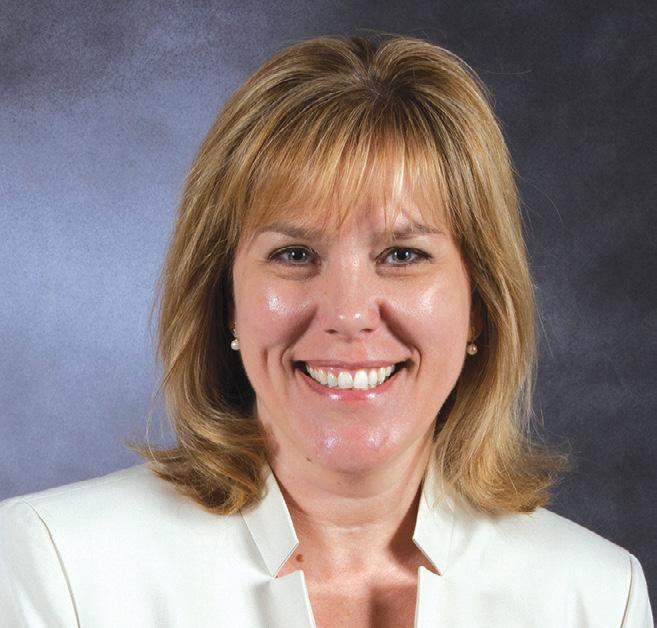
2 minute read
When Will the Supply Chain be “Normal” Again?
We’re nearly three years out from when COVID basically shut down the world, setting off global supply chain issues that have yet to return to normal.
While price and supply are stabilizing for some construction materials, they’re increasing in volatility for others. This may be one time the pendulum will not swing both ways. Even though we have a grip on COVID (for the most part), several other factors that caused the supply chain to implode continue, and there’s no timeline for resolution.
The labor shortage (which is expected to worsen as U.S. infrastructure work gets underway); the war in Ukraine; China’s faltering economy; a huge increase in supply chain cybercrime, and regulations all have a role to play in the supply chain’s recovery.
The outlook is changing month-tomonth, with some estimating a return to normalcy by the end of 2023 or, maybe, 2024. This begs the question: By that time, won’t new approaches have taken root, forever changing how the supply chain works (or doesn’t work)?
Border States, a supply chain solutions company, reports that by mid-September lead times were decreasing, but remained 85 percent longer across all markets and products than pre-pandemic. Similarly, the port backlog is decreasing but it is not back to normal. For construction, distribution equipment (circuit breakers, load centers, panels, switches); EMT fittings (1/2”-4” compression and set screw connectors); wiring devices and wall plates; PVC and weatherproof boxes; fuses; meter sockets and hubs; ground rods, and automation products controls are among the categories that still require extended lead times include
In fact, ConstructionDive.com in September warned, “The reduction in oil prices is slowly being reflected in materials like roofing products, but that remains an area of concern. Similarly, delivery costs are easing, but there is still a shortage of drivers … Our greatest challenges are anything that involves metal, wood or glass in construction.”
In October, FreightWaves.com reported that all major indices used to track supply chain performance show it’s improving, but still has a long way to go to get back to pre-pandemic levels. For example, as of one Sunday in October, “ship-position data and queuing lists showed 109 container vessels waiting off U.S. ports ... That’s down from a high of over 150, but still far above the pre-COVID normal in the single digits,” FreightWaves noted.
Susan Howell, CPA, Partner RBT CPAs LLP
diversified supply chain with enough slack to ride out uncertainty; build for continuity; invest in systems that enable smooth operations in periods of high labor turnover’ and consider smart hedges. Make strategic decisions about where to hedge (e.g., pre-buying raw materials) and consider areas most susceptible to destabilization.”
What can
be done?
A Supply Chain Management Review article advises firms to “proactively address supply chain disruption; focus on building a
Rather than risk an influx of projects and construction growth, some firms are opting for early-stage procurement over the “just in time” inventory strategy of the past. With early-stage procurement, all supplies and materials are purchased and stored at the start of a project, rather than in phases. This can impact everything from warehouse space and equipment to staffing, procurement, project timelines, budgets, insurance policies, and cash flow. As noted by Jason Earnhardt, Austin Commercial Supply Chain Manager, in Building Design + Construction, “We have essentially become our own in-house logistics company, all in the name of keeping our clients’ projects on track.”