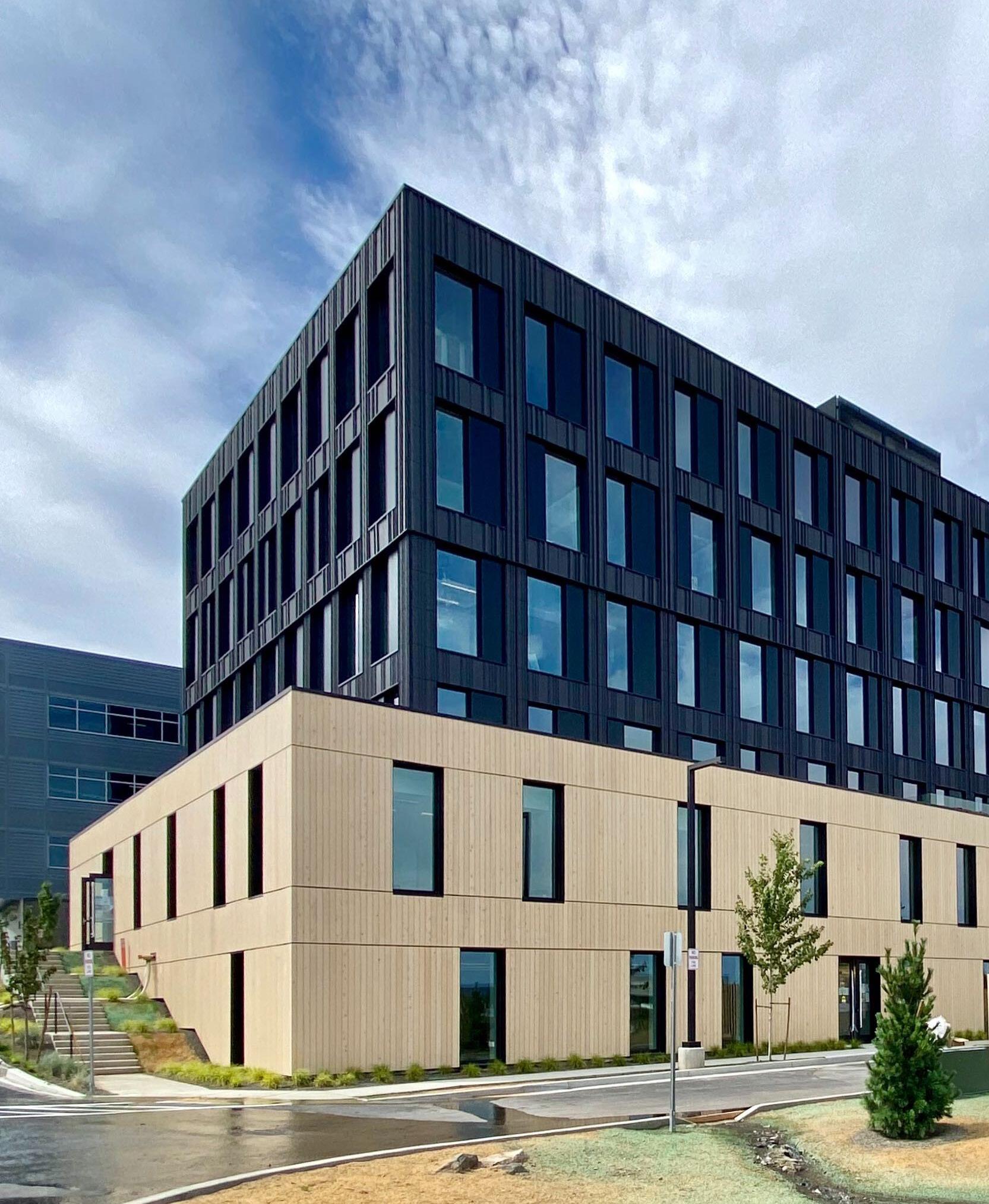
13 minute read
Transformative Vision
LYST CATA
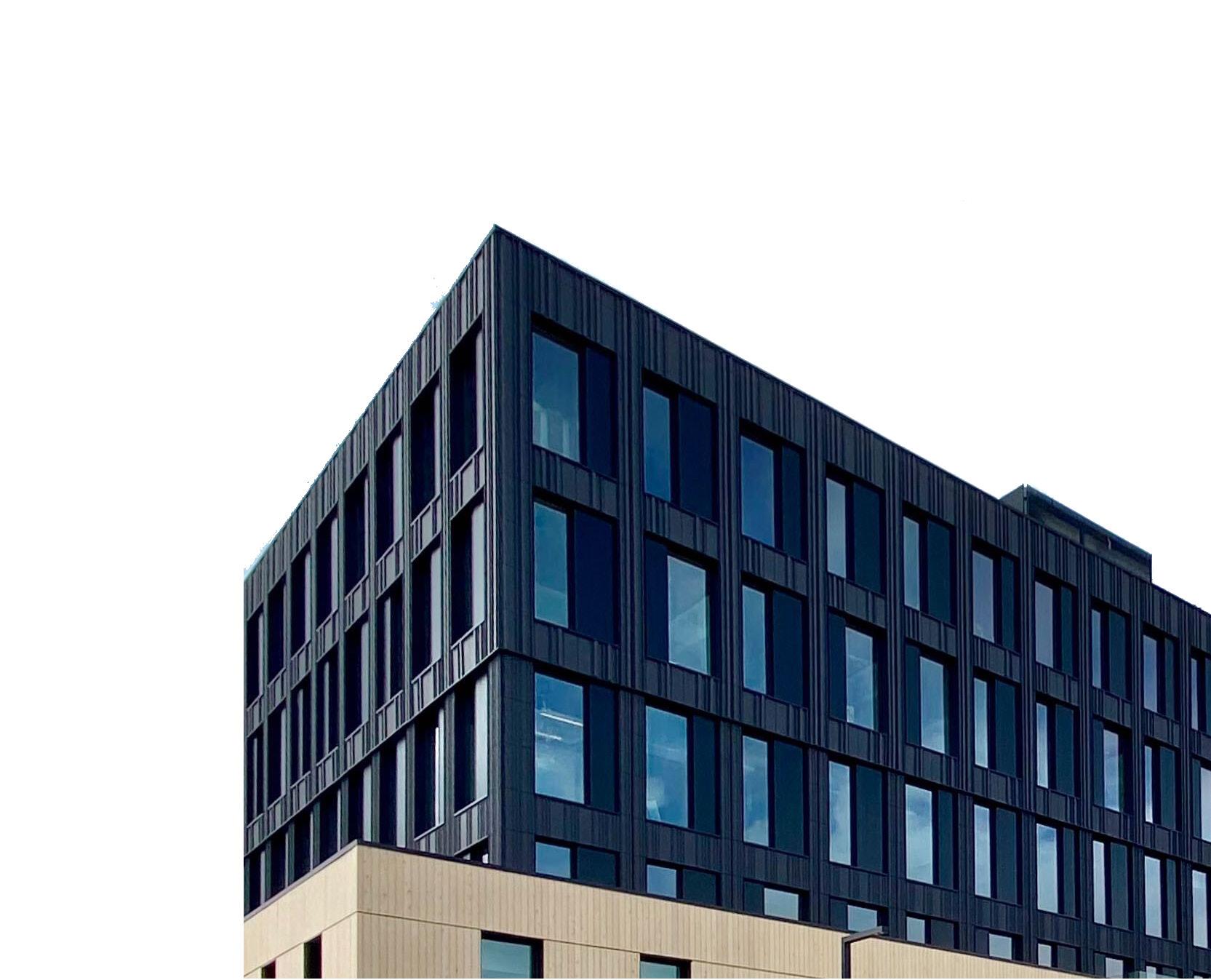
LYST CATA
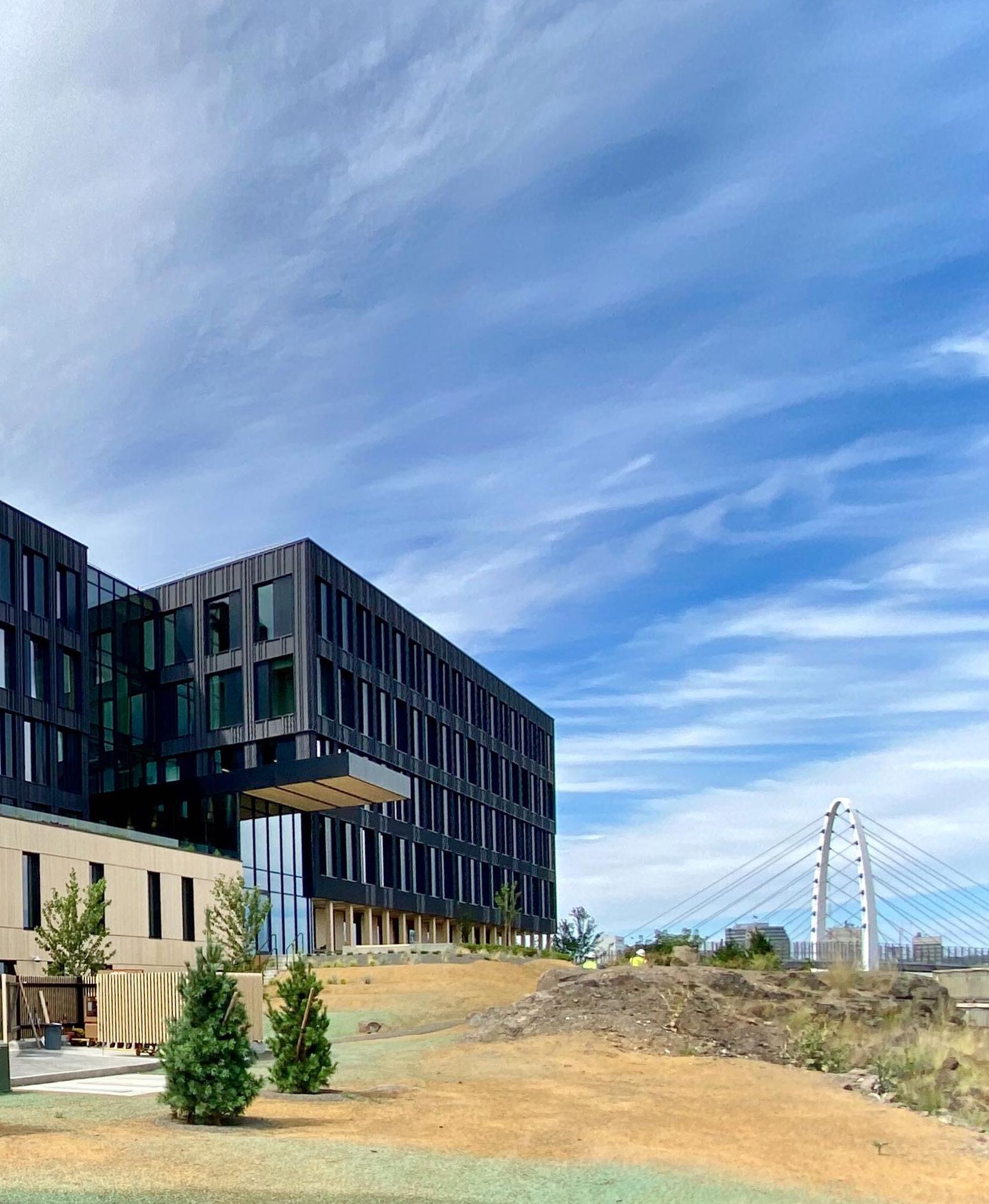
TRANSFORMATIVE
Story by Leilah Langley Photos by Chris Thompson
Innovators can see a future where others see only blight. When they look across an industrialized riverscape, over scrubby railroad tracks to the “wrong” side of town, they see opportunity. The innovators who sparked the South Landing Project in Spokane’s East Sprague neighborhood are leading a powerful transformation. Not only will the new Catalyst they’ve championed help change the way the world constructs buildings, it will alter for the better the way students learn and companies do business — a revolution that Eastern Washington University will be right in the middle of.
The South Landing Project started in 2004 with a bridge — a pedestrian overpass designed to connect the downtown Spokane core, the University District and the medical complexes along the Lower South Hill. Bringing these areas together, the thinking went, was key to encouraging their economic advancement, especially in the burgeoning health science and technology industries.
Fifteen years after its conception, the University District Gateway Bridge opened to foot and bicycle traffic, immediately becoming a new landmark on the Spokane skyline. A 120-foot tall concrete arch seemed to call, “This way to the future.” But the future on the other side of the railroad tracks wasn’t immediately clear to the community. For decades, East Sprague had been an underserved neighborhood often associated with street crime and prostitution.
“When the University District Bridge was funded, it was really exciting, but all of the sudden folks said, ‘What’s going to go on the south side?’” recalls Latisha Hill, vice president of community and economic vitality for Avista. The utility owns the land on the south side of the Gateway Bridge. It was Avista chairman, and CEO at the time, Scott Morris who had the vision to create what he called the “five smartest blocks in the world” there, Hill says.
“We had not only an opportunity, but an obligation to create something that could be really special and long lasting for the next phase of the University District and its connection with health care, business, industry and innovation.”
With this vision in mind, Avista purchased several parcels of land, then partnered with some of the brightest construction minds in the nation to develop them. The goal, ultimately, was to give East Sprague a new identity as a leader in energy innovation, environmentally conscious construction and sustainability.
The heart of the South Landing Project is its ecologically friendly building footprint, a shared space where super-efficient “shared energy” fuels multiple structures.

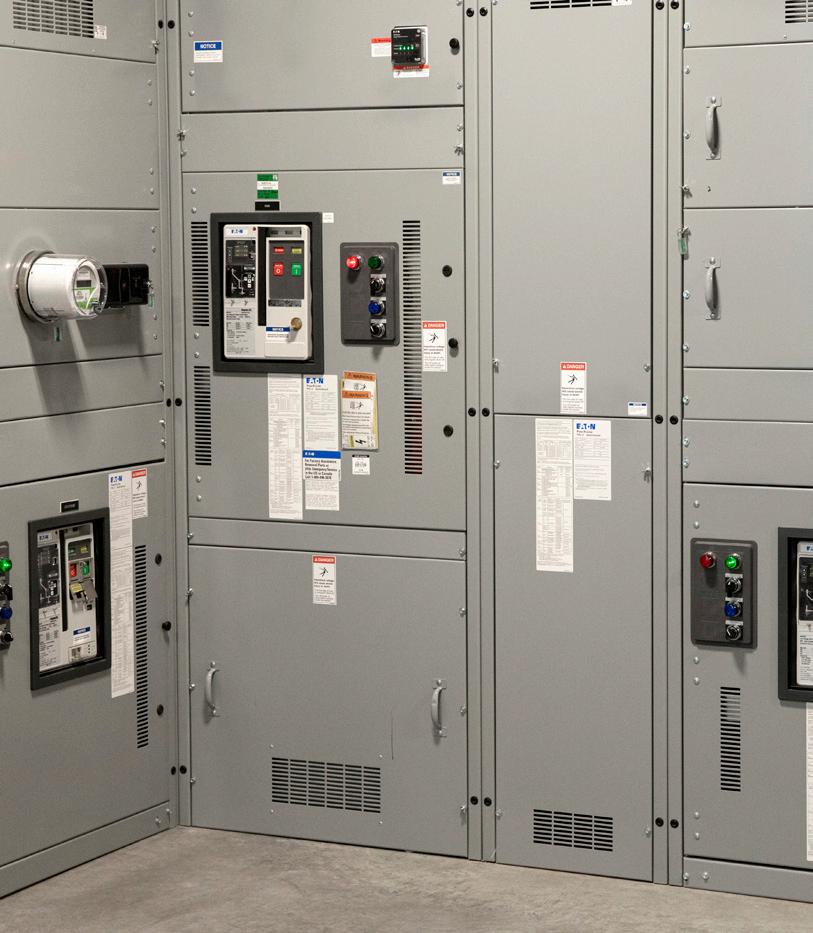
SUSTAINABLE BUILDING, GLOBAL BENEFIT
Job one for utilities is delivering safe, reliable energy to their customers. Typically, once that energy is delivered to a home or business, the utility's responsibility ends.
At the same time, building owners have traditionally focused only on maximizing the operating efficiency of their facilities. They may try to be more sustainable by, for instance, installing energy efficient systems to reduce usage. But they don’t usually think about when they’re using energy.
For utilities, on the other hand, timing is critical — if everyone needs energy at the same time, then the utility needs to build sufficient infrastructure to meet that peak demand.
“If we can shift when people use energy, we can better utilize the existing grid, and delay costly construction of the next substation to meet energy demand, which ultimately makes energy more affordable for everyone,” says Heather Rosentrater, senior vice president of energy delivery for Avista. “What we learn about working together to enhance sustainability and affordability can then be applied to how we operate our entire system.”
And of course, she adds, reducing our carbon footprint and increasing sustainability creates a global benefit we all share.
“Most buildings are constructed one at Eco District as a living laboratory where a time, each with a dedicated heating and the utility will research and test additional cooling system and their own grid connection,” sharable, sustainable and affordable energy says Heather Rosentrater, Avista’s senior vice solutions to benefit all of its customers—and president of energy delivery. “But Avista and hopefully drive change for the entire industry. our South Landing partner McKinstry are The Eco District is only part of the testing a new shared energy model called an equation. Next, Avista’s partner McKinstry Eco District—a centralized heating, cooling needed an anchor building for South Landing and electrical system that reliably, sustainably that would meet the highest energy standards. and affordably serves the energy needs of a “The world is changing rapidly, or if it isn’t, group of buildings.” it needs to change quicker in terms of energy,”
The guts of the Eco District reside within says John Lang, director of design services for the Scott Morris Center for Energy Innovation, McKinstry. “We’re all about saving energy, the first building constructed at the South that’s the bottom line here.” Landing site. Inside, you can see a network of heat pumps, boilers and chillers that supply the heating and M cKinstry is a n a t i o n a l l e a d e r i n cooling. Solar panels line By actively designing and operating much of the roof space of the Morris Center (as managing energy, h i g h - p e r f o r m i n g buildings. The Seattlethey do the neighboring we can maximize based company has in Catalyst building), while thermal and electrical the efficiency of recent years put down r o o t s i n t h e In l a n d storage units ensure that the building and its Northwest, operating energy to the complex can be both generated and operations—along multiple facilities in the Spokane area. stored. with when and Avista recruited local
Instead of operating in how to best utilize timber industry leader, silos, explains Rosentrater, Katerra, to work with the Catalyst and Morris the grid—all while McKinstry to design and Center structures have keeping occupants build the Catalyst building been designed to “talk” to each other. Thousands comfortable. It’s — a 150,000-square-foot, five-story building — using of sensors track ambient a win-win-win. wood. Katerra operates a conditions, air quality, mass timber production occupa nc y and ot her line in Spokane Valley attributes. All of this where it produces a hightechnology allows building quality building material operators to actively manage energy loads and called cross-laminated timber, or CLT, and balance on-site energy demand, generation houses one of the largest presses for creating and storage in real-time, which reduces the CLT in the world. impact on the city’s power grid. Katerra design partner, Michael Green
“By actively managing energy, we can Architecture, based in Vancouver, British maximize the efficiency of the building and Columbia, designed the building. The firm its operations—along with when and how has been leading the global conversation on to best utilize the grid—all while keeping timber construction for more than 20 years, occupants comfortable,” Rosentrater says. “It’s and built the first “tall wood” building in a win-win-win.” North America, a seven-story office building
Avista will also utilize the South Landing in Minneapolis.


CLOUD COVER
Look to the ceiling inside the Catalyst building and you’ll find another first: McKinstry’s initial installation of their innovative new ceiling appliance units called “Clouds.”
“CLT buildings are absolutely gorgeous. You see all that exposed wood and you don’t want to have it cluttered up with what we do for a living, which is the mechanical, electrical, plumbing and data cables,” says John Lang, McKinstry director of design services. “To ensure that the designers could showcase the building itself, we needed a better way to organize our trades.”
From a neatly organized patchwork of utility components in the ceiling, McKinstry installed Cloud units in each room. The white, square panels deliver heating and cooling, lighting, audio speakers, fire alarms and more. The Clouds are even made from sound absorptive material to provide better acoustics. McKinstry subsidiary Overcast Innovations prefabricates the Cloud units in the factory, then ships them to the construction site for quick installation.
Principal architect Michael Green calls cross-laminated timber the “grand daddy” of mass-timber products. “They’re taking a piece of wood, which is already very strong, and they’re gluing it together in a way that makes it even stronger,” he says.
The cross-laminating process involves lining up rows of small-gauge wood, like 2x4s, and gluing the rows on top of one another, alternating each row by 90 degrees. The finished panels can be three, five or seven layers thick. “It’s kind of like a big, thick sandwich of these boards that are cross laminated by rotating every layer,” Green says.
The strength of the material is crucial for building a structure the size of the Catalyst, and of course wood is a renewable resource. But there is an even more important reason to build with wood: It is the only material that stores carbon rather than emits it. According to Green, buildings in the United States represent about 47 percent of greenhouse gas emissions. That’s more than cars. All transportation, in fact, accounts for only 27 percent of such emissions, he says.
“Wood buildings do the opposite. As a tree

grows, it’s giving us oxygen while soaking up the carbon dioxide from the atmosphere. When you cut down the tree and put it into a building, it’s basically storing the carbon dioxide in the building for the life of the building,” Green explains. “That means instead of emitting greenhouse gasses, we’re actually creating a place where we can store greenhouse gasses.”
Green is also a proponent of wood construction due to its positive impact on human stress. According to industry research, when we can see nature or are surrounded by natural products, stress levels go down. We learn more quickly and work more productively. Thus the Catalyst was designed to showcase as much CLT as possible.
The same consideration was given to the design of the Catalyst’s windows. “We spent a lot of time doing day lighting studies in this building, and I think the quality of light surpassed what I was expecting. It’s just absolutely wonderful,” says Lang.
Thirty-foot tall windows flood the space with natural light, while the triple-pane windows are filled with argon gas to minimize heat loss and heat gain. The number of
windows throughout the building was deliberately planned at a that [structures like this] can be done in a cost-effective way, and 60-percent-solid to 40-percent-window ratio to balance the amount hopefully be part of the change we need to make buildings far more of heat-generating daylight with the need for more highly insulated energy effective than they are today.” solid walls. The exterior is constructed with a high-performance terracotta material, which is an excellent insulator and A building bursting with this much innovation deserves to be filled with the brightest minds has a natural texture which breaks up in the region. Some 1,000 EWU students sound—thus helping minimize the noisy The company that will proudly occupy about 70 percent train traffic rumbling by. The exterior and windows are also air tight, which tested Catalyst for air of the Catalyst building, which was purposely designed to allow Eastern to keeps the interior heating and cooling tightness said it was the lead a transformation in the way it and costs down. “The company that tested Catalyst tightest building they’ve other universities collaborate with their communities. for air tightness said it was the tightest ever tested in North “We tried to create a dynamic number building they’ve ever tested in North America. That made us very happy,” says America. That made of spaces that hopefully will bring people together,” says Green. “A building and [its] Lang. us very happy. architecture aren’t important until it fills
“This building is going to be one of up with people who make it special and who the top performing energy buildings in bring the warmth and joy and community the nation, certainly for its size,” adds to the building.” Green. “It’s going to show other builders Eastern, already an important economic driver for the region, is committed to pushing the creative and high-tech vitality of the Inland Northwest forward. Expanding into the Catalyst space will allow some of the university’s most successful programs to better position themselves to work alongside businesses and industry. “Having the opportunity to be housed right in downtown Spokane is going to present an incredible opportunity for faculty and students to apply their learning directly to real world problems with real working engineers, designers and computer scientists,” says David Bowman, dean of EWU’s College of Science, Technology, Engineering and Mathematics. “It’s going to be the epitome of hands-on learning for our students, and hands-on research and scholarly activities for our faculty.” The College of STEM is relocating three programs to the Catalyst: computer science, electrical engineering, and design. The programs were specifically chosen because of their relationship to the tech and business industries. STEM also is planning to create a new program, computer engineering, which will be housed in Catalyst. Additionally, the College of
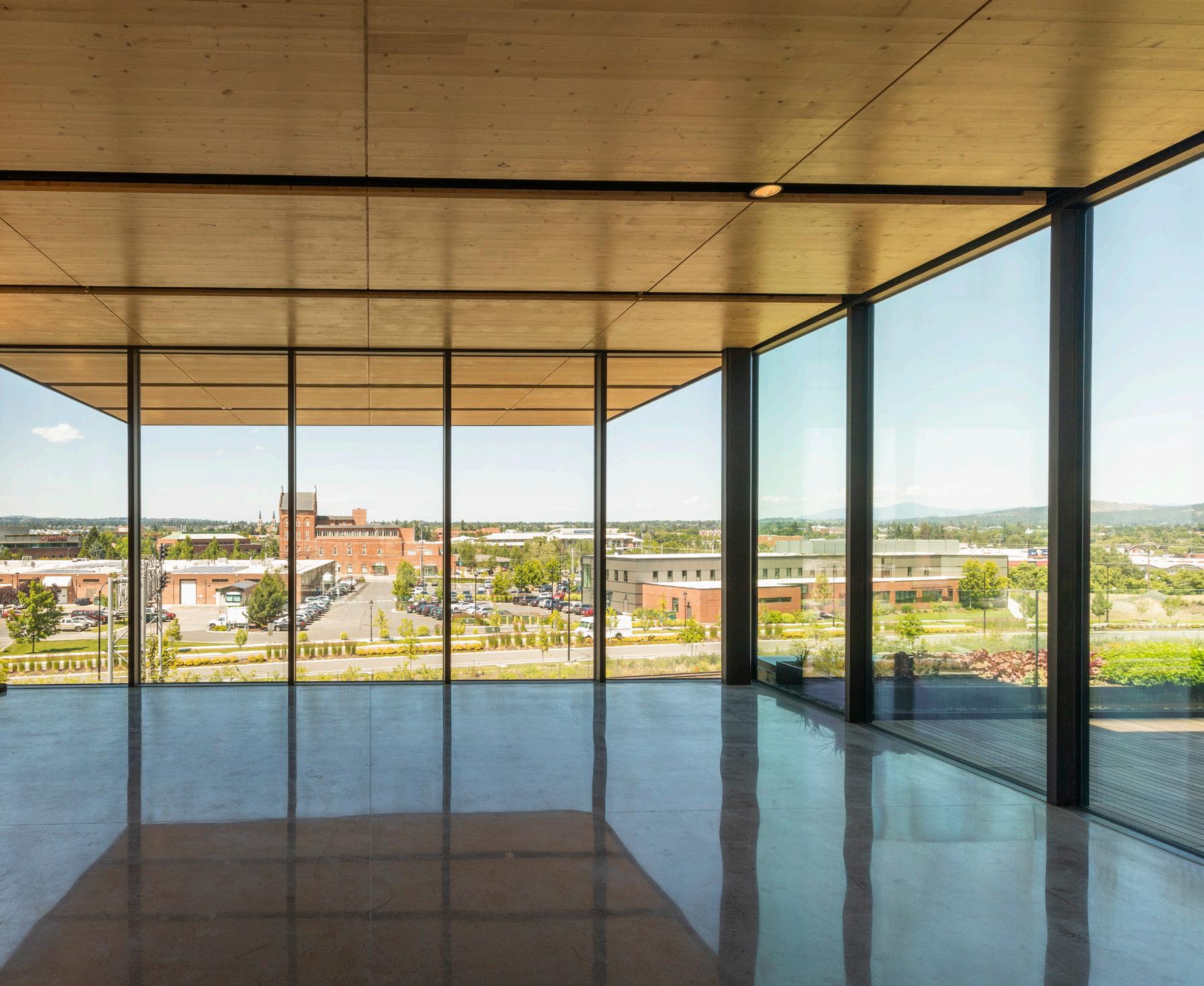
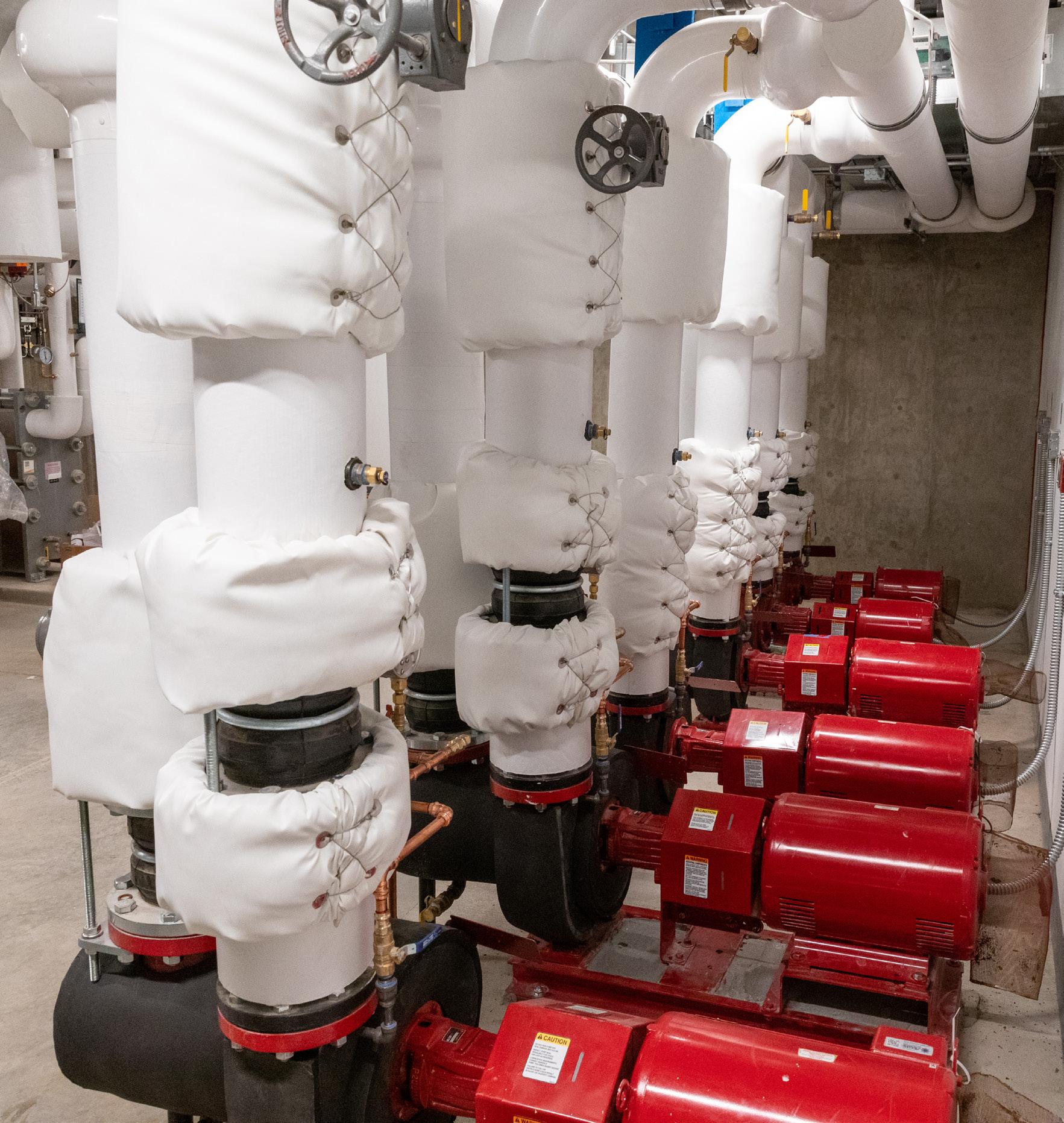
Business, along with some College of Health Science and Public Health programs, will relocate from the north side of the University District to the Catalyst. EWU’s Creative Writing MFA program will also be based there.
“The whole idea behind Catalyst — the reason it’s called Catalyst — is that the entire project should stimulate reactions among our faculty and our students and businesses. Bringing more programs together is just going to allow us to make the reaction event bigger,” says Bowman. “It is such a wonderfully warm, beautiful and comfortable environment. I think it’s a game changer for our faculty and for our students.”
Eastern’s involvement in Catalyst was made possible, in part, thanks to a $5 million gift from the Avista Foundation and the McKinstry Charitable Foundation—a public-private partnership that will serve the community for generations to come. Working together, these agencies have helped raised the bar for future development, and brought higher education closer to the regional businesses and industries it serves.
Another plus is that EWU is now leading the expansion of Spokane’s University District, a move which will allow students and faculty to help the East Sprague neighborhood emerge as a tech and energy center for Spokane.
“ W h a t’s re a l l y a m a z i n g a b o u t o u r community is that we always punch above our weight,” says Avista’s Latisha Hill. “We create grand visions, and then we are often taken aback when we actually achieve them. I think the South Landing is a reflection of that.”
— You can make an impact on EWU’s future in the Catalyst. To find out how, visit ewu.edu/ catalyst. Interested in naming rights? Contact Lisa Poplawski Lewis at (509) 844-5915.
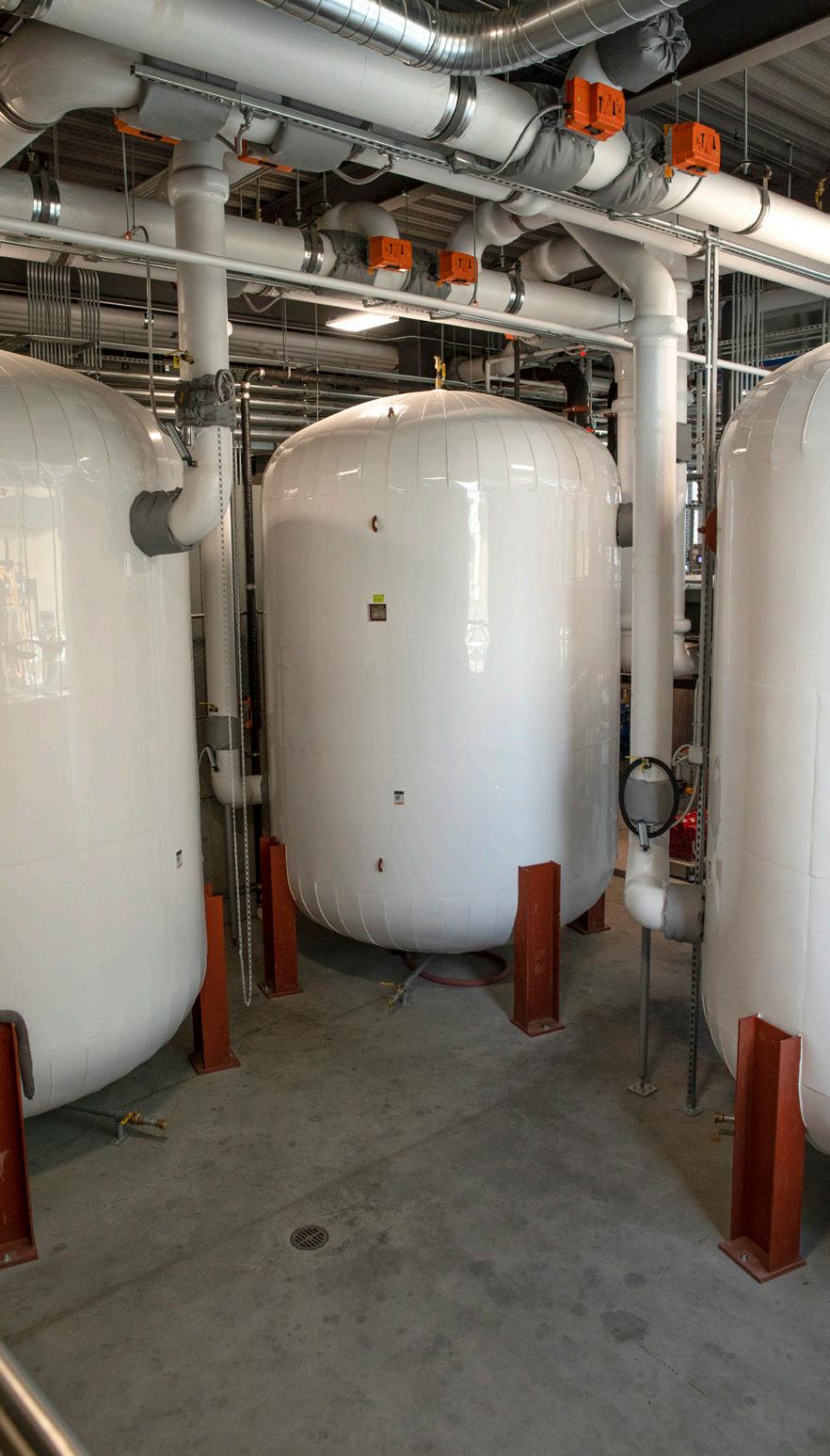
ZERO ENERGY, ZERO CARBON
McKinstry aims to have the Catalyst building be zero energy and zero carbon certified by the International Living Futures Institute. Once completed, Catalyst would become the largest building of its type in the country to be certified as such.
WHAT DOES IT MEAN?
A zero-energy building produces enough renewable energy to meet its own annual energy consumption requirements, thus reducing the use of nonrenewable energy in the building sector, according to the U.S. Department of Energy.
Zero carbon occurs when the amount of carbon dioxide emissions released on an annual basis is zero or negative. The World Green Building Council defines a zero-carbon building as a highly energyefficient building that is fully powered from on-site and/or off-site renewable energy sources and offsets.