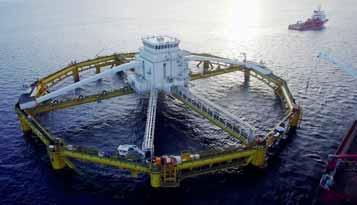
10 minute read
The Norwegian government provides incentives to boost the development of farming technology
by Eurofish
Novel cage systems can be
deployed offshore
Advertisement
The Norwegian seafood industry crossed another milestone earlier this year when exports in 2019 exceeded NOK100bn, according to the Norwegian Seafood Council. Over seven tenths of this value comes from the export of aquaculture products, a category which is comprehensively dominated by exports of salmon. N orway’s story with salmonids started in the 50s, when entrepreneurs introduced rainbow trout into primitive cages in the sea. Two decades later, salmon overtook rainbow trout as the most popular fi sh to farm. Development was rapid as more and more companies entered the industry, the number of permits rose, and the volumes produced increased exponentially. In the 20 years to 1990 production increased 340 times to 170,000 tonnes. By 2006 farmed fi sh exports accounted for more than half the value of total seafood exports. Th ree years later the Ministry of Fisheries and Coastal Aff airs launched a new strategy in support of a competitive and environmentally sustainable aquaculture industry. By 2015 Norway’s output was more than half the global production of Atlantic salmon. Th at year the authorities off ered the fi rst so-called development licences. Th ese are provisional licences intended to encourage the development of innovative technical solutions that would address some of the environmental and spatial challenges facing the aquaculture industry.
The twin challenge of escapes and sea lice are not yet fully overcome Among the challenges faced by the industry is that of fi sh escaping from their cages. Th ese fi sh represent both a fi nancial loss for the company that owns the fi sh and a threat to Salmar’s Ocean Farm can be raised and lowered in the water column and is highly automated to reduce the number of staff needed to operate it. diff erent users. In Turkey, the authorities pushed the industry off shore in the mid-2000s to defuse such confl icts and while the industry grumbled at fi rst, some advantages of the move became rapidly apparent. Th e deeper water and stronger currents were better both for the fi sh and the environment as it prevented a build-up of organic matter beneath the cages, the industry could no longer be accused of stepping on the toes of other users of the coast, and although producing off shore meant higher initial costs for the individual companies, it also laid a foundation of experience, knowledge, and technical competence from which the entire sector stood to gain.
Offshore farming may solve several issues In Norway, aquaculture systems using new technology that allows them to be sited off shore is considered one of the ways of expanding farmed fi sh production in a way that is environmentally sustainable — something that the government wants to encourage. According to a report (Havbruk til havs, 2018) from an inter-ministerial working group tasked with creating a legal framework for the sustainable development of off shore aquaculture, interest in off shore cultivation has been driven by a need for space unconstrained by other users’ claims, and by challenges in the form of environmental (impact of sea lice on wild stocks, build-up of organic matter, fi sh escapes) and fi sh health issues (for example, sea lice) experienced at traditional production sites. Th e release of provisional development licences (Utviklingstillatelser) in 2015 also contributed to the evolution of fi sh farming wild salmon stocks. Farmed and wild Atlantic salmon are genetically the same species (Salmo salar) and can interbreed. However, farmed salmon are selected for traits that make them suitable for life in a cage rather than in the wild. By breeding with wild salmon the farmed fi sh may induce genetic changes in the wild stock that could have an impact on population dynamics and viability. Th e fi sh farming industry takes these threats seriously and therefore funds the monitoring of rivers for escaped salmon, and commissions research into ways to prevent or reduce the problem. Th e salmon farming industry is also beleaguered with the issue of sea lice. Th ese marine parasitic crustaceans attach themselves to the salmon and feed on its mucus, skin, and blood, weakening the fi sh and making it prone to secondary infections. A measure of the extent of the problem is given by the number of lice per fi sh, which has declined from 1.34 to 0.96 in the decade to 2018, though in 2019 it increased to 1.04, according to Lusedata.no, a website based on data supplied to the Norwegian Food Safety Authority. As in other countries, such as Turkey, with big marine farming industries, Norway too must confront the issue of space. Coastal areas, where most fi sh farming is located, are also used for fi shing, shipping, energy generation, recreation, and a host of other activities. Th is can give rise to confl icts among the Salmar
solutions that could be deployed off shore. Allotted exclusively to projects that are innovative, contribute to solving one or more of the challenges currently facing the industry, and that call for signifi - cant investment, these licences enable companies to mitigate the risk of investing in promising fi sh farming technologies. In the two-year window (November 2015 to November 2017) during which applications for development licences were accepted over 100 bids were submitted.
Semi-submersible structures are among the ideas being tested
Ocean Farming, part of the SalMar Group, was the fi rst company to be granted a development licence for its Ocean Farm project. Th e structure draws heavily on the technology and principles that underpin the aquaculture industry as well as the off shore oil sector and consists of a semi-submersible cage that can be raised and lowered on pillars. Th e base and the sides of the cage will be covered with two layers of nets made with highly durable material. Th e outer layer is intended to protect the inner one from fl oating debris in the water or from other threats that could damage the inner net. All operations with the fi sh can be carried out within the structure itself, which, with the help of bulkheads, can be divided into three zones for different processes. Fish will be harvested by connecting a well boat to the cage with a hose. Th e system is largely automated and calls for just 3-4 people to carry out the daily operations and monitor the system. Research into improving fi sh welfare and reducing aquaculture’s environmental footprint will also be carried out on the Ocean Farm and the structure is expected to provide a basis for systems that reduce the risk of escapes.
Cages can be mobile too
Companies that have sought development licences are using diff erent designs for their fi sh farming structures which also have diff erent capabilities. Another company, Nordlaks Oppdrett, has proposed a long and narrow steel structure comprising a bow end with living quarters, a centre section with six 40-60 m deep net cages for the fi sh, and the stern with generators and an ensilage system. Th e structure will have two variations, one stationery and the other dynamic. Th e stationery version will be anchored at the bow allowing the direction of the structure to be infl uenced by currents, winds, and waves. In contrast, the dynamic version will use dynamic positioning and propulsion systems to maintain position without being moored but will also have the ability to move between areas depending on weather and environmental conditions. Th is fl exibility will enable the utilisation of far more exposed (and hitherto unused) areas when the weather is benign with the structure moving to more sheltered sites when conditions get rough. Th e sides of the centre section will be covered by a steel skirt that extends 10 m down from the surface and is intended to limit the impact of sea lice and protect the nets against fl oating debris. Other systems on board the structure will be used to load feed, load and unload fi sh, and process dead fi sh, among other operations.
Innovative ideas to deal with sea lice and escapes
Midt-Norsk Havbruk AS (MNH) has teamed up with Seafarming Systems AS to produce the Aquatraz. Named to evoke a legendary prison on Alcatraz island in the San Francisco bay from which few got away, the Aquatraz too is designed to
reduce the risk of escapes. It will also improve fi sh health and extend fi sh farming to new areas such as off - shore, according to the companies behind the structure. Th e Aquatraz is a rigid net pen that can be raised out of the water for maintenance or to disinfect the nets, which can be done by drying or freezing them in winter — both methods are environmentally friendly without the use of chemicals, and low cost. Th e upper part of the net pen is sealed from the surface to a depth of 8 m, a feature designed to reduce infestation with sea lice as these parasites are typically found in the upper part of the water column. Freshwater from deep in the sea will be pumped into the cage and circulated to ensure the fi sh are continuously supplied with oxygen-rich water at a constant temperature. A healthy environment has been created not only for the fi sh, but also for the workers on the structure as much of the heavy manual work has been automated. Th is also reduces the risk of human failure, one of the main reasons behind fi sh escapes. Another factor contributing to escapes is equipment damage, but as the Aquatraz’ rigid steel construction is built to standards used in ocean-going vessels and off - shore installations, it is more robust than typical net cages used today. Th e fi rst generation Aquatraz has already proved the viability of the concept with more rapid growth, lower mortality, reduced incidence of sea lice, and no fi sh escapes. Th e next generation of the cage has broader gangways and a new electrical system to raise and lower the cage, among other improvements.
A design that replaces the net altogether
Cages with nets are the most widespread way of producing salmon in Norway today. Th e challenge to develop the most environmentallyfriendly salmon farming system, however, has led AkvaDesign a company based in Brønnøysund on the west coast of central Norway, to design a structure that uses a bag rather than a net in which to grow the fi sh. Th is construction will enable the structure to be used in areas where farming fi sh using conventional net cages would not be permitted. Th e advantage of using a bag is that it reduces the impact of fi sh farming on the environment (nutrients from the fi sh production are removed from the bag and do not accumulate on the seabed) and the bag is fi lled with water pumped from a depth of about 20 m which reduces the problem of sea lice. Th e water inlet are at the top of the bag just under the water surface, while the outlet is at the base of the cage creating a downward fl owing current. Th e bag is attached to a fl oating plastic ring which is in turn fi xed to a surrounding concrete ring. Th e concrete structure is made of eight sections that are curved on the inside and fl at on the outside. When connected the inner surface forms a circle while the outer one forms an octagon. Th is allows several concrete rings to be attached together to create a complete system with multiple production units. To reduce the risk of escapes a net is fastened to each concrete ring. Th e net surrounds the bag providing a second layer of protection against escapes and contributing to the company’s claim of environmentally friendly salmon farming.
Th e structures portrayed here are just a fraction of the 20 or so designs that have been accepted by the authorities. Th ey reveal how the salmon farming industry is deploying technology to combat the most persistent issues that are aff ecting the sector. If successful, these technologies may have an impact on other cultivation methods such as rearing fi sh on land. In any case, the spirit that has driven the industry since the 50s seems to be alive and well and just as committed to fi nding solutions as it was 70 years ago.