
40 minute read
for Safety and Control
SAFETY
DEGREASER
Advertisement
PREPSOL is a product of ALLIJAM, a South African company based in Johannesburg. We manufacture and distribute motor vehicle, domestic and industrial cleaners throughout Africa.
Prepsol is pH neutral, making it safe for the user, while reducing the risk of corrosion on metal, paint, seals, stickers and other components.
It is safe to use on canvas, carpets, stainless steel, aluminium, chrome, brass, painted and bare metal, plastic, all stone, drains, seals, gaskets, and rubber.
APPLICATION
Apply through a pressure washer, by brush, broom, mop or trigger spray.
O
UR flagship product TM (registered trade mark 81/7763) has been specifically formulated to clean away mud, grease, oil and grime.
The first water-based degreaser developed in South Africa, it is an industry benchmark cleaner developed specifically for the mining industry, and is an efficient, environmentally friendly product.
This renowned all-purpose degreaser is gentle but effective, making it ideal for use across many different applications. factories, buildings, workshops, offices, trucks and vehicles, equipment, and even overalls.
PREPSOLS MANY OTHER DEGREASING APPLICATIONS INCLUDE:
ENGINES VEHICLES MOTORCYCLES ENGINE PARTS OILY FLOORS AND SPILLS BICYCLES TRACTORS CRANES WALLS UPHOLSTERY OVERALLS TOOLS BOATS AND MANY MORE…
USES
Prepsol ccan be used on most washable surfaces at mine sites, from large mining trucks, electric rope shovels, rotary drill rigs, rock drills, motor graders, large wheel loaders, draglines, wheel tractor scrapers and underground mining loaders.
It is also the optimal degreaser for
SALES
Bulk sales available for wholesalers and retailers, with smaller-quantity sales direct to consumers.
Allijam’s considerable expertise is available to assist with purchasing, delivery and training on the product, to ensure clients enjoy the full benefit of its potential.
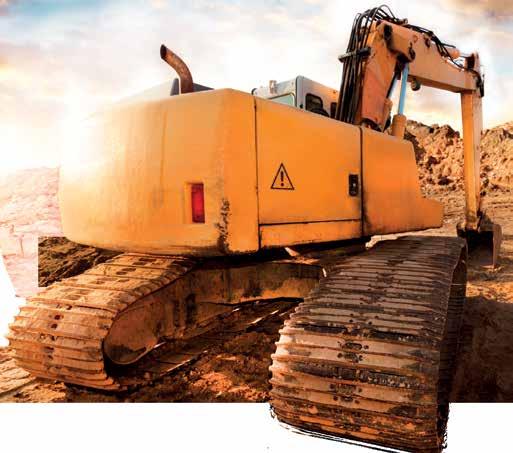
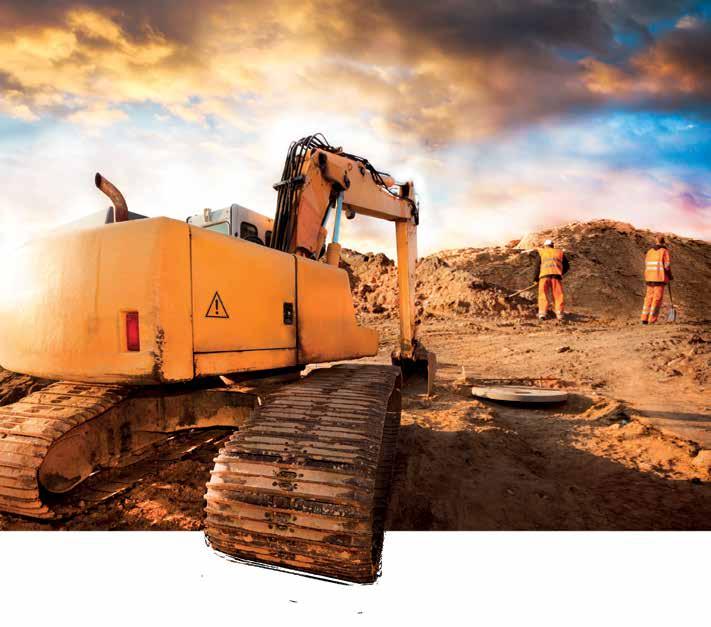
Contact us for more information,
we look forward to doing business with you.
Accurate temperature measurement in high temperature furnaces
Real-time, Accurate, Continuous Monitoring for Improved Furnace Performance
Via the data, they gather through real-time, accurate continuous monitoring, thermal imaging cameras enable predictive maintenance of furnaces, ensuring long periods of availability and optimal performance.
By Nick Barnes
Optimal process monitoring and control is a tried and tested approach to increasing equipment output in mining. In the contemporary atmosphere, it could not have been more relevant – the cost of ore extraction is escalating, squeezing profit margins. And so, to offset this trend, it makes businesses sense for mine mining companies to invest in process monitoring and control techniques that will enable them get more value from their ore in mineral processing. This is most especially, in when it comes to monitoring systems for refractory-lined furnaces and rotary kilns, which always need high accuracy continuous temperature measurement.
Traditional techniques out of kilter
Certainly, traditional processing monitoring and control techniques, inherent with their limitations, would be out of kilter with the current requirements. Conveniently, infrared thermal imaging camera systems, which have emerged as a practical alternative, are filling the void, based on ongoing trends.
Switching from traditional to thermal imaging monitoring
One would ask: How has thermal imaging cameras entered a space where the primary choice has been traditional process monitoring and control techniques? Specifically, why is industry jettisoning the ‘tried and tested’ method shifted to thermal imaging cameras? Recently, when contacted, business development managers from some of the leading providers of thermal imaging cameras in the game, who count mining companies among their major clientele, were eager to share their insights on factors driving the increase in demand for their products. The information they provided is compelling. While there are differences in wording, it points to common factors that render the thermal cameras preferable to traditional techniques with reference to contemporary demands. At least based on the client’s feedback, the thermal imaging cameras, they concur, improved furnace availability and output. The relevance and convenience of thermal imaging cameras can be appreciated better when first analysing the gaps in the traditional techniques and how capably thermal imaging cameras fills them.
Traditional approach
The traditional approach of monitoring furnace process and control involves cutting open refractory-lined furnaces and kilns to view critical areas. Unfortunately, this method does not always produce the desired end. Most often, this results in significant heat loss, as well as the debris entering the opening.
In addition, visual inspection using a camera can take hours to complete. Typically, the visual cameras used do not provide continuous temperature readings. Even more, instances of failure or loss of connection thermocouples cannot be ruled out.
Filling the gap As an alternative, thermal imaging, cameras fill the gap, addressing drawback of traditional methods by providing continuous high-accuracy temperature measurement for process monitoring and control applications in furnaces. With the camera, operators are able to measure inside high temperature furnaces and acquire high-definition images. The camera is installed through a hole bored in the outer refractory wall, which is then sealed.
Through a single high-resolution image, the camera provides real-time, accurate, temperature measurement and monitoring, which is delivered though a high-speed digital connection. It is able to measure product, refractory and heat transfer surfaces from temperature ranges 600 to 1800oc. Besides, there is no interference from the hot atmosphere and furnace gases. With the data gathered, streamed online, operators are able to optimise furnace temperature.
What is more, with advanced control software, simultaneous data acquisition from multiple thermal imaging cameras, additional analysis, archiving, or integrating with the plant’s local network can be done. Accurate data analysis, in addition to automated alarm outputs and control, alert the user in the event of any problem.
Valid business case
Clearly, there is a valid business case supporting the deployment of thermal imaging cameras in the area of continuous monitoring inside furnaces.
This is especially in three areas: 1. The impact of furnace failure, due to inadequate monitoring, can be costly, prompting unbudgeted replacement and repair expenditure.
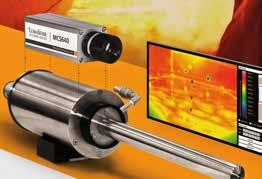
This is without mentioning downtime to processes and the loss of production caused. Thus, the role of thermal imaging cameras in providing critical insight for failure prevention and asset management is central. Specifically with the information gathered by the furnace camera on the thermal situation enables the operator to perform the following:
• Determine whether or not temperature sensors need to be exchanged: • Indicate If the temperature of the piping is within acceptable ranges; • When to raise productivity: and • Whether the burner needs adjustment or cleaning. Ultimately, through monitoring and controlling process temperature uniformly, the life of a furnace can be extended. 2. Thermal imaging cameras also enable energy efficiency savings. 3. Enabling process control optimisation. 4. As the monitoring is done remotely, it removes personnel out of harm’s way.
Application engineering teams and customisation
The thermal imaging cameras may employ state of the art technology but the reality is that every furnace has unique requirements. Thus, bearing this in mind, application-engineering teams from manufacturers are able to customise the cameras to the operators’ requirements. This is common in a number of areas. For instance, use of spectral filters to prevent the burning firing interfering with flame image visibility. In most cases, a spectral filter is used to make flame visible. In addition, some operators do request, the use of additional systems, where a single system does not suffice. Should additional precautions be deemed necessary, a camera enclosure can also be equipped with pressurised air or water for better cooling or be mounted on an automatic retraction system. Customisation is also done in other areas, depending on client requirements.
Robust enough to withstand high heat
The most outstanding feature, as manufacturers claim, is robustness to withstand challenging conditions experienced on mine sites. They point to several features. Most prominent is the protective enclosure, which allows the camera to withstand the high heat and measure temperatures through the combustion gas and flames. The cameras are available in a range of housing dimensions and mounting options.
Metso Outotec launches robust camera solution for smelting furnaces to increase safety and availabilit
Metso Outotec is launching a robust Furnace Camera to reduce or even eliminate the need to power off or cut the feed to inspect the furnace. Operators can safely monitor conditions inside the furnace in real time and react immediately to situations that would otherwise not necessarily be detected. The furnace camera is a fully integrated solution that is fast and easy to install into new or existing furnaces. “The Metso Outotec Furnace Camera is part of our extensive range of smart digital tools designed to support customers by helping them to increase safety, improve efficiency and availability, and reduce costs in their pyrometallurgical processes,” says Tapani Keronen, Product Manager, Digital Solutions, Metso Outotec.
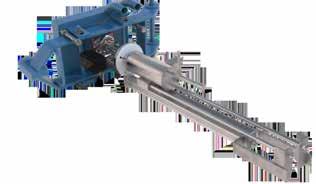
An intelligent user-friendly system
Real-time monitoring of the furnace enables operators to identify potential issues, like water leaks, and to take action to prevent damage. The video feed provides visibility to the condition of internal furnace components, such as electrodes and material feeding. The camera can measure accurate temperature values from user-specified locations and help the user to find hot spots. Additionally, the operator can identify refractory wear from camera images. Image clarity is not affected by fumes or dust. The automatic retraction function protects the camera in case of a break in utilities supply. Video, snapshots, and historical trend data can be viewed on the control-room display or used for later analysis.
Metso Outotec supports customers with the commissioning process and provides training for operators and plant management to ensure maximum benefit from the solution. Technical support is also available via an optional remote connection service.
The Furnace Camera is part of Metso Outotec’s Planet Positive offering.
Key benefits of the Metso Outotec Furnace Camera
• Improved operational safety and reduced need for personnel to work in harsh environments • Improved furnace availability due to continuous monitoring without production disturbances • Faster response to abnormal situations, such as water leaks, electrode breaks, or hot spots • Pre-tested solution with bolt-on design, enabling quick and easy installation • Significantly lower operating costs compared to standard camera solutions due to effective cooling system

Operating your process blindfolded?
It is incredible to imagine how subjective and fragmentary the information is that operators have of what is happening inside their furnace walls. Needed data is gathered from various separate measurements (temperature, pressure etc.) from which the current situation and optimal process values should be deducted. Many times, this leads to straightforward guessing. Fast, unexpected changes in the process or related equipment could even lead to dangerous circumstances. In such cases, reaction time and correct actions are crucial. However, it is an extremely challenging task for the operator to interpret the numeral data and evaluate appropriate operation procedures in a limited time frame. Is it time to take off the blindfold?
Finnish quality
Sintrol is a Finnish company specialized in process measurements, analysis, and safety equipment with a long history of providing a full ecosystem of imaging solutions for process industry worldwide. Whether it is systems consisting of thermal cameras or temperature scanners, customer satisfaction has always been first class. Specialized in high-temperature installations, the Sintrol Vulcan furnace cameras have become a solution relied upon in forest and metal industry providing impeccable support for process safety and control.
Through real-time monitoring of process conditions, operators can swiftly react to unpredicted and potentially dangerous situations. If a picture is worth a thousand words, a video feed is worth a thousand parameters. In addition to visual data, cameras are able to provide comprehensive temperature readings, enabling the operators to have control over their processes unlike ever before.
Care-free solution for safety and control Sintrol camera systems are always custom designed to match your specific needs. Even though we deliver a variety of camera models and a wide range of related options, we and our worldwide support network will make sure that an optimal setup is delivered, installed, and taken care of. Sintrol is committed to provide full service all the way from design and commissioning to service and support.
Cameras are designed to withstand extreme conditions and maintain clarity even in dust or fume afflicted installations. The intelligent safety system prevents it from overheating in case of extremely volatile temperatures. As a result, operators are able to enjoy a clear on-line video feed from furnace, boiler or other process from the comfort of the control room.
Trusted technology in a variety of applications
The history behind Sintrol’s camera technology reaches way back to early 1970’s. During this time the hightemperature cameras have proven their necessity in a myriad of installations.
Providing both visual and IR cameras, feasible applications for Sintrol Vulcan equipment are countless, and as a result Sintrol has become the trusted camera partner of Finland based OEM’s in forest and metal industry.
Key benefits
Safety and control
• Detection of hotspots and leaks • Visual control over process • Temperature surveillance • Continuous and real-time
Smart software
• Automatic alarms based on temperature • Range of options available (e.g. analog outputs and OPC) • History trends
Low maintenance, ease of use • Final design in collaboration with
Sintrol experts • Minimal to none mechanical maintenance • Robust design for extreme conditions • Worldwide support available
Contact Sintrol for more information: info@sintrol.com, +358 9 56 17 360 www.sintrol.com
The future of rock reinforcement:
locally ancored self-drilling bolts
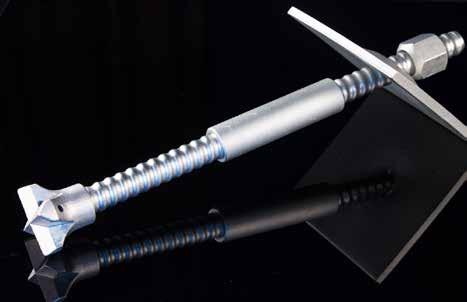
Mines are increasingly digging deeper to access unexploited minerals, and deeper mines present a whole host of challenges, including rockbursts, large deformation, squeezing and creeping rocks. With this in mind, rock bolting and strata reinforcement is more important than ever, and it may not be easy to rely on traditional methods. Normet is an innovative company whose dynamic D-Bolt has not been matched, despite attempts from the competition to reverse engineer a similar product. However, it is Normet’s range of self-drilling dynamic bolts (SDDB) that really has the future in mind.
A challenge with using traditional bolts is that a hole must be drilled before the bolt and grout are inserted, and with rock that deep being under so much stress, there is the risk that these drilled holes will not stay open. Additionally, fractured ground allows for water ingress, which can dilute the cement grout or polyester resin being used. Normet’s SDDBs overcome this problem as they can be drilled directly into the rock, making them ideal for fractured ground or unstable strata. According to Martin Petranek, director of products and production for rock reinforcement at Normet: “Using a selfdrilling bolt does half of the installation for you, and then all you need to do is use a pumpable thixotropic grout or resin to bond the bolt. At Normet, we offer hydrophobic sodium silica-based resins, so it won’t be diluted or flushed by water ingress, and is also able to flow through cracks to consolidate the rock.”
The deformable resin is able to absorb some of the energy from the rock, further reducing the risk of bursts. As for the bolts themselves, the installation of these selfdrilling bolts can be fully mechanised, so workers can stay back at a safer distance. “You can use bolting machines that are able to install these bolts, and the operator is protected in ROPS/FOPS certified cab. Major mining manufacturers are already looking at developing new equipment for installing self-drilling bolts, so it’s really what the future demands,” Petranek says.
With other competitors entering selfdrilling bolts into the market, what is it about Normet’s portfolio that sets it apart? Petranek explains: “Where Normet is ahead, is that we offer variety with these bolts. We have two basic designs based on the material property, and we have several models made of these two basic models that differ in shape. We have the bolt made of seamless tube and a thread on the outer side that is rolled evenly on the left and the right of the tube. These bolts are commonly either 1.5m, 2m, 2.4m or 2.5m, and they can be extended with a coupling. By offering an extendable solution, we are able to substitute cable bolts if you need to drill much deeper into the rock.
“We are not limited to any size, it’s very customisable. Bolts can be tailored to customer demand, for length, diameter, even the length of the threaded section. We can also customise what kind of drill bit they want to use, as bolts will need to be able to drill a hole that is bigger than a coupling if the customer is doing extended drilling, but still kept as small as possible to limit how much grout that you need.”
It is not just the customisable design that sets Normet’s locally ancored selfdrilling hollow rock bolts apart from the competition. Normet has paid close attention to using materials that are best suited for mining applications.
“Conventional rock bolts are usually manufactured from ordinarily construction steels, which is not really ideal. It has certain load-bearing parameters, and is fine for applications such as concrete reinforcement where it is pretensioned, but for mining there are challenges with the impurities in the steel. The steel is rolled in just one direction when it is manufactured into a bar, and the resulting impurities can make it very weak because of the microscopic bubbles in the steel. The material that we use for dynamic bolts is homogenised, which requires a different treatment to get a uniform structure and is much stronger.”
Ventilation and Cooling in Underground Mines

Underground mine ventilation is particularly important in situations where heavy machinery is in operation, as plants such as drills and long haul dumps have a huge impact on humidity and temperature. On top of this, extraction can release gases which are harmful to staff working below ground. For example, radon, which is often present in uranium mines, is poisonous if inhaled.
The main objective of mine ventilation is the provision of sufficient quantities of air to all the working places and travel ways in an underground mine to dilute to an acceptable level those contaminants which cannot be controlled by any other means. Where depth and rock temperatures are such that air temperatures are excessive, mechanical refrigeration systems may be used to supplement the beneficial effects of ventilation.
The Mine Atmosphere
The composition of the gaseous envelope encircling the earth varies by less than 0.01% from place to place and the constitution of “dry” air is usually taken as 78.09% nitrogen, 20.95% oxygen, 0.93% argon and 0.03% carbon dioxide. Water vapour is also present in varying amounts depending on the air temperature and pressure and the availability of free water surfaces. As ventilation air flows through a mine, the concentration of water vapour may change significantly and this variation is the subject of the separate study of psychrometry. To define the state of a water vapour and dry air mixture at a particular point requires the three measurable independent properties of barometric pressure, dry bulb and wet bulb temperatures.
Ventilation Requirements
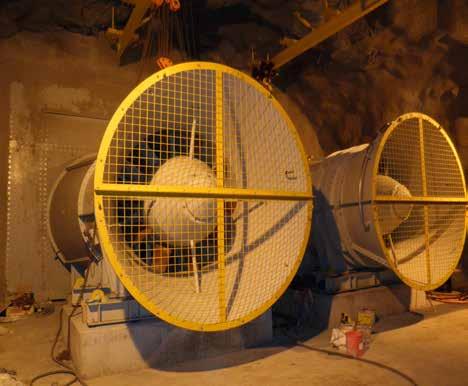
The contaminants to be controlled by dilution ventilation are primarily gases and dust, although ionizing radiations associated with naturally occurring radon may present problems, especially in uranium mines and where the background uranium concentrations of the host or adjacent rocks are elevated.
The amount of air required for dilution control will depend on both the strength of the contaminant source and the effectiveness of other control measures such as water for dust suppression or methane drainage systems in coal mines.
The minimum dilution air flow rate is determined by the contaminant requiring the greatest dilution quantity with due cognizance of the possible additive effects of mixtures and synergism where one contaminant can increase the effect of another. Overriding this value could be a minimum air velocity requirement which is typically 0.25 m/s and increasing as air temperatures also increase.
Diesel-powered equipment ventilation
In mechanized mines using dieselpowered mobile equipment and in the absence of continuous gas monitoring, exhaust gas dilution is used to determine the minimum ventilation air requirements where they operate. The amount of air required normally ranges between 0.03 and 0.06 m3/s per kW of rated power at the point of operation depending on the type of the engine and whether any exhaust gas conditioning is being used.
Continuing developments in both fuel and engine technology are providing lower engine emissions while catalytic converters, wet scrubbers and ceramic filters may further reduce the leaving concentrations of carbon monoxide/ aldehydes, oxides of nitrogen and diesel particulates respectively. This helps in meeting increasingly stringent contaminant limits without significantly increasing exhaust dilution rates. The minimum possible dilution limit of 0.02 m3/s per kW is determined by the carbon dioxide emissions which are proportional to engine power and unaffected by exhaust gas conditioning.Diesel engines are about one-third efficient at converting the energy available in the fuel to useful power and most of this is then used to overcome friction resulting in a heat output which is about three times the power output.
Even when hauling rock up a decline in a truck, the useful work done is only about 10% of energy available in the fuel. Higher diesel engine powers are used in larger mobile equipment which require bigger excavations to operate safely. Allowing for normal vehicle clearances and a typical diesel exhaust gas dilution rate of 0.04 m3/s per kW, the minimum air velocities where diesels operate average about 0.5 m/s.
The provision of suitable thermal conditions to minimize the dangers and adverse effects of heat stress may require mechanical cooling in addition to the ventilation necessary to control contaminants. Although the applied heat stress is a complex function of climatic variables and physiological responses to them, in practical mining terms it is the air velocity and wet bulb temperature that have the greatest influence.
The first mine refrigeration system was installed at Morro Velho, Brazil, in 1919. Since that date, the growth in worldwide capacity has been linear at about 3 megawatts of refrigeration (MWR) per year until 1965, when the total capacity reached about 100 MWR. Since 1965 the growth in capacity has been exponential, with a doubling every six or seven years.
The development of mine refrigeration has been influenced both by the air conditioning industry and the difficulties of dealing with a dynamic mining system in which the fouling of heat exchanger surfaces may have profound effects on the amount of cooling provided.
Initially, the refrigeration plants were installed on surface and the mine intake air was cooled. As the distance underground from the surface plant increased, the cooling effect was reduced and the refrigeration plants were moved underground closer to the workings.
Limitations in underground heat rejection capacity and the simplicity of surface plants has resulted in a move back to the surface location. However, in addition to the intake air being cooled, chilled water is now also supplied underground. This may be used in air-cooling devices adjacent to the working areas or as the service water used in drills and for dust suppression.
Quietaire Australia’s Cooling Solutions
Quietaire Australia offers cost effective and efficient solutions for air circulation, air scrubbing, dust suppression, humidification and cooling large areas, staff or machinery quickly and efficiently. Quietcool Portable Evaporative Coolers are a cost effective and efficient solution for air circulation, air scrubbing, humidification and cooling large areas, staff or machinery quickly and efficiently.
Regular fans simply circulate the existing air, same humidity at the same temperature. The Quietcool takes that same existing air, combines it with evaporating water, which dramatically lowers the temperature. Our fan blades are designed to spread the air as it leaves the unit, pushing away from the unit in a ‘V’ formation, cooling a broader area the further away you move from the unit. Pre cooling can increase the efficiency of equipment and machinery that runs hot such as generators which means they run less and consume less energy. Also, a great solution for cooling machinery and equipment after shut down. Regular fans simply circulate the existing air, same humidity at the same temperature. Evaporative Coolers and Misting Systems takes that same existing air, combines it with evaporating water, which dramatically lowers the temperature.
A wide array of applications benefit significantly from artificially controlled humidity levels. Greenhouse humidity systems promote faster plant growth and increases plant quality and yield. Increasing the relative humidity in wine cellars reduces the evaporation of wine through the barrels. Correct humidification of fresh fruit and vegetables, keeps the produce hydrated and slows the natural deterioration process. In some worksites, the control of dust is an ongoing problem.
There are many health risks related to respiratory complaints, visibility issues and equipment deterioration. Misting systems can effectively suppress dust by producing a consistent mist of uniform droplets that captures airborne dust particles and natural gravity pulls them towards the ground. The cooling pads in evaporative coolers also act as an air scrubber, removing dust and debri from the air that passes through the unit.

TOMRA digitization in mining
TOMRA is tapping the potential of digitalization with a constantly expanding offer of digital services to help mining operations improve their efficiency and profitability – most recently with the introduction of the new augmented reality tool for remote assistance, TOMRA Visual Assist.
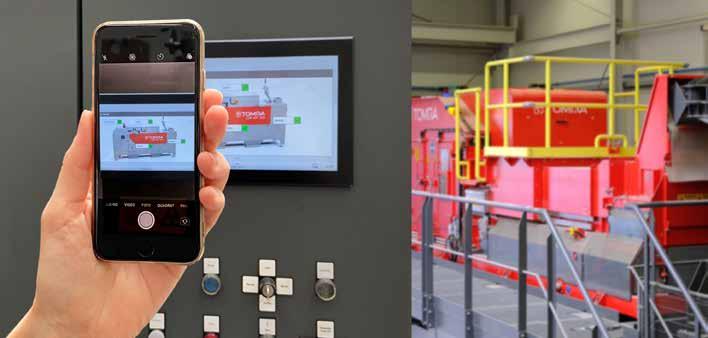
In a challenging market, mining companies under increasing pressure to improve the environmental performance, efficiency, and safety of their operations are turning to digitalization and advanced analytics. Data captured in their mines provides valuable insights, enabling them to make fact-based strategic decisions, improve their processes, reduce downtime, shrink their environmental footprint, and enhance safety. Virtual Reality and Augmented Reality are proving useful in training and problem solving on-site. The mining sector is in the early stages of digitalization, but the Covid-19 crisis has dramatically accelerated the process as companies have looked for solutions to protect employees and address mobility restrictions to maintain effective sales and service support to customers. For example, in October 2020, Management consulting firm McKinsey wrote that mining companies seeking to mitigate the impact of the pandemic had started to relocate around 15 to 20 percent of their on-site workforce by setting up “control towers” to facilitate remote working. It noted a renewed interest in

Klaus Berns, Head of Service at TOMRA Sorting Mining
remote operating centers that build on remote working capabilities, with some companies implementing cloud-based systems that enabled the collection and analysis of data from the mines for decision support. The process of digitalization is set to continue, as more mining companies become aware of the huge potential in operational and financial benefits.
TOMRA Sorting Mining: a constantly expanding offering of digital services
TOMRA is applying its holistic approach to helping customers to unlock the potential of digitalization, with digital services covering the complete customer journey – from sales support and technical consultations to remote service and training. All its digital solutions collect, manage and store data securely following data security best practices.
The cloud-based data platform, TOMRA Insight, turns sorting machines into connected devices that generate valuable process data, which is gathered in near real-time and can easily be accessed on a desktop computer or mobile device. It transforms sorting into a strategic management tool that helps processors in near real-time and retrospect. On the one hand, machine operators can take prompt action in response to changes
in material composition on the line. On the other hand, managers can make operational and business decisions based on more complete information. They can also make more accurate comparisons between multiple sites or lines, and monitor remotely difficult-toreach operations. TOMRA is constantly expanding its portfolio of digital services, and it is now introducing the new Augmented Reality tool for remote assistance, TOMRA Visual Assist. It enables remote experts to provide specialist support to a customer or a TOMRA Field Service Engineer on-site.
“Our service teams cover large areas, generally with one hub per continent, so giving troubleshooting, maintenance and guidance remotely can be a great help,” explains Klaus Berns, Head of Service at TOMRA Sorting Mining. “It enables us to be more efficient and ensure a fast response. If the technical expert is a far away, the customer doesn’t have to wait for qualified and detailed feedback.
Some mines are particularly difficult to reach, for example at high altitudes, 4,000m above sea level, or in harsh climates with temperatures well below zero. In some cases, it may take 2 or 3 days for the technical expert to arrive on site. TOMRA Visual Assist can save time, and long and difficult journeys.”
TOMRA Visual Assist can be used on standard devices like cell phones or tablets, but also with advanced tools such as Smart Glasses, which provide an Augmented Reality experience, so that the technician on-site can follow the remote expert’s guidance with their hands free, working in maximum safety. “TOMRA Visual Assist can also make a big difference for diamond operations where the equipment is located in a red area, where mobile phones or cameras are not allowed, as we can use the headset linked to the local network,” adds Klaus Berns.
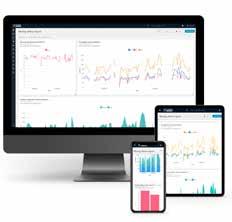
TOMRA has also harnessed digital technology to provide mining companies with a Virtual Demonstration and Test Solution to enable them to test the sorting solutions on their samples without leaving their office. By providing them remote access to its Test Center in Wedel, Germany, which has capabilities for all applications, it enables them to identify the best sorting solution for their mine, discuss the options with TOMRA’s experts, and make a fact-based decision.
TOMRA is also proactively engaged in spreading knowledge about the potential of sensor-based sorting solutions in mining through regular webinars. The sessions explore the various technologies, discuss financial and technical aspects, and analyze how they can add value to different mining operations.
DT HI-LOAD DUMP TRUCK BODIES
Engineered to maximise your payload
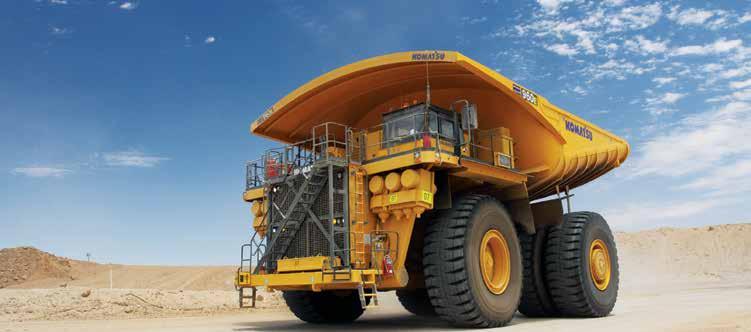
LIGHTWEIGHT increases payload
FLEXIBLE less maintenance
RELIABLE. DURABLE. SUSTAINABLE.
The DT Hi-Load dump truck body is a heavy-duty, lightweight, durable body custom designed to suit the mining application.
The DT Hi-Load body improves operator safety by deflecting rocks away from the canopy and automatically centralizing payload due to the curved design.
Tel: +260 96 849 3249 www.biagroup.com Tel: +27 11 923 1000 www.komatsu.co.za
CURVED DESIGN reduces canopy loading
CUSTOM-MADE application specific
Strong Sustainability Performance sees Perseus Mining deliver US$385 million to Ivorian and Ghanaian Economies in 2020

Perseus Mining Limited (TSX & ASX: PRU) (www.PerseusMining.com) has released its CY20 Sustainable Development Report. The report details the company’s progress over the past 12 months in delivering on its commitment to responsible mining operations in Côte d’Ivoire and Ghana, including an overall economic benefit to host countries totalling about USD$385M.
As part of its longstanding commitment to the communities in which it operates, Perseus reported increasing community investment by 71% to around US$1.9M in CY20, funding critical health and education infrastructure projects for local communities. Additionally, Perseus announced it had increased its proportion of local procurement from 66% in CY19 to 78% in CY20, totalling US$287M, and further expanded its employment of local populations, with 96% of its current workforce local to Ghana and Côte d’Ivoire.
Jeff Quartermaine, Managing Director & CEO of Perseus said: “Sustainability is deeply rooted in Perseus’s culture and operations and has had a large part to play in our resilience during this challenging year. We believe that responsible gold mining can play a key role in sustainable development, and that investing in our employees and our communities to create enduring social value will remain a guiding force in our growth path and future business operations. I am proud of my team’s effective response to the pandemic which successfully safeguarded our operations as well as our people, enabling us to deliver our Yaouré mine in Côte d’Ivoire this year ahead of schedule. Our approach to sustainability has continued to mature as our business has grown, and in the coming years we look forward to expanding our ESG offering and delivering greater impact across Côte d’Ivoire and Ghana.”
Jessica Volich, Group Sustainability Manager at Perseus said: “Despite the challenges the past year has brought, Perseus’s sustainability agenda has continued to strengthen and evolve alongside its expanding operations. Our wide-ranging efforts and
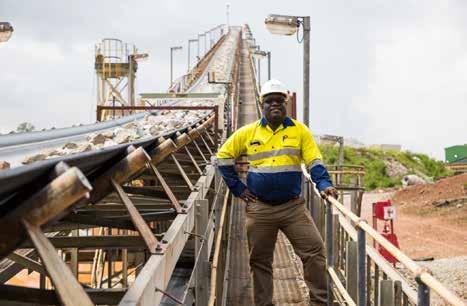
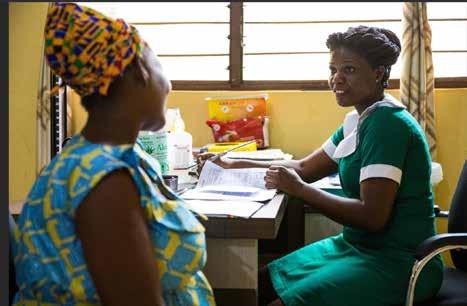
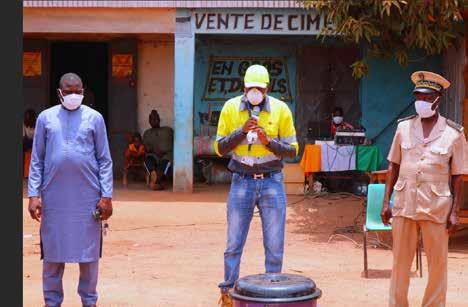
engagement with our local communities and host governments has enabled us to create shared sustainable value for all our stakeholders. We are committed to strengthening these relationships in the coming years as we endeavour to generate socio-economic value for our people, communities and host countries.”
In CY20, Perseus has enhanced its disclosure on sustainability-related risks and opportunities by aligning with the key reporting frameworks used by our stakeholders. These include the World Gold Council Responsible Gold Mining Principles, Global Reporting Initiative (GRI), Sustainability Accounting Standards Board (SASB) and the Task Force on Climate Related Financial Disclosures (TCFD).
Highlights of the report include:
Economic and Social Contribution • Total economic contribution of
US$385M in CY20 to Ghana and
Côte d’Ivoire • Increased community investment by 71% (from CY19) to around
US$1.9M in CY20, funding critical health and education infrastructure projects for local communities and providing COVID-19 support • Creation of new health clinics near Sissingué to improve health outcomes for the ~27,000 residents of the local communities • Increased in-country employment, with over 96% of total employees from host countries • Local procurement spend of $287M, an increase from 66% in CY19 to
78% in CY20 • Held 587 consultations with local communities • Paid >US$69M in taxes, royalties, and duties to Government
Health & Safety performance:
• Maintained record of zero workplace fatalities and reduced injuries • Implementation of comprehensive measures and protocols to prevent introduction and spread of
COVID-19 and maintain business continuity
Environmental stewardship:
• Re-use of 12,495,163 KL of water • Water intensity of 7.46M3/oz gold produced, benchmarked ahead of peers • Enhanced tailings disclosures in line with the Investor Mining and Tailings
Safety Initiative, and completed independent audits of all our Tailings Storage Facilities (TSFs)
Governance
• Worked with independent sustainability risk experts, KPMG, to refresh sustainability materiality analysis and conduct deeper analysis of sustainability risks and opportunities, and start development of a 3-year sustainability roadmap • Announced appointment of a new
Director by the end of FY21 to enhance sustainability skills of the
Board • Release of the first Modern Slavery
Statement to address potential human rights risks in Perseus’ global supply chain.
Future ambitions
• Establish a 3-year sustainability roadmap, and enhance social value and sustainability risk management through updates to the Risk
Management Framework and policy standards • Establish the Yaouré Community
Development Fund in FY21 • During FY21 and FY22, Perseus will complete and commence implementation of our biodiversity plan at Yaouré in Côte d’Ivoire mine site in and establish our site nursery, to be staffed by local community members • Explore strategic opportunities for community partnerships in Côte d’Ivoire and Ghana • Achieve full alignment with the
World Gold Council Responsible
Gold Mining Principles by FY23
Distributed by APO Group on behalf of Perseus Mining Ltd.
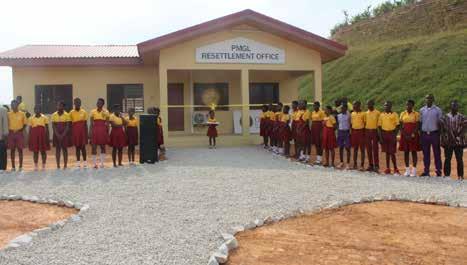
UNE ÉNERGIE HYDROÉLECTRIQUE PROPRE, RENOUVELABLE ET FIABLE POUR KAMOA COPPER GRÂCE À UN DEUXIÈME PARTENARIAT PUBLIC-PRIVÉ ENTRE IVANHOE MINES ET L'OPÉRATEUR NATIONAL DE LA RDC - SNEL
La collaboration entre Ivanhoe Mines Energy DRC, une société-sœur de Kamoa Copper SA, et SNEL, a pour but de produire de l'hydroélectricité pour alimenter le centre minier de Kamoa et pour contribuer au développement durable national de la RDC.
KOLWEZI, LA RÉPUBLIQUE DÉMOCRATIQUE DU CONGO, LE XX AVRIL 2021- Dans l'objectif de soutenir une mise en œuvre réussie et continue du site minier de Kamoa, Ivanhoe Mines Energy DRC, une société-sœur de Kamoa Copper SA, a annoncé la signature d'un protocole d'entente (Memorandum of Understanding MOU) dans le cadre d'un partenariat public-privé avec la compagnie d'électricité appartenant à l'État, La Société Nationale d’Électricité (SNEL), pour fournir de l'énergie hydroélectrique propre, renouvelable et fiable à Kamoa Mine.
Les co-présidents d'Ivanhoe Mine, Robert Friedland et Yufeng “Miles” Sun, expliquent que le partenariat public-privé entre Ivanhoe Mines Energy DRC et l'opérateur national, SNEL, est une collaboration qui a pour but de renforcer la capacité du réseau avec une énergie renouvelable, et cela par l'amélioration d'une turbine principale à Inga II, une centrale hydroélectrique située au sud-ouest de la RDC, sur le fleuve Congo: le plus profond fleuve au monde et le deuxième plus long d'Afrique, après le Nil.
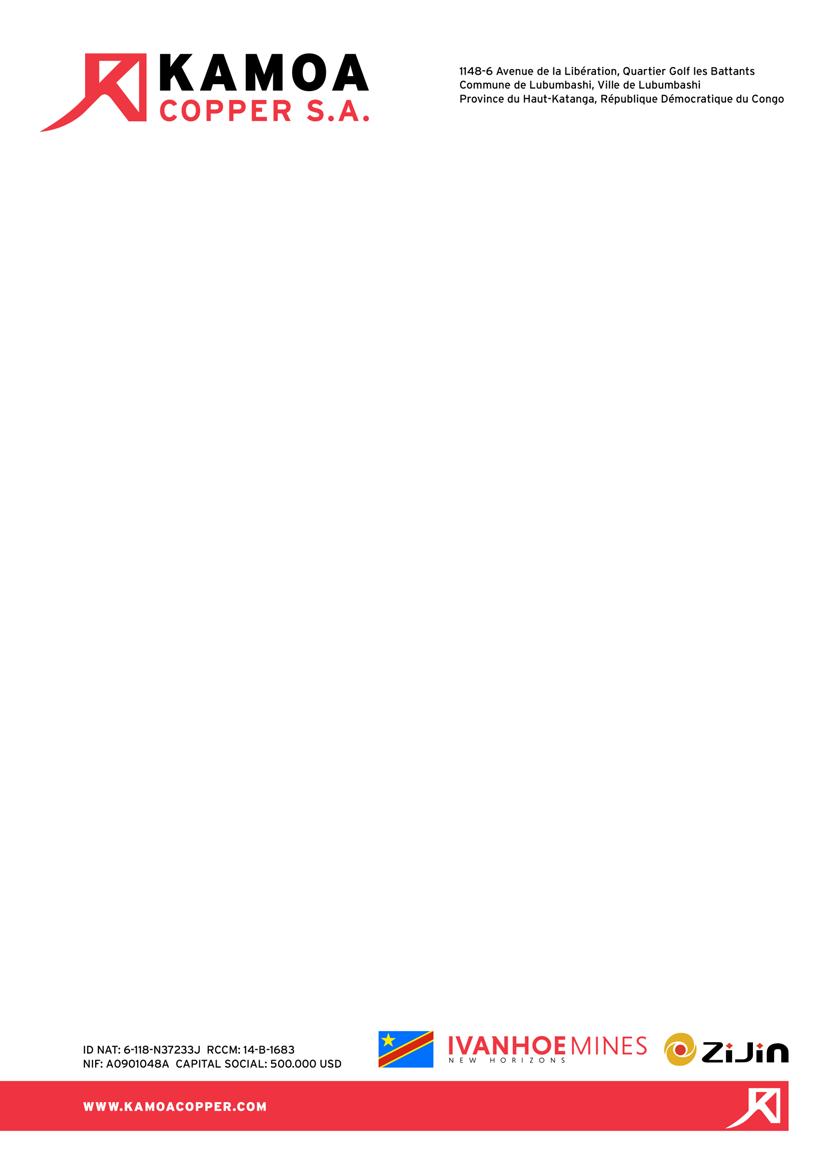
La centrale hydroélectrique Inga II, est opérationnelle depuis près de 40 ans, avec quatre de ses huit turbines qui ont fait l'objet de réfection. La turbine numéro cinq est une des quatre turbines en attente d'amélioration et dont on estime la capacité de production d'énergie hydroélectrique renouvelable à 162 mégawatts (MW). Par conséquent, le centre minier de Kamoa Copper, ainsi que la fonderie prévue, seront alimentés par de l'énergie durable en vue des développements futurs. Une des meilleures sociétés de génie en Allemagne, Voith Hydro de Heidenheim, vient d'être nommée maître d'œuvre pour le prochain projet.
Le Président de la République Démocratique du Congo, Son Excellence Monsieur Félix Tshisekedi, a exprimé son soutien total au partenariat public-privé visant l'amélioration de la turbine numéro 5, étant donné que ceci ne subviendra pas seulement aux besoins de développement de Kamoa Copper, mais permettra d'assurer également une alimentation électrique fiable aux communautés locales. Son Excellence Tshisekedi s'est exprimé au sujet de l'importance de ce partenariat : “La République Démocratique du Congo est dotée de possibilités hydroélectriques extraordinaires. Il est impératif de développer ce potentiel, car l'énergie hydroélectrique est propre, fiable et renouvelable. C'est sans le moindre doute le type d'électricité qui convient le mieux pour accompagner les priorités de développement de notre pays à long terme.”
“Des partenariats comme ceux-ci, entre Ivanhoe Mines et SNEL, nous permettront d'améliorer la capacité de notre réseau électrique et aussi les conditions de vie des citoyens congolais en facilitant l'accès à l'électricité. En même temps, la production électrique supplémentaire permettra à Kamoa Copper d'enrichir ces produits miniers dans la RDC. Ceci assurera des revenus supplémentaires pour le pays et, en tant qu'actionnaire de Kamoa Copper, la RDC estime que cette création de valeur locale est un impératif stratégique,” a ajouté le Président Tshisekedi.
L'approvisionnement en énergie renouvelable à long terme est indispensable à la réalisation de la vision d'Ivanhoe : développer Kamoa Copper de façon responsable sur les plans environnementaux, sociaux et éthiques, pour devenir un des plus grands projets d'exploitation de cuivre au monde. La production d'hydroélectricité améliorera largement, et contribuera au développement économique et social de la RDC. Ben Munanga, Président de Kamoa Copper a déclaré: “Cette nouvelle entente d'approvisionnement en énergie constitue un pas important dans notre parcours vers la durabilité, étant donné que cela permettra à Kamoa Copper Mine d'avoir un accès prioritaire à une puissance combinée de 240 mégawatts d'électricité propre et renouvelable, obtenus en combinant les turbines des centrales hydroélectriques de Mwadingusha et Inga II.”
Le premier partenariat public-privé entre Ivanhoe Mines Energy DRC et SNEL, qui consistait à améliorer la centrale hydroélectrique de Mwadingusha, a connu un large succès. À ce stade, la centrale de Mwadingusha est presque entièrement rénovée avec des instruments de contrôles derniers cris. À ce jour, Kamoa Copper a financé un accès routier de 70km, une station d'épuration, un établissement offrant des soins médicaux ainsi que toutes les infrastructures et tout l'équipement nécessaires pour que Mwadingusha devienne viable et durable. Une fois terminée, la centrale de Mwadingusha produira 78 mégawatts d'hydroélectricité propre, exactement ce qu'il faut pour amener Kamoa-Kakula jusqu'à la fin des phases de production (phase 1 et 2). Un aperçu des progrès réalisés à Mwadingusha est disponible ici: https://1drv.ms/v/s!AucuRMimq5xjgbFk2gpz4tWXMZNn_g?e=wQvdYu (le lien sera remplacé par un lien YouTube)
Kamoa Copper s'est engagé à exploiter le cuivre de manière responsable, pour les générations actuelles et futures. Par ailleurs, Kamoa Copper se fait fort d'opter pour des solutions minières intelligentes sur le plan climatique pour servir aussi bien à la transition aux énergies non polluantes, qu'à l'intérêt des communautés environnantes. Le cuivre produit par Kamoa Copper joue un rôle déterminant dans la transition énergétique mondiale, afin de réaliser des objectifs ambitieux concernant le climat, tout en soutenant les communautés congolaises.
Fin
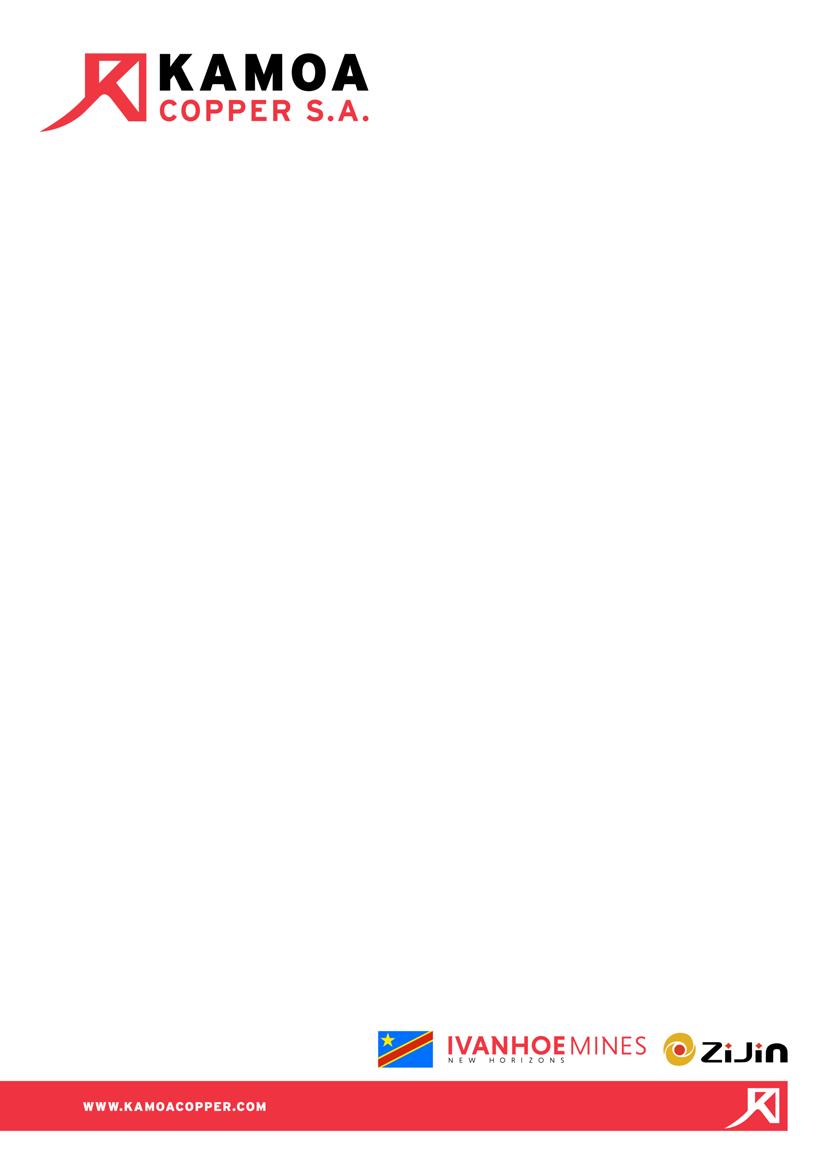
KAMOA COPPER S.A. : DEBUT DE PRODUCTION DANS UN MOIS
La première phase d'installation du concentrateur de 3.8- Mtpa étant achevée à 98 %, Kamoa Copper peut entamer, avec un mois d'avance, la prochaine étape de la mise en exploitation.
KOLWEZI, REPUBLIQUE DEMOCRATIQUE DU CONGO, 07 MAI 2021- la phase de mise en route du concentrateur C4 de Kamoa Copper S.A., qui comprend le broyage du minerai et la première production de concentré de cuivre, devrait commencer entre la fin du mois de Mai et début juin 2021.
Grâce à une construction accélérée et un bon déroulement de la mise en exploitation, la première phase d'installation de l'usine de concentration de Kamoa Copper, d'une capacité de 3,8 Mtpa, touche à sa fin. La plupart des certificats d'achèvement de travaux de construction ont été signés. Kamoa Copper est désormais alimenté en permanence par l'hydroélectricité et les vérifications de l'instrumentation sont en bonne voie. La distribution d'eau dans certaines parties de l'usine annonce le début des vérifications d'étanchéité, l'étalonnage de certains instruments et des contrôles en continu. Ensuite, la dernière étape des travaux sera entamée, autrement dit, le traitement de minerai par l'usine pour produire du concentré de cuivre.
Le Président du Conseil chez Kamoa Copper S.A., Ben Munanga, a eu le plaisir de faire l'annonce suivante : “Dans l'ensemble, la construction liée à la phase un de l'usine de concentration de Kamoa Copper, avec sa capacité de 3.8 Mtpa, et de ses installations connexes, progresse rapidement. Fin Avril, la réalisation était achevée a près de 98 %. Ce progrès nous emballe particulièrement, car le début de la production chez Kamoa Copper annonce l'inauguration d'une région minière cuprifère, qui contiendra un grand nombre de mines à haute teneur, où l'extraction de cuivre se fera de génération en génération ”.

Le développement sous-terrain du mois d'avril chez Kamoa Copper, a battu tous les records une fois de plus, avec une progression de plus de 3,625 mètres, portant le total du développement sousterrain à près de 42.2 kilomètres, soit 15 kilomètres d'avance sur ce qui était prévu. Le minerai entreposé en surface issu de préproduction contient, selon les estimations, près de 3,0 millions de tonnes de minerai de qualité moyenne et élevée, d'une teneur moyenne combinée d'environ 4.74 % de cuivre. L'objectif qu'avait Kamoa Copper d'extraire 3.0-millions de tonne de minerai de qualité moyenne et élevée, a été atteint plusieurs mois avant la date estimée par l'étude de faisabilité conduite en 2020. Pendant la dernière phase des travaux, du minerai à faible teneur sera introduit dans l'usine afin de s'assurer que le rendement de celle-ci, et la récupération de cuivre, seront satisfaisants avant d'augmenter la teneur.
Voici les commentaires de Mark Farren, Directeur General de Kamoa Copper: “En Avril nous avons enregistré, encore une fois, de bonnes performances par nos équipes minières, qui continuent à produire au-delà de nos prévisions. Désormais, nous avons atteint notre objectif de réserves de préproduction de 3.0 million de tonnes. Cette quantité est susceptible d'augmenter étant donné
que le taux d'extraction mensuel dépasse en ce moment le taux de traitement et ne devrait baisser que lorsque le concentrateur de phase deux entrera en service à la mi-2022.”
Robert Friedland, Co-Président Executif d'Ivanhoe Mines, la société mère de Kamoa Copper, a ajouté : “Nous sommes fiers de toute l'équipe de Kamoa Copper S.A. pour leur dévouement remarquable et l'accomplissement d'avoir terminé la phase un de production plus rapidement que prévu tout en respectant le budget malgré les défis que présente la pandémie de la COVID-19. Nous tenons particulièrement à exprimer notre gratitude à l'équipe dirigeante de Kamoa Copper. Leur passion indéfectible, leur vision et leur poursuite de l'excellence, jouent un rôle central dans la transformation et la croissance de l'entreprise.
“Le début de la production à Kakula annonce l'inauguration d'une région minière cuprifère qui contiendra un grand nombre de mines à haute teneur, où l'extraction de cuivre se fera de génération en génération. Nous mettrons désormais l'accent sur le développement de cette immense région cuprifère de façon responsable sur les plans social et éthique, et d'instaurer un nouveau modèle à l'échelle mondiale pour l'élimination des gaz à effet de serre dans la production de cuivre, car le monde en a grand besoin.”
La construction de l'usine de concentration, d'une capacité de 3.8 Mtpa, dans le cadre de la deuxième phase, progresse bien. En ce moment, l'accent est sur le terrassement et le génie civil. Dans les deux domaines, il y a une légère avance sur le calendrier prévu. L'ingénierie et les activités d'approvisionnement avancent bien. Les deux premières expéditions d'acier de construction, ainsi que les trois premiers envois de tôlerie sont partis du fabricant et sont en route pour le site. Nous attendons les premières livraisons d'acier et de tôlerie en juin 2021. Un grand nombre des entrepreneurs principaux ont été retenus pour la deuxième phase de production afin d'assurer une continuité et pour transmettre l'expérience obtenue durant la première phase.
Selon les prévisions, la production combinée de la première et deuxième phase, devrait être autour de 400,000 tonnes de cuivre par an. Cet agrandissement progressif jusqu'à 19 Mtpa permettrait à Kamoa Copper S.A. de se classer deuxième plus important centre minier de cuivre au monde, dont la production maximale annuelle dépassera 800,000 tonnes. Une attention particulière sera donnée au développement de cette immense région cuprifère de façon responsable sur les plans social et éthique, et d'instaurer un nouveau modèle à l'échelle mondiale pour l'élimination des gaz à effet de serre dans la production de cuivre.
Découvrez en survol comment Kamoa Copper s'efforce de produire du cuivre de façon responsable en regardant cette nouvelle vidéo : https://www.youtube.com/watch?v=JWC4S2e1X20
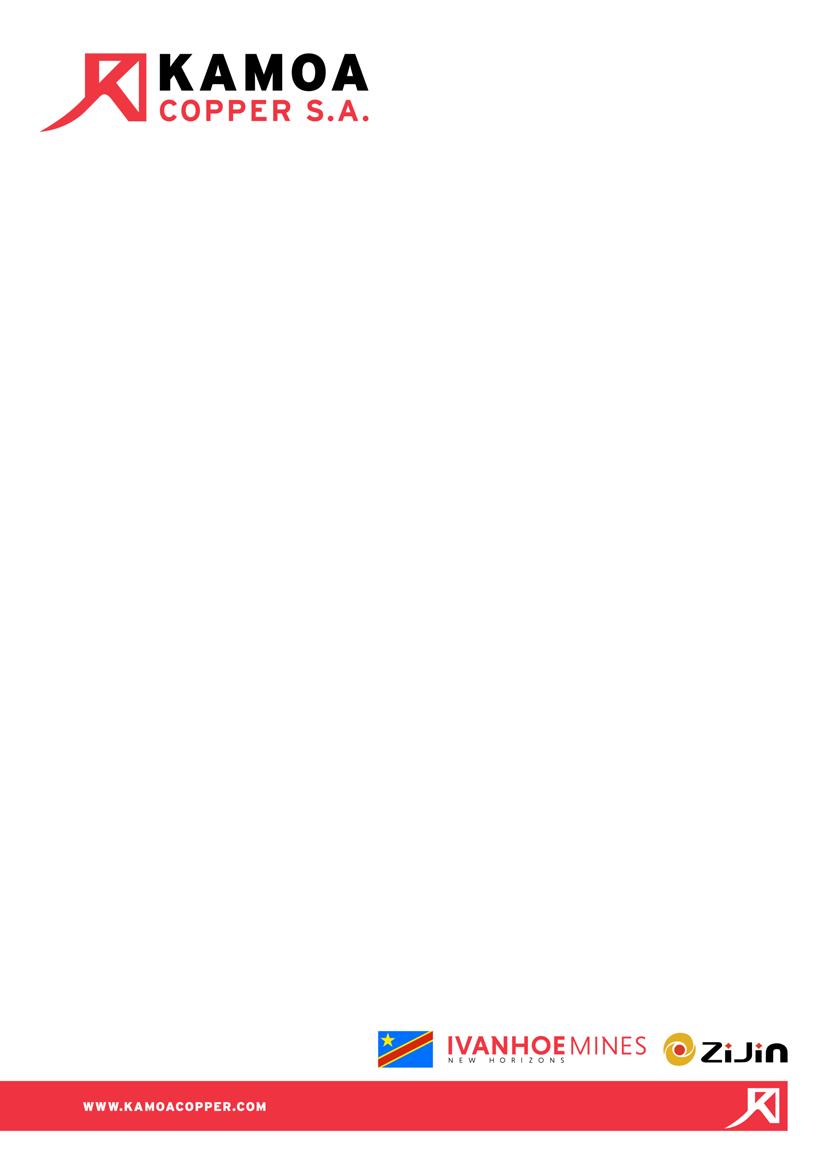
Fin
Note à l'attention des rédacteurs
Concernant Kamoa Copper S.A.

Congratulations to our customers for OPTIMISING

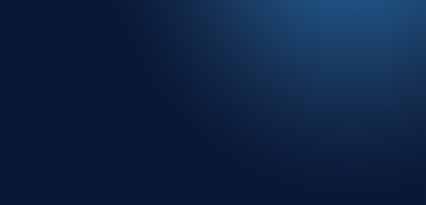
Leveraging Data and Innovation to Optimise the Mining Value Chain in Real Time TRILLION TONNES of HAULAGE over the last 40 years
ADVERTISER’S INDEX
Africa Mining Convention.................................................................................................07 Agruline................................................................................................................................OBC AH Lundberg Systems.......................................................................................................15 Ambra Solutions....................................................................................................................24 Beka Schreder.........................................................................................................................11 Elphinstone..............................................................................................................................21 Junior Mining Indaba.......................................................................................................IFC Komatsu....................................................................................................................................41 Modular Mining......................................................................................................................48 Nanozen.................................................................................................................................IBC
Allijan..........................................................................................................................................31 Quietair.......................................................................................................................................39
Sintrol..........................................................................................................................................35
Speedcast................................................................................................................................27
FMDZ is a bi-monthly magazine for mining industry incorporating, exploration, oil, power, drilling and other large scale extraction, storage, transport, Market and utilisation of Africa’s Copper Belt wealth and resources. First Mining DRC-ZAMBIA is published 6 times per annum: Jan/Feb, Mar/Apr, May/Jun, Jul/Aug Sept/Oct and Nov/Dec.
TO ADVERTISE CALL: +27 11 044 8986 Email: sales@fmdrc-zambia.com
Affiliate publications: