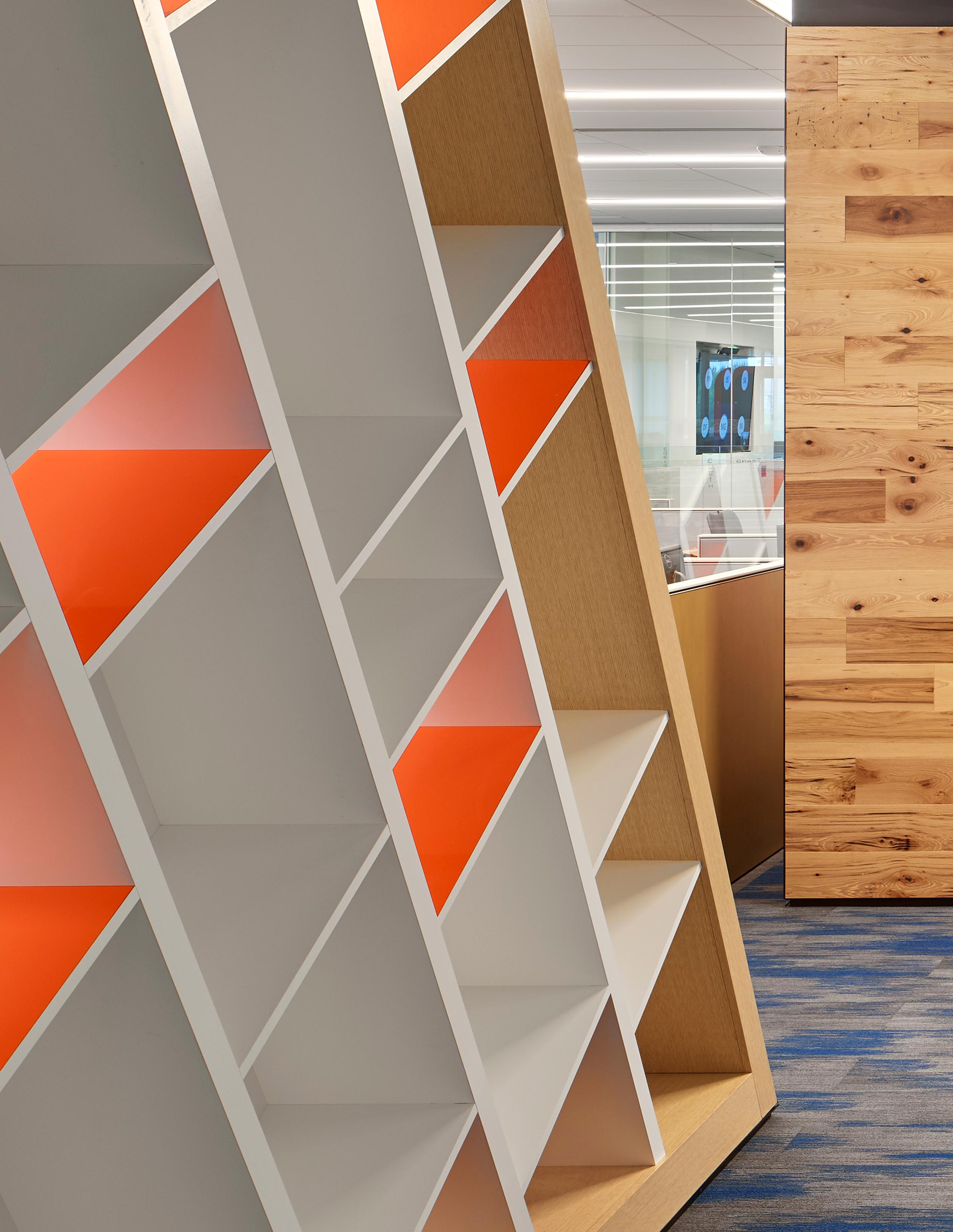

A LETTER FROM THE PRESIDENT
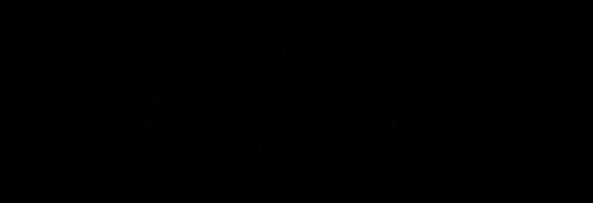
Dear Friends, Partners, and Colleagues,
After a brief hiatus, we are pleased to present you with the latest edition of EwingCole’s Momentum. Since our last issue, our Science & Technology practice has helped our clients take on challenges big and small. Even before the start of the pandemic nearly three years ago, many of us have had the pleasure of enjoying a front-row seat as our clients develop life-saving technologies that are transforming healthcare as we know it.
This issue of Momentum demonstrates how we have grown as a firm parallel to the strides made in cell & gene therapy and the broader biopharmaceutical industry.
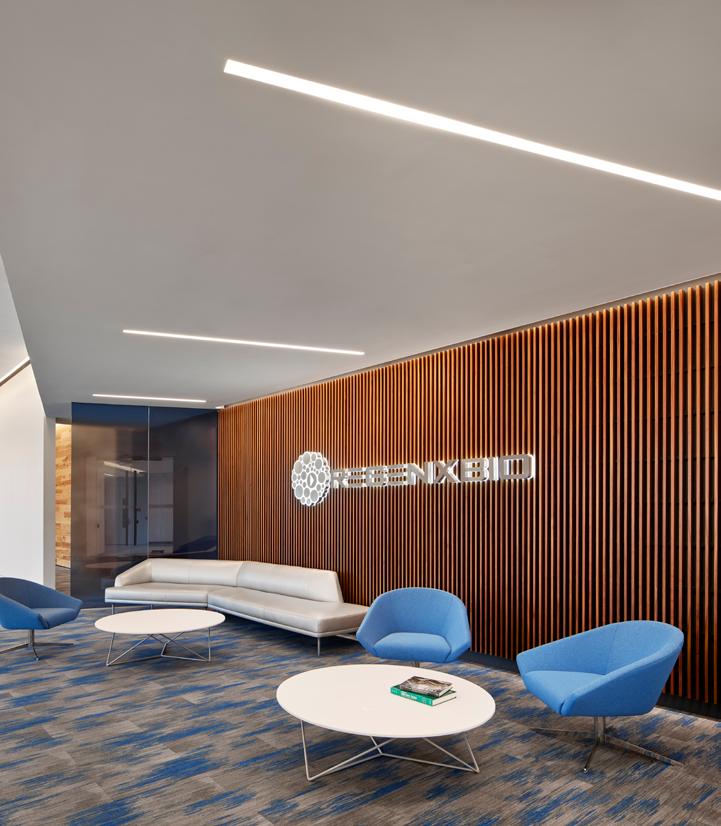
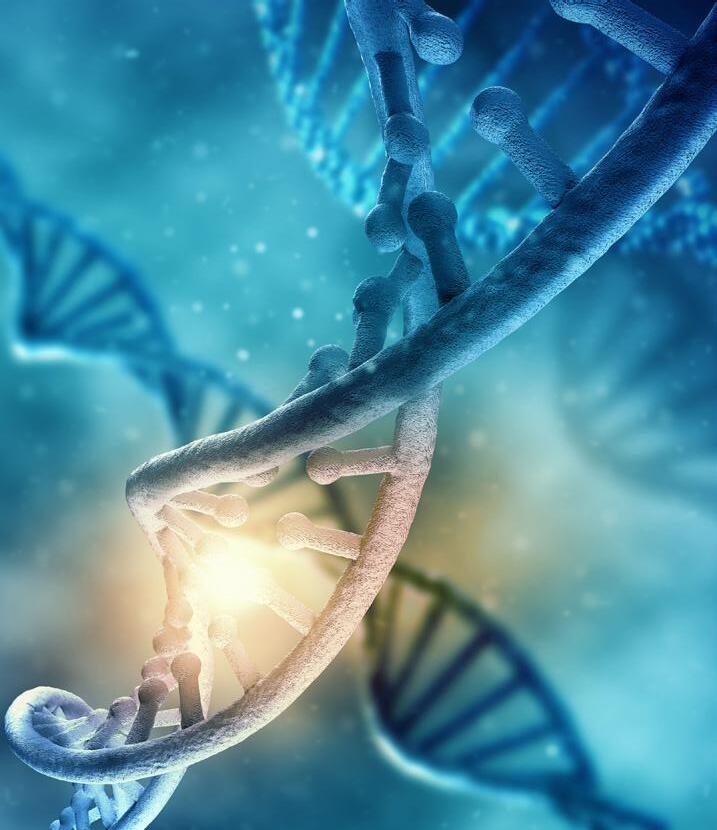
Please enjoy and share this issue of Momentum.
Sincerely,
Robert A. McConnell, AIA President
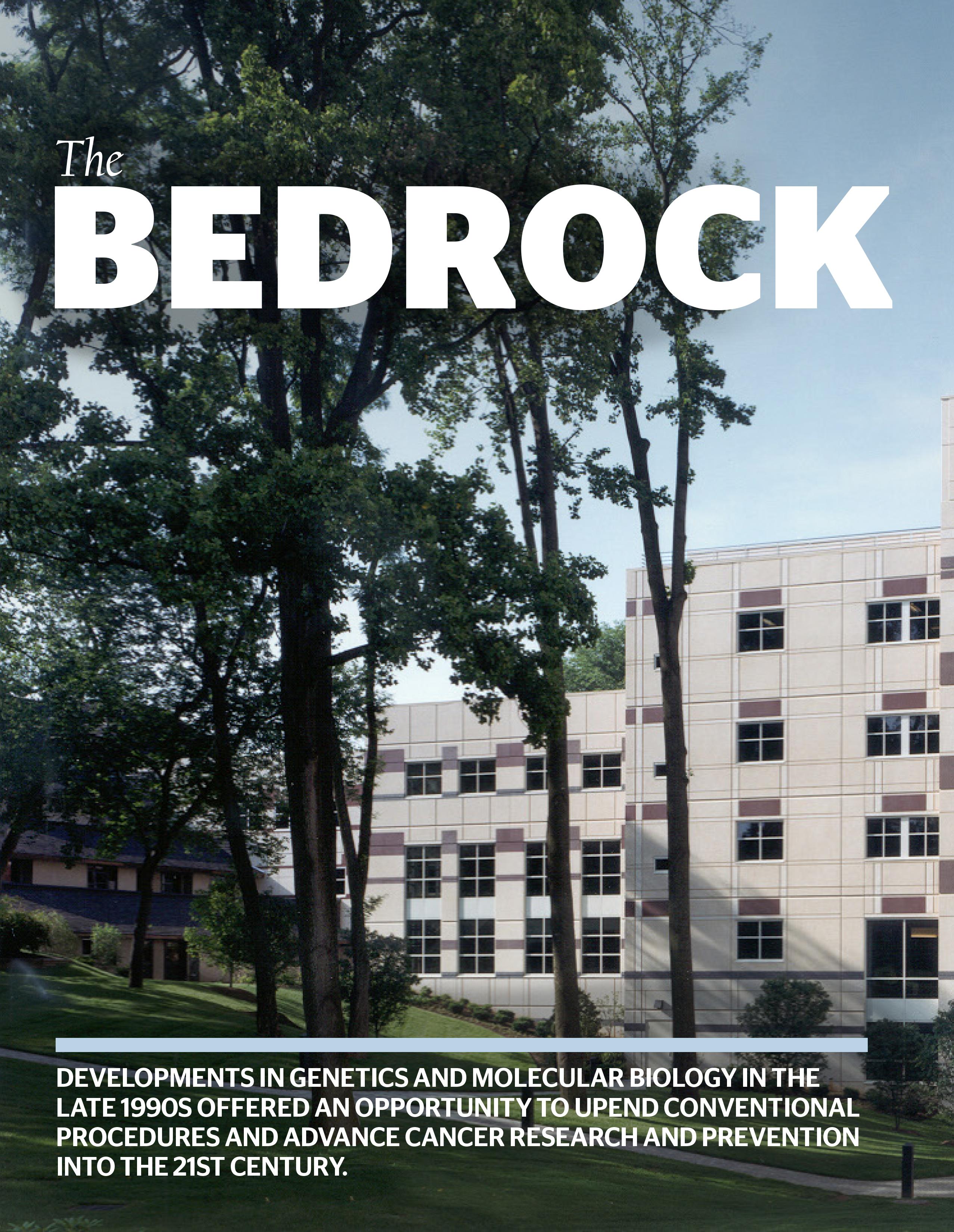

Fundraisers at the Fox Chase Cancer Center capitalized on this opportunity with a new dedicated facility for cancer prevention that would change user interaction to expand research programs and further preventative oncology over the next 25 years.
Fox Chase (now the Fox Chase Cancer Center at Temple Health) partnered with EwingCole to design the Cancer Prevention Pavilion, which opened in 2000. The 120,000 SF facility not only connected previously disparate buildings, but implemented inventive programming to unite research, diagnosis, risk counseling, and behavioral studies on campus for the first time.
“Fox Chase leaders challenged government and healthcare institutions to shift the structure for funding cancer treatment,” said Don Jones, FAIA, a Principal at EwingCole and designer for the project. “If given the resources to identify a gene or predilection for specific cancer types, they can pretreat you. It was radical.”
These changes to institutional models prompted a transformation in traditional healthcare design. Technological developments altered how the medical community interacts, expedites operations,
shares information, and better serves patients. In response, EwingCole’s team designed a centralized link to all operations on campus, allowing a diverse group of scientists and physicians to pursue a more focused and collaborative approach to cancer prevention. The design’s functionality results from creative design solutions that overcome programming challenges with limited benchmarks or precedents. Through comprehensive user engagement and thorough
Fox Chase brings the lab closer to each hospital unit and the patient closer to treatment. More than 20 years later, the facility continues accelerating the translation of laboratory discoveries to effective cancer prevention. These new capabilities and spatial connections were key to personalizing hospital processes and improving outcomes.
EwingCole’s design team implemented long-view solutions for open and flexible labs that support shared
planning, EwingCole developed an optimal healthcare facility with an inherent emphasis on collaboration and interconnectivity.

activity and adapt to evolving research and growing technological infrastructure. Universal exam rooms, multi-purpose areas, and large
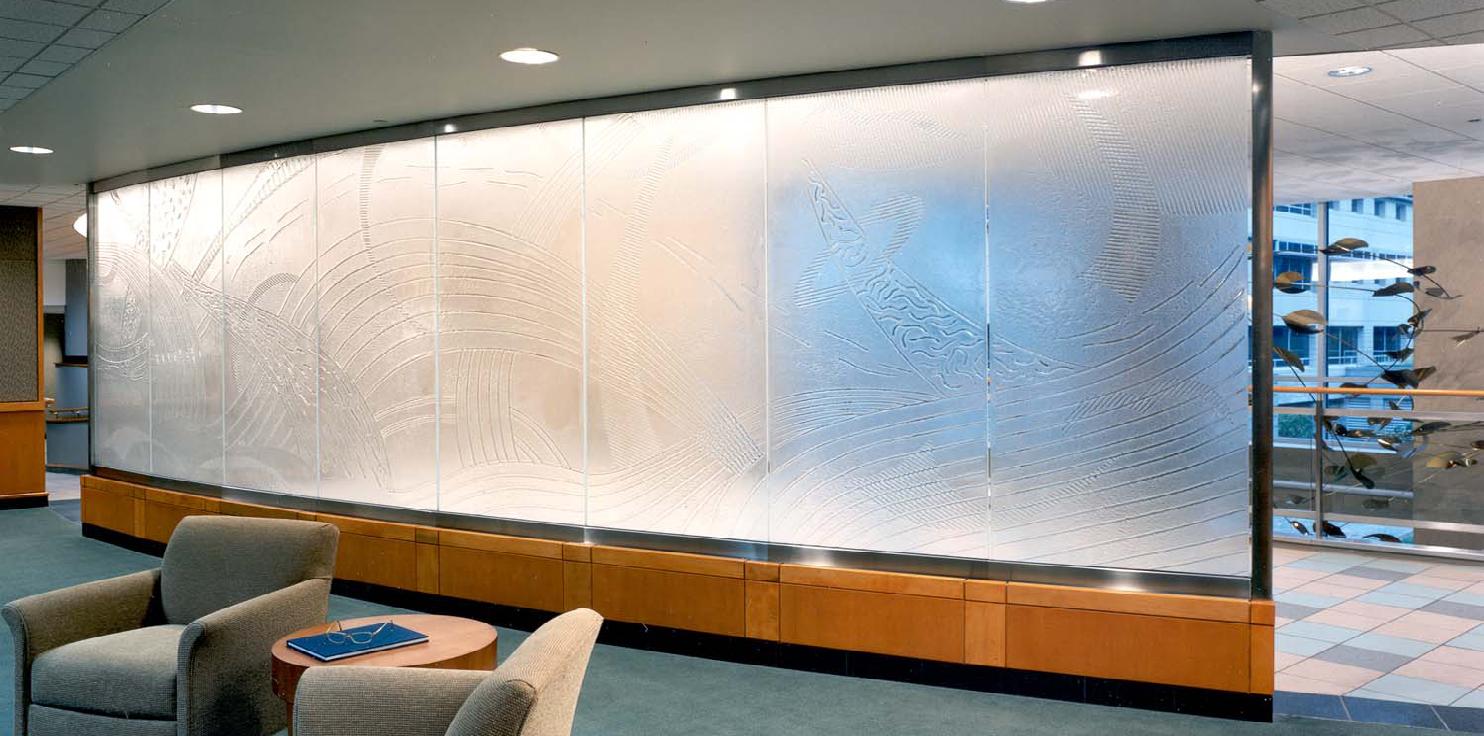
“THE WORKING RELATIONSHIP WITH FOX CHASE WAS INCREDIBLE. WE DID DEEP, INCLUSIVE CHARRETTES WITH EVERYBODY AT THE TABLE, INVITING ALL USER GROUPS TO WEIGH IN. [FOX CHASE] ENCOURAGED EVERYBODY TO FINISH THEIR THOUGHTS AND MADE SURE WE ALL HAD A VOICE.”- Don Jones, Principal, EwingCole
screening rooms accompany growing caseloads and entirely new care plans.
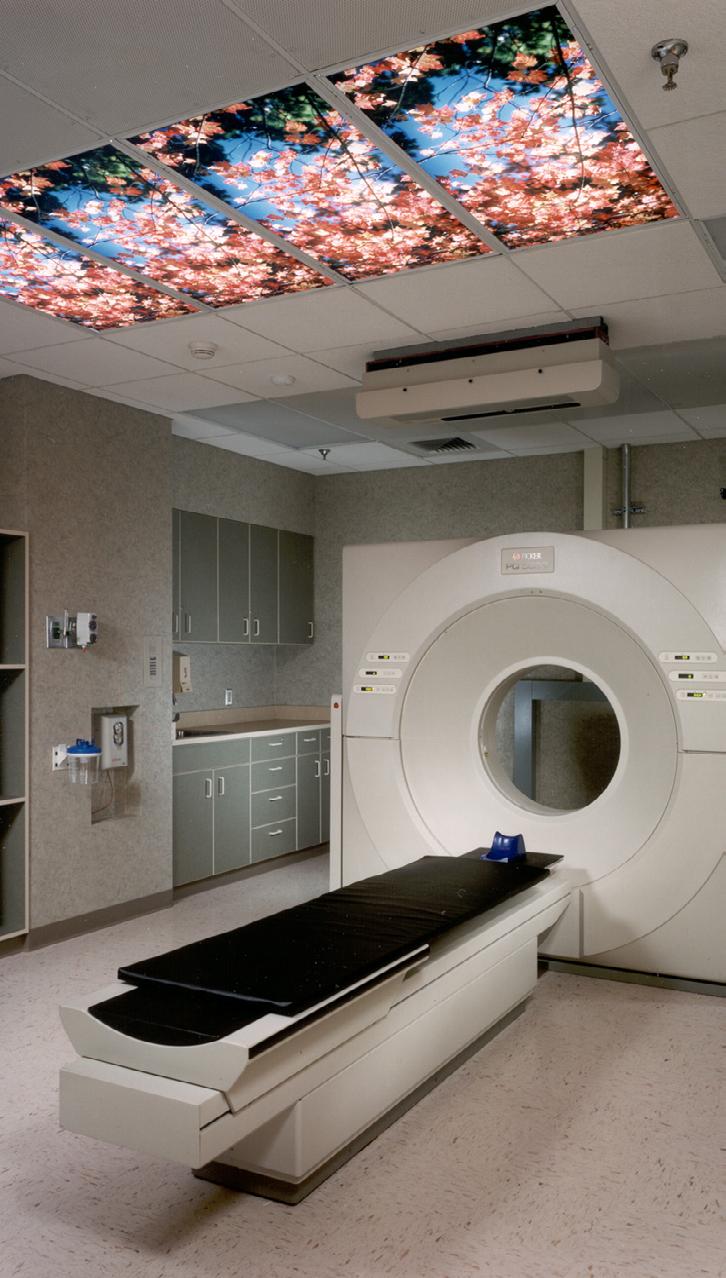
The Pavilion’s layout enables the migration of cancer research from antiquated departmental isolation to a highly collaborative, interconnected, and cohesive unit. The building facilitates the circular flow of research results to the patient and patient experience back to the lab—nobody plays a passive role. For the center
“We reminded each other that ‘hospital’ and ‘hospitality’ obviously derive from the same etymology, pointing us towards the essential need for shelter and comfort,” Jones said. “We borrowed from new ideas in hotel design that can serve patients and make them feel welcome.”
Although clinical surroundings are ground zero for safe, sanitary medical treatment, EwingCole recognized that
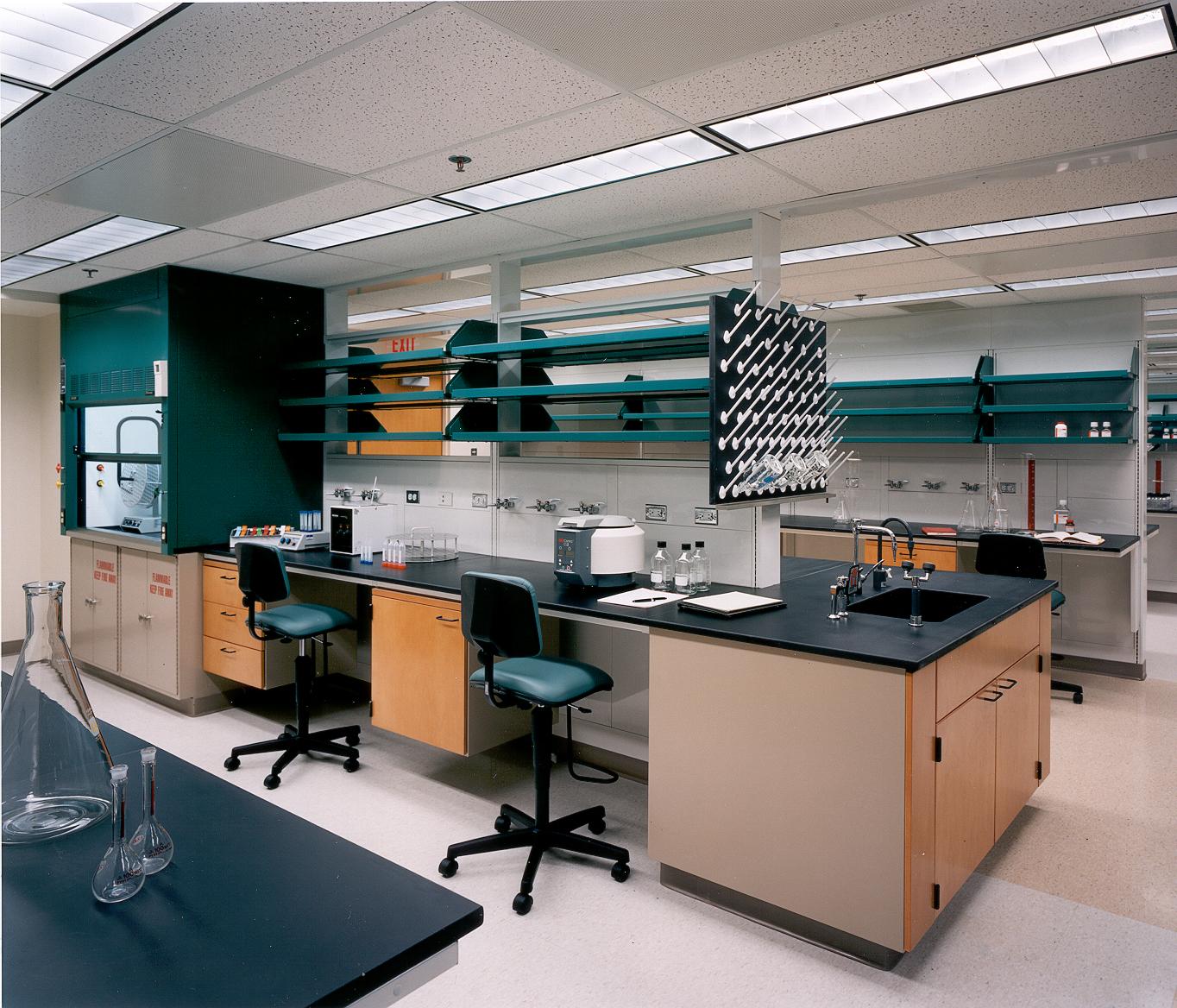
cancer care and prevention. To create a richer visitor experience, the design eschewed commonplace features often repetitive and doused with harsh lighting for relaxed gathering areas, natural finishes, and appropriate daylighting with a connection to the surrounding landscape.
“The site orientation positions conference rooms, labs, and other spaces previously cut off from the outside towards views of Burholme Park,” Jones said. “We prioritized space to give the first-floor atrium ample volume with tall windows for a flow of natural light, which was new for the campus.”
to succeed, it needed to support a positive patient experience, so EwingCole prioritized comfort for patients, families, and the at-risk community.
there was room for a vibrant visitor experience beyond a sterile base. The medical community and EwingCole acknowledge emotional wellness in addition to physical wellness in
The Pavilion’s shared, inclusive spaces provide a physical showcase that continues to encourage visitors during a period of uncertainty and unease. The composition offers a window into the rigorous methodology intrinsic to cancer prevention. More than 20 years after construction, the Pavilion endures as a conduit for breakthroughs in cancer prevention and as a place for optimism, enthusiasm, and trust for patients, families, and the at-risk community.
“WE REMINDED EACH OTHER THAT ‘HOSPITAL’ AND ‘HOSPITALITY’ OBVIOUSLY DERIVE FROM THE SAME ETYMOLOGY, POINTING US TOWARDS THE ESSENTIAL NEED FOR SHELTER AND COMFORT...”
- Don Jones, Principal, EwingCole
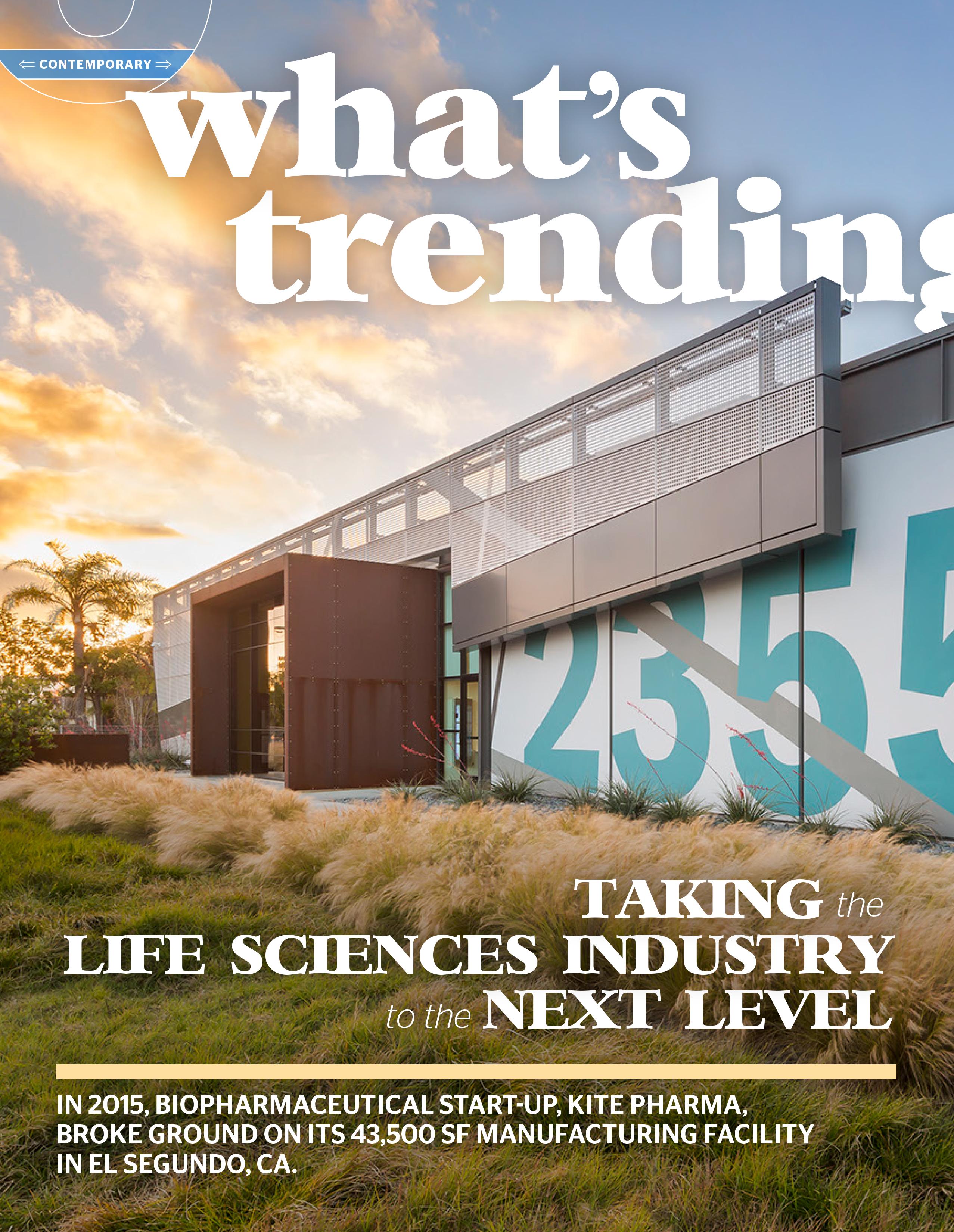
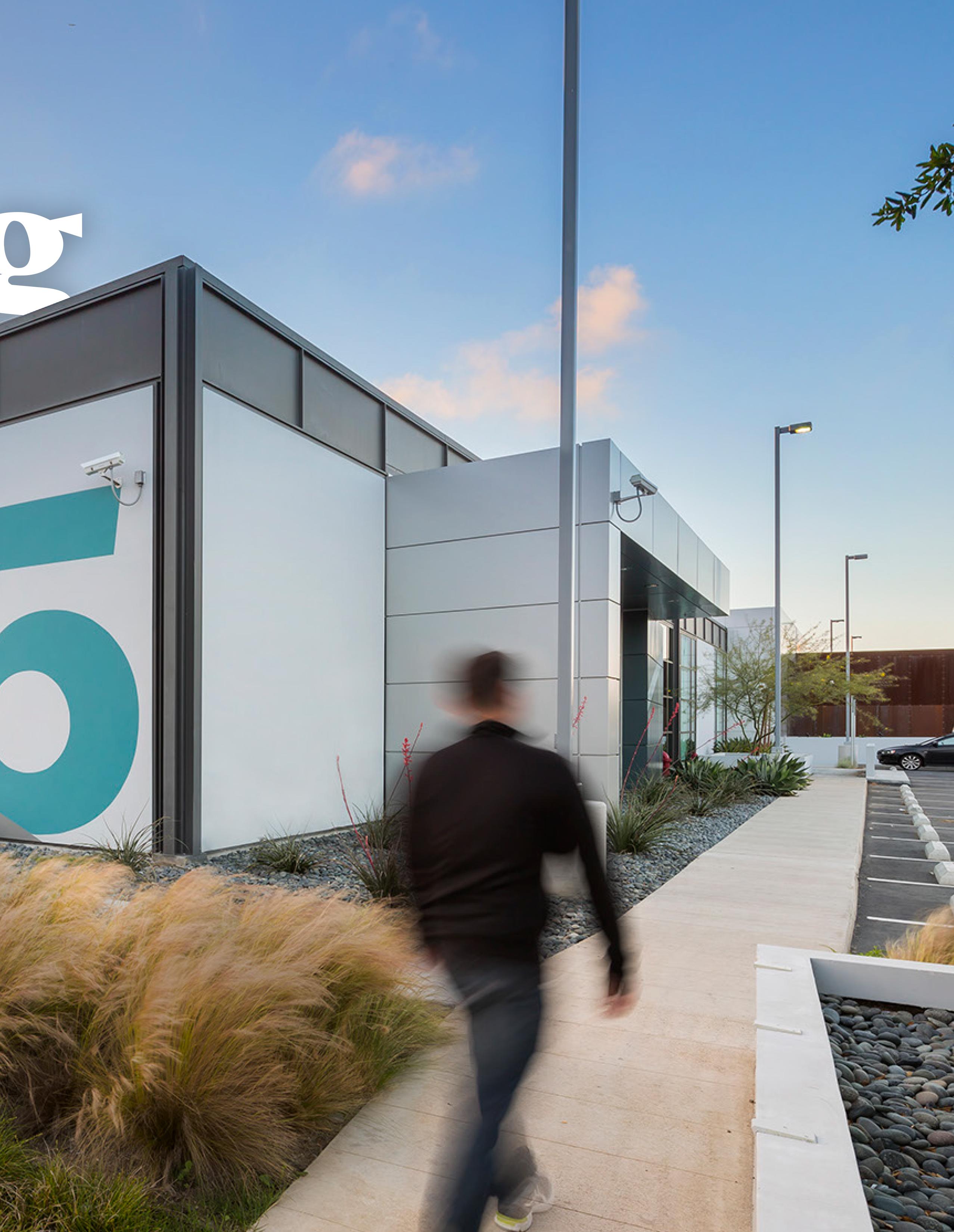
Agame-changer at the time, the facility was Kite’s first to manufacture immunotherapy cancer treatments. Kite’s KTE-C19 is an immunotherapy that leverages a patient’s immune system to attack and destroy cancer cells while leaving healthy cells unharmed. Since the El Segundo site opened in 2017, Kite was acquired by pharma giant Gilead Sciences for nearly $12 billion.
Designed by EwingCole, the facility can manufacture up to 5,000 patient therapies annually and produces clinical trial material for Kite’s other CAR and T-Cell receptor products. The project was as pivotal for EwingCole as it was for Kite. Since then, EwingCole has sown its role as a leading design firm for the industry, designing both clinical and commercial-scale manufacturing facilities and labs for clients such as REGENXBIO, Novartis, and Adaptive Biotechnologies.
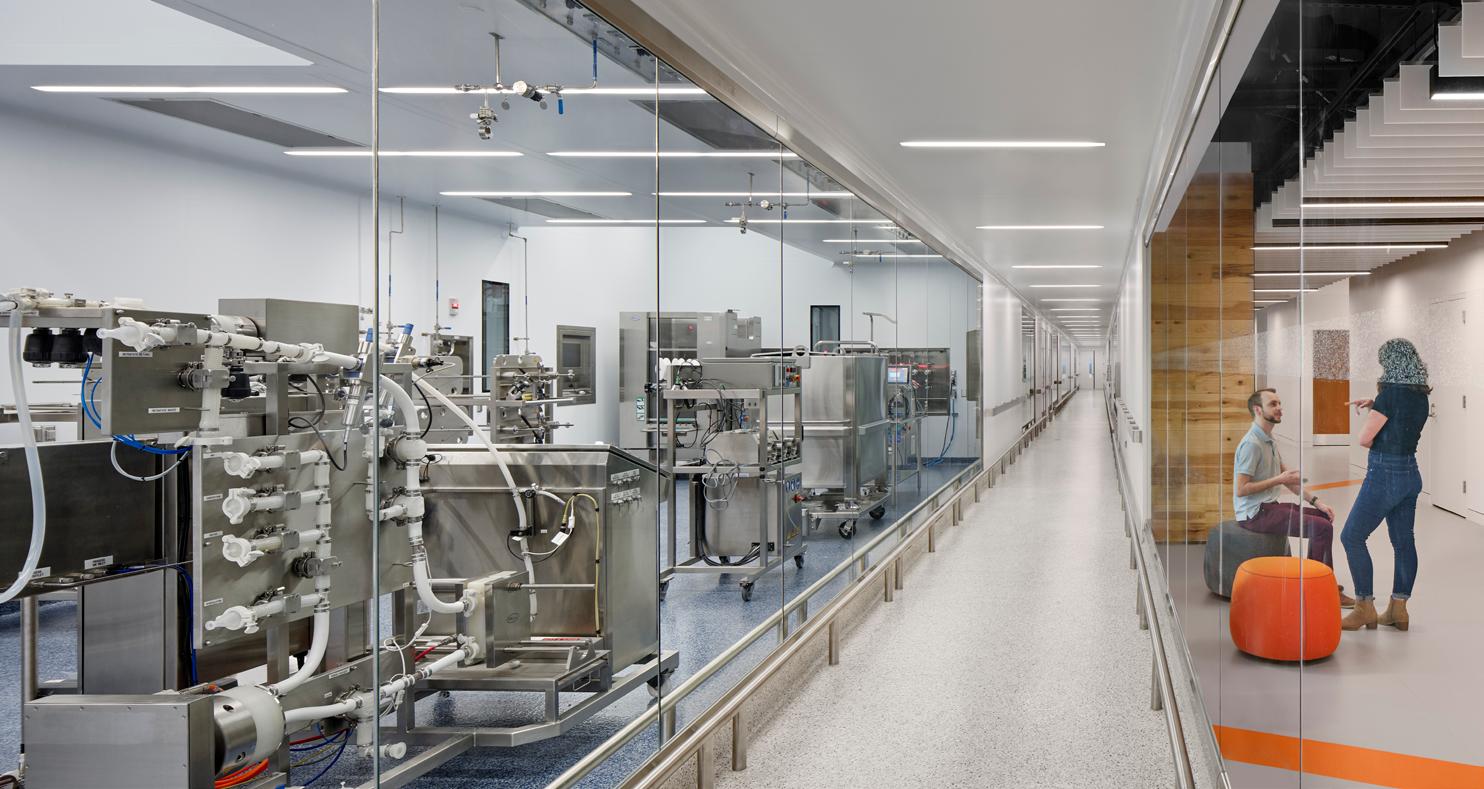
ON THE RISE
The industry has changed significantly since the El Segundo project first broke ground. The life sciences industry has become one of the fastest-rising professions in the United States, growing at a rate of 79 percent between 2001 and 2020, according to a CBRE report. Another report illustrates “all-time highs
reached in funding, job growth, and demand for lab space and construction projects” in 2021, with those numbers expected to continue climbing.
The talent that supports these companies is in no short supply either, but they tend to coalesce in dense urban areas or “tech corridors” that support research and attract investment. These trends are beginning to reshape how and where new manufacturing facilities are designed and built.
“Many of these companies need horizontal square footage, rather than vertical, to support their manufacturing operations, which forces them further away from their ‘innovation hubs’ and into the suburbs,” said EwingCole’s Director of Science & Technology, Sara Eastman, AIA, NCARB.
RAISING PRODUCTION
To enhance a facility’s speed-to-market and avoid supply chain complications and price increases, some companies are turning to existing buildings rather than ground-up, new construction. As a leading clinical-stage biotechnology company, REGENXBIO began ramping up its production capacity, the company decided that its headquarters building, originally designed as a multi-tenant lab and office building
already under construction, would now need to include 26,000 SF of cGMP manufacturing, including ISO 7, ISO 8, and controlled, not classified (CNC) cleanrooms.
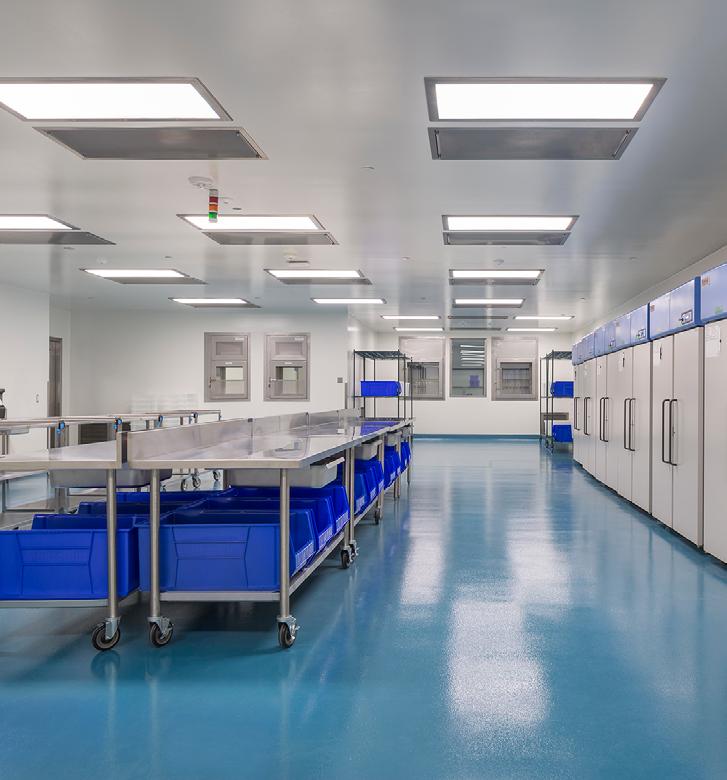
“This project gave us the opportunity to help a client — which had never done manufacturing at this scale — figure out how we could develop the most functional space for them within the scope of an existing building design,” said Sandra Kalanyan, RA, process architect, and planner for the project.
It was a mandate that was further complicated, Kalanyan said, by the client’s desire to keep as much of their operations in view to showcase the company’s capabilities and processes to investors and potential hires. The most significant piece of the puzzle was planning where everything would fit in the 132,000-SF, five-story building.
“Usually, production facilities are placed on the first or second story because the higher you go, the more difficult it becomes to install machinery and the material flows become more complex,” points out Marie Miller, RA, project architect at EwingCole.
The team was repeatedly challenged by the smaller footprint and divided floor plates of the lower floors while
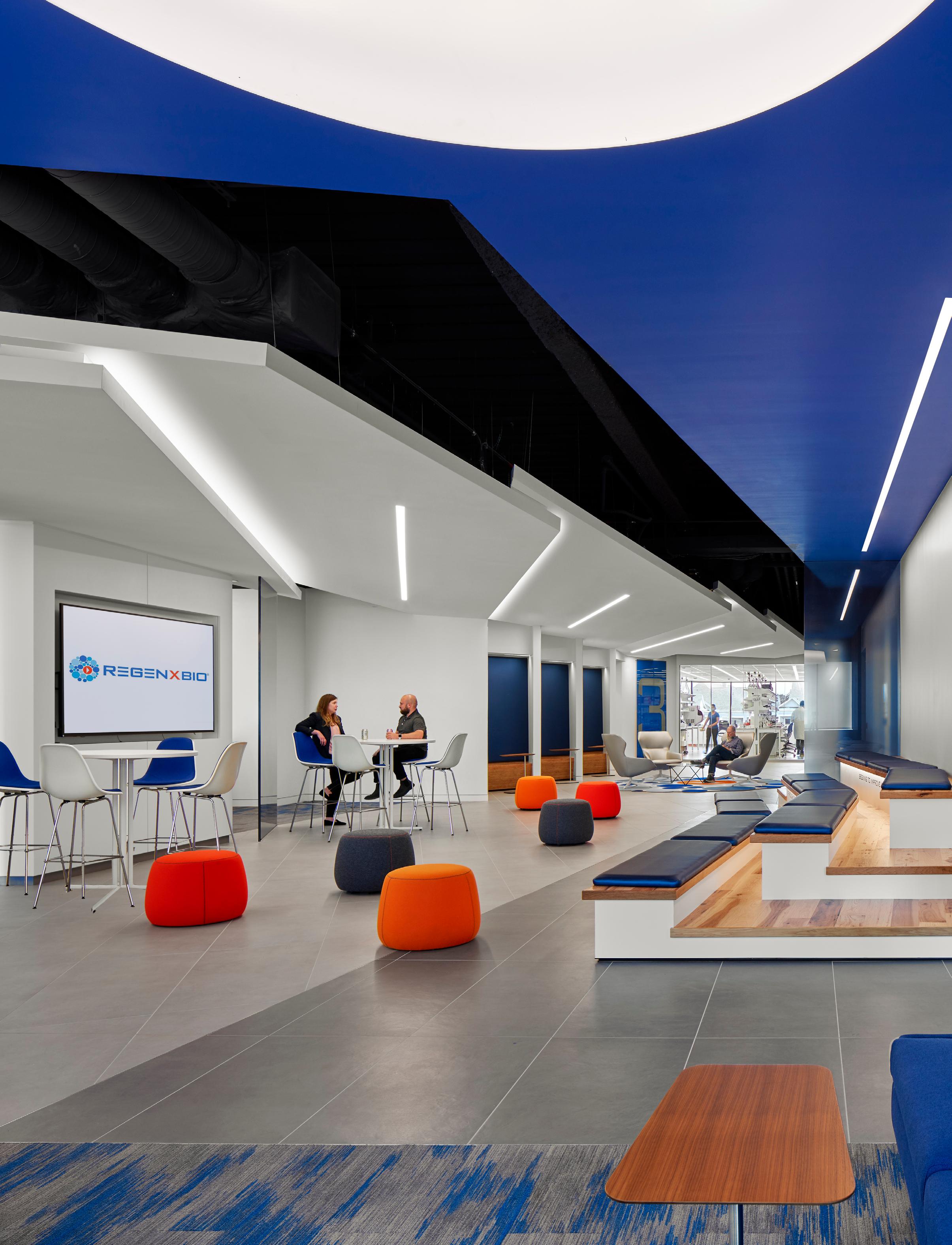
trying to accommodate space for mechanical systems and equipment. They determined that the only way to accommodate everything would be to place the manufacturing function on the top floor.
“That meant that we had to add a whole set of extra systems once the building’s functionality changed from being a mix of lab and office space to primarily labs and clean rooms,” explains mechanical engineer Dan Hazell, PE. “A clean room facility usually requires double the amount of actual production space to account for utilities, services, and maintenance
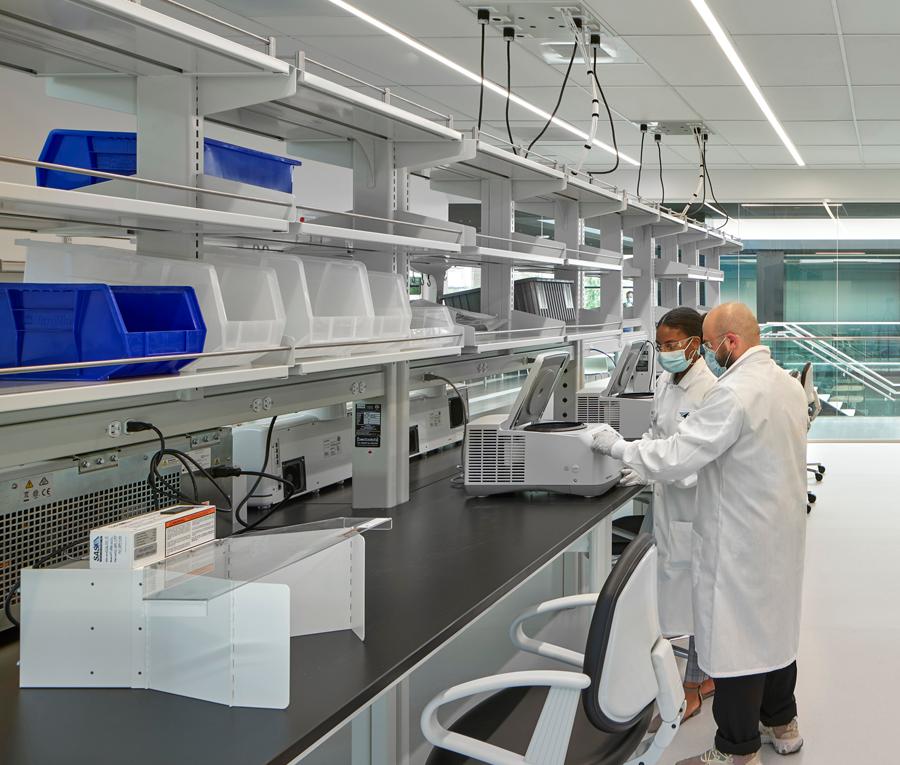
access to the cleanroom, but we also needed to push a diverse array of other mechanical, electrical, and process systems into the building.”
In an inventive solution, the team designed the cleanroom suite on the top floor, increased the floor height, and added the largest penthouse that the municipality would allow without being considered another floor. The penthouse space was leveraged to accommodate additional infrastructure items that could eventually be serviced without any disruption to operations. In addition to this extra space, the rest of the building’s layout includes a
first-floor lobby, a conference center, and a mix of offices and labs on the third floor. The second floor was left as a shell, ready to be transformed into more office space for future employees.
ELEVATING EXPERIENCES
Built on 20 acres in Urbana, MD, Kite's latest manufacturing facility creates more transparency and collaboration between the company's administrative and production teams in one location. At 200,000 SF, the cutting-edge facility includes an office building, a GMP manufacturing warehouse, and specialized clean rooms. The facility runs 24/7, so Kite sought to leverage the
design to foster communication and productivity between the employees on both sides of the operation.
“Kite employs a highly skilled labor force and with that comes a responsibility to create a collaborative culture where training and interactions are prized,” said Brett Spearman, AIA, LEED AP. “Kite suggested an alternative to the common term 'amenity space,' preferring to think of the communal areas as 'productivity' spaces."
These productivity spaces, whether in the cafeteria with a full-service kitchen,
pocket parks, or in a training room, are becoming more common throughout the industry. They allow employees to work in varying environments, with connections to the outdoors and round-the-clock services modern office workers have come to expect.
BUMPING UP FLEXIBILITY
The COVID-19 pandemic reinforced the need for flexibility in biopharmaceutical spaces. For example, Pfizer’s Chesterfield, MO facility was able to pivot its facilities toward developing and manufacturing one of the critical COVID-19 vaccines. The facility’s flexible laboratory layout allowed for sudden

equipment and personnel shifts without disrupting its other operations.
Pfizer scaled up methods and processes at its Chesterfield site required to produce large volumes of its COVID-19 vaccine, including hiring 150 additional personnel to manage the workload. The company was also able to quickly scale up its manufacturing capacity and distribution infrastructure to increase swift vaccine availability.
"The testing of all of the manufacturing controls and consistency of the product that was done here,” Pfizer's
Kite Pharma - Urbana, MD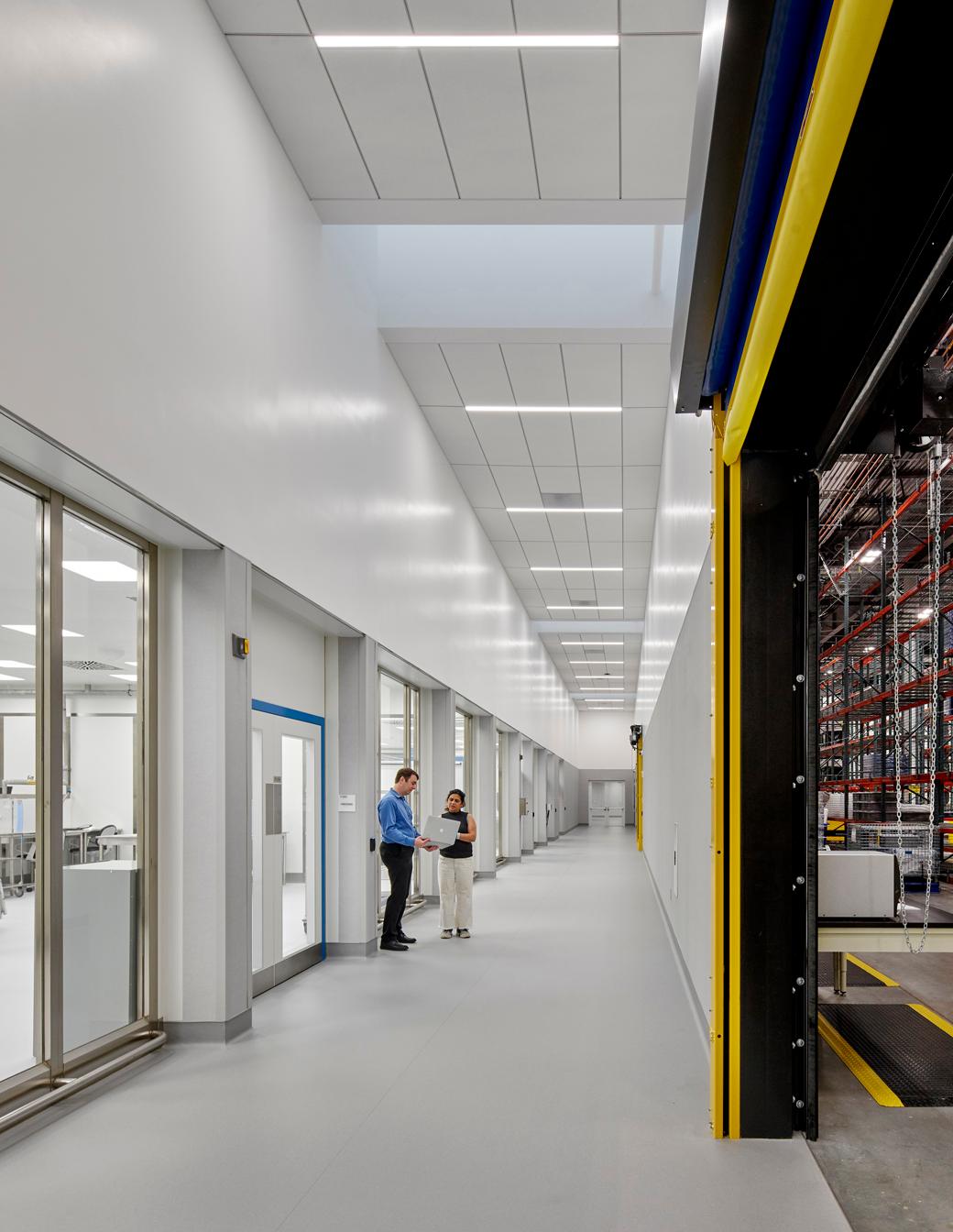
Vice President of Transformational Technology, Justin Sperry told KSDK News in St. Louis. “Every dose that was distributed in the United States was tested in our quality labs here in the St. Louis site."

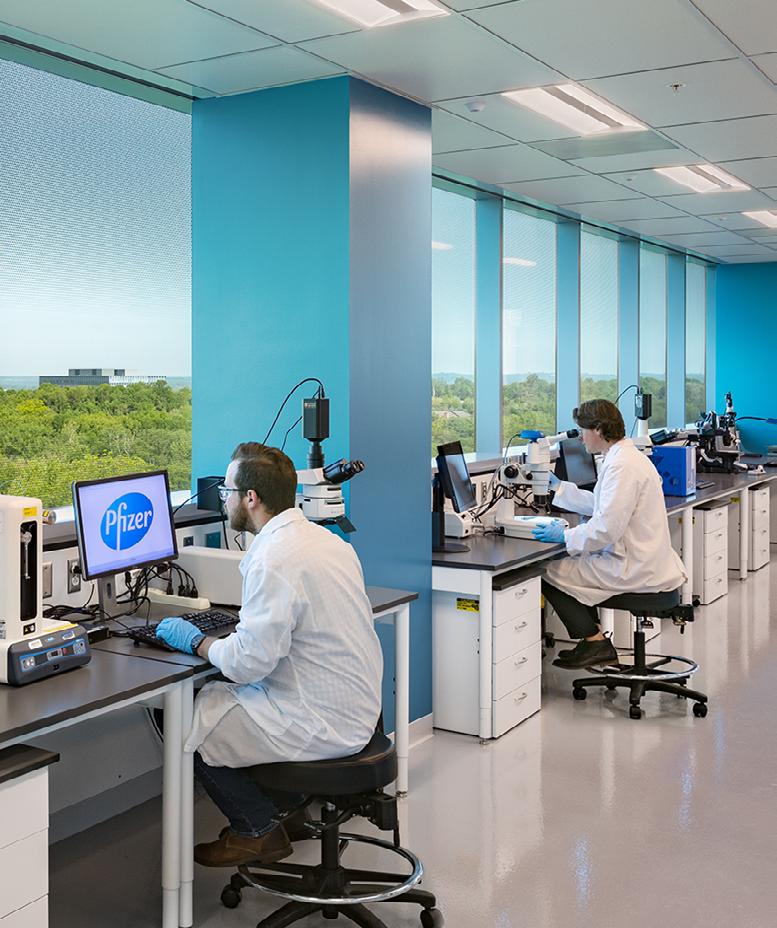
More than 500 million doses of the Pfizer vaccine were distributed in the United States by the end of 2021.
facility, for example, is designed with 78,000 SF of additional shell space for future expansion that would double the manufacturing production capacity while maintaining the facility's operations.
This is accomplished by a network of utilities above the manufacturing facility cleanrooms supported by a structural system separate from the
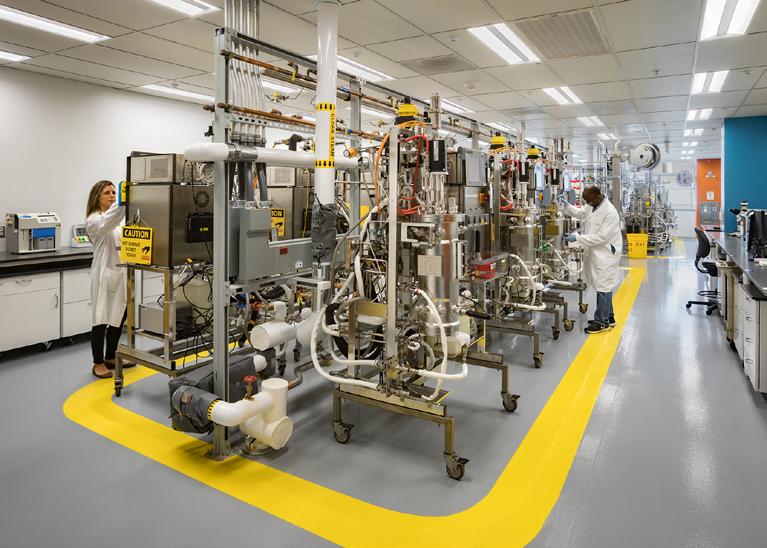
Swift advancements in technology and product development, or emerging diseases, also impact a design's flexibility and adaptability. Effective flexibility, however, is more than just adding shell space. It's about providing well-planned shell space. Kite's Urbana
structure of the building. These spaces are accessible via a walkable ceiling where electrical and HVAC needs connect into the manufacturing suites below, creating ultimate flexibility for changes in products and workflow without disruption.
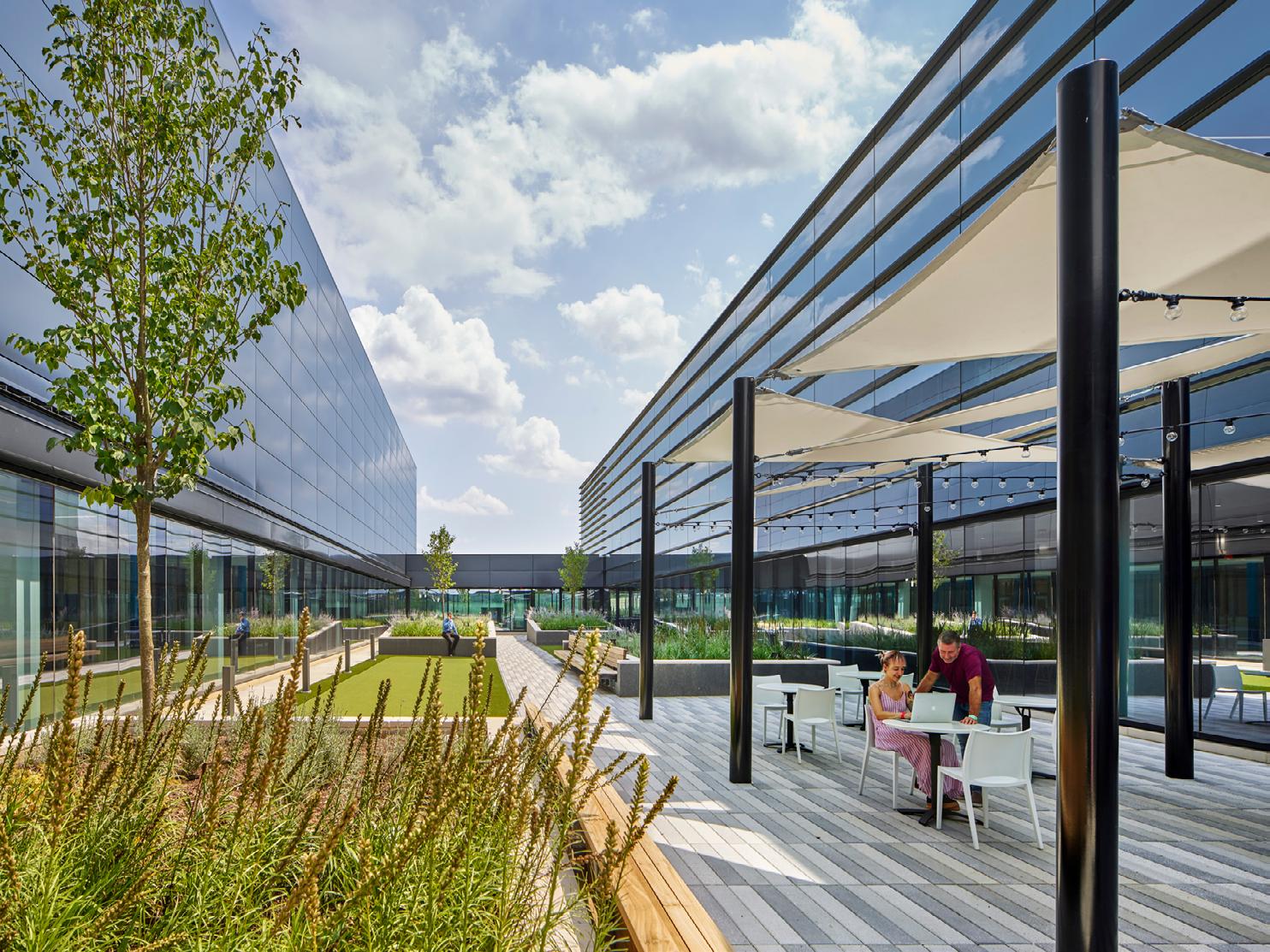
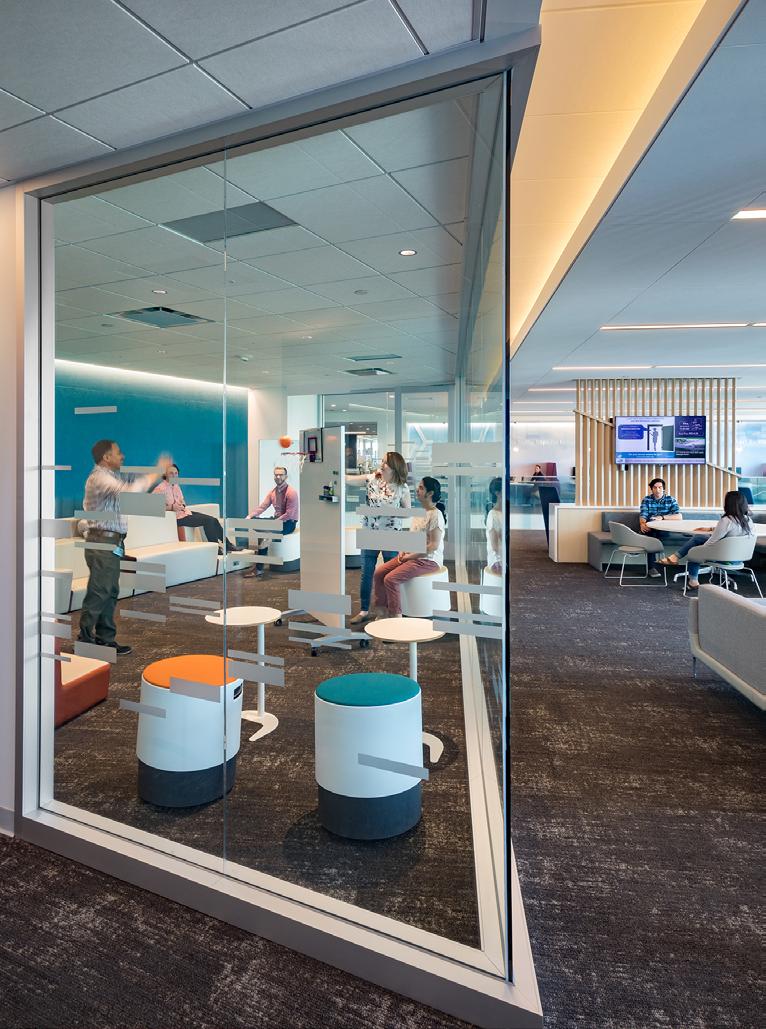
“OUR CLIENTS HAVE TO QUICKLY ADAPT IN AN INDUSTRY THAT EXPERIENCES SUDDEN SHIFTS IN TECHNOLOGICAL CAPABILITIES, NEEDS, AND INVESTMENTS. AS PLANNERS AND DESIGNERS, OUR AIM IS TO BE FORWARD-THINKING, SO THEY ARE BESTPOSITIONED FOR THOSE CHANGES.”
- Sara Eastman, Director of Science & Technology, EwingColePfizer Pfizer Pfizer Pfizer Kite Pharma - Urbana, MD
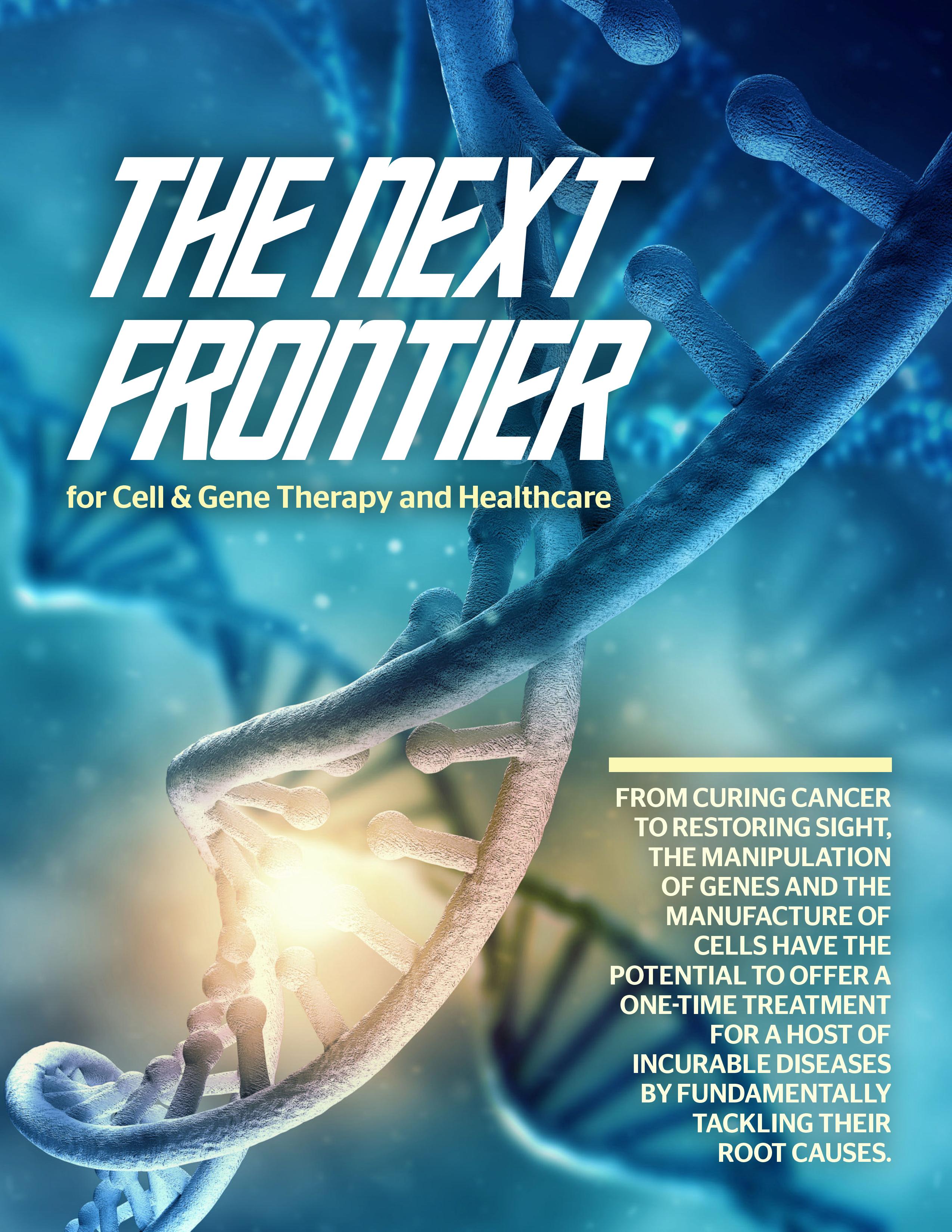
t’s no surprise, then, that pharmaceutical and biotech companies — and increasingly healthcare providers and academic research institutions — are interested in pursuing what’s currently a $3 billion market and is pegged to reach upwards of $6 billion in the next five years.
“Now that cell and gene therapy is proven viable, everyone is competing for a lead in the market,” said Salvador Ceja, AIA, EwingCole principal in the Science and Technology practice. “That means we’re seeing a lot of acquisitions and partnerships. And with them comes a need for new buildings that can accommodate different approaches and therapies and can pivot when any particular one shows commercial potential.”
The building boom promises to allow EwingCole and its clients — whether hospitals or universities, biotech or pharmaceutical firms — the chance to design facilities that best enable these emerging technologies to save lives.
“EwingCole is in a unique position to help all sides,” said Jared Loos, AIA, PE, principal and CEO. “We pride ourselves on the fact that we have overlap between the expertise of our studios and the depth of knowledge of our teams. There’s space for everyone in this field. There are a range of opportunities for our clients, from those that do testing to those that provide customized patient-specific treatments. And we’re seeing all kinds of blurring of the dividing lines between them.”
SIMPLIFYING THE PROCESS
One effective treatment piquing the interest of healthcare providers is autologous cell and gene therapy, a treatment process that uses a patient’s own cells. The cells are isolated and extracted, reengineered, expanded and contracted, and infused back into the patient. Healthcare providers are just beginning to explore its possibilities, but for now, the process can be arduous.

“Right now, these treatment procedures can be inefficient, lengthy, and expensive,” Ceja said.
A typical scenario can involve a sick patient in one place getting their blood drawn and then sent across the country to a facility, where their cells are processed and modified, or new ones are incubated and grown, and
There’s a growing realization that some — but certainly not all — of these procedures can be done at the inpatient facility,” Ceja said. “But patient beds, not clean labs, are a hospital’s core business, so a firm such as EwingCole can help bridge the gap.”
Because the process of autologous cell and gene manufacturing as an inpatient treatment is so new, the industry has some hurdles to overcome, particularly by way of reimbursement. However, consolidating the workflow of the process reduces the risks and drives down manufacturing costs. This has led healthcare systems to try and accumulate the equipment and space needed to close the process within a single facility or campus, pushing them beyond their intended use and forcing building programs to cater to systems and technology they were not intended to support.
“Most healthcare systems lack several key features of a GMP facility or have insufficient capacity to handle the current and future load of cell product and bioengineered product manufacturing on-site,” Loos said. “Because EwingCole is an integrated firm, with architects and engineers working side-by-side and a diverse healthcare, science and technology, and education portfolio, we know we can repurpose and right-size design programs to fit the personalized care delivery model.”
then sent back to their hometown. Manufacturing the cells is an expensive undertaking and at every step of what can be a weeks-long journey, there’s the risk of sample contamination or loss.
A disjointed system causes these inefficiencies. Testing, manufacturing, and the patients are seldom in the same place at once. To streamline the process, clients are beginning to explore the possibilities of bringing this system under one roof.
“THERE’S A GROWING REALIZATION THAT SOME — BUT CERTAINLY NOT ALL — OF THESE PROCEDURES CAN BE DONE AT THE INPATIENT FACILITY, BUT PATIENT BEDS, NOT CLEAN LABS, ARE A HOSPITAL’S CORE BUSINESS, SO A FIRM SUCH AS EWINGCOLE CAN HELP BRIDGE THE GAP.”
- Salvador Ceja, Principal