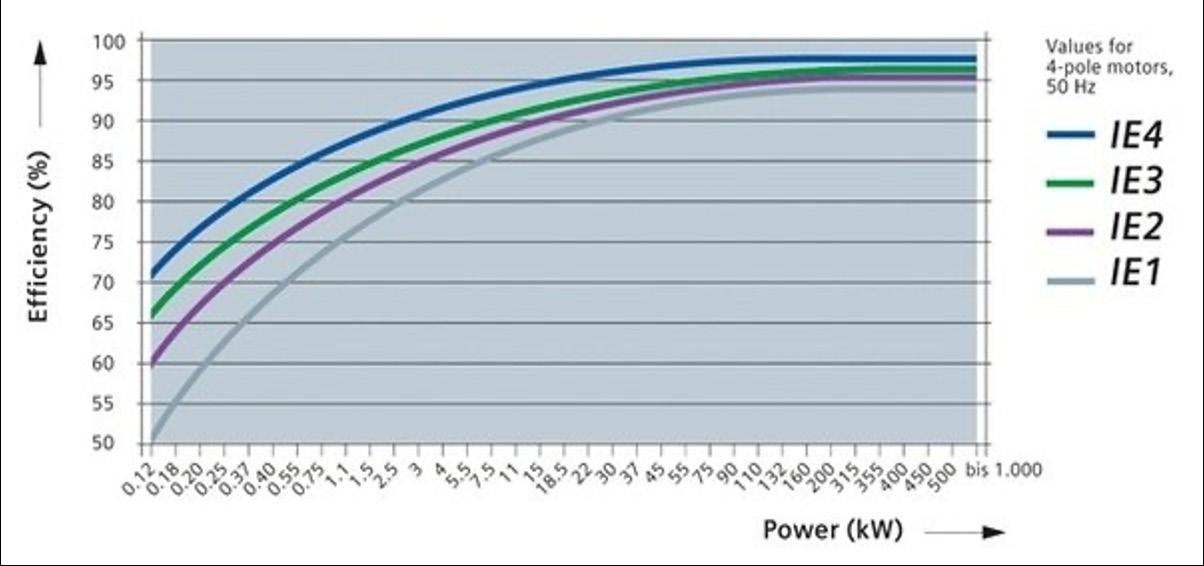
7 minute read
Complance
Take time to understand the repair standard
The thought of reading through lengthy standards documentation strikes fear into many! But Karl Metcalfe believes there are several ways that users of electric motors can benefit from having an understanding of the BS EN IEC 60034-23 repair standard.
Advertisement
The repair standard, BS EN IEC 60034-23, establishes the benchmark for repairing rotating equipment; maintaining efficiency levels, high standards of quality control and improving efficiency in associated pieces of equipment. Before the standard existed, eco-design – in terms of rotating equipment – had mainly focused on energy efficiency. Now, with reference to the circular economy, attention has turned to reducing material consumption as well.
Customers who understand the core principles of the standard are better equipped to choose the correct repairer for their needs. AEMT repair members cover a vast range of repairs and services and could work with equipment from national power stations through to local farms. There will be users that have no interest in this standard, and they will be happy to use anyone to repair their motor, but as awareness of the standard grows, and the focus on motor efficiency widens, an end-user familiar with the standard can ask a repairer more indepth questions around what they can offer.
There are four key aspects of the standard that motor users should be particularly aware of. They are the circular economy, efficiency, root cause analysis and reporting.
THE CIRCULAR ECONOMY
The circular economy and the environment are both written into the standard, promoting environmental good practise and responsible recycling. The circular economy reflects what the repair industry has been doing for over 100 years; repair reuse and recycle. Unfortunately, in recent years the proportion of motors being repaired has significantly reduced due to repair costs going up and the increased availability of lower-priced motors.
Every project has a cut-off point when replacement becomes more appropriate than repair. However, making that decision purely on cost may miss other important benefits.
The standard states that: “The repair or refurbishment of energy-efficient machines ensures the most efficient use of the world’s dwindling resources. When repairing or maintaining a typical 110kW machine with new bearings, the effective life is doubled, and 99% of the original machine is maintained. Plus, the old bearings, making up 1% of the machine, are recycled as highquality green steel scrap. If the machine is rewound, 90.5% of the machine is reused during refurbishment. The same weight of materials used during a rewind is returned as high-quality green copper and steel scrap. The only items not reused or recycled during a repair are the varnish, insulation, paint and grease, representing just 0.9% by weight of the materials present in a typical 110kW machine.”
On this basis, when a repair is a close price match to a replacement, maybe the cost of the environment should be considered too. The circular economy is gaining pace in popularity, the younger generation is making these topics a top priority when choosing employment, and within a few years, those individuals could be deciding which repairer to use.

Figure1: Efficiency by power rating across four motor classes.
EFFICIENCY
As you would expect, the standard promotes the provision of the best efficiency option when repairing a motor, including deciding between whether to repair or replace.
As you can see from Figure 1, across the four classes, there is little difference in efficiency on high-end kW motors. Typically, from 110kW upwards, except for IE1, motors are over 95% efficient. But take a look at midrange motors, around 3kW to 30kW, and the potential for improvements in those motors is clear to see.
A survey conducted by ABB found that in 2016 20% of motors in use were IE1, 40% were IE2, 30% were IE3, and only 1% were IE4. So, the potential savings for the user could be considerable if replacing IE1 motors with IE3 or IE4 equivalents.
On the other hand, if a customer has an IE3 or IE4 motor and a repair is required, by following best practice and the criteria of the repair standard, the efficiency class of the motor can normally be retained even when a rewind is required. This is borne out by a study originally conducted by the AMT and EASA in 2003 and revisited in 2019, which showed that rewinding a motor does not necessarily mean a loss in efficiency.
The standard’s reference to maintaining efficiency includes checks and tests which need to be carried out, plus aspects such as controlling the heat used to remove windings, which should not exceed 370°C to protect the interlaminar insulation and the efficiency of the core.
It also references copy winding techniques, keeping the winding overhang the same or less and the mean length turn as close to original as possible. While correct grease methods are also covered to make sure their repairer uses the same type of grease the customer uses as part of their maintenance.
By choosing a repair that works to the standard, the end-user can be confident that these important points are all picked up, and by appreciating what is involved, they can ask the right questions and understand the decisions and findings they are presented with.

ROOT CAUSE ANALYSIS
The standard promotes the identification and communication of the root cause of any failure, identifying the signs such as colouration patterns on the windings, contaminates, traces of moisture, bearing housing wear or bearing failure.
These findings can be relayed back to the customer, so they are made aware of what possibly caused the failure and what they should check before returning the motor to service.
An end-user may have no idea they have a water pipe leaking above the motor, or that a seized gearbox has caused the motor to burnout, a contact has failed in the panel or the drive belts are too tight.
To the end-user, the motor has failed, and they want it back quickly, but without understanding the cause of the failure, unnecessary future disruption is a real risk. With the current focus on plant reliability and reducing downtime, anything that helps minimise these risks is a real benefit to the end-user.
REPORTING
Reporting is an important area and is designed to support both the repair and the customer.
The standard calls for the use of digital cameras to record key information about the item under repair. It says: “Digital photographs provide an accurate record of how the machine was received. This also provides a visual record of any significant component defects found and provides evidence to the user of the remedial work required.
All findings should be recorded to ensure that a list of remedial action undertaken is available for the final report.”
Photographic evidence of the repair process, from receipt to dispatch, gives clear evidence of how the motor arrived and how it left the repair facility.
A scope of works is also required. Essentially an expanded quote, a scope of works will include information such as a detailed visual inspection, the root cause analysis and the proposed scheme of work.
And in a final report, the repairer should collate all documentation relating to the repair. This will include a record of parts used and the work carried out, plus details of any machine work, balance check reports and tests that have been performed, with the results. The report should also state what tests and checks have not been done, for instance, if no core flux test was performed, or no load or vibration tests were recorded.
This comprehensive level of information enables the end-user to keep a record of the service. If the motor is worked on elsewhere in the future, this information can be supplied to the new repairer, while any repairer working to the standard will keep a record of test results, data, faults and information for at least three years.
CONCLUSION
There are several benefits of working with, and understanding, a repairer working to BS EN IEC 60034-23. But, as the concept of circular economy gains greater popularity, companies that embrace the standard will be able to promote their active participation. This has the potential to highlight the professionalism of both the repairer and the company selecting the repairer. It also demonstrates their collective commitment to reducing waste and minimising the consumption of resources.