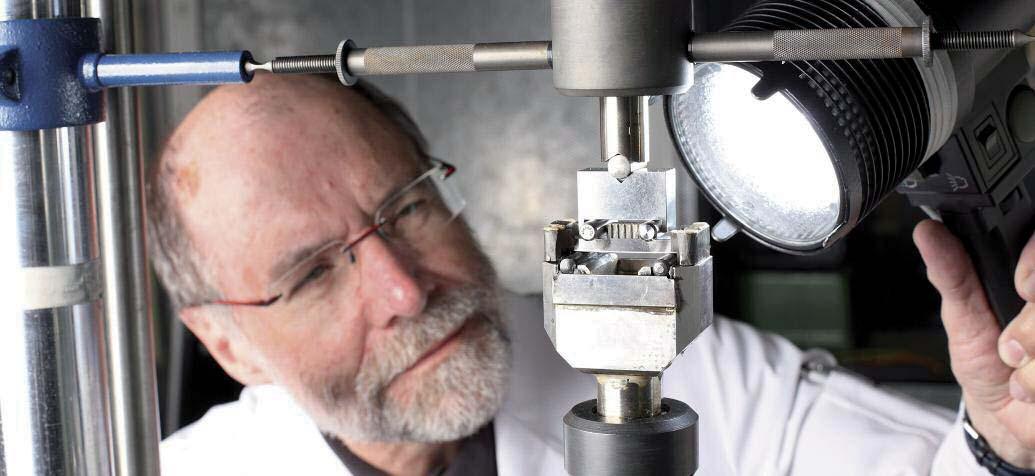
6 minute read
Dr Joachim Wulf, Berlin
New technologies permit reduced noise and climate protection Cutting-edge technologies for geared turbofan engines
by Dr Joachim Wulf, Chief Engineer, Technology Demonstrators, MTU Aero Engines, Munich
Aircraft engines of the future will have to be quieter, more fuelefficient and cleaner than the engines in service today. MTU Aero Engines has been working for years on new technologies to further improve the environmental compatibility of future engines. The future belongs to the geared turbofan engine™ (GTF). Pratt & Whitney and MTU are collaborating on the PurePower® PW1000G to develop a game-changing propulsion concept and are planning to build a complete family of engines based on this concept.
GTF is a real breakthrough This technology holds the promise of reducing fuel consumption and CO2 emissions by 15% each, and of cutting present perceived noise levels in half compared with today’s engines. Among its key components are the unique, high-speed lowpressure turbine made by MTU and a high-pressure compressor jointly built by Pratt & Whitney and MTU. This year, MTU was honored with two German innovation awards for the highspeed low-pressure turbine. The GTF concept is catching on with air framers: Airbus is offering the geared turbofan engine for its re-engined A320neo; Bombardier has selected it as the exclusive engine to power its new CSeries; Mitsubishi will equip its MRJ with this new type of propulsion system; Irkut has chosen it for its MS21, and Embraer has picked the GTF engine for the upgraded versions of its E-170 and E-190 family of aircraft.
Dr Joachim Wulf is Chief Engineer, Technology Demonstrators at MTU Aero Engines and has been responsible for the development of all of MTU Aero Engines’ technology demonstrators since 2012. The longstanding German company engages in the design, development, manufacture and support of commercial and military aircraft engines and industrial gas turbines. Wulf studied Mechanical Engineering at the Technische Universität, Munich, from where he earned his PhD. After joining MTU in 2001, Wulf worked in various positions at the company’s headquarters in Munich before taking on the role of Engineering Director at MTU Aero Engines Polska in 2008, with responsibility for setting up the engineering and development location in Rzeszów. Today, on-site operations include parts repair and assembly activities in addition to engineering and development. Photo: MTU Aero Engines
Reducing noise and protecting the climate Thanks to its efficiency and markedly reduced noise emissions the GTF will make an important contribution towards climate protection in the future and there is still great potential for improvement. Under the European Clean Sky Joint Technology Initiative, which is approaching the home stretch, the successful technology will again be substantially enhanced. The various project activities, which span the whole gamut of game-changing aircraft, engine, system and eco-design concepts, are coordinated by the Clean Sky Joint Undertaking especially set up for the purpose. Targets to be met by the year 2020, let down by the Advisory Council for Aeronautics Research in Europe (ACARE): Aircraft are expected to emit 50 % less carbon dioxides (CO2) and 80 % percent less oxides of nitrogen (NOx) as compared with year 2000 levels. The perceived noise level is to be halved.
Clean Sky activities MTU Aero Engines is participating in this mammoth project. High-pressure compressors and low-pressure turbines have for decades been among MTU’s key areas of expertise. In the Clean Sky activities, too, we are mainly focusing on these two modules for the next generation geared turbofan™ engine applications to demonstrate the maturity of the technologies for new, weight-saving designs and materials when subjected to further increased mechanical and thermal loads. MTU is also responsible for building a demonstrator engine. As part of the programme’s “Sustainable and Green Engines” (SAGE) platform, five demonstrator engines will be built. MTU has taken on responsibility for the SAGE 4 sub-project. Plans are to have the demonstrator assembled and ready for testing in the first quarter of 2015. On July 12 this year, the SAGE 4 team passed the preliminary design review with flying colors and is now mid-way through the SAGE 4 sub-project. The design of the demonstrator engine must be completed; all components must be released for production by the end of 2013. The first component prototypes have already arrived in Munich and these prototypes will be put through their paces in components tests. For this purpose, the modified engine parts are provided with a variety of sensors that measure, for instance, the temperature and pressure distribution under simulated load conditions. They also permit the engineers to analyse the behaviour of the parts when subjected to vibrations at different frequencies. If all tests are successfully passed by mid-2014
46 Four-point bending test: An SLM seal carrier is subjected to vibration resistance testing.
photo: MTU Aero Engines
the components can be installed. MTU experts will assemble and instrument MTU’s high-speed low-pressure turbine and the turbine exit casing developed by Sweden’s GKN Aerospace, another partner in the Clean Sky initiative. Then the test engine can be fully assembled and installed in the test cell. Testing is slated to begin in April 2015.
Saving weight through new technologies One thing is for certain – already at this stage: The engine built for the SAGE 4 sub-project is lighter than any of its predecessors. In the high-pressure compressor, new seals made from carbon-fiber reinforced plastic (CFRP) will replace the previously used titanium parts. These CFRP seals weigh less than their counterparts in the rare metal titanium and are less expensive. Further savings in weight will be achieved by the use of components made by additive manufacturing processes, such as inner rings with integrated honeycomb seals for the high-pressure compressor. These parts are built up from a metal powder bed using the selective laser melting (SLM) technique. Additive manufacturing makes production much easier, faster, lighter and provides engineers with substantially greater freedom of design. Another innovative technology, which likewise helps reducing the weight of the geared turbofan, will make its debut in the low-pressure turbine of the SAGE 4 demonstrator. Normally, the airfoils of the individual turbine stages must be of a particularly rigid design to prevent them from vibrating as they are exposed to the hot gases flowing between them at high velocities. But the good vibration-resistance properties come at a price: The airfoils weigh more. The newly developed airfoils with integrated vibration damping are capable of withstanding the critical frequencies occurring in operation without suffering damage. The airfoils are lighter and leaner. This affords aerodynamic advantages that have a positive effect on the overall efficiency of the engine.
Ambitious Engineer Agenda To further increase the efficiency of the next-generation geared turbofans, MTU’s air system specialists and design engineers are currently working to optimise the use of cooling air in the low-pressure turbine. And since the cooling air is part of total air flow to be compressed further upstream in the engine, less cooling air saves energy, and the engine can produce more thrust as a result. The reduction of noise continues to be a topic featuring high on the engineers‘ agenda. In a first step, acoustic damping liners will be used on the turbine exit casing built by SAGE 4 partner GKN. Such liners, which attenuate the propagation of certain frequencies, have already proved their worth in the bypass duct upstream and downstream of the fan. For use in the hot engine section they had to be modified to make them resistant to elevated temperatures.
With the technologies MTU is developing for SAGE 4, the company wants to reduce the engine’s fuel burn by around 3% as compared with current geared turbofans. The longterm goal is a 5-8% reduction. Such a reduction would be a major step forward. Although today’s engines achieve extremely high efficiencies each additional tenth of a percent makes a whole lot of a difference, helping cut down on fuel burn and hence reduce CO2 emissions. The new SAGE 4 technologies might be mature for use in production engines by 2020. MTU’s associates in the SAGE 4 sub-project are the BritishSwedish GKN Aerospace group and the Italian engine manufacturer Avio Aero. Other partners include a number of small and medium-sized enterprises (SMEs), research institutions as well as universities. These partners work on specific, directly funded SAGE 4 development tasks defined by MTU and its associates for a limited period of time.