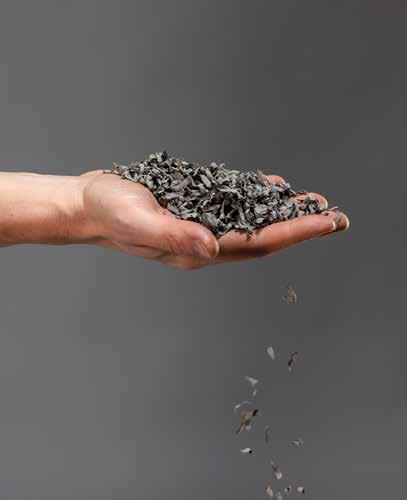
4 minute read
Special Sustainability, ecology, recycling options, and how the avoid transport costs
START WITH THE BASICS
A BETTER WORLD STARTS WITH A COMPLETE PRODUCT RETHINK
Advertisement
Photo – Välinge
For many years, we’ve been bombarded constantly with concepts such as sustainability, circular thinking, re-use, environmental awareness, CO2 emissions, etc. And so, obviously, companies are paying more and more attention to those matters. Yet how do they approach ecology, recycling, and transport? We note that lots of companies start with the basics. They examine their own production in detail and see how proactively they can go to work.
During our market search, we found a perfect example of this ‘optimal ecological thinking at source’: Välinge Innovation. This Swedish company, formed in 1993, has long been known as a pioneer in technological revolutions for the flooring market and has a high-tech R&D centre.
A rethink of one’s own product is clearly in evidence with the Liteback technology which it brings onto the market, technology which is being used by more and more licence holders. With Liteback, the product is viewed from as many perspectives as possible so that it is produced and transported as sustainably as possible even before it leaves the factory.
Less weight
We noticed an initial operation with something so obvious that many people forget it, namely the weight of the supplied product. In the case of Liteback, they use so called core technology for thermoplastic floors, such as LVT, SPC, and WPC. They also use raw materials as efficiently as possible and at the same time they make their floors lighter. The benefit for the environment speaks for itself, as does the benefit for the floor fitter whose back is put under less strain.
According to the producer, they remove material from the core to reduce the weight of the end product by up to 20%. In specific figures they claim that it is possible to remove up to 3.5kg from a single packet of a typical 5mm LVT product. Therefore, various factors mean that all operations with the product are now easier and more efficient, from the delivery from the production unit to the time of purchase and during the fitting by the end user.
Re-use of material during production
Obviously, there’s more to it than just a weight reduction. It is possible to re-use the material used during the process to make new floor products. That can reduce the use of material by up to 20%. Using raw materials more efficiently can lower the number of deliveries to production units and, moreover, means that sea containers are loaded more efficiently with lighter products. This reduces not only the number of journeys and amount of storage space required, but also the CO2 footprint.
If you actually do the calculations, you find amongst other things that the 60 million square metres of LVT, SPC, and WPC flooring sold in Europe in 2017 could have been reduced sharply with Liteback. Firstly, more efficient use of raw materials during that year would have saved no fewer than 117,000 tonnes of raw material. Secondly, about 4,800 fewer trucks would have been needed to deliver the products and, moreover, 3,400 ship containers would never have been shipped. To make this completely clear, less use of raw materials and fewer journeys would have reduced CO² emissions in 2017 by almost 80,000 tonnes, the equivalent of annual emissions from 56,000 passenger vehicles.
Milling grooves
Finally, we still have to explain how all this is achieved in practice. At Liteback, they mill grooves on the rear side of the floor plate using a grooving machine. The material removed during the process is recycled in the production process to reduce material consumption by up to 20%. The grooving unit can be used as a stand alone tool, but at the same time it can also be integrated into the regular production process, so that there is no longer any need for an extra handling of the panels.
CORKART
CORK FLOORING, ECOLOGY & RECYCLING Many flooring options have “green” credentials but not all are environmental and economically sustainable. CORKART cork flooring is. Biodegradable and recyclable, sustainable production processes with a strong positive impact on the local economy and environment CORKART cork flooring has amazing eco credentials. Cork is a 100% natural, renewable environmentally friendly material. It is stripped from the cork oak trees without any damage to the tree and regrows naturally every nine years. Cork biodegrades completely and can be easily recycled. It is remarkably resistant, hypoallergenic, light and particularly comfortable due to its unique buoyant cellular composition, which makes it a perfect noise and thermal insulator. Although nearly all Cork Oak forests are in southern Europe, they play an important role in the planet's ecosystem. Its unique cell structure and composition enables the innate retention of CO2 and supports carbon pollution reduction. Cork oaks have a special characteristic of retaining CO2 innately, contributing for reducing greenhouse gas emissions globally. The striping helps the trees regeneration, strengthening its ability to absorb CO2. Cork oak forests are also vital source of employment, reduce soil erosion and guarantee the survival of local communities. CORKART continuously work to make factory infrastructure and production processes more efficient using ecological materials, lower environmental impact, use effectively and recycle. One of the strategies is the recycling in the manufacturing processes: 90% of the waste is recycled and re-used. Moreover, 90% of the energy used in processing cork is made from burning cork dust, a byproduct of production. Cork floors were popular by its fascinating natural pattern and color. With technological advances you have now different eco-friendly cork flooring selections. CORKART Design Concept has exclusive collections that share the unique features of a cork floor with realistic wood & stone looks.
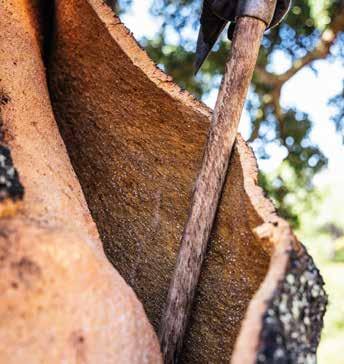