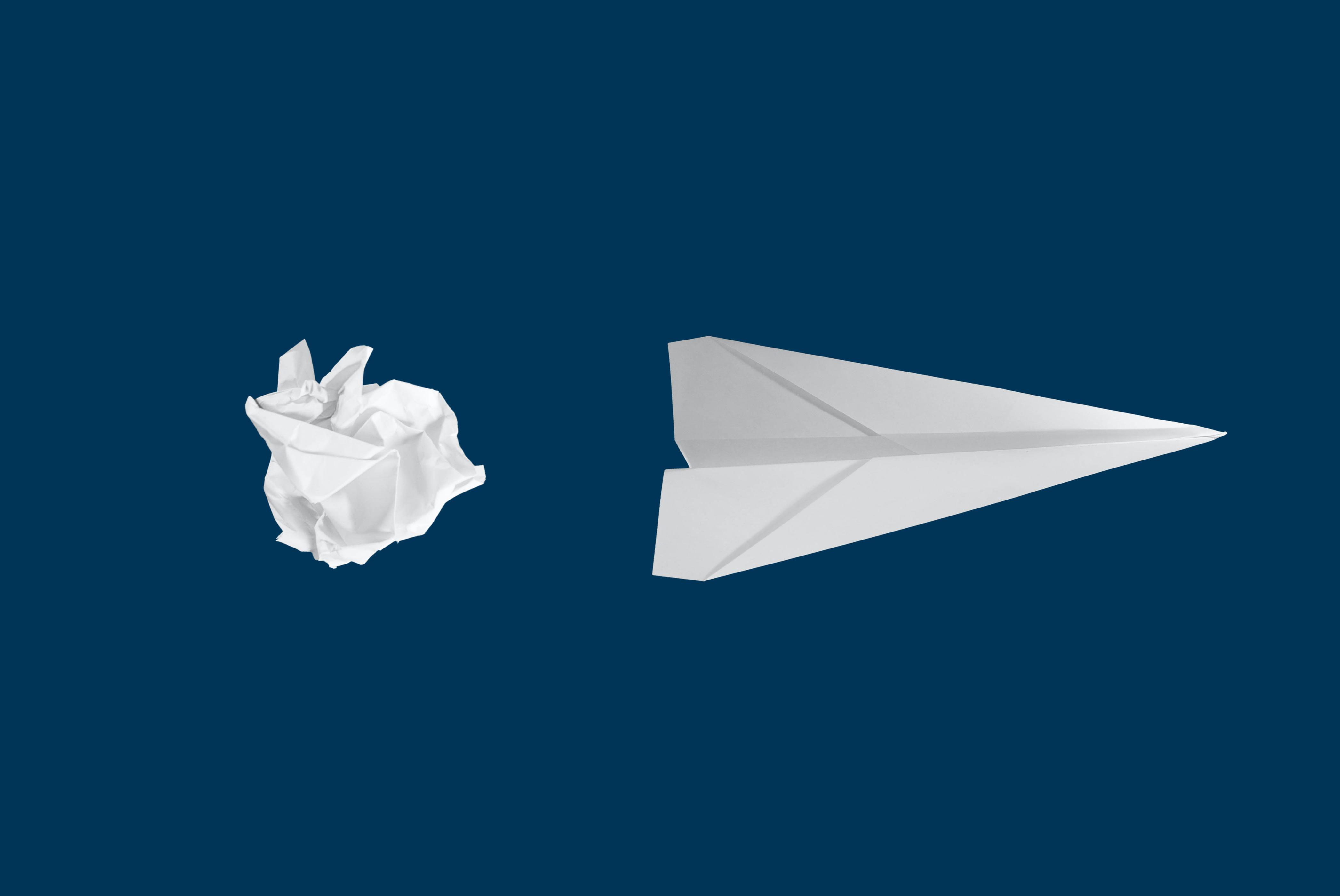
19 minute read
Change And Turning Covid-19 Into Opportunity Innovation As A Recipe For Overcoming Crises
Aleksandar Vekić Assistant Master Faculty of Technical Sciences Novi Sad Department for Industrial Engineering and Management
INNOVATION AS A RECIPE FOR OVERCOMING CRISES AND THE KEY TO
Advertisement
POST-CRISIS GROWTH
Fostering innovation and change is one of the basic tasks of modern societies, as they can be the most effective response to crisis periods both in individual communities and societies, and on a global scale. Their special importance lies in creating conditions for post-crisis growth and development through the creation of opportunities to improve the business of companies and human lives. As innovation is emerging as a leading driver of competitiveness, economic dynamism and economic growth are at the center of economic changes caused by the “creative destruction” of the existing, which leads to the creation of new products and methods, as well as completely new markets [1].
Crises differ in many areas, amongst which are the factors causing them and the scope of their effects. The most prominent current global crisis, for instance, is at first a health crisis caused by the outbreak of COVID-19, but it is increasingly spilling over into the economy, leading to most projected growth plans and goals being called into question. Within the first weeks of the pandemic declaration by the World Health Organization (WHO), major changes already came to pass in the way of life in most countries, along with a slowdown of economic activity. This conditioned the creation of special policies aimed at mitigating the impact of this unprecedented crisis, causing an impact on the global economy in a short period of time and led to the creation of unforeseeable consequences. Some of the issues caused by the introduced changes are so big and harmful that they have surpassed in scope many of the problems that had previously occurred throughout history, especially since the existence of a market economy. Economists explain this crisis in terms of the “Black swan theory” which describes unexpected, disruptive events in history - like global pandemics, financial crises, and wars - that unsettle, uproot, and change governments A historic match between the world’s leading powers is currently being played, as they race against time to find an appropriate innovative solution, a cure that will quickly change everything, reverse negative trends towards positive ones and enable a gradual return of life to normal flows.
Even with all the almost superhuman efforts invested by scientists and researchers, and the vast financial resources allocated for these purposes, the process itself is not advancing nearly as fast as the world expects it to. Scientists and inventors are not only working to create a cure, but they are also creating favourable conditions for new business opportunities, investment, growth and employment. Based on this example, it can be seen and economies [2].
that continuous investment in science, technology and innovation is always a pledge for the future of humanity, and its progress in all areas. In the example of the current crisis, the speed of change in societies and economies is incredible: it is often necessary to make decisions based on very little information, and they are the result of previous experience and intuitive activities. Conditions are very difficult even for companies that are amongst the main carriers of innovation activities, and the consequences that the economic recession caused by COVID-19 leaves on their investment in R&D activities [3], and their ability to launch new products and services is difficult to predict. The negative repercussions are that many global companies have already announced their withdrawal from certain markets and have reduced their business activities, such as Zara, while a large number of them are facing bankruptcy, such as Pizza Hut or Hertz. It should be noted here that among the aggravating circumstances is the intensity of the crisis, which simultaneously affects all functions in companies. So far, the biggest negative effects have been observed in tourism, the aviation industry, the automotive industry, the hotel and restaurant industry, etc.
Innovative companies must rely heavily on available resources and modern technologies, which should enable their survival and further progress in these specific conditions. On this path they cannot stand alone, needing the strong support from economic policy makers in the form of adequate solutions and programs for preserving business activity, and post-crisis recovery based on further encouragement of innovation. These solutions must be efficient and adaptable enough to achieve positive effects. It can be said that the business of companies will be faced with a crucial decision to innovate or die. We should not forget that human creativity is boundless, and it is the main driver of innovation. Together with modern available technologies, a huge base of human knowledge and experience is a powerful engine for further development of mankind and industry. Despite all the current difficulties, the light at the end of the tunnel is noticeable and humanity should hope for a brighter future in which innovations will always amaze us. So, can you revive your innovative spirit and co-create a new reality, making the world an extraordinary place to live?
References:
[1] Schumpeter JA. The theory of economic development: an inquiry into profits, capital, credit, interest and the business cycle. Harvard Economic Studies, Vol. 46. Cambridge, MA: Harvard University Press; 1934
[2] Lovick S. How will innovation change society after this current crisis? [Internet]. Maddyness; 2020 Mar 30th. Available from: https://www.maddyness.com/uk/2020/03/30/how-willinnovation-change-society-after-this-current-crisis/
[3] Santiago F, Dachs B, Peters B. Foster recovery from COVID-19 through sciences, technology and innovation [Internet]. IAP Unido; 2020 May. Available from: https://iap.unido.org/articles/ foster-recoverycovid-19-through-science-technology-andinnovation
Dietrich Local Group Berlin
Rebekka Nagel
Local Group Dortmund SHAPE YOUR HABITS: LONG-TERM ONLINE LEARNING AS A CRISIS INNOVATION “... for my own habits, the program was the cue to actually start doing it and trying to do them daily..:”
Amidst the sea of terrible human and economic costs that a global crisis like COVID-19 brings with it, ESTIEMers have never once stopped to look into new ways to find opportunities and look for the silver linings in our misfortune.
Robin
Just like the ashes of a burned forest provide nutrients for a new generation to sprout, in the ruins of destroyed routines lay the possibility for new patterns of behaviour to flourish - if one takes the initiative to plant the seeds for them. loop.
It was in this spirit that the Shape Your Habits Online Training Program was called to life.
Why Study Habits?
According to the Cambridge Dictionary, a habit is an automated behaviour that you do often and regularly, sometimes without being aware that you are doing it. The Good: it worked for the people who stayed
virtuous cycles. They consist of four elements. After hearing a cue, let’s say the buzzing of a phone, we execute a certain routine e.g. reading a text message which we know will reward us for example with satisfying our curiosity. As the behaviour is repeated, the brain starts craving the reward not after performing the routine but already upon sensing the cue. As a result, the behaviour becomes automated.
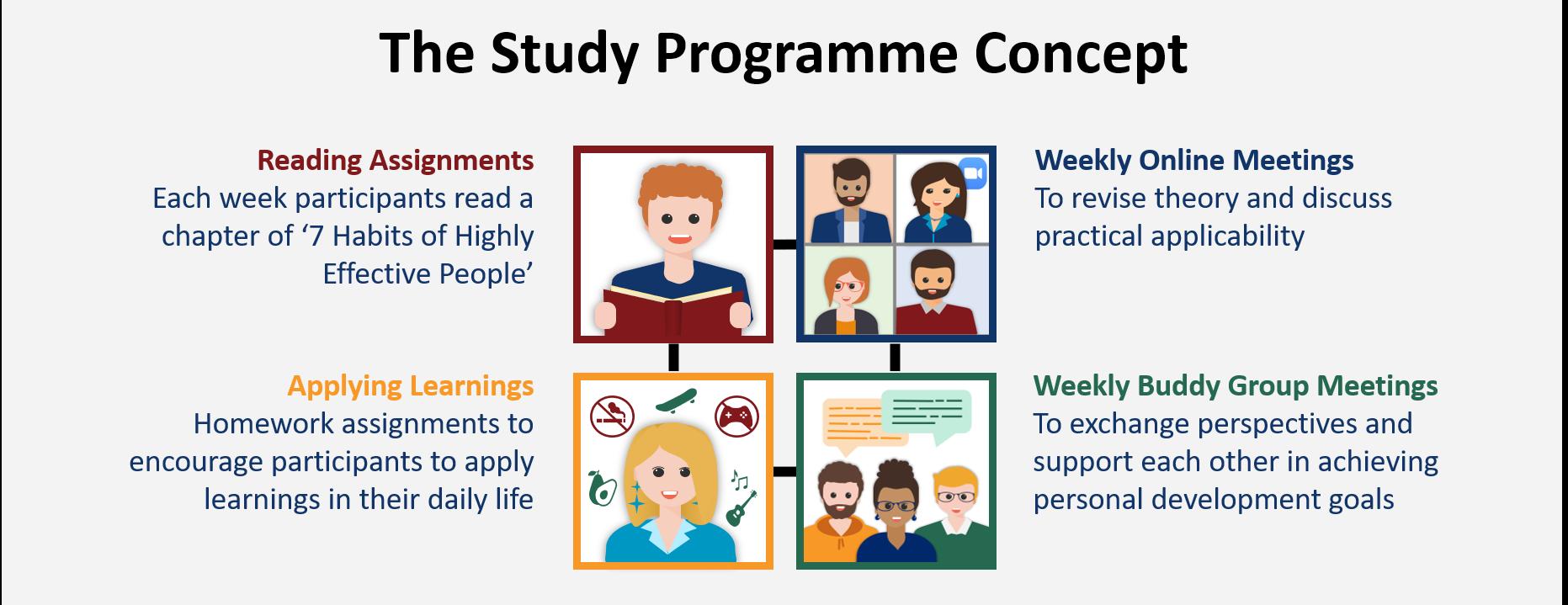
Habits are so powerful because they create subconscious cravings. A tiny act like switching the phone to silent mode can immensely increase our ability to focus simply by interrupting that habit

Outcomes
Habits, whether good or bad work like vicious or
From the outset, the program generated quite some interest, with twice as many people signing up than it was originally planned. The courses received mostly positive feedback, and, based on an informal survey conducted in the 9th of 12 weeks, most participants were able to positively influence their habits thanks to the program. It seems like the content was overall well received and helped the participants fulfill their goals.
“For my own habits, the program was the cue to actually start doing it and trying to do them daily. Now I read everyday, workout everyday, do some German everyday and journal everyday [...] Without the program, I would just read the book and without discussion and some exercises during the week it would not have as big of an influence on me.” - Irina Gromakovskaya, Local Group Minsk course, only about five people could be expected
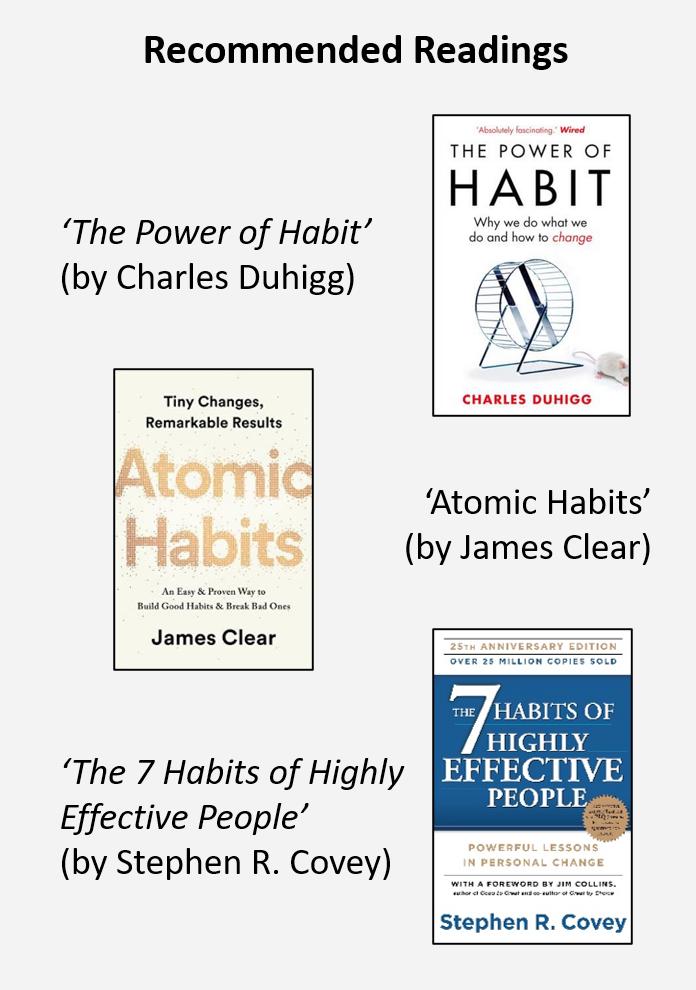
The bad: hemorrhaging participants over time
The most significant problem encountered during the program was the recurring absenteeism and progressive abandoning of the course by a large portion of the participants.
Part of the motivation for accepting 24 applicants, twice the amount of participants originally planned for, was that the trainers team expected a portion of them to drop out of the course eventually. It
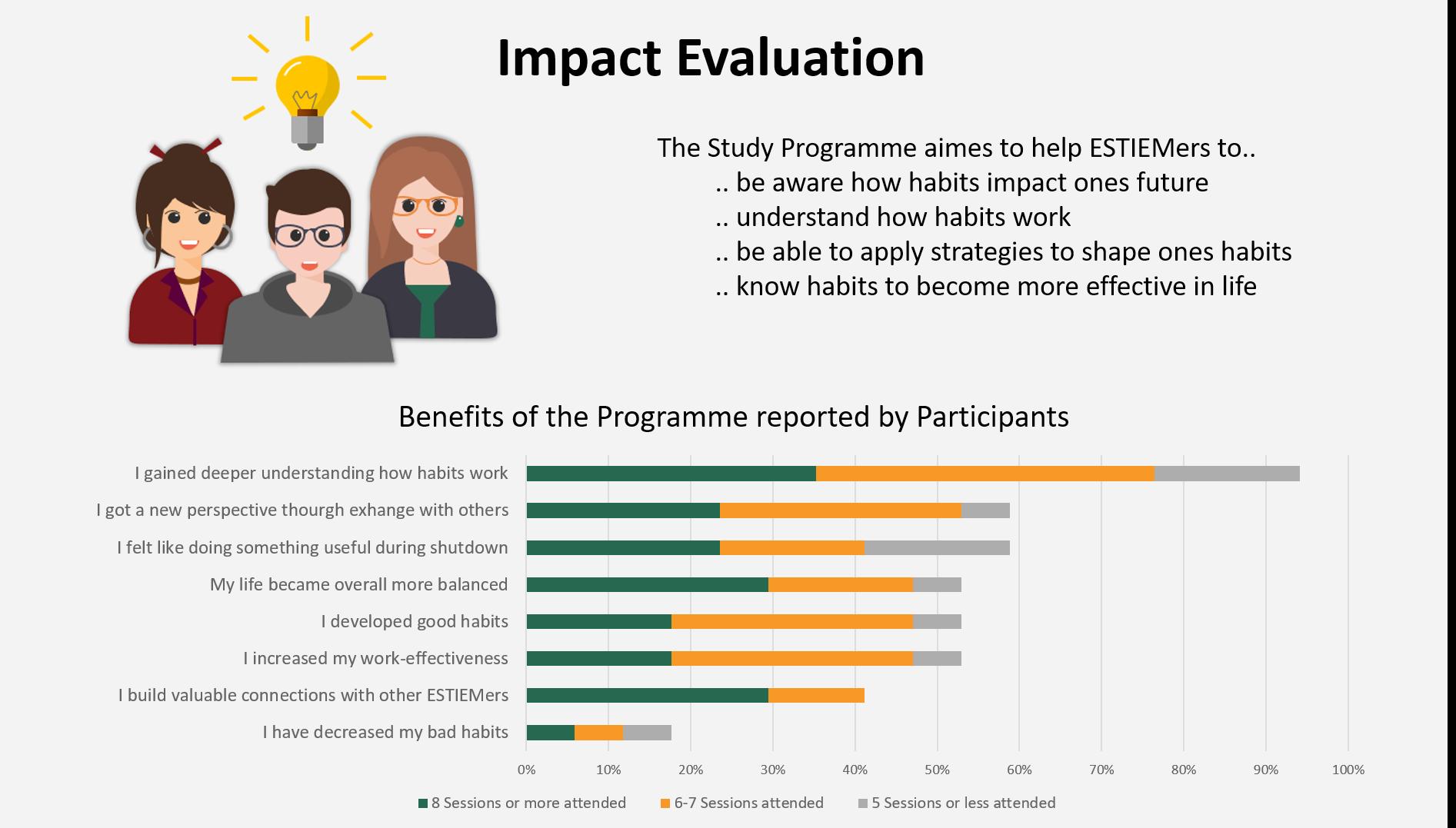
this would be true: towards the second half of the was however never anticipated to what degree
to participate in a week.
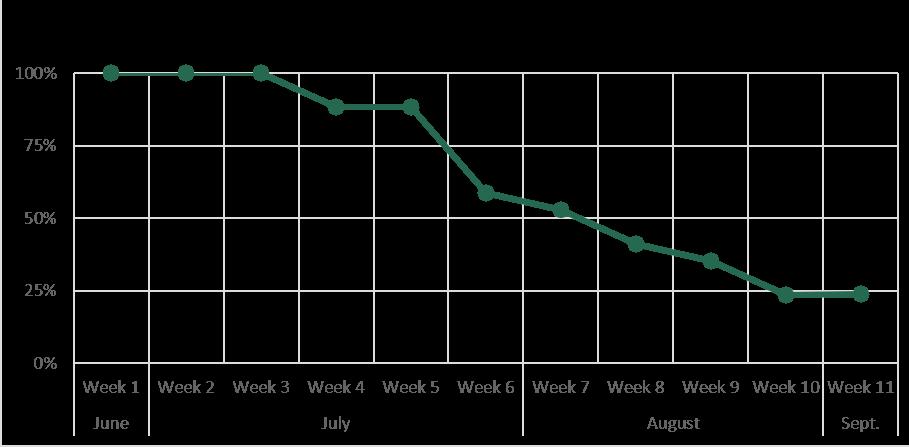
“About the period which is kinda 3 months, it seems long but it does not actually require much time as we have only a session per week. In my opinion, it’s really ok but it becomes difficult to continue (for many of the participants) for that long as different events come around. The academic hour is ok but the length can be rethought or redesigned to make it more productive and sustainable.” - Mohiuddin Resalat, LG Moscow
The PROmise
Low barriers to entry: anyone can take place from anywhere at no cost.
Time to learn: In the week between sessions, you can apply what you learned. Over multiple weeks habits can settle.
Self-directed learning: Study groups and optional homework empower the participants to share their knowledge and direct their own learning experience.
The PROblem
Low barrier to exit: The missing cost of entry also attracted participants who were not committed enough to the program to prioritise attendance.
3 months is a long time: Unforeseen obstacles made participants quit, even if they were committed. Also, not all participants started with the idea of attending the full course.
Optional options are too optional: The possibility to attend optional activities and organise studying in self-directed groups was used rarely by participants.
The PROposal
Be Flexible: Let a lot of people in, be ready to adapt to diminishing numbers. Provide exit and re-entry points to allow flexibility.
Break it down: Instead of making one long consecutive course, design the material to be modular and to allow people to join or leave later, without continuity problems.
Partial Supervision: Have the Buddy groups supervised by trainers for at least the first instances, or assign responsibility for them to individuals rather than groups.
Lessons for The future of Long online Events come to form a recurring event type in ESTIEM,
in ESTIEM
Based on the generally positive feedback from the participants, the concept of prolonged events aiming at gaining skills that take time to learn still show a lot of promise. In keeping with the spirit of renewal mentioned in
From the outset, the course was designed with the idea in mind that some of its participants would hopefully end up acting as trainers in the next edition of the program. Some particularly enthusiastic participants have expressed interest In the future, courses like “shape your habits” may and expand their focus on any possible range of topics, as long as there are books out there that can be used as a basis for them.
already. the introduction to this article, there is hope that the harsh conditions of the past months can leave a new offering for ESTIEMers as a lasting legacy, and ultimately lead to positive changes in their lives.
How often did we take part in the following activities?
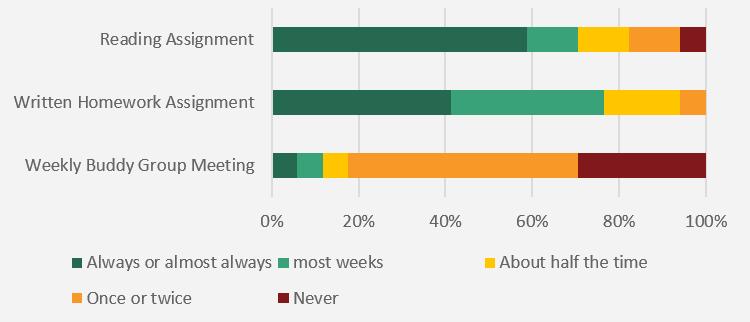
LEAN ENGINEERING EDUCATION: A MUST FOR INDUSTRIAL ENGINEERING
This short paper briefly presents the Lean production concept, its origins and the need for Industrial Engineering and Management (IEM) students to learn Lean. Lean Engineering Education (LEE) is presented as well the competencies pulled by LEE. The most adequate learning methodologies used to teach Lean are referred. Finally, the paper highlights the importance of learning Lean for IEM students.
What is Lean Production and when did it emerge?
Lean Production Systems was the name given by Krafcik (1988) to the Toyota Production Systems (TPS) in the late 80s. Toyota made a shift from textile machines to automobile production in a successful way by adopting some of Ford’s production system elements and innovating in others. TPS was “doing more with less” with less meaning less development time, less human effort, less goods in stock, less of everything, according to Womack et al. (1990). At the same time, it used more suggestions given by employees, (LT) principles (Womack and Jones, 1996).
more teamwork, more creativity and continuous of excellence and curriculum designs to provide
improvement mind-set.
The TPS represented a “turning point” in the culture of factory production models, following a distinctive path from the traditional Ford model, it directed employee behavior into new and different attitudes and routines, involving competencies such as systemic and ethical thinking. Many different perspectives contributed to the success and knowledge of TPS (Imai, 1986; Monden, 1998; Ohno, 1988; Shingo, 1989; Sugimori et al., 1977). “Making people before making products” is the TPS education model basis (Suzaki, 1993) that emerged from the need to adapt the learning process to new demands, which were a result of a change in the industrial production culture. Toyota exists within the factory in all activities at all levels. highlights the need to educate engineering students, namely, IEM students, in Lean Thinking Competencies pulled by LEE are whole-system thinking, sustainability and ethics competencies (Alves, Flumerfelt and Kahlen, 2017; Alves, 2018, 2019). Black and Phillips (2013) defined Lean Engineer as: “The Lean Engineer (LE), has an Industrial Engineering foundation, enhanced with lean tools, six sigma capability and a lean to green outlook to take the plant to zero waste going to the landfill.” To create this engineer profile, it is necessary to equip the students with Lean competencies, as the ones presented above.
Some authors are working in creating centers Education Model (TEM) is a learning system that
students with Lean competencies suitable for Industry 4.0 (Enke et al., 2018; Dombrowski, Wullbrandt and Fochler, 2019). Learning factories, Project-Based Learning, experiential learning, serious games, hands-on, among others are useful active learning methodologies to learn Lean (Goerke et al., 2015; Abele et al., 2017; Alves et al., 2017; Bauer et al., 2018; Enke et al., 2018; Abele, Metternich and Tisch, 2019; Garay-Rondero, Rodríguez Calvo and Salinas-Navarro, 2019; Gento, Pimentel and Pascual, 2020; Pascual et al., 2020; Tan et al., 2020). Consequently, teachers should teach Lean, not just as a “program”, but as a philosophy of life (Alves et al. 2020).
Why is it important to learn Lean?
What is Lean Engineering Education and how do students learn Lean?
The TEM is also the basis of Lean Engineering Education (LEE) (Flumerfelt et al., 2015) that Lean Thinking principles are aligned with logistics, ergonomics, coaching, leadership, project management, product development, systematic innovation (TRIZ), six sigma, among others, thus allowing processes improvement
Anabela Carvalho Alves Department of Production and Systems, School of Engineering, University of Minho

of such functions and having synergies when combined. Also, it could be applied in goods and/ or services companies, large or SME (e.g. office, textile, healthcare, hotels, schools, courts…) (Alves, Flumerfelt and Kahlen, 2017). Thus, companies are applying Lean in their processes to obtain economic, social and environmental benefits (Maia, Alves and Leão, 2013; Sanidas and Shin, 2017; Amaro, Alves and Sousa, 2019).

A Lean holistic approach in the organizations will contribute to the implementation success of Industry 4.0 (Bittencourt et al., 2019).
A more sustainable production and consumption is also obtained by applying LT principles. This application of LT, in order to obtain a better environmental performance, is called by many authors as Lean-Green synergy (Abreu, Alves and Moreira, 2017). Lean, indeed, promotes a global sustainable development (Alves et al. 2019), being this recognized even by people outside of the IEM field. For instance, Bea Johnson (2013), inspired by “zero waste” policy, launched an excellent book about how people can have a waste-free lifestyle. She implied in her book that the more we have, the more we spend. Many times this is due to the producer that “forces” their clients to buy more by offering promotions and discount quantities. Additionally, if they think someone else is paying, people tend to spend more because “it is not from my pocket” mentality, for example, in hotels. However, this behavior could happen in big companies too as the case described in Dias et al. (2019), where with a new product introduction, new equipment was bought and the “old” was discarded, not reused. Womack and Jones in their book “Lean solutions” (Womack and Jones 2005) discussed how customers and providers should work together to create value and eliminate waste. This calls for new sustainable business models. Conclusion
With this article, the author hopes to inspire IEM students to learn Lean or, at least, to stimulate students’ curiosity to further research literature on this important philosophy. Lean is not just a program or a cost-cutting exercise, it is a way of life. These few words should be understood only as the tip of the iceberg.
References:

Abele, E. et al. (2017) ‘Learning factories for future oriented research and education in manufacturing’, CIRP Annals, 66(2), pp. 803–826. doi: 10.1016/j.cirp.2017.05.005. Abele, E., Metternich, J. and Tisch, M. (2019) Learning Factories. Cham: Springer International Publishing. doi: 10.1007/978-3-319-92261-4. Abreu, M. F., Alves, A. C. and Moreira, F. (2017) ‘Lean-Green models for eco-efficient and sustainable production’, Energy, 137, pp. 846–853. doi: 10.1016/j.energy.2017.04.016. Alves, A. C. et al. (2017) ‘Effective Tools to Learn Lean Thinking and Gather Together Academic and Practice Communities’, in Volume 5: Education and Globalization. ASME, p. V005T06A009. doi: 10.1115/IMECE2017-71339. Alves, A. C. (2018) ‘Lean Education: provider of system-thinking, ethics and sustainability competencies’, in 4th edition 2018 - 11th EPIEM Conference on Innovation and Sustainability 2018. Bucharest, Romania, 26/27 October 2018. Available at: http://innovation.pub.ro/ archive/2018.pdf. Alves, A. C. (2019) ‘Competencies driven by Lean Education: System-thinking, sustainability and ethics’, in International Symposium on Project Approaches in Engineering Education, pp. 710–713. Alves, A. C. et al. (2019) Lean Engineering for Global Development. Edited by A. C. Alves et al. Cham: Springer International Publishing. doi: 10.1007/978-3-030-13515-7. Alves, A. C. et al. (2020) ‘The knowledge and importance of Lean Education based on academics’ perspectives: an exploratory study’, Production Planning & Control, pp. 1–14. doi: 10.1080/09537287.2020.1742371. Alves, Anabela C., Flumerfelt, S. and Kahlen, F.-J. (2017) ‘Introduction’, in Lean Education: An Overview of Current Issues. Cham: Springer International Publishing, pp. 1–23. doi: 10.1007/978-3-319-45830-4_1. Alves, A.C., Flumerfelt, S. and Kahlen, F.-J. (2017) Lean Education: An Overview of Current Issues, Lean Education: An Overview of Current Issues. Edited by Anabela Carvalho Alves, Shannon Flumerfelt, and Franz-Josef Kahlen. Cham: Springer International Publishing. doi: 10.1007/978-3319-45830-4. Amaro, P., Alves, A. C. and Sousa, R. M. (2019) ‘Lean Thinking: A Transversal and Global Management Philosophy to Achieve Sustainability Benefits’, in Lean Engineering for Global Development. Cham: Springer International Publishing, pp. 1–31. doi: 10.1007/978-3-030-13515-7_1. Bauer, H. et al. (2018) ‘Integration of Industrie 4.0 in Lean Manufacturing Learning Factories’, Procedia Manufacturing, 23, pp. 147–152. doi: 10.1016/j.promfg.2018.04.008. Bittencourt, V. et al. (2019) ‘Contributions of Lean Thinking Principles to Foster Industry 4.0 and Sustainable Development Goals’, in Lean Engineering for Global Development. Cham: Springer International Publishing, pp. 129–159. doi: 10.1007/978-3-030-13515-7_5. Black, J. T. and Phillips, D. T. (2013) Lean Engineering The Future Has Arrived. Virtualbookworm.com Publishing. Dias, M. et al. (2019) ‘Reusing Equipment in Cells Reconfiguration for a Lean and Sustainable Production’, Procedia Manufacturing (25th International Conference on Production Research Manufacturing Innovation: Cyber Physical Manufacturing). Chicago, Illinois (USA), In Press. Dombrowski, U., Wullbrandt, J. and Fochler, S. (2019) ‘Center of Excellence for Lean Enterprise 4.0’, in Procedia Manufacturing. doi: 10.1016/j. promfg.2019.03.011. Enke, J. et al. (2018) ‘Industrie 4.0 - Competencies for a modern production system: A curriculum for Learning Factories’, in Procedia Manufacturing. doi: 10.1016/j.promfg.2018.04.028. Flumerfelt, S. et al. (2015) Lean Engineering Education: Driving Content and Competency Mastery. ASME Press. Garay-Rondero, C. L., Rodríguez Calvo, E. Z. and Salinas-Navarro, D. E. (2019) ‘Experiential learning at Lean-Thinking-Learning Space’, International Journal on Interactive Design and Manufacturing (IJIDeM), 13(3), pp. 1129–1144. doi: 10.1007/s12008-019-00578-3. Gento, A. M., Pimentel, C. and Pascual, J. A. (2020) ‘Lean school: an example of industry-university collaboration’, Production Planning & Control, pp. 1–16. doi: 10.1080/09537287.2020.1742373. Goerke, M. et al. (2015) ‘Holistic Approach of Lean Thinking in Learning Factories’, Procedia CIRP, 32, pp. 138–143. doi: 10.1016/j. procir.2015.02.221. Imai, M. (1986) Kaizen: The Key to Japan’s Competitive Success. McGraw-Hill. Johnson, B. (2013) Simplify Your Life by Reducing Your Waste: ZERO WASTE HOME. Scribner. Krafcik, J. F. (1988) ‘Triumph of the Lean Production System’, Sloan Management Review, 30(1), pp. 41–52. Maia, L. C., Alves, A. C. and Leão, C. P. (2013) ‘Sustainable work environment with lean production in textile and clothing industry’, International Journal of Industrial Engineering and Management, 4(3). Monden, Y. (1998) Toyota Production System: An Integrated Approach to Just-In-Time. Third. Engineering and Management Press. Ohno, T. (1988) Toyota Production System: beyond large-scale production. Portland: Productivity Press. Pascual, J. A. et al. (2020) ‘A Learning Factory for Remanufacturing: A New Configuration at Valladolid Lean School’, in Proceedings of 6th European Lean Educator Conference (ELEC2019). Springer International Publishing. S. Shingo (1989) ‘A study of Toyota Production System from an Industrial Engineering’. Sanidas, E. and Shin, W. (2017) ‘Lean Production System and Economic Development across the World Today’, International Journal of Economics & Management Sciences, 06(06). doi: 10.4172/2162-6359.1000480. Sugimori, Y. et al. (1977) ‘Toyota production system and Kanban system Materialization of just-in- time and respect-for-human system’, International Journal of Production Research, 15(6), pp. 553–564. doi: 10.1080/00207547708943149. Suzaki, K. (1993) The new shop floor management: empowering people for continuous improvement. Tan, H.-S. et al. (2020) ‘Conceptual development of learning factory for industrial engineering education in Indonesia context as an enabler of students’ competencies in industry 4.0 era’, IOP Conference Series: Earth and Environmental Science, 426, p. 012123. doi: 10.1088/17551315/426/1/012123. Womack, J. P., Jones, D. T., and Roos, D. (1990) The Machine that changed the world. New York: Rawson Associates. Womack, J. and Jones, D. T. (1996) ‘Lean Thinking: Banish Waste And Create Wealth In Your Corporation’, Siman & Schuster, New York, USA. Womack, J. and Jones, D. T. (2005) Lean Solutions: How companies and Customers can create value and wealth together. New York, USA.: Siman & Schuster.