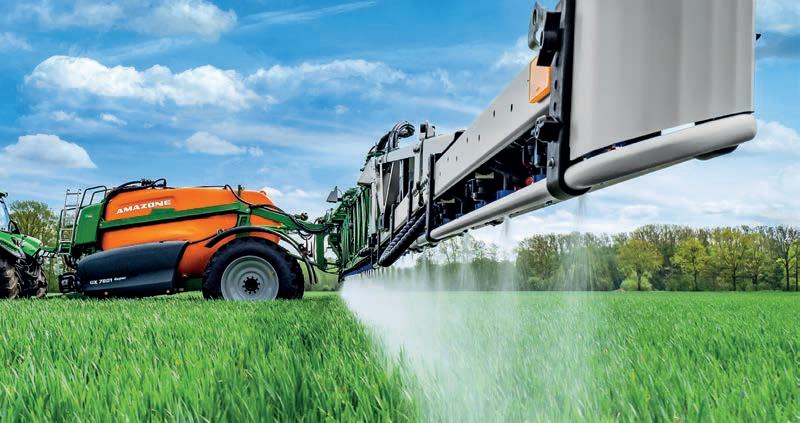
4 minute read
Utilising responsible application technology to provide sustainable agrochemical usage
Ensuring safe agrochemical handling and application is the key factor when it comes to sprayer design and development. Having the technology to hit the selected target – be that pest, weed or disease – with the correct dosage yet leaving as little impact as possible on the environment, operator or bystander is paramount.
The level of technology available on Amazone crop protection sprayers has mushroomed over the last few years and increases now exponentially, year-on-year, as pressure from regulators and consumers grows. The spraying operation that, until recently, was a farm-wide operation, is becoming increasingly part-area, site speci c as the ability to apply product plant-by-plant starts to become reality.
What used to be manual control over boom on/o on the headland and in short work is now done automatically by GPS down to the last 0.5m sections, using systems such as GPS-Switch and the Amazone AmaSelect system. Individual nozzle control can o er 85% reduction in overlap and savings in agrochemical usage of up to 10% in comparison to manually switched-o boom sections. This reduced over- and under-dosing on the ins and outs can also lead to increased yields, reduced residual levels in crops and a lowering of chemical resistance risk by a more even application.
Automatic control
The overall amount of liquid applied is controlled by accurate ow monitoring and modern electronics, but more importantly these days is the automatic control of droplet size depending on the task to hand. We need to adjust the type of nozzle and the droplet size depending on the target to be hit, the type of application – to plant, within plant, under plant, as an example – and also droplet size is dependent on forward speed and hence application rate. Increasing forward speed without increasing nozzle size will reduce droplet size and increase drift. The AmaSelect individual nozzle control system opens and closes di erent nozzle sizes, or a combination of multiple nozzles to ensure that the correct droplet size is maintained – irrespective of speed or application rate. A di erent style of nozzle, double at fan, air inclusion, low drift, etc. can be selected from the cab on the move for maximum exibility.
Spot application nozzles, such as the Agrotop SpotFan nozzle, o er a concentrated dose over a smaller area so making small area application a reality. By using 25cm spaced nozzles and the SpotFan jet, de ned areas of weed infestation can be identi ed by weed mapping or sensing and then chemical applied to that target at conventional spraying speeds. AmaSelect Spot utilises a weed map loaded into the Isobus terminal and then switches individual nozzles on and o to match the need in the eld.
Boom widths are still on the increase, the new 8,000-litre and 9,000-litre UX 7601/8601 coming now with booms of up to 45m. Application rate compensation along the boom when turning is important so as to ensure adequate coverage and avoid reduced application that can lead to chemical resistance. AmaSelect CurveControl carries out this compensation without the need for PWM technology by changing the size of nozzle at di erent points along the boom width thus enabling droplet size to be maintained as well as rate when turning at speed.
Dependant on nozzle type and spacing
The optimum boom height depends on nozzle spacing and style of nozzle and it is imperative that the boom is kept at the correct height above target to ensure optimum application and minimal drift. A 20cm increase in boom height above that optimal height will see drift double, impacting the environment, wasting product and reducing the e cacy of the product on the target. Boom guidance systems such as ContourControl ensure the optimum height is maintained in any topography and at any speed. When changing nozzle spacing from 50cm to 25cm, the boom is automatically lowered to compensate for the di erent overlap between nozzles. SwingStop takes out any tip vibration and prevents any boom whip when accelerating and decelerating, thus eliminating over- and under-spray at the boom ends.
The new Amazone DirectInject system, a silver medal-winning innovation at Agritechnica 2021, enables the introduction of an additional chemical into the nozzle on a part-area basis alongside the conventional tank mix to give a quick, exible, needs-based approach to chemical application. This separate 50-litre tank is easily accessed and works with undiluted chemical meaning that any unused product is not wasted. Any crosscontamination of the main tank mix is not possible due to the secondary spray-line on the boom.
Looking ahead
And where is the future? The UX AmaSpot sprayer already o ers green-on-brown application of glyphosate meaning individual weeds and volunteers can be targeted, night or day, at speeds of up to 20kph.
In large, extensive farming areas this can amount to savings of up to 80% in glyphosate usage. The new generation SmartSprayers use similar technology but can now pick out green from green in row crops; again, minimising chemical usage, speeding up the spraying operation and protecting the environment. Real-time agronomy advice is received using BASF’s xarvio decisionmaking engine to analyse the data and make the decision to apply or not apply from what the sprayer is seeing.
High-tech Amazone spraying systems o er responsible application technology that decreases operator contact, reduces chemical input, reduces environmental impact, speeds up the spraying operation and lowers operator stress, the company reckons. With tank sizes from 900–3,500-litres mounted, 2,200–12,000-litres trailed and also self-propelled, the switch to an Amazone sprayer could provide enormous nancial bene t, it appears. FG
