New solution for the fridges of the future
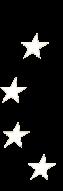
The EU F-Gas regulation sets out new restrictions on the use of hydrofluorocarbons in refrigerators. Researchers in the LIFE-TURBOALGOR CO2 project aim to show how an innovative solution can improve the energy efficiency of refrigerating plants and reduce their environmental impact, as Maurizio Ascani explains.
The use of chlorofluorocarbons (CFCs) as refrigerants in fridges was banned under the Montreal Protocol in 1987, and regulations have since grown increasingly stringent, as efforts to limit the environmental impact of the sector have intensified. Beginning 2024 the EU updated its regulations on the use of f-gases, greenhouse gases that contribute to global warming, accelerating the shift towards natural refrigerants. “CO 2 is now the most important refrigerant under the new regulations,” says Maurizio Ascani, Innovation Technology Manager at Turboalgor, an Italian SME which specialises in developing patented expansion devices as efficiency tools for refrigeration systems. This move towards a new type of refrigerant will also require changes in the actual fridges, a topic Ascani is addressing as part of his work on the LIFE-TURBOALGOR CO 2 project. “CO 2 has completely different features to those of older refrigerants,” he explains. “In the past Turboalgor developed a turbocharger to increase the energy efficiency of refrigeration systems operating with HFC. The main difference is that CO 2 works at a very high level of pressure - it has a much higher density. Because of this physical difference, it is necessary to move from a conventional turbocharger to a device that can work even with fluids at high pressure and high density.”
Through the FREEEX brand, a device called a Free Piston Expander (FPE) has been developed by the team at Turboalgor to meet these requirements, together with a Fluid Control Unit (FCU), which is designed to reduce the amount of energy typically required to operate a refrigerator. The FPE performs a dual function, as both an expander and a compressor, which reduces the workload on the existing compressor within a refrigerator. “There is always a compressor in a refrigerator to compress the refrigerating fluid, which requires a supply of electricity. The amount of electricity consumed is proportional to the level of compression,” outlines Ascani. While the main compressor in a fridge consumes electricity in the normal way, the compressor within the FPE operates on energy recovered from a novel thermodynamic cycle developed in the project. “We introduced significant
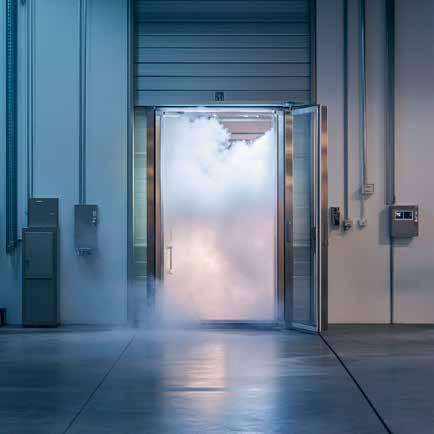
modifications to the thermodynamic cycle to recover energy and improve efficiency. So energy is recycled from inside the refrigerator,” explains Ascani. “This means that the FPE doesn’t rely on electricity as the primary source of energy, it uses recycled energy.”
FPE is managed, is entirely new, and Ascani and his colleagues at Turboalgor are keen to explore the wider potential of both devices. “Patents have been filed for both the FPE and the FCU,” he says. A few prototypes of the FPE have been developed, and researchers are developing a range of products to meet different needs. “The goal in the LIFE-TURBOALGOR CO 2 project is to move from a single prototype to a point where we have a range of products. We want to produce FPEs for different types of refrigerators, related to their power level and temperature,” says Ascani. “We aim to develop three types of FPEs, modifying the size of the free piston in each. The three devices are geometrically similar, but with different sizes and volumes. They can be used either alone, or in parallel.”
Researchers are working to develop the three types of refrigerators, with different
“We introduced significant modifications to the thermodynamic cycle to recover energy and improve efficiency. Energy is recycled from inside the thermodynamic cycle of the refrigerator.”
Free Piston Expander
The concept of a FPE has previously been explored in the scientific literature, but the project team are breaking new ground by exploring its potential application in refrigeration units. The FCU meanwhile, the unit by which the operation of the
levels of cooling capacity, which will then be installed on-site at a customer of one of the project partners, EPTA SPA. This will provide invaluable information about the practical operation of the FPE and its impact, complementing data from the internal tests that have already been conducted. “These
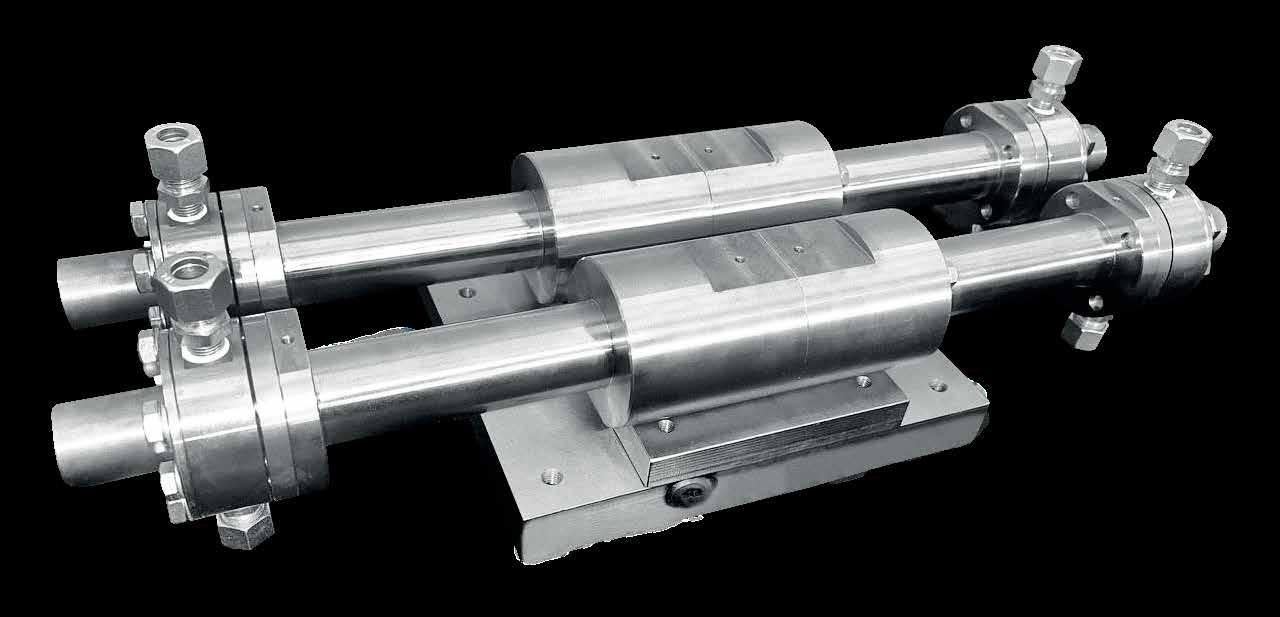
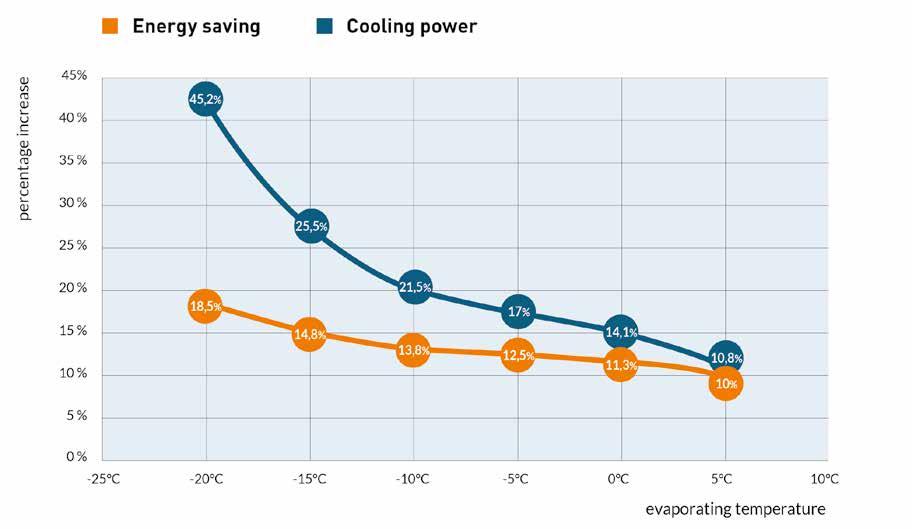
tests will provide us with new information from the field,” outlines Ascani. The project team are also working to calculate the environmental impact of the device and assess its impact on energy efficiency. “On one side the device helps reduce electricity consumption, but on another additional raw materials are required to produce it,” continues Ascani. “One outcome of the project will be an assessment of the total impact of the device, which is expected to lead to energy savings of 19 percent. The impact of the materials used in development is important, but it is negligible in comparison to reductions in energy consumption.”
Refrigeration plants
This research is targeted at larger refrigeration plants / heat pumps rather than domestic units, as they offer a quicker return on the initial investment in terms of energy saving and running costs. The cost of installing the device in a domestic refrigerator is roughly similar to putting it in a large refrigerating plant, so Ascani says the upfront cost can be recovered more rapidly in the latter case.
“With plants of 10 kW or more, a return on the initial investment can be achieved in the space of 1-2 years,” he outlines. Economic considerations were also prominent in the decision around how to integrate the FPE into a refrigeration plant. “We have decided to integrate the FPE during the assembly of the refrigerator rather than to integrate it into an existing plant,” says Ascani. “This is largely because the FPE can be integrated during the assembly of a plant with negligible additional costs. Whereas if you decide to upgrade an existing plant, it is necessary to halt operations, cut pipes and connect the FPE, which leads to further costs.”
The ultimate objective in the project is to prove the effectiveness and commercial viability of the FPE and help reduce the
environmental impact of refrigerators. While the primary focus at this stage is larger refrigeration systems, Ascani believes this FPE solution could eventually be applied more widely as the costs of production change. “In terms of the economics, the point at which this solution is viable is likely to change as a function of the cost of electricity and various other parameters. We expect that limit will move to a lower range in future,” he says. The more immediate priority is to optimise the FPE however, with Ascani and his colleagues in the project still preparing and modifying the product range. “In a few weeks we will start with tests at EPTA where the FPE has been installed. The goal is to have a few FPEs integrated in refrigeration plants by the end of the project,” he outlines. “We have also started with marketing work, and recently attended the Chillventa refrigeration event in Germany to publicise this research and the potential of this solution.”
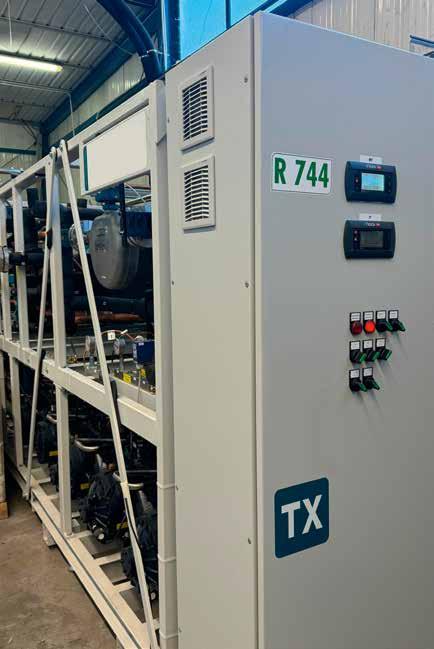
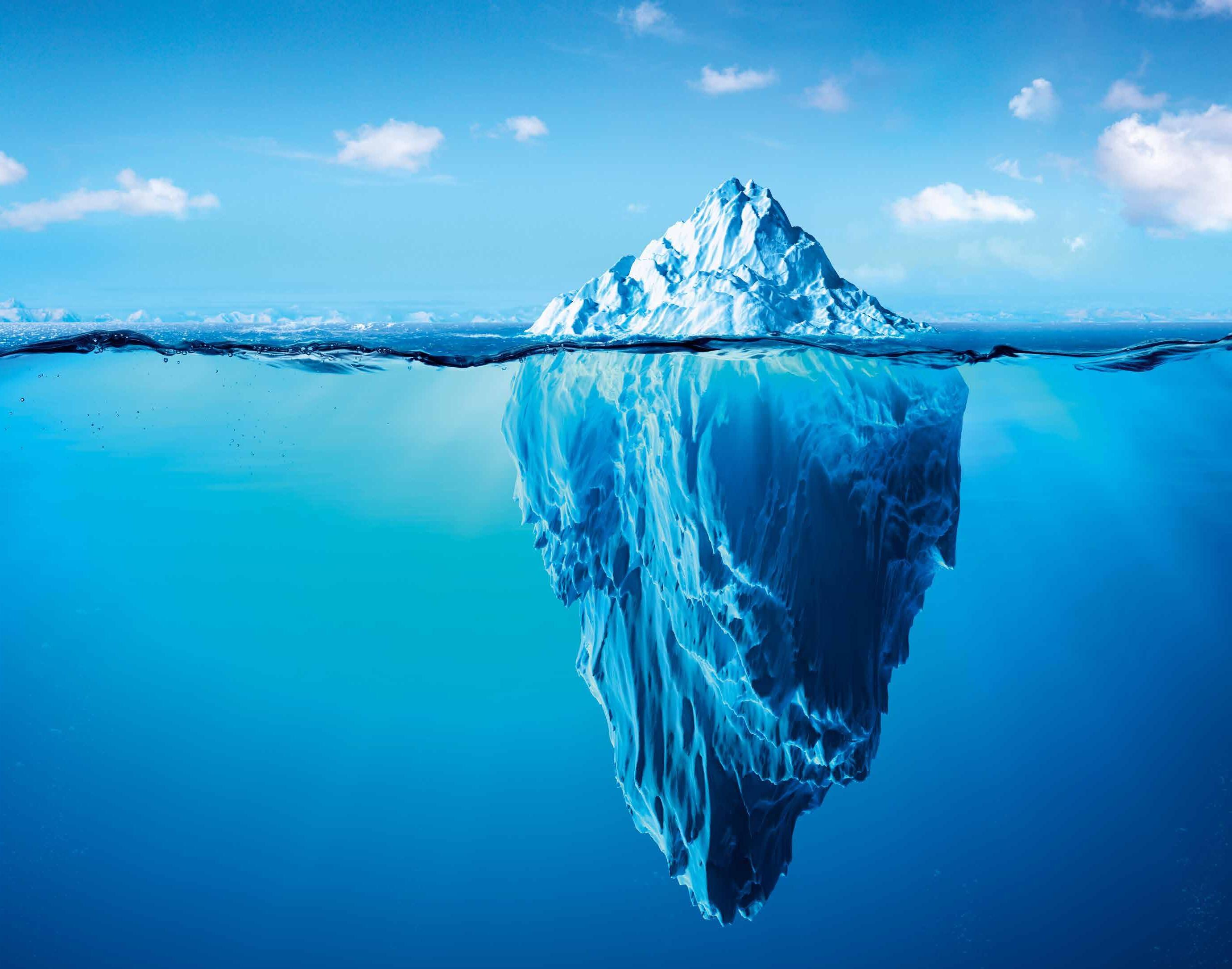
LIFE-TURBOALGOR CO 2
Project Objectives
The main objective of LIFE-TURBOALGOR CO₂ is to demonstrate the technical feasibility and commercial viability of an innovative solution to significantly improve the energy efficiency of transcritical refrigeration plants using CO₂ as a fluid. The solution, which consists of a new patented thermodynamic cycle with two heat exchangers, a Free Piston Expander (FPE) and a Fluid Control Unit (FCU), guarantees -
• an increase in energy efficiency of up to 19%.
• an increase in cooling capacity of up to 42%.
- addressing the technological barriers that have so far limited the adoption of CO₂ refrigeration systems.
Project Funding
Turboalgor is co-funded by the European Union LIFE22-CCM-IT-LIFETURBOALGOR CO2/101113796.

Project Consortium
The LIFE consortium, coordinated by TURBOALGOR, is composed as follows:
• TURBOALGOR SRL
• EPTA SPA
• C3 CONCRETE CUBE CERTAINTY S.R.L.
• NOESIS SRL
Contact Details
Project Coordinator, Turboalgor
Loc. Cimacolle, 464 - 06056 Massa Martana (PG) - Italy
T: +39 075 8955 1
E: maurizio.ascani@turboalgor.it
W: https://www.turboalgor.it/en/press/thelife-project
W: https://www.turboalgor.it/en/freeex
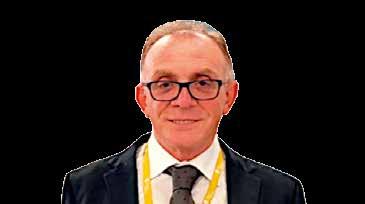
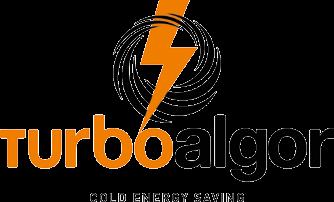
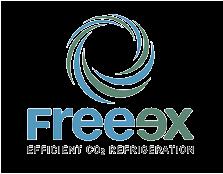
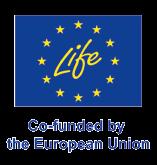