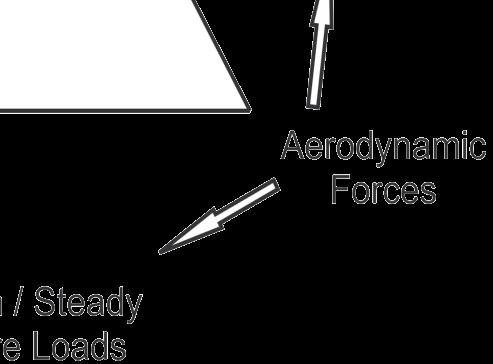
7 minute read
ALPES
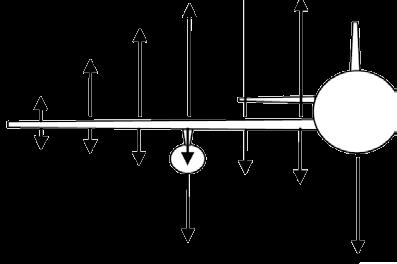
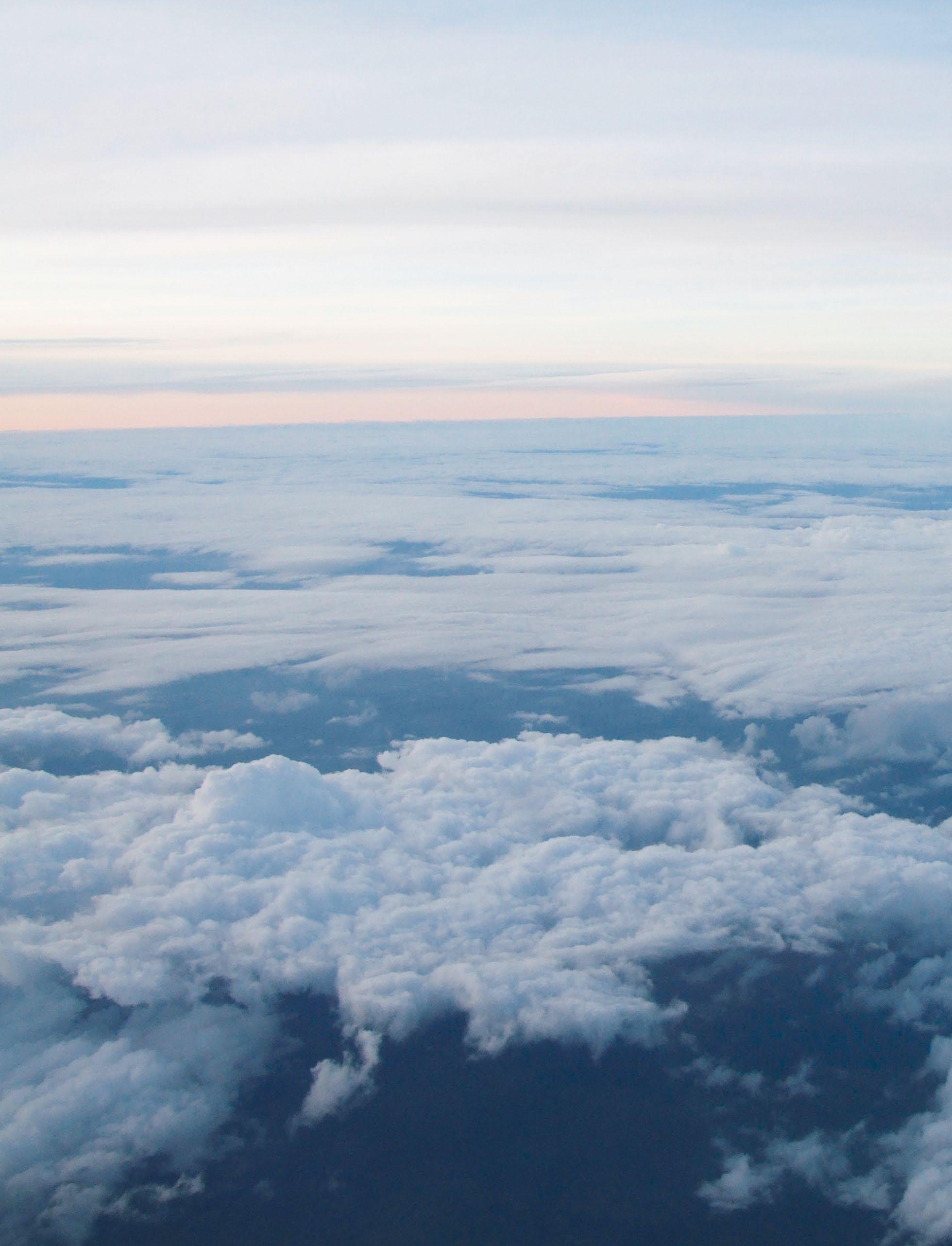
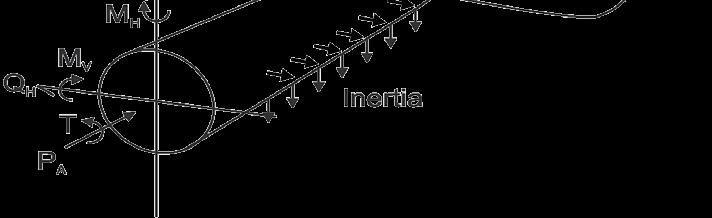
Creating Efficiencies in Aircraft Design
Two EU funded projects, ALPES and AeroGust, coordinated by the University of Bristol, are developing new methods to speed up and improve the accuracy of key processes involved in the design of more environmentally friendly aircraft. The aim is determining how loads, such as those caused by gusts of wind, interact with aircraft. Professor Jonathan Cooper explains the methods and the objectives of the projects that will lead to more efficient and cost effective aircraft designs
A key job in the design of an aircraft is to make sure it can cope with the stresses arising in flight or from manoeuvres on the ground. For instance, when an aircraft is buffeted by strong winds, this will affect all the parts of the plane’s structure as well as impacting on passenger comfort, so calculating the way that each component and also the entire aircraft reacts to gusts is essential knowledge before a plane can be built.
“Say you’re flying and the pilot says, ‘buckle up, we’re going through bumpy weather’,” explains Professor Cooper, illustrating the challenge. “This is an example of loads, in this case due to socalled gusts or turbulence. Aircraft need to be designed to cope with those loads and also those resulting from manoeuvres as a plane flies around, or during take-off and landing, turning and braking. So the loads department, in conjunction with the aerodynamicists, will compute the hundreds of thousands of different loads that might be encountered during a flight, and stress calculations then need to be performed for many different parts of the aircraft.”
A massive computation
The computational task has to account for the effect of loads on every element of the aircraft design, in every possible situation. In practical terms, this means calculating all possible combinations of fuel and passenger weights in different situations such as flying high or low, or flying fast or slowly. The number of variables is vast. From these calculations it is possible to reveal a complete picture of all the stresses on the structure of the plane and to determine the critical cases. Only when Aircraft flying in a vertical gust field.
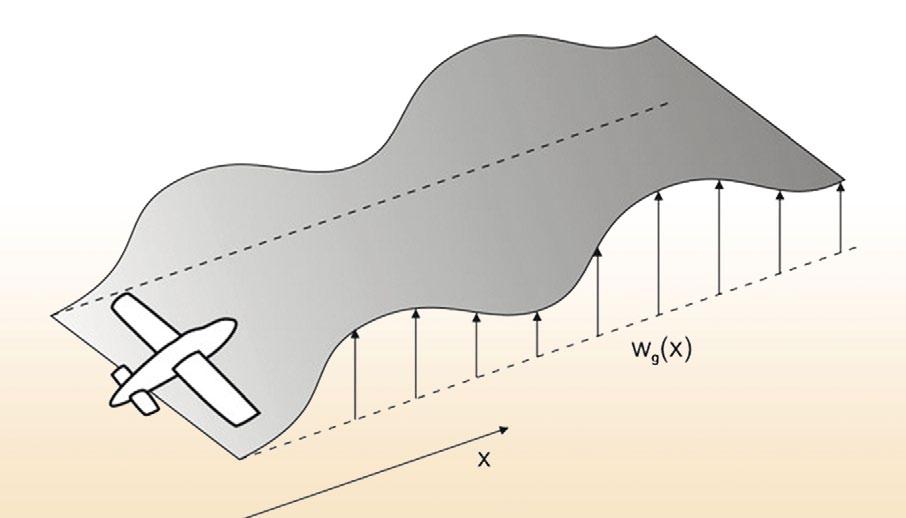
you have that information, can you understand where you might be able to make adjustments in the design, such as making parts thicker where the stress is too high, for example.
“Some parts of the aircraft will be most affected by gust loads, and others by landing, or turning on the runway and so on, and these critical cases are determined from all the simulations. Once you’ve done one entire set of simulations, the structures department can work out where they may be able to change the structure in some way to make it safer and also lighter in weight – and then the process starts over again.”
The problem is, as it takes so long to process each set of variables, the time and expense to rethink major aspects of design may not always be practical. It would be hugely beneficial therefore, if the time and effort it takes to compute loads early on in the design phase, was made more efficient. New approaches need to be explored to see where efficiencies can be made, whilst maintaining accuracy.
This is where the five researchers in the ALPES project come in, working on solutions that will streamline processes whilst improving accuracy. The engineers are all engaged in PhDs, conducting new research, whilst dividing their time between the University of Bristol, Siemens in Belgium and Airbus.
“We are doing some brand-new science but we are doing it with an industrial focus,” said Professor Cooper. “We are doing things that Airbus are interested in, that are going to help improve their aircraft designs. It takes 8-10 years to develop a new design but if we can bring that down to five years, you get a tremendous competitive advantage. So we are looking at creating efficiencies – if we’ve got 500,000 different cases that we need to look at and we can reduce that to 50,000, or even 5000, we immediately speed the process up dramatically.”
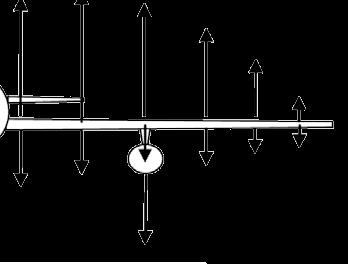
Improving Aircraft Design
If researchers can make new aircraft design concepts faster and easier to process and evaluate, it will lead to more refined aircraft and possibly novel configurations.
For example, by exploiting more flexible and lighter materials and new aerodynamic designs, it will be possible for planes to burn less fuel. This is the ultimate goal, to make aircraft more environmentally friendly and more cost effective at the same time. “It is important in this process to try to get the aircraft the right shape in-flight. Part of what we’re looking at is how we design the wings taking the
flexibility into account. The other aim is to reduce weight; if you can find ways of reducing the loads, you can therefore reduce the weight.”
“The use of carbon-fibre composites is becoming increasingly important, because you can use less weight but still carry the same amount of load, and also control the wing deflection in-flight ” says Professor Cooper. “In addition you’re always trying to do things with the aerodynamic shape to reduce the drag. A lot of aircraft now have winglets, which are the parts at the end of the wing that bend upwards. The reason for having winglets is that they help to improve the aerodynamics. One of the students in the ALPES project is looking at how we can use the wing tips to reduce the loads due to gusts.
By working closely with industrial partners, Airbus and Siemens, the PhD students have a unique opportunity to affect an industry by improving simulation. The project sits right on the edge between academia and industry and has the potential to make big differences in a competitive market.
“Hopefully some of these methods will eventually find their way into Airbus. Siemens’ role is developing software packages, so a win-win would be that we develop methods with Airbus and then our PhD’s code is used in collaboration with Siemens to make software, which does what Airbus wants it to do. If our methods are used, then it’s a success. The other bonus is that the five researchers from ALPES go and work in the industry.”

Some parts of the aircraft will be most affected by gust loads, Some parts of the aircraft will be most affected by gust loads, and others by landing, or turning on the runway and and others by landing, or turning on the runway and
so on, and these critical cases are determined from all the so on, and these critical cases are determined from all the
simulations Once you’ve done one entire set of simulations, the simulations Once you’ve done one entire set of simulations, the structures department can work out where they may be able to structures department can work out where they may be able to
change the structure in some way change the structure in some way
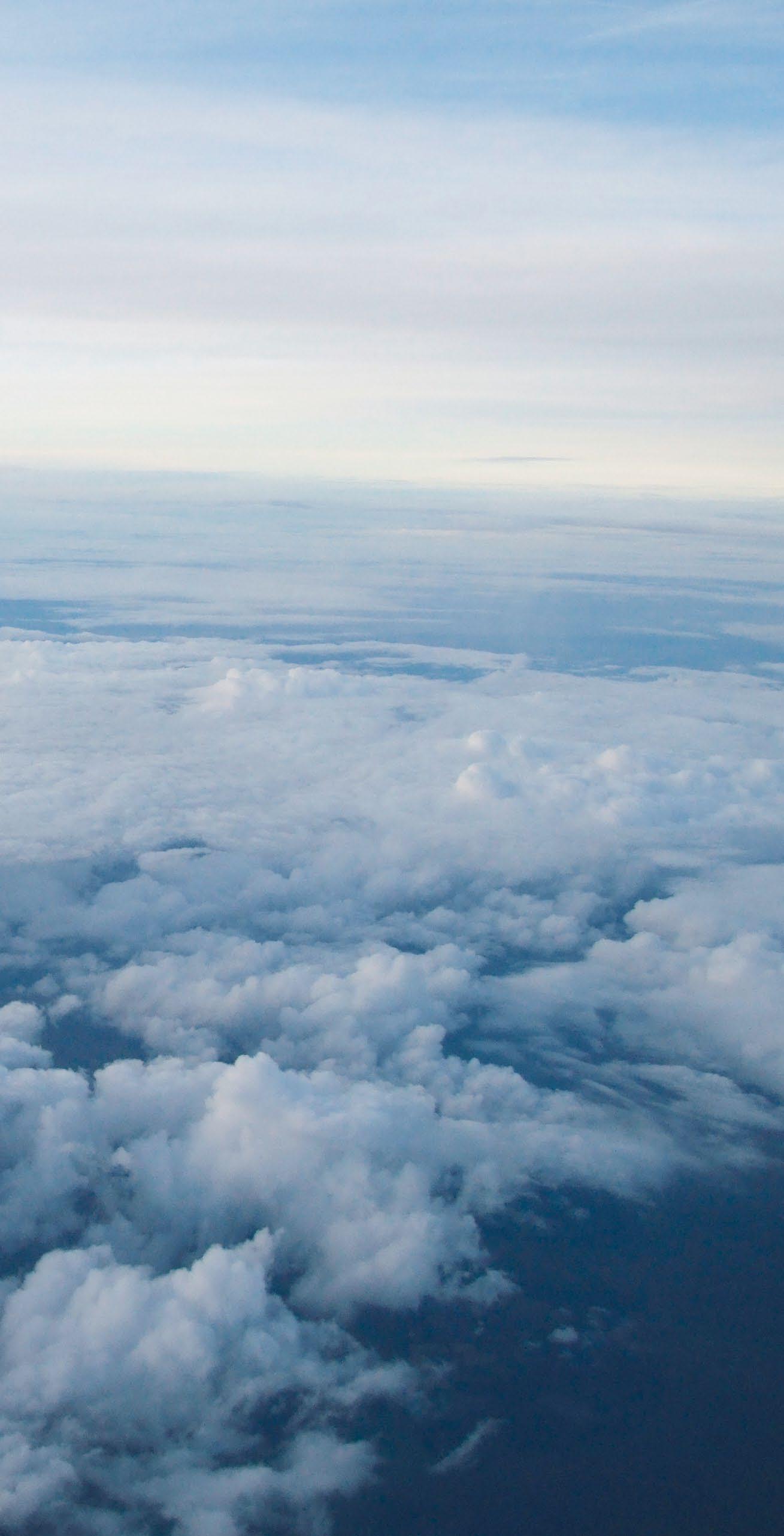
ALPES Early Stage Researchers
Full Project Title
Aircraft Loads Prediction using Enhanced Simulation (ALPES)
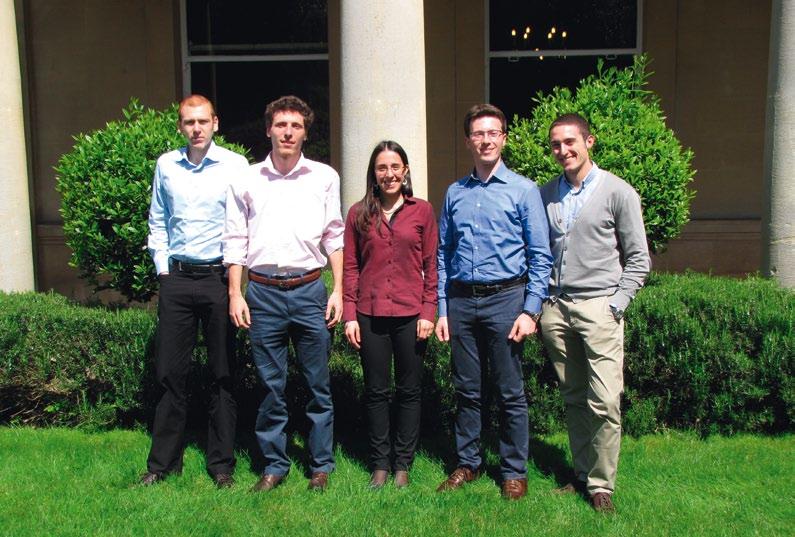
Project Objectives
ALPES is an EC FP7 Marie Curie European Industrial Doctorate Training Network which runs from 1 October 2013 to 30 September 2017. The aim of the network is to improve the prediction accuracy and efficiency of the loads experienced by an aircraft in-flight and on the ground.
Project Partners
The ALPES network involves five PhDs combining a novel research programme with a highly industrially focused training schedule, including placements at Airbus in the UK and/or France.
Key Participants
• University of Bristol: Professor Jonathan Cooper, Dr Ann Gaitonde, Dr Dorian Jones, Professor Mark Lowenberg, Sarah Hassall. • Siemens PLM Software: Dr Yves Lemmens, Dr Jens de Boer, Els Tops. • Airbus: Tom Wilson, Murray Cross, Simon Coggon, Etienne Coetzee
Contact Details
Professor Jonathan Cooper RAEng Airbus Sir George White Chair in Aerospace Engineering Queen’s School of Engineering, University Walk, Bristol BS8 1TR T: +44 (0)117 33 15819 E: j.e.cooper@bristol.ac.uk W: http://www.bris.ac.uk/aerodynamicsresearch/projects/alpes/
Professor Jonathan Cooper
Professor Jonathan Cooper is the Royal Academy of Engineering Airbus Sir George White Chair of Aerospace Engineering at the University of Bristol. His prime research areas are in aeroelasticity and loads, and he is also co-author of the Wiley textbook “Introduction to Aircraft Aeroelasticity and Loads”.