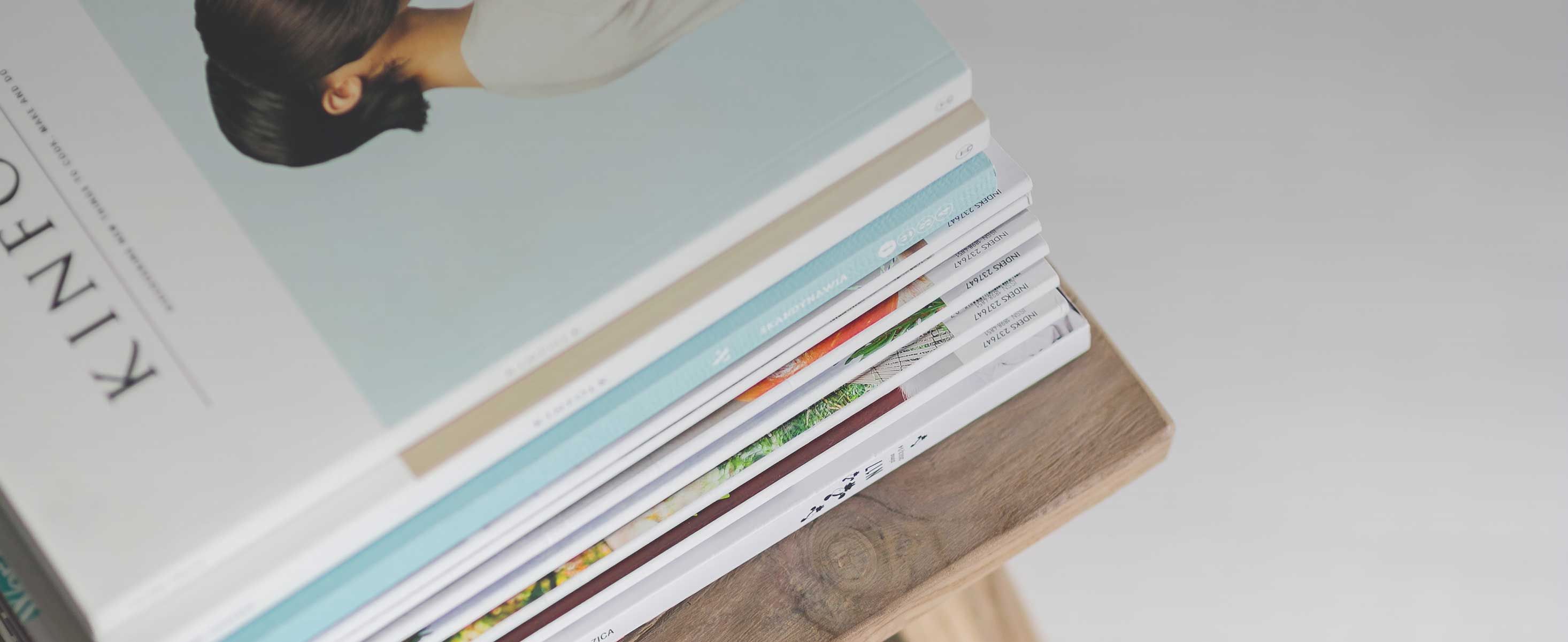
2 minute read
FILM COATING OF ORAL SOLID DOSAGE FORMS: THE CRITICAL PARAMETERS
from EPM July/August 23
by EPM Magazine
Author: Prashant Deshpande, Head, Process & Technology Support at ACG Engineering, discusses the critical process parameters of film coating and the measurement, monitoring, and recording of tablet bed temperature in batch manufacturing.
Achieving the optimal spray rate is also vital in preventing coating defects. These range from blistering, chipping, colour variations, and smudging, through to logo bridging and the rejection of entire batches due to non-complying product standards and specification. Physical appearance is one of the quality tests as a standard in the specification for pharmaceutical products. Too high a spray rate may result in coating defects such as picking, sticking, and twinning. At the other end of the scale, a low spray rate can cause spray drying and a reduction in coating efficiency.
Spray rates are monitored and controlled precisely by defining process variables in the batch manufacturing process. They are continuously monitored with a display showing the flow of the coating and its dispersion via the transfer pump.
Managing Extremes
Generally, for a process developed and designed based on the QbD principle, each critical process parameter is defined, ranging from lower to higher limits. Overheating or underheating can lead to a defective product profile such as surface irregularities, twin tablets, or product non-complying standard specification. To monitor and control process parameters, several temperature sensors are incorporated in the equipment, including:
- Resistance Temperature Detector (RTD) - a sensor that measures and senses the temperature of the tablets during the coating process. The RTD’s resistance increases as the temperature of the sensor increases.
- Infrared temperature sensor (IR) - it is important to note that this sensor will sense and measure the temperature of the top layer of tablets and not the bulk of tablets with the help of IR light’s wavelength that falls on the surface of the tablet.
Optimising Tablet Bed Zones
In the smart coater the rolling tablet bed is divided into two distinct zones - the coating zone and the drying zone. The temperature of the tablets in each zone varies by just a few degrees depending on the formulation, solvent system, and process. Typically tablets in the spray zone are at a lower temperature than tablets rolling in the drying zone, which is inside the perforated coating drum.
Process airflow plays a key role during the process in the coating drum, where the product is coated and dried simultaneously. The drying process is a function of the volume, velocity, temperature, and relative humidity of incoming airflow. The negative pressure in the coating drum is maintained and monitored during the process. Optimised process parameters ensure final product coating is uniform and smooth in appearance.
Monitoring Temperatures
Measuring, monitoring, and recording tablet bed temperature ensures that operators work within a validated range to impose a limit for the product temperature. The limit is defined based on the principle of risk analysis during the development stage.
Others work on process control, based on the adjustment of inlet temperature to maintain the required exhaust temperature. This measure is widely used as it is assumed that it closely resembles the tablet bed temperature.
The exhaust temperature is one of the process parameters that is monitored during the process. In the absence of tablet bed temperature data, the exhaust temperature provides a reasonable estimate. The temperature of the exhaust air flowing across the tablets is measured by a sensor kept near the tablet bed, outside the perforated coating drum.
Whether the manufacturing process adopted is based on the measurement, monitoring and, recording of the tablet bed temperature, or a process control based on the inlet and exhaust temperatures, during the batch manufacturing process, there will always be a margin of error for either practice. However, such small variances in product or exhaust temperature do not have any impact on the critical quality attributes of the film-coated tablets. The critical process parameters are spray rate, pattern, atomisation, drum revolutions per minute (RPM), inlet air temperature and airflow across the tablet bed.