ASPE
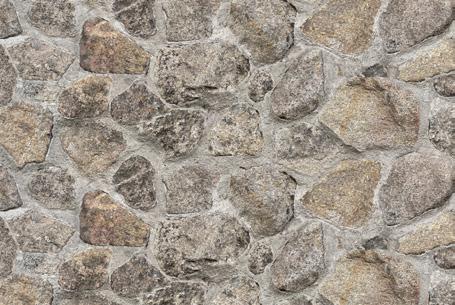
BOARD
2022 - 2023 President
M.
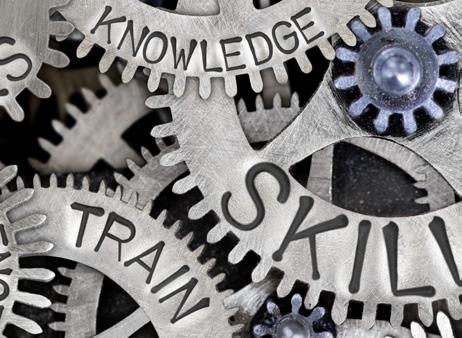
First
Second
Immediate
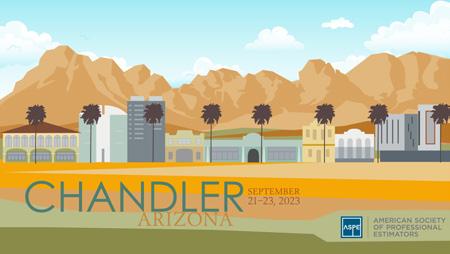
BOARD
2022 - 2023 President
M.
First
Second
Immediate
Assumingthe tech gods smile on us, our new website should be up and running by the time you are reading this. Kudos to Tina Cooke, Natasha Crumbliss, and Joanne Warren for all their work in making this happen!
ASPE has always emphasized our educational and certification programs, but we have not recently discussed another important aspect of being a member – leadership. We offer great opportunities for you to develop skills in leadership through participation as an officer, board member, or committee member in your chapter. Chapter elections are being held this spring, and so many positions end up unfilled.
As Colin Powell once said, “Leadership is all about people. It is not about organizations. It is not about strategies. It is all about people motivating people to get the job done.” This is your opportunity to step up, contribute to your chapter, and start to or continue to develop your leadership skills. Please consider becoming a leader in your chapter!
Finally, as always, please feel free to contact me or any board member if you have any questions or suggestions on how we can improve our Society. Thank you for your continued support of ASPE!
Taylor Dow
Rachel Sanders
Leon Benham
Drew Dines
Tyler Gilbert
Christopher Horrocks
John "Clark" Benson
Jason Lee
Kim Ume
Donald Grant
Dean VanLith
Javier Gaitan
Robert Dyer
Tyler Crouch
Mike Moore
Mark Dade
Charles Campbell
Baxter Horton
Ryan Engdahl
Jimmie Hampton
Ashley Evans
Bryan Riehle
Robert Van Heyde
Henry Frondorf
Matt Kohls
Sandra Lucero
Walter Miller
Jeremie Elsey
Jorge Jaramillo
Mariana Maldonado
Nanette Giron
Sameer Siddiqui
Philip Tenorio
Roger Hein
Giocondo De Filippis
Jeff Peterson
Prince Winston
Wayne Birch
Sofia Covelli
Ivan Schmidt
Daniel Cervantes
Nolan Johnson
Matt Angelucci
Nicholas Peetros
Theodore Baumgardner
Syed H. Abbas
Daniel Tompos
John Childs
Dominic Papa
Jordan Landreman
Shane Steele
Russell Whitworth
Aaron Schoenthaler
Tyler McCann
Caleb Jones
Rachel Comerford
Stuart Hoyer
Howard Wheeler, II
Robert Castro
Michael Chaffin
The Austin Company
Leon Benham
New Millennium
ProCraft Mechanical
AR Mays Construction
Agate Construction
Lloyd Construction Company
Privent Construction
Ujamaa Construction
Dynamic Glass LLC
Rocksolid General Contractors Inc.
Dyer Insulations Inc
Tyler Crouch
Baldwin & Shell Construction Co.
Baldwin & Shell Construction Co.
Baldwin & Shell Construction Co.
Baldwin & Shell Construction Co.
Baldwin & Shell Construction Co.
Batten & Shaw, Inc.
Al Neyer
Silver Hills Construction
Prus Construction Co.
RJ Beischel Building Company
Builders Source
Terracon Consultants, Inc.
RedCap Staffing
Fulcrum Contracting Group, LLC
Fulcrum Contracting Group, LLC
University of Texas at El Paso
Defacto Consulting Group, Inc.
Missions Construction
nStone Corporation
Greenstone Construction LLC
nStone Corporation
State of Florida
Construction Management Ser.
Anser Advisory
JR Merit, Inc.
Derivi Castellanos Architects
A/Z Corporation
McCloskey Mechanical Contr.
Clemens Construction Company
Thomas Jefferson University
Weitz Industrial
Lighting Solutions
GFP Cement Contractors
J.H. Findorff & Son Inc
WIlloughby Robinson Associates
GW Builders LLC
Garver
Stellar
Chris-Tel Construction
Chris-Tel
Chris-Tel
ASPE has a new online look! I am very pleased to announce that ASPE has launched a redesigned website (www.aspenational.org). The site is organized around our new tagline—Learn. Certify. Join. to clearly reflect ASPE’s value proposition and the “three steps” to estimating success:
Learn – enroll in the ASPE Estimating Academy, an essential online training resource that focuses on the core competencies necessary for a beginning estimator.
Certify – more experienced estimators can test and validate their skills with our benchmark certification options: Associate Estimating Professional (AEP) and Certified Professional Estimator (CPE).
Join – unlock access to thousands of experienced estimators to grow your professional network and career through ASPE membership.
The website redesign is part of an overall effort to increase awareness of all ASPE has to offer as the industry’s leader and recognized authority in professional estimating. You are invited to visit and explore the new site.
We are also excited to announce that registration is open for ASPE Summit 2023 (September 21 – 23) at the beautiful Crowne Plaza –Chandler Golf Resort in Chandler, AZ (just outside of Phoenix). The Summit Planning Committee has developed an outstanding lineup of presentations on a variety of industry topics, as well as ample time for networking with your colleagues from across the country. It’s never too early to register. I look forward to seeing you there!
Please feel free to reach out anytime with your ideas and input— I’d love to hear from you.
The American Society of Professional Estimators Governance Committee calls attention to your duty as a member in good standing of the Society to nominate those individuals who are qualified, willing to serve, and capable of being an officer and a director to establish policy and conduct national business.
The positions to be filled for two‐year terms beginning January 1, 2024, are as follows:
• National President
• National First Vice President
• National Second Vice President
• Northeast Regional Governor
• Central Plains Regional Governor
• Southwest Regional Governor
Nomination forms are available on the ASPE website: ( https://www.aspenational.org/page/BODRoles)
This form must be completed in full and certified by the nominator's Chapter Nominations Committee Chairman or the Chapter President.
If the nomination is a MAL, the form must be certified by the Governor of the nominator's region.
The nomination must also be accepted by the person being nominated and the associated fact sheet completed by him/her.
The form must be received no later than 11:59 p.m. PST on Monday, June 12, 2023.
Please submit nominations and questions to Executive Director Joanne Warren, Jwarren@aspenational.org
Mark your calendar to join your friends and colleagues at the beautiful Crowne Plaza – Chandler Golf Resort (Chandler is just outside of Phoenix) on September 21 – 23 for ASPE Summit 2023!
$1,095 in-person early registration
$1,195 in-person late registration
$550 virtual early registration
$650 virtual late registration
$225 guest ticket
Join colleagues from across the country with diverse estimating backgrounds as Summit takes us through presentations ranging from preconstruction, risk, value engineering, and more. Also enjoy the time to network and fellowship with other professionals and sponsors.
• The Art and Science of Risk in Estimating
• Construction Economic Forecast Models - Trends and Risks
• How to Estimate for Risk and Improvement
• Value Engineering in Estimating
• Building Relationships During the Preconstruction Phase
• The Competitive Edge in Preconstruction
• And More!
If you ask my 13-year-old son, he will tell you that he already knows everything. I've quizzed him thoroughly on random occasions and surprise surprise, he doesn’t. I thought I knew everything as well. I hate to admit it but this train of thought continued a bit too far into my twenties. While my emotionally immature type-A man brain still trips me up at times, I do my best to learn something new every day. Eventually one day I had the benefit of a company owner I worked for offering to pay for a continuing ed course in Business Management. My 27-year-old self thought "I'm already further along than most in my field, what do I need to know?". In retrospect, I have wanted to smack my younger arrogant self on the side of the head for many reasons, but primarily for thinking this way, that I had nothing left to learn.
So, I took the course, and it wasn’t necessarily the course material that was eye-opening but rather the instructor's knowledge and my fellow students' knowledge. My younger know-it-all self was learning along people two and three times my senior—CEOs, VPs of major corporations—and it was immediately humbling. I learned more from my classmates than anything else. I learned that I don't know everything and most importantly I learned that I never will. I remember listening to my classmates, ACTUAL titans of industry, asking for help, seeking to learn. I thought to myself well hell, if they can keep an open mind to learning every day, then I should as well if I want to be successful personally and professionally.
I started offering estimating training a few years back and I have learned more than I have taught. It's easy to know about something, it can be very difficult to teach what you know to someone else. Since we have offered classes, we have had the benefit of teaching nationwide to a variety of contractors, owners, and design professionals and in doing so, it made us better at our job. It has taught us how others think and how that should affect how we think about not only our role in the food chain but all roles.
The long and short of it is that learning something new every day, even a trivial fact or a seemingly menial task is important for personal growth. For professional growth, it is important to keep taking classes to gain the required knowledge to stay abreast of how the world is evolving. It helps us in our jobs and I've noticed that the real benefit is that it helps us grow as a human, and this comes more from the interaction with other professionals. As an employer of others, I was able to return the favor recently and send
our head of Business Development back to school. She is deeply invested in advanced business strategy courses at the University of Virginia. The investment in her financially will have a ten-fold benefit, not only to our company but to her personally. When you learn new things, you gain confidence, which trickles down to all areas of your life. It's a win-win all around for a minimal investment of time and money.
My point of all this is that continuing education is paramount. As a business owner, investing in your employees often leads to benefits for you but on a higher philanthropic level, investing in others benefits humanity as a whole, as sappy as that may sound.
If you are an industry professional, I implore you to teach. We need more teachers. We need the next generation to learn not only professional skills but life skills from those that have been there and done that. I learn something new every time I teach…a new way of doing something, a better way of thinking about something. I learn something new every time I take a continuing education course, and that is mostly from my fellow students. Continuing education benefits us all for many reasons beyond the syllabus.
Robert W. Peppel, CPE
Robert W. Peppel CPE passed away on November 5, 2022 at the age of 81. Robert joined ASPE Chapter 14 (Atlanta) in 1996. He received his CPE in 2001 and attained CPE, Lifetime status in 2017. ASPE salutes this longtime member.
Michael (Mike) D. Luke
Michael D. Luke, formerly a member of ASPE Chapter 51, Great Salt Lake, passed away unexpectedly on December 15, 2022, at the age of 66. Mike served ASPE as a regional governor and supported the organization through generous monetary donations. He will be missed by many.
Anser Advisory is a national capital project and advisory consulting firm offering tailored, creative solutions to an exciting range of public and private sector clients. Our services cover the entire lifecycle of capital development, starting with early-stage project readiness and continuing through to marketing successful execution.
Our diverse and talented team of 800+ professionals includes architects, engineers, project managers, inspectors, ESTIMATORS , certified professional accountants, financial analysts, and more.
“Our business exists as a combination of the individual and diverse backgrounds and talents of each of our employees. One of our founding core values is to foster diversity, equity, and inclusion in our organization…We embrace what makes us unique and foster creativity, agility, and innovation to Deliver Excellent Results for our Clients and Community.
- Bryan Carruthers, Chief Executive OfficerThe purpose of this Technical Paper is to illustrate how to estimate the cost of Adhered Manufactured Stone Veneer (AMSV). The task of calculating the price of AMSV requires an understanding of an AMSV system and the estimating process. In subsequent sections, this Technical Paper will outline technical and trade information associated with AMSV, summarize estimating process, and explain how the interpretation of technical information facilitates a mechanism to calculate the cost of an AMSV system.
National Concrete Masonry Association (2020) defines AMSV as a “lightweight, architectural, non-load-bearing product that is manufactured by wet cast blending of cementitious materials and aggregates, with or without pigments, admixtures, or other materials to simulate the appearance of natural stone and other masonry materials” (p. 4).
AMSV is an economical alternative to natural stone veneers. Natural stone procurement is limited to local quarries, while its considerable weight precludes shipping over long distances and requires a cumbersome installation process. AMSV capitalizes on natural stone's physical appearance while eliminating its drawbacks. AMSV's wet-cast process is an inexpensive production method, while its lightweight composition allows simplified installation and competitive shipping costs.
C1780) have not been published until 2013 and 2017, respectively (Bradfield, Lang, 2017).
However, AMSV is a relatively recent product. Although it was first designed in 1962 by Garrett and Floyd Brown (Lograsso, 2020), the set of standards that guide the minimum physical properties of AMSV (ASTM C1670/C1670M) and its installation instructions (ASTM C1780) have not been published until 2013 and 2017, respectively (Bradfield, Lang, 2017). Table 1 provides a brief overview of AMSV physical characteristics as required by ASTM C1670. Installation Guide and Design Options for Compliance with ASTM C1780 by NCMA outlines the requirements of ASTM C1780.
Table 1 provides a brief overview of AMSV physical characteristics as required by ASTM
C1670. Installation Guide and Design Options for Compliance with ASTM C1780 by NCMA outlines the requirements of ASTM C1780.
Table 1
Summary of ASTM C1670/C1670M Physical Requirements
Property
Compressive Strength –concrete mix tested
Freeze-Thaw – concrete mix tested
Linear Drying Shrinkage – concrete mix tested
Test Method Requirement
ASTM C39/C39M (cylinders)
ASTM C666/C666M
Procedure A (modified to be percent mass loss)
At least 2,100 psi (14.5 MPa) average, with no individual specimen testing lower than 1,800 psi (12.4 MPa)
1.5% mass loss maximum for each of five tested specimens after 50 cycles of testing and no disintegration
ASTM C157/C157M 0.10% maximum length change
Shear Bond – unit tested ASTM C482 50 psi (350 kPa) minimum
Weight per Square Foot – unit tested
ASTM C140/C140M (modified calculations) 15 lb/ft2 maximum
Thus, ASTM C1670 and ASTM C1780 form the technical and trade-associated information necessary to estimate the cost of AMSV.
Thus, ASTM C1670 and ASTM C1780 form the technical and trade-associated information necessary to estimate the cost of AMSV.
Estimating process is the identification, quantification, and analysis of data to produce a likely cost of resources vital to complete a task (Cost Engineering Consultancy, 2020). Woolsey
Estimating process is the identification, quantification, and analysis of data to produce a likely cost of resources vital to complete a task (Cost Engineering Consultancy, 2020). Woolsey (2017) segments the estimating process into five essential functions:
• Identification of scope
• Quantification of scope
• Application of unit costs to scope
• Aggregation of costs
• Analysis
The first function, the process of identifying the scope, involves reviewing construction documents or verbal directives. Woolsey (2017) explains that “estimating begins with a thorough understanding (and visualization) of the project’s scope of work” (para. 1). Visualization is the fundamental requirement of the identification of scope. An estimator should attempt to answer as many questions as possible to develop a mental image of the scope of AMSV. Often, plans merely outline the proposed final condition. Therefore, an estimator must visualize the sequence of events necessary to transform existing conditions from their current state to a state that reflects the proposed design. At this stage, an estimator must understand how existing conditions affect the proposed scope to form a complete understanding of the project
After identifying the scope, the next step is to quantify it. The process of quantifying scope occurs through take-offs. Notably, the take-off process can co-occur during the scope identification function or separately, as preferred by an estimator. Take-offs can be derived from plans (hard copy or electronic format) or by visiting the jobsite. A digitizer, a scale ruler, and measuring tape are tools that allow the estimator to take off hard copy plans.
The estimator can use any estimating software or the measuring tool of Adobe Acrobat to take off digital format plans. Rarely, hard copy or digital plans may be unavailable and physical objects may be used for takeoff using standard tools like measuring tape, measuring wheel, or laser distance meter. Regardless of the preferred take-off method, the estimator needs to quantify
each component of an AMSV system. Another aspect to consider during the quantification of scope is that an estimator should use correct units of measurement (UOM). The following list outlines the common UOM of an AMSV system:
• AMSV unit, sealer, mortar setting bed, and Water Resistive Barrier (WRB) – SF.
• Outside corners and accent (sill and wall caps), weep screed, flashing, and casing bead – LF.
• Scratch coat and lath – SY.
• Upon completion of scope take-off, the estimator should record quantities for future reference and recordkeeping. These take-offs will be the basis of assigning unit costs to scope.
Construction waste factor is a contingency added to material take-off to compensate for overages resulting from field installation methods, manufacturing defects, and shipping damage. Ultimately, an estimator should identify the exact amount of waste. For example, installing a 20”-long sill over a 24”-long area will require installing one sill and field-cutting the second sill to fit the remaining distance. Likewise, lath and WRB need an overlap for proper installation. Occasionally a precise calculation is impractical with AMSV as AMSV units come in various lengths and heights. A rule of thumb is to include 1015% of waste on all ordered materials.
Suppliers sell materials packaged in specific quantities. For example, AMSV suppliers sell AMSV in large and small boxes. Some manufacturers sell large and small boxes that contain 110 SF and 8 SF of AMSV, respectively. Furthermore, suppliers sell lath in sheets and WRB in rolls. Mortar powder is sold in bags but is mixed with water to produce the final product. The amount of mortar necessary on a project depends on the amount of AMSV and the specified grouting technique. Figure 1 showcases grouting techniques for AMSV.
The optimum temperature range for installation of AMSV is between 40°F (4°C) and 90°F (32°C). If the temperature is outside of this range at the installation time, the estimator should account for unique installation procedures like heated enclosures or a delayed AMSV installation.
After quantifying the scope, the estimator needs to assign prices to take-offs. This function implies that the estimator needs to set the financial value to materials, labor, equipment, and indirect costs.
Note. Three popular grouting techniques for use with Adhered Manufactured Stone Veneer. From Finishing Details, by Eldorado Stone, 2008 (http://www.eldoradostone.com)
Every drawing should reference the correct scale, but sometimes plans may reference the wrong scale. A prudent estimator will confirm the accuracy of scale in both directions: horizontal and vertical. This verification is essential to ensure that the architect referenced the proper scale and that the printed drawing or saved file is correct.
Construction documents are a two-dimensional representation of a three-dimensional product. The estimator must use their experience to read plans accurately. For example, an oblique wall may not scale correctly on an elevation, which would skew the measurement.
Extended shipping to a project in a remote location may result in additional product damage. The estimator may hedge this risk by increasing the waste factor or include
Although a typical set of construction documents should reference the required AMSV system, the novelty of AMSV regulations may result in partial and even erroneous design, especially during preliminary design stages. The experienced estimator must know every component of an AMSV system, its function, and its application. For this reason, the following list outlines nine primary components of an AMSV wall system with a brief description of their purpose within the system:
• AMSV units (field stones, corners, and accents) –decorative layer.
• Mortar setting bed – adheres AMSV to a wall surface.
• Pointing mortar – fills gaps between AMSV units to reduce water intrusion.
• Topically applied coating – to provide cleaning surface or water penetration resistance.
• Mortar scratch coat – to give a rough surface to enhance adhesion of mortar setting bed to the lath or appropriate wall surface to install AMSV.
• Lath – to provide a mechanically fastened surface to allow adhesion of mortar scratch coat to the proper wall surface to install AMSV.
• Flashing and accessory detailing (weep screed, casing bead) – to minimize water penetration and allow water drainage within the AMSV system.
• WRB – to reduce water penetration of water trapped in the AMSV system to wall surface behind.
• Backup – refers to a suitable wall surface for the installation of AMSV.
It’s important to note that there are only three required components of any AMSV application: AMSV units, mortar setting bed, and backup. All other parts either supplement the AMSV system to satisfy the proper installation requirements of AMSV or are required to meet the desired architectural appearance.
Architectural appearance components of AMSV include grouting, accents, and topical coating. Standard grout, overgrout, and dry stack are three grouting techniques used with the AMSV wall system. Dry-stack application features AMSV units installed tightly together without any grout in between each AMSV unit. This technique is highly susceptible to moisture intrusion. Subsequently, Kwon and Wu (2016) recommend the dry stack grouting only in dry, warm climates where water intrusion will not result in thaw/freeze conditions and will not subject the wall system to prolonged moisture exposure. Alternatively, in all other environments, Kwon and Wu (2016) recommend a fully grouted technique to decrease water infiltration into the AMSV wall system.
Note. Principal components of Adhered Manufactured Stone Veneer Wall System, From Installation Guide and Design Options for Compliance with ASTM C1780 by National Concrete Masonry Association, 2020 (https://ncma.org/ resource/msv-installation-guide/)
Accents and trims for the AMSV system include wall caps and sills. Wall caps do not require any additional structural support as the wall below supports the weight of the wall cap. Sills, on the other hand, need angles attached to inwall blocking to support their weight. While sills and wall caps can be wet cast using the same cement and aggregate mix as the AMSV, some architects may specify precast concrete accents, which would be outside of the scope of this Technical Paper.
Topping coatings provide a protective surficial coating to allow cleaning. However, any selected topically applied coating must enable the wall system to breathe to support the evaporation of moisture trapped inside the system.
Furthermore, the estimator needs to know the physical properties of the AMSV wall system. The list below outlines key characteristics:
• AMSV, as a siding element, merely provides “ornamentation and the first layer of weatherization protection” (Eldorado, 2020, p. 1).
• AMSV has negligent waterproofing properties.
• As per ASTM C1780, the minimum shear bond strength for AMSV to adhere to a backup is 50 psi (345 kPa).
• AMSV is suitable for interior or exterior applications.
• Considering that only AMSV units, mortar, and backup are the only three required components of the AMSV system, the estimator must know conditions that require the use of other elements
For AMSV to maintain a minimum of 50 psi (345 kPa) shear bond strength, the mortar setting bed must adhere to structurally sound backup. Examples of such backups include concrete wall, concrete masonry wall, and metal stud/wood-framed wall with studs spaced at 16” on center with sheathing.
The next element to consider is the adhesion of the mortar setting bed to backup. Concrete and concrete masonry walls with porous, non-painted surfaces allow for direct bonding of mortar setting bed to backup. All other wall surfaces must receive corrosion-resistant lath and scratch coat to allow the recommended adhesion of mortar setting bed to backup. Alternatively, cement board and a layer of WRB could substitute lath and scratch coat.
Another element to consider in the AMSV wall system is Water Resistive Barrier. Any interior application of AMSV and exterior application over concrete or concrete masonry do not need WRB, while all other methods require WRB. Frequently, WRB is used together with corrosion-resistant lath and scratch coat to provide a rough surface to allow adhesion of mortar to backup.
The final element of concern for the AMSV system is water intrusion. “Moisture-related failures make up the majority of warranty claims with the nation’s largest homebuilders” (Lisow, 2019). AMSV has a water absorption rate of 12-23%, and, as such, the AMSV system absorbs water quickly. Once inside, water may weaken the bond between mortar and AMSV, may result in system failure in thaw-freeze conditions, or may cause water damage to WRB and backup. Consequently, proper detailing is essential for AMSV
systems. Good detailing for an AMSV system includes a weep screed 4” above grade, casing bead on each side, and flashing on the top. Estimators should review NCMA’s Installation Guide for further detailing and any components not mentioned in this Technical Paper.
Knowing the properties of the AMSV system, components of AMSV, and their required application will enable the estimator to assess the required materials of the AMSV project properly. After such materials have been identified and quantified, the estimator needs to assign a price to each component. The most precise way to do it is to request material quotes from multiple suppliers
Labor is the employee’s contribution of expertise and manual work to convert raw materials into finished products and services in exchange for tangible and intangible benefits. The task of installing AMSV components accounts for most of the labor on an AMSV project. However, some additional functions like offloading, inventory, staging, and cleanup require labor as well. Thus, the process of pricing out a labor scope requires identifying labor scope, establishing labor crews, calculating the duration of time to use labor crews, and determining labor unit costing.
One way to identify the labor scope is to analyze labor requirements for every AMSV component and then supplement that with any other task needing labor. Also, to identify labor scope, the estimator needs to determine the required crew. The crew is a combination of labor and equipment required to complete the job effectively. Identifying crew composition involves experience. Estimators who lack experience should reference online publications like R.S. Means or consult with project managers and superintendents. The crew should be large enough to efficiently complete the task but not too large to be ineffective. Notably, AMSV crews are not limited to bricklayers but may use tile setters and stucco plasterers instead. Moreover, the estimator must identify if union labor or prevailing wage would be required, as these factors will drive up the cost.
After successfully identifying the appropriate crew, the estimator needs to figure out the length of time for this crew to complete the project. To calculate the time, the estimator needs to divide the quantity of material to be installed by labor productivity rate. The estimator will use the resulting length of time to calculate labor cost. To identify labor productivity
rates, the estimator should rely on prior experience with similar projects, online publications, or a survey of the local labor pool. For projects that require labor for cleanup, offloading, and staging, the estimator should use historical data from previous similar projects.
Before further evaluating labor cost, it is crucial to differentiate various terminologies associated with labor costing. Net pay is the amount an employee takes home after deductions. Gross pay is the wage employer pays employees before deductions. Direct compensation is the base salary and incentive pay the employer pays to the employee. Indirect compensation, or total compensation, is the sum of direct compensation and any other costs employer pays for an employee like the employer’s portion of benefits, training, paid time off, etc. Upper management may be responsible for assigning total compensation costs because of the complexity and confidentiality of these calculations.
Further considering that an estimate represents a cost for a company, and not the employee, to perform a service, the proposal must use the total compensation labor rate because it accurately displays labor cost borne by the employer. Thus, to calculate labor cost, the estimator needs to multiply the total compensation expressed as an hourly or daily price by the appropriate length of time necessary for the crew to complete the project. Repeat this step for each crew member and each task. The sum of costs will be the total labor cost to perform the project.
After correctly estimating appropriate labor crews, the estimator should select the right equipment to maximize the crew’s labor production rate. Every AMSV project will need standard tools like buckets, wheelbarrows, trowels, staple guns, tape measure, and tile saw. Additionally, AMSV installation above 5' would use a rolling scaffold, while AMSV installation above 8' should use a steel scaffold. Some large jobs may require a concrete mixer, scissor lift, forklift, and even a crane. At this point in the bidding process, the estimator should answer the question as to which equipment maximizes selected crews’ production rate.
Upon determining the complete equipment and tools list, the estimator must assign costs to equipment. Equipment is either owned or rented. If a project assumes using rented equipment, the estimator must request rental quotes and confirm scope accuracy. Rental companies may omit additional fees like delivery, pick up, installation/setup, taxes, and even fuel and environ-
mental fees/surcharges. Subsequently, it’s crucial to solicit multiple suppliers for pricing.
A project that utilizes in-house equipment requires management’s input to determine equipment pricing. The price for owned equipment should be a pro-rated share of equipment’s total cost (initial purchase price, any finance charges, maintenance costs, storage fees, transport, and depreciation expenses). For example, scaffolding with a 5-year (60-month) depreciation schedule when used on a month-long project would result in a cost of 1/60th of a total scaffold cost. Nevertheless, even when a company uses contractor-owned equipment, the estimator should request rental prices to assess the competitiveness of in-house equipment prices.
A combination of AMSV material, labor, and equipment costing on a project will yield only direct costs but not a total cost. Additionally, the estimator must account for indirect costs. Indirect costs (or overhead) are any costs borne by the employer that are not accountable to any project. Indirect costs include office, staff, and miscellaneous expenses like travel, training, advertisement, etc.
An essential aspect of indirect costs is that these costs are unrelated to any project, and therefore, to any specific bid amount. Instead, indirect costs are a percentage of the total volume of operation. Overhead remains a cost regardless of if a contractor wins or loses a job. Thus, the calculation for indirect cost must account for any projects that a contractor bids and does not win. For these reasons, upper management determines indirect costs.
Moreover, the estimator must consider project funding when calculating indirect cost. For example, a Funds Control project may require additional reporting by the accounting department. Similarly, some banks may require audited financials as part of the bid submittals. The estimator should review bidding documents for any information regarding project funding and bid submittal requirements.
The final aspect of a proposal is profit. Profit is “a positive gain generated from business operations or investment after subtracting all expenses or costs” (Nitisha, 2015). Multiple factors affect the decision of profit markup: current and expect economic activity, competition on a project, the competence level of competition, and even the size of the project. Although estimators should know factors that affect profit and how profit affects
proposals, often, upper management will determine the correct profit markup.
After assigning labor, material, equipment, indirect costs, and profit, the estimator needs to aggregate these costs to prepare for analysis.
Please recall that an estimate is an offer to perform work for a stipulated price while adhering to specific requirements. As such, the accuracy of the project’s proposal determines the contractor’s profitability. Consequently, it is of utmost importance for an estimator to be confident in the accuracy of his/her bid. After aggregating all costs, the estimator must analyze the estimate. The first portion of such analysis consists of reviewing the bid and project scope for unique risks.
In March of 2020, the World came to a standstill. Factories closed, businesses shut down, and developers canceled contracts or placed projects on hold. Thus, when construction resumed in May of 2020, things were not the same. Yet, many contractors realized that they could continue operating at nearly pre-pandemic production with the proper safeguards. Similarly, many developers realized that the slowdown was a perfect opportunity to finally remodel their store or build new ones in anticipation of eventual reopening. Suddenly, the construction industry was booming again.
Unfortunately, global suppliers have not kept up. As a result, construction materials began running out. Everything had a lead time. Prices for lumber, steel, PVC, and cement skyrocketed. Because cement is the primary raw material for making the AMSV, AMSV prices began to rise while lead times increased. At one point, many suppliers were advertising lead times of 16-20 weeks and could only hold the price for 30 days.
Consequently, the estimator must confirm the supplier price expiration date and lead times. Furthermore, extended lead times mean that if the estimator miscalculated the initial order and did not order enough material, it may take 16-20 weeks to receive the next shipment. Estimators may hedge this risk by purchasing more material (higher waste factor).
Moreover, personnel safety during COVID-19 was paramount. Employers needed to provide additional Personal Protective Equipment and set up extra hygiene mea-
sures. Doing business during a pandemic resulted in decreased productivity, too: sick or potentially exposed employees had to take time off to undergo testing and quarantine. The estimator should adequately account for these conditions in their bid or exclude them from their proposal entirely.
Similarly, building departments had to adjust their operations. Some municipalities required the entire project halted and building cleared out before an inspector can inspect the job. The estimator should research any unique operational conditions from local Authority Having Jurisdiction and adjust their bid accordingly.
In Refton, Pennsylvania, a stone veneer company’s negligent operation of steel scaffolding resulted in a $154,440 citation (Occupational Safety and Health Administration, 2012). Thankfully, no one was hurt, but this example highlights the importance of safety. Many AMSV projects require the use of scaffolding and saws. Occupational Safety and Health Administration (OSHA) requires a daily inspection of steel scaffolding, lifts, and other equipment. Besides daily checks, steel scaffolding should be designed by a registered professional and installed by trained personnel.
Additionally, using a tile saw to cut AMSV requires goggles, gloves, and hearing protection. Failure to adhere to these safety requirements may result in fines, injury, or even death. The estimator should review the company’s safety manual for other safety procedures and identify their impact on productivity and pricing.
After reviewing the bid and project scope for unique risks, the estimator needs to analyze the proposal compared to other projects. There are two main methods of accomplishing this analysis:
• Evaluate bid to prior historical data.
• Evaluate bid to subcontractors’ pricing or pricing published online.
Historic data evaluation requires a comparison to a database of previous projects with similar scope. Thus, an estimator needs to establish and maintain a database of historical prices. Such database should include the following information:
• Project name.
• Bid date.
• Geographic area.
• AMSV specifications.
• Area of installed AMSV.
• Labor (expressed in person-hours).
• Equipment used on the job.
• Percentage of overhead.
• Percentage of profit.
• Maximum height of AMSV
One such case of using historical data is comparing labor and material as a ratio of direct costs. For example, material and labor costs for an AMSV project should account for 48% and 50% of the project's direct cost, respectively.
As outlined above, the AMSV wall system consists of nine components. However, the AMSV installer may not install every piece of the AMSV system. Often, a sheet metal subcontractor may install flashing; a stucco subcontractor may install WRB, lath, scratch coat, weep screed, and casing bead; and a painter may apply the topical coating. Similarly, the AMSV installer may use equipment provided by others. For example, a general contractor may have a forklift on site that the AMSV installer can use to offload the material. Furthermore, the stucco subcontractor may have scaffolding set up because they needed it to install lath and scratch for the stone veneer. The estimator needs to understand everyone's responsibility and adequately account for every component of AMSV without missing anything and without having overlapping coverage.
By following the bidding process and incorporating technical and trade information, at this point, the estimator should be ready to finalize the price. The price would consist of material, labor, equipment, and indirect costs. Moreover, the estimator would have evaluated each price for any special conditions and analyzed the total bid for validity compared to other historical data.
A word of caution on historical data and ratios: these methods should never be used for reverse estimating (identifying the price of a project based on limited information like area of AMSV or percentage of labor) unless the bid is preliminary and includes appropriate contingency.
A word of caution on historical data and ratios: these methods should never be used for reverse estimating (identifying the price of a project based on limited information like area of AMSV or percentage of labor) unless the bid is preliminary and includes appropriate contingency.
Another way to analyze a proposal is to compare it to the subcontractor’s pricing or online estimating program like R.S. Means. Yet even these two methods may contain errors. Online estimating programs are highly dependent on an estimator entering the correct information because, if not, the output data would be inaccurate as well. Also, the subcontractor's price could be too high if the estimator selected only one subcontractor to bid on this project, and this subcontractor is not competitive. Many estimators who competitively bid out projects know that the variance between subcontractors’ pricing could range as much as 400% between the low and high bidder.
Another way to analyze a proposal is to compare it to the subcontractor’s pricing or online estimating program like R.S. Means. Yet even these two methods may contain errors. Online estimating programs are highly dependent on an estimator entering the correct information because, if not, the output data would be inaccurate as well. Also, the subcontractor's price could be too high if the estimator selected only one subcontractor to bid on this project, and this subcontractor is not competitive. Many estimators who competitively bid out projects know that the variance between subcontractors’ pricing could range as much as 400% between the low and high bidder.
As a bidding example, this Technical Paper estimates the installation of AMSV at a drive-through restaurant in El Cajon, California. This project is a 2,000 SF ground-up, single-story, wood-framed building. The primary finish on this building is stucco with approximately a 3’ high AMSV wainscot throughout most of the building perimeter. The specified AMSV was Eldorado Manzanita installed in a dry-stack pattern with a sill to match the stone veneer.
The example project is non-union and does not require any bonding. The onsite general contractor will have a forklift for offload, while the sheet metal subcontractor will install flashing. Similarly, the stucco subcontractor will install WRB, lath, scratch, weep screed, and casing bead. AMSV will not be sealed. AMSV installer will furnish and install AMSV, mortar setting bed, AMSV corners, and sill with angle supports. AMSV will be installed using type S mortar in a climate with an average temperature of 60°F.
Table 2
Table 2
Material Take-offs
Material Take-offs
Note. This table follows the methodology of converting take-offs to ordered quantities.
Note. This table follows the methodology of converting take-offs to ordered quantities.
Note. This table follows the methodology of converting take-offs to ordered quantities.
* The length of sill corners and area of AMSV corners is deducted from total sill length and total AMSV area to accurately calculate the required quantity of sills and area of AMSV, respectively.
* The length of sill corners and area of AMSV corners is deducted from total sill length and total AMSV area to accurately calculate the required quantity of sills and area of AMSV, respectively.
* The length of sill corners and area of AMSV corners is deducted from total sill length and total AMSV area to accurately calculate the required quantity of sills and area of AMSV, respectively. Table 3
Table 3
Table 3
Material Take-Off (Continued)
Material Take-Off (Continued)
MATERIALS (Continued)
MATERIALS (Continued)
3
Note. All prices are April 2021 pricing.
Note. All prices are April 2021 pricing.
* AMSV Area (SF) includes the total area of AMSV and sills with all applicable corners.
* AMSV Area (SF) includes the total area of AMSV and sills with all applicable corners.
Figure 12
Typical Material/Labor Ratio for an AMSV Project
Figure 12
Material/Labor Ratio of Sample Bid
Material/Labor Ratio of Sample Bid
A word of caution on historical data and ratios: these methods should never be used for reverse estimating (identifying the price of a project based on limited information like area of AMSV or percentage of labor) unless the bid is preliminary and includes appropriate contingency.
Funds Control is “an arrangement employing an independent third party to disburse the construction funds to the various trade contractors and suppliers on a given project” (International Risk Management Institute, Inc., n.d., para. 1)
Lead time is the amount of time between placing an order and receiving goods. Lead times are subject to the length of the approval process, manufacturing timeline, and shipment duration. Prevailing wage is “the average wage paid to similarly employed workers in a specific occupation in the area of intended employment” (United States Department of Labor, 2021, para.
Another way to analyze a proposal is to compare it to the subcontractor’s pricing or online estimating program like R.S. Means. Yet even these two methods may contain errors. Online estimating programs are highly dependent on an estimator entering the correct information because, if not, the output data would be inaccurate as well. Also, the subcontractor's price could be too high if the estimator selected only one subcontractor to bid on this project, and this subcontractor is not competitive. Many estimators who competitively bid out projects know that the variance between subcontractors’ pricing could range as much as 400% between the low and high bidder.
Take-off is the process of identifying, quantifying, and recording the scope of work detailed in construction documents.
Union labor is an organization formed by workers in a particular trade, industry, or company to improve pay, benefits, and working conditions (Boyle, 2021).
Boyle, M. J. (2021, March 21). Labor Union. Investopedia. https://www.investopedia.com/terms/l/labor-union.asp
Cost Engineering Consultancy. (2019, January 26). The key role of cost estimating in project management. Cost Engineering. https://www.costengineering.eu/blog-article/the-key-role-of-cost-estimating-in-project-management
Eldorado Stone. (2008). Finishing Details. https://www.eldoradostone.com
Eldorado Stone. (2018, March). Installation Guidelines. https://www.eldoradostone.com/wp-content/uploads/2016/03/MSV-Installation-Guide-5th-Edition-2nd-Printing_042718.pdf
International Risk Management Institute, Inc. (n.d.). Fund Control Agreement | Insurance Glossary Definition | IRMI.com. Retrieved May 12, 2021, from https://www.irmi.com/term/insurance-definitions/fund-control-agreement.
Kwon, R., & Wu, J. (2016, September). Adhering Masonry Veneer Systems: Understanding a Sticky Situation. Wiss, Janney, Elstner Associates. https://www.wje.com/assets/pdfs/articles/Adhered_Stone_Veneer_-_Understanding_a_Sticky_Situation.pdf Lang, N., & Bradfield, M. (2017, October 1). Codes and Standards for Manufactured Stone Veneer. Mason Contractors Association of America. https://www.masonrymagazine.com/blog/2017/10/01/codesand-standards-for-manufactured-stone-veneer/
Lisowe, T. (2019, May 5). Moisture Management in Natural Stone Veneer Masonry Construction. Buechel Stone. https://www.buechelstone.com/moisture-manage-stone-veneer-masonry/
Lograsso, S. (2020, June 29). An In-Depth Look at Manufactured Stone Veneer. Mason Contractors Association of America. https://www.masonrymagazine.com/blog/2020/06/29/an-in-depth-look-at-manufactured-stone-veneer/.
National Concrete Masonry Association. (2020, August 19). Manufactured Stone Installation Guide. NCMA. https:// ncma.org/resource/msv-installation-guide/
Nitisha. (2015, August 11). Profit: Types, Theories, and Functions of Profit. Economics Discussion. https://www.economicsdiscussion.net/business/profit-types-theories-and-functions-of-profit/3329
Occupational Safety and Health Administration. (2012, May 9). US Labor Department’s OSHA proposes more than $154,000 in fines to Quality Stone Veneer in Refton, Pa., for scaffolding hazards at Hegins site | Occupational Safety and Health Administration. https://www.osha.gov/news/newsreleases/region3/05092012
United States Department of Labor. (2021). Prevailing Wages (PERM, H-2B, H-1B, H-1B1, and E-3) | US Department of Labor. https://www.dol.gov/agencies/eta/foreign-labor/wages/prevailing-wage
Woolsey, R. (2017, August 11). Mastering the Full Process of Construction Cost Estimating. Design Cost Data. https:// www.dcd.com/articles/the-process-of-construction-cost-estimating
Unified Building Group (UBG) is a nationally licensed construction company with offices located in Broomfield, CO, West Palm and Pompano Beach, FL. UBG specializes in the telecommunications, corporate real estate, educational, power, energy, health care, restaurants, residential and commercial industries. UBG’s core capabilities range from real estate, site acquisition, investment, pre-construction, construction management, design build, to complete building lifecycle facilities management and maintenance. Our team has a combination of over 300 years of construction industry experience. UBG was formed to change the way the industry builds, collaborates and executes on projects. With branches in Arizona, California, Colorado and Florida, we are here to serve you!
Multiple Scholarships Available
Up to $25,000 to be Awarded
Application Due Date - April 28, 2023
For more information, visit ASPEnational.org
Education Tab - Scholarship
Our Estimating Academy is building a course catalog of standardized online classes for the estimating industry. We are searching for subjectmatter experts to assist us with the creation of specific estimating class topics. If you have an estimating or construction education background, we would love to explore opportunities with you.
• Mechanical Estimating
• Electrical Estimating
• Plumbing Estimating
• Estimating Drywall
• Estimating Resilient Flooring
• Estimating Carpeting
• Estimating Tile
• Estimating Hardwood
• Estimating Standing and Running Trim
• Estimating Cabinetry and Countertops
• Specialty Estimating (all types)
• Estimating Soft Skills
Class development work is fully compensated and ranges from $500 to $3,000, depending on the class topic and length.
For more information and questions, please contact Natasha Crumbliss: Natasha@aspenational.org, or 940.435.4604.
March 3 2023 Summit - Registration Opens for Chapter Representatives
15 Deadline to submit “Intent to Submit” form for Award Submittals
April 1-30 Chapters hold annual elections
3 All Award Nominations / Applications due to SBO
10 Deadline for Chapters to identify their 2023 Summit Chapter Representative 24 Award Winners to be announced (to Winners only) 28 Scholarship applications due to SBO
May 12 Deadline for Chapters to submit Chapter elections result form to SBO 26 Scholarship Winner(s) to be announced (to Winners only)
Chapter Reports due to Regional Governors 29 SBO Closed for Memorial Day
June 12 Nominations for Board of Directors Due to SBO
Honoring Members + Chapters for their contributions to ASPE and the construction industry Honoring Member Estimators for their project successes
EST IMATOR OF THE YEAR
For excellence in advancing the art of construction estimating through Standards, Ethics and Practice, while leading and training others, and promoting ASPE throughout one’s career
CHAPTER PRESIDENT OF THE YEAR
For excellence in leading, promoting and supporting the goals and growth of the Chapter
FELLOW AWARD
For having attained national recognition for achievements in the art of construction estimating and for having made exceptional contributions to the Society
LEGACY - HOWARD S. PROUT FOUNDER OF CERTIFICATION AWARD
For Excellence in Promoting and Mentoring the Certification Program
LEGACY - FRANK E. YOUNG EXCELLENCE IN EDUCATION AWARD
For excellence in pioneering and promotion of Educational Opportunities and Advancements
LEGACY - MERLE W. HECKENLIVELY FOUNDER OF STANDARDS AWARD
For excellence in promoting and utilization of Standards of Ethics and Practice
INDUSTRY AWARDS
Celebrating projects displaying overall estimate efficiency and accuracy, unique and innovative design, technology solutions or community involvement
CHAPTER CHAMPION
For dedicated effort and contributions made to the advancement and growth of the Chapter
CHAPTER ACHIEVEMENT
For excellence in promoting ASPE and supporting its Members at the Chapter level
TECHNOLOGY AWARD
For promoting Technology innovation in advancement of the estimating profession
Intent to Submit Forms – Due March 15, 2023
Candidate Nominations + Chapter Applications - Due by April 3, 2023
Begin planning by nominating an ASPE Member who exemplifies the qualities needed and who deserves acknowledgement for their contributions
ASPEnational.org/page/ Awards
ARIZONA
Arizona #6
Where: Varies
Website: n/a
Meeting Contact: Jerry Chandler j.chandler@cox.net
ARKANSAS
Arkansas #33
Where: Varies
Website: n/a
Meeting Contact: Jack Guess jguess@baldwinshell.com
NW Arkansas #79
Where: Varies
Website: n/a
Meeting Contact: Danny Chadwick, CPE estimatordan@gmail.com
CALIFORNIA
Los Angeles #1
Where: Virtual Website: laestimator.org
Meeting Contact: Bruce Danielson la1ofaspe@outlook.com
Golden Gate #2
Where: Virtual Website: aspe2.org
Meeting Contact: Robert Muir, CPE robmuir72@hotmail.com
Orange County #3
Where: Virtual Website: aspe-oc3.org
Meeting Contact:
Troy Thomas constructionpro1984@yahoo.com
San Diego #4
Where: Virtual Website: aspesd4.org
Meeting Contact: Paul Chang pchang@balfourbeattyus.com
Sacramento #11
Where: Varies
Website: n/a
Meeting Contact: Bryan Hall bryan.hall@vanir.com
Silicon Valley #55
Where: Virtual Website: aspe55.org
Meeting Contact: Shawna Alvarado shawna@odonnellplastering.com
COLORADO
Denver #5
Where: Virtual Website: aspedenver.org
Meeting Contact: Jennifer Farmer, AEP jennifer@livingdesignstudios.com
CONNECTICUT
Nutmeg #60
Where: Back Nine Tavern Website: n/a
Meeting Contact: Lee Sullivan lee@lionsheadcc.com
Yankee #15
Where: n/a
Website: n/a
Meeting Contact: Bill Jacabacci jacabacci@gmail.com
DELAWARE
Delware #75
Where: Virtual Website: n/a
Meeting Contact: Brett Mucklow bmucklow@bpgsconstruction.com
DISTRICT OF COLUMBIA
Greater D.C. #23
Where: Varies
Website: n/a
Meeting Contact: Carlos Rosales aspe23president@gmail.com
FLORIDA
Tampa Bay #48
Where: The Pub Resturant Website: aspetampabay.com
Meeting Contact: Ray Velez reymvelez@gmail.com
Gold Coast #49
Where: Varies Website: n/a
Meeting Contact: Danny Chadwick, CPE estimatordan@gmail.com
Orlando #50
Where: Anser Advisory Website: https://aspeorlando50.com
Meeting Contact: Andrew Kleimola akleimola@anseradvisory.com
GEORGIA
Atlanta #14
Where: Virtual Website: n/a
Meeting Contact: Clinton Aldridge ca45@gatech.edu
ILLINOIS
Chicago #7
Where: Virtual Website: n/a
Meeting Contact: Bryan Mixer, CPE bmixer_rvc@msn.com
INDIANA
Central Indiana #59
Where: Varies
Website: n/a
Meeting Contact: Jeremy Adkins, CPE jadkins@wccci.com
Old Fort #65
Where: Virtual Website: aspechapter65.org
Meeting Contact:
Thad Berkes tberkes@designcollaborative.com
IOWA
Quad Cities #71
Where: Varies
Website: aspequadcities.org
Meeting Contact: Scott Robinson, CPE scottr@jlbradyco.com
Greater Des Moines #73
Where: Varies
Website: iowaaspe73.org
Meeting Contact: Hui (Huey) Su huey@concordconst.com
LOUISIANA
New Orleans #9
Where: Varies
Website: n/a
Meeting Contact: Danny Chadwick, CPE estimatordan@gmail.com
MAINE
Maine #37
Where: Varies
Website: aspemaine.com
Meeting Contact: John Brockington, CPE jbrockington@woodwardcurran.com
MARYLAND
Baltimore #21
Where: Varies
Website: n/a
Meeting Contact: Steve Dooley, CPE sdooley@phoenix-eng.com
MASSACHUSETTS
Boston #25
Where: Virtual Website: aspe17.org
Meeting Contact: Eric Rennell eric@rennellcapitalgroup.com
MICHIGAN
Detroit #17
Where: Virtual Website: aspe17.org
Meeting Contact: Matt Burress, CPE mburress@performanceservices.com
MISSOURI
St. Louis Metro #19
Where: AGC Training School
Website: aspe19stlouis.org
Meeting Contact: John Smith, CPE jpsmith@tarltoncorp.com
Heartland #32
Where: Varies
Website:aspe32.org
Meeting Contact: Eric Soriano esoriano @hermeslandscaping.com
NEW JERSEY
Garden State #26
Where: Virtual Website: n/a
Meeting Contact: Robert Sibilia, CPE sibiliaconstructionservicesllc @gmail.com
NEW MEXICO
Roadrunner #47
Where: Fiestas Restaurant
Website: n/a
Meeting Contact: Joshuah Crooker-Flint, CPE joshc@auiinc.net
NEW YORK
New York #10
Where: Virtual Website: n/a
Meeting Contact: Rose Jesse rosejesse.aspe@gmail.com
Empire State #42
Where: Athos Resturant
Website: n/a
Meeting Contact: Alvaro Garza, CPE Alvaro.garza@nationalgrid.com
OHIO
Southwestern Ohio #38
Where: Varies
Website: aspe-cincinnati.org
Meeting Contact: Dan Frondorf, CPE dan@dgfrondorf.com
OKLAHOMA
Landrun-OK City #80
Where: Varies
Website: aspeok.org
Meeting Contact: Mike Phillips, CPE michaelp@miller-tippens.com
OREGON
Columbia-Pacific #54
Where: Varies
Website: n/a
Meeting Contact: Steve Watkins steve.watkins@bnbuilders.com
PENNSYLVANIA
Greater Lehigh Valley #41
Where: Varies
Website: n/a
Meeting Contact: Dexter Murphy, CPE dextercmurphy@comcast.net
Three Rivers #44
Where: Varies
Website: n/a
Meeting Contact: Dexter Murphy, CPE dextercmurphy@comcast.net
Philadelphia #61
Where: Varies
Website: na
Meeting Contact: Stephen Biddle SBiddle@oliverfps.com
Central Pennsylvania #76
Where: Loxley's Resturant
Meeting Contact: Shawn Buckwalter, CPE sbuckwalter@egsconstruction.com
TENNESSEE
Middle Tennessee #34
Where: Varies
Website: n/a
Meeting Contact: Ricky Sanford rsanford7159@gmail.com
TEXAS
Houston #18
Where: Varies
Website: n/a
Meeting Contact: Larry Lucero, CPE llucero@redlineinsulation.com
Rio Grande #40
Where: Varies
Website: n/a
Meeting Contact: Rodolfo Barba, CPE rodolfobarba1@gmail.com
Dallas/ Ft.Worth #43
Where: Virtual Website: sites/google.com/view/aspe-dfw
Meeting Contact: Steve Patmon ASPE.dfw@gmail.com
UTAH
Great Salt Lake #51
Where: Virtual
Website: na
Meeting Contact:
M. John Shampton, CPE mjohnshampton@gmail.com
VIRGINIA
Richmond #82
Where: Varies
Website: aspe-richmond.org
Meeting Contact: Sid Bass, CPE sbass@reynolds.edu
WASHINGTON
Puget Sound #45
Where: Virtual
Website: na
Meeting Contact: Eric Benton Eric.benton@pmsvs.com
WISCONSIN
Brew City #78
Where: Varies
Website: na
Meeting Contact: Matt Washkoviak, CPE mattwashkoviak@camosy.com
Please Note: Information is subject to change. Report changes in your Chapter’s information with an email to Tina@ASPEnational.org
EDUCATION:
ASPE educates and mentors professional estimators for the sustainability of the construction industry.
PROFESSIONALISM:
ASPE promotes the lifelong pursuit of excellence and credibility in professional estimating.
ASPE is the construction industry’s leader and recognized authority in professional estimating through excellence in education, certification and standardization.
FELLOWSHIP:
ASPE develops a fellowship of professional estimators that connects and leads the construction industry.