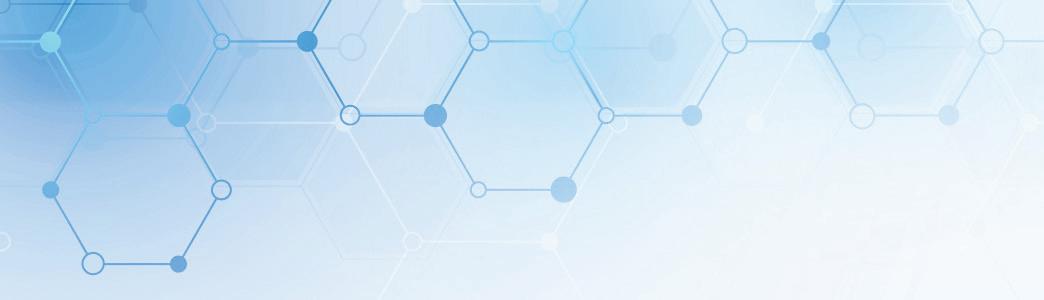
2 minute read
THE PAIN OF CHANGE –COULD SUPPLIERS BE PART OF THE CURE?
from EPM July/August 23
by EPM Magazine
Author: Matt Cokely. Global Technical Consultant Regional leader (APAC).
The Pharmaceutical and Medical Device industries rank amongst some of the most highly regulated industries in the world. Safety is quite correctly a primary concern, so the industry can often seem conservative, slow to react, and unwilling to change procedures and practices. However, somewhat counter-intuitively, a constant feature for this allegedly conservative industry is change.
This can be driven by new excipients or APIs, changes to delivery methods or systems, novel manufacturing equipment and techniques or the shift towards individualised drug therapies often using a patient’s own cells that have been adapted or manipulated. Pharmaceutical companies must be ready to adapt to new ways of doing things, whilst still maintaining a high degree of control, complying to regulatory requirements, and at the same time carefully documenting and assessing the impacts of any changes.
Companies are unlikely to make a change unless there is a compelling event or a change imposed upon them. Whilst the industry does have a commitment to continuous improvement, the reality is that in a busy pharmaceutical manufacturing plant with a time challenged workforce, people are unlikely to initiate or engage with any changes where there is perceived to be little benefit.
A recent example of a compelling event is the revision of EudraLex Vol.4 Annex 1. End users now need to consider cleaning prior to disinfection, and management of residues, both of which could require the introduction of new chemistries, changes to long standing disinfection practices and procedures, and to application frequencies, sequence, and rotation of agents.
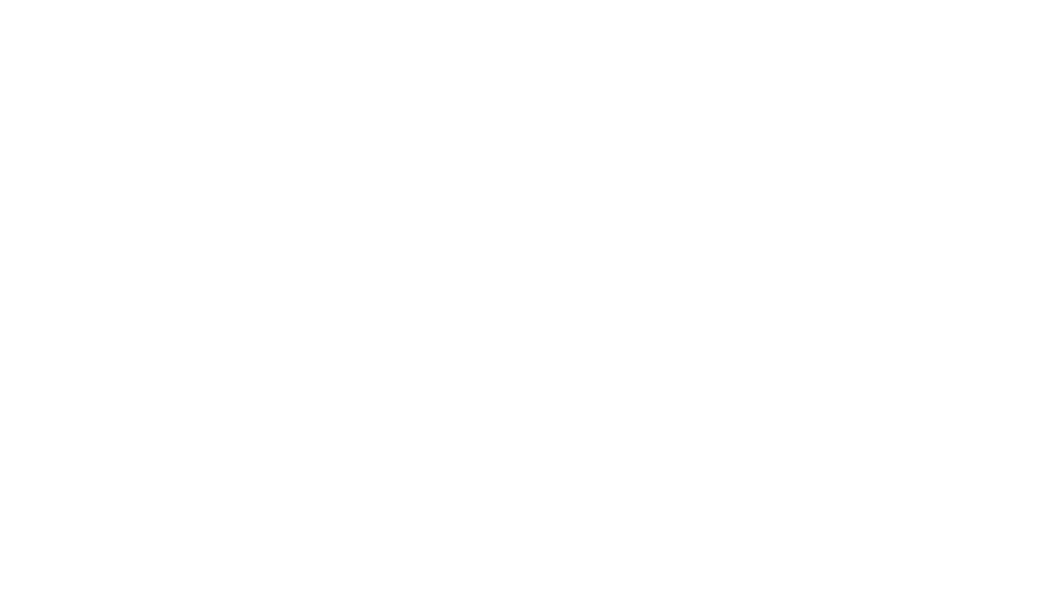
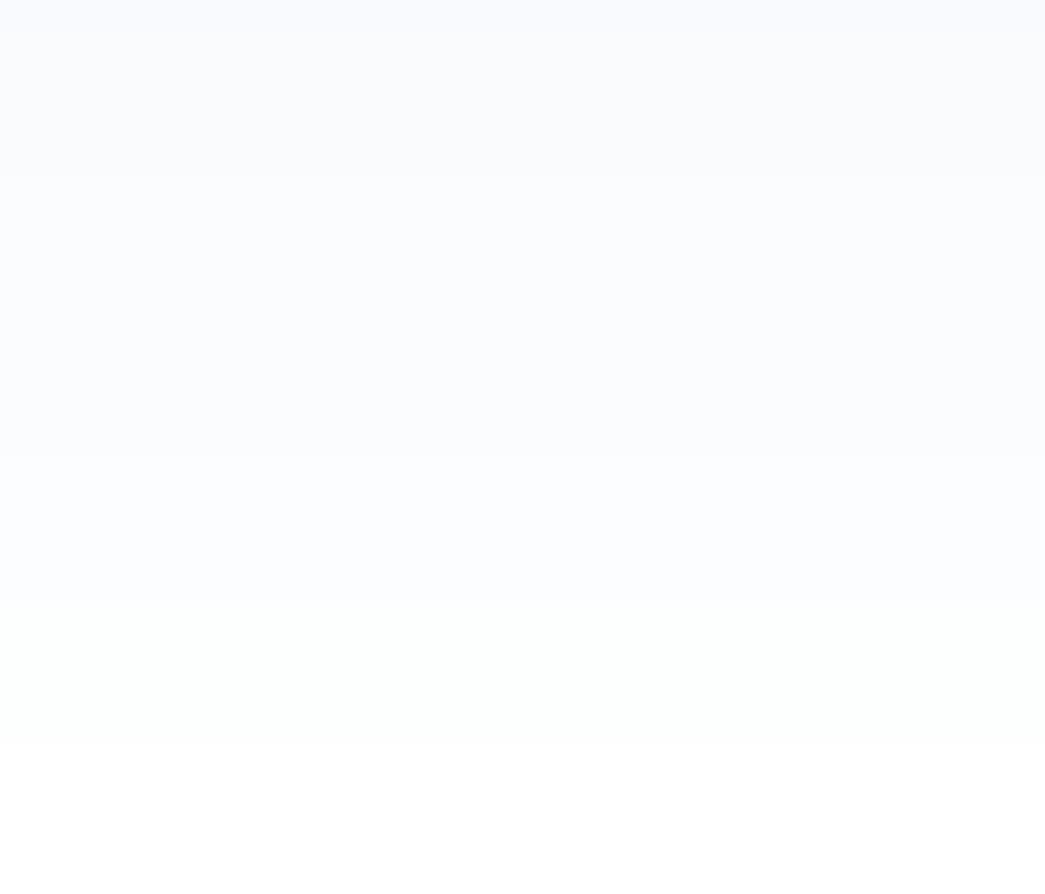
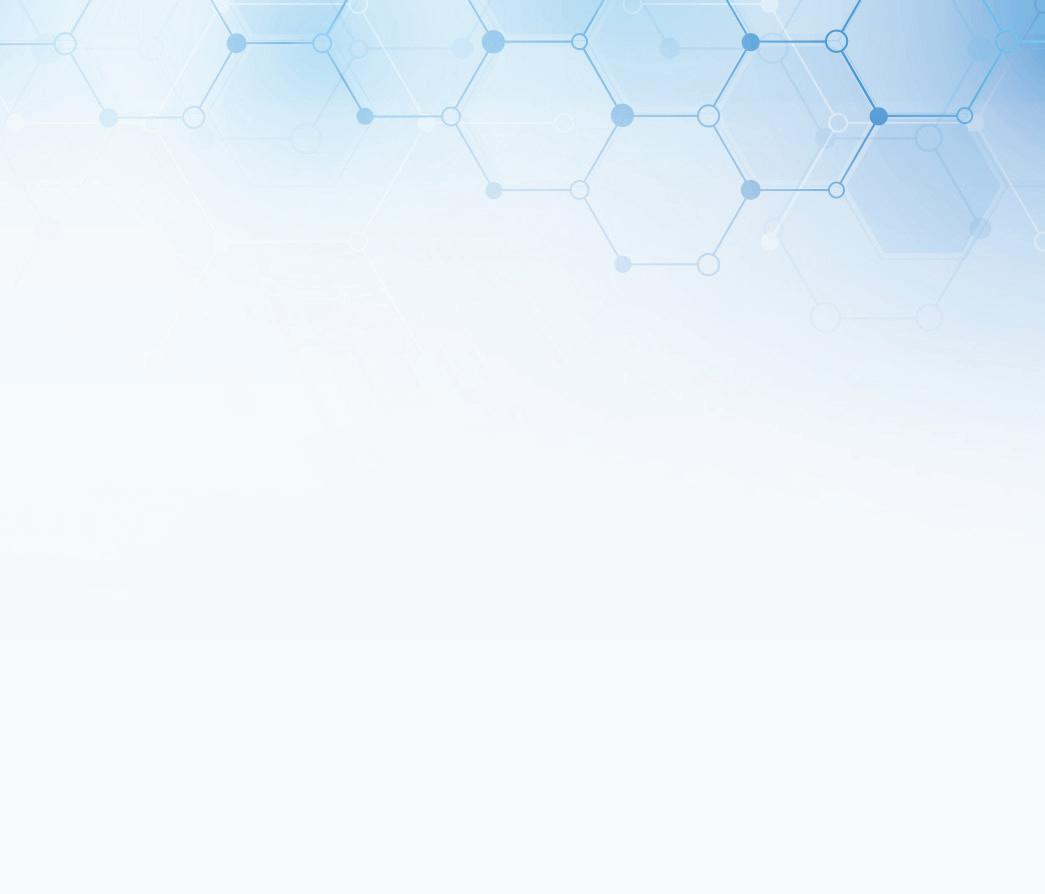
For any changes, end users must produce written documentation detailing the rationale, reason, or purpose for the change, whilst also assessing it for any impacts on safety, health, and the immediate manufacturing and wider environment. Only then can they move to final authorisation, approval, and implementation of the change.
This documentation process, whilst entirely necessary can also seem cumbersome and daunting, and be a barrier to making changes. Reputable suppliers of detergents, disinfectants and sporicides for cleanroom surfaces such as Ecolab Life Sciences should be able to support change management processes to try and alleviate some of the burden. Support packages should include both standardised and bespoke documentation services designed to offer practical help, guidance, and in some cases the complete provision of various document types that can broadly be divided into five key categories:
1. RISK ASSESSMENT
• Documented rationale, reason, or purpose for making the change.
• Risk assessment and CCS for cleaning and disinfection practices.
2. SUPPLIER APPROVAL
• Documented assessment of any alternative disinfectant supplier, or existing suppliers’ manufacturing conditions.
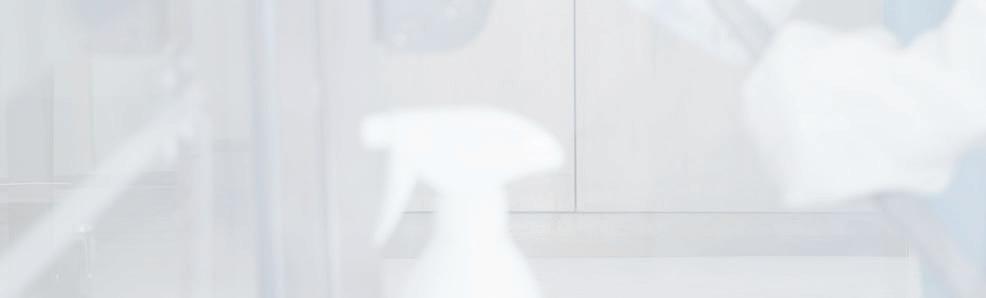
3. PRODUCT SELECTION
• Creation of a rationale for selection of cleaning and disinfectant agents.
4. VALIDATION
• Authorship of validation strategy or plan (Phase II or laboratory study).
• Assessment of independent, accredited, experienced third part test laboratory to conduct validation (recommended).
• Support with creation and approval of validation protocol(s).
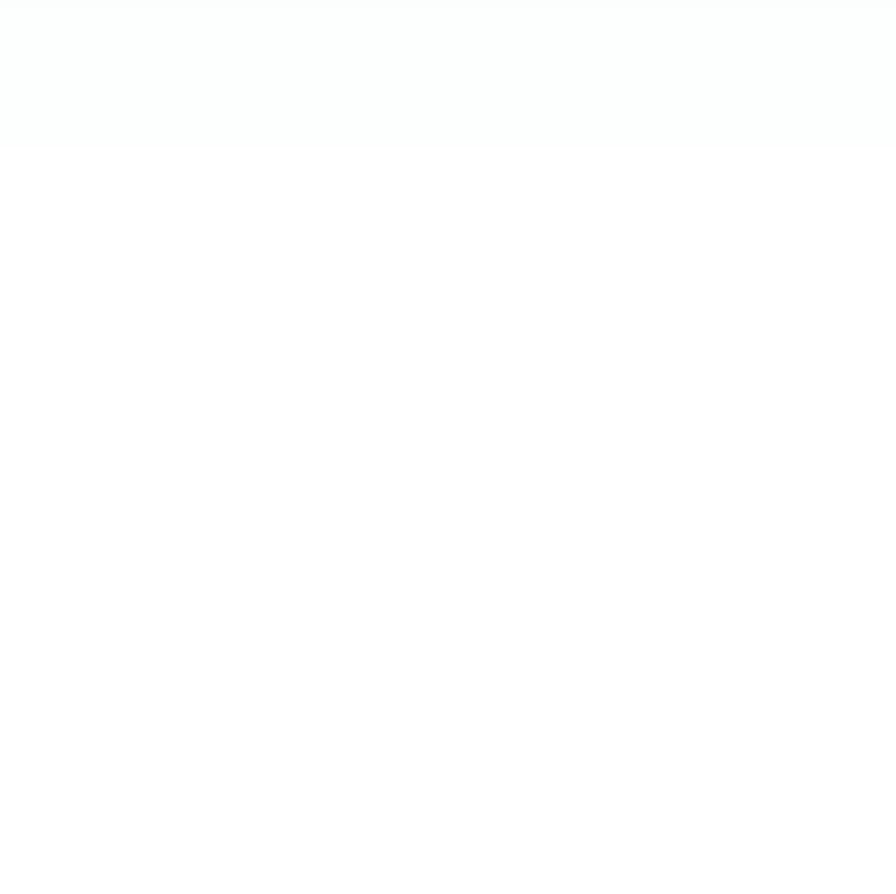
• Validation results review and re-test strategy advice.
• Help to design of end user trial under ‘in-use’ conditions (aka Performance Qualification (PQ), Field trial or Phase III study).
5. IMPLEMENTATION
• Help with creation of a Change Control document to implement new cleaning/disinfection products (or HPV bio decontamination equipment or procedures).
• Training of relevant personnel.
• Assistance for changes to SOPs, procedures, logbooks, and other controlling documents.
Change Management is integral to Good Manufacturing Practice (GMP). The change management and change control system provide a consistent and wellstructured approach towards managing deviations and changes. It also enables end users to document the details of these deviations and changes and helps in risk control and management.
However, change management programs must be conducted in a considered and measured way, using all available (and wide ranging) expertise both at an end users’ site and any external support that is appropriate and available. Commissioning support for this from a third party can reduce the burden of these document changes.
So, whilst change can be seen as a challenge within the pharmaceutical industry, with the right support and services from experts in the field such as Ecolab Life Sciences, the burden associated with change can be lifted, and more efficient, successful outcomes, achieved.
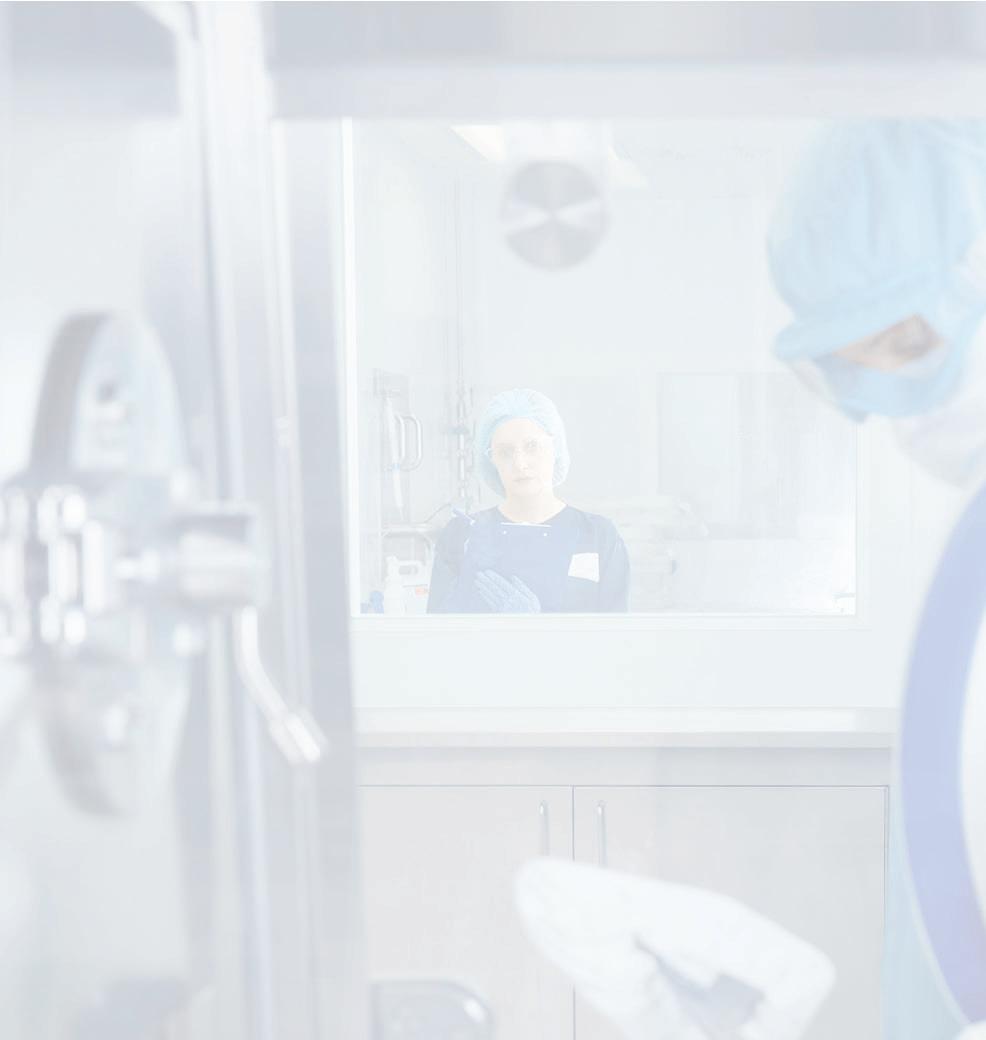