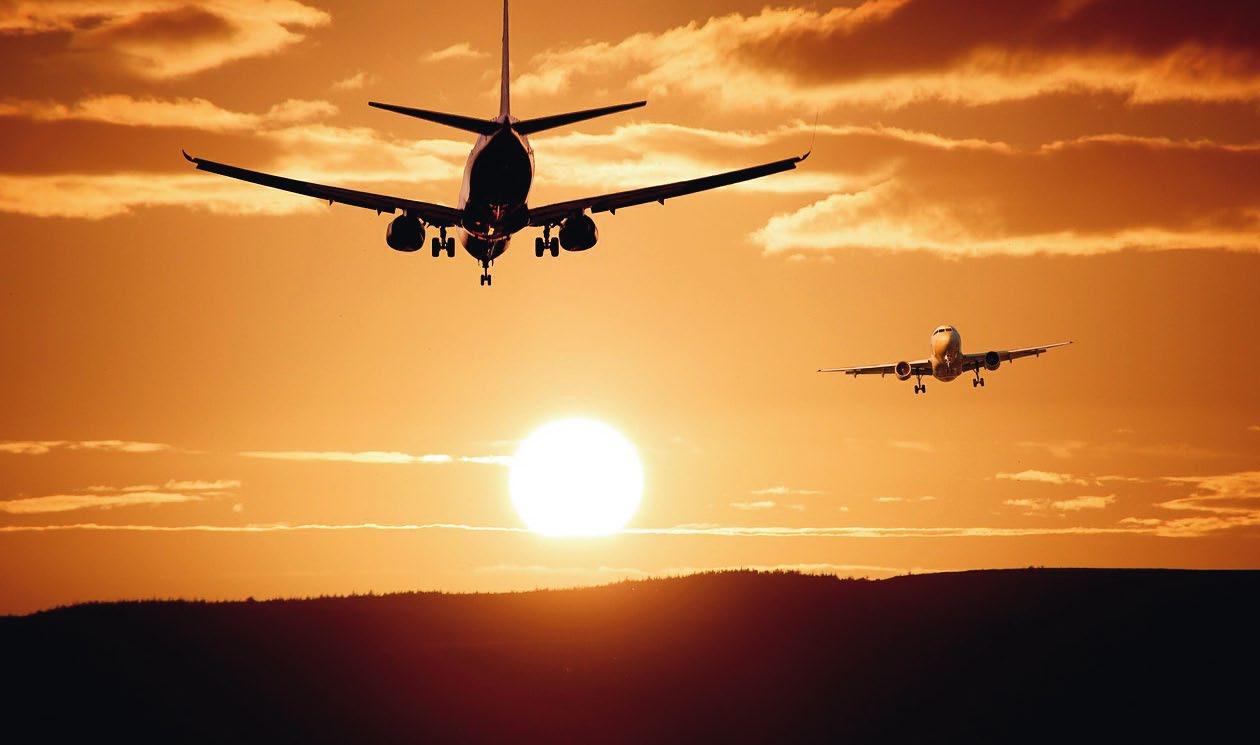
3 minute read
AeroGust
Full Project Title
Aeroelastic Gust Modelling (AeroGust)
Project Objectives
AeroGust aims to investigate and develop improved simulation methods for gusts by responding to three main areas of work: 1) Investigations using Computational Fluid Dynamics (CFD). 2) Creation of a numerical gust loads process that does not require wind tunnel data for early design stages. 3) Development of efficient reduced order models for gust prediction that account for aerodynamic and structural complexity at an acceptable cost.
Project Funding
Funded by the European Union’s Horizon 2020 Research and Innovation programme under grant agreement number 636053.
Project Partners
University of Bristol (Coordinator), Inria, NLR, DLR, University of Cape Town, NUMECA, Optimad Engineering S.r.l., University of Liverpool, Airbus Defence and Space, Dassault Aviation, Piaggio Aerospace and VALEOL.
Contact Details
University of Bristol, Queen’s School of Engineering, University Walk, Bristol BS8 1TR T: +44 (0) 117 33 15015 E: AeroGust-project@bristol.ac.uk W: www.aerogust.eu
Dr Ann Gaitonde (left) Dr Dorian Jones (right)
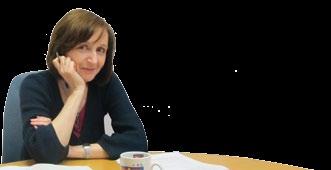
Dr Ann Gaitonde is joint Head of the Fluid and Aerodynamics Research Group at the University of Bristol, working alongside Dr Dorian Jones. She was awarded her PhD in 1991 and subsequently worked in the Department of Aerospace Engineering as a post-doctoral researcher developing computational methods to calculate unsteady fluid flows. Dr Dorian Jones is joint Head of the Fluid and Aerodynamics Research Group at the University of Bristol along with Dr Gaitonde. He was awarded his PhD in 1995 following his studies into the Direct Numerical Simulation of turbulent ducted flows. His research concerns the development of numerical methods for the prediction of unsteady fluid flows.
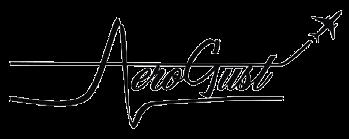
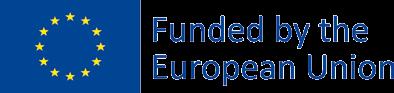
The AeroGust Project
Another project, under the leadership
of Dr Ann Gaitonde and Dr Dorian Jones, that links to ALPES is AeroGust, which focuses on the interaction of gusts with aircraft. As with ALPES, this project is aiming to scale down the bulk of work in the design process, by creating new efficiencies in simulations and reducing the reliance on expensive and time consuming wind tunnel testing. It is also intended that the AeroGust research will transfer into renewable wind technology, aiming to reduce the loads on wind turbines.
“A wind tunnel is used to drive air around a fixed aircraft model rather than flying it through the air. There are very few wind tunnels worldwide that are able to accurately reproduce the conditions for a full size aircraft in flight, and such testing is really expensive, in the region of tens of thousands of euros a day.”
Both computer simulations and model testing are required in conjunction to generate and validate designs but if there was a bias towards accurate computer simulations in initial design experiments, the process can be speeded up dramatically. Reducing the number of experiments save costs and time.
A key tool at the disposal of the researchers working on the AeroGust project is Computational Fluid Dynamics (CFD) software, which is used to produce accurate models of the aerodynamic gust flows around the flexible aircraft structure which, in turn, is modelled using Finite Elements (FE). The new computer codes generated in AeroGust will streamline the processes of tests and simulations. “One of the advantages of simulation is that once you’ve got everything working, you can make design changes – you can make things longer, or change any aspect of design just by changing a couple of lines of code. Whereas, normally, you’ve got to go through the whole process again and again of building another model every time you try something out. AeroGust is looking at better modelling techniques for gusts. With CFD, it means
With CFD, it means we have sophisticated methods of modelling the air flow over the wing for example,
we have sophisticated methods of modelling the air flow over the wing for example, to discover how those airflows interact with the wing. CFD for gusts is still an area that is very much a current research topic. The methods that have been used before are much less sophisticated.”
Using better simulation techniques will lead to more efficient time use and high levels of effectiveness and accuracy in the resulting designs which can be made lighter. Entirely new kinds of design, including the use of different structural materials can be explored easily.
Summary
Both AeroGust and ALPES have objectives that can be used to make future aircraft designs more environmentally efficient and to be evaluated much quicker. The work being conducted from both these projects could be pivotal for shaping the future of aircraft design.