
9 minute read
Special The new sanding method with various discs, heads brushes, and nets
SANDING IS HARDER THAN IT LOOKS
IF YOU DON’T FOLLOW THE RIGHT STEPS, YOU’RE JUST ASKING FOR TROUBLE
Advertisement
Michaël Devriendt (Bona - B)
‘The aim is still to help parquet floor fitters work as ergonomically as possible.’
What do new abrasives mean for parquet floor fitters? We called on Bona Belgium, where Michaël Devriendt is well qualified to give us some idea. Not only has he worked for 18 years as a parquet floor fitter, but also in the last three years he’s been working as a travelling sales representative for Bona Belgium with responsibility for the whole of Flanders.
First of all, we want to know which products Bona sells as new abrasives. ‘Our range of abrasives specifically for the parquet sector is highly varied. It goes from classic silicon carbide 8100 and aluminium oxide 8500 over the better zirconium 8300 and the modern ceramic mix (8600 and 8700) to the ultimate Diamond Abrasive System,’ says Michaël Devriendt. ‘Our abrasives are available in endless belts, discs, and even material in mesh form, and in all sorts of measurements and /or widths.’
What are the main developments which Bona will have for the sector within the foreseeable future? ‘In all honesty, this is a matter of conjecture. Our sector has progressed quite fast in recent years after a period of standstill and further progress actually depends mainly on what floor fitters want. In all cases, Bona is pressing on, and certainly in developing machines which are designed mainly to help users work as ergonomically and efficiently as possible.’
Efficient alternatives
One of the key questions is why we have to abandon the classic abrasives at all. How do you see new abrasives at Bona? ‘Our classic abrasives, types 8100 and 8500, are still good, but Bona can now offer better and more efficient alternatives. I’m thinking here of the 8300 series, for instance, and the newer 8600 and 8700 series. These types of abrasives each have a longer lifespan and work more aggressively. The purchase price may be somewhat more expensive, but in this case a higher price is far from being a negative factor. It is precisely due to the longer lifespan that these new abrasives are cheaper to use than the classic types.’
On which machines can these abrasives be used? Are there any restrictions? Our interviewee laughs: ‘Qualitatively correct abrasives require qualitatively correct sanding machines. In the past, you always started sanding parquet with a belt sander, then you switched to an edge sander, and you ended with the buffer. That’s still the same in many cases, certainly when it comes to bigger rooms. An interesting development is that we’re living in increasingly smaller homes and that rooms have thereby become more compact. In those cases rotary sanding wins the day from classic sanding with the belt sander. Rotary sanding is just quicker in combination with the right abrasives.’
‘The time saving lies mainly in the fact that you have fewer machines to transport. This means that you spend a lot less time and effort on the edge sanding, precisely because you can sand closer to the edge. My advice: Do you have a room of 400m² with a floor with an old coat of varnish which has to be completely removed? If so, use the belt sander first and then switch to the Bona Flexi Sand, and that will save you lots of time. By contrast, if you are talking about a room of 70m² which has to be sanded to remove a top layer, you only have to take the Bona Flexi Sand with you to the site. This powerful, versatile, and rotary machine makes sanding seem a “little job”, certainly in combination with the right choice of abrasives.’
Third Bona DCS is on the way
Finally, we ask about the dust extraction: ‘All Bona sanding machines are compatible with our two types of dust extraction: the Bona DCS25 in combination with the Bona Flexi Sand and the edge sanders or the Bona DCS70 in combination with a belt sander like the Bona Belt. With both types you can sand virtually without any dust.’
‘The Bona DCS70 goes even further. This vacuum cleaner operates with seamless dust bags of 20 metres, the Bona Longopac. And so, there are 20 metres of dust bag ready for use in the vacuum cleaner. And so, the sum of 20 metres x 70 litres of content means that you can suck up 1,400 litres of dust without coming into contact with the sanding dust. For that matter, hot off the press, I can share this: This year, we’re unveiling a third Bona DCS version!’
This is a translation of an interview conducted originally in Dutch.
In the testimony with this article Bona tells us how they deploy new abrasives and we present in detail what it has on offer. What’s worth considering again is how to approach the various sanding jobs and how you can avoid a lot of common sanding mistakes. For that purpose we spoke to Lecol The Netherlands.
Sanding is a part of the parquet trade which is harder than it looks, certainly with the use of coloured finish layers where pigments from used colours reveal deeper abrasions. And so, that’s why we asked how you can best tackle this job. We list the various steps, illustrated by Lägler sanding machines.
Coarse sanding
Coarse sanding is usually the first step. Its purpose is clear, namely to remove old finish coats, grind the floor flat, and remove deep scratches from the floor. After this coarse sanding, you certainly can’t yet apply a finish and the scratches which have arisen need to be removed. To do this, it’s best to grind with a medium coarse grain for the removal of deep scratches. After this step, the wood still isn’t fine enough for a finish layer. That’s why the floor usually still has to be fine-sanded. As a last step, the floor is often polished to yield a smooth and even end result.
The item used by this company for the grinding of the entire floor is a big belt sander with sanding belts of 200 x 750mm in size (often with the Lägler Hummel). An edge sander is then used for the edges. For the bigger edge sander you have the Lägler Unico with discs with a diameter of 178mm and for the lighter models the Lägler Flip, with discs of 150mm. An eccentric hand sander with a diameter of 150mm is often used to polish the edges.
A 16” buffing machine is often used to polish a whole floor. This machine is suitable for sanding discs or abrasive nets with a diameter of 406mm. A high-quality polishing machine is the stationary Lägler Trio. This sanding machine has three discs with a diameter of 200mm and yields a scratch-free result.
Sanding machines need abrasives and the abrasives of the Swiss trademark Sia are commonly used. Several qualities of abrasives and various grains from very rough (grain P16) to very fine (grain P240) inclusive can be deployed for both the belts and the discs. Various abrasive grains are also on offer, such as aluminium oxide grains, zirconium grains, and ceramic grains. Common sanding mistakes
Lecol provides training in scratch-free sanding for experienced workers and it is noticeable how the same sanding mistakes tend to occur regularly. We list a number of them here: - Sanding scratches which stand out mainly on a coloured finish such as coloured impregnation oil are a regular cause of complaints. And so, it’s good to be well informed in advance. - Beginners often make the mistake of lowering the cylinder of the belt sander to the floor quickly and abruptly. This causes a deep indentation of 20cm wide in the wooden floor and something like that isn’t always easy to rectify. - No more than one grain should be bypassed in the sequence of abrasives to be used. If you fail to respect to this rule, it might not be possible to rectify deeper scratches which have arisen from the sanding with a previous grain. - Always remember to vacuum clean between the various sanding sessions. Otherwise, scattered sanding grains from a previous and rougher sanding session could be left lying on the floor and be absorbed by finer abrasives. This can cause deep abrasive scratches. - You must keep sanding machines well tuned, cleaned, and maintained for a good end result. And so, be sure to check the tuning of the machine and, if necessary, have it examined by a specialist technician.
Source: Lecol.nl: Sanding parquet.
Bona
Bona Flexi Sand 1.9, the powerful, multifunctional machine for all floor operations, from sanding down to the bare wood and polishing oil to grinding concrete. The Bona Flexi Sand 1.9 can be fitted with various drive plates for various tasks such as sanding down to the bare wood, fine sanding, applying oil and polishing it, and grinding concrete. Thanks to its powerful 1.9kW motor and its sturdy construction, the Flexi Sand is always easy to operate. The system is compatible with the unique Bona Power Drive (CONNECT), a drive disc which enables you to sand powerfully and in any direction down to the bare wood. Connection to Bona DCS is possible for maximum dust reduction. The machine can be deployed for various tasks such as applying oil or cleaning floors. However, sanding is the primary function: ∫ With the Bona Power Drive (CONNECT) + Coarse sanding: Bona 8700 / Medium sanding: Bona 8300 abrasive. ∫ Fine sanding: Bona Diamond Abrasives material ∫ Medium sanding + parquet joint kit; removing: Bona Net discs.
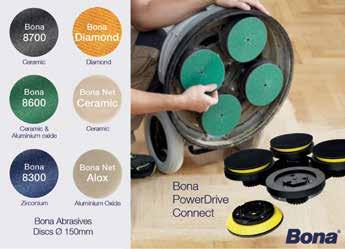
But also for brushing wooden floors: To obtain a nicely brushed structure floor. With the Bona Power Drive CONNECT: 1 disc for sanding and brushing. Simple click system for a simple change (within one minute) between the traditional sanding discs and specially developed brushes. Moreover, also concrete grinding, for a smooth base. Accompanying segments: Bona PCD Maxi Segment for removing thick adhesive residue, epoxy, and carpet foam / PCD Split Segment for removing polyurethane, thin adhesive residue and paint / Diamond Segment for removing sinter layers or processing concrete surfaces. Other types of floor surfaces: The Bona Flexi Sand can be fitted with the Bona Diamond Blades for stripping elastic floors. Pallmann
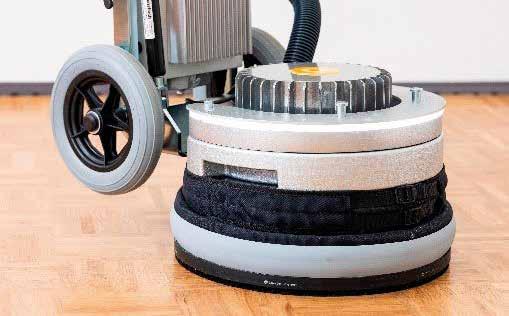
Sanding, polishing, basic cleaning or brushing - the rotary sanding machine Pallmann Spider is very versatile and user-friendly. The tripledisc-plate is suitable for coarse, fine and intermediate sanding of wood floors. Thanks to the drive plate with coupling, the low machine weight and infinite speed adjustment the Pallmann Spider can be used for a variety of jobs, e.g. deep cleaning, daily cleaning and application of oils and polishes. The Spider dusk skirt enables almost dust-free working and comes in a dust repellent material. The LED light ring guarantees a 360° illumination for easy work. With the Pallmann brush technology and the dedicated brush set for the Pallmann Spider the unique structure and the special character of a real wood floor can be created. The softer annual growth can be brushed out, while the hard wood is preserved.
Professional Flooring Technology
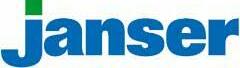
Floor Scrapers in suitable weight classes!
German Quality
Ride-on ADB HS 1180 kg Ride-on ADB 950 kg Ride-on Electro 565 kg
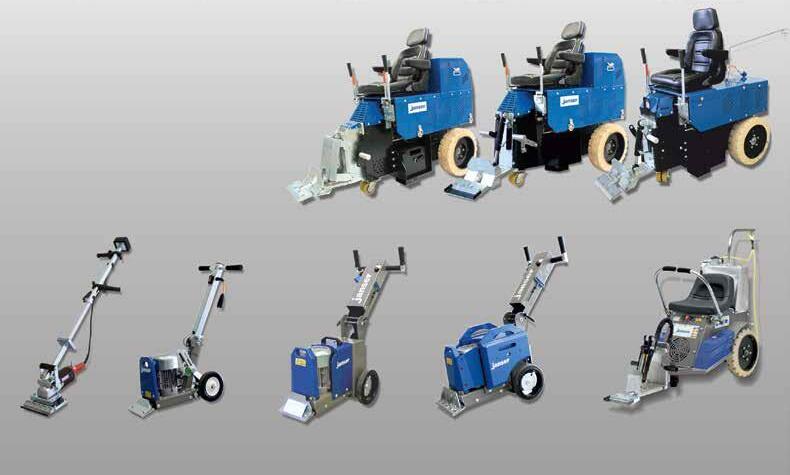
Power-Stripper 14 kg COSMO IV 39 kg MASTER MOBIL III 105 kg STRATO MOBIL IV 190 kg JUNIOR Ride-on 420 kg
