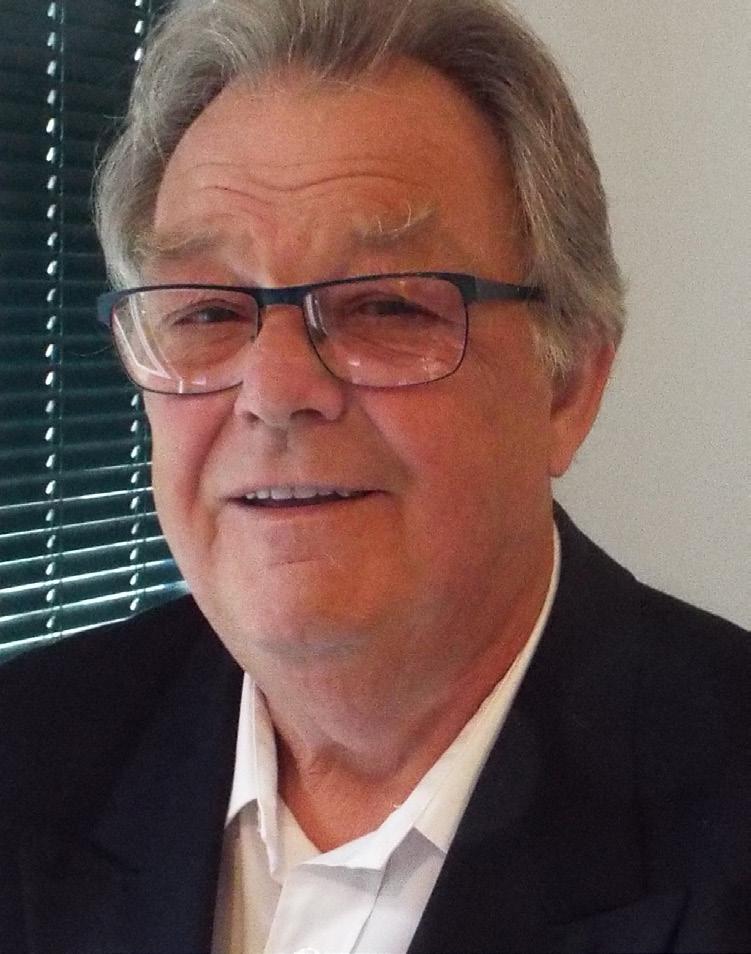
7 minute read
Degassing: futureproofing, or eliminating installation problems?
Dave Cannon, Technical Manager, UK, for Reflex Winkelmann, points out some of the issues that can be solved by degassing in a pumping system, and offers some advice for selecting a suitable solution.
Many within our industry would think of the installation of degassers, in both atmospheric and vacuum formats, as being methods by which issues such as air locking were cleared. Other than that, they are seen as a long-term solution to corrosion issues. We have all probably seen these problems encountered by both installers and manufacturers, but over the years we’ve gained an understanding of those issues, and the solution. With experience, our views on these issues have probably changed significantly.
Advertisement
Some years ago, when most pumps had a fixed speed drive, it was my experience that service engineers would often be called to sites to be told ‘your pumps are down on duty’. This caused delays in practical completion, as systems could not be signed off. After a while, a pattern tended to emerge. Generally, the flow was down to 80-90% of duty, and it was often on chilled water circuits. In each case, it would be found that the pumped medium was highly micro-bubbled, compromising the hydraulic performance. Had a vacuum degasser been installed, the system would have been clear of any air/gas and the pumps’ performance would have followed the published performance curve. In each case, the project experienced unnecessary and often costly delays.
These days, variable speed drives are the norm, but under fixed speed conditions, where a pump selection would have been made with an envisaged operating frequency of 40Hz, it was found that the pumps needed to run at nearer 50Hz to achieve the required duty. It’s worth remembering that because the hydraulic properties of the pumped medium are compromised, the efficiency of devices across the system will be severely reduced. By simply restoring the hydraulic properties to the correct values, the energy savings across the entire system can be considerable.
Let’s look at a real-life example at Heathrow Terminal 2. It’s a chilled water system, with a content of some 1.3 million litres. I had spent some considerable time on site, wiring and setting up a dual Reflex Giga system and had always attributed the shaking of the building’s structure to sympathetic vibration, generated by the jets outside. Although ten years ago, I can still remember on a Monday morning, the commissioning manager asking how long it would be before the equipment would be operational, and how long it would take to degas the pumped medium atmospherically. He went on to explain, they were unable to balance the system hydraulically, and it was proving impossible to achieve repeatable readings across the metering stations. I gave an estimate of about seven days, before I went off to complete the commissioning, and set the units up to operate in a continuous degassing mode. It was only four days later when I returned to site that the commissioning manager was delighted to tell me that the system readings were now stable; however, that was not what impressed me the most about this installation. With the now smooth, laminar flow through the pump volutes and impellers, the structure of the building was no longer shaking, and the plant rooms were now relatively quiet. The vibration had been due to the 200kW pumps shuddering as small pockets of air entered the impeller vanes.
The mechanical stresses on the pump shaft bearings must have been considerable. It is theseconditions under which you will see spreading “The energy savings of the impeller keyways, rolling of the key steels across the entire system and in extreme cases, can be considerable.” failure of the impeller hubs. At that time, it also occurred to me that the amount of energy being dissipated must be huge to shake a structure of that size.
Both from the manufacturers and installers points of view, one of the biggest issues is the repeated failure of mechanical seals on some of the larger pumps. Not only can this ruin the finish on an otherwise pristine plant room floor, but the installer will also ask if substandard seals are being used. An engineer will attend site, remove the mechanical seal, see that the rotating assembly is covered in deposits of material, the rotating and stationary seats are scored and conclude that the system has not been fully cleaned.
Not only does this cause delay to a project, understandably it leads to disputes between all parties, including the water treatment engineers. They will produce samples of system content that are usually described as ‘bright and of a light straw colour’. The water engineers are right, but they are relying on a sample that may have been out of the system for many hours, possibly even days. You need to be looking at a sample of water drawn off from the discharge side of a running pump. Initially, it can look almost as white as milk, but it will slowly clear from the bottom to become the liquid described by the water treatment engineers.
You must realise that the condition of the pumped medium when decanted is the same as seen by the pump impeller and mechanical seal. A good indication of the presence of entrained gases is the rapid oscillation of the pump discharge pressure gauge needle.
A mechanical seal, by design, must leak but in a very controlled manner. When the pump is stationary, the rotating and fixed faces of the seal are pushed together with a combination of spring and hydraulic pressure. When the pump is running a film of water, only microns thick, holds the faces apart. However, if the pumped medium is highly micro-bubbled, the hydraulic properties of the lubricating film are compromised and the two seal faces will touch. This can be witnessed in quiet plant rooms, by a ‘chippering’ noise coming from the pumps. That is the noise of the seal faces, ‘kissing’ each other.
As the seal faces touch, friction can elevate the temperature at the seal faces to over 200ºC at the point of contact, even on a chilled water circuit. It follows that the water content flashes off to steam. What it leaves behind are the solids in suspension. In some cases this will be sodium nitrates and other materials from the water treatment, although we have seen an instance where the material was residue from glycol in a cooling system. Over a relatively short period the materials form an abrasive slurry which can damage the seal faces, creating a leakage path. When an engineer changes the seal, based on his observation that the seal components are contaminated, he may conclude that the pumped medium is not clean.

Glandless or canned rotor pumps use a film to lubricate the motor shaft’s carbon or ceramic bearings. If the hydraulic properties of the pumped medium are compromised, deposits of the former solids in suspension are left on both the shaft and the bearing bores. This is not an issue when the pumps are running, but when they are stopped, ‘heat soak’ causes the material to form a bond between the two components. When the pump is restarted the motor cannot produce enough break-out torque and this can result in a ‘locked rotor’ burn out.
There is another problem that took some lateral thinking to establish the cause. A pump that had run without issue for a month was stopped, and its counterpart put online. Some twenty-four hours after stopping system water pressurised to 3.0 bar started to gush out from the mechanical seal housing. Some twenty seconds later it stopped. The pump was on a system with known micro-bubble issues and there had been a formation of slurry in between the faces, but it was not enough to prevent closure. In the warm plant room the sodium content of the slurry had dried and started to crystallise. This action lifted the seal faces apart causing a significant leakage path.The resultant flush of water across the seal faces then washed away the crystals, and the seal closed.
It would seem fair to estimate that 90% of circulating pumps that have the issues addressed relate to micro-bubbled systems. In all cases the introduction of a vacuum degasser proved to offer a satisfactory solution. However, I would advocate caution when selecting the right unit to address these issues. Most of these units are produced outside of the UK where the water treatment regimens are very different from the ones utilised here in the UK. To that end, solenoid valves are used for the regulation of flow. These devices are extremely susceptible to any solids in suspension and will often be seen discarded in plant rooms. It makes sense to try to select units that do not employ a combination of solenoid and pressure reducing valves. Units that use selfcleaning motorised valves, with automatic hydraulic optimisation, are a far more viable option. chevron-
www.reflex.de/en