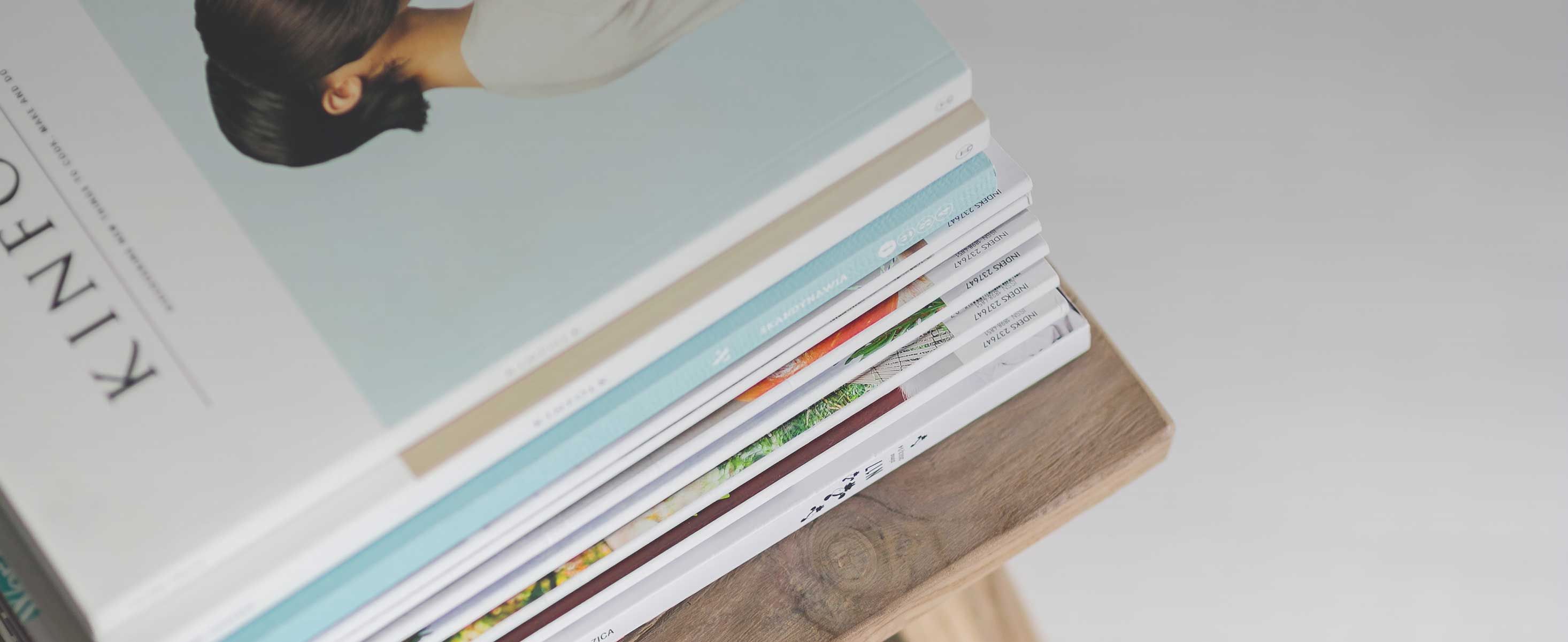
4 minute read
Special The main benefits of ‘The new abrasives’: abrasive materials geared to the single-disc machine instead of the traditional method with abrasive nets
ABRASIVES HELP TO DETERMINE THE QUALITY OF THE WORK
CONSTANT RESEARCH ON THE USE OF NEW MATERIALS
Advertisement
We have often explained how the various disc sanders can be used. The possibilities are still impressive. The deployment options remain highly extensive partly due to developments in the abrasives which can be used with these sanding machines. Equipped with very hard abrasives (brushes or heads), the machines can, as it were, ‘scrape’ the screed. This means it is easy to remove old carpet or adhesive residue, putty, and such like. We do all that in the preparatory phase.
The secrets of sanding One of the hardest tasks in fitting solid parquet is the sanding. The execution of the various sanding sessions largely determines the quality of the end result. Let’s be honest here. That’s precisely why fitting solid parquet, and certainly traditional parquet (with no tongue and groove), is still the pride and joy of professional parquet fitters. Perfect sanding requires a combination of elements: It requires a certain force, a certain motion, and a specific grain. All three elements have to be perfect and, to that end, the worker’s skill, the machine used, and the abrasive play a major part.
Certain force Wood (even hard wood) can be eroded if the necessary force is exerted. The force exerted on the wood during sanding comes from the quality of the machine and the way in which it is used. The machine affects the sanding force in two ways, firstly through the speed at which the abrasive passes over the wood and, secondly, the downward force exerted by the weight of the machine.
Specific abrasive Traditional abrasives, namely sandpaper and emery cloths, consist of layers. The ingenious construction of the diverse layers determines the technical features and the final quality of the end product. The shape of the abrasive is designed for the sanding machine for which it is meant i.e. endless belts for a belt sander, round discs for a rotary machine, smaller discs for a multi-disc machine, abrasive pads for the orbital sander, etc.
Structure The ‘bearer’ A conventional abrasive basically consists of four or five layers. The bottom layer is the bearer. The various bearers largely determine the flexibility and strength of the abrasive.
Adhesive layers and grains An adhesive layer is applied to the bearer. We then sprinkle the abrasive grains onto the adhesive layer. An ingenious technique ensures that the grains always have the sharpest edge upwards in the adhesive layer. The various possible grain materials determine the scope of the abrasive. A layer of adhesive is applied on top of the grains in order to anchor the grains fully on the bearer.
Top layer You can also add an active abrasive as a top layer. This top coating ensures that the sanding dust is discharged properly during use and pro vides cooling. However, as the title says, the bearers, abrasives, structure, and the entire sanding technology are constantly subject to research and development. We will let the players themselves say who offers innovative bearers or abrasives.
Materials In the world of parquet there has been an improvement in the quality of abrasives in the direction of zirconium and ceramics. Glass is not used in the world of parquet and diamond even less so in view of its cost price. The four most important materials are corindon, carborondum, zirconium, and ceramics. Each of these materials has specific assets and drawbacks. The key is to choose the right material for the right application. For parquet and wooden floors, and certainly for the application of certain specific designs such as ‘distressed’, the market offers scores of new and innovative brushes and other fairly hard moving tools. These, too, are developing constantly.
Two specialists
Blanchon In the world of parquet there has been an improvement in the quality of abrasives in the direction of zirconium and ceramics. Glass is not used in the world of parquet and diamond even less so in view of its cost price. The four most important materials are corindon, carborondum, zirconium, and ceramics. Each of these materials has specific assets and drawbacks. The key is to choose the right material for the right application. Blanchon strongly recommends three sanding sessions (with separate grains) and (usually) a polish with a single-disc machine. Blanchon offers an assortment of various abrasives and bearers such as endless sanding belts, rolls, discs, etc. An important trend which is noticeable here is the increase in the use of the multi-disc sander. These machines are extremely efficient, but due to their relatively low weight they cannot be deployed for some heavy tasks (e.g. the removal of old coats of lacquer).
Pallmann Aluminium oxide abrasives have been virtually obsolete in woodfloor sanding and technological progress has moved on from zirconia alumina to ceramics and finally to diamonds as the current cutting materials for sanding wood flooring. Diamonds are becoming more and more important for the sanding of wooden floors, because it is possible to remove extremely hard coating systems, such as UV-hardened lacquers or DD lacquers. Pallmann abrasives are optimally adapted to Pallmann sanding machines and the intended use. So Pallmann recommends ceramic abrasives for coarse sanding, zirconia alumina for subsequent sanding and silicon carbide for fine sanding. With the new abrasives, it is possible to replace almost all the work of a belt sander with the Pallmann Spider triple disc sanding machine. In addition, the brushing technique for the Pallmann Spider offers the possibility to structure existing floors as well as to renovate already structured surfaces without having to sand the structure.