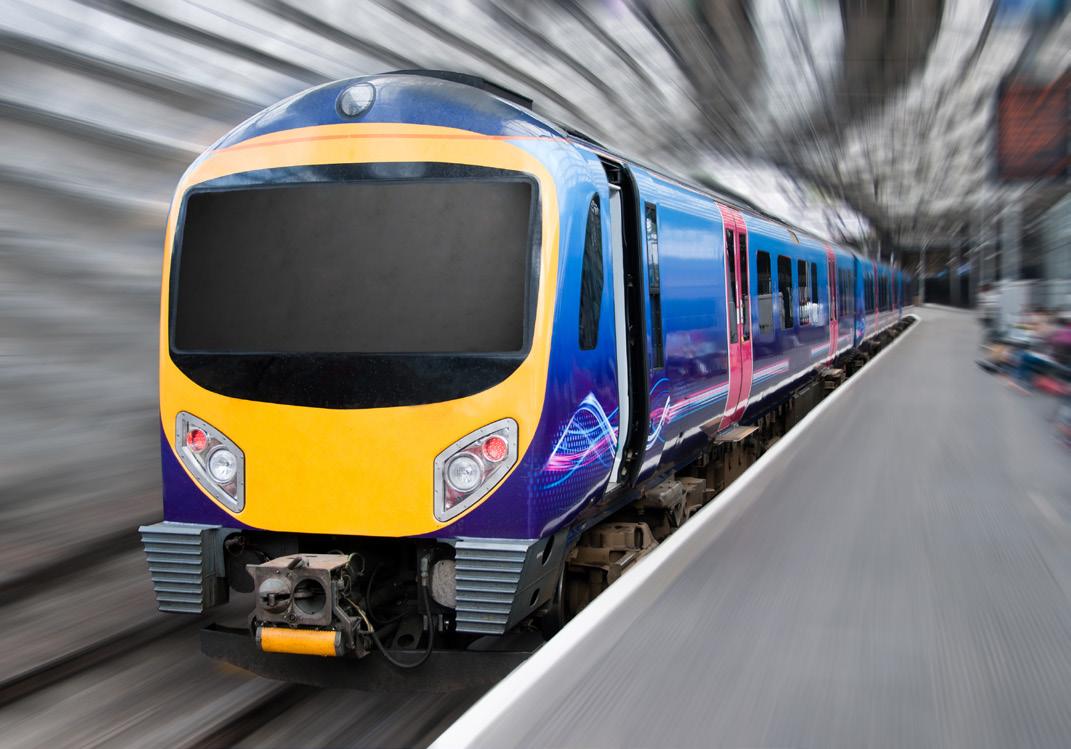
5 minute read
Project updates
PROOF THAT VIBRATION MONITORING MAKES SENSE
WHEN ENGINEERS ON A NORTH SEA platform reported that an 800kW Ex de certified induction motor was exhibiting high vibration levels Quartzelec’s Aberdeen service centre was approached to investigate and undertake any necessary repairs on an urgent basis before the issue led to a major machine failure.
Advertisement
High vibrations in rotating electrical machines can indicate issues with operational performance which will impact machine availability so, with the 800KW production critical motor displaying increased vibration levels, Quartzelec advised that it was quickly removed from operation and sent to Aberdeen workshop for investigation. The motor was stripped and inspected to determine the repairs needed. All repairs were then completed within an agreed timeframe, and it was then immediately returned to the platform.
Commenting on the project, Paul Oliver, Quartzelec’s business unit manager in Aberdeen, said: “We had successfully repaired the sister machine on the North Sea platform two years earlier after catastrophic bearing failure. On that machine, the bearing failure also led to further damage and a full rotor and stator rewind was required. Whilst the first motor repair was costly to the customer in terms of financial outlay and the resulting lead times, following our recommendations, they incorporated ongoing vibration monitoring which helped them spot problems developing before the failure occurred. This resulted in them saving considerable time and money; whilst maintaining a safe working environment without impacting output.
“When budgets are tight, condition monitoring can sometimes be sacrificed, but this is a perfect case which proves that investing in the correct condition monitoring system makes perfect business sense,” concluded Paul.
www.quartzelec.com
In-situ machining of a traction motor

EARLIER THIS YEAR MERSEN POWER TRANSFER Technologies UK, working with Mersen Benelux, started the in-situ machining of more than 90 brushed MA set DC motors at the customer depot.
The MA Set commutators had started to show signs of wear and tear after many years of service, with some motors flashing over and failing on the Class 455 locomotives, causing train availability and reliability issues.
Mersen deployed its Motor Maintenance and Services (MMS) team, in very strange times due to the ongoing pandemic, and started the machining of the DC commutators to return them to a nearly new state. The project should be completed by the end of this year.
www.mersen.co.uk
CAUSING A STIR

ENGINEERS AT WESTIN DRIVES came up with an innovative solution when they were presented with a paintstirring machine that was only able to run at one speed.
Fraser Lynch, Technical Manager at Westin Drives, explained that the machine’s owners needed to diversify their paint offering, but the bespoke, single-phase agitator was not up to the job. A cost-effective solution was needed to enable them to upgrade the unit so it could run at variable speeds to reduce over-agitation of certain paints and to increase it for others.
Because single-phase motors have limited and expensive variable speed drive controls, a progressive output three-phase motor and single to threephase IP66 inverter from Invertek was offered as a suitable engineering solution. Because it was still perfectly serviceable, the existing gearbox was retained.
The customer was delighted with this neat and effective solution and was able to adapt to present and future requirements with only 24 hours of downtime.
www.westindrives.com
MINIMISING DOWNTIME IN AN EGG GRADING FACILITY

IT IS A FACT OF LIFE THAT THE MORE specialised your equipment, the harder it is to repair or replace parts in the event of a failure. In the food industry, unexpected downtimes can be costly, which is why an egg grading facility turned to Rotamec – an electro-mechanical engineering service provider for engineered equipment – to deliver repairs and source spares.
The grading facility assesses each egg that reaches its processing lines from partnered farms before packaging. By checking for any imperfection with specialist equipment, grading ensures every egg is in optimum condition before it is packaged and delivered to customers.
Reducing downtime through the use of responsive maintenance was very important to this facility. Darryl Beecham, business development executive at Rotamec, takes up the story: “We have to react quickly to minimise downtime. For example, the customer required a double-sided open length timing belt to keep a conveyor operational after a failure of the OEM part. With the cost of downtime on this machine being around £3,000 an hour, lead time was all-important. In this case, the maintenance team decided to order two parts, one from us and one from the OEM, to maximise its chances of getting the machine back up and running the same day.
“We were able to deliver the belt within two hours, while the OEM took six hours. Our belt was quickly installed, and the OEM item was added to spares. All in all, we managed to save this customer around £12,000 in downtime costs.”
The egg grading facility operates varied motors and gearboxes. Reliable supply of a wide range of standard parts from a single supplier is important to help keep equipment running. Thanks to existing warehouse stock and in-house distribution capabilities, Rotamec can deliver standard parts quickly – typically the same day if required. Further, its inhouse machining capabilities mean that bespoke items such as shafts in various bore sizes can be easily produced too. Rotamec can offer 24-hour turnarounds on motors and gearboxes, so despite different configurations and equipment throughout the site, it can still offer reduced repair and sourcing lead times.
This customer does present some specific challenges, as Darryl explains: “One repair job required us to source specialist foam material that cushions the eggs during grading. The egg comes through to a sensor, where it taps against the foam, which detects any hairline cracks as part of the quality control process. Improper foam will crack the egg, so only an exact solution will do. The grading facility required replacement foam for the machine, but the OEM lead time was going to take too long, so we were approached. It was a bit different from the mechanical issues we typically deal with, but we managed to source the foam within the required timeframe.”
Both the grading facility and Rotamec understand that reducing downtime is one thing, but preventing it is another. This is why engineers from both businesses are building redundancy into maintenance and repair operations. By undertaking asset inspections and identifying ‘showstoppers’ – equipment that risks overall uptime if it fails – the engineers are prioritising maintenance to focus on the most critical assets. Rotamec has also enacted a policy of ordering spares from relevant OEMs during each repair, ensuring maintenance work is backed by a growing spares inventory.