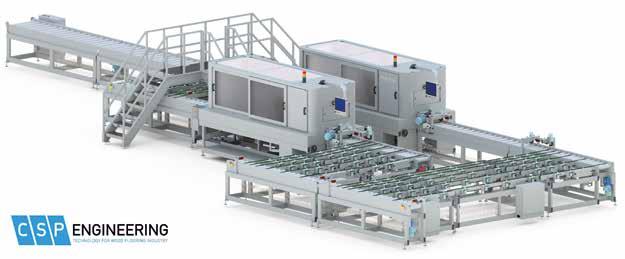
5 minute read
Special Suppliers of filling machines
REPAIRING HOLES AND CRACKS MECHANICALLY
BOTH SMALL PARQUET PRODUCERS AND MAJOR FITTERS ARE INCLUDED
Advertisement
Parquet production involves some manual work. One job which springs to mind is the manual and visual inspection of the floorboards. Planks with obvious cracks, gnarls, or other flaws are removed by one manual worker and collected by another for repair. We can all imagine how that repair work proceeds. The hole is repaired with a filler which is spread, dried, adjusted, sandpapered, and possibly coloured. All those chores are carried out away from the production line.
Machines for parquet production We now know that some renowned machine makers have designed several high-tech machines to computerise parts of the parquet production process. A modern parquet production line is full of those technological solutions. As we have often said, anything can be computerised, from the plank input over the floorboard production, finish application, and packing and labelling to the collection for transport to the warehouse. Since the application of the finish (oil or lacquer) is now increasingly part of the production process, the preparatory tasks for the finish also have to be included: tracing and repairing small flaws which cannot be reconciled with the planned selection (A, B, etc).
Smart filling machines Semi-automatic or fully automatic filling machines can be deployed on the production line to take over partly or fully the tasks of everyone who is (was) involved in the inspection and repair of possible imperfections. The extent of perfection with which this is done has given rise to the term ‘wood cosmetics’: manicure, pedicure, and perfect facial treatment down to the last detail. Here, too, technology yields a higher degree of perfection than that of human skill. The machine simply doesn’t make any human errors, either in terms of judgement or in terms of repair.
Tracing faults Faults in the floorboards are detected via scanning. The scanner works in 2D or 3D and processes the images in seconds. One thing’s for sure: Nothing escapes the watchful eye of the scanner. Each flaw, however small, is detected and assessed. No human being could ever rival that same vigilance over each individual floorboard. Since the machine is deployed for use on the production line, it is also not necessary to collect the damaged plank from the conveyor belt for repair.
Measuring and filling In this area, too, the machine achieves a higher grade of efficiency than a human being. Indeed, the scanner measures the exact dimensions of the damage and calculates infallibly the amount of filler required. Another important point here is that the filler achieves the same hardness as the wood. The filling is done under pressure. The amount of filler is calculated exactly so that no product is lost.
Machines for large and small The big specialists offer solutions in fully automatic or semi-automatic machines. They can be stand-alone or included on a fully computerised production line. This means that machines also offer solutions for smaller parquet manufacturers or for fitters who carry out some of the production themselves. You could call this ‘semi-customised’.
Two specialists
CSP Engineering PAR-Filler® is the brand name for automatic filling machines, developed for the industrial production of wooden floors. These high-tech machines have a unique detection and injection system. Defects such as cracks and knots in the surface of wooden floorboards are detected with great precision, after which wood filler is injected under pressure into the defects. CSP Engineering has 3 models in the range, each aimed at a specific production capacity. In consultation with the customer, CSP Engineering provides the most appropriate configuration on the input
and output, ranging from semi-automatic to full-automatic solutions. Most PAR-Filler® installations are operated by 1 operator. - PAR-Filler® Mono is equipped with 1 applicator. This machine is set up as a singular machine for limited production capacities. A duplex arrangement of this machine is particularly suitable for growth companies. - PAR-Filler® Duo is equipped with 2 applicators, particularly suitable for medium-sized production companies. - AR-Filler® Duplex is a high capacity machine and has 2 parallel filling lines. The 2 process lines can work separately for filling different qualities and / or various colours. This machine comes with automatic feed for loading the machine and can be equipped with a double push-off buffer for manual stacking of filled floorboards.
Since 2014, more than 30 PAR-Filler® machines are operational internationally. PAR-Filler machines are developed in accordance with Industry 4.0. The many data generated by the machines enable
CSP Engineering to advise its customers on various facets of the machine, capacity utilization, yields, periodic maintenance and more. New developments: - Through this 'partnership' with the customers, new needs in the market are noticed, which are converted by the R&D engineers of
CSP Engineering into new functions, new product types and even 'smarter' working of the machines. - CSP is fully committed to new developments. With regard to wood fillers, innovation projects are in progress. The new fillers will be even better suited to the needs and finishing processes of large industrial production companies.
Wintersteiger NEW: TRC Preclean.
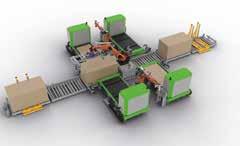
Automated system for removing soft, loose damaged parts. TRC Preclean enables automated pre-cleaning of wood surfaces. Before repairing defects – before filling – it used to be necessary to manually pre-clean raw planks. For example, bark inclusions or soft parts are removed from knotholes while cracks or similar defects are cleaned. The TRC Preclean scans the defects, evaluates the data, and processes these areas, leaving the wood with a completely natural appearance. Process-optimized alternate processing of two clamping tables allows secondary processes such as loading and unloading, scanning, and evaluation to be carried out while defects are being cleaned. The TRC Preclean can be upgraded with additional modules and can process plank layers and boards up to 2,500 x 1,300 mm. Wood dimensions: Length: Up to 2,500 mm Width: Up to 1,300 mm More information: www.wintersteiger.com/trc
Filling technology for wood flooring MACHINED FILLING OF KNOTS IN PARQUET
before after
High quality filling result
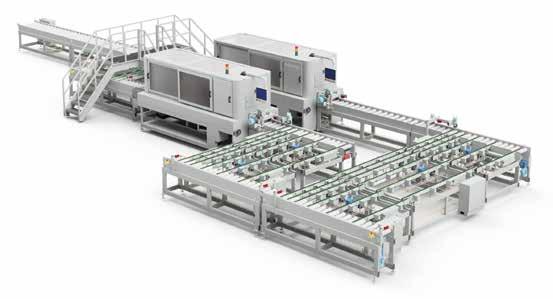
Reduction of labour costs High production capacity Only 1 operator Wood filler ready for use Available in 8 colors