
16 minute read
Quality ‘cascade’ can optimise water treatment on mines
Relatively little water used during mining and processing needs to be clean or potable, so mines can reduce both water consumption and treatment costs by understanding what water qualities are needed where.
According to Peter Shepherd, partner and principal hydrologist at SRK Consulting, the mining sector’s drive towards ambitious water conservation targets means recycling more – so that less fresh water needs to be procured. There is also a financial benefit to recycling, as having to treat water before use or discharge is an expensive exercise. Shepherd highlighted that treatment can be kept to a minimum if mines are clear about what level of water cleanliness is required by its different on-mine processes.
Advertisement
“Clearly, a mine does not want to be using potable water to mix with tailings for pumping to a tailings storage facility,” said Shepherd. “Most of a mine’s water will generally be used in the process plant, and these applications can usually manage with much lower water qualities.” That said, there would be specific phases of the plant that require cleaner water – for the mixing of reagents and chemicals, for instance. There is also a need for water that is low in sediment particles for use in the gland seals of pumps.
Mines can therefore optimise the reuse and recycling of their water through developing a water quality ‘cascade’, explained Bjanka Korb, principal environmental engineer at SRK Consulting. This will detail the minimum water quality demanded by each process, so that water is not treated to higher levels of quality that needed at the point of use. “This approach opens the door to increasing the volumes that can be reused and recycled,” said Korb.
“The accumulation of water in the system and resultant discharge of low-quality water into the environment is thereby also minimised.”
An additional benefit is that the mine would be able to reduce its reliance on treated municipal water and therefore the operational cost to the mine could also be decreased. Where untreated dam water can be procured from a municipal source, the mine could use this directly in the plant – and only treat water to potable standards that is used in bathrooms, kitchens and drinking use.
Korb pointed out, however, that with more extensive reuse of water, the water quality within the mine system can deteriorate to the point where regular intervention is required. This is a consequence that must be carefully managed.
“Fortunately, most regions have seasonal rainfall which assists with keeping the water quality cleaner,” she said, “however, concentration of salts will occur over time regardless of this, and the reality is that mines may need to consider water treatment for recycled water in the later stages of the life of the mine”.
Developing the cascade approach needs a good understanding of the water and salt balance within the broader system – including the mine workings, the processing circuit, the tailings dam, the fresh water supply and the receiving watercourses.
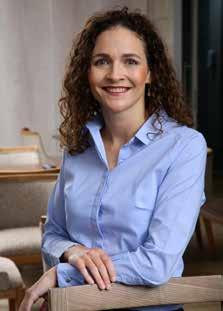
Bjank Korb
“By identifying the major drivers of water use, a mine can better target its recycling efforts,” said Korb. “For instance, if the water being returned from the tailings dam is sediment-laden or there are other elements within the water that do not easily settle out, then it may not be usable in certain key plant processes.”
Achieving the best results from a water quality cascade relies on good communication between the management of the mine’s process plant and its tailings facility. Plant managers,
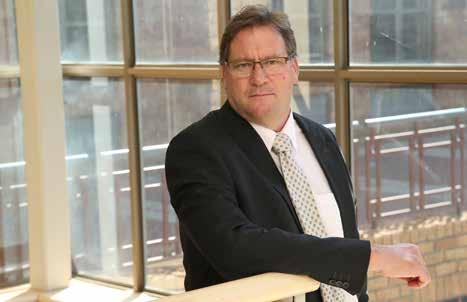
Peter Shepherd
who know the water volumes and qualities required from day to day, are important players in determining whether the process water demand can be fulfilled by return water from the tailings dam. The communication is vital as the tailings return water dams are often where most of the mine’s water is stored.
“The process plant and tailings teams together can assist significantly in managing the mine’s water balance, and in helping reduce the volumes of water being procured externally,” she said. Shepherd noted that leading mining companies have recently begun appointing dedicated experts to focus on water stewardship, to ensure that strategies are implemented and coordinated mine-wide to conserve water use. This, he said, was a positive step towards balancing a mine’s need for optimal recoveries in the plant, with the need to reduce water consumption from external sources.
HESCO
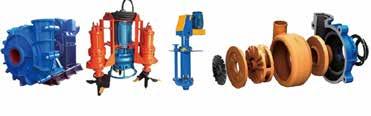
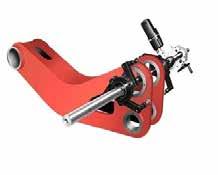
HESCO-HARDRICH ENGINEERING SERVICES COMPANY LTD MECHANICAL ENGINEERS, PRECISION MACHINING, FABRICATION, HYDRAULICS & PNEUMATICS, PIRTEK AGENTS Plot 1014 Zomba Road Kitwe, Plot 385 Kasakula Road, Mazabuka P.O Box 670430 Mazabuka 0955/0973 / 0966 411000, 0966925142 sales@hardrichengineering.co.zm, hesco@hardrichengineering.co.zm, hesco.kt@hardrichengineering.co.zm
Solid handling pumps for mining and mineral processing projects
Robust Pumps, Effective Slurry Handling
Using a traditional pump to handle a slurry is akin to the folly of putting a square peg in a round hole – simply put, it won’t work as desired. Instead, using a specified solid handling pump works wonders.
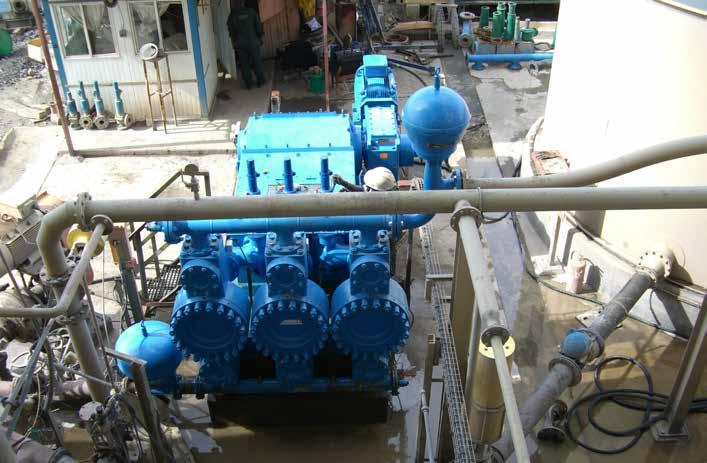
By Eric Peters
The War in Ukraine and the persistent effects of the COVID-19 pandemic lockdowns may have considerably negated the envisaged gains from global mineral resources prices for mining companies. While this is out of their control, what is within their reach is sustaining and improving productivity, pursuing cost containment measures and enhancing safety and reducing environmental impact. Using suitable equipment in the mining and mineral processing stages is the proven approach guaranteeing that each of these is met. Among the critical processes in which informed choices should be made in the procurement of equipment is in the pumping and transporting of slurry (fluids mixed with a concentration of solids).
Abrasive slurries encountered in dredging, mine tailings and others need special solid handling pumps. The relevance of solid handling centrifugal pumps becomes more appreciated when one considers the shortcomings experienced with traditional pumps in solid handling tasks.
Traditional pumps don’t perform
There are times - and it can be tempting - to use the traditional pumps in solid handling tasks because it is the easy way out, the most convenient. This happens when traditional pumps are deployed in solid handling tasks where, more often than not, they do not perform to the desired level.
Usually, abrasive materials wear down the traditional pump and the pump’s critical components within a short time. When this occurs, maintenance is needed at shorter intervals, resulting in unnecessary downtime and loss of production.
Solid handling pumps
Alternatively, solid handling pumps allow for easy pumping and transporting of fluids mixed with a concentration of solids. Due to their versatility, they can be used in dredging, mine tailings and other industrial applications.
Mainly, three types of pumps are used for slurry pumping: horizontal slurry pumps, vertical slurry pumps and submersible slurry pumps.
Recommended features
Based on information from some OEMs that supply mines and other industries, the following are common features of solid handling for mining projects: • Large flow path suitable for high solids and heavy slurry situations from the pump’s inlet port to the
discharge port; • They are made with different metal types with a proven ability to withstand corrosion and abrasion; • Self-cleaning design for easy cleaning; • There is the option of fitting grinders or even cutters to reduce the size of solids in sewage handling and related applications. • Noteworthy, last but not least, these days remote monitoring has become a standard in pump monitoring and controlling tasks. When equipped with remote monitoring, pumps can adapt to operating conditions in real-time, sustaining efficiency and reliability at lower costs.
Assured of immense gains
In the final analysis, a mining company gains immensely when it makes a prudent decision in the procurement of solid slurry pumps. It is assured of a low cost of ownership due to low maintenance and energy consumption and high performance.
Ticking the right boxes
A pump that is to be deployed for duty in the the application of transporting abrasive and corrosive slurry should tick the following boxes, mainly: • The right design: It should be robust and heavy. • Right configuration: The technical department of the supplier should be consulted for the suitable configuration for a mining application. • Low cost of ownership: A pump should have a low cost of maintenance • Ease of movement: The pump should be moved easily between applications.
SAM TURBO
INDUSTRY PRIVATE LIMITED
T 50
HE P O W ER OF
YEARS
INNO V A T IONS
SUCCESSFUL GLOBAL ADHERENCE
INDUSTRY LEADING MINING PUMPS
Mining pumps for mineral processing, slurry transfer, abrasive sludge dewatering, acid and chemical reagent dosing, water supply and boosting, and wastewater and tailing transfer. Our Single/ Double Casing - ARH/ARM/ARG models from 50mm to 300mm suction sizes, Provide reliable and effective performance to your mining needs
We also Supply Pumps & 100% Equivalent Spares for other Make Pumps
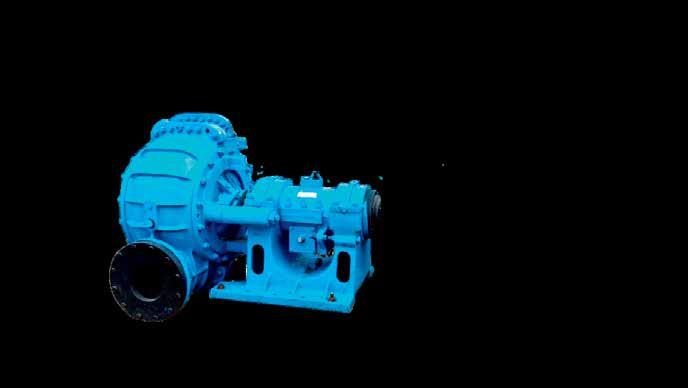
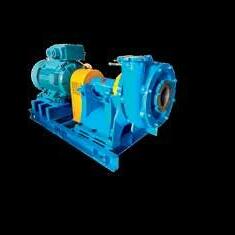
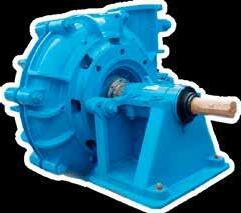
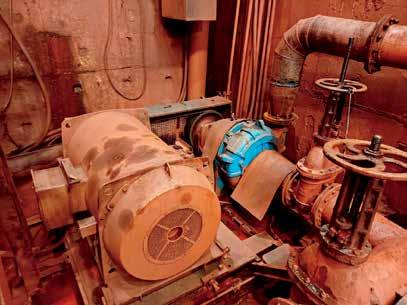

W O N E I R Q U E N
0422 6193555 mktg@sampumps.com www.sampumps.com Avinashi Road, Neelambur, Coimbatore - 641062 , Tamil Nadu, India
ABEL Piston Diaphragm Pump
Best Solution for Abrasive Tailings, Paste and Backfill applications
A success story: Konkola Copper Mines, Chingola, Zambia - Transfer of abrasive tailings through long distance pipelines and backfilling.

ABEL HMT pump used for tailings transfer since over 20 years HMT Triplex Piston Diaphragm Pump
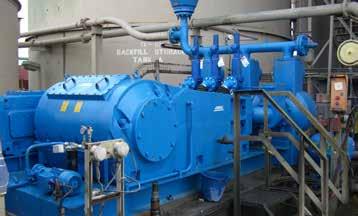
The Application
At the Konkola Copper processing plant in Chingola, Zambia, classified copper tailings from a thickener and cyclone installation had to be transferred over a distance of 3.5 km to the underground mine to be backfilled. The quantity of dry solids is 70 ton per hour.
The ABEL Solution
An ABEL triplex single acting piston diaphragm pump (HMT) was installed for the transfer of these abrasive tailings. The solids concentration in the slurry is 50%. The quantity of slurry tailings to be backfilled is 90 m³/ hr (390 GPM), the required pressure to cover the 3.5 km distance is 50 bar (725 PSI).
The Experience
Since start-up of the pump in 2001 the operating costs had been extremely low: due to the high efficiency of the PistonDiaphragm pump, the absorbed power at 90 m³/hr (390 GPM) and 50 bar (725 PSI) was less than 160 kW.
During almost 20 years of operation, the spare parts consumption of the HMT pump had been limited to the exchange of the valves every 5000 to 7000 hours. The diaphragms were replaced every 12000 to 16000 hours for preventive maintenance.
ABEL piston diaphragm pumps offer very low wearing and operating costs due to the physical separation of the abrasive slurry from the hydraulic side and pump’s main moving parts by preformed and hermetically separating rubber diaphragms. Only the product valves on the suction and discharge side and diaphragms are in direct contact with the abrasive slurry. The reciprocating principle of the piston diaphragm pump ensures a very high mechanical efficiency of >93%.
Consequently, the pumping costs (power consumption, spares etc.) and downtimes are minimal and make the operation of this type of pump very feasible and reliable when compared to more conventional methods of slurry transfer and backfilling.
Operating principle
The investment in a piston diaphragm pump needs to be protected against a number of potential risks.
In the ABEL pump therefore, the gears are forced lubricated in order to enable low stroke rates and smooth operations that prevent wearing and guarantee a long lifetime of the hydraulic system. Also, the pistons are lubricated to avoid overheating. The pump diaphragms are protected against overstretching by a reliable mechanical stroke monitoring system.
In addition, the pumps are equipped with pulsation dampeners which dampen pressure fluctuations, thereby protecting the pump and the piping system. The ABEL Piston Diaphragm pump is well known for its robust design and few parts makes it easy to install and maintain.
Main Applications
ABEL piston diaphragm pumps are the right solution for Mining - whether metallic or mineral mining, whether open pit or underground mining. In addition to tailings transfer, ABEL Piston Diaphragm pumps are also being used for other Mining applications such as: • Ore Concentrate pipeline transfer • Mine Dewatering • Thickener Underflow • Tailings transfer • Paste pumping • Backfilling • Slurry / Fluid transfer • Autoclave feed • Filter Press Feed
ABEL HMT/HMQ Pump Range
ABEL HMT (Triplex, single acting) and HMQ (Quadruplex, double acting) pumps range in pressure up to 23 MPa (3335 PSI) and in capacity up to 400 m³/ hr (1760 GPM).
ABEL Piston-Diaphragm Pumps Benefits • Efficiency of over 90% • 24/7 operational availability • Reliability for critical processes • Solids content > 75% • Accomodates a wide range of particle size • Dry running capability • Low Power consumption • Low Mechanical Wear
In addition, the ABEL Service team fulfil all service requirements around the globe. ABEL sales and distribution network is assisted by local partnership and distributor in Southern Africa, AQS Liquid Transfer, www.
aqsliquidtransfer.co.za.

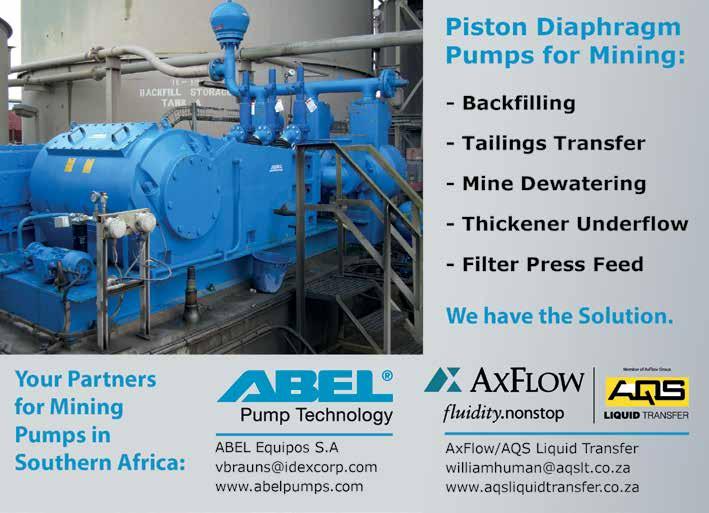

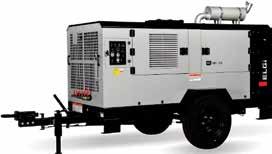
HOLDINGS

Offering you a 360° Healthcare and Emergency Medical solution
Protecting the health and well-being of your workforce can be challenging, especially in remote regions with limited access to healthcare facilities. Our Medical Services Teams are specifically designed to help you maintain the health of your workforce and ensure the continuity of day-to-day operations, with a strong focus on prevention.
Empowering Locals
With years of experience in the Medical, Rescue and Emergency Training fields, we offer our clients the opportunity to empower their workforce through a variety of internationally accredited courses or through bespoke training specific to your remote site.

Why Choose Us?
Experts in Healthcare & Emergency Medical fields
Committed to providing quality products & excellence in customer service
Exceed Industry Benchmarks
Bespoke Turnkey Solutions Provider
Delivering services across Africa since 2008
With years of experience in the Medical, Rescue and Emergency Training fields, we offer our clients the opportunity to empower their ses or through bespoke training specific to your remote site.
+27 (0)11 450 4263
info@ata-international.com
Rosond celebrates one year Zero Harm at Sishen
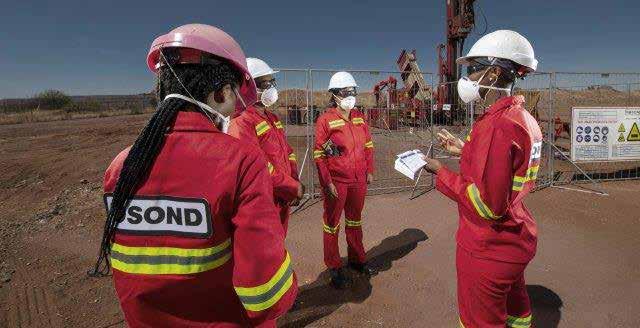
Rosond has had great success in training all female crews at Kumba iron ore Rosond safety manager Andre-Kleynhans
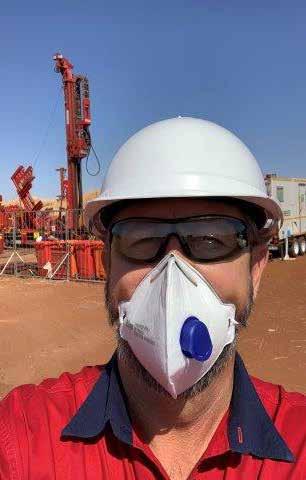
Drilling technology solutions provider Rosond of Midrand has celebrated one year Zero Harm at its diamond drilling operation at Kumba Iron Ore’s Sishen mine near Kathu in the Northern Cape. Senior Site Manager Clayton Coetzee attributes the achievement to close cooperation between department heads, line management, and HSE officers to continually improve standards.
“We always try to improve our processes and strive to make the working environment safer and easier to manage,” says Coetzee. Employee suggestions and input is encouraged, together with client interaction. “We are all in this together, and together we truly can make a difference.” Rosond Safety Manager Andre Kleynhans comments: “The biggest contributing factor to this achievement is that we are truly our sister’s and brother’s keeper, meaning we always look after each other’s safety and well-being.” A culture of caring and responsibility is inculcated on-site, which allows anyone at any time to stop somebody who is doing something unsafe, so nobody is injured.
“At the end of the day we all go home safe to our families,” says Kleynhans. He adds that the new drill rig technology Rosond has introduced at Kumba has played a major role in safe operations, especially in carrying out hazardous tasks such as handling drill rods, which is now automated. As a result, Rosond has successfully trained female drill rig team members at Kumba.
“We are very proud of our safety culture and aim to keep our employees safe at all times,” concludes Rosond MD Ricardo Ribeiro.
“We always try to improve our processes and strive to make the working environment safer and easier to manage.” – Clayton Coetzee, Senior Site Manager, Rosond
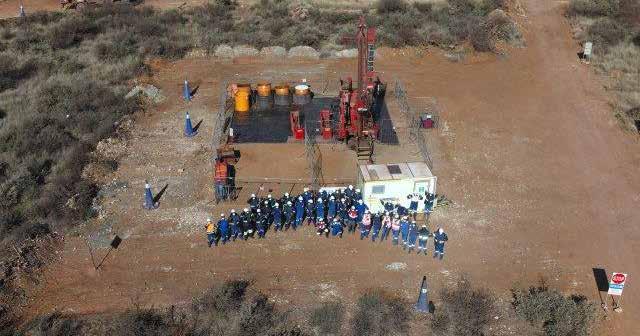
Rosond played a major role in safe operations at Kumba Rosond senior site manager Clayton Coetzee
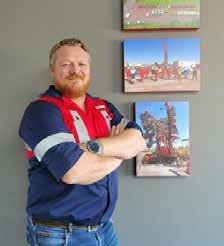
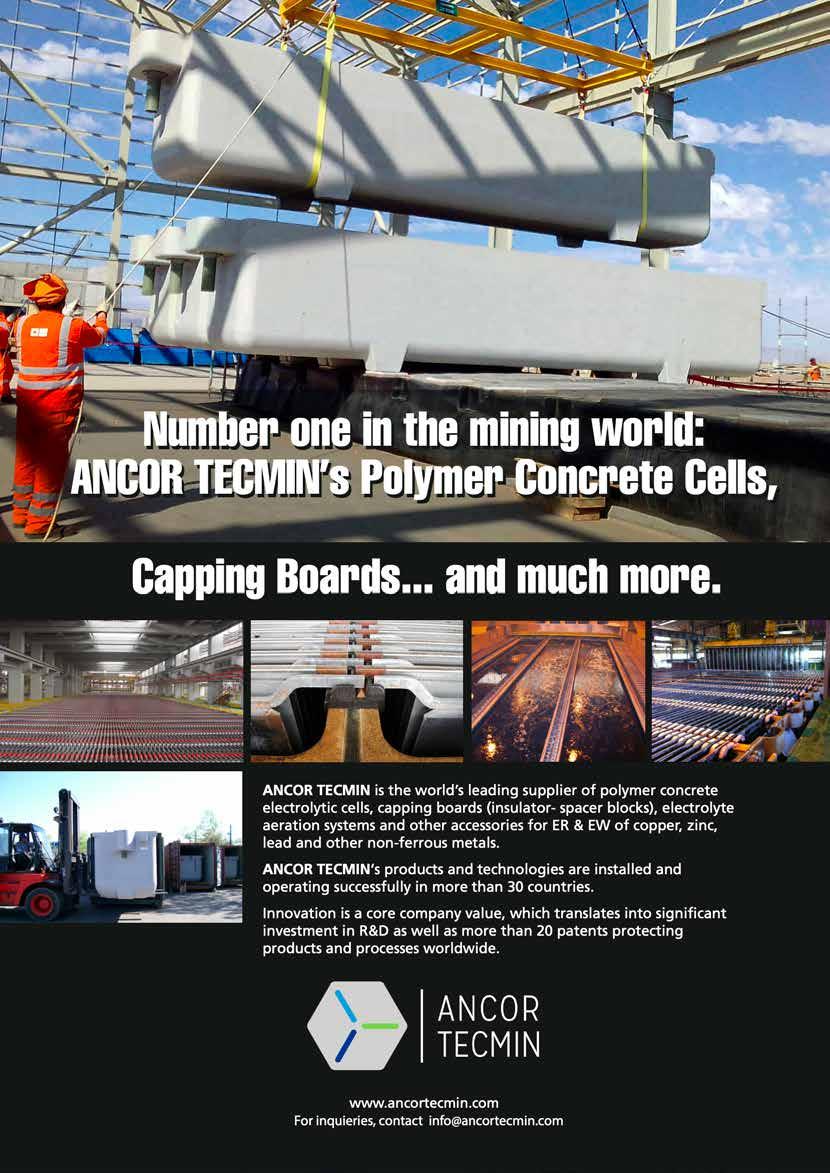
Metso Outotec to deliver key concentrator plant equipment to a copper mine in Africa
Kamoa Copper S.A. has selected Metso Outotec to supply key concentrator plant equipment to the company’s copper mining complex expansion in the Democratic Republic of Congo. The value of the order, which is not disclosed, has been booked in Minerals’ Q2/2022 orders received.
Metso Outotec’s scope of delivery consists of Planet Positive processing equipment, including energy efficient HIGmillTM regrind mills with polyurethane wear linings. The delivery also includes Larox® PF 60 Series concentrate filters and TankCell® flotation cells for the efficient recovery of valuables.
“One of the key missions for Kamoa Copper S.A. is to implement low-carbon technology to advance sustainable production of copper. Metso Outotec’s Planet Positive offering supports our customer’s ambition, allowing us to be a true partner for positive change,” says Charles Ntsele, Vice President, Minerals Sales for Metso Outotec in Africa.
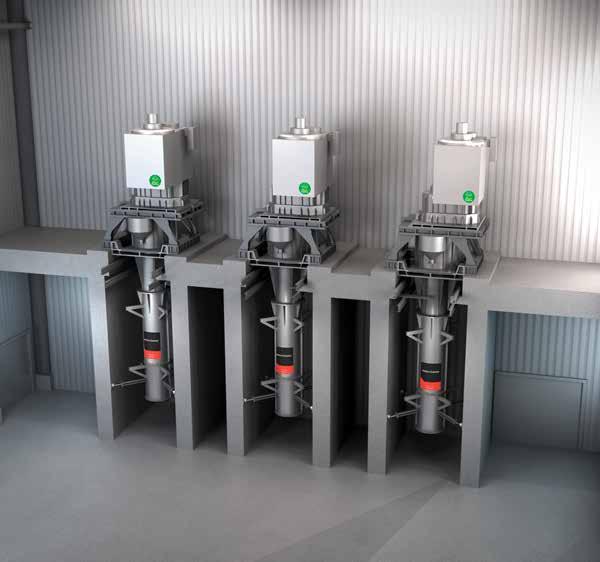
Metso Outotec to deliver Planet Positive PremierTM grinding mills to a copper mine in Zambia
Canadian First Quantum Minerals (FQM) has awarded an order to Metso Outotec for two very large horizontal grinding mills for the company’s copper mine expansion in Zambia. The value of the order, which is not disclosed, has been booked in Minerals’ Q2/2022 orders received.
Metso Outotec’s delivery includes two Planet Positive PremierTM grinding mills with a total installed power of 50MW. To meet the need for efficient and fast replacement of the lining systems, as well as ensuring a long wear life, the ball mill will be equipped with the Metso Outotec Megaliner™ and the SAG mill will be equipped with Metso Outotec metallic mill lining and a highperformance discharge system. FQM’s Kansanshi mine, located near Solwezi in the North-western Province of Zambia, is amongst the largest copper mines in the world and the largest in Africa.

First Quantum Minerals are currently working on its further expansion including a standalone 25Mtpa processing plant that will increase copper production substantially. Metso Outotec grinding mills provide advanced user-friendly operations, main bearing systems, high availability and ease of maintenance.
Visit our website to read more about Metso Outotec PremierTM mills and Metso Outotec Megaliner™ solution.