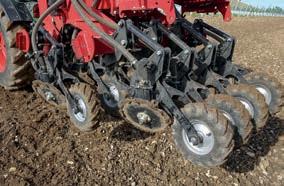
5 minute read
Narrow seeder with proven big drill design
The double-disc coulters are the same as used on the full-size GD Drill. The discs have a slight stagger, and the leading disc cuts an opening, and the second disc lifts a ap of soil and holds it while the seed is placed beneath. A press wheel at the rear controls the seeding depth and closes the ap while ensuring e ective seed to soil contact.
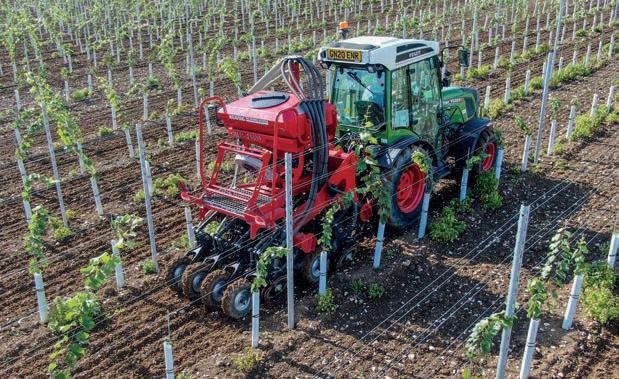
A new narrow drill designed to work where space is restricted has been added to the Weaving line-up. David Williams saw it in action.
The Weaving Vineyard Mini GD Drill is best described as the standard full-size Mounted GD Drill cut in half, with a Magnum seed hopper and metering system mounted centrally above. The new drill retains the full-size drill’s double disc coulter seeding system so it isn’t light, but the compact layout keeps the weight in close to the rear of the tractor making it easier to lift and allowing use with smaller models. There are two versions – 1.5m and 2.0m working widths, both with 166mm row spacing and adjustable coulter pressure up to 200kg to ensure e ective penetration even into dry, hard ground.
Many applications
As its name suggests, the new drill provides a solution for vineyards and fruit orchards, but it is just as suitable for municipal areas as well as sports grounds and amenity sites, and anywhere else that working space is limited. It is also an ideal solution for farmers and contractors establishing grass and cover crops in areas under Environmental Stewardship Schemes, due to the minimal ground disturbance.
User experience
Farmers Guide saw the new drill establishing a complex 27-variety cover crop mix in the rows between the vines in a newly planted vineyard. Contractor Sam Barnes trades as SJ Barnes Ltd, and he specialises in vineyard establishment and maintenance for owners across the UK. “Much of our maintenance work is establishing and repairing grass and cover crop strips between the vine rows, and we built our own combination power harrow drill with a mounted air seeder several years ago especially for the task. It worked well, but increased use of complex seed mixes in recent years highlighted limitations of its air seed delivery system,” he explained. “We considered replacing the metering system with a new Weaving Magnum seeding unit, but sales director Simon Weaving suggested that he could build us a bespoke drill utilising the successful GD Drill coulter design instead. We agreed that this would be a more versatile solution, so we placed an order.”
The bespoke drill was used in autumn last year and it proved immediately successful. Demand
continued over…
FIND YOUR FUTURE SOLUTIONS AT

www.vantage-ag.uk
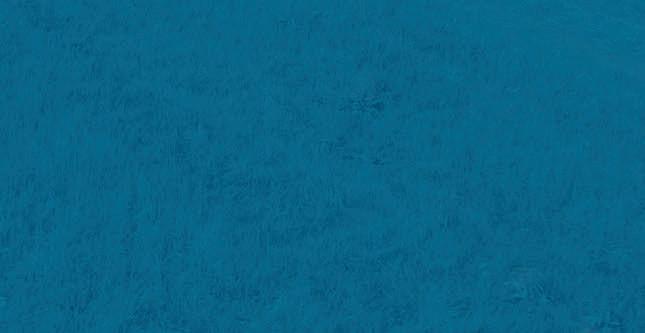
Authorised Distribution Partner
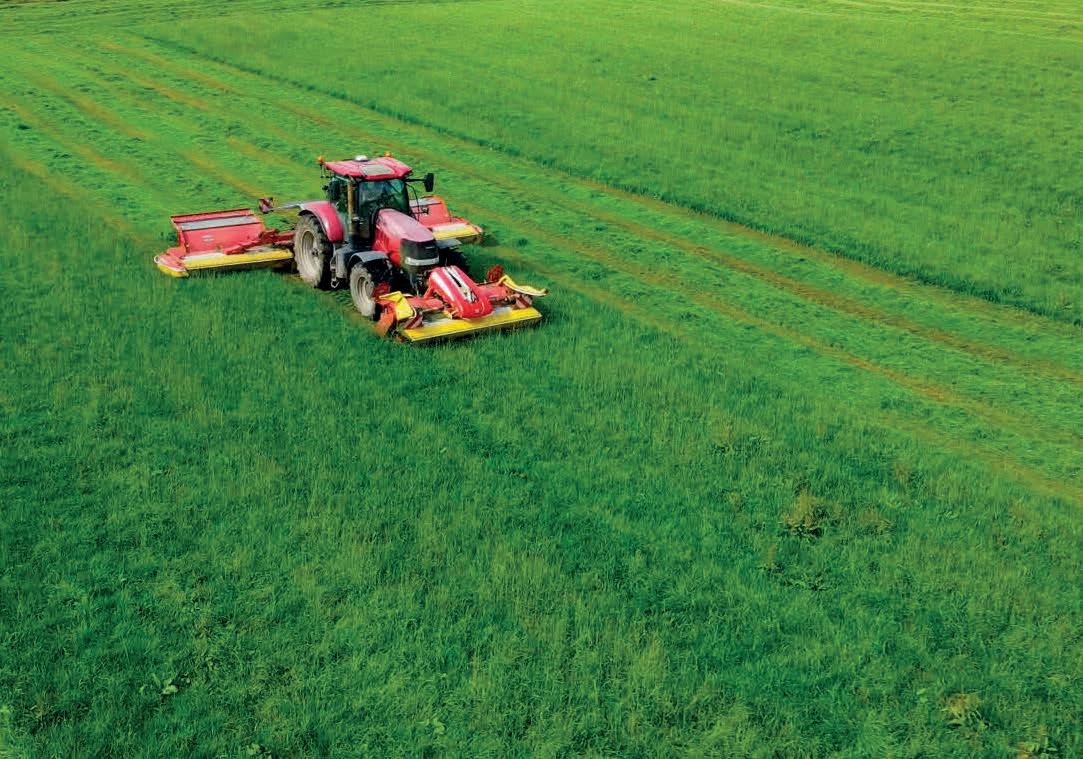
Vantage England & Wales, giving you more than just straight lines.
Your ‘go to’ for the best products and expert advice bringing you e cient, sustainable, and pro table solutions, as well as industry best service and support.
Vantage-ag.uk | 01480 861824
…from previous page for similar drills for a wide range of applications is increasing, so Weaving put the drill into production and it is now available to order.
Proven seeding technique
The coulter design and working action are identical to the Mounted GD Drill. Each set of coulters has a large diameter angled outer leading disc which cuts an opening, then a slightly smaller inner disc lifts a ap of soil and holds it while the seeds are dropped below. As the machine moves forward the ap is released onto the seed, and a following press wheel closes the ap and seals the slot – retaining moisture and ensuring e ective seed to soil contact. The versatile design allows direct drilling into existing grass and cover crops, or it will perform just as well working on pre-cultivated ground. Each set of discs is mounted around a central vertical pin, allowing the coulters to pivot to avoid obstructions and follow the direction of travel.
Minimal surface disturbance
“Since investing in the new drill, there have been many situations where we have drilled direct into existing vegetation, avoiding the need for pre-cultivation. This is an advantage for patching in grass seed to repair damaged areas. Even in very short and thin grass, it’s been almost impossible to see where the drill has been until the new grass emerged," Sam explained. "We still have the power harrow drill too as there are situations where its soil levelling capability is an advantage. Vineyards are naturally a controlled tra c environment in which wheelings remain in the same place year after year. In time ruts develop, and the power harrow redistributes the soil to create a level surface, then we plant the grass or cover crops into the loose soil using the new Weaving drill.”
Time and cost savings
Sam said that for inter-row seeding the Weaving drill easily achieves 8–10ha per day. “Work rates are much higher than the power harrow drill, and our fuel consumption is signi cantly lower. The Weaving is well made and heavy which ensures e ective penetration, but it’s still very easy to pull.”
Additional advantages of the Weaving drill over the power harrowbased seeder include lower wear rates. “Many vineyards are on inty soils and the Weaving drill’s disc coulters su er less wear and can pivot to avoid obstructions which reduces the risk of breakages,” added Sam.
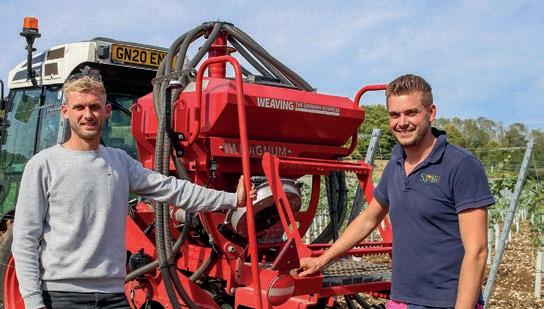
Will Barnes (left) is the drill’s main operator, and he is pictured with Sam Barnes.
Simple and reliable
Sam’s brother Will Barnes is the drill’s main operator, and he likes the simple, reliable design and excellent build quality. “If anything, it’s over made and we like that as it means it will last well and put up with intensive use. It’s easy to set up and look after, and the rear steps provide convenient hopper access.
“We’ve used it in a variety of conditions including hard and soft soils, and we’ve never had a coulter blockage. The coulters themselves are no trouble and because they are all independently mounted their contour following capability and depth control is superb. Additional weights can be added, but we haven’t needed them.”
Stitching in
“To give crops the best start and achieve optimal establishment; seeds have to be at the ideal depth, and need e ective seed to soil contact,” stressed Sam.
“Our new Weaving drill achieves this in a wide variety of working conditions. We have gained signi cant time and cost savings, but these aren’t only due to the higher working speed. Previously relying on the power harrow drill meant carrying out additional operations including spraying o existing vegetation, then cultivating, drilling and rolling, whereas the Weaving drill usually achieves successful plant establishment in a single pass.” FG
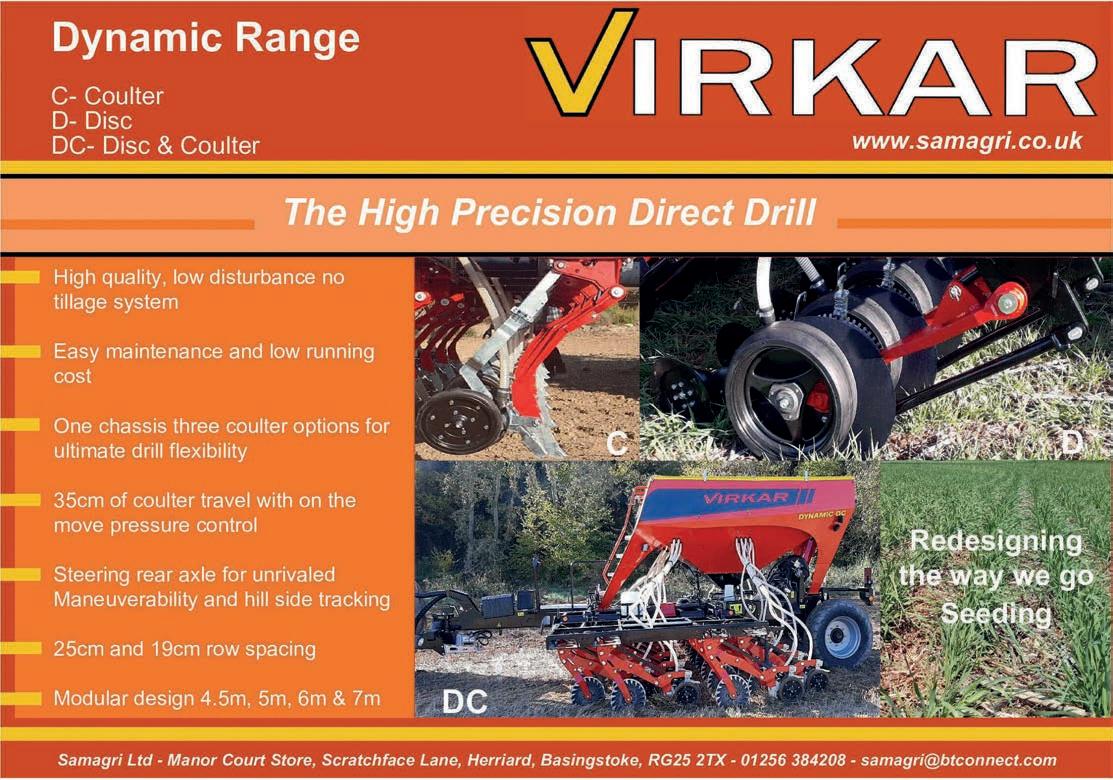