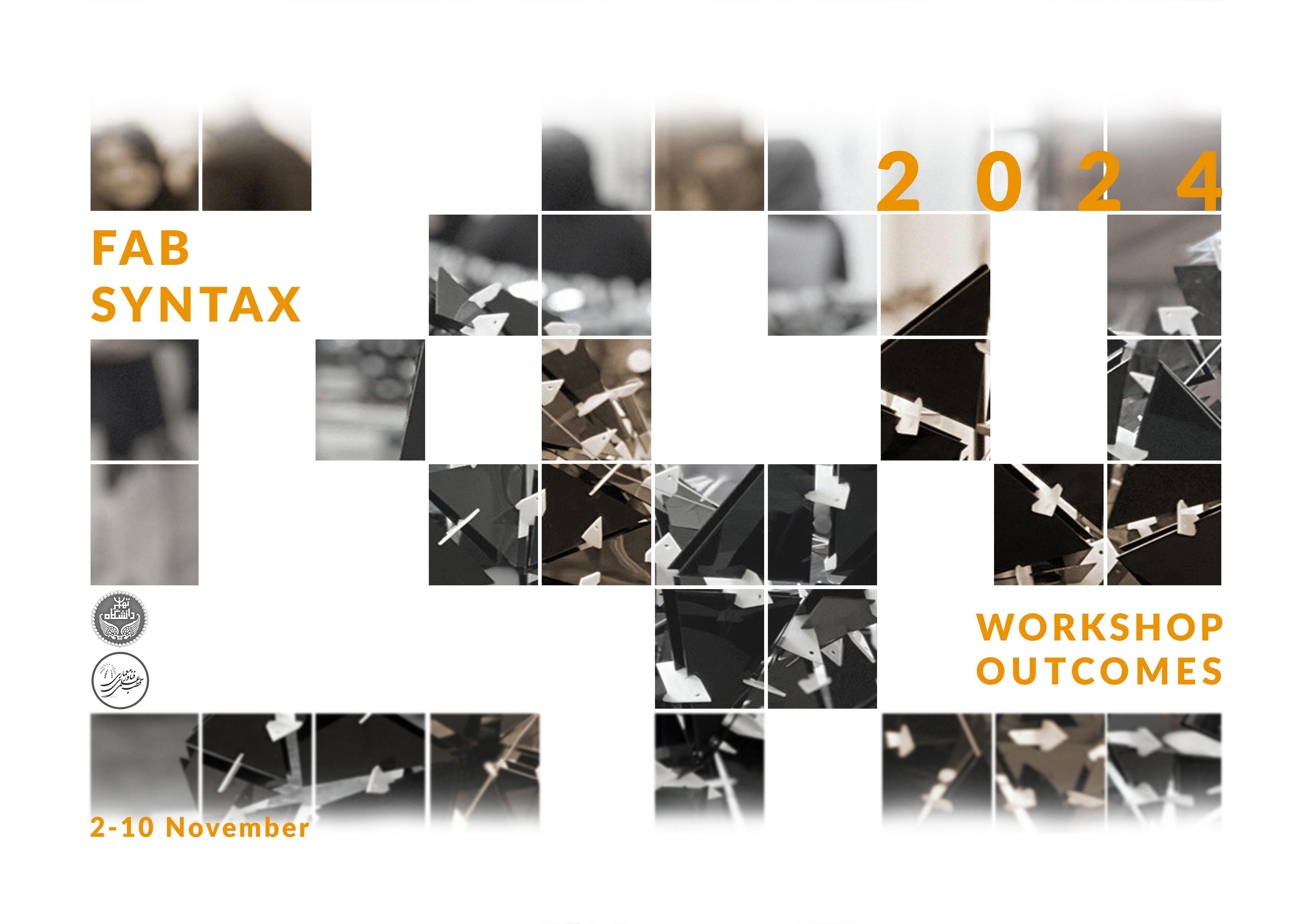
Fab-Syntax workshop
Instructors:
Ali Goharian
Hossein Yavari
Fereshteh Ghafarpoor
Guess Lecturers:
Milad Showkatbakhsh
Ramtin Haghnazar
Nils Opgenorth
Teaching Assistants:
Fatemeh Zarei
Shiva Khamizadeh
Fatemeh Moradalian
Year: November 2024
Organizer:
College of Fine Arts, University of Tehran
Dean of Fine Arts, University of Tehran:
Dr Hamed Mazaherian
Manager of Center of Excellence in
Architectural technology:
Azar Mortazavi
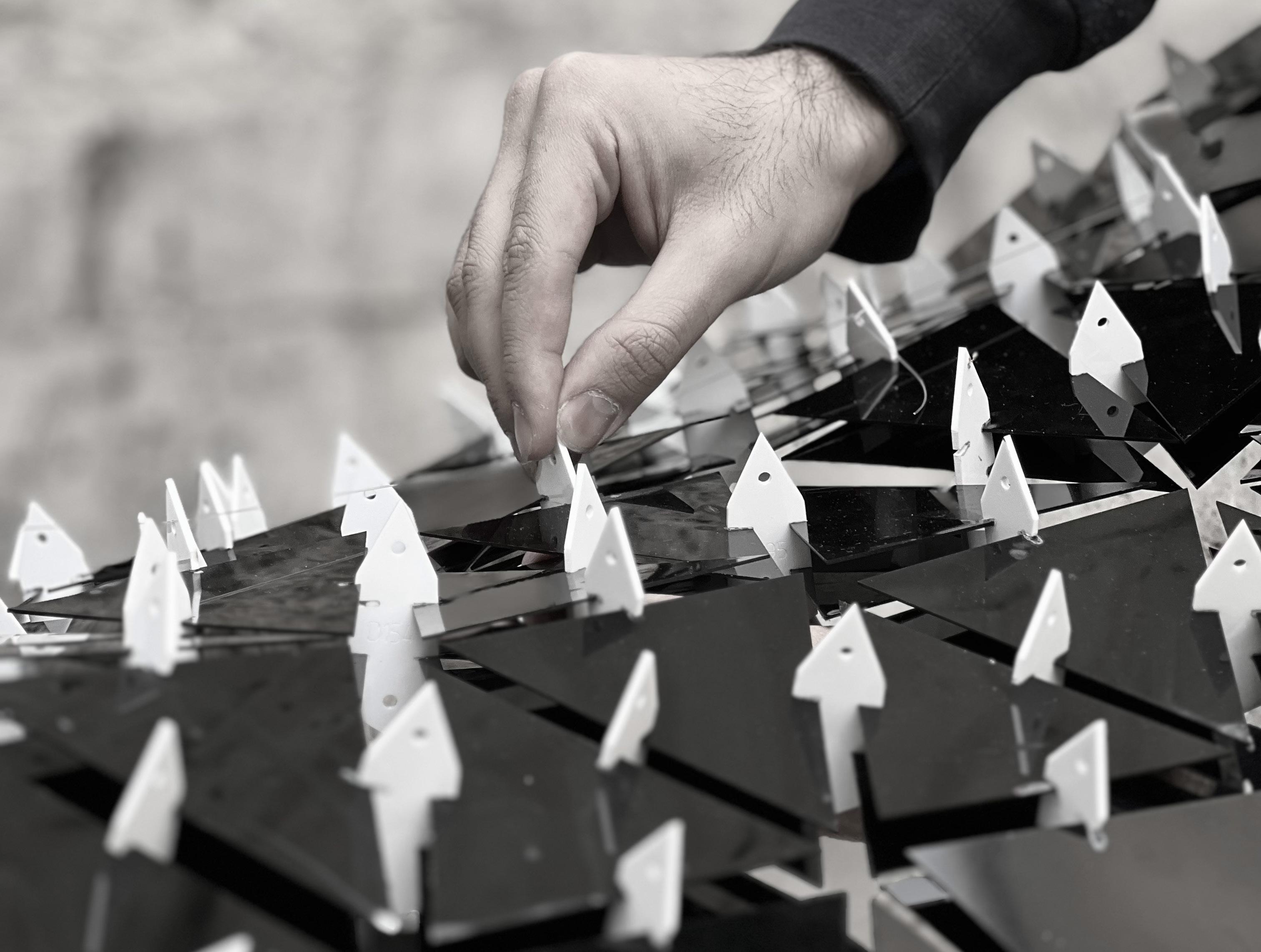
Workshop Overview: Fab Syntax
The Fab Syntax workshop held in November 2024 at the Faculty of Fine Arts, University of Tehran, focused on the design and digital fabrication of multi-shell structures. Participants engaged in an intensive program combining theoretical and practical approaches to explore innovative architectural solutions.
Introduction
The resulting configuration is a highly efficient, lightweight structure that offers an optimized balance of strength, adaptability, and material efficiency. The inclusion of plexiglass and the strategic integration of cables enhance bending resistance, making the design suitable for use in demanding scenarios while maintaining a visually appealing aesthetic.
This advanced design approach holds immense potential for a variety of applications, particularly in the fields of interior design and urban infrastructure development. Within building interiors, the structure can serve as a sophisticated and functional element, offering both decorative appeal and practical functionality. For urban elements, the lightweight nature, combined with the structure’s strength and ability to adapt to external forces, makes it ideal for dynamic public spaces, such as canopies, pavilions, or innovative shading systems.
As cities continue to densify and space becomes increasingly constrained, this design exemplifies how cutting-edge materials and engineering strategies can address the challenges of modern urban living. By utilizing lightweight, durable, and flexible solutions, architects and designers are empowered to create sustainable and high-performance environments that meet contemporary demands while reducing environmental impact.
Ultimately, this smart design strategy represents a significant evolution in architectural engineering. It not only redefines traditional approaches to structural design but also serves as a stepping stone toward the creation of resilient, adaptable, and visually striking architectural solutions that will shape the future of modern architecture.To enhance the effectiveness of boundary conditions in lightweight structures exhibiting shell behavior, particularly with regard to improving bending resistance while minimizing material usage, this innovative design has strategically employed a multifaceted and highly adaptive approach.
The system is engineered to optimize performance under dynamic and variable loads, ensuring efficiency in both material use and structural capacity. Central to this design is the incorporation of two flat plexiglass layers, skillfully interconnected to provide enhanced structural integrity and robust performance across a range of conditions. Plexiglass, a material renowned for its lightweight properties, exceptional strength, and high transparency, is employed here as a superior alternative to traditional materials. Its unique combination of durability and flexibility makes it particularly suited for advanced architectural applications, where weight reduction is critical but must not compromise structural stability. The design takes full advantage of plexiglass’s ability to withstand significant loads while maintaining its form, ensuring long-term performance and aesthetic appeal.
A creative and meticulously engineered connection system links the two layers of plexiglass. This system is pivotal in ensuring the layers work in harmony to resist external forces effectively. The interconnection not only enhances the overall rigidity of the structure but also allows for stable and seamless load transfer, minimizing localized stress and distributing forces evenly throughout the framework.
In addition to these connections, strategically integrated cables play a vital role in the structural system. These cables are designed to manage both positive and negative deviations in the structure, allowing it to respond dynamically to varying loads and environmental conditions such as wind or seismic activity. This innovative cable system enables the structure to adjust to movements and fluctuations while maintaining its integrity, ensuring reliability and safety across a range of applications.
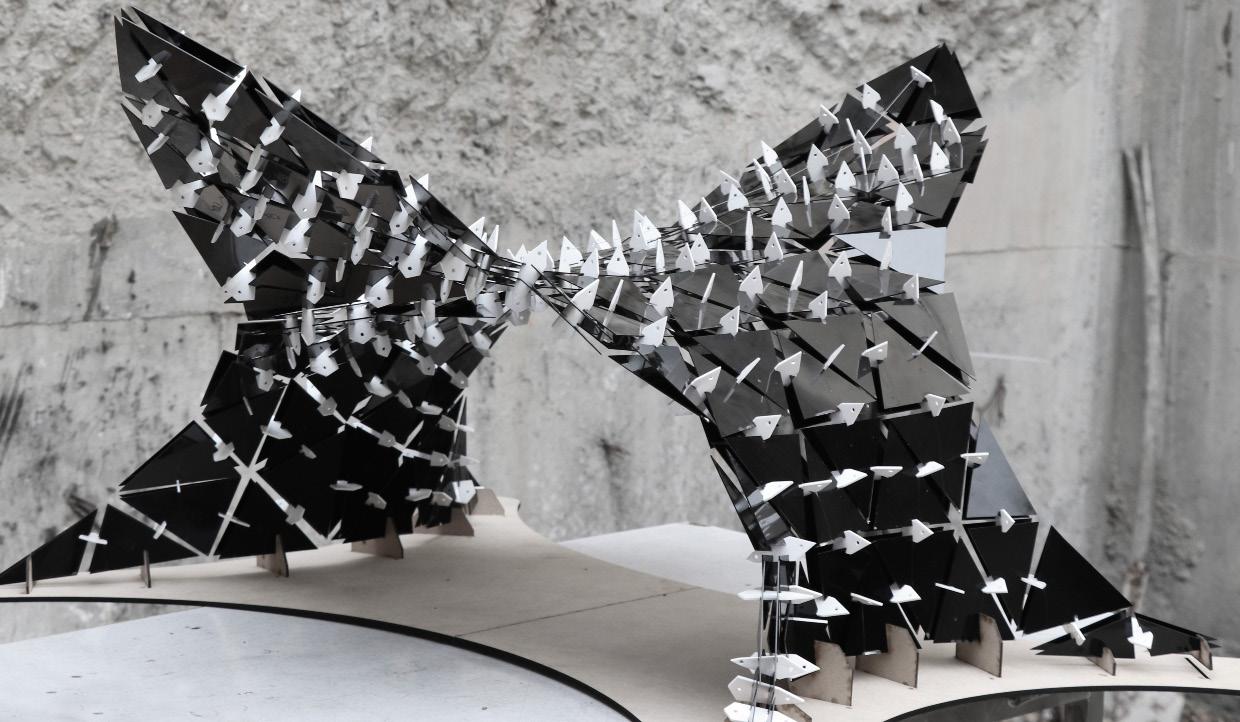
Experimental Design
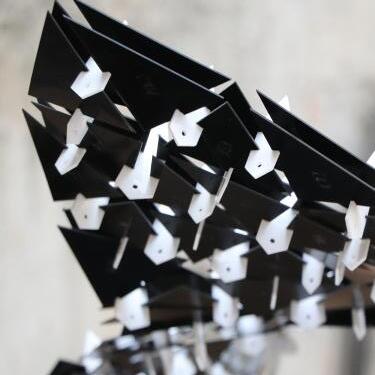
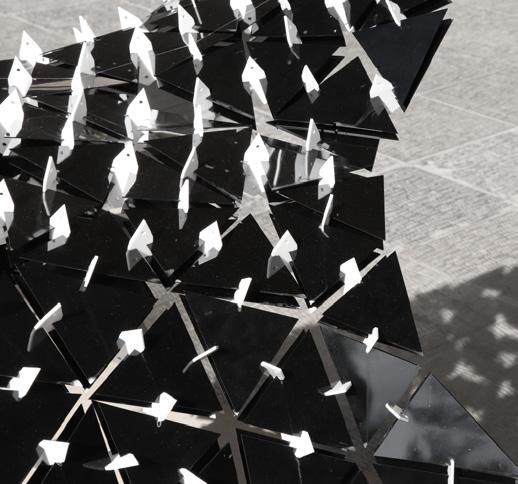
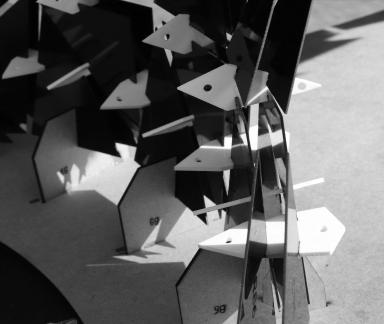
In the development of the pavilion design, which prominently featured the innovative use of double triangular panels, a sophisticated algorithm was implemented within the Grasshopper plugin to enable intricate architectural explorations. The process began with the TriRemesh component, partitioning the desired surface into geometrically coherent panels and forming the design’s foundation. The Offset Surface tool was then used to refine panel shapes, ensuring structural integrity and aesthetic appeal.Advanced Brep topology analysis was employed to map the relationships between panels and establish seamless connections. The Polyline component calculated the midpoints of adjacent panels, enabling the creation of connecting curves that defined the pavilion’s overall flow. Local planes of each joint were established through the Is Planar component, ensuring precise alignment and structural coherence. Finally, points at the peaks of the joints were extruded, resulting in a diamond-like shape that added visual interest and created a dynamic interplay of light and shadow. This approach culminated in an innovative architectural solution, harmoniously integrating form and function while showcasing the potential of modern design technology to push boundaries.
Design Process
This project was based on the concept of combining two Iranian arches to create a unified surface. Initially, the resulting surface was triangulated and then modeled and designed parametrically in two layers, along with connections (joints). After completing the design, the pieces were oriented on the ground and numbered. In the next phase, to examine the structure and connections, a small-scale model was created using laser cutting, providing a physical representation of the final shape and the functioning of the components.
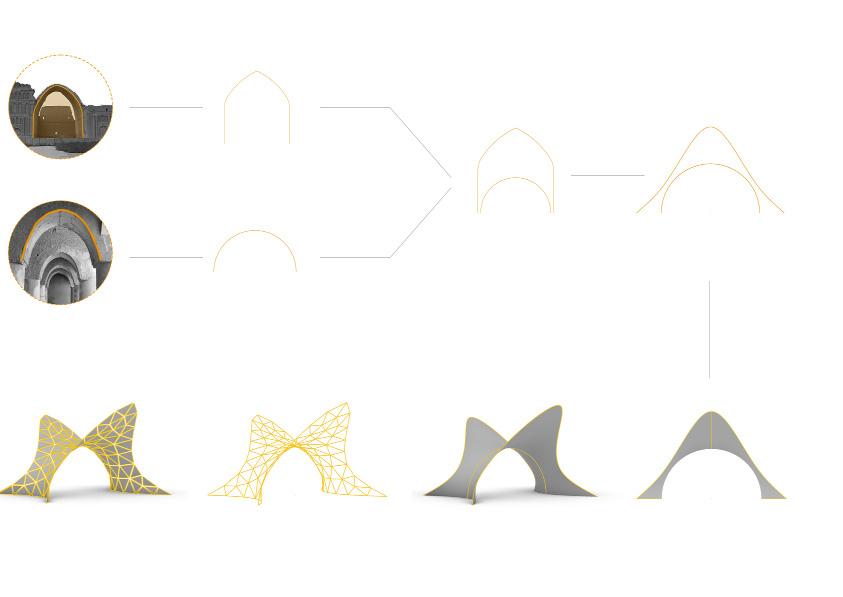
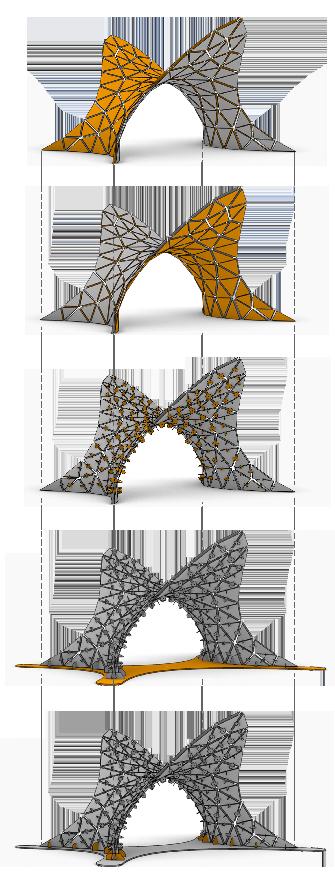
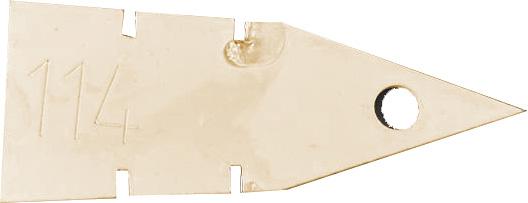
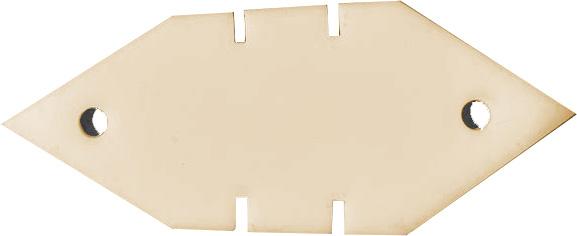

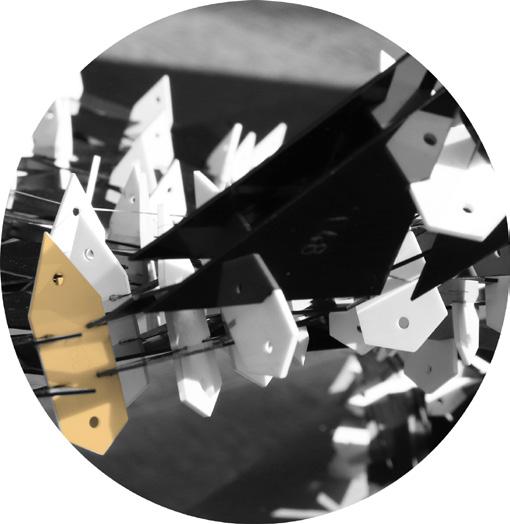
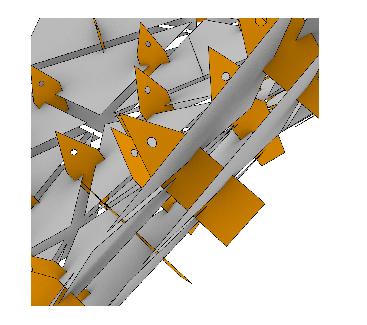
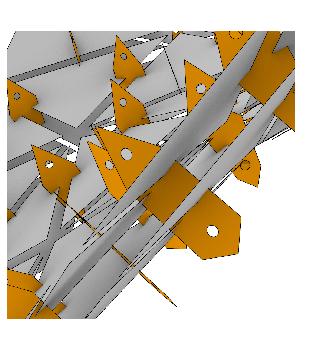
Numbering
In the final design stage, the model is prepared for fabrication by generating a 2D file for laser cutting and applying unique tags to all components for seamless assembly. Using the Text component in Rhino or Grasshopper, each panel, joint, and support element is assigned an identifier for accurate placement. The 3D elements, along with their tags, are then oriented onto a 2D layout using tools like Orient or Flatten, ensuring proper alignment and organization. The layout is optimized for material efficiency, with components arranged to minimize waste while maintaining clarity. Tags remain visible and accurately positioned, serving as reference points during assembly. Additional alignment marks or notches may be added for ease of construction. The finalized 2D file, typically in DXF or AI format, is then exported for laser cutting, ensuring a smooth transition to physical fabrication. This process ensures precision, efficiency, and streamlined assembly for the final structure.
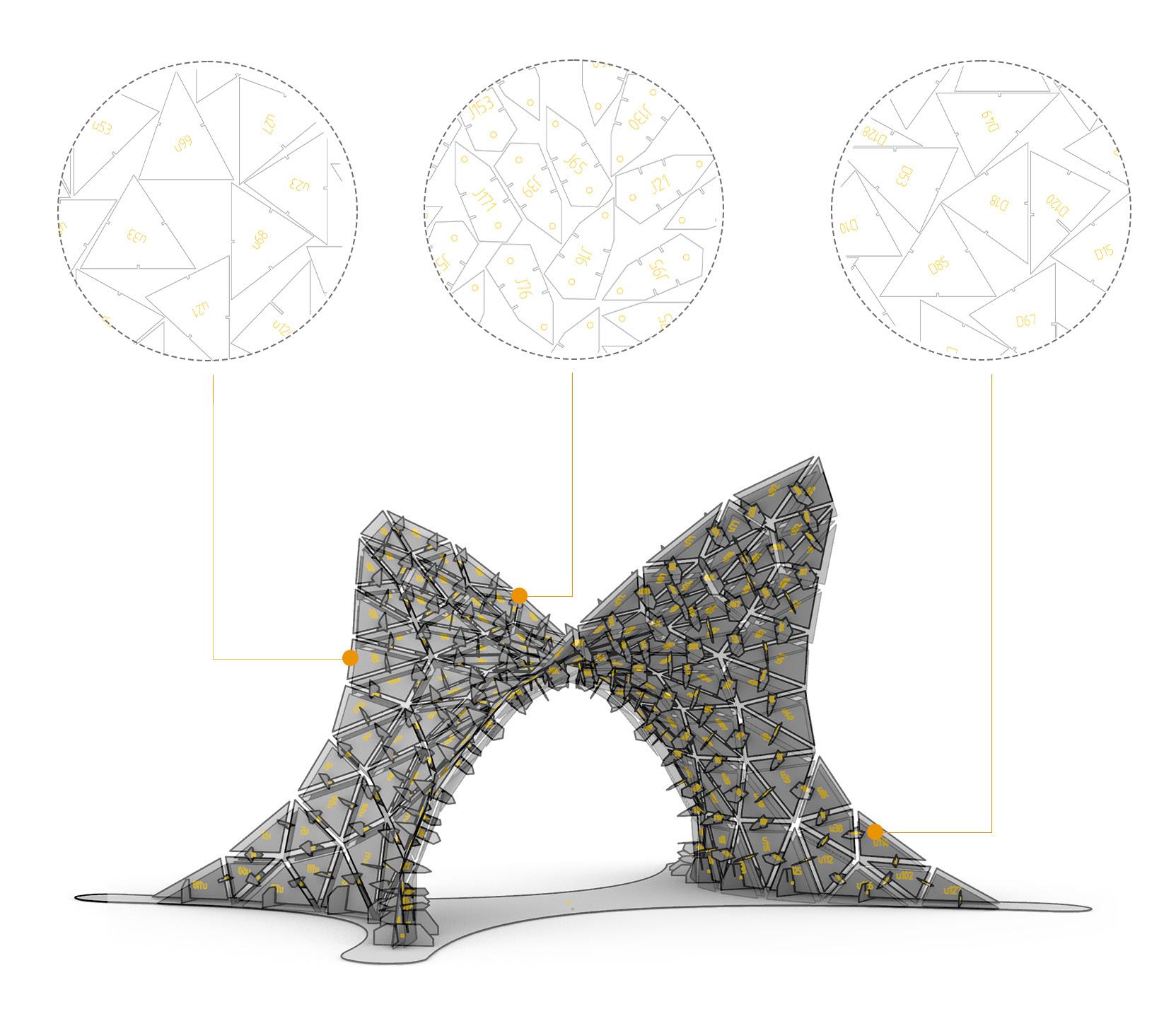
Structural Analysis
To enhance the potential of boundary conditions in lightweight structures with shell-like behavior, while simultaneously increasing bending resistance and reducing material usage, this structure has addressed the challenge with an intelligent approach. The design consists of two flat layers (made of polycarbonate material) connected through an innovative joint system that ensures sufficient structural integrity. Additionally, cables attached to the joints effectively respond to both positive and negative deflections. Overall, this structural configuration has created a lightweight system that provides maximum integrity for optimal load distribution and high bending resistance. This methodology can be highly applicable in interior building design as well as urban elements, offering significant versatility and potential.
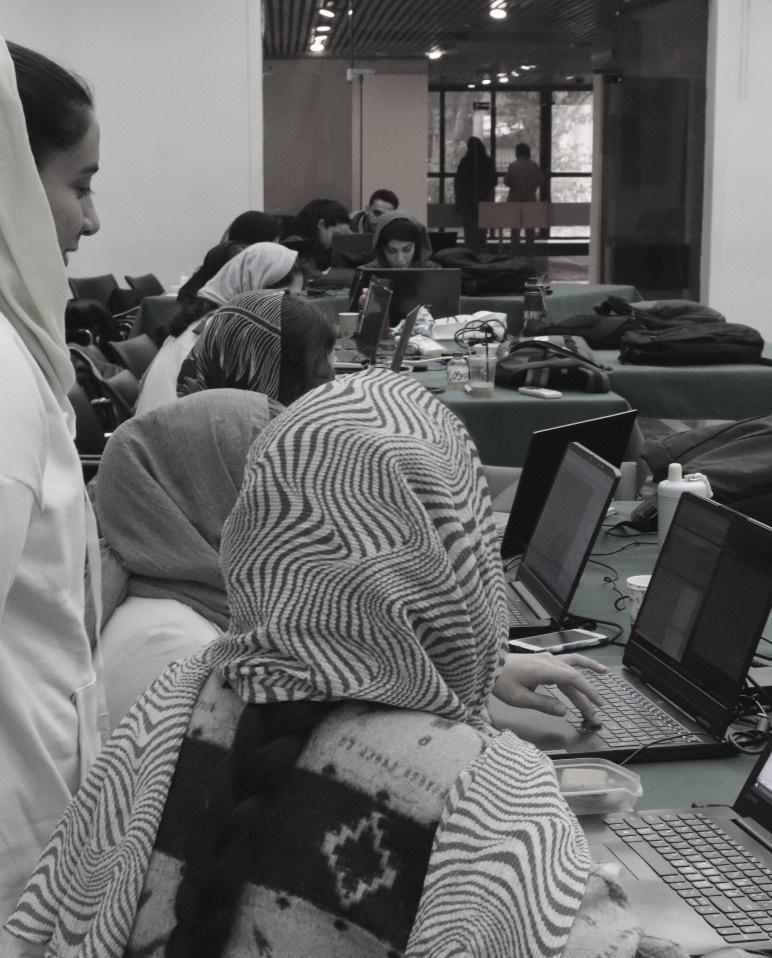
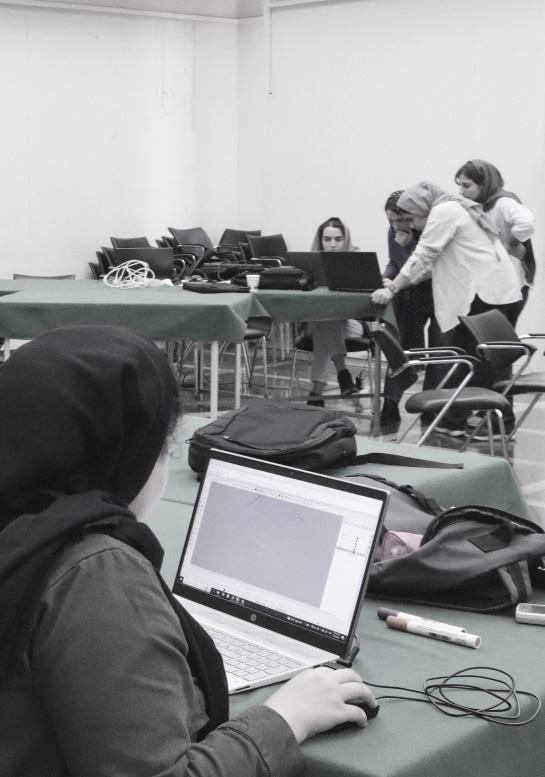
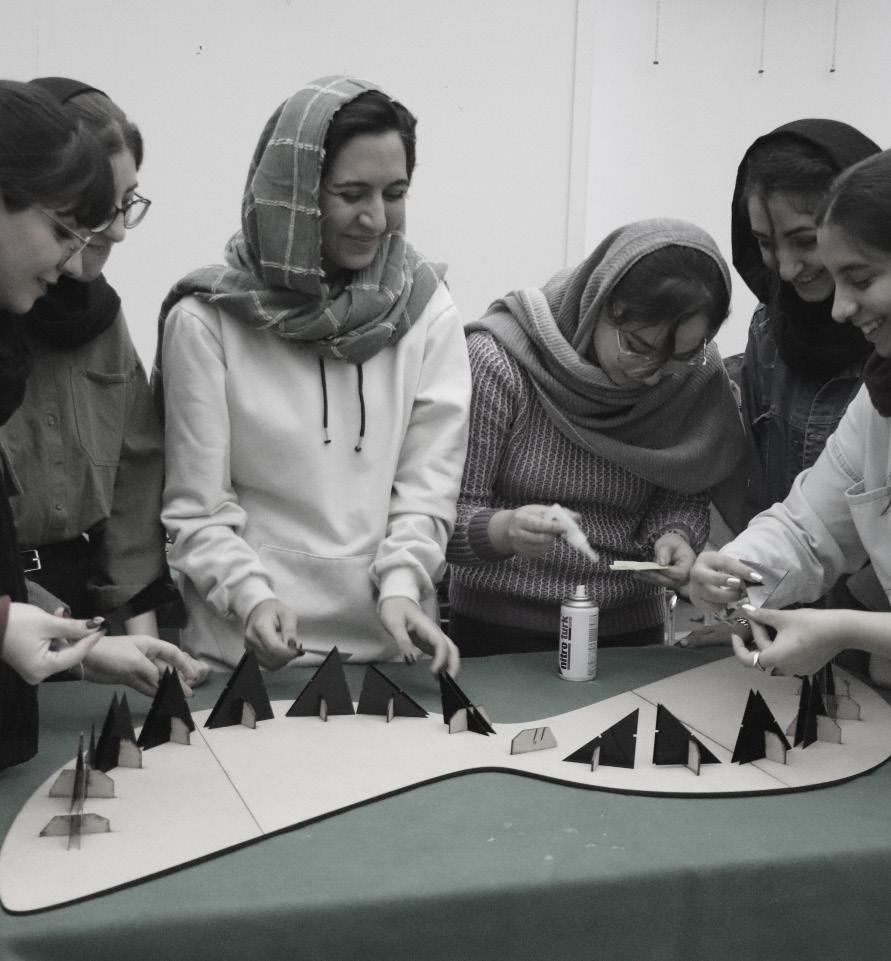



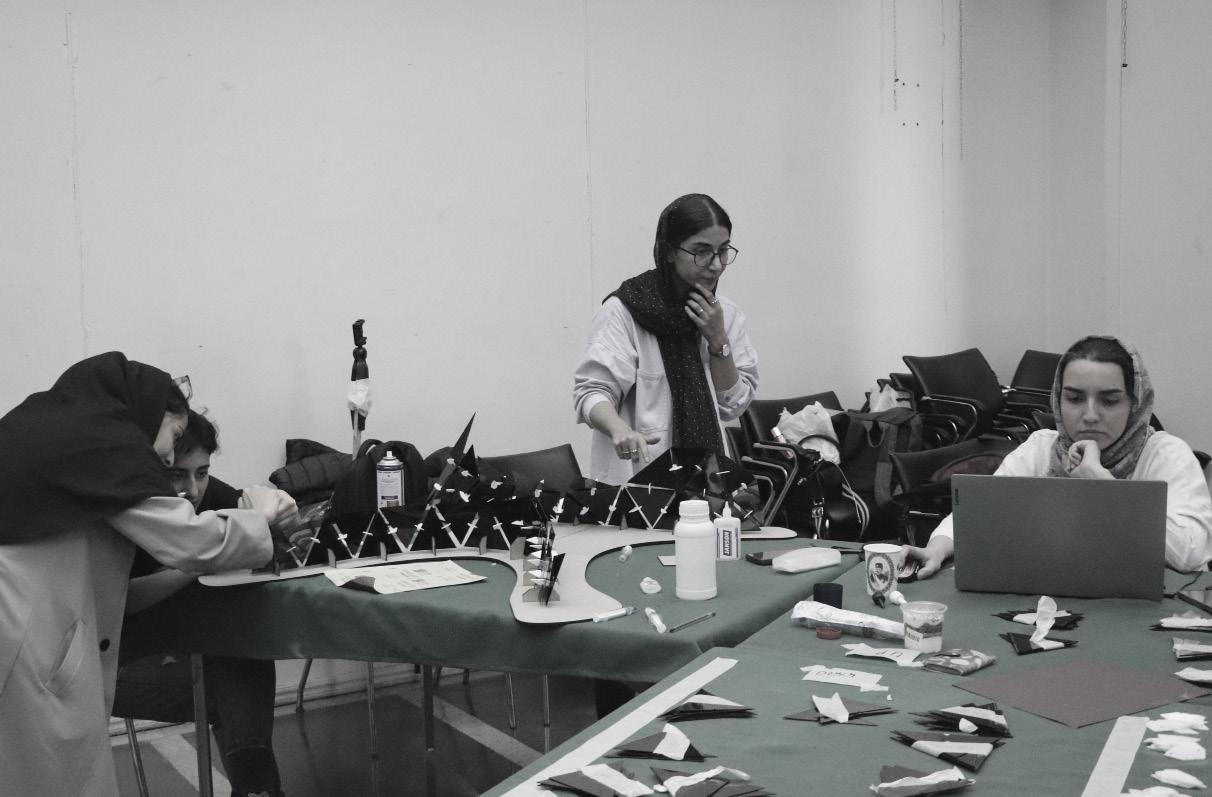
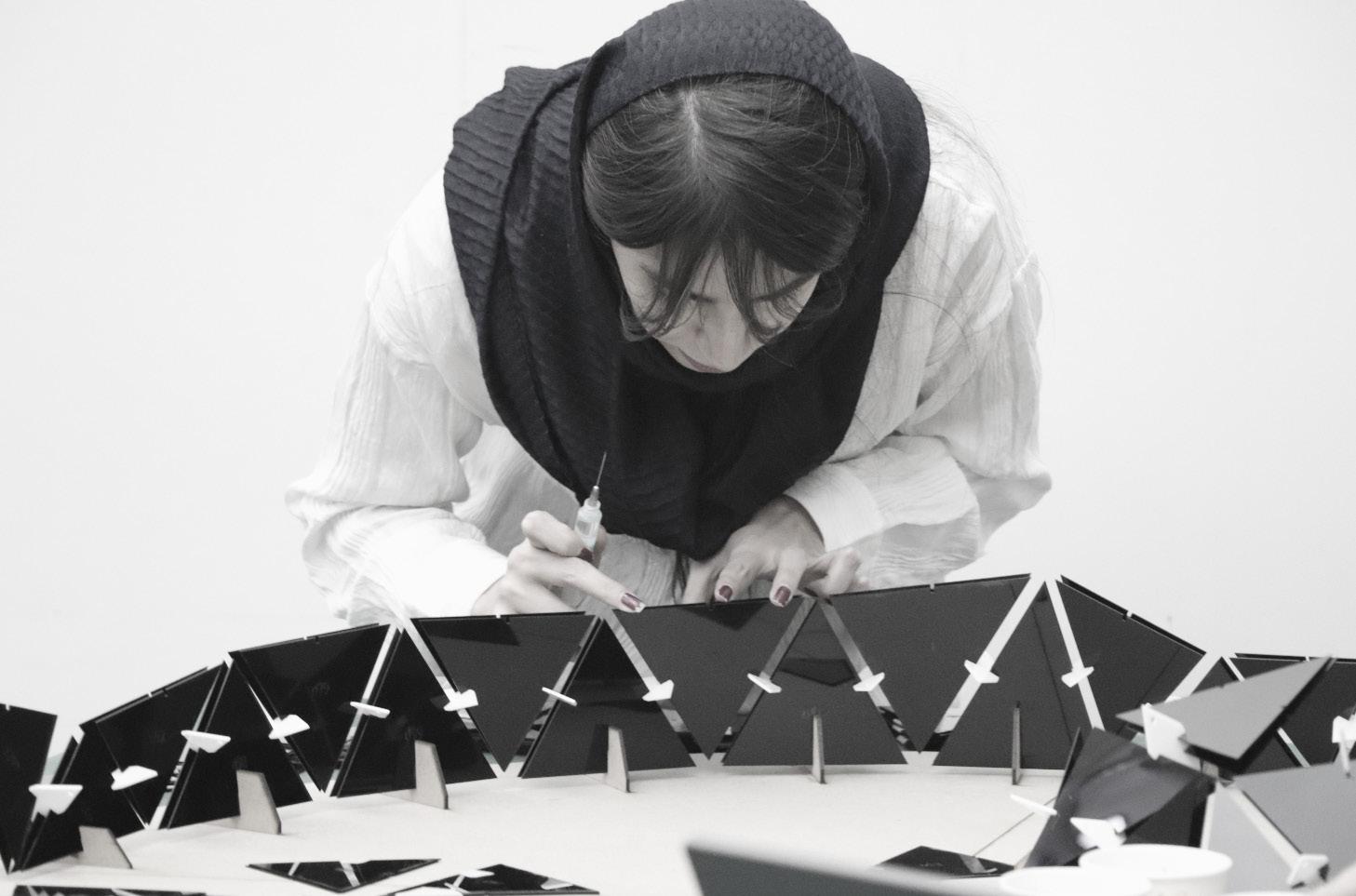
