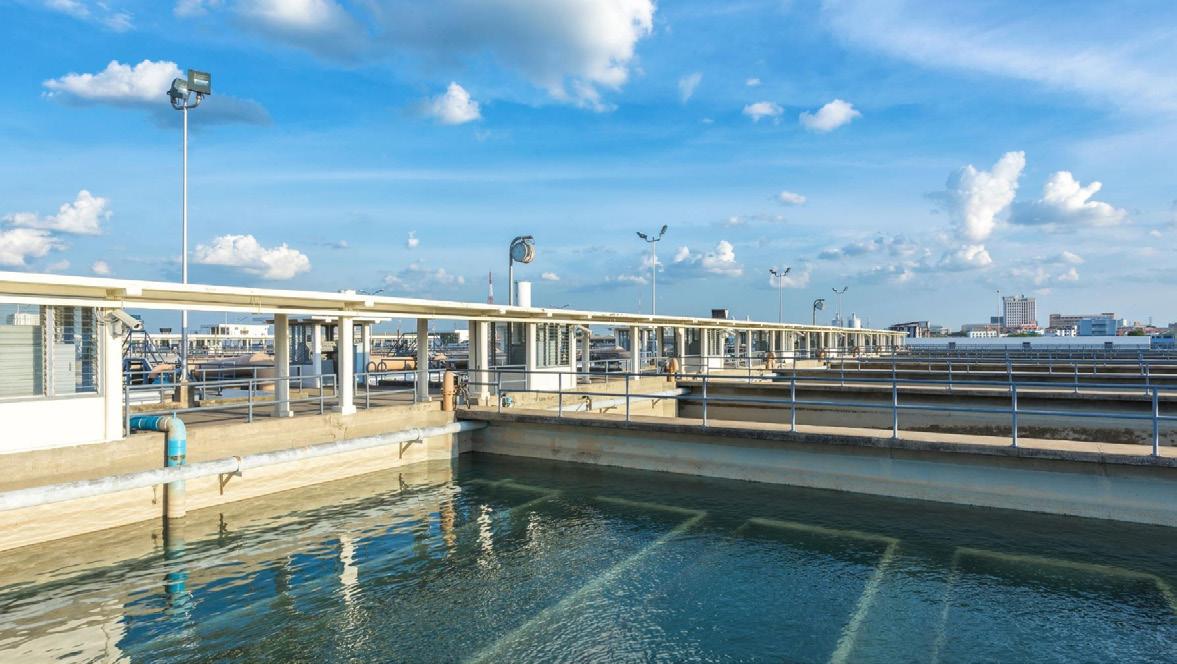
3 minute read
Managing changes in water demand
Marek Lukaszczyk, European and Middle East Marketing Manager at motor and drive manufacturer, WEG, explores three equipment upgrades that water companies can make to increase their agility and efficiency.
In July 2020, the Met Office reported that most UK water companies had seen an increase in average water consumption during lockdown, especially those operating in suburban areas.
Advertisement
This sudden surge sits alongside a six-fold increase in global water usage over the past 100 years, as reported by the United Nations World Water Development Report 2020. Climate change is undoubtedly a longstanding consideration for water management, but low rainfall, high population density and intensive agricultural or industrial activity may also result in sustainability issues – without throwing a global pandemic into the mix.
Faced with these challenges and ageing infrastructure, the European water industry is focussing on rejuvenating its existing assets, building resilient systems, and improving operational and energy efficiency. So, where should a water company start in implementing system upgrades?
THE TOTEX BASED APPROACH
Firstly, it’s important to build an effective strategy. The totex (total expenditure) approach continues to reshape the water industry. This framework considers total cost throughout the lifecycle of a project, allowing water companies to be assessed against long-term outcome measures. In addition to cutting costs, the framework looks to provide better value to consumers, and to achieve better efficiency management and operational efficiency. Predictability is therefore high on the optimisation agenda, through close integration and collaboration with manufacturers at the design stage.
CUTTING DOWN WASTAGE
Waste, in the form of unnecessary energy usage or pipe leaks, can be a real problem, affecting a water company’s maximum output. According to the International Energy Agency, a quarter of the electricity consumed by the water sector is for wastewater collection and treatment. For this reason, companies operating in this space must consider investing in energy-efficient technologies. Reducing energy wastage not only offers environmental and cost-saving benefits, but also allows businesses to commit more resources to meet changing demands.
Opting for an energy-efficient motor that conforms to IE4 and IE5 standards is a good place to start, but it is also important to ensure the motor is matched to the load. For example, at a water pump station in Surrey, WEG supplied three 900kW W50 IE4 super premium efficiency motors with IP55 protection, operating at 96.9% efficiency. With new pump impellers, gearboxes, drives and the WEG motors, the facility was upgraded from its existing 400 megalitres per day capacity to 750 megalitres per day, with an efficiency increase from 80 to 86%.
CONDITION MONITORING
To ensure that motors are running optimally, water plant managers can retrofit sensors. By using smart technology such as Industrial Internet of Things (IIoT) data, watercompanies can monitor their assets and processes in real-time, allowing them to ensure that their systems are performing optimally and to respond quickly to unexpected events.
Key metrics such as vibration and temperature changes can be early indicators of more serious system faults. This predictive maintenance approach reduces the risk of downtime and consumer disruption.
USING A VARIABLE SPEED DRIVE
Pumps consume a large proportion of the energy usage of electric motors. Upgrading to a variable speed drive (VSD) instead of using a fixed speed motor allows companies to account for varying process load. A VSD can automatically control the speed of the motor and rapidly respond to the required demand. This also allows for more efficient operation, instead of continually operating at a water flow designed for the maximum demand of the system.
Going one step further, companies can invest in sophisticated process control software, such as WEG’s Pump Genius. This built-in VSD software enables engineers to increase their process accuracy and protection while offering system monitoring. The software allows one VSD to control up to five pumps, monitoring the operating hours and adding and subtracting pumps as demand changes. Automatic broken pipe detection in the VSD can also identify fluid leakage and adjusts motor performance accordingly.
By implementing the totex framework, intelligent design decision making can be achieved, which will give water companies of all types, added flexibility, better performance and superior cost savings. chevron-
www.weg.net