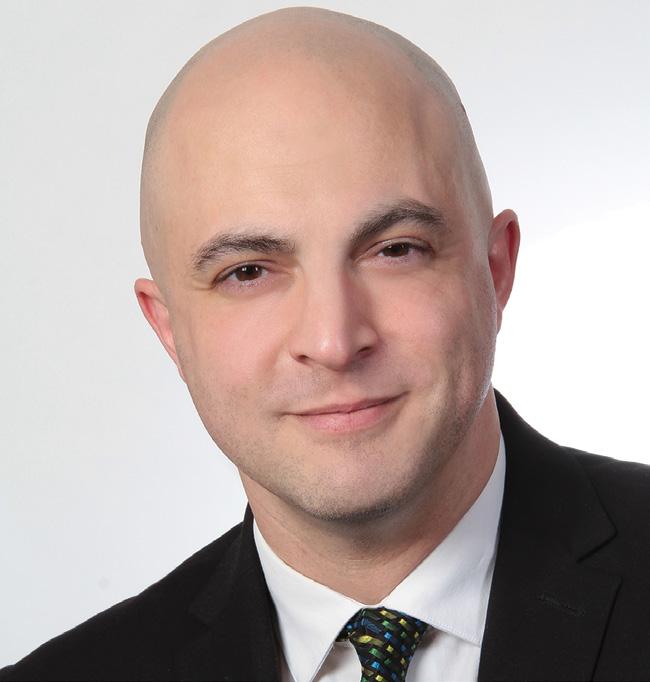
3 minute read
Safety is in the Details; Proper Planning Lowers Risk and Protects Everyone
“By
- Benjamin Franklin
Grinch jokes aside, the list is a good reminder of the importance of worksite safety, especially when working at heights. Citations for Fall Protection (inadequate or nonexistent fall protection systems) remain in the top spot for the twelfth year in a row. When you include categories such as Fall Training (proof that those toolbox talks actually take place); Ladders (overloading, improper landing areas/clearance), and Scaffolding (failure to provide fall protection/ arrest systems), fall-related citations for fiscal year 2022 accounted for over half of all violations.
Hazard Communication citations remain a perennial problem. Citations for mislabeling hazmat or for failing to maintain MSDS on site continue to plague contractors. Indeed, many of the remaining categories on the list involve, at least in part, documentation and record keeping violations. Given the ever-increasing penalty amounts — up to $14,502 per violation and $145,027 for repeated or willful — what action can contractors take to lower their risk of citation and, more importantly, reduce worksite accidents? Create, revise and implement site specific safety plans.
SITE-SPECIFIC SAFETY PLANS
A site-specific safety plan (SSSP) is a written outline that addresses safety procedures, reporting obligations, and other rules, regulations and obligations at a particular location. It describes the steps a contractor has and will take to protect employees and others at the site from accidents and hazardous conditions.[1]
A SSSP will identify site-specific hazards and detail procedures that are to be put in place to minimize exposure to each. It also describes how safety concerns, injuries and illnesses are to be reported and documented. Emergency preparedness plans, such as those for evacuation, rescue, and medical emergencies, should also be included.
HERE ARE SOME ADDITIONAL TIPS:
• Pre-Construction
Site specific plans should not be an afterthought. Instead, Kevin A. Viaña, Senior Vice President and co-construction group leader at Marshall & Sterling, Inc., advises that SSSP should be developed during the pre-construction or bid stage. This allows “the actual costs of implementing the plan to be incorporated into the bid.”
Site inspections are crucial as well, as they often uncover potential safety hazards not otherwise visible from the plans. For example, locations of temporary structures and staging areas can impact scaffolding which in turn can render an otherwise acceptable safety policy or system impractical or ineffective.
• Make it Project Specific
While a SSSP’s outline and general requirements typically carry over from job to job, specific requirements may not. Potential hazards can vary greatly from job to job, as well as the plan of action for each. Emergency measures that work in New York City may not be effective in Albany.
Project type further impacts SSSPs. A shovel ready multi-family project with open access might involve far fewer hazards and safety concerns than a rehab project at an existing hospital. The same goes for each SSSP’s communication plan. A subcontractor working for a CM at a private job may have a far different communication tree than a Prime on a public job being supervised by a CM. Add an owner’s representative to the mix and the plan might require further revision.
• Provide Details
An SSSP should provide enough detail so that its objectives can be met. For example, reporting criteria for hazardous conditions is hardly effective if the responsible individuals are neither identified nor the methods of notice stipulated. This is why the recent trend of issuing boilerplate or canned SSSPs, none of which provide the necessary project details but instead simply restate OSHA and other regulations, is so troublesome. This practice causes further problems where the cited regulations are updated but the plan is not.
SSSPs deserve just as much attention as any other contract document, perhaps even more. Fortunately, there are many online resources that contractors can look to for help. OSHA’s website offers much information, including a step-by-step guide on how to implement a safety program.[2] Your insurance agent can also be a tremendous resource, helping you create a comprehensive safety plan specific to your trade and its inherent hazards, and to identify the measures and training required to prevent or lessen the risk of injury and to quickly respond to accidents should they occur.
Finally, don’t forget implementation! The best plan is useless if it is not followed. This is why construction-oriented Insurance Risk Manager/Brokers offer loss control services, services that include, per Kevin Viaña, “routine site visits to make sure the employees and sub trades are following the plan as well as make suggestions on improving the plan as the project progresses.”
[1] See “29 CFR 1926, Safety & Health Regulations for Construction.”
[2] https://www.osha.gov/safety-management/step-by-step-guide