
16 minute read
Turbine, and new rollerbed beet transfer option demonstrated at Norfolk harvesting event
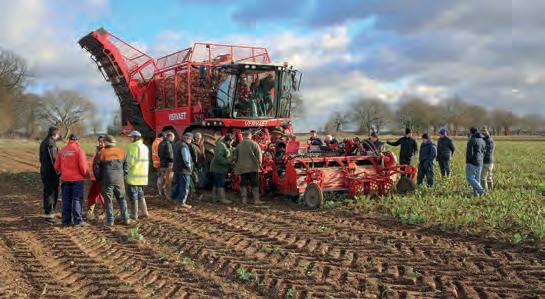

An opportunity to see the latest Vervaet self-propelled beet harvesters in action tempted hundreds of beet growers and contractors to visit a late season working day. David Williams was there.
The demonstration was organised by Vervaet importer, J Riley Beet Harvesters (UK) Ltd. The biennial event proved extremely popular as the relatively easy 2021–22 beet harvesting campaign was ending. Approximately500 people attended and managing director Jeremy Riley (pictured right) said there was a good mix of farmers and contractors – most of who were current Vervaet users as well as many who are considering switching to the brand. 500 people attended and managing director Jeremy Riley (pictured right) said considering switching to cleaning action.
Jeremy stressed that the rollerbed isn’t replacing Vervaet’s popular turbine cleaners. “Turbines provide exceptional results in a wider variety of soil types and working conditions, and will remain the preferred system for most users. However, there are potential
New option
Vervaet demonstrated its new rollerbed primary cleaning system for the rst time. Availability of the rollerbed as an alternative to Vervaet’s long-favoured turbinebased system was announced last year, and two machines tted with the new cleaner were trialled in the UK this season. Rollerbeds have been standard on several competitor brand harvesters for many years, and by adding them to its options list, Vervaet is guaranteed to attract new customers who prefer the roller cleaning action.
Jeremy stressed that the rollerbed isn’t replacing Vervaet’s popular turbine cleaners. “Turbines provide exceptional results in a wider variety of soil types and working conditions, and will remain the preferred system for most users. However, there are potential customers for Vervaet machines currently using other brands because of their rollerbed cleaners, in areas where soil types allow. Adding rollerbed cleaning to our options list means that these users will also be able to use our harvesters and enjoy all the other advantages associated with Vervaet machines, too.”
Beet arrive on the rollerbed direct from the lifters and travel in one direction to the centre turbine which transports them to the main cleaning turbines under the machine.
Optimised beet ow
The new rollerbed consists of seven full width 100mm diameter rollers mounted directly behind the lifting shears. The parallel rollers are mounted perpendicular to the direction of travel. The rollers have external scrolls which grip the beet and distribute them across the bed. The two front rollers direct beet to the outsides of the bed, while subsequent rollers pull the beet back towards the middle. Shorter rollers on both sides at the rear of the bed create a backstop and direct beet towards the channel between the two front wheels.
The speed of the rollers’ rotation is adjustable from the cab. The front six rollers rotate at the same speed, while the seventh roller has separate adjustment and can also be run in a reverse direction to contra-rotate against the preceding roller for more aggressive cleaning.
Turbine transfer retained
The J Riley team says that use of a central turbine which transports beet from the primary cleaner at the front, to the main cleaning turbines beneath the harvester, has always been considered a strong point of Vervaet’s design. This is retained when the rollerbed option is tted, whereas competitor rollerbed machines use a conveyor trace running between the front wheels, and it is argued that the turbine ensures greater reliability and reduced maintenance.
Roll-out across line-up
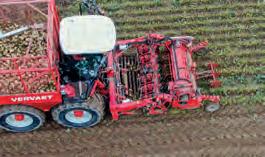
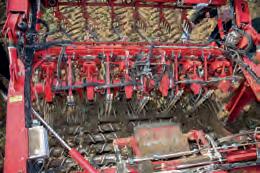
The new rollerbed is an option for the larger Beet Eater 625 model rst, and it is expected to be available for the smaller Q-series soon. Even with the rollerbed tted which replaces the two primary cleaning turbines, the Beet Eater 625 still has six turbines which Vervaet says provide marketleading cleaning capacity.
Potential speed increase
J Riley sales manager, Matt Carse, says that in some conditions a rollerbed allows faster working speeds. “On the right soils they o er good cleaning and are generally regarded as being gentler on beet. During testing, the 625 with a rollerbed operated in challenging conditions at more than 8kph and did a good job. I’m very pleased to be able to o er both turbine and rollerbed cleaning options which will broaden our range’s appeal.”
Rollerbed user
North Norfolk-based beet contractor, Robert Wright was at the event. Trading as RC Wright Ltd he replaced his Vervaet 625 with turbine primary cleaning, with the rst Vervaet 625 with a rollerbed, and was pleased with its performance through this year’s campaign. “Beet are lifted and delivered directly onto the rollerbed and that makes sense to me,” he
continued over…
Contractor Robert Wright (right) with Sam Wilton who worked with Robert this season.
…from previous page explained. “Rollers are gentler on beet than turbines, although I never had problems previously, and losses are minimal. I think rollers preserve more of the taproot.
“We harvest on mixed soils, including light, stony and heavy, and Vervaet’s cleaning system works well. Vervaet harvesters clean beet all the way through from lifting to the main elevator, and from the rollerbed a central turbine transports them between the front wheels rather than a web. I think it’s a better system as turbines are generally trouble-free.”
Robert has owned 11 Vervaet harvesters and most machines were part-exchanged after two years having lifted 1,500ha of sugar beet. “In my opinion, Vervaet makes the best harvesters and we can always depend on the back-up from the Riley team,” he said. “My new 625 was excellent this year. It achieved harvesting speeds up to 9kph with no problems, even though it was a season of big tops and high yields.”
Robert said the rollerbed option also gives a clearer view of the lifters, so the operator can watch beet as they are transferred to the rollers.
His 625 also has Vervaet’s new telematics system, although as an owner-operator Robert said its main bene ts will include allowing the Vervaet and Riley service teams to access operating data and identify faults.”
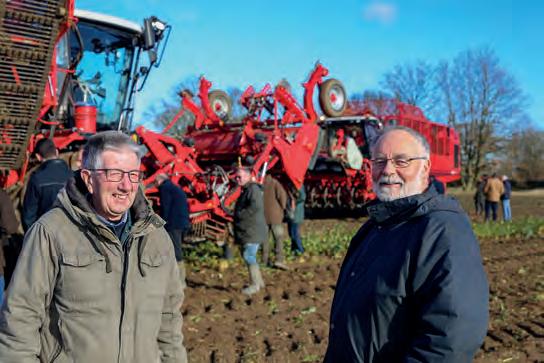
Experienced operator
Ninety-year-old Vervaet 625 harvester operator, Fred Campling is pictured at the demonstration. Fred has been involved with agricultural contracting for almost 70 years, and his family business, based at Sutton-St-James, Lincs, operates two harvesters currently alongside a haulage business.
Fred said that when he started working as a contractor; beet were lifted by hand and transported by horse and cart. He later used a Catchpole harvester on a David Brown tractor, followed by Standen machines. Now the business lifts approximately 400ha of beet per year across four farms – two of which have used the family’s services for almost 40 years.
“The service from the Riley team, and especially service manager Harry Skeet, is very good. If there is anything we need to know then Harry has the answer. Spares back-up is superb and, nine times out of 10, whatever we need is with us within an hour.”
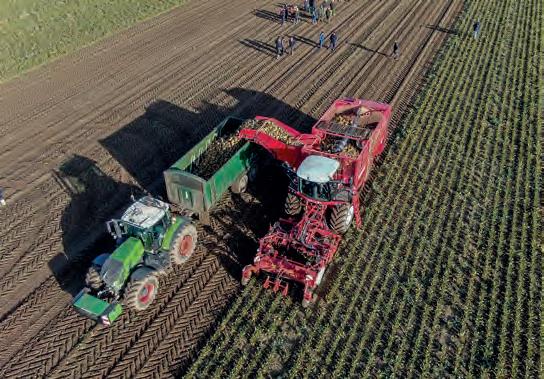
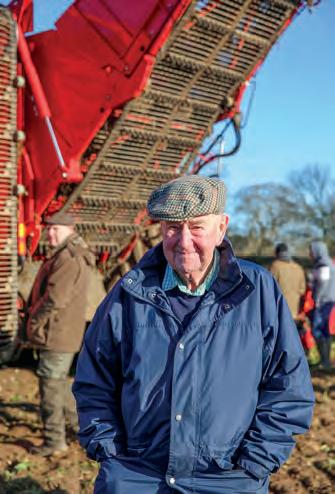
Brian Waters (left) with Stuart Waspe.
Continued reliability
Su olk-based farmer and Vervaet harvester user, Stuart Waspe, and Brian Waters who used to work on his farm but is now retired, were at the event. Trading as V&R Waspe & Sons and based at Boyton Hall, near Stowmarket, the Waspe family has owned its 1995-model Vervaet 17t harvester since 2014. Stuart, and his brother Colin Waspe operate the harvester and Colin also does most of the maintenance.
“By the 2014 harvest, we no longer had enough manpower for our trailed harvester-based system, which also needed two tractors and trailers to cart the beet. We decided to replace our existing Garford machine with a self-propelled tanker model and looked at various options.
“We could only justify a low-priced, second-hand model, but Jeremy Riley couldn’t have been more helpful. He introduced us to a customer who was selling a Vervaet which had worked nine seasons. We bought it, and it remains reliable and works well, even though it has accumulated 7,000 hours.”
Colin said J Riley storesmen Carl and Andy, and service manager, Harry Skeet, are always keen to help. “When we call, they recognise our machine, and know what parts are needed. Harry talks us through repairs on the phone which is a big help. We can’t rate the service highly enough.
“We grow less beet now, and it has an easier life although we have very heavy clay soils and steep slopes. Our land is challenging but the Vervaet copes well; and when it’s wet, if the beet in the trailer aren’t clean then we shouldn’t be on the eld.
“Modern versions have upgrades over our machine, including improved beet feed from the lifters to the cleaning turbines, and walking shears which move independently to follow ground contours – but the basic principles remain similar. We are impressed by Vervaet and the dealer.”
Su olk & Norfolk contractor
Trading as PJ Stent Ltd, Paul Stent operates two Vervaet Q616 harvesters. He owned a larger Beet Eater 625 previously which operated alongside a Q616 but has now opted to run two Q616 machines. “Operating two similar size machines works better, and the performance of the latest Q616 is excellent,” he explained. “It’s more manoeuvrable than the 625 and it’s lighter. Our customers appreciate the reduced compaction.”
Paul tried the 625 with the rollerbed primary cleaner. Asked about his experience; Paul said he agrees there is an advantage in terms of gentler beet handling on light and medium soils, but for his customers in Su olk and Norfolk who farm a wide range of soil types, he feels that the proven turbine system will give better performance in a di cult lifting season. Paul has operated Vervaet harvesters for 20 years and he said the service from the J Riley team is second to none. “I have a great relationship with the Vervaet and J Riley teams – they help me, and I’m always happy to help them.”
In-house telematics
Vervaet Connect telematics was demonstrated for the rst time. Developed in-house for the manufacturer’s sugar beet harvesters and self-propelled slurry applicators; Vervaet Connect will be standard on applicators produced this year, and beet harvesters from 2023.
Sensors collect machine performance and operating data which is then transmitted to Vervaet’s server. It can then be viewed from anywhere through the MyVervaet online portal.
Machine data refreshes every 10 seconds, and historic data can be viewed at any time through the MyVervaet app from anywhere with an internet connection.
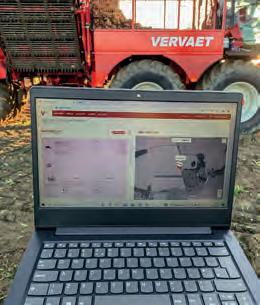
Vervaet has developed its own telematics system allowing remote task and performance monitoring and making it easier to maintain accurate work and eld records.
Monitoring and record keeping
Information recorded and available through the app includes: • Real-time vehicle tracking • Machine operating status • Current settings including live screen sharing
continued over…
…from previous page • Service information • Error codes and alerts • Historic work data • Yield mapping • Application maps. Advantages for owners and managers include the ability to ascertain the machine’s location and working status at any time. Accurate work records allow parameters including fuel consumption and work rates to be analysed and compared, providing opportunities to increase e ciency and reduce costs. Contractors can utilise the data to calculate precise working costs and check pro tability.
Maintenance management is also easier as machine working hours can be viewed from the o ce allowing servicing to be planned.

Reduced downtime
The dealer and manufacturer can also view performance data and error codes – for quick and easy problem diagnosis. This allows faults to be corrected remotely when possible, but if a technician visit is needed then the correct tools and required parts can be brought to the machine rst time – reducing downtime. There is also the possibility for engineers to alter settings remotely – but only with the
Compatible data
Compatibility with other farm management platforms enables task data to be imported and analysed easily, so that fact-based management decisions can be made.
Application and yield mapping
Optional yield mapping through an integrated weighing system is now available for Vervaet machines, which allows root crop yields to be analysed in the same way that cereal crop yields have become an accepted part of modern farm management.
For the Vervaet Hydro Trike and Quad; application maps provide accurate recording of what was applied and where. Options include adding an NIR sensor to analyse slurry constituents for precise monitoring.
Positive market
“It’s been a very busy season,” said Vervaet managing director Robin Vervaet, who was at the event with his son, Siebe who plans to join the company when he nishes further education. “In recent years there was doubt regarding the future of sugar beet across Europe, and about how Brexit might a ect the industry in the UK. There is now reassurance that the crop will remain important, and there is growing interest in beet’s use as a green fuel for anaerobic digesters.
“There is a correlation between sugar beet values and oil prices and the trend in recent years has been upwards, which is very positive for the industry.”
Asked about the new rollerbed cleaner, Robin said it was costly to develop but the option is valued by customers. “On lighter land it will handle beet more gently,” he continued, “whereas for use where conditions become sticky when it’s wet, then we expect turbines to be preferred. Feedback regarding performance of test machines last year was very positive and a contractor who bought a pre-series machine has con rmed that he would choose the same again.”
Robin said Vervaet’s telematics make it easier to meet increased requirements for accurate record keeping. “Demand for precise slurry application records is growing, and our telematics system will allow contractors to generate this information for their customers, adding value to their service. Using wireless data transfer will reduce machine downtime for users of our slurry applicators and beet harvesters as problems are diagnosed more quickly. For all users, access to precise fuel use information and working data will highlight areas where operating e ciency might be improved. Vervaet telematics is available this year on slurry applicators, and from 2023 for the full range of beet harvesters.” FG
Pictured are (l-r) contractors Robert Wright and Paul Stent, Robin Vervaet and his son Siebe.
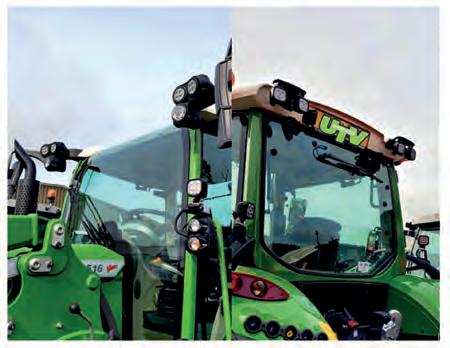
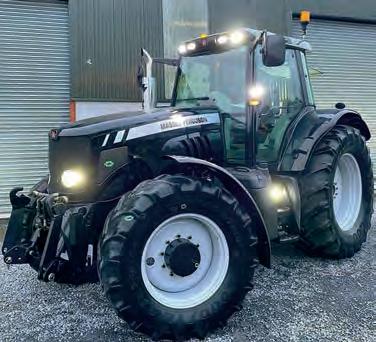
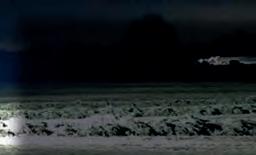
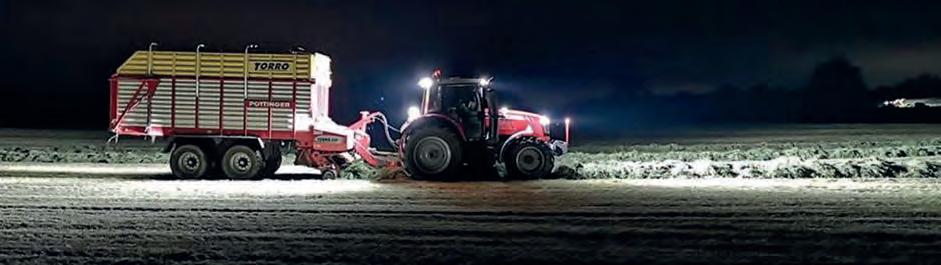
NEW TRACTOR PACKAGES FOR DEALERS OR BUYERS
UTV Products Ltd are an Industry Leading Agricultural LED lighting company, priding itself in; QUALITY . PRECISION . PERFORMANCE . INNOVATION
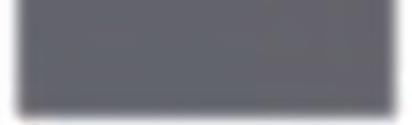
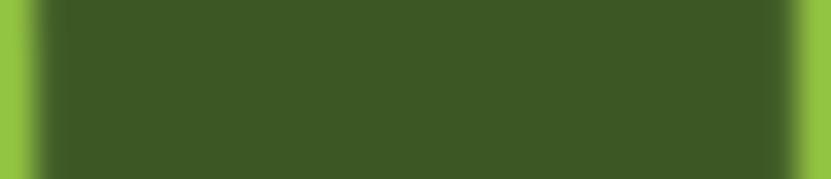
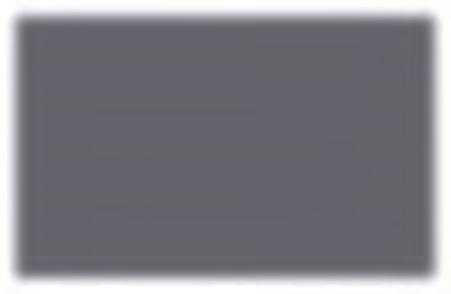
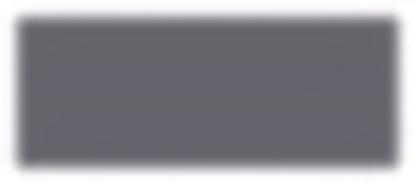

Tel: 01270 895344 Email: sales@ledlightsforsale.co.uk www.ledlightsforsale.co.uk
Security package launches for GPS equipment
Amid reports of rising GPS thefts, Vantage ASC says it has seen this trend rst hand through the number of customers purchasing equipment linked with insurance claims.
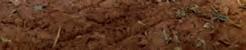

Vantage ASC has developed the following solutions categorised under the security package:
Receiver tracking: New as of February, this includes recon guring of the receiver, activation and two years monitoring. Should a theft take place, the company can access the equipment’s location.
For new receivers the customer can add the option to their purchase, and Vantage will complete the activation before the receiver leaves the premises. Customers can ship existing receivers back to Vantage ASC premises and the company will recon gure and activate it, before shipping it back to the customer for installation on the machine.
After two years, renewal of the service includes a welfare check of the receiver. The company will proactively contact customers four weeks in advance.
Smartwater forensic marking:
This option is o ered for displays/ receivers/ECUs and includes: • 100ml of unique marking uid • Six small circular SmartTrace stickers • Three large rectangular SmartTrace stickers • Assets serial number registration to
SmartWater database • Access to SmartWater investigation services/representation for proof of ownership • Asset serial registration on Trimble worldwide database.
If this option is chosen, Vantage marks all equipment at its premises and registers assets before shipping/ installing on farm. Surplus stickers/ uid is shipped to the customer. Customers can request kits for existing equipment; just supply the assets and serial numbers so Vantage can register them on the databases.
Receiver quick release brackets:
Vantage ASC can provide brackets for Trimble receivers so they can be removed from the machine without any tools. These allow insertion of the receiver which is then secured with a lock back clasp, making it tool free and the install/removal of equipment much easier. The lock back clasp also has a hole for the padlock if required.
Display quick release brackets:
Vantage o ers RAM Mount products which can be speci ed for numerous locations in a vehicle and allow the simple removal of equipment from machine cabs. Trimble equipment comes with RAM Mount xings as standard; or for existing equipment customers can get in touch.
Cloud-based storage and
auto sync: Taking advantage of Trimble cloud software, Vantage can provide automated data backup of display data including eld A-B lines, boundaries, farm and eld names, application information and task data. It equips the machine with a modem for wi- and connects it to the cloud software. Sim cards for the modem can be supplied or the customer can use their preferred network. This service ensures personalised farm data is being backed up and is available to download onto replacement displays should the worst happen.
Whilst there are no o cial reductions in insurance premiums as yet, insurers are actively encouraging the options as it mitigates the risk. Vantage ASC works with the main insurers and provides a full service from survey, con guration, and quotation. This can save on administration associated with claims. FG

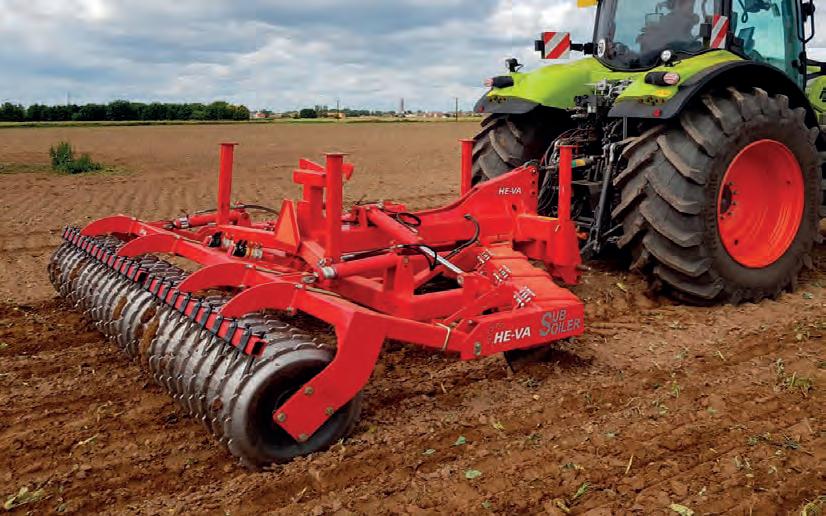
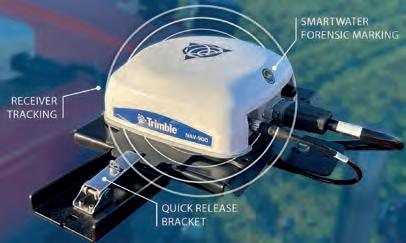
he-va.co.uk
Distributed by


SUBSOILERS
Restructure your soil
BREATHE LIFE BACK IN TO YOUR SOIL
Is it time to proactively manage your soils? HE-VA’s subsoilers improve drainage, alleviate compaction and breathe life back into damaged soils, thus encouraging crop rooting.
All HE-VA Subsoilers have hydraulic depth control from the tractor seat, quick change points and are available with either hydraulic auto-reset or ‘hammer thru’ shearbolt stone protection.
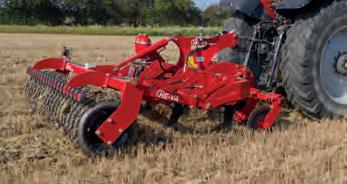
Stealth Subsoiler
• Designed for minimum draught
& maximum heave
• Mounted and trailed version from 3 – 13 legs • V formation • Variable leg spacing • Suitable for tractors 100 – 650hp • Stealth low disturbance medium depth legs & points - optional