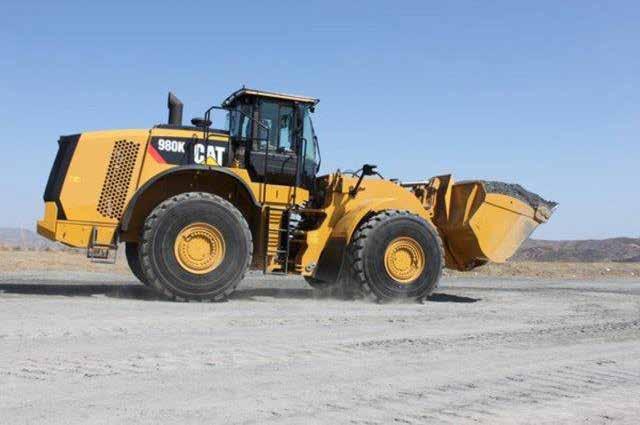
28 minute read
Dealing with fire risk in a mining environment
ASP Fire designs systems to suit individual vehicles and their specific requirements
Advertisement
Mining vehicles such as excavators, haul trucks and even drag lines are high-value assets that operate in arduous conditions where there is a high fire risk. This means that pre-shift and weekly inspections on mining vehicles are essential to ensure that the fire prevention system is in good working order.
“We assist mining operations to mitigate any risk posed by fire, which can affect productivity and profits,” says ASP Fire CEO Michael van Niekerk. The fire engineering expert designs systems to suit individual vehicles and their specific requirements. This means examining the conditions not only inside the vehicle, but also within the surrounding environment. The design and installation of a vehicle fire-protection system requires that mining vehicles are subjected to a Hazard Identification and Risk Assessment (HIRA) of potential fires. Each vehicle needs to be assessed carefully within its specific operating environment to understand what hazards and fire risks that vehicle is exposed to. Inherent fire risks include the turbochargers and brake system overheating, as well as high-pressure hydraulic systems and electrical equipment that may ignite a combustible or flammable component of the vehicle. Although Dry Chemical Powder (DCP) extinguishers are highly effective in firefighting, they offer minimal cooling properties. This results in re-ignition of flames, especially in liquid fuel and rubber fires, thereby increasing the risk of property damage and loss of life. The powder inside DCP extinguishers
can also compact due to vibration when placed on a moving vehicle.
The compacted powder increases the risk of malfunction when activated. As a result, DCP extinguishers placed on mobile equipment need to be serviced more frequently. DCP extinguishers also pose serious operator and environmental hazards. When used in confined spaces, they can affect the fire respondents’ visibility and capability to effectively suppress the fire, or to safely evacuate an area should the fire spread out of control.
A much more effective and ‘greener’ solution is water-mist handheld fire extinguishers. Utilising water as the main agent and nitrogen as a propellant, these can extinguish most types of fires, including rubber and plastic, diesel and petrol fires, and electrical fires rated up to 245 kV.
The atomised mist generated by the extinguisher increases the surface area of the water by more than a hundredfold. The micro-droplets rapidly turn into cold steam when meeting burning or very hot materials, further increasing the surface area by 1 600 times. The endothermic reaction effectively cools down any hot surfaces in the immediate environment.

ASP Fire CEO Michael van Niekerk Not only is the fire extinguished, but any hot spots also cool down without any thermal shock. The thermal heat radiation barrier created allows the operator to approach the fire without sustaining burns to deploy the extinguisher. A protection mechanism eliminates any false alarms. This consists of a heatsensitive pressurised activation tube that requires heat to rupture and open a differential valve on the main cylinder to activate the system.
Another solution offered by ASP Fire is an Aqueous Film Forming Foam (AFFF) for fire-extinguishing and vapour suppression of hydrocarbon fuel fires. The AFFF blanket blocks oxygen supply to the fuel and cools any hot flammable liquid by effectively sealing the surface.

Mining vehicle fire-protection systems are based on a Hazard Identification and Risk Assessment (HIRA)
How do you control dust in a crushing plant?
Operations related to the extraction of mineral ore such as blasting, transportation, grinding, and crushing can release large amounts of dust into the atmosphere. This is particularly true in a crusher plant where the demolition of stones, an operation that generates vast amounts of dust, is a daily procedure.
Dust can generate a series of problems for industrial operations. Not only can dust cause health problems, but it can also reduce the productivity of a mining site by limiting visibility and increasing wear-and-tear on equipment.
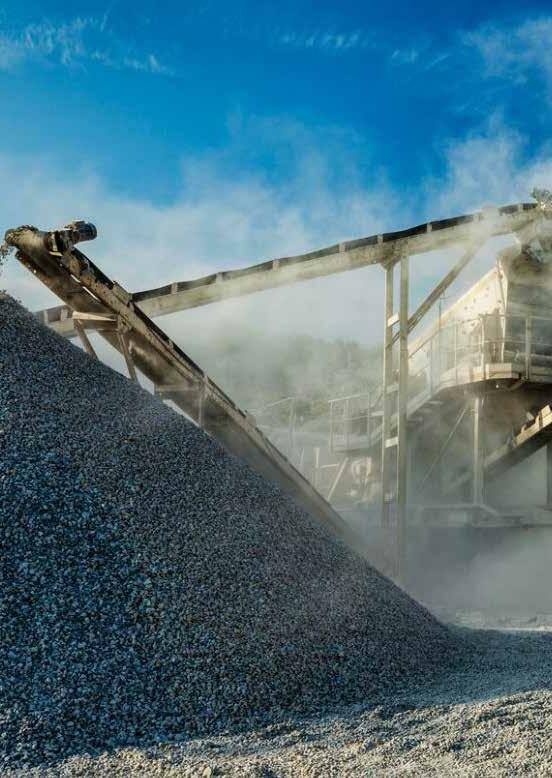
What is crusher dust? Crusher dust is a type of fine dust, which contains very small 0-5mm aggregate particles as well as sand. It is formed as a by-product from mining operations and is often recycled for different applications such as construction.
Whenever rocks are crushed by rock crushing equipment, tiny PM 1, PM 2.5 and PM 10 dust particles spread through the air. This by-product of rock crushing may cause harm to the health of workers and nearby communities and damage the durability of equipment, leading to bearing failure, lubricant contamination, and increased risk of fire autoignition.
Particles coming from high compressive strength rocks (hardness), with a higher mosh index and angularity (sharp edges) cause the greatest damages, such as silica, quartz and diamond dust.
Health effects of crystalline silica
Silicon dioxide, also known as silica, is a chemical compound commonly found in quartz. Silica normally presents itself in a crystallized form, and it is a component of sand in various parts of the world. Industrial uses of silica include the manufacturing of microelectronics and structural materials. Some living organisms, such as grass, use silica as a defense mechanism to drive off herbivores (source).
Breathing dust particles from crystalline silica can have scathing effects on a person’s health. Airborne dust can stay lodged inside the lungs, causing inflammation and scarring on lung tissue. This condition is known as silicosis and can result in permanent lung damage or even the death of the patient.
Chronic silicosis can occur after periodic exposure to silica dust, but exposure to large amounts of dust can drastically hasten the development of the condition. Even after exposure to dust is discontinued, silica dust particles can remain in the lungs for prolonged periods of time. Symptoms of silicosis include: • Cough • Fatigue • Shortness of breath • Chest pain
Silica dust from stone crushing can be a major factor in a person developing silicosis, leading professionals to catalog it as an occupational lung disease. Complications from developing silicosis can also cause patients to develop more serious diseases.
Examples of other serious diseases caused by silica and other airborne dust exposure include: • Tuberculosis • Lung Cancer • Chronic Obstructive Pulmonary
Disease (COPD) • Kidney Disease • Rheumatoid arthritis • Systemic lupus erythematosus • Systemic sclerosis (scleroderma)
How do you control crusher dust ?
The most efficient method of controlling dust generated in a crushing plant is the use of dust suppression systems within a methodology and understanding of your process, mechanical stressors, enclosures, weather conditions and operational context.
First, you should always try to avoid/ eliminate dust generating activities as much as possible, by choosing and maintaining equipment that have lower dust emissions, proper enclosures and filters systems that keep the dust within the process and avoid dust emissions. Keeping the house in order can reduce dust emission by up to 50%.
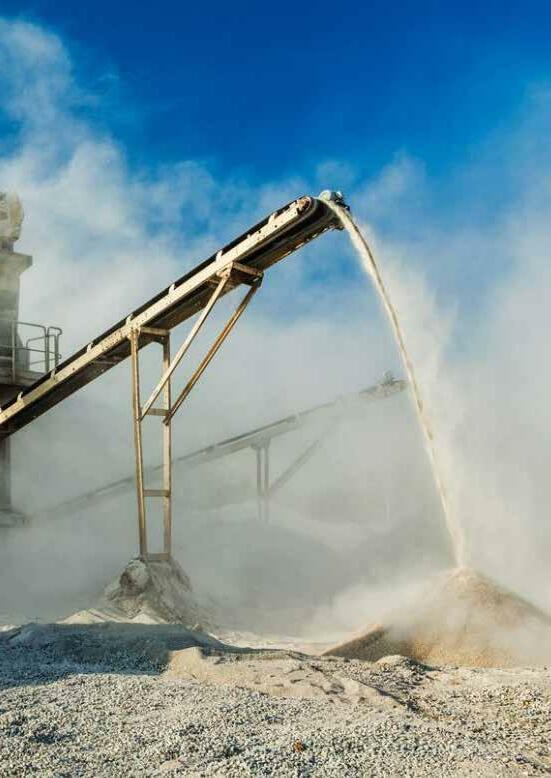
Secondly, a dust control specialist can recommend to you a combination of engineered dust control solutions such as dry fog, fine mist, dust collectors, improvements of feeding, discharge and transfer points and enclosures.
Finally, you need to put in place control loops taking into account dust concentrations, visibility indicators, throughput, and weather conditions such as wind speed, wind direction and air pressure, moisture and temperature changes that lead to air stagnation conditions. This is key to incorporate, assess and improve control measures and ensure you run a continuous dust controlled operation at your site as well as to make sure your personnel are wearing the right personal protective equipment in terms of respiratory protection and are not exposed to health risk due to uncontrolled dust levels along their work schedules. For mining industrial groups, dust suppression ensures the safety of the labor force and the productivity of operations, so investing in the best dust suppression solutions, monitoring solutions and continuous improving systems is a major priority for mining companies.
DMS-FOG
DMS-FOG is an effective dust control solution that uses smart dry fog and fine mist systems. Dust suppression systems in DMS-FOG consist of stainless nozzles that can produce either fog or mist. Using microscopic amounts of water, the system covers the source of dust and prevents dust particles from going airborne. Emissions of dust can also be avoided by applying dust control additives to the water suppression systems.
The system can be equipped with specific stainless nozzles depending on the purpose it is being used for. This increases the durability of the hardware and therefore reduces the amount of time
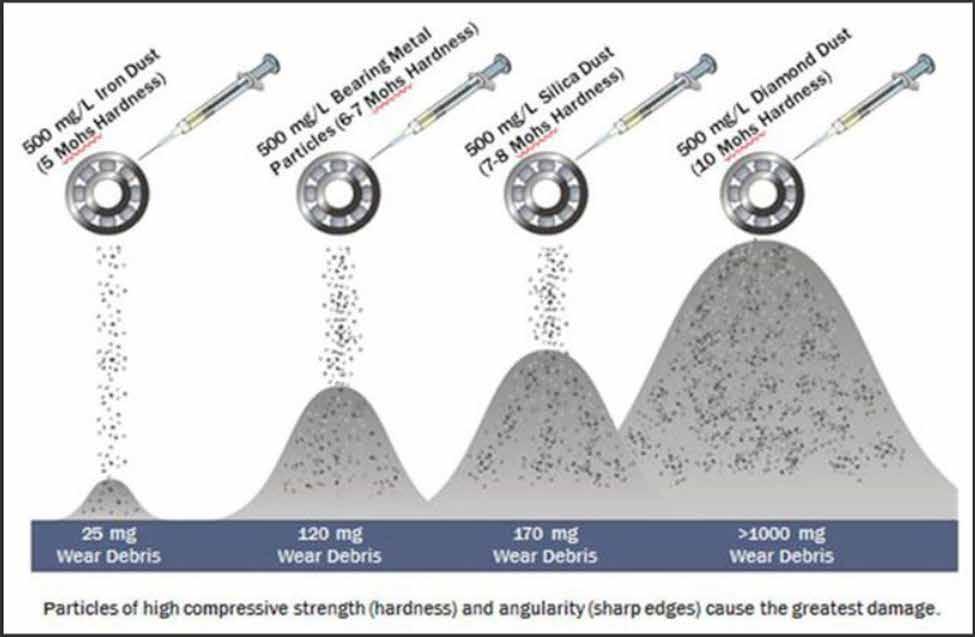
and resources needed for maintenance. Furthermore, controlled temperature technology implemented by DMS-FOG guarantees its effectiveness regardless of weather conditions.
DMS-FOG is the result of 20 years of dust capture method development, making it an efficient and resourceeffective solution. By using DMS-FOG in tandem with other dust control solutions like DMS-TDS additives, the efficiency of dust suppression can be drastically enhanced while also saving on water and operational costs.
The on-site information display and control capabilities of DMS-FOG can be integrated into ABCDust’s DMS-ONE platform. With the use of the DMS-ONE system, the capabilities of DMS-FOG can be monitored and optimized. The control system has many automation features, which include timing controls using input and output sensors and extreme dust particle monitoring to optimize dust suppression and resource use. and control the flow of air and water. Integrated time relays and auxiliary contacts (PLC) are implemented for a remote start alongside pilot lights, ball water valves, and manual shutoff valves. The system is delivered in an IP66 enclosure and is water and dustresistant.
DMS-TDS
DMS-TDS is a non-ionic chemical additive that can help control dust by restructuring water particles. This substance is designed using a proprietary mixture of non-ionic surfactants, alcohols, and nano-polymers. The resulting mixture of these components is highly surfactant, efficiently reducing the tension between H2O particles and other materials.
The main attributes and characteristics of DMS-TDS are: • Minimizing dust in the atmosphere, improving air quality and visibility • Drastically increasing the resource effectiveness of water • Being a highly concentrated solution, which facilitates its transport and storage • Resistance to acidic, alkaline, and salt water • Having a non-ionic, non-toxic, and non-corrosive chemical composition • UV resistance
Water particles modified by DMS-TDS are able to capture and absorb fugitive dust particles, effectively minimizing dust in the atmosphere. DMS-TDS solutions are often used as dust suppression plant aggregates for cargo fronts, conveyor belts, and other structures at risk of dust collection.
A major advantage of implementing DMS-TDS is the resource-effective use of water. Using DMS-TDS to suppress dust can reduce water needs by up to 90%. The chemical is applied by mixing it with water and spread using water cannons or sprinkler systems. The specific dose of DMS-TDS used is determined by the type of dust being suppressed. It is possible to use a DMSTDS solution together with the dust suppression systems of DMS-FOG, creating an extremely efficient integrated system.
Extreme dust level monitoring DMSEXTREME
ABCDust can monitor airborne dust levels by using state-of-the-art measurement technologies. Alongside solid methodologies supported by years of research and development, this technology can be used to assess dust levels in the atmosphere under different environmental conditions. Using this data, you can determine which suppression method can best ensure mine safety while guaranteeing competitive mining operations.
The extreme dust levels monitoring technology implemented by ABCDust includes the following features: Perpetual measurement of dust levels of up to 4,000 mg/m3 for different PMs. • Weight analysis of samples to measure mg/m3 dust emissions and characterize them. • Creating predictive and analytic models of dust emissions based on different factors including wind, air pressure, temperature, air inversion, humidity, production levels, type of materials involved, and more. • Recommendation of the most
effective servicing of dust extraction, including alerting about pending maintenance. • Conducting evaluation before and after implementation of dust suppression solutions to measure their success. • Producing emission reports before and after the use of dust suppression methods. DMS-ONE Dust management and continuous improvement system Many mining companies leverage DMSONE to optimize crusher dust control programs. The platform integrates sensors for dust control, weather conditions, throughput, visibility, and moisture to optimize dust suppression and crusher maintenance costs.
DMS-ONE facilitates prevent and mitigate extreme dust concentrations and improves your crusher maintenance, avoiding risk of fires and advising the proper workers health and safety measures be implemented.
Smart dust control and soil stabilization ABCDust distinguishes itself by providing an integrated solution for dust control and monitoring systems in any mining environment. Backed by application, monitoring, and control systems, ABCDust can deliver effective dust control measures and soil stabilization aggregates. Together with constant analysis of production indicators, ABCDust’s dust suppression systems offer an efficient, safe, and friendly work environment.Partners of ABCDust can expect the following services when working in a crusher plant: • Monitoring with the use of stateof-the-art dust suppression methodologies • A field visit to collect operationcritical information • Development of a situation analysis of the crusher plant • Proposal of different dust suppression strategies • Dust measurements before and after operations have been developed • Setting strategic guidelines for an implementation plan with continuous improvement as its central focus.
Source: ABCDUST
FREEBASE
LAND SURVEYOR SERVICES

We offers a full range of land surveying services by providing a comprehensive surveying service to clients and guarantees an accurate, professional and reliable service. • GPS Surveys • Subdivisions • Title Surveys • Town Planning • Feature Surveys • Lease Area Surveys • Engineering Surveys • Topographic Surveys • Development Consultants • Existing Conditions Survey • Adverse Possession Claims • Earthwork Volume Surveys • Construction and Building Set Out
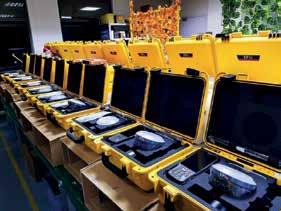
General Construction and Civil Engineering Works Project Management MCH 2 Number 17 NAPSA Complex Kalulushi, Zambia
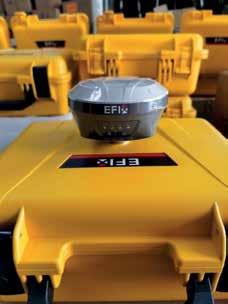
Contact Details
We are also the official distributors FREEMAN CHIPALILA Cell: +260 767200400 of EFIX GEOMATICS GNSS Equipment +260 978 971 910 Email: freebasezambia@gmail.com Kitwe Branch Office: ANCHRIS HOUSE, Second Floor, Room 24&30
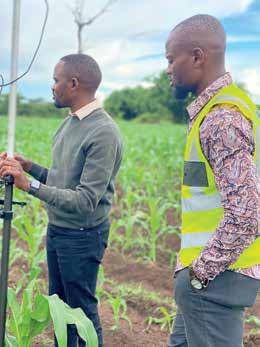
The strength of your machine is defined by its pivot joints
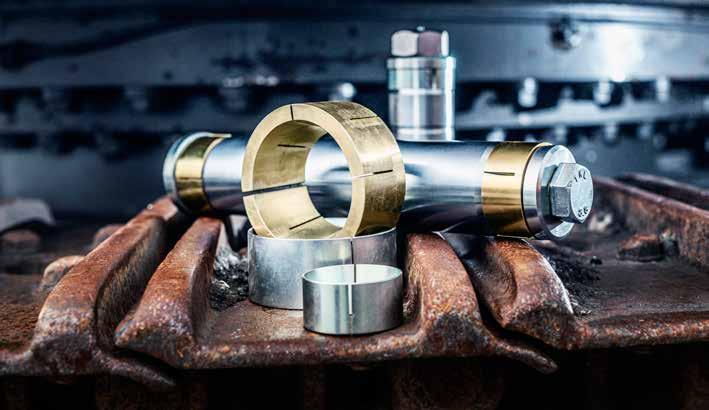
BMG’s Nord-Lock range of bolting solutions includes Expander System pivot pin components that comprise advanced pivot pin technology, to offer dependable solutions that combat the challenges of lug wear in diverse industries.
BMG’s Nord-Lock range of bolting solutions includes Expander System pivot pin components that comprise advanced pivot pin technology, to offer dependable solutions that combat the challenges of lug wear in diverse industries.
Pivots, which are at the centre of any rotational movement, often experience lug wear, which occurs due to the clearance between the bore and the conventional pin. This is commonly repaired with line boring – a technique associated with high costs and protracted downtime.
“Through Nord-Lock’s advanced Expander System, which consists of a comprehensive range of components, BMG specialists are able to supply the correct pivot to prevent the problems that lug wear causes excavators, mobile cranes and dump trucks, in order to maximise uptime, enhance safety on site and minimise maintenance costs,” says Wean Marais, National Product Manager - Nord-Lock Group, Fasteners Division, BMG. “The Expander System – which comprises an assembly that includes an axle tapered at both ends, two expansion sleeves, two tension washers and two fasteners – has been designed for convenient onsite repairs. Even in a situation where the lugs are badly worn, a repair can be made in the field, with minimum downtime. The sleeves of the Expander System simply expand to conform with the wear pattern and lock the system in place, without the need for time consuming and costly welding and line boring. Once retorqued, the system locks from both sides, significantly increasing stability.
“This system has also been designed to improve safety on site. By replacing a traditional straight pin with an Expander System pivot pin of the same diameter, the risk of axle breakage is reduced and the strength of the machine is enhanced through the system’s double sided axial locking design. “There are many other benefits, which include a permanent solution to lug wear, quick and easy installation and removal, increased service life of bushings, bearings and seals and greater safety. A key advantage of this system over conventional pivot pins is pressure distribution. A conventional system only distributes the load onto a very small area, where the Expander System distributes pressure over the whole contact area in the direction of the force.
“There is no need for additional fastening holes, threads or welding of locking rings on the machine and no need for fine machining in the lugs, as this system makes it possible to use wide tolerances. The Expander System can also be combined with Nord-Lock washers for enhanced efficiency in vibration-intense applications.”
BMG’s customised Expander System pivot pins are specifically adapted to suit exact requirements, through the use
of specific materials, hardening treatments, surface coatings and the correct tolerance for each application.
This system is suitable for use in many industries, including construction, steel, railway, bridge building, mining and quarrying, forestry and agriculture, manufacturing and processing, shipbuilding, marine energy and power generation, oil and gas, transportation and machine building.
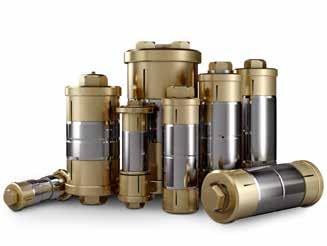
Severe vibration of heavy machinery is a major challenge in the mining industry. BMG specialists recommend the use of the Expander System in conjunction with Nord-Lock wedge-locking washers as an efficient vibration-resilient pivot solution for reduced maintenance and downtime in loading and hauling equipment, drilling, excavators and mechanical scalers.
Safety and productivity are critical on any construction site, where the continuous operation of equipment and machines makes lug wear prevalent. The Expander System has been designed to extend the service life of pivot joints in articulated haulers, excavators, dump trucks, backhoes, wheel loaders, cranes and bulldozers.
Forestry and agricultural machinery often operate in isolated locations, which are long distances from workshops and technical support. This makes them susceptible to long periods of downtime if they break down. The Expander System is quick and easy to install and remove, allowing for on-site maintenance, substantially decreasing production losses associated with downtime.
In the oil and gas sector, the Expander System increases control and precision during the handling and setup of drilling equipment, while enhancing safety on the rig or extraction site.
This system is also designed for efficient use in manufacturing and processing. For example, in cutters, sludge filters, centre rollers and jack-screws in paper mills, and balers, intake and trimmers used in saw mills. In energy plants, these pivot pins are used in roasters, stoker feeders and grapples and in steel mills, in cooling beds, tensioning arms, oscillator and segment machines, side roller guides and side tensioner frames.
Nord-Lock Expander pivot pins - used by many leading Original Equipment Manufacturers - have been endurance tested for over 50,000 hours without failure and more than 1 million pivot pins have been installed in over 60,000 applications.
BMG specialists work closely with customers in all sectors, to offer a complete service solution, where the team’s technical expertise supports quality structural fasteners and fastening components.
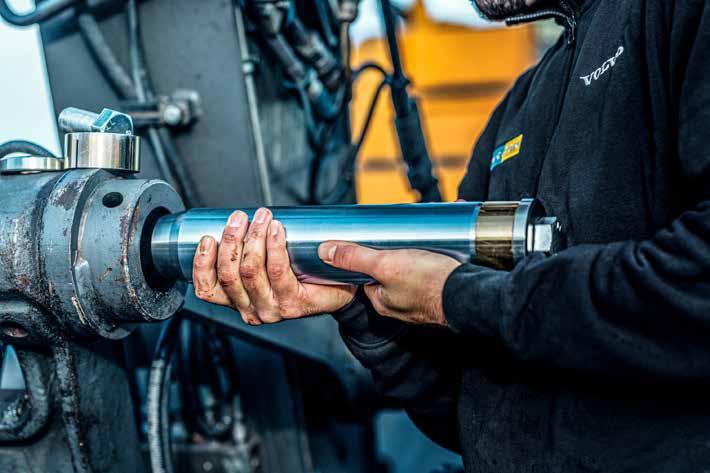
AR Controls well positioned to ride copper, cobalt and nickel wave in Africa and South America
OEM also extending its global footprint into West Africa, Australasia Pacifica and South America
With the global mining industry on the cusp of a commodity super cycle the likes of which was last seen in 2015, this remains the largest, most lucrative, and low risk market for valves in Africa. “Copper has proven especially robust during a depressed financial market,” notes AR Controls Managing Director Julien van Niekerk. It has placed the spotlight firmly on the Central African Copperbelt, the largest copper and cobalt resource in the world, centred on Zambia and the Democratic Republic of Congo (DRC). The leading importer and manufacturer of a comprehensive range of internationally recognised valves and instrumentation is successfully undertaking major work in the DRC. “We had already made inroads into the DRC a decade ago when it was considered a difficult and closed market, and now it is one of the most favoured mining destinations on the continent, especially in terms of copper,” says van Niekerk.
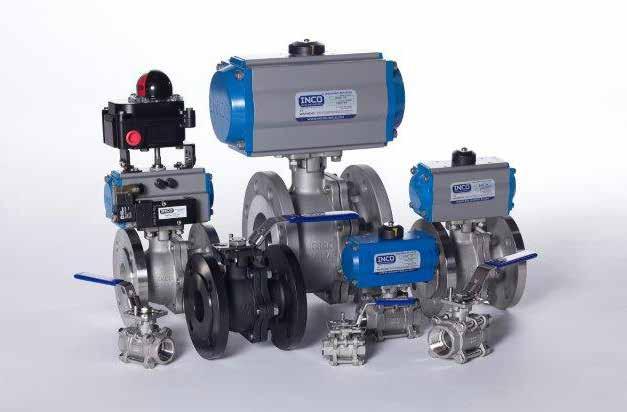
Apart from its ongoing expansion in Africa, AR Controls continues to extend its global footprint. This includes a strong focus on niche markets in Africa, Australia and Pacific Islands, and South America. “Our international expansion is made possible due to our dual role as both a manufacturer and a stocking distributor, as well as the excellent supply-chain management we leverage globally,” highlights van Niekerk.
The impact of the Covid-19 pandemic on the mining industry in particular has been increased lead times. As the largest valve stockist of its type on the continent
and possibly even in the Southern Hemisphere, AR Controls is hence in a unique position. “Having such a major inventory on hand is definitely a significant advantage against our competitors. Apart from supplying premium products, we also back this up with exemplary service,” highlights van Niekerk.
A major challenge remains the influx of sub-par valves into Africa from lowcost manufacturing countries. Quality is critical as it relates directly to gains in plant availability and revenue while operating in very arduous environments. “It makes it challenging for us in that we have to be innovative and at the same time have boots on the ground to physically add value to our customers’ supply chains in terms of operations and their procurement processes,” adds van Niekerk.
“Extending our reach through our channel partners, our distributors have factory trained personnel, and our aggressive on-site support maximises availability and uptime and reduces production losses. It goes a long way to forging very close relationships between ourselves and all our end users.”
AR Controls has been manufacturing the ARVALV® range since 1999 in its Vanderbijlpark factory, which has proven highly successful and has achieved a significant market penetration in critical process applications in the mining industry.
“Looking at our current market share, it is not inconceivable for us to double this in the foreseeable future,” says van Niekerk. In addition to ARVALV®, AR Controls owns the IncoValve and Controls® brand, which it acquired in 2016, and is the exclusive African and Central American distributor for international OEM DeZURIK.
“Our strategy is to break into new territories and industrial sectors, as well as continue to grow those markets where we are already entrenched. We are aggressively involved in offering new product lines to complement our existing range and ensure our pricing is competitive,” says van Niekerk.
The range of valves and actuation accessories available is robust and ideal for harsh mining environments. The core product lines are knife gate valves, concentric and high-performance butterfly valves, ball valves, non-return

AR Controls Managing Director Julien van Niekerk valves, control valves, actuation, and automation.
A key product line that has seen significant growth in demand is pneumatic enclosures, which are supplied in various materials to house and protect-critical instrumentation. It also ensures that valves installed in hard-to-reach or hazardous areas can be operated with ease from an easily accessible and clearly marked safe remote area.
AR Controls will be a major presence at Electra Mining Africa 2022 from 5 to 9 September at the Johannesburg Expo Centre. This is the first time the trade show has been held since Covid-19, with the OEM planning to take full advantage of displaying its full manufacturing and distribution capabilities and international presence. “Our significant presence will communicate clearly that we are a major contender and the partner of choice when it comes to premium valve and actuation products and back-up support and service for the mining industry,” concludes van Niekerk.

AR Controls butterfly valves AR Controls has been manufacturing the ARVALV® range since 1999
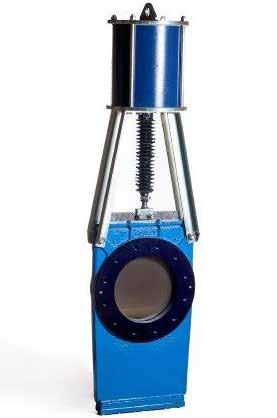
Africa’s green future is now thanks to thyssenkrupp Uhde’s cutting-edge green technologies solutions
thyssenkrupp Uhde, as a proudly environmentally-conscious company, is helping to green the planet through its leadingedge green technology solutions. Combining decades of experience and expertise, the company owns a large portfolio of chemical process technologies, including those for the production of green chemicals such as green ammonia and green methanol. For large scale green hydrogen production based on alkaline water electrolysis, thyssenkrupp Uhde collaborates with its sister company, thyssenkrupp nucera.
The global adoption of green hydrogen and fuel cell technologies for clean energy and transport applications is rapidly gaining traction as the urgency to tackle climate change accelerates. Energy transition holds great potential for Africa, unlocking the continent’s economy through new sustainable energy investments and becoming an exporter of clean energy.
In South Africa, insecurity of energy supply and its accompanying negative effects on the country’s economic growth is speeding up the demand for the green energy transition. Decreasing the country’s dependence on coal-fired power stations and moving to renewable or clean energy generation is the way forward. It holds countless advantages that will underpin economic growth and stimulate foreign investments. According to a recent statement by the Global Wind Energy Council (GWEC), the clean energy transition has the potential to create 250 000 jobs in South Africa over a period of 25 years. South Africa’s energy security can be addressed by fast tracking projects focussed on green energy i.e. wind, solar and green hydrogen.
thyssenkrupp Uhde’s Senior Sales Engineer, Nithesh Mohun, notes that the rapid deployment of these green technologies is essential. “Fortunately, South Africa’s climate and geography are well- suited for a hydrogen economy; we have an abundance of sun and wind as well as large expanses. In line with the South African Government’s hydrogen strategy, massive investments are being made ininfrastructure for the large-scale production of green hydrogen. This includes the development of the Green Hydrogen Valley project in the Provinces of Limpopo, Gauteng and KwaZuluNatal.”
Mohun unpacks the potential of green hydrogen, noting that it is so much more than a mere zero- carbon energy carrier. As an enabler, green hydrogen is the basis for other green technologies. It can be used to create a suite of products including green ammonia, explosives, green methanol, synthetic fuels, and synthetic natural gas. Moreover, green hydrogen applications include mobility and power generation via fuel cells and can be conveniently stored for deployment when needed.”
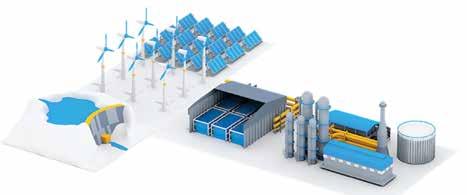
While the world clearly wants hydrogen, Mohun points out that getting it to countries in Europe for example, poses a challenge. He explains: “Gaseous hydrogen takes up more space than liquid hydrogen. Transporting large quantities of it in gas form is not feasible. Therefore, the solution would be to transport hydrogen as a liquid and to then convert it to gas at the point of storage or use. However, this requires the energy intensive liquefaction process, which itself is not economically feasible. We therefore look at hydrogen carriers as an alternative. We can take the hydrogen we produce and combine it with nitrogen to produce ammonia, a high-density energy carrier.”
thyssenkrupp Uhde has a CO2-free green ammonia production solution based on thyssenkrupp nucera’s AWE technology and 100% renewable feedstocks. Once Europe receives the ammonia, the ammonia can be cracked to hydrogen and nitrogen at the point of receipt. The associated cracking technology is also part of the ThyssenKrupp portfolio. When green hydrogen is combined with carbon dioxide green methanol can be produced. Methanol, like ammonia, is also a feasible energy carrier. Methanol is used as a raw product in the manufacturing of plastics and polymers. It is also used as a fuel additive for cleaner, less harmful CO2 emissions during combustion. thyssenkrupp Uhde also offers carbon capture technology for cleaning up the gases that are emitted into the air from smoke stacks. The harmful substances that have been captured can be stored and beneficiated later.
Green technologies also hold advantages for Africa’s agricultural industry with green ammonia and green urea serving as green fertilizers. All that is needed for the production of green urea is ammonia and a source of CO2.With over four decades of experience in the design and construction of urea plants, thyssenkrupp Uhde is regarded as one of the top international contractors in this field.
South Africa is advancing into green ammonia solutions with a proposed green ammonia export facility planned for construction at the Coega Special Economic Zone in Nelson Mandela Bay, Eastern Cape. According to various reports, the facility shall produce up to 780,000 ton-per annum of green ammonia with full operation scheduled by the end of 2026.
Crimar Industrial:
A leader in fiberglass industrial Equipment manufacturing
For over 30 years, Crimar Industrial has been providing high quality fiberglass industrial equipment (tanks, piping, ductwork, thickener covers, process equipment, custom fabrication, and field installation and maintenance services) to mining, municipal, petro-chemical and other industrial applications around the world.
Through their sister company, Shijiazhuang Beman Commercial Co. Ltd. (SBC) which handles sourcing and project management in China, the company can negotiate and enforce contracts with all the rights and privileges of a Chinese company and provide complete quality control and expediting services.
With a strong customer base which includes companies such as: WesTech, FLSmidth, Glencore Mining, Hatch Engineering, CODELCO, Freeport McMoRan, Jacobs Engineering, ASARCO, M3 Engineering, IMC Kalium, Abbott, Labs, Intrepid Potash, Siemens/US Filter, Biorem, Grupo Mexico among others, Crimar Industrial/SBC continues to be a major player in the industry.
Crimar Industrial/SBC also utilises top notch expertise both internal and external during the design stage of their products to ensure high quality products.
“While we have extensive internal expertise in fiberglass design and fabrication, we also have the full support of the design center at our subcontract facility in as well as of Professional Engineers in the US and Canada that specialize in fiberglass design and inspection services,” says company president Roger Beman.
All design, fabrication and inspection is in accordance with international standards such as ASME RTP-1, ASTM 3299, ASTM 4097.
As a testament of their rigorous internal QC, most customers have accepted in-house QC inspections as sufficient evidence of compliance. But when appropriate Crimar also contracts or coordinates with internationally known third party inspection companies such as Moody, Veritas, TUV Rheinland, and others to provide certified inspection reports of materials, production procedures, dimensions, and overall compliance with the terms of the contract.
To serve their customers better, Crimar Industrial/ SBC have sales & support offices in Tucson, Arizona; Toronto; Santiago; Lima; Shijiazhuang; Johannesburg; and Medellin in Colombia. Their office in China (Shijiazhuang Beman Commercial Co. Ltd.) provides complete sourcing, QC, import - export and expediting.
Key to their success has been in assisting customers by understanding their requirements, assisting them in design when appropriate, and the delivery of high-quality products on time for a competitive price.
In fact, Mr. Beman, the President and Owner of Crimar Industrial and majority owner of the Shijiazhuang Beman Commercial Co. Ltd. (SBCCO-China) has been traveling to China an average of 10 times a year for the past 15 years to ensure that suppliers understand and meet customers’ needs.
Products and services at a glance • Fiberglass Reinforced Plastics (FRP) Products • Steel Pipes & Fittings • Crushing and Milling Equipment and Wear Parts • Casting & Forging • Steel Process Equipment • Custom Fabrication - Steel and FRP • Dampers & valves • Solid/Liquid Separation Equipment • Project Management
For further information see • www.crimar.com • www.sbcco-china.com

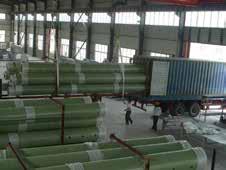

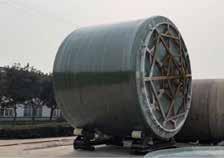
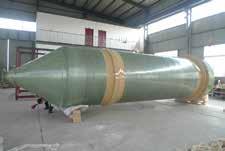
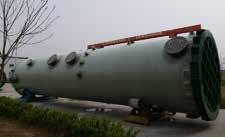
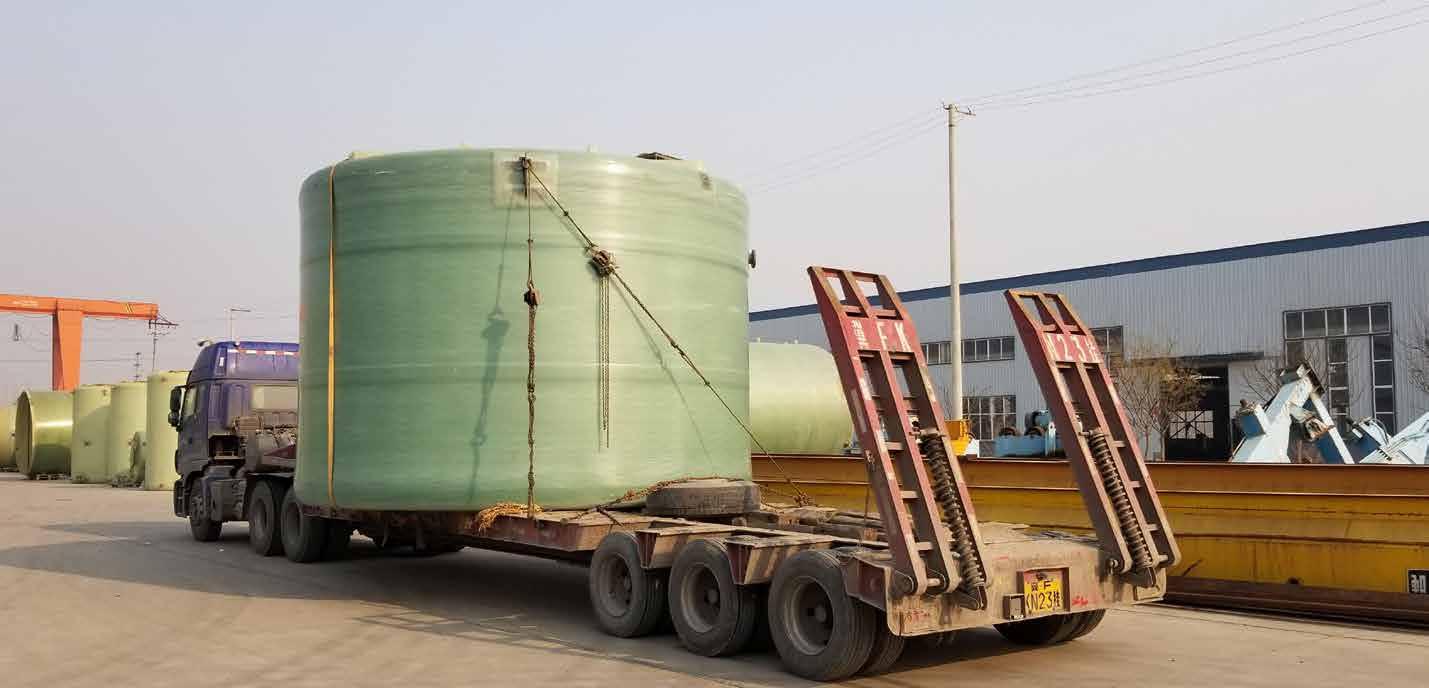
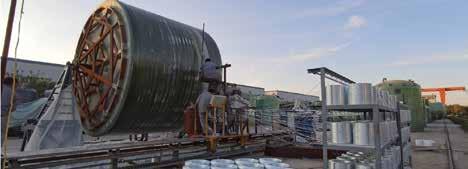
There are many different kinds of glass fiber to provide a wide variety of laminate strengths: • Glass fiber • Carbon fiber • Bamboo fiber
And different textures
• Winding glass • Chopped strand glass • Woven glass • Unidirectional glass • Corrosion veil •
FABRICATION METHODS
• Filament winding • Chopper gun • Hand lay up • Resin Transfer • Pultrusion
FRP DESIGN
Some of the information required for FRP design include the: • structural loading • chemical resistance required • temperature • seismic loading • wind loading
When appropriate we prepare finite element analyses (FEA’s) to model the design and loads to ensure that the project requiremenst will be met
We can help you from the beginning of the project through completion. We can assist with the design, fabrication, and shipping of the products sold. Where appropriate we can also provide on site fabrication or assembly. Once the installation is complete, we can provide ongoing support and maintenance services.
For further information please contact Zish Zhao at zishzhao@sbcco-china.com
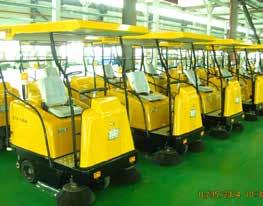
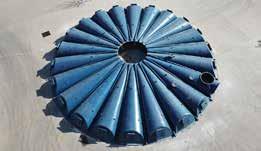
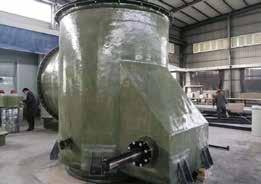

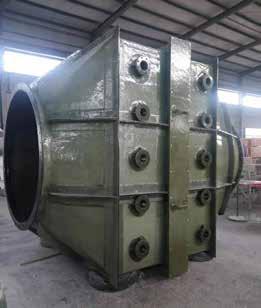
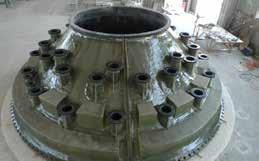

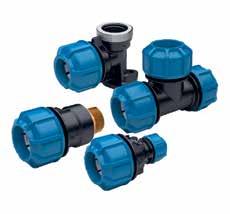