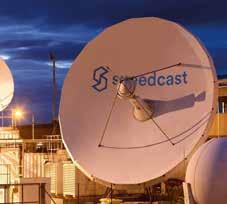
15 minute read
of mining for Africa
Hybrid satellite communications
Seamless Communications for Mining Operations Via Satellite
Advertisement
By Nick Barnes
It is hard to ignore the rise to prominence of satellite-terrestrial hybrid connectivity as one of the critical enablers of efficient communications in modern remote mining areas in the past decade. Interestingly, this is the face of other ‘tried and tested’ conventional techniques which enjoy wide usage. Satellite-terrestrial hybrid connectivity involves the combination of Very Small Aperture Terminal (VSAT), and terrestrial services, based on either Multi-Protocol Label Switching (MPLS) or Post Office Protocol (POP). With keen interest, it is hard to resist the urge to find out what is behind this phenomenon. When asked about what could be driving increase in the adaptation of satellite-terrestrial hybrid -enabled communications in a survey, providers of hybrid satellite communications packages more or less pointed to similar factors.
The need for reliable communications
The significance of satellite-terrestrial hybrid communications becomes better understood when one looks at the need for reliable communications to drive operations and how the satellite as a means fills void. Reliable connectivity gives decision makers in mining companies the ability to make effective and timely decisions. In particular, reliable communications serves a number of critical purposes in mining operations, mainly: • Enabling the connection of mines, which are located in remote areas, to the outside world as well as machine to machine networks; • Improving site safety and security; • Facilitating the provision of internet access.
Perfect fit for communications in mines
Providers of satellite-terrestrial hybrid communications, share the view that satellite would be perfect fit for the scattered nature of Africa’s mining operations, mainly due to the following factors: Short lead time; No need for infrastructure; and connection of scattered operations under a single platform.
i. No need for costly infrastructure
There is no need for time-consuming and frustrating process of developing land-based infrastructure. This makes satellite communications comparatively cost effective.
ii. Short lead time
By eliminating the need for costly landbased infrastructure, satellite offers the benefit of a short lead time. In this way, it enables a mining company to have efficient and cost-effective communications.
iii. Single management hub (no need for infrastructure)
Broadband internet, delivered through satellite, connects scattered mining operations together under a single management hub. This is possible through uniting high-capacity very small aperture terminal (VSAT)/MSS Satellite connectivity resources to provide a single, seamless network experience. For instance, through MPLS connection, a mine can be able to get satellite connectivity between production sites and hybrid satellite/terrestrial connectivity to its headquarters in the UK.
What mines would need
The service providers indicate that mines operating in remote areas with poor signal would need the following to fully exploit the benefits of broadband satellite internet: the assurance of more broadband, single provider for all terrestrial and hybrid networks, and most of all reliability. Most importantly, mine operators need the confidence of assistance, should there be any issue with connectivity.
More relevant and integral
If well deployed, multiple satellite networks and terrestrial connections, which act as the single point of contact for the entire network, through seamless communications, can achieve high end to end performance in any mining environment worldwide. What makes satellite communications all the more relevant is that currently mining is undergoing a revolution, with equipment automation becoming integral, and advanced communications is pivotal.
The world leader in industrial private LTE networks
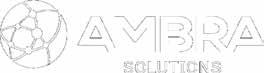
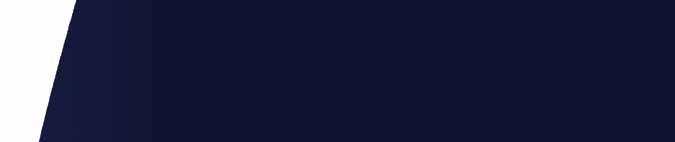
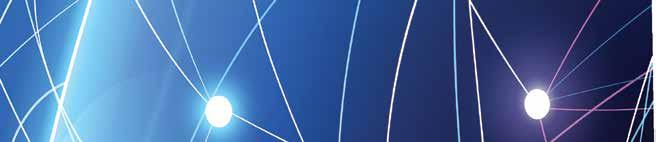
www.ambra.co sales@ambra.co
Transforming the future of mining for Africa

James Trevelyan, SVP, Enterprise and Emerging Marketing, Speedcast
Mining in Africa is now starting to recover from the global pandemic, with GlobalData predicting gold production in the western part of the continent will see a significant rise this year in growth. Therefore, it is imperative operators utilize the power of digital transformation to revolutionize their operations and bounce back as strongly as possible. Mining has long been an uncertain sector in Africa but coupled with the global economic downturn and the falling prices of metal and oil prices, it needs a drastic shift.
Technology is the answer
With mine sites vast and spread across a large area, whether open bit or below ground, the Connected Mine builds upon the essential communication needed for day-to-day operations. It layers digital systems and applications over the top to provide a complete digital transformation.
The systems put in place can be leveraged to boost productivity of both workers and resources. Sensors placed on mining equipment and other applications enable
huge amounts of data to be collected, which can then be sophistically analysed to reveal any operational bottlenecks and cost inefficiencies. Technology, such as autonomous haulage and drilling systems, has been shown to have an immediate impact, achieving higher utilization, resulting in more engine hours and more tons of material to be moved per day. Due to their programmed nature, tire life is also significantly improved with vehicle collisions and sidewall punctures being completely avoided. Analytics can also generate predictive maintenance schedules so equipment can be swiftly taken offline at a convenient time and serviced without causing the need for a major breakdown bringing operations to a stop.
Digital twin technology can transform how companies operate even further. Using data from every device, sensor and application within the mine, it is possible to create a digital replica which is kept up to date with data flowing in from the field in real-time. This enables any proposed changes or additions to the site to be tested with a great deal of accuracy before physical on site implementation. This technology is being adopted at a rapid rate, as operators save millions of dollars by eliminating any errors prior to installation.
Mining has long been one of the most world’s most dangerous professions. The Connected Mine drastically improves safety as the most hazardous jobs can be performed autonomously, keeping staff out of harms away. Meanwhile, work site surveillance provided via video CCTV systems and analytics play a key role in keeping employees safe, as unlike human supervisors, cameras and data processing platforms never sleep or get distracted.
The health of people living near the mine is equally important. The same surveillance and analytic capabilities enable mines to monitor their environmental impact and take pre-emptive action to prevent harm to nearby communities. Technology offers significant opportunities for mines across Africa to transform their operations and boost performance.
High-quality connectivity is essential
The Connected Mine can only be successful if there is robust, reliable connectivity. This places special requirements on the network and requires a fully managed service that can seamlessly integrate a mix of communication technologies, including microwave, Wi-Fi and satellite services. It also needs to be intelligent and able to dynamically select the best price performance at any time to avoid stranded capacity or transmission bottlenecks.
The network must also be able to deliver extreme uptime and be highly secure to protect the sensitive information that is always being transmitted. It also needs to support critical enterprise applications such as e-learning to remote management and have installation services, field maintenance and technical support accessible worldwide.
Incorporating private LTE solutions such as the Nokia Digital Automation Cloud (DAC), provided by Speedcast, will enable a private wireless network that can support every application and system operating within any mine, regardless of the environment or remoteness. To enable smart manufacturing, predictive maintenance, remote operations and machine-to-machine communication, a high-quality network is essential.
Success for the long term
With mining starting to recover from COVID-19 in Africa, it is now a good time for operators to embrace digital transformation and the benefits it can bring. With remote management more of a priority now than ever before, it is imperative they look at incorporating the Connected Mine to totally rejuvenate their processes with increased productivity and safety.
To do this successfully, they need solutions that guarantee high quality communications and connectivity to manage all of the applications running at the mine and ensure access to the outside world for vital information, entertainment and news. This will protect the recovery of Africa’s mining industry with technology affording greater efficiency and return on investment alongside all the benefits remote management, automation and detailed insights can provide. The operators that utilize technology today, will guarantee their success for the long term and be one step ahead of their competitors at what is a crucial time for the industry.
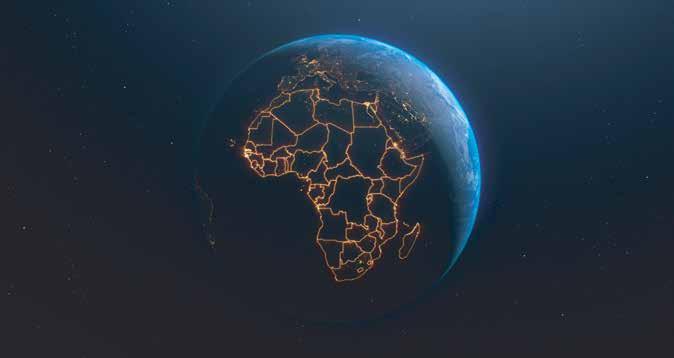
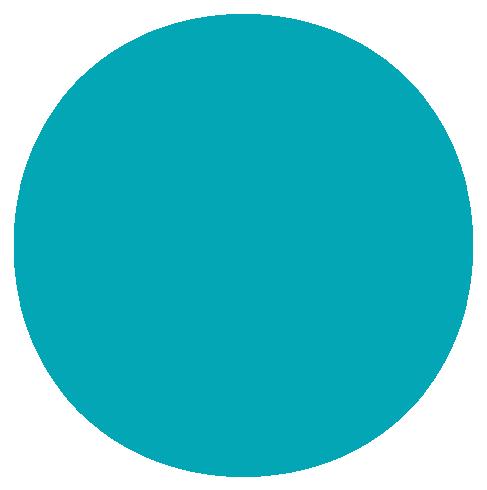
Amos-17 C-Band
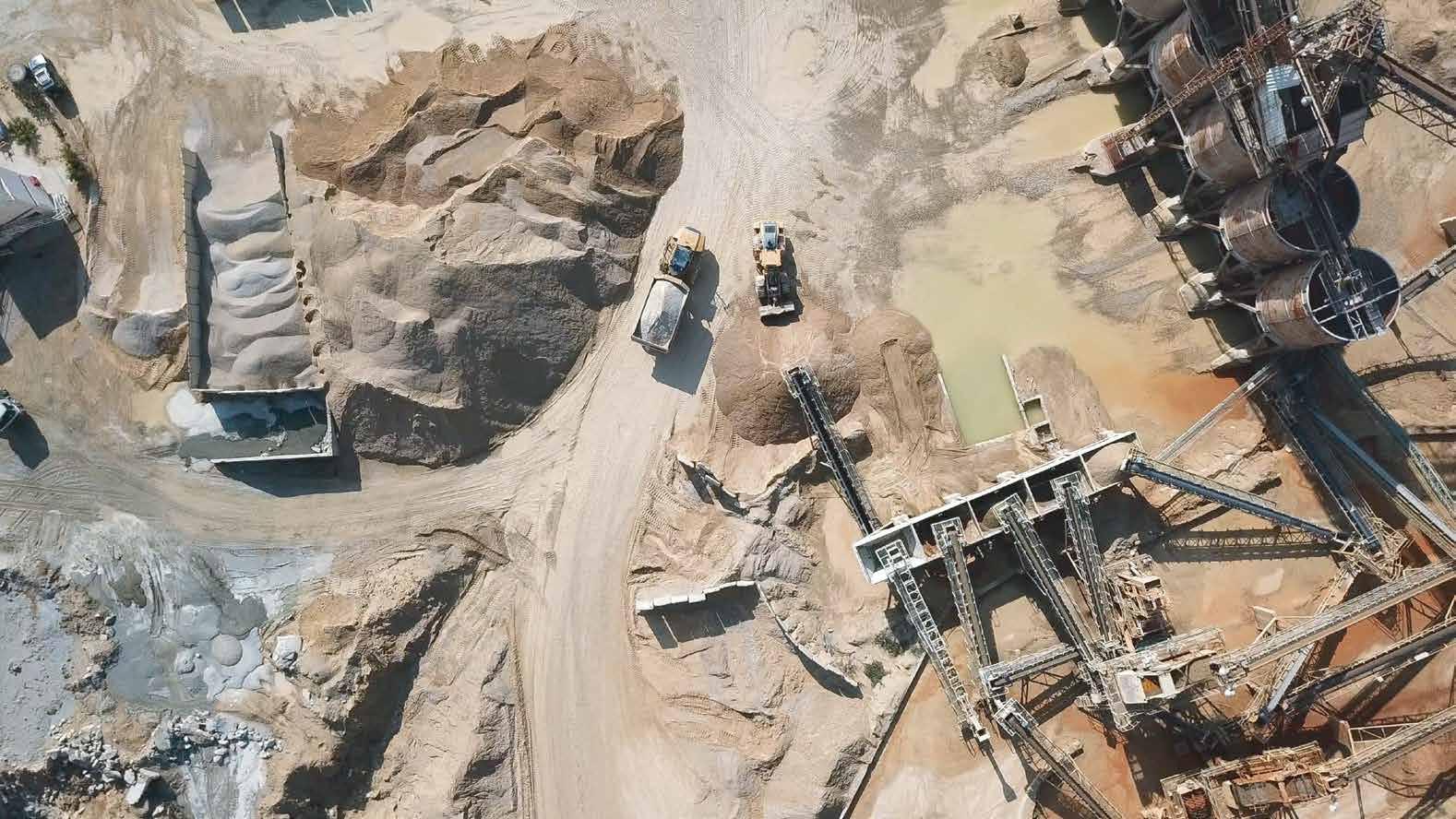
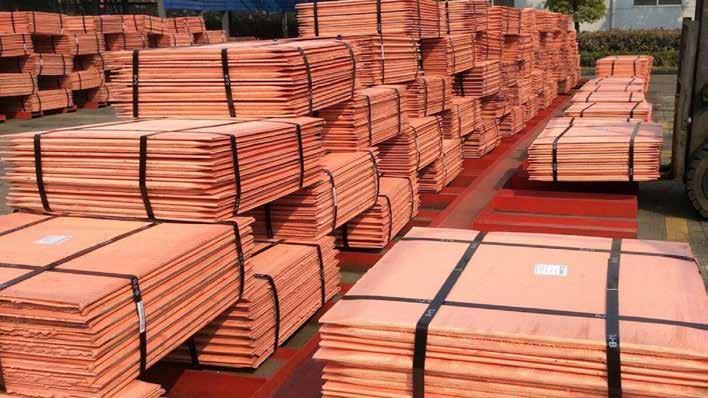
Copper, Africa’s oil? transition, as it is used to manufacture batteries for electric vehicles. Another significant advantage, for
Until now, professionals in the mine, according to this specialist, there companies based in the African copper mining sector thought that the are not enough sites in operation or belt, is that they have easier access charismatic Robert Friedland, in the pipeline to meet the inevitable than South America to Asian markets CEO of Ivanhoe Mines, which is explosion in demand. – especially China – thanks to logistics developing the Kamoa-Kakula copper megaproject in the DRC, was simply looking out for his best interests when he presented copper as the ‘metal of the The irony of it all “The environmental regulations for producing copper are also becoming that are geared towards the major Indian Ocean ports of Dar es Salam and Durban, from where ore is shipped. future’ at his investor conferences. increasingly strict, which makes it more expensive to produce,” he says. Even Finally, the cost of smelting ore – which Copper is currently trading at around though the current price is higher than transforms copper concentrate into pure $9,500 per tonne in London, which is in the past, it is not enough to make ore – is currently very low, which benefits already its highest price in a decade. A all mines profitable, which has led to a African producers who do not have year ago in April, it was selling at below decrease in investment in the industry. foundries on site. They can therefore $5,000 per tonne, the same price it was The Swedish analyst also notes the send concentrate to China to process going for in November 2015 and October irony of having, on the one hand, at a lower cost. “It is currently more 2016. financial partners who are reluctant to profitable to invest in mine expansion support copper mining on the grounds than in foundries,” says Löf.Anton Löf, a metals market specialist at of environmental and social risks, while the Stockholm-based RMG Consulting, at the same time championing an energy agrees for the most part with Goldman transition that requires its widespread Sachs’ analysis. “The transition to a low- use. carbon economy cannot happen without copper, which is both a key electrical According to Löf, the African copper belt, conductor – far more efficient than other which straddles the DRC and Zambia, metals such as aluminium – and a crucial should be the main region of the world component for solar and wind power – with South America to a lesser extent plants, electric vehicles and batteries, – to benefit from renewed interest from as well as energy-efficient buildings,” he investors. Many of the African deposits – says. But while it takes about 10 years to particularly in the DRC – contain not only get a copper project off the ground and copper, but also cobalt, which is another three to five years to expand an existing mineral that is crucial to the energy

Industrial degreasers for mining equipment
Informed Degreaser Choice, Optimum Equipment Performance
Oil and industrial lubricants can be a double-edged sword - good when they keep machinery operating and production going, on the one hand; and on the other bad (a liability) when greasy surfaces attract dirty and contaminants. A suitable degreaser has to be used to clean the affected areas. Decisions on purchasing a product have to be informed by correct data on exact needs.
By Nick Barnes
With mining activity truly on the upswing, it is unavoidable for unwanted grease, tar, oils, hydraulic fluid, cutting fluids, corrosion inhibitors and other greasy build-up to get stuck on engine components or equipment. Cleaning using heavy-duty degreasers is a technique commonly used in mining. Nonetheless, as it has been established, the quality of the degreasers used can have a huge bearing on effectiveness of the cleaning process. Unfortunately, there are many implications for using cheap or unproven products – at best, a poor cleaning job, or more time spent on cleaning, resulting in loss of productivity due to equipment unavailability, at worst. And so, consistently, hard but rational decisions that are good for business have to be made. not least at a time when Environment, Social and Governance (ESG) has become part of the DNA of business operations.
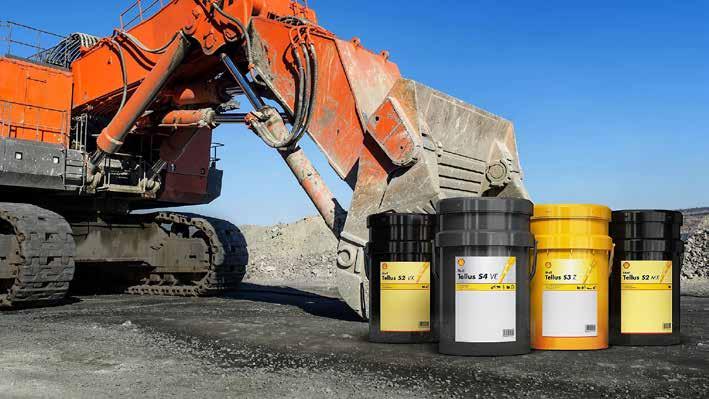
First Mining DRC - Zambia sifted information from product managers of suppliers of heavy-duty degreasers to mines in Zambia and the Democratic Republic of Congo to find out what properties of products would perform better cleaning job in contemporary mining conditions.
Eventually, what emerged is that legislation obligates mine operators to use high-quality industrial degreasers that are both safe (do not contain elements that can cause harm to employees handling them), as well as environmentally friendly (as lubricating grease contains additives and petroleum oils generally considered contaminants).
So, environmentally-friendly degreasers are preferred or highly recommended,
Degreasing a necessity, not a costly distraction
Before delving into what would make good degreasers for the current mining conditions it is important to ask: Is degreasing a distraction to production a mine operator can do without?
Of course, when production is at its peak, it is very tempting for plant engineers with an eye on increasing productivity to ignore the grease and grime on components, nonchalantly ‘business as usual’. Routine maintenance sacrificed in hot pursuit of profit. However, inevitably, there is a price to pay, sooner or later.
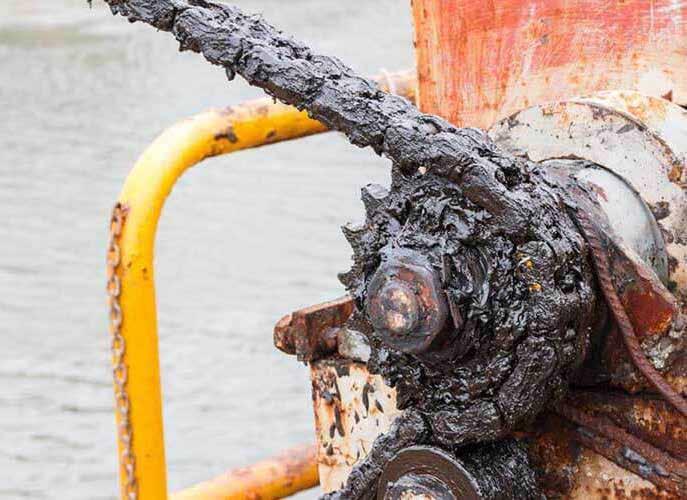
Effects of grease and grime on equipment
When small bits of grease and grime are ignored, and left to accumulate, they create conditions for a myriad of challenges that, in most cases, are difficult to address.
These challenges include and may not be isolated to: • Engine or hydraulic leaks going unnoticed; • Contaminants causing workplace safety hazards like fires or injuries to operator; • Slowing down machinery, causing abrasion that degrades performance of equipment like pumps as metals gets scored; • Reduce the value and life of equipment; • Inspection failures and fines, even legal action; • High energy consumption. An area which Peter Crossen, VP of the Maintenance and Partsmaster
Innovation Platform at NCH Europe, in the journal, Engineer Live, observes: “Something seemingly insignificant as 0.25mm of dirt on a heating exchange coil can lead to a 40% increase in electricity usage, which in turn drives up operation costs for businesses.”
Quality of degreasers (recommended product properties)
That is why the quality of degreasers used is of paramount importance. In general, the following are cited as recommended properties of degreasers for mine operators: • Ability to remove most stubborn grease and grime and easy to rinse away; • Safe to use on all kinds of metals, aluminium and zinc, and all paintwork • Biodegradable, non-toxic and nonhazardous to humans, animals and aquatic life • Non-flammable and unable to support combustion • Storage and handling in ambient temperatures and atmospheric pressures within buildings or roofed outdoor storage.
Options - Solvent or Water-based?
Armed with this information, an informed decision on whether to use solventbased or water-based degreasers has to be made. The assumption is that environmental considerations, a high priority in current conditions, would render water-based degreasers as the obvious choice. However, how environmentally friendly a degreaser is cannot be the only factor that to influence a decision. So, it is best to look at the merits and demerits of both of these two options. Of course, solely on environmental friendliness grounds, solvent degreasers, which use chemical formulations, won’t be recommended. Solvent degreasers contain volatile organic compounds which dissolve grease and remove stubborn contaminants from parts and equipment. However, the volatile organic compounds (VOCs) they contain are regarded as extremely hazardous.
For instance, if inhaled, the fumes the degreasers produce are harmful. Also, many solvent degreasers are flammable.
From an environmentally friendliness perspective, this leaves water-based degreasers as an alternative. Nonflammable, water-based degreasers use latest surfactant technology to emulsify the greasy soil; the penetrating agents increase the speed of degreasing. From a safety perspective too, available as concentrates, water-based degreasers are non-flammable and do not produce harmful vapours. This would leave, water-based degreasers as the only option to be used in cleaning equipment.
Nonetheless, an interesting fact emerged - water-based degreasers may not be the suitable for all equipment. They are not recommended for electronic and electrical applications. Instead, it would be advisable to use solvent degreasers. The fast evaporation of solvent degreasers allows electrical equipment to be back up and running sooner. However, as far as regulatory compliance goes, the use of low Volatile Organic Compounds (VOC) would get a thumbs up any day.
Decisions, decisions, decisions
The decision about a degreaser to invest cannot be made at the whim. Careful thought has to go into it as it is money being spent on a suitable consumable, nothing should be taken for granted. Extensive research should be made when shopping around to select a product carefully. It would be even more convenient to contact a maintenance solutions specialist. An informed decision can result in improved energy efficiency, reliable operation and minimal production cost. They create a safe working environment, reduce maintenance costs and manpower requirement.