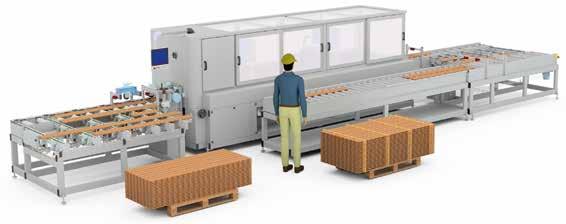
9 minute read
Special Producers of filling machines
MECHANICALLY PERFECT
FILLING MACHINES ARE OFTEN USED ON FULL PRODUCTION LINES
Advertisement
Jan Peeters (CSP Engineering -B)
‘The development of a new and much broader filing machine is well advanced’
When it comes to developing and producing machines tailored to processing wooden floorboards, it is highly likely that you have heard of CSP Engineering, which is based in Dessel (Belgium). This company, the brainchild of general director Jan Peeters, was formed early in 1994 and supplies high-tech machines and computerised solutions for various phases in the production of wooden floors.
You can divide their machines into four main parts: glueing installations; packing lines, logistical systems, and filling machines (which we consider specifically in this article). We want to know how CSP Engineering approaches the market with its filling machines and during the course of the interview Mr Peeters also gives us some interesting news. For instance, the company seems to be well on the way towards developing an additional machine for the PAR Filler® Series which presently comprises three parts. They can announce officially that next year they are extending their working area outside Europe, with new clients in Canada and the USA.
To Canada and the USA
Jan Peeters: ‘Next year, we’re selling our first filling technology machines in Canada and, shortly afterwards, we expect some more deliveries for the USA. We’ll still be developing and producing everything in Belgium for the full 100%, but the overseas machines will supplement our present clients. Those clients are small, medium-sized, and large wooden floor producers, who are now starting out in Europe with two and three-layer parquet in 12 countries in Europe.’
Jan Peeters believes that the step beyond Europe is a logical consequence of the ongoing experience which the company has built up. He outlines how the company has developed in a few major blocks: ‘I had a special affinity with the wood industry and in the first phase we concentrated on developing and building tailored machines. After that, we moved on to constructing production lines, something which we did for several years for the parquet, pallet, and general timber industry; our expertise lies in constructing production lines for elongated items, so everything is computerised. Since 2009, we’ve concentrated for 100% on industrial parquet floor production.’
‘Until 2008, our working area was mainly between Paris and Amsterdam. In that same year, we did a, in-depth strategy exercise and realised how we could make a difference in the parquet industry. We established that there were lots of excellent new opportunities with no market solution and that we could launch our own production on the market. At the same time, we also saw an increase in our sales area. Firstly, we extended our working sphere in Europe and now we’re going a step further.’
Extension in filler machines
‘In filler machines the PAR Filler® Series comprises three models: PAR Filler® Mono, PAR Filler® Duo, and PAR Filler® Duplex. The Mono is fitted with one applicator and is suitable for small to medium-sized production, the Duo version is suitable for medium to large production capacities, and, finally, the Duplex is the most powerful one. The Duplex has two filling lines, which work independently of each other and can fill wooden floorboards of the same or different product qualities and colours.’
‘For the filling we have to go back a good ten years in time, when the wooden flooring industry underwent a transformation which is comparable, for instance, to what happened with ready-made laminates. Lots of smaller players sold semi-finished products which parquet floor fitters then finished on site. That changed as the finish and therefore also the filling work shifted more towards producers, certainly with a lot of medium-sized players. That’s where we fit in with our machines.’
‘The very latest news is that we’re now working to develop a new filling machine which will offer a solution for a specific market segment. We’re working on a broader filling machine, which can also work on panels and can fill with several heads. The machines now operate floorboard by floorboard, but soon it’ll be possible to fill multi-strips simultaneously on a panel, followed by the sawing and finishing. To express it in figures, so far we can cope with widths of up to 310mm. In the future, we’ll be able to manage panels from 960 to 1250mm wide.’
Obviously, we want to hear about the market launch. At this point, Jan Peeters is a little more reserved: ‘The only thing that I can say with certainty at the moment is that it’ll be soon (he laughs). I prefer not to commit myself to a set date, development always proceeds in steps, and that means you have to be careful with assessments.’
The new norm: remote work
Finally, we still want to hear how CSP Engineering has come through the corona pandemic. Their story shows how you can turn a drawback into a benefit.
‘We’ve already always committed ourselves to offering a great deal of remote professional help with maximum use of various forms of technology. We already offered access to machines via Internet, we had a keen eye for diagnostic tools, and for maintenance instructions. Our machines log huge amounts of data and that enables us to offer remote professional help, so it’s only in highly exceptional cases that we have to provide our services on site.’
‘This pandemic has demonstrated how we can prepare for the future even better via investing a lot of time in providing support. Our support consists of three sections: training machine operators, supervisors, and technicians. This means that we can solve a lot of problems remotely. An example for the filling technology: If a client wants to fill a new wood sort and does not achieve the desired result, we can assist 100% remotely.’
‘To talk specifically about covid 19: Initially, as was the case everywhere, there was a lot of uncertainty in our sector amongst clients and prospective clients. However, confidence was restored quickly and strongly from the summer of 2020. What was particularly noticeable was how quickly people learned to use and accept digital technology and we’ve taken full advantage of that. We’ve gone far beyond the normal round of digital meetings. We even give digital demonstrations on machines using products from clients who’ve sent us some of their products. Once a project is ready, we now have a digital factory acceptance.’
Filling technology for wood flooring
Machined filling of knots in parquet
PAR-Filler Duo
before after
High quality filling result Reduction of labour costs High production capacity Just 1 operator Wood filler ready for use Available in 8 colors
Photo – CSP Engineering
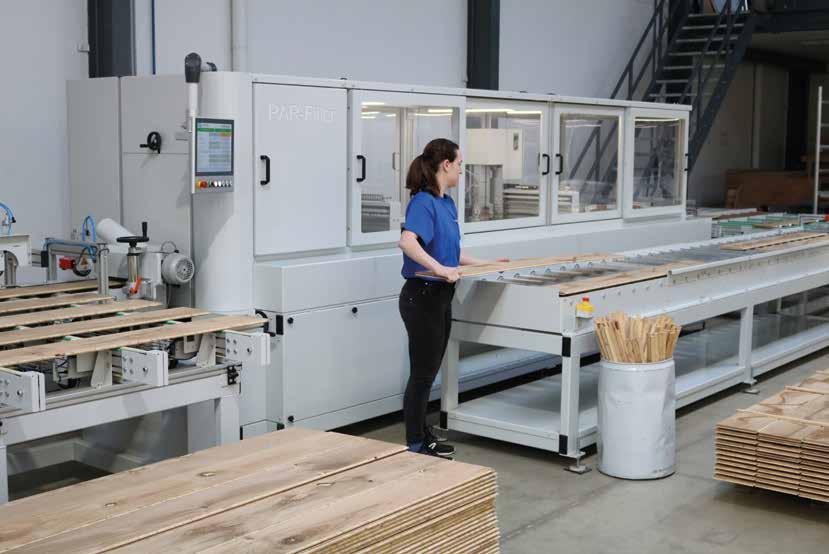
Wooden flooring experts often meet customers who do not want to see any gnarls or cracks in their parquet and therefore insist that all imperfections are removed. The ageold solution was to repair shortcomings by hand using wood filler paste, and sometimes that meant working on hands and knees. The market, too, has noticed this tendency, and that’s why filling machines have emerged.
You can guess what this is about. As early as the production, traders use automatic systems to trace and eliminate blemishes in parquet planks. These systems use sensors and cameras, and then the filling machine on the production line infallibly fills in any unevenness with a special wood paste.
Higher production capacity and better welfare
The machines have all sorts of benefits and obviously the main one is the much higher production capacity which is generated. At the same time, these machines also benefit the operators’ health and welfare because they eliminate physical strain. Those same operators now have a directive and controlling function in the production cycle. What’s also noticeable during the production process is that machine manufacturers are striving to produce machines which need just one human operator, even for high capacity and production volumes and for more than one filling line. As is the case everywhere, all filling machines are different and they come in different sizes and weights. It is noticeable that they are often deployed in total production lines which transform the bare wood into labelled and finished parquet which is ready to be fitted.
What happens is that these machines carry out the necessary preparation for the application of a finish (an oil or a lacquer). And so, they detect and repair not only major blemishes, but also minor ones too to ensure that the required end product is up to standard. And so, floorboards are scanned (sometimes in 3D) and the resulting images are processed in no time at all. The advantage of such a scanner is that it detects and assesses any blemishes whatsoever with the utmost precision and thereby outperforms both machines and human beings.
The planks stay on the belt
This brings us (almost automatically!) to another major asset. Since the machines are integrated into a production process, there’s no need to remove ‘damaged’ planks from the belt to repair them. Indeed, the scanner calculates the extent of the damage and determines the amount of filler with absolute precision. When the filler is then applied under pressure by injection, that brings out other assets as compared to manual filling. The amount of filler needed is calculated so precisely that there is little surplus, if any, and this reduces considerably the number of floorboards to be reworked.
The ideal filler
Finally, we need to say something about the filler which is used. Obviously, this has to meet specific requirements because it has to blend in seamlessly with the plank on which it is used. The ideal filler is one which hardly shrinks, if at all, adheres perfectly, is as porous as wood, dries quickly, and is available in several standard colours. In 2021, it goes without saying that this filler also has to meet the necessary environmental standards. And so, ideally, a good wood filler also contains neither water nor solvents, even with mechanical application. Is everything made in line with top professional standards? You should realise that the best fillers which are ready for use hardly shrink, absorb colours nicely, can easily be planed and sandpapered, and do not disintegrate.
CSP Engineering
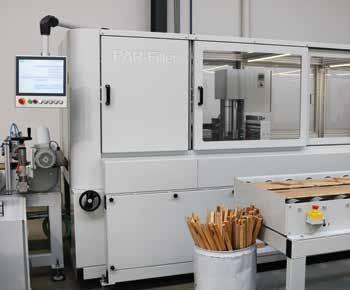
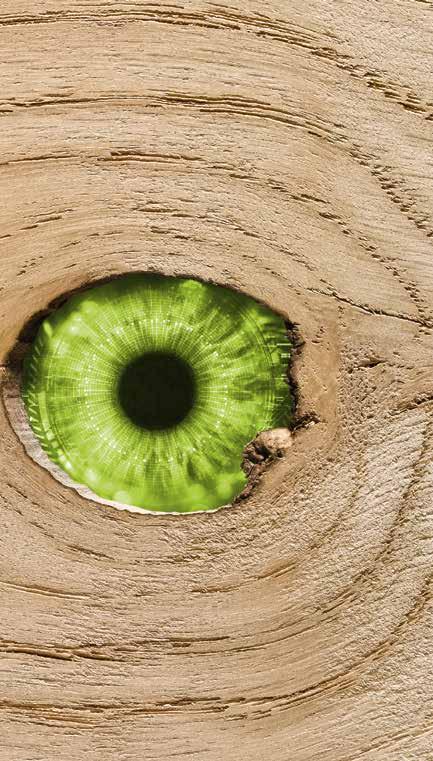
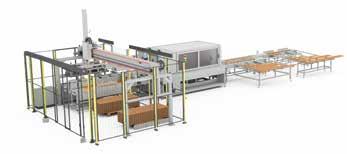
CSP Engineering developed PAR-Filler®, a unique filling machine, specifically built for the parquet industry. This filling machine optimizes your production process in many areas. The PAR-Filler® Series currently consists of three models. PAR-Filler Mono, equipped with 1 applicator, is well suited for small to medium-sized productions. PAR-Filler Duo, with its 2 applicators in line, is very suitable for medium production capacities. PAR-Filler Duplex, the most powerful of the 3, has two filling lines, which work independently of each other and can fill wooden floorboards of the same or different product qualities and/or colors. A single operator can control and monitor the PAR-Filler® and receives targeted training and all necessary tools from CSP. Cosmetiwood® is a wood filler developed for the PAR-Filler® machines. Cosmetiwood ® has fantastic properties, is available in 8 standard colors and is ready to use. Color can be changed quickly in the machine and the loss of filler is minimal.
Focused on damage & surface treatment!
TRC WOOD COSMETICS The TRC concept stands for „wood cosmetics“ in unprecedented quality, with enormous potential for economization. Pre-cleaning, repair, and design of wooden surfaces can be fully automated with the TRC Preclean, TRC 1500, and TRC Manufactory trio of solutions. Whether semi-automatic or fully automatic, WINTERSTEIGER has in terms of „defects & repair timber cosmetics“ the appropriate solution!
For more information: www.wintersteiger.com/trcWINTERSTEIGER AG A-4910 Ried, Dimmelstraße 9 Tel.: +43 7752 919-0, woodtech@wintersteiger.at