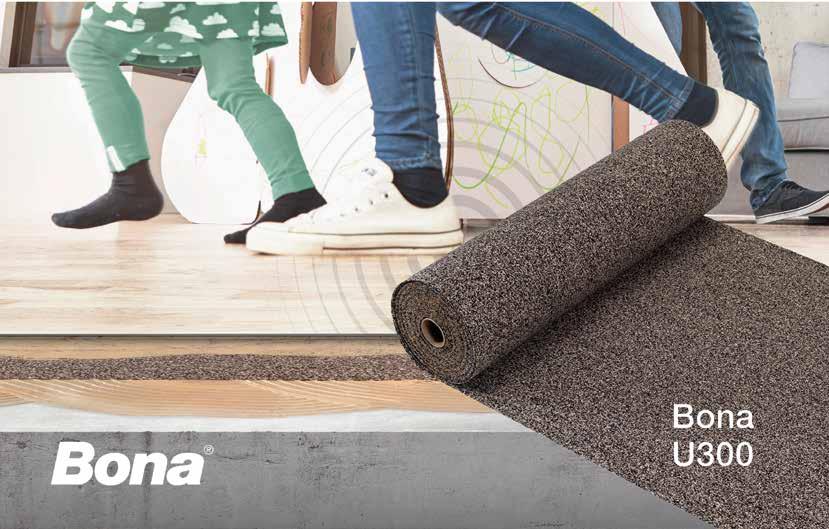
4 minute read
Special Subfloors : part III
THE SECRET OF THE SCREED
BASIC CONDITIONS FOR A GOOD CEMENT-BOUND SUBFLOOR
Advertisement
It’s a truism to say that an attractive floor starts with the quality of the subfloor. A popular underlay is the traditional screed, also called a covering floor, subfloor, or wear floor. We’re talking here in particular about the layer fitted between the bearing floor and, in our case, laminate or parquet.
What does a good screed consist of? The traditional cement-bound screed is the first thing which springs to mind. This consists of a mixture of sand, cement, and water which you use to achieve a perfectly level surface. You find a traditional screed in three variants: - The adhesive covering floor: This comes directly onto the concrete bearing floor and is the best option if the substrate is not porous and if there is no risk of cracks and rising damp. - The non-adhesive covering floor: This is fitted on a PVC foil or water defence partition. - The floating covering floor: This is fitted onto floor insulation with a thermal or acoustic function.
Calculating the drying time
It’s important to realise that a traditional screed needs quite a long time to dry. The drying time depends on the thickness of the screed layer, the air humidity, and the temperature.
To be precise, you can say that on average you should wait one week per centimetre, up to a thickness of 5cm, but that varies. If your screed exceeds 5cm, the drying will take about two weeks per centimetre. Logic is respected here, whereby the following principle holds: The
thicker the screed, the slower the drying (for instance, if your screed is 8cm thick, you have to wait 12 weeks). Professionals are opting increasingly for fast-drying screeds to speed up the drying. In this case they add a drying accelerator to the traditional mixture.
Furthermore, don’t forget to check the residual moisture content. This must not exceed 2.5% for a screed with no floor heating. If there is floor heating, this maximum figure is 2%. Always use your carbide measure, as measuring means knowing.
In all this, it’s absolutely essential to ensure good ventilation at all times for effective drying. And so, if necessary, open all the windows, even in the winter. After all, you don’t want to have problems from damp and, therefore, mould. Avoid the use of a hot air blower! It’s not until after about one month that you may start to provide some heat, but always make sure that there is some wind.
Check the substrate and comfort
Once you’re ready with the fitting, keep a special eye on the purity of the substrate. If there is a floating covering floor, fit a PVC foil under and above the floor insulation, unless the client has opted for floor insulation in sprayed PUR. In addition, fit sufficient thick edge strips, something which will be particularly important if floor heating is fitted later. Fit a reinforcement mesh if the screed is fitted floating, if you use a floating or soft insulation, or if the choice is for a thin layer of screed. And whatever you do, avoiding problems means preventing problems. If you want a perfect screed, you have to provide the necessary expansion joints. It’s also good to know that floorboards may have a maximum surface of about 40m² and a maximum length of eight metres. For the acoustic comfort make sure that the screed does not come into contact anywhere with the building structure. An acoustic mat can provide a solution in that regard because it eliminates disruptive impact sounds.
Two specialists
BONA
BONA U300 – Sound insulation subfloor
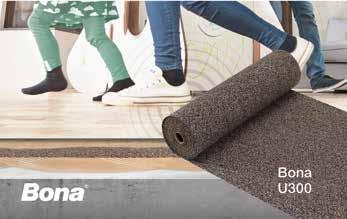
A subfloor made of bound cork and rubber granules. To be used as a subfloor for parquet, laminate, and other flooring. The material has a sound insulation effect. ∫ Easy to fit ∫ much more comfort all round ∫ low flammability ∫ low VOC base content: fine PU foam and cork granules from recycled rubber, polyurethane binding agent; Colour: brown (cork), black/grey/beige/brown (PU foam). EMI CODE: EC1 Plus Density: about 550kg/m3 Tensile strength: about 0.8N/mm2 Elongation before rupture: about 30% Thickness: 2, 3, and 5mm (± 0.3mm) Temperature range: -30 to 80°C Heat transfer coefficient: 0.04m²K/W for 3mm Resistance Flammability: Efl (EN 13501) Suitable bases: (also with floor heating, if required) ∫ heated or unheated covering floors ∫ covering floor elements, chipboard, or multiplex ∫ concrete ∫ mastic asphalt ∫ other professionally prepared bases. BONA U310 Bona U310 is a product to be glued. It is a felt which reduces tension in wooden and laminate floors. It solves problems in case of technically doubtful bases. Thanks to its great tear strength, the felt reduces tensions from the base so that the top layer is not affected. It is easy to cut and fit, porous, actively breathable, only 1mm thick.
Design Parquet
You choice your underlayers according to the use. There are 3 objectives : to sound insulation, to reduce the resonance noise or to create a barrier against moisture backing. Design Parquet offers different underlayers according to your needs. The most popular Design Parquet underlayers for their convenience are : - L’iso dB, patented system, is a ecological system (without CO2 emanation), providing both fixing the parquet floor with sound insulation (18dB). This underlays allows fast implementation thanks to 2 adhesives faces. Glue isn’t necessary. - L’iso alu, meanwhile, is a waterproofing underlayer, a real barrier against moisture. We warranty until 10% of humidity in the support.
It’s easy to install with the adhesive face. The wood floor is glued on this underlayer with NAVYCOL PS glue.
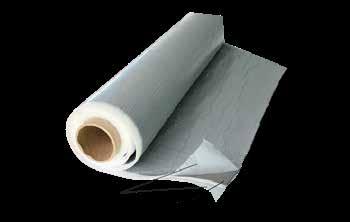
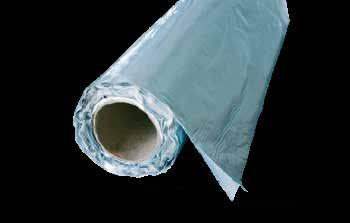