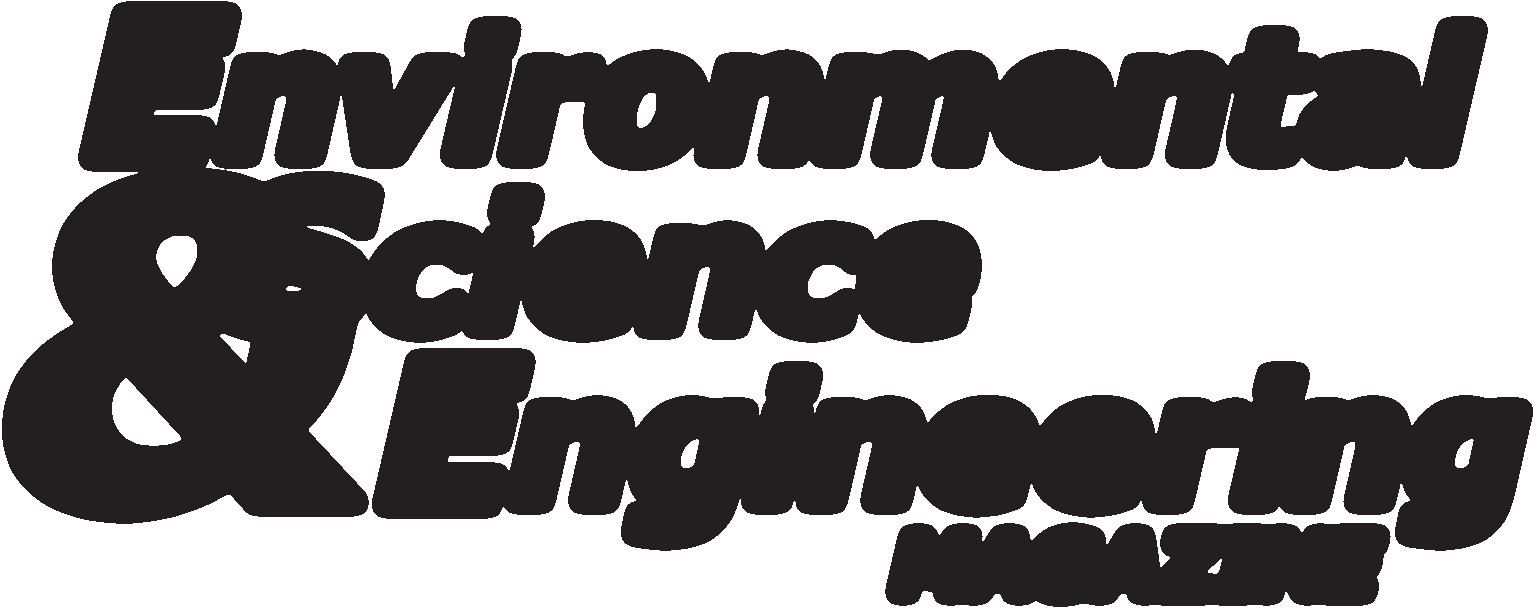
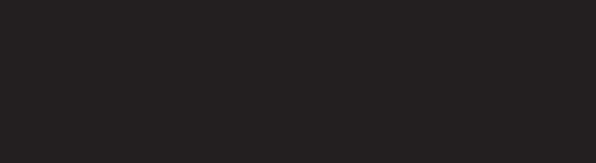
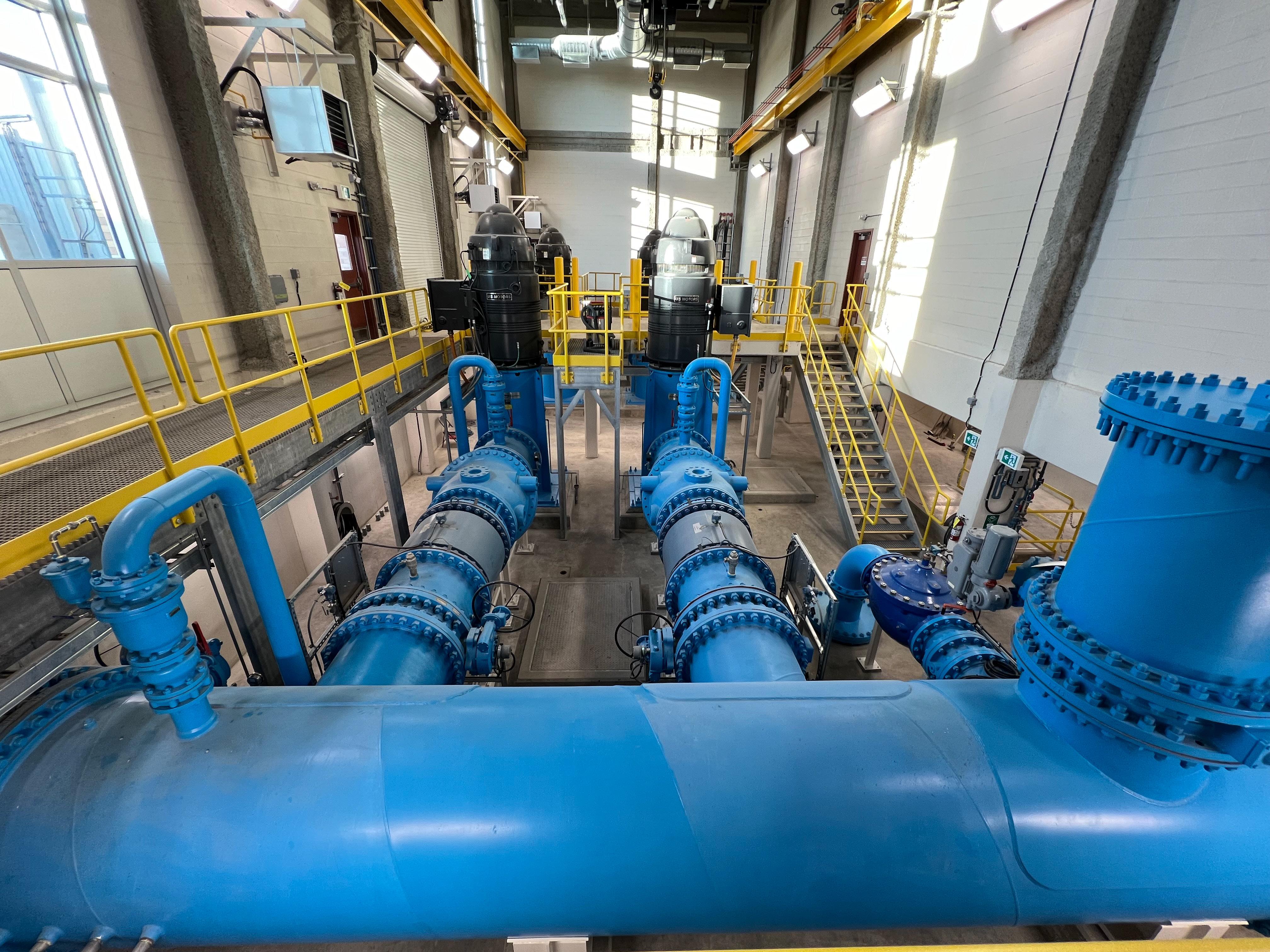


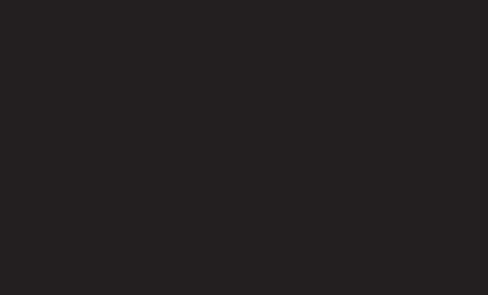
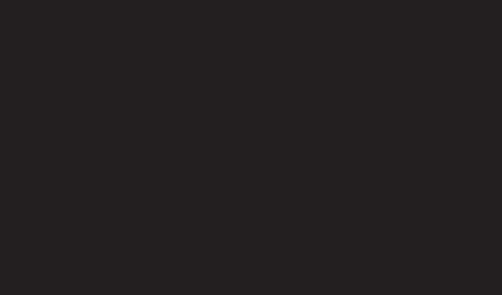
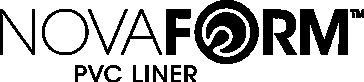
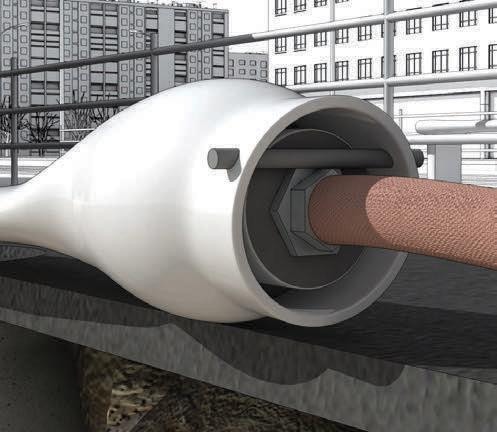
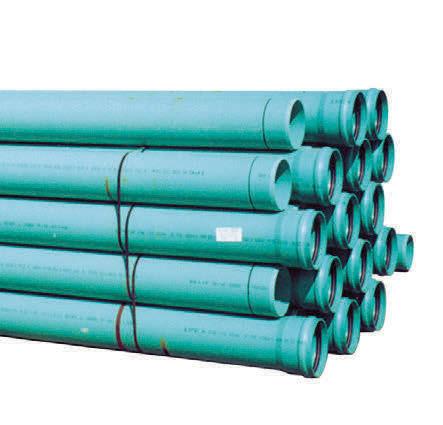
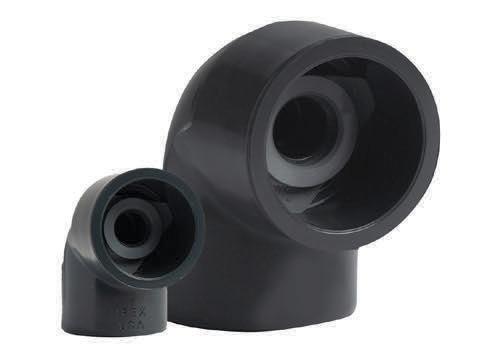
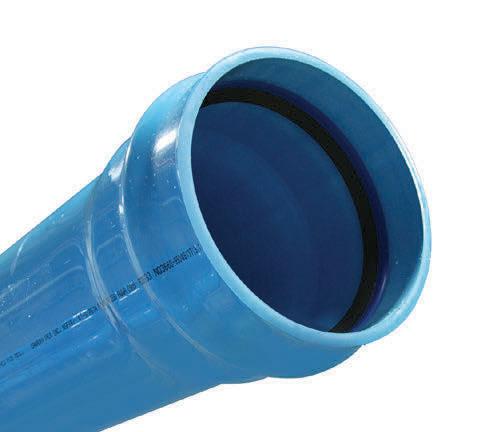
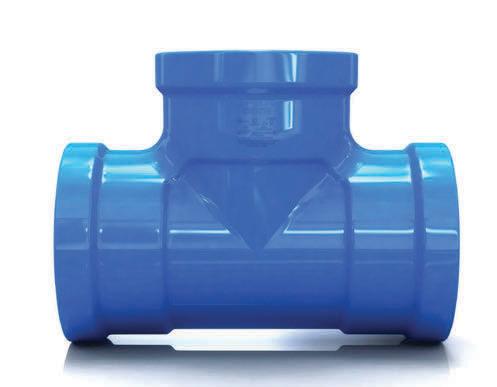
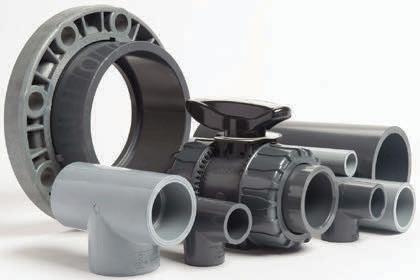
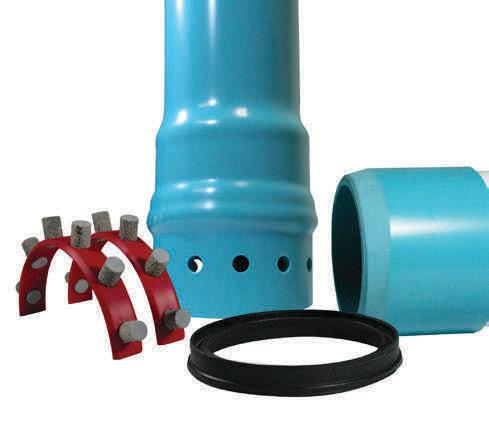
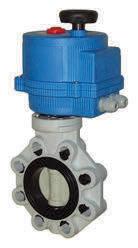
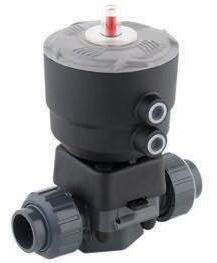
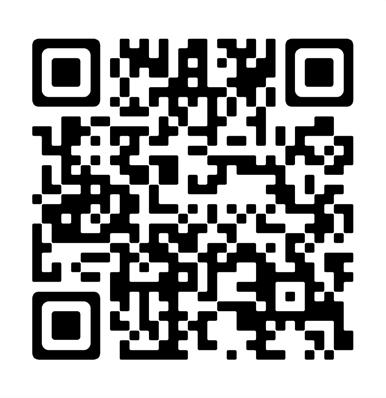

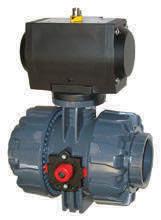


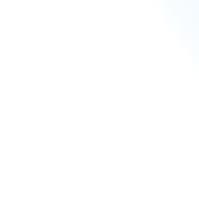

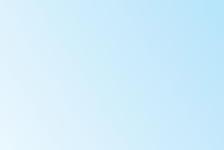
With over two decades of installed experience at more than 100 facilities worldwide, Nereda® technology is the One and Only true aerobic granular sludge on the market today.
Since its introduction to the U.S. and Canada in 2017, more than 40 AquaNereda® plants are currently in design, under construction or in operation throughout North America.
Consultants and end-users continue to realize the process and cost saving benefits associated with AquaNereda technology through on-site pilot testing, installation visits and technical seminars.
ADVANTAGES OF AQUANEREDA ® TRUE AGS TECHNOLOGY:
• Design MLSS of 8,000 mg/l greatly reduces footprint
• Capable of enhanced nutrient removal
• Suitable for retrofits and greenfield sites
• Exceptional effluent without chemical addition
• Robust process that adapts to changing conditions
• Applicable for municipal and industrial waste streams
• Significantly less construction cost compared to conventional treatment
• Energy and chemical savings results in lowest cost of ownership
Represented by:
www.acg-envirocan.ca sales@acg-envirocan.ca
Editor and Publisher STEVE DAVEY steve@esemag.com
Managing Editor PETER DAVEY peter@esemag.com
Contributing Editor DAVID NESSETH david@esemag.com
Sales Director PENNY DAVEY penny@esemag.com
Sales Representative DENISE SIMPSON denise@esemag.com
Accounting SANDRA DAVEY sandra@esemag.com
Design & Production MIGUEL AGAWIN miguel@esemag.com
Circulation BRIAN GILLETT ese@mysubscription.ca
Archis Ambulkar, Toledo Technology Academy of Engineering
Gary Burrows, City of London
Patrick Coleman, Stantec
Bill De Angelis, Metrolinx
Mohammed Elenany, Urban Systems
William Fernandes, City of Toronto
Marie Meunier, John Meunier Inc., Québec
Tony Petrucci, Black & Veatch
Environmental Science & Engineering is a bi‑monthly business publication of Environmental Science & Engineering Publications Inc. An all Canadian publication, ES&E provides authoritative editorial coverage of Canada’s municipal and industrial environmental control systems and drinking water treatment and distribution.
Readers include consulting engineers, industrial plant managers and engineers, key municipal, provincial and federal environmental officials, water and wastewater plant operators and contractors.
Information contained in ES&E has been compiled from sources believed to be correct. ES&E cannot be responsible for the accuracy of articles or other editorial matter. Articles in this magazine are intended to provide information rather than give legal or other professional advice.
Canadian Publications Mail Sales Second Class Mail
Product Agreement No. 40065446 Registration No. 7750
Subscription Changes?
Please email reader subscription changes to ese@mysubscription.ca, or call 705-502-0024
Advertising
Penny Davey
Sales Director 416 807 3812 penny@esemag.com
6 What does a second Trump presidency mean for the environment and for Canada?
8 Transforming ammonia in wastewater into green hydrogen
10 Oakville ramps up stormwater fee engagement
12 North Battleford modernizes its water infrastructure
14 Screening out invasive fish to restore a large freshwater coastal wetland ecosystem
16 Improving the efficiency and sustainability of Saskatoon’s drinking water supply
18 Choosing the right secondary containment system
20 Calgary’s new Highfield stormwater management facility will protect the Bow River
42 Preparing for PFAS — The next chapter of water regulation in Canada
54 Trends and challenges developing for Canada's water and wastewater sectors
55 Determining the true financial cost of environmental liabilities
22 Mind the Gap! Transitioning from academia to consulting
26 Meaningful Indigenous community engagement delivers better project outcomes
30 Understanding the current PFAS landscape and how it might evolve
32 Preselection and prepurchase considerations for effective project delivery
36 Consider alternative risk vehicles as a means of building resilience
38 Excess soil management: The ground is shifting
47 WWTP streamlines dosing equipment for improved function
48 Operator-designed battery backup system creates sustainable wastewater management
50 WWTP achieves biological nutrient removal process visibility
51 Metro Vancouver uses sonar to inspect 50 tonnes of fatbergs
Denise Simpson Sales Representative 905 960 4064 denise@esemag.com
Environmental Science & Engineering
220 Industrial Pkwy. S., Unit 30 Aurora, Ontario L4G 3V6
Tel: (905)727 4666 www.esemag.com
60 A new sector-specific management system standard for Ontario wastewater systems
52 Combining electronics and hydraulics for robust water plant power failure safeguards
Are The Exclusive Suppliers
Pro Aqua, Inc. ca rr ies a co mpl ete range of market leading and innovative products. Let us show you
Providing treatment solutions for more than 30 years.
• Archimedes Screw Pumps
• Screens – Multi-Rake, Perf Plate, Drum, Travelling Band, Step, Climber, Vertical Pump Station Screens, Screenings Washer /Compactors
• Grit Separation, Washing & Dewatering
• Conveyors – Shafted & Shaftless Screw, Belt
• • Disinfection – UV, Ozone
• Tertiary Filters – Travelling Bridge, Disk, Membrane
• Sludge Thickening & Dewatering –Disk Thickener, Gravity Thickener, Filter Press, Screw Press, Centrifuge
• Blowers – Rotary Screw, Rotary Lobe, Single Stage and Multistage Centrifugal, Turbo, Integrally Geared, Advance Control, Rebuilds
• Aeration – Surface, Membrane & Ceramic, Fine & Coarse Bubble, Gas & Liquid Cleaning, DO Control, AlphaMeter
• Mixers – Anoxic & Swing Zones, Sludge Holding, Digester; Mechanical, Hydraulic and Gas Bubble
• Tank Components –
Decanters, Swivel Joints, Telescoping Covers, Watertight Doors
• Primary & Secondary, Circular, Chain & Flight, Inclined Plate Settlers, Weir Washing
• Rotary Lobe Pumps & Grinders
• Anaerobic Digesters – Sludge Conditioning, In-line Screening, Degritting, Membrane Gas Holders, Liquid Mixing, Nutrient Recovery
• Sludge Drying – Belt, Fluid Bed and Solar
• Septage Receiving – Screens, Dump Stations, Truck Access & ID, data gathering & equipment control
• Sludge Treatment, Transport & Storage – Cake Pumps, Silos, Sliding Frames, Live Bottom Hoppers, Push Floors, Truck Loading, Alkaline Stabilization
• Odour Control – Tank Covers, Chemical & Biological Treatment, Activated Carbon
• – snoitatS pmuP & retawmrotS ,OSC
Tipping Buckets, Bending Weirs, Flushing Gates, Flow Regulating, Vortex Valves, Storm Screens
• Biological – SBR, MBR, RBC, MBBR, MABR, Oxidation Ditch, BioMag, CoMag Polymer – Liquid and Dry Systems
• Digester Gas – Gas Holders, Gas Conditioning: chilling; compressing; and removal of moisture, sulphur, carbon dioxide and siloxane, complete Co-Generation facilities
Like it or not, Canadians have to accept that Donald J. Trump will be the 47th President of the United States. So many long-standing political issues are now again in flux, including infrastructure, water, climate change, etc.
During his last presidency, the U.S. backed out of the Paris Agreement and will likely do so again. This has many very concerned, especially considering that this year and the last will be the hottest two years on record worldwide. This is according to Berkley Earth, an independent U.S. non-profit organization focused on environmental data science and analysis.
Shortly after the U.S. election, I participated in a webinar entitled “Impact of US Election on Canadian Climate Policy and Action”, organized by Profoundry (www.profoundry.ca), which gave me some hope.
Panelists included Catherine Abreu, International Climate Politics Hub; Tabatha Bull, Canadian Council for Indigenous Business; Phil De Luna, Deep Sky; Shawn McCarthy, Sussex Strategy Group; and former Toronto Mayor David Miller, who is now with the C40 Centre for City Climate Policy and Economy.
During the webinar, Miller noted that while the U.S. federal government is set to pause climate reduction plans, most of the world’s population lives in cities. He says that mayors have long been at the forefront of climate action, delivering innovative policies at the local level and that this momentum is not likely to change.
According to C40’s website, “the role US cities have historically played in bringing the world together to accelerate climate action will not end. C40 mayors in the United States and elsewhere remain focused on achieving the commitments of the Paris Agreement and ensuring continued progress towards reducing emissions, improving resilience, and preventing climate breakdown.”
Other panelists noted that the green economy strategies embraced by many other nations continue to advance. As such, corporations in America that export will still need to meet these requirements regardless of domestic policy.
With COP29 taking place during my writing of this piece, I learned that China might have reached peak CO2 output last year. While this is encouraging news, it's not definitive. China is outpacing other countries by installing new solar and wind capacity, cutting its emissions growth. However, to meet increased power demand, it is also commissioning new coal-fueled power plants. Balancing these factors is complicated, but it is still looking positive.
Turning to water issues, President-elect Trump has named Lee Zeldin as administrator of the Environmental
Protection Agency (EPA). According to The Hill, an online news service, “Zeldin would be expected to look to roll back regulations on the environment as part of the Trump administration, something the president signaled in his statement. He will ensure fair and swift deregulatory decisions that will be enacted in a way to unleash the power of American businesses, while at the same time maintaining the highest environmental standards….”
According to an article by the Bloomberg Industry group, a number of EPA clean water and drinking water regulations stand to be re-evaluated in the second Trump administration, with wetlands and PFAS among the most likely to get a closer look.
Alan Roberson, executive director of the Association of State Drinking Water Administrators, said he believes the Biden administration’s new Lead and Copper Rule Improvements regulation, which was finalized recently and mandates all lead drinking water pipes to be removed by 2027, and the PFAS drinking water regulations, to be vulnerable in the second Trump administration.
While watching highlights from one of Presidentelect Trump’s many election rallies, his comments on increasing the import of Canadian water concerned me. “Canada has a massive faucet that would take only one day to turn on, and all of that water would come right down here and right into Los Angeles,” he said.
This is not a new idea, but one that has been refuted many times. According to Canadian author and activist Maude Barlow in a recent Toronto Star article, “there have been many plans to commercially export our water to the U.S. Canadians successfully opposed a number of commercial water export schemes, including the GRAND Canal that would have diverted water from James Bay, and the NAWAPA, that would have dammed rivers in northern British Columbia for diversion to the southern U.S. Public outcry also stopped two proposed massive water export plans in the late 1990s, one from Lake Superior, the other from a glacier lake in Newfoundland, both bound by tanker for Asia.”
Barlow goes on to say that the North American Free Trade Agreement’s successor, the Canada-United StatesMexico Agreement (CUSMA), reasserted Canada’s control over much of its water.
Of concern now is Trump’s stated intention to re-open CUSMA and use tariffs to influence the policies of other countries, including Canada. This means that protecting our water resources will once again be a key issue.
Steve Davey is the editor and publisher of ES&E Magazine. Email: steve@esemag.com
By Parisa Chegounian and Lillian Zaremba
Ammonia is a byproduct of wastewater treatment that can be transformed into hydrogen, which is a powerful source of clean energy. When produced using renewable energy, hydrogen can help achieve carbon neutrality goals by serving as a fuel for vehicles, an energy source for industrial processes, and as a means for generating electricity and heat. This positions it as a flexible option in the transition to a low-carbon economy.
Metro Vancouver’s goal is to become a carbon neutral region by 2050. Recovering low-carbon energy and resources from wastewater in the region can contribute to this goal. With population growth, wastewater treatment facilities are experiencing higher ammonia levels that must be reduced to meet regulatory requirements. This challenge presents a unique opportunity to address effluent quality, while also creating low-carbon energy, by recovering ammonia from wastewater and converting it to hydrogen.
Traditionally viewed as a challenge in wastewater treatment, ammonia is undergoing a transformation in perception. Its discharge needs to be controlled, since it can be toxic to aquatic life when present at high levels. The challenge increases with population growth, as rising ammonia loads require additional treatment to ensure that final effluent complies with regulatory requirements.
Ammonia in final effluent originates from the influent stream entering the facility, and ammonia produced within the facility can be attributed to the breakdown of organic matter, particularly during the digestion of sludge in the solid stream.
Dewatering of digested solids generates a centrate stream that is rich in ammonia. Centrate is typically returned to the facility’s liquid stream, contribut-
ing to the overall ammonia load.
Traditional approaches for managing ammonia focus on removing it from wastewater through biological processes. These methods involve large footprints, significant capital investment, and high energy use that can result in increased greenhouse gas emissions.
In addition, if these systems are not operated optimally, microbial activity can cause the formation of nitrous oxide, a potent greenhouse gas with a global warming potential 265 times that of carbon dioxide.
A paradigm shift from viewing ammonia as a pollutant to be removed, to viewing it as a resource to be recovered, transforms this challenge to an opportunity and opens new pathways for sustainability. This approach protects aquatic life, while also generating low-carbon fuel.
Metro Vancouver recently engaged GHD to complete a feasibility study to evaluate the production of green hydrogen from wastewater byproducts, including ammonia. The study showed promising results for the business case compared to ammonia removal by biological treatment. However, the technology readiness level of ammonia-to-hydrogen systems is still low, highlighting the need for pilot testing.
Integrating hydrogen production with wastewater treatment leverages existing infrastructure and waste byproducts to effectively protect the environment, while pursuing new avenues for cost recovery and revenue generation. To validate the potential of this integration, it is important to demonstrate that
hydrogen production using innovative technologies can be scaled up successfully for larger projects.
Additionally, the cost of hydrogen production in wastewater treatment facilities must be competitive with other hydrogen production methods. To be considered are both capital costs and operational expenses, along with revenue from hydrogen sales and carbon credits.
GHD Project Manager, AJ McCoy, notes that “it is only worthwhile to produce hydrogen at wastewater facilities, if there is a nearby market for it.”
McCoy adds that hydrogen can be integrated into existing energy systems, such as blending with natural gas, fueling light-duty passenger vehicles or heavy-duty transportation, or being sold to other industries seeking sustainable energy solutions.
Metro Vancouver envisions that the green hydrogen produced at wastewater facilities could potentially be used within its own fleet vehicles, or in contracted heavy-duty trucking. This circular econ-
Green hydrogen production from ammonia at a wastewater treatment facility.
omy approach extends beyond hydrogen production to embrace the entire cycle of resource recovery, hydrogen generation, and hydrogen utilization.
Metro Vancouver is planning to pilot test ammonia-to-hydrogen technology, possibly at the Annacis Island Wastewater Treatment Plant, and re-evaluate the
business case. If this pilot succeeds, it will represent a promising advancement in wastewater management.
Parisa Chegounian and Lillian Zaremba are with Metro Vancouver. For more information, email: parisa.chegounian@metrovancouver.org
Up to 55% energy saving potential in the biological wastewater treatment process
Minimising CO2 footprint by 65% to achieve your common climate goals
Optimizing blower technology mix for a sustainable aeration process
about efficiency and sustainability www.aerzen.com/canada
By ES&E Staff
The Town of Oakville, Ontario, recently launched a survey and hosted a series of public meetings to determine the feasibility of introducing a stormwater fee.
The town’s Rainwater Management Plan estimates it will cost upwards of $732 million to care for and improve the stormwater system over the next 30 years. Oakville currently collects an average of $12.6 million each year for stormwater management from property taxes.
Oakville manages 30,000 catch basins, 70 stormwater management ponds, 240 km of ditches, and 690 km of stormwater pipes. As critical infrastructure reaches its end of life quicker due to extreme rainstorms and more severe temperature changes, local officials say they are looking for a fair and sustainable way to fund the challenge to reduce the type of substantial flooding that damaged local docks and flooded residents’ basements in mid-July.
Currently, property owners pay a portion of their property
tax based on how much their home is worth, not how much their property impacts the stormwater system. Residential taxpayers fund more than 70% of the $24 million to run the system each year, despite contributing less than half of the runoff water flowing into the stormwater system, according to a Town council presentation.
Although local officials are also exploring a flat tax and tiered option, the concept of a variable stormwater fee means that in addition to property size, homeowners with greater areas of hard surface that create more runoff would also pay a greater share of the cost to manage stormwater.
A system of credits could also be explored, local officials said, allowing for stormwater fee reduction for landowners who implement on-site stormwater management practices.
Oakville officials point to neighbouring cities in Ontario, such as Waterloo, Guelph, Mississauga, Markham and Richmond Hill, where residents have already transitioned to a stormwater fee.
Keeping the stormwater system running smoothly includes street sweeping, as well as replacing old sewers, catch basins and culverts. It also involves cleaning swales and ponds, as well as monitoring or fixing erosion along creeks and the lakeshore.
For more information, email: editor@esemag.com
WE HAVE AN EASY
INSTALL A SWM SHIELD TO PRE-TREAT YOUR POND
By Alex McGregor
Aging water infrastructure is consistently ranked among the most pressing issues facing the water sector. Municipalities all over the world are considering the rehabilitation or replacement of aged utility systems, and the City of North Battleford, Saskatchewan, is no exception.
The city faced issues with aging infrastructure, water loss and inefficiency that affected both operational costs and customer satisfaction. Officials made the forward-thinking decision to upgrade their utility’s water system by installing advanced metering infrastructure (AMI) to address these challenges and modernize their operations.
“We needed to modernize our technology for the 21st century. At one point, we tried to estimate our water losses,
and our old metering system was so inaccurate that our calculations showed that we were charging for more water than what we were producing at the plants,” said Stewart Schafer, director of operations at the City of North Battleford. “Transitioning to AMI allowed us to generate timely and accurate meter readings to serve our customers more efficiently.”
This shift not only modernized the city’s infrastructure, but also laid the groundwork for a more proactive and efficient system that benefits both the municipality and its residents.
North Battleford leveraged the realtime data delivered by Xylem’s smart water meters and the Sensus FlexNet® communication network to improve
their operational efficiency. The system provides the communications backbone to transmit data seamlessly between the utility and its meters. This upgrade allowed the city to implement proactive leak detection through continuous consumption alerts to immediately notify their customers.
Jeff Blanchard, assistant director of operations for the city, provided two examples of how customers immediately benefited from North Battleford’s upgraded utility network.
In the first example, a local store installed new low-flow fixtures to reduce water usage, but a faulty sensor caused one of the fixtures to leak 1.7 cubic metres of water per hour. The new AMI water meters quickly detected the excessive water usage and allowed the customer to correct the problem, before it resulted in a substantial water bill.
In another case, an elderly homeowner was unaware a flapper valve had not sealed properly in the downstairs toilet. This caused an unnecessary and continuous water flow. Upon notification, the homeowner took action to stop the leak. She appreciated the quick detection, which saved her from an increased water bill.
“We’ve achieved remarkable results through proactive leak notifications. We can now alert our customers of leaks in 24 hours that would have previously gone for months,” said Blanchard.
Both instances highlight how the city’s proactive approach to consumption monitoring and customer notification saved the customers money and helped conserve valuable resources.
“You don’t think about water until it is a problem,” said Schafer. “This advanced technology shows us and the citizens of North Battleford how they are using their water and how the new communication network can proactively inform them of a small leak, before it becomes a bigger problem.”
North Battleford’s smart utility network includes the ally® residential water meter, which enables staff to remotely turn on, or off, water services or reduce flow to minimize lost revenue. This is helpful with the high turnover of sea-
sonal tenants in rental properties. Landlords can now be proactively notified of potential water issues, and the automatic shutoff can save them from high water bills at vacant properties.
For property owners, this feature is also an invaluable tool. It provides peace of mind and financial security, especially for those managing multiple rental units or who leave town for extended periods of time during the winter.
Utility operations became more efficient with the ally® residential water meter in remotely managed services. This efficiency freed up time for staff, allowing them to focus on other important tasks, while reducing costs related to manual curb stops. The city’s waterworks staff reduced the number of manual curbside shutoffs, or reconnects.
Since implementation, the city’s cost savings are approximately $125,000 in staff time, reduced fleet maintenance and fuel costs. These savings not only improve the city’s bottom line, but also contribute to sustainability efforts,
The new smart utility network enables staff to remotely turn on, or off, water services or reduce flow to minimize lost revenue.
reducing environmental impact with a smaller carbon footprint.
“As an operations professional, I see the main benefit for us is the system’s instant feedback and how granular we can get with the data,” said Blanchard. “This detailed information has allowed us to decrease accounting errors and
quickly identify customers with continuous consumption. The precision of the data is invaluable, and it enables us to address issues in a matter of hours, rather than days or weeks.”
The city’s water is affordable at a rate of $1.60 per cubic metre and combined water/sewer rate at $3.20. However, costs can add up quickly with potential leaks and North Battleford’s system can provide near-instant alerts to identify spikes in usage or continuous water flow.
“It saves a lot of money in running the system,” added Blanchard. “The biggest benefit from an operational standpoint is getting the information as quickly as possible. Being able to respond with speed and accuracy has transformed our day-to-day operations.”
Alex McGregor is with KTI Limited/ Sensus Canada. For more information, email: kim.genardo@xylem.com
By Paige Kowal
Along-term study has recently been done on a common carp exclusion project on Delta Marsh, a large freshwater coastal wetland located in south-central Manitoba. Most fish species, including common carp (Cyprinus carpio), overwinter in Lake Manitoba and migrate each spring to feed and spawn in the marsh.
Exclusion structures with removable screens were installed on connecting channels between the lake and marsh and were deemed the best management option to exclude common carp from the marsh. Using a combination of delayed exclusion screen placement and 70-mm screen openings, Ducks Unlimited Canada (DUC) reduced the number of large common carp present in the marsh with minimal impacts on the native fish population. Suggested changes were also made to the timing of screen placement, in order to increase common carp exclusion.
Common carp is a freshwater invasive fish species found in North America and around the world that can negatively contribute to the deterioration of aquatic habitat. Their destructive feeding and spawning behaviours can decrease water clarity and damage submersed aquatic vegetation. Submersed aquatic vegetation is an especially important food for fall migrating waterfowl, which is of particular interest to conservation organizations like Ducks Unlimited Canada and its focus on issues affecting wetlands, waterfowl and other wildlife.
Exclusion structures are a frequently used management option for limiting common carp access to vulnerable aquatic habitats. While habitat improvements after common carp exclusion had been reported, little was known about impacts of exclusion structure operation
Exclusion structures with removable screens were installed on connecting channels between the lake and marsh to exclude common carp.
on native fish populations.
In a long-term project launched in 2012 with many collaborators and stakeholders, DUC researchers limited access of large common carp to Delta Marsh, with the goal of restoring its historical habitat conditions as well as its ability to support large numbers of migrating waterfowl in the fall.
Delta Marsh was selected as the project’s focus, because it is a large freshwater coastal marsh of great ecological and cultural significance. The presence of invasive common carp, among other factors, degraded the marsh and its ability to support migrating waterfowl. Delta Marsh is approximately 18,000 ha in size, making this carp exclusion project the largest of its kind in North America.
The project included the construction
of dikes and carp exclusion structures at seven locations at the marsh, where channels connect the wetland to Lake Manitoba. The carp exclusion structures were installed in the winter of 2012-2013 and a habitat and fish community monitoring program took place until 2018.
Common carp typically migrate a few weeks later than native fish species, such as northern pike.
Each spring, bar exclusion screens are deployed to prevent migrating large carp from entering Delta Marsh from adjoining Lake Manitoba. Narrow openings between the steel bars of the exclusion screens prevent large common carp from entering the marsh. Dikes built adjacent to the exclusion structures keep the invasive species from sneaking around the structures when water
levels peak. The screens are removed mid-summer when the spawning season is over. Since 2019, the Province of Manitoba has managed operation of the structures.
This important, long-term study was an opportunity to evaluate if carp exclusion structures could be used to restore a massive freshwater coastal marsh and improve conditions that support migrating waterfowl. There was also a need to evaluate if a balance could be reached excluding large carp, while having no impact on native fish populations. In the case of Delta Marsh, the answer was a resounding yes! The return of healthy aquatic habitat resulted in:
• An increase in diving and dabbling ducks, with a 339% increase in diving duck density and a nearly 400% increase in dabbling duck density between the pre(i.e., 2000s) and post-exclusion periods.
• Improved water clarity, largely driven by a reduction of inorganic suspended solids.
• Submersed aquatic vegetation doubled in percentage cover through the six years of monitoring post-carp exclusion.
• Diving duck abundance was associated with increasing submersed aquatic vegetation cover.
Results found that, in Manitoba, the optimal bar spacing in carp exclusion screen bars is 7 cm apart. Spring deploy-
ment of the screens should occur when channel water temperatures exceed 9°C and continued warm air temperatures and southerly winds are forecast.
Information from this study can be used by habitat managers around the world to help inform carp exclusion efforts. This study addressed a knowledge gap by evaluating optimal screen bar spacing size and timing of spring deployment.
Enhance efficiency and reduce downtime with Boerger Rotary Lobe Pumps and Macerating Technology.
+ Space-Saving Solutions
+ For Sludge, Biosolids, Grease, Sewage, Scum, Slurries, Polymers, etc
+ Maintenance In Place (MIP®)
Paige Kowal is a research biologist with the Institute for Wetland and Waterfowl Research, Ducks Unlimited Canada. For more information, visit: www.ducks.ca
By Scott Miller and Eric Gaudet
Since 1906, the City of Saskatoon, Saskatchewan, provided residents and businesses with drinking water from its Avenue H Water Treatment Plant. This facility is a conventional surface water treatment plant, drawing water from the South Saskatchewan River and providing coagulation, filtration, and disinfection treatment, before distributing potable drinking water to the city and the surrounding area.
Since its construction, the plant has undergone numerous upgrades and expansions. In 2015, the city and Associated Engineering (AE) completed design and construction of the Avenue H Reservoir, ultraviolet disinfection, and high lift pump station. The project involved a temporary solution for transferring filtered water from the existing filter clearwells to the new facility, including modifications to the former high lift pumps.
The city recognized that a sustainable long-term transfer pumping plan was required for improved operational reliability and energy efficiency. Major electrical upgrades were needed at the plant to replace an aging 4160V/600V system and improve redundancy. In 2017, the city engaged AE as the prime consultant to deliver preliminary studies and long-term plans. This included conceptual, preliminary, and detailed design, construction, administration, resident engineering, and commissioning services for the project.
The project includes design and construction of a new 450 million litres per day capacity transfer pumping station and electrical system upgrades with a new medium voltage electrical room, a low voltage electrical room, and two new 2-megawatt generators to match the existing generators at the plant. These generators are designed as a “pooled” system, working interchangeably to provide back-up power.
Several piping tie-ins were required to connect the plant’s existing filter clearwells with an underground piping network to convey water by gravity to each of the new transfer pumping forebays. From the transfer pumping station, two 1,200mm steel pressurized pipelines supply the existing Avenue H high lift pump station.
Structural design included a 10-metre-deep pump station substructure complete with two isolated pump wells to allow for fully redundant operation. The facility superstructure includes the new electrical rooms, generator and pump room, and rooftop mechanical and electrical equipment.
Due to the complexities of tying in to the existing water treatment plant facilities, the electrical and pumping systems were designed to allow closed system commissioning through a detailed functional testing plan, while avoiding impact to the existing water treatment plant operation.
AE followed current guidelines and recommendations from the Hydraulic Institute with optimal pump selection, where the pumps’ best efficiency points correspond closely with the most frequent flow rate analyzed from historic data.
Several construction challenges were encountered when building the new facility within the confines of the existing plant site, including demolition, replacement, and tie-ins to existing infrastructure. Working in a century-old facility, there are many unknowns. Abandoned, below-ground structures and pipelines, and contaminated soils from an early 1900s electrical power plant were uncovered.
The new transfer pumping station is designed for energy efficiency and long-term sustainability. It follows current guidelines and recommendations from the Hydraulic Institute with optimal pump selection, where the pumps’ best efficiency points correspond closely with the most frequent flow rate analyzed from historic data. This new system has resulted in significant and noticeable energy cost reduction and reliability for the city.
Climate change adaptation was considered in the design of the HVAC systems, including free cooling for the low voltage electrical room with allowances for higher air flows, if required, for increased cooling days in the future. As well, the mechanical cooling system for the medium voltage electrical room was designed for projected increases in temperature and cooling demands. As of writing, this project was nearing completion.
Scott Miller and Eric Gaudet are with Associated Engineering. Email: millers@ae.ca, or gaudete@ae.ca
Flood control protects the vibrant New Orleans community from rising waters. At the world’s largest drainage pumping station along the Gulf Intracoastal Waterway (GIWW), 11 Pentair® pumps help NOLA play on.
By Marshall Lampson
Secondary containment is an important safeguard that helps plant operators mitigate the risks associated with chemical spills.
Systems typically consist of a primary container, which is surrounded by a secondary container or wall. Between the two is an interstitial space. If the primary container fails and a chemical leaks out of the primary tank, the secondary system prevents the chemical from spilling out beyond the unit.
Most chemicals used in water treatment pose risks of contamination, or harm to humans, in the event of a leak or spill. Chemicals such as sodium hypochlorite, citric acid, and sodium hydroxide are commonly used to clean and flush membrane filtration materials. Sodium hypochlorite is also commonly used to disinfect water. Often, hydrofluorosilic acid (fluoride) is added to municipal water supplies and it is extremely dangerous if not stored properly. To balance pH levels, sulphuric acid, or a base chemical such as sodium hydroxide, may be added to the water.
Chemical manufacturers and chemical supply facilities rely on secondary containment units to safely store the hazardous liquids they use. These facilities frequently store aggressively corrosive compounds, and they must take great precautions to ensure the proper safeguards are in place in the event of storage, spill or failure.
When mining companies leach copper from oxide ore, they often use concentrated sulphuric acid. This highly exothermic acid presents serious storage challenges, because it’s an extremely heavy chemical that will test the mechanical integrity of any tank system.
In the high-tech industry, chemicals vary from manufacturer to manufacturer—and in many cases they’re proprietary. Many of the solutions are high-purity or ultra-high-purity chem-
These tanks provide enclosed secondary containment to prevent damage to equipment or property, lost chemicals, and injury to employees in the event of a spill.
icals that are used for applications like circuit board manufacturing.
Manufacturers of de-icing fluids can use several harmful chemicals, including brine, magnesium chloride, propylene glycol, and ethylene glycol. Whichever chemical is used during the de-icing process, it is important to store it safely so that it is properly contained according to environmental regulations.
All secondary containment systems have their advantages and disadvantages. Whichever option you choose, it’s important to make the right choice for your operation’s needs. Selecting the wrong system can result in unplanned expenses, more maintenance, or more operational frustrations.
There are several components of a chemical storage system with secondary containment. You must consider costs of the primary tank, the secondary tank, any coating on the containment structure, maintenance costs, fittings and accessories, and the potential cost of purchasing new chemicals in the event of a spill.
While an open-top tank system is less expensive than concrete, you could expect a total loss of the chemical. As with concrete systems, the entire chem-
ical supply can become contaminated by rainwater or debris in the event of a chemical spill or leak.
A crosslinked polyethylene (XLPE) double wall tank system is a “tank-within-a-tank” that keeps contaminants from entering the interstitial area. These tanks provide enclosed secondary containment to prevent damage to equipment or property, lost chemicals, and injury to employees in the event of a spill.
In the event of one, the tank system’s all-in-one design features a protected containment area that safely isolates reactive chemicals, protects employees from harm, and protects organizations from environmental remediation costs, all within the footprint of a standard vertical tank.
If the primary tank develops a leak, the liquid is captured by the outer sealed secondary tank and the system essentially becomes a single-wall tank until it can be repaired. This allows continued use of the chemical within the primary tank until the tank system can be emptied, inspected, and repaired if necessary.
Poly Processing double wall XLPE SAFE-Tanks are suitable for almost all chemicals, including those that have dangerous exothermic reactions to water that could occur in a traditional containment that will capture rain or wash water.
The XLPE double wall tank system reduces the footprint of the containment system by taking up less space around the primary tank. Since it’s built from high-density cross-linked polyethylene that can hold the chemical, there is no need to designate a large area for a concrete containment structure. Only one tank pad is needed. Since any spills are self-contained, acids and bases can be stored next to each other.
Marshall Lampson is with Poly Processing. Email: mlampson@polyprocessing.com
• No Corrosion or Contamination
• No Chemical Absorption or Wicking
• No Tearing, Cracking or Peeling
• No Significant Abrasion
Each Vanton thermoplastic pump features wet-end components that are inert to corrosive chemicals across the full spectrum of pH, will not contaminate ultra-pure liquids, and are also abrasion resistant.
Handling flows to 1150 gpm (261 m3/h) heads to 185 ft. (56 m) and temperatures to 275o F (135o C), Vanton pumps are ideal for:
• Chemical Transfer
• Neutralization
• Dosing
• Effluent Control
• Lift Stations
• Odor Control
• Recirculation
• OEM Applications
By Cory Albers
The Bow River offers some of the best fishing in Alberta. It is key in supporting the province’s sport fishing community and the area downstream of Calgary’s downtown is abundant with brown trout, rainbow trout, and mountain whitefish.
As such, protecting the Bow River and conservation of its aquatic life is paramount and is one of the goals of the city’s stormwater management strategy. In 2018, Stantec was hired to complete the design, tendering, and construction of a stormwater management facility (SWMF) adjacent to a major storm outfall in the city’s southeast, which discharged untreated stormwater into the Bow River.
Stantec then hired Source2Source Inc. (S2S) to assist with the facility design, especially with the application of Nautilus Pond® technology.
The existing storm ducts discharging to the SWMF on the west side of the Bow River are twin 1500-mm span by 1650-mm rise box structures. This outfall drains a catchment area of approximately 1050 hectares, which consists of residential, commercial, and industrial use land.
The facility was designed as a Nautilus Pond system, comprised of an inlet structure, two stilling basins, two overflow berms, two biofiltration pockets, a large settling basin, and multiple precast concrete high flow structures. Erodible
areas of the Nautilus Pond are lined with articulated concrete matting.
The storm ducts direct untreated stormwater flows into the pond system’s first stilling basin. As flow fills the first basin and ultimately overflows into the second stilling basin and through the flow dispersion blocks, flow velocity slows, and settlement of fine solids begins.
Once the second stilling pond fills, it will overflow into the large settling basin, via a second set of flow dispersion blocks. In the settling basin, flows will further reduce to a velocity where all statutory sediment removal objectives for the SWMF are achieved.
Once the settling pond is filled with
storm flows, settled water can exit the system through the high-capacity precast concrete outlet box structures. As the basins are filled, the biofiltration pockets also fill.
These pockets reduce the bio nutrient load for nutrients, like nitrogen and phosphorus, that otherwise would be discharged into the Bow River. This helps create a healthy riparian habitat along the river.
The custom shallow cover precast concrete outlet structures from the Nautilus Pond were designed by S2S and Stantec and manufactured by Precon. Each structure includes manhole access and is designed for CL800 loading, to enable unrestricted movement of fully loaded hydrovac trucks.
There are three individual structures that make up an outlet. Each one is a box structure, with custom openings for the inlet and outlet. Inlets at the downstream of the settling basin have galvanized steel grating covering the openings.
Grating acts as a solids strainer for any debris that has floated through the Nautilus Pond system. Structurally, the precast and grating is designed to support the weight of track or skid-steer loaders, so they can drive over it in order to clean off debris.
The downstream side of the outlet structure is covered with a pipe trash rack, made from galvanized steel. This closes up the structures to ensure the safety of any person, or wildlife, that may be walking in the area.
These precast concrete outlet structures were designed with
flat joints, where a compression butyl rubber gasket strip seals the joint. The box sections are held together with a proprietary compression pocket, which provides a tight seal with no gaps between the precast concrete sections.
Cory Albers is with Source2Source Inc. For more information, visit: www.source2source.ca
SCANTO WATCHIT INACTION
By Pat Coleman
Agap exists between academia and consulting. Where there is a gap, there are challenges. The industry knew of the gap over 50 years ago. For example, the gap inspired W.J. King to write three articles in 1944 for Mechanical Engineering Magazine on “The Unwritten Laws of Engineering”. His articles struck a chord because the American Society of Mechanical Engineers still publish his articles as a book.
Researchers documented the disappointment, or delight, of new hires when they discover what engineering is. For example, two studies found a deep level of disappointment among some students they followed into employment because they could not use their knowledge and capacities in their job (Stiwne and Jungert 2010; Baytiyeh and Naja 2012). Others regretted becoming engineers because it was not what they thought it was. Perhaps engineering is something that until you do it, you do not know what it is.
James Trevelyan defines engineering as a collaborative enterprise based on specialized technical expertise distributed among participants, accessed through a network of trusting relationships shaped by workplace social norms (Trevelyan 2019).
The cause of regret or excitement among students is not the technical expertise part of the definition, but the parts about “collaboration”, “participants”, “trusting relationships”, and “workplace social norms”. Successful employees can communicate and collaborate within workplace norms. For this reason, the correlation between
Who is the client?
Whose name is on your work?
What happens to your work when it is done?
Why are you here?
You are. Professors are paid to teach you, assess you and read your stuff.
Yours and other members of your group.
You either bin it or put it into a box once the course is done.
To obtain knowledge and a qualification.
Differences between student and employee environments.
academic performance and success at work is weak, because coursework does not assess these skills.
Universities do not graduate engineers. Knowledge is what we know, competence is knowledge successfully put into action multiple times, and performance is competence demonstrated.
Once demonstrated, students can obtain a licence and can call themselves engineers. A university’s role is to teach students to think via technical coursework. Knowledge has a shelf life and that must be expanded upon throughout an engineer’s career. Therefore, the first step, of gaining knowledge occurs at the university, while the second two steps are accomplished once the student obtains an engineering job.
Table 1 lists four differences between student and employee environments. The crux of the change is the shift from “it is about me” to “it is about us”. A new employee needs to remember that clients hire their employer, they do not hire them.
Everyone else is. You are being paid to be a team member and serve the client.
Your employer’s logo and the supervising engineer you work under.
Your employer retains the documents and the responsibility for their contents long after the project is finished.
To become a competent engineer and a valued employee.
Different researchers list skills that fall into one of three themes: the ability to build a network, manage negative relationships, and balance self-awareness with assertiveness and confidence.
A new employee faces a steep learning curve. The work they will be asked to do and the people they will work with are unfamiliar. If the employee can build relationships with colleagues that they have nothing in common with apart from work projects, they will be successful. These networks become conduits for work, knowledge and support.
The employee may encounter negative relationships. Individuals may be competitive rather than collaborative, hoard work, or be apathetic or indifferent. They may mistake being busy for being productive and run their life using Outlook Calendar.
Employees need to speak up when they encounter gender or cultural roadblocks. Roadblocks snarl productivity and hurt staff. The employer needs to clear the jam. continued overleaf…
Up to 50% reduction in mechanical room space required 90% fewer joints = 90% less risk of leakage Simple, consolidated operation AFTER simple. intuitive.
Once the employee receives work, they must learn to balance their awareness of their inexperience with their team’s expectation that they will be confident and assertive. The employee may find themself intimidated by age and experience, not know how to formulate a question, and not know who to ask what. As such, the network of relationships a new employee builds needs to include mentors and allies who can help.
The employer hired the employee because they were the best candidate. Consequently, they want the employee to succeed. However, the employee must come to work with the professional skills to adapt and build relationships. Those skills make the employee “employable”.
“Managers seek young professionals who possess non-technical skills, especially communication skills and the ability to work across ‘borders’ both disciplinary
and organizational.” (Brunhaver et al 2018). A new candidate should exhibit four classes of skills: general, technical, affective, and cognitive (Ahn et al 2012).
If a student is offered an interview, the employer probably decided that the student possesses the first two sets of skills:
• General: you can express ideas, are aware of the community you live in, aware of environmental and economic challenges.
• Technical: you possess technical skills, practical awareness, computer skills and can manage your work.
The other two skills will be rated higher in the interview because the employer must decide if they can graft the student onto their project teams. They will never hire a talented individual who upsets their employees. For this reason, they will focus on the student’s affective and cognitive skills:
• Affective: leadership, teamwork, collaboration skills, stress management, recovery from failure.
• Cognitive: critical thinker, adaptable, interdisciplinary thinking, growth mindset, aware of safe practice.
The only way an employer can assess a potential hire is on their experience. The student should be prepared to answer “this I know, this is what I do or what I have done, and this is one positive impact.”
Employers hire people, not degrees.
Consulting is a business, and like most businesses it thrives on satisfied repeat customers. Read up on the business. Remember that employers sustain themselves by winning work, doing the work, and managing the work. The staff do this together with clients and other interested parties.
Remember that small actions send huge messages. Skakoon and King advise that, “However menial and trivial your early assignments appear, give them your best effort.” Similarly, cleaning up after yourself, thanking those who
Associate Vice President, Water Resources
Enhancing our water resources management and infrastructure development expertise.
To find out more visit: rvanderson.com
ERIS would like to express our profound gratitude to our clients and partners across the country for their tremendous support on our 25 years in business. Yes, ERIS has served the due diligence market in Canada with environmental and property risk data and products since October 1999!
As we look forward, we will continue to provide leading-edge products and imaginative software solutions to serve our clients for their North American due diligence work.
www.ERISInfo.com
help you, showing respect to all, asking a person’s name and then remembering it, and arriving on time confirm to those who watch you that you belong.
Bring a notebook and a pen and be seen by your colleagues making notes. Note taking sends the message that you value people’s time. Check your spelling in emails and documents. A spelling mistake can be interpreted as a sign you do not care about your work.
Be professional. Learn to read a room, put your phone away, and when feeling distracted, practice the Pomodoro time management technique. When given a task, ask how long it should take, what you are expected to provide, and can they provide an example or a name of person who has done the task before. Don’t spin. Ask for help or for a name of someone who can help you. If you are low on work, seek more.
In the first 90 days, your employer
will assess if you fit in and if you are who you said you were. In the first two years, you want to demonstrate that you fit comfortably within the competency range of your grade. After four years, you want your employer to know you can work independently and with others, that you can supervise other staff, and that you know when you are over your head and need help. Be aware of cognitive traps and logical fallacies. Be creative and check details.
Stiwne and Jungert 2020 followed four cohorts after they completed their degree and became employed. They noted that the first cohorts placed more emphasis on their own efforts and capacity to meet the programme’s goals, while the later cohorts placed the emphasis on what the programme offered them and what options they have.
The two researchers concluded, “Our
results also suggest that we pose the question: Is it the mission of an engineering programme to make students employable, or is it the responsibility of students to become employable?”
Students are responsible for becoming employable. The university can prepare them to swim across the gap and employers can support them while they do so. But, no one can do it for them. When they come up for air on the other side, they will discover what engineering is (Roman 2019): “Engineering is more than being mathematically proficient and technologically creative. Ultimately, it is about people doing great things in service to other people and society — something no mathematical expression can quite capture.”
Pat Coleman, PhD, P.Eng., Principal Process Engineer, Wastewater, with Stantec. Email: pat.coleman@stantec.com. References available upon request.
By Jeremiah Pariag
When planning, designing and building critical infrastructure systems in Canada, it is important for proponents to engage with the public, stakeholders and Indigenous communities that may be impacted. Though many agencies have an established public and stakeholder outreach process, traditional engagement strategies don’t always adequately identify the needs or address the concerns of Indigenous communities.
Indigenous concerns often differ from those encountered in other public outreach. Unlike typical public concerns such as community character and construction disruptions, Indigenous concerns are often rooted in culture and history, such as the protection of traditional lands and treaty rights.
To effectively engage Indigenous communities, a more intentional and customized outreach strategy is necessary. In Canada, the level of engagement with them often begins with standard requirements set by relevant agencies; however, proponents and their consultant teams need to be prepared to develop engagement protocols that are customized based on their organization, their specific projects and the Indigenous communities they are engaging.
There is now a direct link between project viability and Indigenous participation on projects in Canada. This has been the case in some infrastructure sectors, such as mining and energy, for quite some time. More recently, participation programs have become more established on transit projects.
In Canada, the government requires public agencies and private developers to consult with Indigenous communities who might be adversely impacted by, or have an interest in, an infrastructure or development project. Impacts could include the disruption of fishing, hunting, and harvesting activities, or disturbances to cultural and archaeological resources. While unconditional consent is usually not required, the preference of the government is for agencies and private proponents to meaningfully engage these communities.
Public awareness and opinion are evolving as well, adding pressure to engage with rights-holders in a meaningful way. Media coverage has become more attentive to Indigenous communities, largely due to inequities and the ongoing mainstream discourse related to atrocities at residential schools in Canada.
As a result, project proponents are recognizing they must be
more proactive in their engagement efforts prior to proceeding with infrastructure development to establish early, broad community support and avoid costly delays.
Before a project begins, it is important to identify the general geographic area of the planned infrastructure and determine which Indigenous communities might be impacted or interested. There are usually governmental resources that can help. Reach out and meet with leaders and representatives from each of those communities to develop personal relationships and better understand their key challenges and priorities.
A strong relationship with an Indigenous community cannot be built overnight. Relationships are built on a foundation of trust and require patience, honesty, and genuine respect. Building this trust starts at the earliest stage of project development. It requires ongoing engagement and a deep commitment to understanding and respecting Indigenous knowledge and practices.
Taking shortcuts when it comes to engaging with Indigenous communities does more harm than good. If mistakes are made along the way, relationships and trust can be ruined, significant reputational harm might occur, and projects could be put at risk. It is always better to put in the time that it truly takes to deliver engagement well.
1.8 billion people lack access to clean water
2.5 billion people—more than a third of the world’s population —lack access to a toilet
Women and children spend 200 million hours a day collecting water
Hygienic practices such as washing hands with soap can reduce the risk of diarrhea by at least 35%
More than 3.4 million people each year die from water related diseases—that’s nearly the population of LA
Nearly 90% of global cases of diarrhea are estimated to be attributable to unsafe drinking water, inadequate sanitation and poor hygiene
is
We’re taking big steps to solve the world’s water crisis—permanently. We want complete water coverage for every family, every school, and every clinic. And we’re teaming up with Everyone to make this difference last Forever.
Water For People brings together local entrepreneurs, civil society, governments, and communities to establish creative, collaborative solutions that allow people to build and maintain their own reliable and safe water systems. We’re not just addressing the symptoms of the problem, but preventing it from happening again in the future.
The road to permanent water coverage for Everyone Forever is challenging. If we invest more now to create sustainable and replicable water and sanitation infrastructure, we can achieve incredible outcomes—more children are in school, more individuals are employed, more families are healthy and thriving, and more communities are collaborating and growing. From there, the impact continues to ripple out on a national and global scale.
Indigenous communities are not homogenous. Each has its own preferences for engagement, as well as its own distinct priorities. Engaging communities begins with a willingness to listen and learn. On a single project, one community might have ecological concerns, another about language preservation, while another is troubled with water quality or economic funding of their community. It is important to understand how each community could be impacted, as well as each community’s unique concerns and how a project can work within the scope of their needs.
Early engagement with Indigenous communities does require an initial financial investment; however, this investment can enhance project outcomes, improve public opinion, and build genuine relationships by demonstrating a commitment to collaboration and equitable outcomes.
It can aid in understanding the needs and concerns of each community early in the process, making it easier for proponents to adjust or make necessary design or construction phasing changes to mitigate potential impacts and prevent schedule delays or work stoppages. Clear, consistent communication
channels and the inclusion of community members in the decision-making processes have proven effective on many infrastructure projects. This inclusion fosters a sense of mutual ownership and respect, which is vital for successful project delivery.
In recent years, there has been an increasing trend of non-Indigenous individuals and groups misappropriating Indigenous voices to serve their own project outcomes, often sidelining genuine Indigenous perspectives. Such actions can distort the representation of Indigenous views, leading to project decisions that do not align with the true interests of their communities.
However, when proponents engage proactively and dedicate time to building meaningful, trust-based relationships with Indigenous communities, they benefit from receiving authentic insights and information directly from them. This direct engagement not only helps prevent the intentional misappropriation of Indigenous voices by non-Indigenous groups but also significantly mitigates the risk of proponents unintentionally misrepresenting or misunderstanding Indigenous perspectives
Selecting the right partners is crucial for any project, especially when working
directly with Indigenous communities. It is vital to be aware of the history and track record of potential partners in terms of their experience and success with Indigenous communities. Many consulting and communications firms, unfortunately, do not have a strong track record of effective collaboration with Indigenous communities, and partnering with such firms can jeopardize project delivery and the trust-building process.
One practical strategy for proponents is to actively involve Indigenous communities in the selection of partners. Before finalizing any decisions about bringing on a partner consulting firm, reach out to the communities affected by the project and ask for their feedback on their past experiences with the potential partner.
If the feedback is positive, it is likely a suitable partner. If the feedback is negative, it may be prudent to consider other options. This approach helps proponents make an informed choice and take a first step toward demonstrating respect and a commitment to genuine collaboration with the communities involved.
To ensure that trust extends beyond the current project, it is crucial to document and honour any commitments made to Indigenous communities. Con-
Associated Engineering is pleased to introduce two new managers in our Ontario Buildings Services & Energy team, led by Division Manager, Tom Hummel, MBA, P.Eng., CEM: Roy Gong, M.Eng., P.Eng., Manager, Building Structural. A Structural Engineer, Roy has 13 years of experience designing water and wastewater facilities, specializing in water retaining structures and buildings.
Azad Khamforoush, M.Sc., P.Eng., Manager, Energy & Mechanical. Azad is a Mechanical Engineer and Project Manager with over 18 years of experience specializing in building mechanical systems with a focus on energy efficiency. Congratulations, Roy and Azad!
tinued engagement with a community after project completion provides longterm benefits and facilitates mutual learning, strengthening the relationship for future initiatives.
Moreover, both Indigenous engagement practitioners and proponents must recognize that the outcomes of current projects, both positive and negative, will influence future engagements. Approaching each project as one part of a long-term relationship with Indigenous communities positions all parties for continued success.
When building longer term relationships, it is also important for proponents to be aware of any changes to the governance structure of Indigenous communities. A new chief and council are elected every few years. Meeting with and developing relationships with these new community leaders, even past the planning phase, can help keep project needs aligned with potential changes that come with their priorities and preferences.
The prominent role of Indigenous communities is only increasing, and the transition from being a consulted community to a project proponent has already begun. In several industries in Canada, these communities are now becoming equity owners on major projects. In fact, on some energy projects, Indigenous ownership is becoming a determining factor for the project’s overall success, and this could be the case with future road, transit and rail projects. Representatives from Indigenous communities could also take a governance or oversight role on project committees. Technical advisory committees and community advisory committees have been a core element of infrastructure projects for years. As reconciliation becomes a reality for many agencies, governance roles such as Indigenous advisory committees are on the horizon. It is not widespread yet, but this has already started in Canada in many unofficial capacities, especially on projects where there are significant environmental or archaeological concerns.
It is essential to acknowledge that the impact of infrastructure projects reaches far beyond the construction and completion phases. While the immediate focus may be on the primary infrastructure, the ripple effects are often much larger. For example, transit projects frequently lead to the development of additional infrastructure, including new housing, expanded water services, improved power transmission networks and new roadways. All of which have their own impacts.
As a result, Indigenous communities are increasingly focused not only on ensuring that infrastructure projects respect their way of life and culture, but that these developments additionally provide tangible, long-lasting benefits for their community members as well.
Collaboration with Indigenous communities is no longer just a best practice
in infrastructure development in Canada. It is a crucial element of project success. This collaboration helps to build trust, foster long-term relationships and create opportunities for shared prosperity. Ultimately, the success of many infrastructure projects in Canada now hinges on the depth and quality of this collaboration.
As the landscape of development in Canada evolves, so too must the approach to engagement, ensuring Indigenous voices are not only heard but actively shaping the future of infrastructure in the country.
Jeremiah Pariag is HDR’s Indigenous Engagement Practice Lead. Email: jeremiah.pariag@hdrinc.com
By Stefano Marconetto
Per- and polyfluoroalkyl substances (PFAS) have become a growing issue in the scientific community, as we work to develop solutions to replace, manage and remediate these “forever chemicals” in a way that reduces their harmful impact on human and environmental health.
In Canada, actions taken by the federal government are starting to yield some positive results, and have provided lessons that industry and other levels of government can build upon to address this difficult issue.
The research community has been attempting to better understand the impacts of PFAS exposure on both humans and the environment. Health Canada and Environment and Climate Change Canada, as part of their Updated Draft State of Per- and Polyfluoroalkyl Substances (PFAS) Report released in July 2024, shed some light on what’s been learned so far.
The report says that some well-studied PFAS have been demonstrated to be readily absorbed into the body and are eliminated very slowly. Consequently, some PFAS can accumulate and persist in the body for years. Exposure to PFAS can affect multiple organs and systems. The main targets include the liver, immune system, kidney, reproduction, development, endocrine disruption (thyroid), nervous system, and metabolism (lipids, glucose homeostasis, body weight). Effects on most of these endpoints have been observed in both animal and human studies.
It goes on to say that since humans are
typically exposed to mixtures of PFAS, it is reasonable to expect that cumulative effects may occur. However, the specific hazards associated with these mixtures are largely unknown.
If further negative impacts on the health of either humans or animals are identified, it would likely speed up the adoption of stringent policies related to the use, containment and remediation of PFAS chemicals.
Until now, the majority of policy and regulatory work done related to PFAS in Canada has been initiated by the federal government. As the entity responsible for regulating the manufacturing, import and use of substances across the country, it undertook the first actions to regulate PFAS-containing products.
These federal actions began with limiting or prohibiting the use of a few specific PFAS that could be readily replaced in products. This approach represented a first step that limited the shock to the economy and supply chain while further scientific evidence was gathered.
Canada stepped up the game recently by signaling its intention to regulate PFAS as a class by issuing a draft risk management scope, requiring companies to report on their PFAS manufacturing, import and use, and consulting on the inclusion of several PFAS in the National Pollutant Release Inventory.
For contaminated sites, the primary focus to date in Canada has mainly been on firefighting foams, which are a significant PFAS source. Since many of the key sites impacted by these foams are under federal government control (military bases and airports), targeting them as a source provided a good starting point to determine how best to investigate and address concentrations of these chemicals without significantly affecting multiple market sectors or requiring unprecedented investment.
However, the most challenging chapter starts now. With the intention of the federal government to regulate PFAS as a class, industry can no longer respond to a regulated limit on one specific PFAS by using another non-regulated PFAS.
The challenge is on to look beyond PFAS for substances that will achieve the same desirable or essential properties in consumer products. These include the ability to repel water, grease and stains, while maintaining durability, temperature resistance, and more. These products range from rain jackets, for which we may have a higher tolerance for compromise in water resistance, to specialty medical devices or healthcare equipment in which PFAS replacement and alternatives development will have higher stakes.
Furthermore, with globally connected supply chains, a ban or restriction on PFAS content in products will require coordination with other countries to maximize benefits and avoid negative effects on business operations and investments in our country.
While federal PFAS limits will apply to the manufacturing, import and use of substances in Canada, as well as environmental cleanup targets at sites under federal jurisdiction, it will be up to provinces to establish limits for PFAS for environmental media such as drinking water, wastewater and contaminated sites. So far, some provinces have issued or adopted certain PFAS limits, but most are lagging behind the federal regulations.
Without question, there is an expectation that more provincial regulations are coming, at least for drinking water, wastewater and contaminated sites. The federal government recently updated its PFAS Drinking Water Objective, and the provinces will need to decide if or when to adopt it.
In terms of environmental protection and contaminated sites, there are several potential sources of PFAS contam-
ination beyond firefighting foams. Furthermore, PFAS-containing firefighting foams have been widely used beyond federally regulated sites, including at the municipal level (e.g., fire stations) and in the industrial private sector.
PFAS mitigation projects are complex due to the numerous environmental media that may be implicated, including drinking water, surface water, groundwater, soil, sediment, air, wastewater, stormwater, solid waste, and biosolids.
Critically, the burden to address PFAS in response to potential new provincial regulations for these media will primarily be on municipalities and corporations. It will require significant operational changes and investments, different than for any other type of contaminants we have seen before. The impact that any provincial regulations would have on municipalities and corporations will directly affect taxpayers and the economy as a whole.
Considering the magnitude of investments and changes required, it is critical to prioritize PFAS regulatory actions and management approaches that can achieve the most benefit and are supported by a solid cost-benefit analysis. Canadian data are being compiled with existing information from other jurisdictions on the magnitude of PFAS use and potential environmental releases. These, combined with potential for exposure, can inform prioritization.
Lessons from the United States teach us to avoid new environmental standards that may be below the concentrations that we can reliably measure in a laboratory or below PFAS concentrations in rainwater. Such standards would result in a magnitude of sites requiring action that would be financially overwhelming and unattainable to the point of causing paralysis.
In addition, the more uniform the approach we implement to regulate and address PFAS across Canada, the better it will be for our connected economy. In this regard, we could take some lessons from Australia, where the federal government and states have joined forces
to develop a standardized management plan to deal with PFAS-contaminated sites and waste across the country.
Along with prioritization of regulatory and management actions, supporting the development and implementation of PFAS destructive remedial technologies that fully break the PFAS cycle could help Canada become a leading player in the sustainable fight against PFAS. There are promising signs that point in this direction.
Being able to address PFAS challenges is going to demand expertise from within the current environmental engineering and science industry, but also from future leaders of the sector. Ensuring that the next generation is armed with the skills to address PFAS and has the right mindset will be crucial.
We need the next generation to bring forward an innovative mindset, with a desire to put a stop to the PFAS cycle (demand for certain products/practices).
That’s going to mean creating capabilities related to product chemistry (innovation and safe product substitution), supply chain management, and optimization of destructive treatment technologies as opposed to concentration/separation technologies that may move the problem elsewhere.
The writing is on the wall. Future policies at all levels of government will cause us to invest in the substitution and destruction of PFAS. With this in mind, we need to support companies to safely re-engineer their products, work with governments and industry to prioritize actions to sustainably address PFAS contamination, and prepare our next generation for the immense amount of challenging and innovative work that lies ahead.
Stefano Marconetto is a Senior Principal Environmental Engineer and the Emerging Contaminants Practice Lead for WSP in Canada. Email: stefano.marconetto@wsp.com
By Tyler Yang
Equipment procurement has traditionally been conducted by the contractor, with a focus on cost to encourage competition and innovation in an open market. Nonetheless, alternative procurement approaches are frequently employed by owners for additional control over time and quality. Equipment preselection and prepurchase are procurement processes that provide many benefits for capital projects. Planning of the process is paramount to its success, as well as risk identification and mitigation of potential failures. Details can often be overlooked, which can be all the difference between an exemplary project and an unremarkable one.
Selection of the appropriate procurement approach is one of the first and most important steps when considering alternative equipment procurement. As a consultant, it is vital to review the advantages, disadvantages, and anticipated outcome with the owner and determine how well each approach aligns with the objectives of the project. Particularly for private owners or small municipalities, the resources to administer and manage the additional procurement may not be available. In other words, the “do nothing” approach should also be evaluated. Literature is widely available on the common alternative procurement approach and the driving factors to employ them. As general guidance within the typical design-bid-build projects, cost driven projects should consider tradi-
tional procurement, and time- and quality-driven projects should consider prepurchase and preselection, respectively. However, it is important to emphasize that time and quality issues are often reflected in the life cycle cost of the project.
As such, provisions for adequately meeting cost, time, and quality constraints should not be neglected, and some of these are discussed further. Establishing the objectives and desired outcome early on could help reduce the risk of resource expenditure without generating significant value for the owner.
In general terms, the procurement documents for a preselection or prepurchase request-for-proposal (RFP) or request-for-quotation (RFQ) may include terms of the proposal (i.e., information to proponents), general conditions of the contract, details of the deliverables (scope of work and specifications), and additional supplements based on the contents of the aforementioned components. There are currently no industry standard documents and general conditions for alternative equipment procurement.
It is up to the owner to define the terms and conditions of the particular procurement contract. Incorporating detailed terms and conditions for the procurement contract could offer risk mitigation or protection to both owners and suppliers during the performance of the contract, or the failure thereof. Many owners have such standard documents, but those with limited experience in these contracts may rely on the design consultant to help develop them.
In addition to the requirements of the local purchasing bylaw or policy, several optional items can be reviewed based on the project needs.
A performance guarantee is a let-
ter signed by the supplier guaranteeing the equipment will meet the specified requirements. At the proposal evaluation stage, it may not be possible for the owner and consultant to review the expected performance of a manufacturer’s complex engineered systems. The performance guarantee assures that the supplier will provide a complete system which is fit for its intended use. For equipment with a measurable performance metric (e.g., pumps), a performance guarantee is likely not necessary.
Proposals could be evaluated against cost, technical, experience, and environment criteria, with each category further broken down into requirements that are specific, and ideally, quantifiable. The specifics of each criterion and assigned weights should be tailored for the owner’s needs. Consideration should be given to disclose the details of the evaluation method to the suppliers. At a minimum, it is recommended to provide high-level descriptions of the categories and criteria.
A clear outcome for the procurement should be envisioned at initiation. In both preselection and prepurchase, an equipment supply contract is a typical product of the RFP/RFQ. The owner may choose to manage the supply contract with their own forces or transfer (i.e., novate) the contract to the contractor responsible for construction.
If novation is the preferred approach, it is recommended to disclose the intent to novate, as well as the anticipated conditions of the construction contract (e.g., CCDC 2) within the RFP/RFQ for the equipment. This provides clarity for contract administration and mitigates the risk of non-compliance by the supplier during construction.
However, additional contractual requirements typically result in additional efforts to administer, and over-
head costs which are ultimately additional costs to the owner. The benefits and costs for each option should be reviewed with the owner when developing the procurement package.
In a traditional construction project, the contractor is held responsible for fulfilling the requirements of the contract, such as supply, installation, and commissioning of equipment. Therefore, management and coordination with the supplier, as well as occasional field engineering are required of the contractor. Where owners take on a portion of the equipment selection and purchase, they should include additional measures to facilitate successful installation.
Delineating responsibilities between owner, consultant, supplier, and contractor provides a means to manage scope and protect against claims, particularly if additional supplier design or field ser-
vices are required.
Supplier design services are typically required where supplied equipment needs to be integrated with the overall system (e.g., a treatment plant). The owner and design consultant may choose to include constraints on the supplier’s design, design around the supplier’s system, or a combination of the two.
The supplier may be required to review, modify, and otherwise coordinate the designs, which can be a significant effort for the supplier depending on the size of the project. It is recommended that this scope of work be clearly defined in the contract. A reasonable basis would be to align the coordination work with the design milestones. The owner should also consider the payment for this work separate to the actual supply of the equipment.
Supplier field services are standard inclusions in the supply and installation of equipment, regardless of procurement method. It is often advantageous
to carry out field services under the contractor’s scope of work, as it alleviates some liability from the owner and consultant for the proper installation of the equipment. However, it could create an opportunity for the selected supplier to adjust the price for the supply of the equipment through the contractor. Conversely, a firm price could be agreed upon on the basis that the contractor would not be involved in the supplier’s scope. Additional details in the scope of field services would therefore help promote fairness for both the owner and supplier.
Cost escalation arises from a number of factors, such as base material cost, outsourcing, and currency exchange rates. In a small timescale, cost escalation is manageable. However, the design period for large projects could span mulcontinued overleaf…
tiple years, which exacerbates this risk. A long price validity period transfers the risk of cost escalation to the supplier, but in response, the supplier could increase their price to offset this risk.
The contract could include provisions to share the risk of cost escalation by defining a method to justify cost increases based on external indices or factors. This increase can then be shared between the owner and supplier, based on the owner’s acceptable level of risk. It is important to keep in mind that methods used to determine the justifiable cost increases will not be completely accurate, and the owner should take this into consideration when reviewing risk sharing.
Schedule delays are a risk that could ultimately result in cost to the owner, if not managed properly. Delay in the manufacturing of the equipment will impact the contractor’s ability to per-
form their work. If the supplier was determined by the owner, delays resulting from equipment lead time may be grounds for claims against the owner.
To hold the supplier accountable, the owner may consider means to recover cost from them, such as through liquidated damages based on a guaranteed delivery time. On the other hand, delay in construction work could result in the equipment being delivered to the site, before the contractor is ready to install the equipment.
The owner may incur costs to provide storage for the equipment, but more importantly, prolonged storage of the equipment may give rise to quality issues due to deterioration of the equipment and uptake of the warranty period. Quality control issues can be mitigated by proper storage and preventive maintenance for the equipment, which can be provided by the supplier or manufacturer. Provisional scope for these services can be considered, and it is recom-
mended to include additional clarity for the conditions of storage, maintenance, delivery, and warranty.
Proper management of the preselection and prepurchase contract is required to reap the benefits of this process. For example, suppliers that are not accustomed to alternative equipment procurement may find challenges in meeting the schedule. This is especially detrimental to projects that need to coordinate timelines and milestones.
The consultant should take the initiative in coordinating the execution of the supply contract. Accordingly, consultants should consider reasonable professional fees for coordination and engineering services when developing budgets.
Tyler Yang, P.Eng., is a Water Project Engineer with R.V. Anderson Associates Limited. Email: yyang@rvanderson.com
April 29 – May 1, 2025
CANECT has been the leading event of its kind in Canada for over 30 years. Since 1992, CANECT has earned a reputation for excellence in meeting the information needs of environmental practitioners in industry, government and the associated legal and engineering communities.
We hope you will join us at CANECT25. Contact Denise Simpson, to learn about exhibiting and sponsorship opportunities.
905-727-4666 ext. 21 denise@esemag.com
CANECT conference delegates are a high-quality audience of decision makers responsible for environmental engineering, regulations and compliance issues. CANECT 2025 is designed to be a high-quality opportunity for you to promote your products and services and network with existing and potential clients.
By Shane McCarthy
There is increasing pressure on businesses today. Recent catastrophic weather events have led to the largest insurance claims the Canadian insurance world has ever seen.
In fact, estimates suggest that just four catastrophic weather events from summer 2024, including the Ontario and Quebec floods, the Calgary hailstorm, and the wildfire in Jasper, Alberta, have broken records for the largest claims. They brought the year-to-date total of claims to $7.7 billion, which is even larger than all of 2016. That year included costs for the wildfire in Fort McMurray, Alberta.
Predictions indicate that these kinds of costly weather events will only continue to increase. While property owners and operators are concerned, environmental scientists and engineers will need to take notice as well. Building resilience means taking steps to protect assets and make it easier for business and real estate owners to weather the storm, whether that storm is a flood, a wildfire or a tornado.
Engineers must do what they can, whether through modelling systems or carbon projections, to guide construction and rebuilding work in the proper direction. Owners will need to use every avenue they can find, adopting both risk mitigation strategies and alternative insurance vehicles, to prevent them from getting to a place where they won’t even have access to insurance.
In the wake of a major disaster, it’s no longer enough to rebuild the same structure on the same spot. Engineers and
property owners will have to build back smarter than ever before, with environmentally-conscious firms looking to decrease the environmental impact of the entire claims process.
This may mean considering several different strategies, including rebuilding with sustainable materials. The construction industry is a notorious user, and even abuser, of resources. Standards for sustainability clearly state that building materials should be natural and locally available, but they also could be recycled or refurbished to save on needing to manufacture a new product.
While three-quarters of construction and demolition waste has a real monetary value and could be reused or recycled, it all too often winds up in a landfill. Encouraging builders to make use of all sustainable options can help lessen the environmental impact of repair.
On the other hand, adopting risk mitigation improvements can help increase resilience in already-completed structures. Addressing specific risks can help to prevent problems before they occur again. Some of these could include backflow valves to protect against sewer backups, snow load meters to warn of rooftop weaknesses, fire-resistant building materials to slow down fire damage and impact-resistant glazing, or hurricane shutters to protect windows during a storm.
These strategies are popular because they demonstrate to a potential insurer that the structure is prepared for a catastrophic weather event and unlikely to suffer devastating damage. These are the kinds of structures that insurers prefer to cover.
At the same time, however, risk mitigation strategies can’t be the whole story. Risk transfer solutions, or insurance coverage, also plays an important role. Unfortunately, with climate change wreaking havoc in many regions, many
owners are struggling with an asset that is almost uninsurable.
Many buildings that are hit repeatedly by weather events won’t qualify for traditional coverage, but that doesn’t mean no coverage is available at all.
While alternative insurance vehicles are gaining traction, traditional insurance remains the first line of defense for most businesses. Standard property insurance policies provide critical coverage against a range of risks.
However, businesses in high-risk regions, especially those affected by repeated natural disasters like floods, wildfires, and hurricanes, are finding it increasingly difficult to secure affordable coverage. In such cases, traditional policies may impose high premiums, deductibles, or even deny coverage. This growing gap has made alternative insurance vehicles, such as parametric insurance, a crucial complement to traditional policies. Together, these options help businesses manage both expected and unforeseen risks in a changing climate landscape.
Parametric insurance is increasingly valuable for businesses facing frequent weather-related disasters. Unlike traditional policies, parametric insurance doesn’t rely on the assessment of physical damage. Instead, it triggers a payout based on a pre-defined event, such as a specific amount of rainfall, wind speeds, or temperature extremes.
This makes it especially useful for properties exposed to recurring environmental risks. For example, a commercial real estate firm in a flood-prone area might purchase a policy that triggers after a certain level of rainfall, providing quick financial relief without waiting for lengthy damage assessments.
Similarly, a construction firm could secure parametric insurance against project delays caused by extreme weather, while agricultural businesses
use it to protect against losses due to droughts or storms. By responding swiftly to measurable conditions, parametric insurance offers a predictable, customized risk management solution for those facing regular climate threats.
Because the coverage is based on a measurable event and not based on the amount of damage, the policies pay out quickly. This provides a necessary lifeline to help organizations bounce back quickly from an extreme weather event. What’s more, these policies are usually tailored specifically to the client, which means property owners determine their risk appetite and budget when defining terms.
Parametric insurance is sometimes considered a gamble, but for properties that are hit repeatedly by flooding, heat waves or other storms, this coverage may be the smoothest road to recovery and resilience.
Carbon credits are important for engineers and construction firms that are building green structures or other environmentally friendly businesses. These credits are often tied into funding, but when things go awry it may cause some to miss out on those funding sources.
Carbon credit insurance mitigates the risks associated with carbon credit projects, such as building a windfarm or reforesting an area of land.
In the past there was little to no confidence in the carbon credit program, but with insurance coverage to back it up, buyers can have greater confidence in their projects. Similarly, when catastrophic weather events have the ability to derail an entire project, insurance coverage offers a way for owners to recover more easily from a setback.
This coverage reduces financial uncertainty associated with carbon credits and even attracts new investors. It offers protection on many fronts, such as financial, reputational, regulatory
and climate exposures. Some qualifying events might include a reforested area that is hit by a wildfire or a regulatory change that means the project doesn’t have enough credits to qualify for funding. In each case, the policy would provide remuneration to help the business recover from the hit.
The insurance industry is continually innovating to adapt to the challenges posed by climate change. New products are being developed to address specific climate risks. For instance, insurers are offering specialized coverage for climate adaptation investments, such as flood barriers, firebreaks, and other structural improvements that reduce risk exposure.
Additionally, advancements in data analytics and artificial intelligence are allowing insurers to model and price climate risks with greater precision. This technology is helping property owners secure more accurate, data-driven policies that reflect their true risk profile, even in the face of a changing climate.
Partnering with an insurance broker who specializes in climate risk is crucial in navigating today’s complex insurance market. These experts can help businesses assess their risk exposures, identify the most appropriate combination of traditional and alternative insurance products, and even advise on implementing physical risk mitigation measures to reduce premiums.
Moreover, with the risk landscape changing rapidly due to climate impacts, regular policy reviews with a qualified broker ensure that coverage evolves to meet new threats. Working with a broker not only helps secure the right insurance coverage but also empowers business owners to take proactive steps toward resilience.
Shane McCarthy is Vice President and Environmental Practice Lead with HUB International’s Complex Risk Unit. Email: shane.mccarthy@hubinternational.com
By Jeff Goldman
Over the past five years, attitudes, practices and regulations regarding the management of excess soil from construction projects have shifted. This soil, which has historically been regarded as a costly and useless impediment to achieving the built form of the construction project, is slowly being appreciated for its potential benefits.
Moreover, accelerated consciousness about the environmental consequences of contaminated soils being improperly disposed when coupled with heightened aspirations to decrease the carbon emissions associated with the transport of soils have compelled industry stakeholders to find better solutions in this arena.
If all that were not enough, developers and project owners are finally awaking to the reality that they can significantly improve their bottom lines, along with regulatory compliance, by embracing new planning methods and technologies to achieve improved outcomes.
New provincial regulations have been implemented in Ontario, Quebec and British Columbia. Each have their differences, but there are commonalities that aspire to provide greater transparency and accountability for those involved in the excess soil chain of custody. This ensures that soil from a generating site is appropriately tested, characterized and subsequently taken to a licensed receiving site that is approved for accepting the particular soil being transported. These regulations also place emphasis on the maintenance and retention of accurate records that can verify what soil went to what place at what time. The result has been the decline of use of the tri-part paper ticket system that has been the industry standard for commercial transactions for generations. Unfortunately, this standard has been rife with abuse, inaccuracies and headaches for account reconciliation.
Management of excess soil from construction projects has enormous eco-
nomic and environmental impacts. Testing, excavation, transport and deposit of soils from construction activities costs billions of dollars per year in Canada. Transportation of these soils from generating to receiving sites via tri-axle diesel dump trucks (the preferred mode of transport), generates hundreds of thousands of metric tonnes of greenhouse gas emissions annually. The consequences from improperly disposed of soils pose considerable risk to human and environmental health.
Changes that have evolved in this industry are in their early stages. But, because this activity is so profound in scope and intrinsic to the construction paradigm, they have been notable. These changes can be largely grouped into categories of planning, execution and disposition. If an organization does not currently take advantage of these kinds of improvements, it is missing opportunities for improved bottom lines and enhanced outcomes.
With respect to planning, tenders and performance contracts, the assistance of expert legal counsel is better defining scope of performance, associated responsibilities and liabilities in earthworks activities. This also leads to better-informed bids and decreased tensions about excess soil cost-overruns and the assignment of blame.
It is becoming more common for those tasked with the management of excess soil to begin liaising with one another well before ground is broken to devise a comprehensive and efficient soil management plan.
In the execution sphere, recognition that specialized knowledge of soil management issues is essential to proper handling and risk reduction has occurred. In Ontario, the formation of QPCO (Qualified Persons Community of Ontario) was done to share enhanced knowledge among those specialists in this field (as opposed to generic engineers or other environmental consultants) and define best practices, and is an example of such recognition.
The creation and adoption of userfriendly digital technologies, such as SoilFLO® have revolutionized soil management logistics. These applications
provide such benefits as automated tracking and hauling records, superior management of inbound and outbound truck scheduling, budget tracking, record keeping and cost reconciliation.
These are of tremendous value to project managers, site supervisors, site owners and back-office accounting personnel. They also happen to assist stakeholders with regulatory compliance as a bonus. This is worlds apart from the manual management of soil disposition, accounting and record-keeping methods of the past. There are cost savings from the efficiencies being realized by users.
Regarding execution, the increased awareness that the best excess soil management plan is one that greatly reduces or eliminates off-site disposal of soil is gaining traction. Accordingly, more attention is being paid to creative use of soils within the project area, as well as beneficial reuse of excess soils in nearby or associated projects.
Creative and innovative technolo-
gies that adopt the mantra of reducing the volume of excess soils from generating sites by either in situ remediation, or recycling soils for a higher level of reuse are starting to abound. At this past September’s annual Excess Soil Symposium held in Toronto, more than 350 soil experts were informed by presentations and displays from companies such as GRT Environmental Services (Canada), CDE Group, and Menard Canada, that are providing such solutions.
On the disposition side, the soil provenance assured by good management, soil classification and tracking technologies allow for increased acceptance by receiving facilities of soils from a variety of source sites. The more that such provenance is assured, the more soils can be received.
Market economics dictate that as more sites accept soils that they are assured are proper, associated tipping fees will decrease over time. The more excess soil is designated for beneficial reuse, the
faster the benefits of such can be realized. This is circular economy thinking.
For receiving sites, the secret to opening their doors wide for construction soils is assurance that they get the soil they have been told they are getting and not an undesirable substitute.
Despite these advancements, the new era of excess soil management is still in its youth. Old ways and attitudes die hard in construction, where loyalty to traditional practices and stubborn resistance to adoption of technology remains. In addition, disposal costs for soils are an enormous expense in construction endeavours.
Whenever such large amounts of money are at play, the temptation to find unsavory solutions to cut costs, along with the engagement of parties willing to participate in such activities, may be found. The excess soil world is no stranger to this phenomenon, although this is not reflective of most practices. continued overleaf…
Looking forward, there is much to be done to improve how we regard and handle excess soil. To appreciate this activity’s scope and size, we need to be able to measure it. Despite its profound impact on the construction industry and environment, we have little data to assist in understanding this activity. Schools of civil engineering, urban planning, environmental studies, stakeholder industry associations and government agencies would be well-advised to dedicate financial resources to study this area so further improvements may be forthcoming. Regulatory improvements without meaningful compliance enforcement are not effective. In Ontario, a fairly wellcrafted provincial excess soil regulation is being ignored by too many, as the threat of incurring penalties has been in scarce evidence to date.
In Quebec, recent enforcement and court interventions in some high-profile cases of what appear to be egregious examples of harmful dumping practices have recently been launched. Unfortu-
nately, it appears that government initiative on this front only came after significant public outcry against the activities of the suspected perpetrators.
In the meantime, in the U.K., where they treat this matter seriously, a number of convicted offenders involved in the improper disposition of significantly contaminated soils have been sent to prison. We don’t want soil police, but the willingness of authorities to follow through with appropriate enforcement and prosecution when serious transgressions are in evidence, is needed as a wake-up call to others who may be inclined to skirt compliance.
It has been heartening to witness greater awareness in the risk management and project financing sector of their exposure associated with improper soil management. Companies such as Berkley Insurance Canada have recognized that this is a specialized area that requires attention and understanding in the insurance sector.
I was delighted to attend a gathering
earlier this year, organized by Stantec, on excess soil management that included insurance underwriters from a variety of large firms. The moment that project lenders and risk underwriters require those to whom they lend and insure to demonstrate compliance with good soil management practices as a condition of their participation is the moment the landscape in this arena will change dramatically for the better.
These banks and insurance companies, who seem to expend considerable energy expounding on their environmental, social, and corporate governance (ESG) commitments may do well to consider the excess soil compliance component of the billions of dollars they administer for construction projects in respect to such commitments.
In recent years, the construction industry has embarked on various endeavours to measure and reduce its environmental impact and promote sustainability. Programs such as LEED or Net Zero are examples of these goals. Yet, to my knowledge, no programs to incentivize and recognize good excess soil management practices exist.
A company can garner LEED “points” for installing bicycle racks at its new office tower or condominium. However, a soil management program, that significantly reduces dump truck traffic or redirects thousands of cubic metres of soils to construct a public amenity gets nothing.
Probably the most formidable hurdle in improving excess soil management practices comes from attitudes and perceptions of those in the industry. Regarding excess soil as a resource rather than a waste is suspected, by some, as part of a new-age “woke” agenda. After all, it is just dirt. Right?
At the risk of pontificating, I say to my colleagues in the industry that everything we do should have at least a modicum of regard for its environmental consequence. If not, our eventual survival will be more imperiled than it is already. Remember, good excess soil management planning, plus the use of technologies, equals cost savings.
Jeff Goldman is with SoilFLO Inc. Email: jeff.goldman@soilflo.com
APRIL 29 – MAY 1, 2025
CANECTʼs practical professional development courses are designed to help you meet your environmental compliance and regulatory responsibilities.
Receive a Certificate of Attendance featuring Continuing Education Credits (CECs).
Access leading experts for one-on-one compliance problems.
Demonstrate your organizationʼs commitment to environmental due diligence.
Take home valuable reference and guidance materials.
Update your knowledge of new and changing regulations.
Connect with technology and service providers.
By David Nesseth
Now that Canada has finalized its objective value threshold for 25 types of PFAS in municipal drinking water, what’s next?
But what even is an objective value? Questions are swirling.
Health Canada told Environmental Science & Engineering Magazine that objective values are based on a rapid review of new scientific research and consider international regulatory information available at the time of their development. Like guidelines, the department says that drinking water objectives are externally peer-reviewed to ensure scientific integrity. They exist to reduce potential exposure to per- and polyfluoroalkyl substances (PFAS) through drinking water, while the full guidelines are given strict focus.
Ultimately, objective values are something to strive toward, says Robert Haller, executive director of the Canadian Water and Wastewater Association (CWWA). But he says that the association’s membership is more accustomed to dealing with a Maximum Acceptable Concentration (MAC), one which enables prov-
inces to develop enforceable regulations. That’s a point in PFAS regulation that Health Canada says could take some four to six years to reach.
“A MAC is a clear line in the sand — something measurable — where this was a little harder for us to get our heads around,” explains Haller. “It doesn’t mean we ignore it and put it on a back shelf. We’re recommending to our members to start taking action on this now.”
The action turns on a new objective of 30 nanograms per litre (ng/L), a threshold introduced and consulted on in draft form since early 2023. But it was not confirmed by Health Canada until August 2024. Municipalities can now test for all 25 listed PFAS, and when added together, they shouldn’t exceed that number.
It’s a limit that’s nearly been doubled in places such as North Bay, which has been working to remediate PFAS water contamination from firefighting foam. In 2023 the average concentration of PFAS in Trout Lake measured 56 ng/L. In other cities, like Ottawa, testing for various PFAS substances has been con-
ducted for some five years with little results for concern. The City of Toronto has been much the same story. In 2023, there were only a handful of detectable results out of some 300 samples, with only perfluorooctanoic acid, or PFOA, registering once in the realm of the new threshold, according to Toronto’s drinking water analysis data.
Still, Haller says it’s time for municipalities to start monitoring and determine whether there is an issue with PFAS levels. But there are challenges depending on the municipality. Fredericton, New Brunswick, for instance, is a place where testing would have to occur at a number of wells as opposed to one intake source. Haller says municipalities will need to thoughtfully target where they test and potentially study industrial impacts to determine the likelihood of PFAS in certain sources.
“If you take Toronto, and they’ve got one big pipe going out into the middle of the lake, they can test their source water out of a couple of plants. But if you go to Waterloo, they have say 100 wells and 100 potential test sites to determine the source of any potential PFAS. So, it can have a far greater impact on a community like that.”
Haller adds that PFAS requires testing from qualified labs with very specific
REGISTER TODAY!
EARLY BIRD DEADLINE IS FEBRUARY 14
MAY 5 - 7, 2025 FOR MORE INFORMATION
Certifying engineering technicians and technologists since 1965.
Health Canada says that drinking water objectives exist to reduce potential exposure to PFAS through drinking water, while the full guidelines are given strict focus.
Credit: francescoscatena,stock.adobe.com
equipment, which is not quite as simple as a lot of the standard testing that occurs locally.
Sampling should be conducted at least once per year, Health Canada recommends. It should be collected after treatment, but prior to distribution, typically at the entry point to the distribution system. Paired samples of source and treated water should be taken to confirm the efficacy of the treatment.
Scan to get your free information package and for your chance to win a $100 Amazon gift card!
certify@oacett.org www.oacett.org
“The objective offers Canada’s drinking water sector an efficient approach for risk management by providing only one target value for this group of chemicals, thereby reducing exposure to PFAS and potential health risk,” said a spokesperson for Health Canada.
At the association level across Canada, flurries of factsheets, FAQs, webinars and conference speakers are emerging as the industry looks to prepare for PFAS.
Ontario Municipal Water Association (OMWA) President Justin Pulleyblank told Environmental Science & Engineering Magazine that PFAS is challenging municipal water suppliers in Ontario, but the OMWA is “working to support the Ontario water sector as they ramp up efforts to assess and deal with potential impacts on their operations.”
Pulleyblank said the OMWA, in collaboration with colleagues from its Water, Wastewater, Stormwater Equipment & Technology Advisory Council, has recently delivered virtual webinars
on various operational aspects of PFAS chemicals, including potential sources and occurrence information, sampling and analytical methods, as well as treatment technologies.
The Manitoba Water and Wastewater Association held an entire day of sessions on PFAS issues in April, where speakers from the likes of ASL Global and Pinchin Ltd. shared their perspectives on how best to prepare for the changes PFAS may eventually demand.
Other associations, such as the BC Water and Waste Association (BCWWA), have formed task forces to help fast track education and awareness around PFAS. Stephen Horsman, a past president of the BCWWA and B.C. market lead for environmental engineering firm Carollo, says the eight-member task force will work to provide information and context for those in the water community who are not yet well-versed on the full scope of PFAS. The task force will get the conversation going full steam ahead, he says.
“It’s about empowering utilities about what is known, and what is still unknown,” Horsman told Environmental Science & Engineering Magazine
Local governments do want to get out in front of the PFAS issue, but the actual exposure is not comprehensively documented, adds Horsman. Labs in Canada are working to get proper methodologies in place to sample down to the objective value.
Horsman says he currently knows of about five medium- to larger-sized util-
ities in B.C. that have been testing for PFAS.
“Some of the utilities that did want to get out in front of it did their sampling and said, ‘hey, you know what? We don’t have a problem. It’s good.’ However, they were screening at the higher levels, and that doesn’t necessarily speak to where we’re at now.”
Of course, the next challenge is knowing what to do with the data once municipalities have it.
“The reluctance is what’s the next step? Communications is a critical component of that. This is going to be a shared response strategy, and who takes the lead on it, and how we approach it is going to be complicated and I think challenging,” says Horsman.
A similar challenge has been on Haller’s mind, in terms of what municipalities do with PFAS once collected.
“It becomes a problem for ourselves that when we treat PFAS, it doesn’t eliminate it, it just collects it. So what do we do with those toxins out of treatment?”
When most people hear about PFAS these days, it’s in the same breath as lawsuits, which have been coming fast and furious. B.C. is suing PFAS manufacturers, and a class action eyeing the likes of 3M and BASF got underway in Quebec earlier this fall. B.C. Attorney General Niki Sharma said she intends for the province to lead on PFAS accountability in Canada the same way it led on civil actions “against corporations that cause widespread public harm to people in B.C., including in recent years against tobacco and opiate manufacturers.”
Even further legal battles south of the border involve water associations or utilities suing PFAS manufacturers, or water groups headed to court over the U.S. Environmental Protection Agen cy’s (EPA) rule itself. In April, the EPA approved even stricter drinking water standards of 4 ng/L for two particular types of PFAS called PFOS and PFOA. At the heart of that complaint is the EPA’s use of a novel “hazard index” in place of an MCL for mixtures of certain PFAS, as well as the issuing of a preliminary determination to regulate certain PFAS simultaneously with the proposed rule.
Over the course of the last decade Health Canada detected 13 PFAS in 566 freshwater samples, according to the objective value report. Credit: africastudio,stock.adobe.com
Some U.S. associations warn that the Safe Drinking Water Act does not give the EPA authority to use a hazard index as an MCL.
“The hazard index for the mixture of four PFAS in the new rule is a novel approach where the MCL is based on a sum of the ratios of four observed PFAS concentrations and each PFAS’s respective ‘health-based water concentration,’” stated the American Water Works Asso-
ciation in June.
When it comes to standardized methods available to quantitate PFAS compounds in drinking water, Health Canada recommends the use of EPA Method 533, as it follows current best practices related to isotope dilution and is a solid phase extraction liquid chromatography-tandem mass spectrometry method.
Water products plus PERIPRO 4.5 x 4.875 Holistic.pdf 1 1/19/2023 3:40:41 PM
The EPA estimates between 6% and 10% of the country’s 66,000 public drinking water systems may be subject to the new PFAS rule and need to reduce PFAS to meet the new standards. Florida and California are the states with the most people relying on public water supplies drawn from potentially contaminated groundwater sources, researchers of a fall 2024 study found using U.S. Geological Survey data. The agency, however, believes the new limits are achievable using a range of available technologies that include granular activated carbon, reverse osmosis and continued overleaf…
ion exchange systems.
Health Canada states that while there are treatment technologies that can effectively remove certain PFAS, no single treatment can remove a wide range of PFAS under all conditions. To ensure continued and effective removal, the department’s objective value report suggests that each facility should establish operational conditions and parameters based on the selected treatment technology and the characteristics of the raw water, including PFAS type, concentration and treatment goals.
“The key issues to consider when selecting treatment technologies for PFAS removal are the presence of competing anions and PFAS species, organic matter and the frequency of regeneration or replacement required for the sorptive media used,” states Health Canada.
But discovering PFAS still continues to be the first order of business. A University of Montreal study published in 2023 analyzed PFAS contamination in tap water from 376 different munici-
palities in Quebec. More than 99% of the tap water samples were positive for at least one PFAS, which ranged from below detection limits to 108 ng/L. But only about 5% of the total water supply samples had levels above Canada’s new objective value.
“Achieving the objective may take time given the technical complexity and cost of measuring and managing PFAS as well as the prioritization and regulatory processes of individual jurisdictions,” said a spokesperson for Health Canada.
Over the course of the last decade Health Canada detected 13 PFAS in 566 freshwater samples, according to the objective value report. PFBA, PFPeA, PFHxA, PFHpA, PFOA and PFOS had higher detection frequencies than the other PFAS. One of the highest readings, too, was for one of these emerging subgroups: 137 ng/L for PFHxA, which is also one of the 11 problem PFAS facing North Bay, and the only other type of PFAS found in Toronto’s water last year.
As recently as September 18, the Euro-
pean Union restricted the use of PFHxA, although businesses will have transition periods to adapt. Officials noted the new restriction will ban the sale and use of PFHxA in consumer textiles, such as rain jackets; food packaging, like pizza boxes; consumer mixtures such as waterproofing sprays; cosmetics, like skin care products; and in some firefighting foam applications, like for training and testing, without compromising safety. It does not affect other applications of PFHxA, for example in semiconductors, batteries or fuel cells for green hydrogen.
In Canada, some efforts are already underway on a long road ahead to stop PFAS at the product stewardship level before water contamination ever becomes an issue. Alternative formulations continue to be developed; however, the federal government is requiring businesses to report on the presence of PFAS in their supply chains by January 29, 2025.
David Nesseth is with ES&E Magazine. Email: david@esemag.com
By Jeanne Hendrickson
The Carol Stream Water Reclamation Center (WRF), located in Carol Stream, Illinois, treats influent flow which is largely of a residential nature, with a small percentage coming from industry. As the name suggests, the Water Reclamation Center is owned by the Village of Carol Stream, but is operated and maintained by Jacobs Engineering.
The plant was experiencing good results using Blue-White® FLEXFLO® A2 peristaltic metering pumps. Two of them were dosing sodium hypochlorite, and three were being used to dose sodium bisulfite.
The issue the WRF faced was not that the system wasn’t working properly, it was the layout of the system. The equipment room was cramped and the piping cumbersome, so operators turned to a firm specializing in municipal and industrial water and wastewater treatment to assist in streamlining the equipment room.
The original project scope was focused on the side dosing sodium hypochlorite, and included the replacement of two 7,600-litre bulk storage tanks used for the hypochlorite. Removal of the old tanks meant some of the piping would also have to be replaced.
While considering piping replacement, the operators took a broader look at the overall piping system, as well as the location of the metering pumps and use of a flow meter. It was decided that what made the most sense would be to start over and reconfigure the entire piping system to simplify the look, as well as to add components such as a flow meter/wye strainer, and to properly size the delivery system.
A decision was reached to incorporate CHEM-FEED® wall mount skid systems. These are complete metering systems, delivered fully assembled and equipped with all necessary components. Other features include maximum chemical resistance with four pipe material options from which to choose, PVC, CPVC, PVDF, and Chem Proline®
Furthermore, the wall mount skid system included the desired flow meter as well as a calibration cylinder, pressure gauge with guard, a flow indicator, and an inlet Y strainer.
The fact that this complete system could be mounted on a wall meant much needed floor space would be opened up. Also, it would eliminate unnecessary process piping, clean up electrical and communications, and simplify housekeeping.
It was also at this time the decision was made to replace the FLEXFLO A2 pumps that had been in use, with the more feature-rich FLEXFLO M2 ones. These deliver gentle, low-shear pumping action, making it a great choice when dosing off-gassing chemicals such as sodium hypochlorite.
The fact that this complete dosing system could be mounted on a wall meant much needed floor space would be opened up.
In addition, the M2 has remote control signal options that includes remote start/stop, flow verification, pulse, and 4-20mA. The M2 is also equipped with a patented tube failure detection system, which warns of tube failure and stops the pumping action so spills don’t get out of hand.
The use of the wall-mounted skid system equipped with the M2 metering pumps produced such favorable results on the sodium hypochlorite side, that the WRF decided to undertake the same cleanup efforts and convert the sodium bisulfite side in the same manner.
Both the sodium hypochlorite installation and the sodium bisulfite installation have provided a highly functioning system that is clean, well-organized, and easily maintained.
Jeanne Hendrickson is with Blue-White Industries. Email: jeanne@bwadvertising.com
By Paul Getman
The Regional District of Mount Waddington (RDMW) on northern Vancouver Island is transforming how its remote villages handle wastewater management during power outages. With frequent power interruptions that often last over 12 hours, particularly during winter, maintaining functional wastewater operations in the villages of Coal Harbour and Sointula has been a significant challenge.
Historically, these areas relied on portable diesel generators to manually power wastewater pumping stations during outages. This strained resources, and often fell short of Ministry of Environment guidelines. However, the need for a more reliable and environmentally-friendly solution sparked an innovative project to build stationary battery backup systems that would keep critical infrastructure online.
Unlike more populated areas, northern Vancouver Island’s rural communities face unique difficulties in maintaining utilities. Coal Harbour and Sointula, for example, have sewer systems that rely heavily on pumping stations, which require continuous power. These are typically located near bodies of water, making the use of three-phase diesel generators risky, due to environmental concerns.
The village of Woss, with its gravity-fed wastewater system and passive lagoon treatment, did not face these same difficulties. However, for Coal Harbour and Sointula, power outages posed an operational challenge that required an innovative solution.
In the fall of 2020, RDMW’s former Chief Administrative Officer, Greg Fletcher, and former engineer Patrick Donaghy, initiated a search for more
Several of the 21.6 kWh battery backup inverters during construction.
sustainable alternatives to diesel generators. Initially, I as the project lead, was skeptical due to the high anticipated costs, but the team persisted.
After an extensive search, I did find some portable battery backup power units used in construction and on movie sets, but these proved to be unsuitable or too expensive to modify for our needs.
In the end, it became obvious that in order to meet our requirements, we would need to build our own battery backup systems. The decision was also made to assemble, rather than purchase, 25 LiFePO4 batteries (lithium iron phosphate) for the backup battery units, as this would save approximately $25,000. This way, the battery backup units would be tailored specifically to the needs of the Regional District.
By the summer of 2021, a proof-of-concept unit was developed using LiFePO4 batteries and three Outback inverters configured to produce 10.8 kW of 208 volt three-phase power for the sewer pumping station’s 3 kW (5hp) pumps.
This battery backup unit was assembled into an aluminum kiosk and designed to automatically switch to backup power during outages. It can provide the first 24 hours of power to the sewer pumping station and can, in an extended outage, be charged with a portable 2,500 watt inverter generator and 48 VDC battery charger.
After successful testing of the initial unit, we built and installed eight additional units, completing the project in the summer of 2022, despite the pandemic and resulting supply chain delays.
Each battery backup unit is connected to our local SCADA system and is able to be monitored and adjusted, sending alarms out as necessary. We expect that these units will need battery replacement in 10 to 15 years and inverter replacement in 15 to 20 years. Time will tell if our estimates are realistic.
The new battery backup units, which have now been in service for two years, have performed flawlessly, reducing the environmental risks associated with die-
sel generators and offering a “greener” solution to wastewater management. Though the initial cost was about 160% of diesel alternatives, long-term savings are expected through reduced maintenance.
The RDMW continues to explore more sustainable practices, with the possibility of additional battery backup systems for their wastewater treatment plants. The success of this project has positioned Mount Waddington as a leader in adopting green technologies in wastewater management. This achievement may inspire other regions to follow suit.
The project underscores a potential for more widespread adoption of battery systems in municipal and industrial infrastructure. The innovative approach taken by RDMW highlights the district’s commitment to sustainability, energy efficiency, and operational reliability.
By Annmarie Delfino
The McDowell Creek Water Resource Recovery Facility, part of Charlotte Water, a U.S. water utility in North Carolina, expanded from a permitted capacity of 23 to 46 megalitres per day in 2007. The expansion prompted the plant to invest in ChemScan analyzers for online and continuous process measurements. Fifteen years later, McDowell Creek was ready to replace them with two new ChemScan sample sequencers, developed specifically for plant-wide monitoring of nutrient removal processes.
“Specifically, for this plant, my permitted effluent limits are very stringent,” says Daniel Matias, plant supervisor. “So, the earlier I can detect an issue, the quicker I can resolve it. We need the predictability of catching it before it’s too late.”
Infrastructure modifications and seasonal influences on microorganism activity can add further complexity to the biological nutrient removal (BNR) process. A combination of monitoring methods is needed to ensure correct dosing and mixing in each zone of the plant and to verify measurements for confident decision-making.
In addition to the ChemScan units, phosphorus analyzers at the first and final stages of the process run continuously to provide additional points of reference. A wet lab ammonia analyzer at the start of the treatment process also contributes measurements. Additionally, plant operators take process control samples during each shift to monitor changes throughout the treatment process over a 24-hour period.
Still, plant staff have responsibilities beyond process control and would be overwhelmed if required to conduct multiple process-control sampling events during each shift. While operators conduct sampling events as frequently as possible, this still leaves an eight-hour interval between manual sampling. Even with the phosphorus and ammonia analyzers, staff wanted the ability to keep
tabs on the entire process at more frequent intervals.
Plant-wide monitoring 24/7 allows operators to treat analyzer and grab sample data as confirmation of process trends, rather than relying on them as guides for process adjustments.
The new sample sequencers expand the plant’s ability to correct issues that come up in between grab samples. The two units provide measurements of each of the plant’s seven sample locations every 55 minutes. One sequencer monitors the BNR basins, while the second takes samples from primary clarifier influent through tertiary filter effluent.
The sequencers also give Matias the ability to customize the sampling order. “The new installation lets us test where we want, at the time we want to test,” he says. . In addition to pulling samples consecutively from each zone in the usual influent-to-effluent direction, Matias can also set the units to sample from each zone in reverse.
If process adjustments are needed, he can also set the sequencer to take sam-
ples of select locations repeatedly. “For example, if I think there might be a phosphorus issue, it’s usually at the last three sample locations,” he says. “So, I can change the sequence and test just the back half. I can set it to test just zones five through seven and update data every 10 minutes instead of every 55.”
This freedom to set sampling direction and frequency makes it much easier to verify if process adjustments are having the desired effect.
Matias can now be even more proactive about managing their process adjustments thanks to customizable alarms that alert him to deviations in standard measurements.
“I was able to work with my electrical engineer and set pre-warnings,” Matias says. “If I see a number that’s out of the norm, it will send me an alarm so I can keep an eye on it. We couldn’t do that manually with the manpower we have.”
Integrating equipment into the plant’s infrastructure so the sequencer could provide a full-plant view of the BNR process was critical to the installation’s longevity.
Usually, ChemScan products are connected to multiple submersible pumps that bring samples up from the different zones of the treatment basins and through the analyzer system. But this design was less effective for the plant’s infrastructure, which features large vertical mixers and a single main sample pump connected to seven actuators, one for each sample location.
“The submersible pumps just didn’t fit how we mix in our zones,” says Matias. Consequently, engineers programmed the sequencer to control the plant’s sample zone actuators, manipulating the sample control valves to draw samples from each of the treatment basins’ seven zone locations through one main pump.
Annmarie Delfino is with In-Situ. For more information visit: www.in-situ.com.
By ES&E Staff
As Metro Vancouver in B.C. rolled out its “Wipe It, Green Bin It” campaign, local officials shared reports that crews removed 50 tonnes of fatbergs over recent months from the city’s Lulu Island Wastewater Treatment Plant.
The disposal of fats, oils, and grease (FOG) into the sewer system is an ongoing issue that contributes to sewer clogs and overflows that cost Metro Vancouver and member jurisdictions $2.7 million every year, according to a recent report. The recent removal of fatbergs alone has cost almost $1 million.
“Subsequent investigations discovered significant quantities of grease on the roof of the inverted siphon sewers in the upstream Gilbert Trunk Sewer, causing capacity restrictions. Traditional inspection and cleaning tools don’t work on siphons,” states a report from Peter Navratil, general manager of Liquid Waste Services.
Navratil noted that staff used non-traditional sonar technology equipment to clearly define where, and how much grease, was present. The flushing equipment was able to effectively remove grease from the large siphons. The work had to be completed during low flow conditions and required considerable coordination and support from the City of Richmond and local residents.
As the season turned to fall, crews had removed about two-thirds of the fatbergs, or 45 m³, (equivalent to six dump trucks full) from the most problematic siphon. Inspections and cleaning continue, with the goal of returning full capacity to the system.
“This discovery will lead us to create a new maintenance plan, which we plan to share with your municipalities, to prevent this type of buildup from occurring in the future,” says Navratil.
The region’s “Wipe It, Green Bin It” campaign started before Thanksgiving
Metro Vancouver crews removed 50 tonnes of fatbergs (chunks of hardened grease) over recent months from the city’s Lulu Island Wastewater Treatment Plant. Credit: Metro Vancouver
to reach residents when they are preparing heavier, holiday-oriented meals. Creative materials highlight various forms of FOG and raise awareness of the impacts of foods that are less known for causing problems in sewers, like dairy products.
The target audience continues to be Metro Vancouver adult residents.
This year’s campaign will aim to reach more of the younger demographic, who
are more likely to put FOG down their sinks, as shown by recent survey results. The campaign’s paid placements include YouTube, social media, Pinterest, television, Google search, and advertising on bus sides and in SkyTrain stations.
For more information, email: editor@esemag.com
By Roger Lah
Conventional motorized valves are often designed for a single control function, with limited or no capacity for multiple electronic operations or hydraulic backup. In contrast, hybrid valves that combine electronic and hydraulic control mechanisms offer several advantages.
These hybrid systems can streamline valve counts in a given setup, while providing crucial safeguards against power disruptions and expensive line failures. The following three case studies demonstrate how this hybrid approach effectively shielded systems during electrical outages.
In the event of a power outage, water treatment plant operators face a complex and time-consuming task to avert water spillage onto the plant’s floor. This procedure requires the manual shutdown of multiple motorized valves controlling the inflow and outflow. Additionally, when a filter becomes saturated with sediment, a backwash is initiated by reversing the water flow to loosen the filter bed, with the dislodged waste directed away. The flow rates are carefully increased and then decreased throughout the backwash cycle to ensure the filter is thoroughly cleansed before resuming normal operation.
The valves are usually controlled by a programmable logic controller (PLC) to control flow into a filtration backwash process, utilizing Venturi flow meters. These operate on the principle of differential pressure, that utilizes the Venturi effect where a fluid’s velocity increases as it passes through a constricted section of the pipe, resulting in a pressure
A hybrid multi-function electronic and hydraulic metering valve.
drop. This pressure difference is measured and used to accurately calculate the flow rate.
These butterfly valves are susceptible to cavitation problems and therefore a hydraulic pressure reducing valve is normally installed upstream to reduce the pressure and prevent cavitation. This traditional arrangement requires significant piping space for two valves and a Venturi flow meter. Furthermore, power failure to the motor-operated valve can cause significant problems.
Another approach is to replace the hydraulic pressure reducing valve with a hybrid multi-function electronic and hydraulic metering valve. This valve is capable of measuring and controlling flow based on valve position and differential pressure sensors installed on the valve. It also incorporates anti-cavitation trim to prevent cavitation due to the high
pressure drop into the filtration process.
The electronic metering function utilizes dual solenoids and simply changing the upstream closing solenoid from “normally closed” to “normally open” will result in hydraulic valve closure when a power failure occurs. This allows the plant operator to handle other important duties when loss of power happens.
The single metering valve replaces the previous lengthy piping arrangement, saving significant space. As the replacement valve discharges directly into the filtration process, a hydraulic pressure limiting function can be added to provide a “hydraulic guarantee” against overpressurizing the system.
In another treatment plant application utilizing prefabricated treatment
equipment, a hydraulic pressure-reducing valve was used to limit the pressure in the process. A relief valve was used to provide protection for a 16-km long pipeline feeding into the plant, with a fast-closing butterfly valve to shut down the process during a power failure. However, this sometimes resulted in a surge. The engineer’s surge analysis determined that the pressure-reducing valve was required to close in 12 minutes when this occurs, and a standard closing needle valve is incapable of controlling these long closing times.
The simple answer was to modify the pilot control system to perform a switch between the normal pressure-reducing function and electronic controlled closing of metering flow to zero flow, in a programmable period.
In addition, a third solenoid was installed to switch between the normal hydraulic control to electronic control in the event of a system shutdown. Operators can easily see on the valve controller screen the status of the closing sequence. They are also able to adjust closing times if the required closing time requires amendment.
This valve therefore accomplishes two very important functions: a hydraulic pressure-reducing function during normal operation, and an electronic “time of closure” function to prevent surging in the long upstream pipeline.
In a recent new treatment project startup, an electronic flow control valve began to open but was barely able to move. A check of the downstream pressure gauge revealed that downstream pressure had already reached the setting of the pressure-limiting pilot control. It transpired that the water district had forgotten that an isolation valve had been closed some distance downstream.
In effect, the hydraulic control system prevented a pipe break from occurring. The electronic control system is capable of multiple functions such as flow control and pressure reduction. In this instance, the hydraulic pilot was used as “backup insurance” where the pilot control adjustment was set to not interfere with normal electronic multi-function control. Normal operation consists of electronic flow control and electronic pressure-reducing control and seamlessly transfers between functions with specialized software. In the event of power failure, or solenoid malfunction, the hydraulic pilot will take over and limit downstream pressure, preventing pipe breakage.
Up to four modulating electronic functions are possible, including flow, sustaining pressure, reducing pressure, and level control. Reservoir level control, for example, can include flow control and pressure-sustaining control.
Conversions of existing altitude control valves often include the hydraulic altitude control pilot for backup control to prevent the overflowing of a tank. Often there is a long pipeline upstream of these valves which is susceptible to surging during valve closure. A hydraulic “surge relief override” pilot control will prevent surges in case of faster than normal valve closure.
Integrating various hydraulic and electronic functions into a single valve can streamline your system by minimizing the number of valves required. This not only safeguards aging infrastructure and sensitive piping but also mitigates the risk of overflows in tanks and reservoirs. A favored integration is the pairing of electronic flow control with hydraulic pilot control, which maintains downstream pressure within desired limits. Such a hybrid approach ensures electronic flow control is maintained until the hydraulic pilot’s threshold is surpassed.
To optimize a treatment plant and water distribution network’s protection, especially during power failures, consider collaborating with valve manufacturers. Their expertise can help tailor solutions to your specific needs, potentially leading to better long-term outcomes and increased system reliability.
Roger Lah is with Cla-Val. For more information, visit: www.cla-val.com/cla-val-canada
During WEFTEC 2024 in New Orleans, Peter Davey, ES&E Magazine’s Managing Editor, sat down with Marc Larivière and Jeff Peeters from Veolia Water Technologies to discuss trends and key issues facing Canada’s water and wastewater sector.
What are the major trends developing for Canada’s water and wastewater sectors?
Marc: One of the major trends we are seeing all over Canada is what I would call “future proofing”. Engineers are looking at upcoming regulations, such as those concerning micro-pollutants and other emerging contaminants, and they are asking us to design treatment plants that are highly robust and resilient.
We are being asked about resilient infrastructure and technologies a lot, and we are looking into it as the demand is quite high. While climate change is certainly a big driver, there are also other factors to consider such as oil spills.
What challenges are customers coming to you with?
Jeff: For wastewater, we are seeing population growth putting more pressure on treatment plants, as well as new regulations in Canada, and we think wastewater intensification is a solution. This means using new technologies instead of doing what we have done for 100 years and building big concrete tanks. We are now putting technologies into existing tanks to get more capacity, such as IFAS and MABR.
Another consideration is greenhouse gas emissions. It is not necessarily driving decisions today, but I think it is in the back of people’s minds. We are looking at ways to offer solutions that also reduce emissions, whether that is energy consumption, or Scope One emissions of methane and nitrous oxide. However, while there is lots of chatter about it, and while some customers are concerned with it, there is not much action yet.
Marc: Many major treatment plants, especially in Quebec, are currently using only primary clarifiers. We are working with these facilities to evaluate different technologies that will help them meet the Wastewater Systems Effluent Regulations (WSER). Vancouver is another area where we are seeing a demand for advanced solutions. They are looking at different technologies to add secondary biological treatment, and we are involved in this process, offering solutions such as MBR technology, biological aerated filtration, IFAS, MBBR and so on.
On the drinking water side, we are seeing increasing opportunities related to the treatment of blue-green algae. For exam-
ple, at a project in Moncton, they started experiencing problems with algae that their existing clarifier could not handle effectively. While we can remove the algae, we are also prepared for scenarios where toxins are released. In such cases, we can treat the water with a powdered activated carbon (PAC) tank before the Actiflo process. Additionally, we are evaluating several technologies using ozone or PAC to remove these toxins efficiently.
How does the industry-wide challenge of an aging workforce influence technology development, especially for a company like Veolia that has a significant operations division?
Jeff: From our part of the business where we offer technologies, it is making sure those technologies do not require a whole lot of operations and maintenance, or that they can even reduce operations and maintenance. So, we have a digital solution called Hubgrade that can take some of the control and the know-how off the plate of the operator, and ease the operation and its requirements for future programs.
What global trends or lessons are you seeing that might influence the sector in Canada?
Jeff: There are parts of the world that are really focused on greenhouse gas emission mitigation, such as Australia, New Zealand, the U.K., and the Nordic countries. They are trying to determine the baseline — what are their emissions today — and then look for actions to reduce that, which Canada could be doing better than we are.
Water reuse is happening more in other parts of the world. Although Canada is blessed with lots of fresh water, reuse could become a reality for us in the future. The earlier we start preparing society for that the better.
Marc: With drinking water, we are seeing more stringent regulations in other parts of the world, for instance in France. There, we are already implementing treatment plants designed to treat pesticides and other similar contaminants, so we already know the technologies that will be most effective in this matter. While regulations are not as stringent in Canada yet, we will probably see it eventually.
Jeff: Another thing we could be doing better is preparing in anticipation of challenges and regulations. For example, what do we do for a phosphorus limit of 1 mg/l now, and what if it becomes 0.1 mg/l in the future? How are we to manage that? And for micro-pollutant removal, how do we design our secondary treatment systems to anticipate that? It goes back to what Marc said about future-proofing.
Can you speak about trends in the industrial water sector?
Jeff: Micro-electronics is a big deal in the U.S. with the CHIPS
and Science Act, so there is lots of investment both for the front-end water treatment and the back-end wastewater treatment. With these big chip fabrication plants being built, they have a huge water demand that requires ultrapure water to make sure you are not contaminating the chips. And, they produce wastewater that has wide variabilities, so you need specialized treatment on the back-end.
Water reuse is also a big deal for data centers. They might be built where there is lots of power but limited water supply, and they need water for cooling. So, there is a big water demand for these data centres that we are supporting.
Marc: But the biggest industrial market for us in Canada is mining, with mining companies increasingly focused on sustainable water management as a core part of their operations. Key priorities include effective tailings management, wastewater treatment, and minimizing environmental footprint while maintaining operational efficiency. The industry is actively investing in water-efficient technologies and resource recovery solutions to ensure long-term sustainability and maintain strong community relationships.
What are you hearing from WEFTEC attendees? What is the industry excited about?
Marc: PFAS is a topic generating a lot of buzz at the show. While it is a little bit less in Canada, it is coming, so we are hearing about that a lot.
Jeff: Talking to customers, it seems that there are a lot of well-developed projects. They have a plan, they know what they need to do, they are just evaluating a couple of different technical options. But these are real projects that are happening, so it is encouraging! It also feels like there is a lot of activity in the municipal market too.
Jeff Peeters is the Innovation & Incubation Leader with Veolia Water Technologies & Solutions.
Marc Larivière is Vice President, Business Development – Municipal Canada, with Veolia Water Technologies. For more information, email: peter@esemag.com
By Louisa Bastone, Celina Li, Jennifer Burnett and John C. Fisher
How to properly record the costs of Asset Retirement Obligations (AROs) has given rise to many discussions in public sector accounting. These discussions have led the Public Sector Accounting Board (PSAB) to create a new Public Sector Accounting Standard, PS 3280, which came into effect on April 1, 2022.
AROs are legal obligations associated with the retirement or remediation of tangible capital assets. According to the PSAB, these obligations should be recognized. Specific examples include, but are not limited to, the removal of asbestos from buildings, decommissioning of underground storage tanks and closure of landfills or waste storage facilities.
• The organization expects further economic benefits will be given up.
• A reasonable estimate of the cost can be made.
Due to the excessive cost that usually comes with AROs, organizations are required to recognize, evaluate and distinguish them from other activities in their financial statements to reflect the overall values. The new accounting standard PS 3280 has filled in the gaps with previous accounting methodologies by providing specific guidelines for organizations to report standardized measures of AROs.
PS 3280 provides guidance to public sector accountants on how to report AROs, including how they should be recognized, measured, and disclosed. This standard applies to all tangible capital assets controlled by a public sector organization, regardless of the asset’s status.
According to the standard, an ARO is recognized under PS 3280 by the following criteria:
• There is a legal obligation to incur retirement costs, in relation to a tangible capital asset.
• The transaction or event that created the obligation has occurred.
Following these criteria will ensure that the AROs are recognized, and the costs are reflected within the organization’s financial statements.
Once an ARO is recognized, accurate measurements of liabilities relating to retirement, as well as post-retirement activities such as labour, materials and overheads, must be determined to evaluate the obligation and analyze the direct cost and impact on the financial statements. The time value for money and discounted rates specific to the liability should also be considered during the process.
In the subsequent measurement, the standard also mandates the organization to reconsider the carrying amount of the asset liability on annual financial statements relating to fiscal years. In particular, the period-to-period changes in liability, including revisions to cost estimates or aging, must be recognized in the financial statements.
The amended carrying amount of the tangible capital asset is adjusted according to the asset’s remaining useful life. The disclosure requirements under the standard must include a detailed descrip-
tion of the ARO, the basis for the estimate, and a reconciliation of the beginning and ending balances of the liabilities.
Another consideration in PS 3280 is to ensure that organizations take a proactive approach to their liabilities. In following the standard, an organization must identify all assets that have followed the four criteria mentioned above and determine if they are classified as obligations. This process involves many departments, such as legal, environmental, and financial, to collaborate in order to collect all necessary data.
Once an ARO is identified, an organization would have to measure and document these obligations. This process would involve hiring an external expert,
Since the introduction of PS 3280 in 2022, it has been anticipated that a substantial impact would be exerted on the environmental consulting industry, leading to a higher demand for more specialized services. Expertise in environmental consulting, including hazardous material management and removal, public health risk assessment, and site remediation, will be sought after, with an emphasis on compliance with these new requirements.
As a result, environmental consulting experts who can provide accurate and precise asset valuations, asset management, and mitigation strategies for AROs will become highly needed for both public and private sectors.
Environmental consulting firms, equipped with tools for carrying out
Adherence to ARO regulations will yield significant benefits in preventing environmental degradation and protecting community health.
such as an environmental consultant, to provide estimates on costs and additional factors.
During this process, experts conduct a visual inspection of all identified assets to look for the possible presence of hazardous materials, such as asbestos, lead, and mercury. The estimated costs for abatement/remediation to be performed will then be provided by the inspection expert. This report can be used for the organization’s financial records, and if there are any hazardous materials identified, it can be used for the commencement of the abatement/remediation process.
Finally, organizations must stay updated on any changes to PS 3280 or related regulations to ensure ongoing compliance. This includes regular reviews of asset inventories, re-evaluation of cost estimates, and timely updates to financial statements. Failure to comply with PS 3280 can result in significant financial and reputational risks, making it imperative for public sector entities to prioritize ARO management.
comprehensive ARO-related measurements, can grow and benefit from the rising demand of this specialized expertise. This is especially true for multi-disciplinary consulting firms who are already offering integrated service platforms consisting of not only engineering, data and environmental science but also legal expertise to provide systematic solutions for prompt ARO assessments.
With the multidisciplinary and interdisciplinary capabilities to solve problems in environmental consulting, firms will be well positioned to thrive and become the market leader. Furthermore, technological advancements and software innovations stemming from the adoption of the new ARO standards are anticipated to gradually emerge, thus improving the accuracy of financial reporting and streamlining the compliance process.
On the other hand, rigorous ARO regulations can also ensure and validate whether health and safety standards are fulfilled. For instance, management and removal of hazardous materials such as
asbestos from the environment will be actively pursued because organizations and companies are obligated to follow stricter guidelines with greater care for regulatory compliance.
Since the responsible parties are required to disclose AROs and publish the related costs identified to retiring the asset, public awareness and accountability around environmental health and safety will therefore also be improved.
Ultimately, organizations and companies will be expected to consider and prioritize the actions taken to handle AROs diligently to avoid increased scrutiny from the public and stakeholders. This transparency will foster a culture of responsibility where both public and private entities are held accountable for the environmental impacts of their operations.
In the long term, adherence to ARO regulations will yield significant benefits in preventing environmental degradation and protecting community health. By ensuring that asset retirements are managed safely and sustainably, these regulations will help mitigate the risks of pollution, contamination, and other environmental hazards.
Ultimately, compliance with PS 3280 will contribute to the creation of safer, healthier communities and a more sustainable future, as well as help organizations manage decommissioning costs associated with asset retirement.
AROs are an inherent aspect of financial management for public sector entities. With the implementation of PS3280, organizations are now required to account for these obligations with greater precision and transparency. By understanding the requirements of the standard and taking a proactive approach to compliance, public sector entities can not only meet their legal obligations but also ensure that they are effectively managing their environmental and financial responsibilities for thebenefit of all stakeholders.
Louisa Bastone, Celina Li, Jennifer Burnett and John C. Fisher are with T. Harris Environmental Management Inc. For more information, email: info@tharris.ca.
The AquaPrime® cloth media filtration system is designed as an economical and efficient solution for the treatment of primary wastewater and wet weather applications with high quality effluent, even under varying influent conditions. This system utilizes a disk configuration and the exclusive OptiFiber PF-14® pile cloth filtration media to effectively filter high solids waste streams without the use of chemicals.
Represented by ACG-Envirocan
T: 905-856-1414
E: sales@acg-envirocan.ca
W: www.acg-envirocan.ca
Aqua-Aerobic Systems, Inc.
T: 815-654-2501 | F: 815-654-2508
E: solutions@aqua-aerobic.com
W: aqua-aerobic.com/filtration/
The Aqua MegaDisk® tertiary filter “expands” on the reliability and exceptional performance of the original AquaDisk® filter, but on a larger scale. The Aqua MegaDisk offers larger diameter disks and fewer mechanical components than the AquaDisk filter. The result is the smallest footprint available, operating in 80% less space than sand filters with comparable hydraulic capacity.
Represented by ACG-Envirocan
T: 905-856-1414
E: sales@acg-envirocan.ca
W: www.acg-envirocan.ca
Aqua-Aerobic Systems, Inc.
T: 815-654-2501 | F: 815-654-2508
E: solutions@aqua-aerobic.com
W: aqua-aerobic.com/filtration/clothmedia/
A clogged air filter increases pressure loss and energy consumption, reducing overall system efficiency. This can lead to significant extra electricity costs each year. Regular filter changes help avoid these expenses. AERZEN offers filters in a series of options tailored to a wide range of machine technologies, such as positive displacement-, screw- and turbo blowers as well as screw compressors and room air conditioners.
AERZEN CANADA INC.
T: 450-424-3966 Montreal
T: 437-703-7630 Toronto
T: 587-316-0155 Calgary
E: service-ca@aerzen.com
E: sales-ca@aerzen.com
W: www.aerzen.com
AERZEN Delta Lube 06 offers superior lubrication and extended service life for blowers and compressors. With a high lubricity, this low-viscosity oil doubles the interval between changes by up to 16,000 operating hours, leading to 40% cost savings over two years. Designed for extreme conditions, Delta Lube 06 ensures reliable performance even under high mechanical loads, temperature variations, and air humidity.
AERZEN CANADA INC.
T: 450-424-3966 Montreal
T: 437-703-7630 Toronto
T: 587-316-0155 Calgary
E: service-ca@aerzen.com
E: sales-ca@aerzen.com
W: www.aerzen.com
Wondering how to maintain or clean modular stormwater detention tanks? Discover the Vario 800 flex shaft system, offering easy maintenance access for long-term functionality. It efficiently manages stormwater, reduces flood risks, controls soil erosion, and conserves water. Its adaptable design complies with HS-20 ratings and allows for flexible installation in diverse conditions.
BARR Plastics Inc.
T: 1-800-665.4499
E: info@barrplastics.com
W: www.barrplastics.com
The low-shearing pumping action of the FLEXFLO M4 Peristaltic Metering Pump allows it to gently and precisely pump chemicals that off gas, including peracetic acid and sodium hypochlorite, with no vapour lock and no lost prime. The advanced features of the M4 include a highly responsive 5 inch display, firmware that can be field updated, and easyto-attach M12 watertight connectors.
Blue-White Industries
T: 714-893-8529
E: info@blue-white.com
W: www.blue-white.com
BW DIGI-METER Paddlewheel Flow Meters provide dependable accuracy, are simple to install, and are easy to operate. The panel mount readout may be installed remotely in the most convenient location, while the sensor is installed in an obscure area of the pipe system. The water range is between 0.4 and 8000 GPM and can fit 3/8" to 12" pipe sizes.
Blue-White Industries
T: 714-893-8529
E: info@blue-white.com
W: www.blue-white.com
The Chlor-Scale 150™ from Force Flow provides a simple and reliable way to monitor the amount of chlorine or ammonia used, and the amount remaining in the cylinder. The solid PVC scale platform, with a 5-year warranty, provides the strongest defense against the corrosive environments associated with gas feed applications. Electronic and hydraulic options are available.
Force Flow
T: 925-686-6700 or 800-893-6723
E: info@forceflow.com
W: www.forceflowscales.com
The Terminator™ Actuator from Halogen Valve Systems can be used on chlorine ton containers and 150 lb cylinders to instantly stop the flow of chlorine in case of an emergency. Shutoff is initiated when the controller receives a close contact signal from a leak detector or included emergency shutoff switch.
Halogen Valve Systems
T: 949-261-5030
W: www.halogenvalve.com
Harmsco® Hurricane® housings provide effective performance, with up to 20% in energy savings. Their patented design combines three filters into one compact housing, with flow rates to 2,400 GPM. The outer chamber induces cyclonic separation of dense solids prior to up-flow cartridge filtration, resulting in extended cartridge life and increased dirt-holding capacity, fewer maintenance intervals, and reduced overall operating costs.
Harmsco Filtration Products
T: 800-327-3248
E: sales@harmsco.com
W: www.harmsco.com
The new Stormceptor® EF is an oil grit separator (OGS)/hydrodynamic separator that effectively targets sediment (TSS), free oils, gross pollutants and other pollutants that attach to particles, such as nutrients and metals. The Stormceptor EF has been verified through the ISO 14034 Environmental Management – Environmental Technology Verification (ETV).
Imbrium Systems
T: 800-565-4801
E: info@imbriumsystems.com
W: www.imbriumsystems.com
Inspection and maintenance are fundamental to the long-term performance of any stormwater quality treatment device. The Stormceptor EF/EFO design makes inspections and maintenance an easy and inexpensive process conducted at grade. Once serviced, the Stormceptor EF/EFO is functionally restored as designed, with full pollutant capture capacity. Learn more at: www.imbriumsystems.com
Imbrium Systems
T: 800-565-4801
E: info@imbriumsystems.com
W: www.imbriumsystems.com
Orival Water Filters remove unwanted organic and inorganic suspended solids to protect nozzles, RO and ion exchange units, ozone and UV treatment systems or chlorination systems. With models from ¾" to 24" and filtration degrees from 5 to 3,000 microns, Orival Automatic Self-Cleaning Filters are designed to withstand the day-in and day-out rigours of POTWs and stay on-line during the rinse cycle, providing uninterrupted flow of clean water.
Orival
E: filters+ese@orival.com W: www.orival.com
HUBER, a proven German manufacturer, now provides watertight doors that allow safe access to tanks for construction and/ or maintenance. Doors can be provided as round or rectangular for installation onto existing concrete surfaces or cast-in-place in new concrete. They can handle heads up to 30 m and hold pressure in seating and unseating directions. HUBER’s watertight doors can greatly reduce construction and maintenance costs and dramatically improve safety/access.
Pro Aqua, Inc.
T: 647-923-8244
E: aron@proaquasales.com
W: www.proaquasales.com
Invent Environment is the manufacturer of hyperboloid mixers which have revolutionized anoxic and swing zone mixing. Invent provides low-shear, efficient mixers with no submerged motors or gear boxes for easy access for maintenance. They have now released the Hyperclassic Mixer Evo 7 which has increased the number of motion fins and adjusted the geometry of the mixer to maximize mixer efficiency, reducing operation costs even further.
Pro Aqua, Inc.
T: 647-923-8244
E: aron@proaquasales.com
W: www.proaquasales.com
Vanton’s vertical thermoplastic sump pumps are engineered for the dependable handling of corrosive, abrasive, and ultra-pure process fluids, plant effluents and wastewater, over broad temperature and pH ranges. These rugged pumps are widely used by various manufacturing industries and water treatment facilities. They are available in polypropylene, PVC, CPVC, or PVDF. Every Vanton pump is performance tested to the specified service condition intended.
Vanton Pump & Equipment Corporation
T: 908-688-4216
F: 908-686-9314
E: mkt@vanton.com
W: www.vanton.com
Vanton Chem-Gard CGM-ANSI magnetically driven end suction pumps are seal-less, single-stage process pumps which meet ANSI B73.1 specifications and conform to Hydraulic Institute Standards. All wet-end components are homogenous, injection-molded polypropylene (PP) and polyvinylidene fluoride (PVDF), eliminating metal-to-fluid contact, making them ideally suited for handling corrosive, hazardous and ultrapure fluids. Flows to 450 GPM, heads to 180 ft, and temperatures to 225°F.
Vanton Pump & Equipment Corporation
T: 908-688-4216
F: 908-686-9314
E: mkt@vanton.com
W: www.vanton.com
Waterloo Barrier® is a containment wall for the control of contaminated groundwater or soil gases. Formed of steel sheet piling with interlocking joints that are sealed in-place in the ground, the Barrier offers a long service life, exceptionally low hydraulic conductivity, and documentable construction QA/QC. Installation is clean and rapid with minimal site disturbance.
Waterloo Barrier Inc.
T: 519-856-1352
E: info@waterloo-barrier.com
W: www.waterloo-barrier.com
Register
By Edgar Tovilla
The initial impetus for innovation in municipal water governance in Ontario was the Walkerton tragedy in 2000, when an estimated 2,300 people became seriously ill and seven people died from exposure to microbially contaminated drinking water in Walkerton, Ontario, a town of approximately 5,000 people located northwest of Toronto.
Afterwards, an independent inquiry led to a series of legislative, policy and governance responses that focused on the drinking water sector. In particular, following Justice Dennis O’Connor’s Inquiry recommendations, the Ontario government modernized its legislation on municipal drinking water.
The resultant framework for Ontario’s drinking water follows a risk-based management approach and includes a legislatively mandated quality management system developed for drinking water: the Drinking Water Quality Management Standard (DWQMS). The DWQMS draws on the ISO 9001 standard for Quality Management Systems (QMSs), as well as the Hazard Analysis and Critical Control Points (HACCP) for the food industry, and also considered elements of ISO 14001 standard for Environmental Management Systems (EMS).
The municipal wastewater and stormwater sectors have largely been left behind, still operating pursuant to a regulatory structure originally established in the 1950s under the Ontario Water Resources Act (OWRA). In recent years however, the province, through the Ministry of the Environment, Conservation and Parks (MECP), accomplished great progress on its modernization of permitting through: the O. Reg. 208/19, the Prescribed Person regulation (enacted in 2019); a new permissions
approach with the consolidated linear infrastructure environmental compliance approvals (CLI-ECA), which has rolled out since 2013; and a collection systems design criteria.
These actions brought a level playing field to the wastewater sector that to some extent mirrored the Safe Drinking Water Act. That said, there has been no wholesale updating and integration with management systems akin to the DWQMS.
Prior research found evidence in support of, and wide recognition of, the practical value of EMS, by assisting municipalities in meeting their environmental objectives, addressing environmental and property damage risks, providing an additional mechanism of public accountability and transparency. It also improved the alignment with the existing legal structure.
It was also apparent that there is no political appetite in the provincial government to embark on a mandated EMS, so the preference was a provincially-endorsed, voluntary sector-specific standard for wastewater, which could constitute a catalyst to boost voluntary uptake of EMS by small to medium municipalities (as it is already occurring with large municipalities). Prior research also supports the propositions of an existing global trend to develop sector-specific standards on multiple industries (e.g.,
asset management, petroleum, petrochemical, natural gas, and water
The wastewater management system (WWMS) standard is a quality and environmental management standard that brings together elements of ISO 9001 for Quality Management, ISO 14001 for
Environmental Management, and the DWQMS.
The scope of the standard is centered on the operational processes for wastewater collection, treatment and biosolids, and other emissions management. These operational processes have on the front the inputs (i.e., sanitary sewer, combined sewer, rainfall, inflow and infiltration and surface spills); as well as the outputs at the back (i.e., reclaimed wastewater to the environment, biosolids management, odour and other emissions). This framework is supported by a combination of support processes, some of which are in-scope, and others that are out-of-scope. The in-scope support processes are grouped into three areas. See Figure 1.
standard for wastewater, which could constitute a catalyst t small to medium municipalities (as it is already occurring wit research also supports the propositions of an existing standards on multiple industries (e.g., cybersecurity, asset ma petrochemical, natural gas, and
The wastewater management system (WWMS) standard is a quality and environmental management standard, which brings together elements of ISO 9001 for Quality Management, ISO 14001 for Environmental Management, and the Ontario Drinking Water Quality Management Standard (DWQMS).
The out-of-scope processes include: watershed planning, environmental assessments, occupational health and safety, engineering design for new development and expansions, construction and business continuity.
Since 2019, the Canadian Standards Association (CSA Group) has partnered with representatives from public and private sector organizations to develop
a new standard for wastewater management systems in Ontario. This standard was developed to be applicable to both public and private organizations who own and/or operate wastewater systems.
The scope of the standard is centered on the operational processes for wastewater collection, treatment and biosolids, and other emissions management. These operational processes have on the front the inputs (i.e., sanitary sewer, combined sewer, rainfall, inflow and infiltration and surface spills); as well as the outputs at the back (i.e., reclaimed wastewater to the environment, biosolids management, odour and other emissions). This framework is supported by a combination of support processes, some of which are in-scope, and others out-of-scope. The inscope support processes are grouped in three areas. See Figure 1.
Conceptualization of this standard had strong support from the MECP, the Water Environment Association of Ontario
(WEAO, a Water Environment Federation Member Association), the Ontario Good Roads Association, Ontario municipalities, the Greater Toronto Sewer & Watermain Contractors Association, the Ontario Sewer & Watermain Construction Association and consulting firms.
continued overleaf…
The out-of-scope processes include: watershed planning, environmental assessments, occupational health and safety, engineering design for new development and expansions, construction and business continuity
This new CSA Group standard is meant to be adopted on a voluntary basis by any organization, public or private. Although originally envisioned to be a standard applicable to Ontario only, it was really developed to be applicable nationwide.
In 2024, the CSA Group formed the W217 Technical Committee with a wide representation of stakeholders that included provincial and municipal governments, industry associations, water management system auditors, private operators and consultants. These stakeholders saw the need for a standard to address quality, environmental and property damage risks, while providing an additional mechanism of public accountability, and improving alignment with the Canadian and Ontario water legal structure.
The WWMS is intended to apply to the operation of public and private municipal wastewater system physical assets, from initial commissioning until operation ceases, including protecting the life cycle of infrastructure assets. For the WWMS standard, while other standards were considered (e.g., ISO 45001, Z45001, ISO 55001, ISO 14044, and ISO 31000), the standard was developed on a customized variation of ISO 9001, ISO 14001, and Ontario’s Drinking Water Quality Management System.
The W217 WWMS standard will be made available to the public after its publication (estimated in the Spring of 2025) for a period of five years and will also include free computer view-access and the opportunity to purchase and download the standard in English or French.
The W217 Technical Committee was formed by 25 members from different stakeholder groups: government, private sector, industry associations, and others. Committee members spent a significant amount of time since January 2024 working to develop the content of this standard.
As experts in their respective fields, they brought forward engaged discussion and enriched conversations from different perspectives. Of significant value for the content development phase
Lavina Ahuja
Chris Angelo
Akli Ben-Anteur
Shannon Boland
Justyna Burkiewicz
Gary Burrows
Kenneth Clogg-Wright
Pat Coleman (Vice-Chair)
Sandra Gay
Pamela Guenther
Scott Hall
City of Hamilton
Good Roads
City of Greater Sudbury
Ontario Ministry of the Environment, Conservation and Parks (MECP)
The Regional Municipality of Peel
City of London
CSA Group
Stantec
City of Ottawa
City of Barrie
R. V. Anderson Associates
Andrew Henry Huron Elgin Water
Christine Hill
Krystal Lewis
Adam Long
Christopher Manning
Charlene McKay
Gus Morelli
Meredith Pratley
Kristin Pressey
Brigitte Roth
Darlene Suddard
Edgar Tovilla (Chair)
John Zhang
Ying Zheng
Arcadis Professional Services (Canada) Inc.
Clearford Water Systems
Utilities Kingston
Ontario Ministry of the Environment, Conservation and Parks (MECP)
City of Hamilton
OSWCA and GTSWCA
York Region
City of Guelph
Acclaims Environmental Inc.
Municipal Water Solutions Inc.
City of Markham
OCWA
Toronto Water
CSA Group W217 WWMS Technical Committee members.
was the critical mass of knowledge created under the Drinking Water Quality Management Standard across Ontario over the past 17 years since it became a regulatory requirement.
Edgar Tovilla, P.Eng., PhD, is the CSA W217 WWMS Technical Committee Chair, and Post Doctoral Fellow at Toronto Metropolitan University. Email: etovilla@markham.ca
References are available upon request.
Whether you’re looking to change over an existing blower in your system, or install a new efficient blower with extensive volume, one of TNE’s High-Speed Turbo Blowers is your solution.
TNE Turbo Blowers are uniquely engineered with full three-dimensional back-swept impeller design offering unrivaled efficiency, comparable to the efficiency of medium/large size turbo blower.
Each blower in the wide-ranging TNE collection reduces energy consumption, while their ultra-high speed high efficiency air-cooled permanent-magnet synchronous motor delivers up to 100,000 RPM for high pressure turbo blower applications.