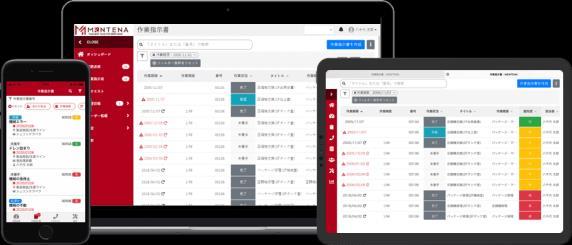
4 minute read
CMMS (Computerized Maintenance Management System
Shuhei Yamaguchi, Japan
Shuhei Yamaguchi is a chief development officer of MENTENA, a computerized maintenance management software, working for Yachiyo Engineering Co., Ltd. He has been working as a system consultant for thirteen years and has provided maintenance systems to administrative agencies such as the Ministry of Land, Infrastructure, Transport and Tourism. Based on this experience, he is currently engaged in a maintenance SaaS (Software as a Service) business for a private company in the manufacturing industry.
Yu Morimura, Japan
Yu Morimura is a manager of sales and customer success of MENTENA working for Yachiyo Engineering Co., Ltd. He has been working as a consulting engineer for five years and has designed river structures managed by the Ministry of Land, Infrastructure, Transport and Tourism and created maintenance plans. Based on this experience, he is currently engaged in a consulting service on facility maintenance management.
Mikiko Iwago, Japan
Mikiko Iwago is a Junior Consultant working for Yachiyo Engineering Co., Ltd. She has been working as a consulting engineer for two years and has been engaged in a consulting service on electric power system and power plant mainly in Africa. Also, she is currently working on BIM/CIM (Building Information Modelling/ Construction Information Modelling/Management) for infrastructure.
Online communication tools enable us to have face to face meetings without meeting physically, which during COVID-19 has allowed us to continue our economic activities against the challenges that the global pandemic has caused, with many companies working remotely. Through this experience, online tools are further attracting worldwide attention. Even in the infrastructure industry, the use of such online tools had been discussed for years before the COVID-19 pandemic from the perspective of cost reduction, knowledge sharing, and diversity and inclusion etc. Such discussions, however, have been accelerated across many fields including the field of the maintenance of industrial facilities or plants.
The challenge When the COVID-19 began to spread worldwide, many companies started to limit the number of workers working on site to reduce a risk to be infected. Before the COVID-19, they could operate and maintain their facilities by watching on site directly, discussing based on the hard copies of log data sheets and ledgers and instructing physically. After the COVID-19, however, the managers are needed to make decisions/instructions remotely without physically viewing based on the data and work report which local operators obtained. Also, the operators are needed to obtain and report the
data rapidly. Therefore, the system to improve the productivity to obtain and visualize the data with easy accessibility are required, which contribute to keep productivity under such a situation and share the data, work report and instructions with all the concerned people working remotely rapidly.
Regular maintenance of equipment and facilities is important for stable operation. The Internet of Things (IoT) and the technologies for monitoring operation, detection and prevention of abnormalities have in recent times significantly improved. On the other hands, since it is still commonly practiced that paper work is physical and offline management software uses non cloud based software such as Excel as the means of creating a databases and knowledge repositories, it is difficult to store and share the know-how and intellectual property of the organization. As such these practices are starting to be recognised as causing delay or omission against troubles that need immediate follow-up as well as for keeping regular operation and maintenance. We are therefore in a new normal.
Action People become positively choose to shift the management of maintenance from paper work or offline tool like Excel to the online system management, by using smartphone or operation tools that are connected to database like Fig. 1. So what could this new world look like? Fig.1 Image of the online computerized Asset Ledger maintenance management system The data including location of the factories and plants, details of line, facilities, parts used for building or facilities, spare parts and track record of repair, etc. can be recorded and managed in the cloud.
Maintenance Record The recording of regular maintenance, parts replacements and transactions for unexpected issues, etc. are logged in the cloud. Managers can confirm the progress of works and are able to make necessary directions/decisions, and such data can be utilized for a regular inspection and troubleshooting.
Analytical Function Regular maintenance works recorded by users are accumulated in a dashboard where they are visualized as a charts automatically. Showing statistics such as the number of man-months, cost of works, details of stoppage and their causes in which numbers, date and time of such troubles are identified. This means that the managers can swiftly assess and analyse the on-going problems on site as well as related maintenance records. This system can be utilized for identifying causes of failure and effective prevention measures while reducing associated costs.
As such, in the new normal, cloud based systems will be helpful for the persons from the bottom to the top of organisations, with those in charge of operation and maintenance able to see changes/updates as they occur. This contributes to optimizing PDCA (Plan, Do, Check, Action) cycle from formulating operation and maintenance plans, grasping the conditions on site, and analysing and reviewing works via records on the cloud data and to take necessary actions for the improvement of works and/or asset management. Such technologies being developed/upgraded under the severe situation during COVID-19 would contribute to the rapidly changing world.