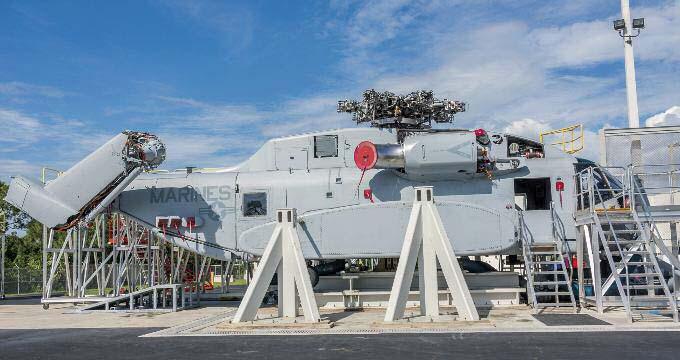
6 minute read
Chris van Buiten, Washington
Passion and the courage to innovate lead to remarkable results The future of rotary wing flight
by Chris Van Buiten, Vice President, Sikorsky Innovations, Stratford, USA
When you lead an organization whose charter is the aggressive and sustained attack on the toughest problems in vertical lift flight, you know your outlook will be long-term. We at Sikorsky Aircraft ask ourselves, what we can do today to ensure a portfolio of competitive rotorcraft products and services in 2020 and 2030.
Find skilled people, and let them innovate Several years ago, Sikorsky brought together a small group of deep thinkers and talented engineers under the banner of Sikorsky Innovations with the aim of being intensely collaborative and agile. These attitudes drove our desire to design, build and fly a small next-generation fly-by-wire co-axial helicopter to 250 knots flight speed from vision to reality in just 43 months. The program proved the efficiency of the X2 co-axial design for just $50 million.
S-97 RAIDER rapid prototyping Since 2010, Sikorsky Innovations has carried the same collaborative model, again within a rapid prototyping construct, into a second X2-based project. By the end of 2014, our 35 industry team members will have designed, fabricated, assembled and flown the first of two 11,000-pound gross weight S-97 RAIDER™ light tactical helicopters. Currently in final assembly at Sikorsky’s West Palm Beach, Fla., facility, the aircraft will demonstrate the game-changing capabilities of an armed scout helicopter capable of carrying six troops and external weapons. The combination of counter-rotating main rotors and a push propeller will give RAIDER helicopters a full range of extraordinary agility and maneuverability with 3G turns at high speed, and hover capability at 10,000 feet in hot temperatures where most helicopters cannot operate.
Cooperative R&D with Government In Poland, Sikorsky-owned PZL Mielec leads a consortium of manufacturers that is collaborating with the Polish Government to invest in innovative new manufacturing technologies. The goal is to design and build advanced composite and metallic aero structures in a multi-year research and development partnership that brings together industry and universities.
Manufacturing technologies in Poland Among the manufacturing technologies supported by Sikorsky is Additive Manufacturing, a technique that progressively adds
Chris Van Buiten is the Vice President of Sikorsky Innovations at Sikorsky Aircraft, where he runs the group for maturing next-generation technologies, including X2 technology™, active rotor and autonomy, as well as defining next-generation products. He was a Glenn L. Martin Aerospace Scholar at the University of Maryland, where he received a Bachelor of Science in Aerospace in 1989. He received a Master of Science in System Design and Management from the Massachusetts Institute of Technology and Sloan School of Business in 1999. In 1989 Chris Van Buiten joined Sikorsky, where he has served as Chief of Preliminary Design and Manager of Advanced Design and has led Sikorsky’s Strategic Planning Group. Photo: private
metal or plastic to produce parts. A second technique, called Friction Stir Welding, combines frictional heat and pressure to join two metal surfaces. Yet another process seeks to develop simplified structures by eliminating fasteners, such as rivets and adhesives.
Developments in the United States We are developing a third X2-based rotorcraft in the medium weight class for the US Army’s Joint Multi-Role (JMR) Technology Demonstrator program. JMR seeks to evaluate next-generation technologies for a Future Vertical Lift helicopter that will replace BLACK HAWK and Apache helicopters by the mid2030s. In October 2013, we and our partner Boeing signed a six-year investment agreement with the Aviation and Missile Research, Development and Engineering Center. The SikorskyBoeing JMR team will make a significant investment to design, build, fly and test a technology demonstrator aircraft for its flight in 2017.
Autonomous and adaptive Speed is just one pillar of innovation for Sikorsky. We are also working to make aircraft more autonomous, and more aware and adaptive to their operational environment. What if a helicopter could transition between dual-pilot, single pilot and unmanned flight modes simply by turning a switch? Or if it could adapt the shape or speed of its rotor blades? We believe these features will appeal to operators looking for multi-mission versatility. Safety of flight is another pressing issue that we are addressing head on. In August 2013, Sikorsky Innovations unveiled a major research program — designated Matrix Technology™ —
48 Sikorsky prepares the CH-53K heavy lift helicopter program’s Ground Test Vehicle at West Palm Beach, Florida, for “light-off” in December 2013 when the GE engines and rotor blades are turned for the first time. photo: Sikorsky
to develop, test and field systems and software that will improve significantly the capability, reliability and safety of flight for autonomous, optionally piloted, and piloted VTOL aircraft. Developing on-board system intelligence and multilevel contingency management is the key to success. The Matrix aims to improve the unmanned rotorcraft loss rate, from one aircraft per 1,000 flight hours today, to one per 100,000 flight hours. Only with this order-of-magnitude improvement in flight safety and reliability will operators allow their large helicopters to perform complex autonomous missions with minimal human oversight and at low altitudes where obstacles abound. For its autonomy initiative, Sikorsky Innovations has acquired and outfitted both an S-76® and a BLACK HAWK helicopter with fly-by-wire controls and MATRIX autonomy technology to act as flying labs. These aircraft will test new applications almost daily.
CH-53K helicopter The courage and passion to innovate resides across Sikorsky, not just within a small band of specialists. That is especially true with the CH-53K heavy lift helicopter programme where Sikorsky has introduced a suite of new technologies and tools that is changing the way we design and build helicopters. The 88,000-pound (4t) gross weight “K” model will enable the US Marine Corps to carry 27,000 pounds (12,2 t) over 110 nautical miles under “high hot” ambient conditions. This more than doubles the external load carrying capacity of the current CH-53E SUPER STALLION™ helicopter. Three years before assembling the first prototype “K” helicopter, we began building the aircraft in a 3D virtual reality lab. This VR lab allowed Sikorsky engineers to “get inside” an animated view of the airframe to determine whether the aircraft would be as simple to put together, and then maintain in the field, as designed. This approach saved months of rework, and delivered cost savings in the tens of millions of dollars.
Fleet analytics Our fleet analytics initiative is aimed at reducing the operating cost of helicopters while improving availability, safety and operational tempo. A data center collects and analyses the maintenance, operations and health data downloaded from every helicopter across a fleet, every day. Over time trends and patterns become visible. Sikorsky Aerospace Services has matured fleet analytics since monitoring the first S-92 helicopter in 2006. Today, more than 200 S-92 aircraft have accumulated 600,000 flight hours. It’s a goldmine of data that lets us predict material requirements, and recommend cost savings and maintenance reductions — ensuring that every S-92 helicopter benefits from the experience of the entire fleet. After benchmarking the S-92 program, the US Marine Corps recently established an analytics center for the H-53E helicopter fleet. The intent is to migrate the capability to the CH-53K platform when the first squadron becomes operational in 2019.
Human powered flight Though not a Sikorsky accomplishment, we can take partial credit for a feat of human engineering that occurred in July. AeroVelo, Toronto, was the only team able to meet the technical requirements set by the American Helicopter Society in 1980, to design and build a helicopter that could rise three meters, and hover over a 10-meter-by-10-meter box for one minute using only human-generated power. The Atlas team flew for 65 sec., reached a height of 3.3 meters, and stayed within the 10-meter box to win the $250,000 Sikorsky prize. www.vtol.org/aerovelo
Ninety years strong At 90 years young, Sikorsky Aircraft has spent the last 74 years designing, building and supporting the world’s best performing, safest and most reliable helicopter products. Our company founder Igor Sikorsky proved that if you have the courage and passion to innovate, you can achieve remarkable results. His first flight of the VS-300 helicopter in 1939 launched the rotorcraft industry that sustains us still. Three generations later, we continue to redefine what is possible in vertical flight.