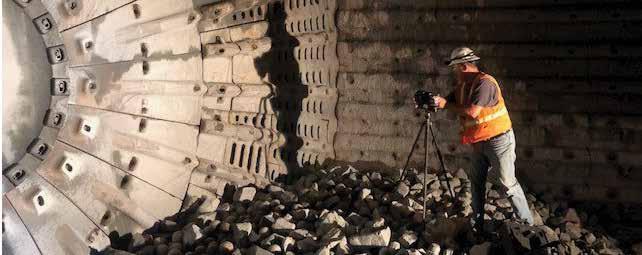
10 minute read
Elecmetal

Innovative Grinding Solutions
Advertisement
ME Elecmetal . . . Always here when you need us
ME Elecmetal o ers more than mill liners — We o er innovation, support, custom designs and valuable tools to develop a total grinding solution speci c to your needs. We are your trusted partner at every stage of the optimization process to provide valuable insight based on over 100 years of experience and advanced technologies. We will help you optimize your process, reduce downtime and increase productivity, resulting in higher pro ts. One more thing you can count on with ME Elecmetal . . . We will ALWAYS be here when you need us!
ME Elecmetal’s products and services include: - Grinding mill liners (castings, rubber and composite) - Grinding media (SAG, ball and grinding rods) - Crusher wear parts - Smelter ladles and slag pots - 3D laser scanning for wear analysis - Reline simulation services - 2D/3D simulation services (DEM and FEM)
ME Elecmetal Minneapolis, MN • Tempe, AZ 763-788-1651 • 480-730-7500
Email: sdevos@meglobal.com www.me-elecmetal.com Ask Us About ME FIT Solutions
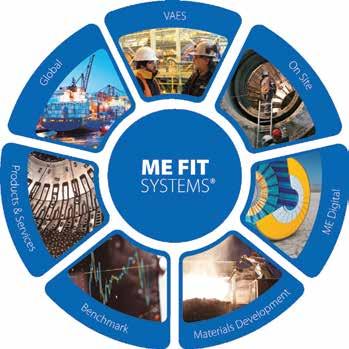

At ME Elecmetal, our goal is for our customers to meet their goals
With over 100 years of experience in mining and metallurgy, ME Elecmetal is With over 100 years of experience in mining and metallurgy, a company very well known for its excellence and leadership in providing ME Elecmetal is a company very well known for its excellence and leadership in providing integral solutions that add value to its customers’ mining processes. integral solutions that add value to its customers’ mining processes.
ME Elecmetal’s History
Historically, ME Elecmetal has been a visionary company. Founded in 1917, it truly revolutionized the industry and market by utilizing the latest technology innovation — the electric arc furnace. This was clearly a technological change that shaped the way we tackled the market, seeking constant, ongoing renewal, which is how we continue to approach the business today. In the 1960s, the company started selling steel castings to manufacturers of railroad machinery, trucks, pressure valves and mining companies. Seven years later, the company successfully manufactured the rst mining mill liner, catapulting the company in a new strategic direction where it began to focus and specialize in the production of impact- and abrasion-resistant wear parts for ore processing, speci cally mill liners and crusher liners.
Today, ME Elecmetal has ve foundries in the United States, Chile and China, with a combined annual production in excess of 134,500 metric tons. With our joint-venture facilities (including a ball plant in Zambia), ME Elecmetal has an annual grinding media installed manufacturing capacity exceeding 590,000 metric tons of forged grinding balls for SAG and ball mill grinding, in addition to steel rods for secondary grinding. Mill Liners: ME Elecmetal is the world leader in designing and supplying highly engineered mill liners and total liner solutions for SAG, AG, ball and rod mills.
Premier Product Lines
Grinding Media: ME Elecmetal designs, manufactures and supplies the highest quality forged steel grinding media for SAG, ball and rod mills.
Crusher Wear Parts: ME Elecmetal o ers wear parts for all makes and models of primary, secondary, tertiary and pebble crushers.
Technology: ME Elecmetal also o ers 3D laser scanning, liner design and engineering services, discrete and nite element modeling and mill and crusher optimization services as part of our extensive service portfolio.
Integral Solutions Add Value
ME FIT System® is a program designed to deliver ME Elecmetal’s integral solutions for grinding and crushing applications. FIT stands for Fully Integrated Technology. Through the ME FIT System programs, we help our customers achieve their goals by combining wear parts with technology tools, advice, training and monitoring — all of which allow us to develop customized solutions to address speci c challenges and add value to our customers’ operations.
We become a partner to our customers by understanding their needs. To accomplish this, we collect operational data including processed tonnage, available power, down time, load levels and all other relevant information about how their mills operate. We measure how long media and liners last, what production levels they are achieving and what opportunities there are for improvement in the comminution process.
The system takes advantage of ME Elecmetal’s highest standards in quality, manufacturing, service and logistics — along with the multifaceted team who bring it all together.
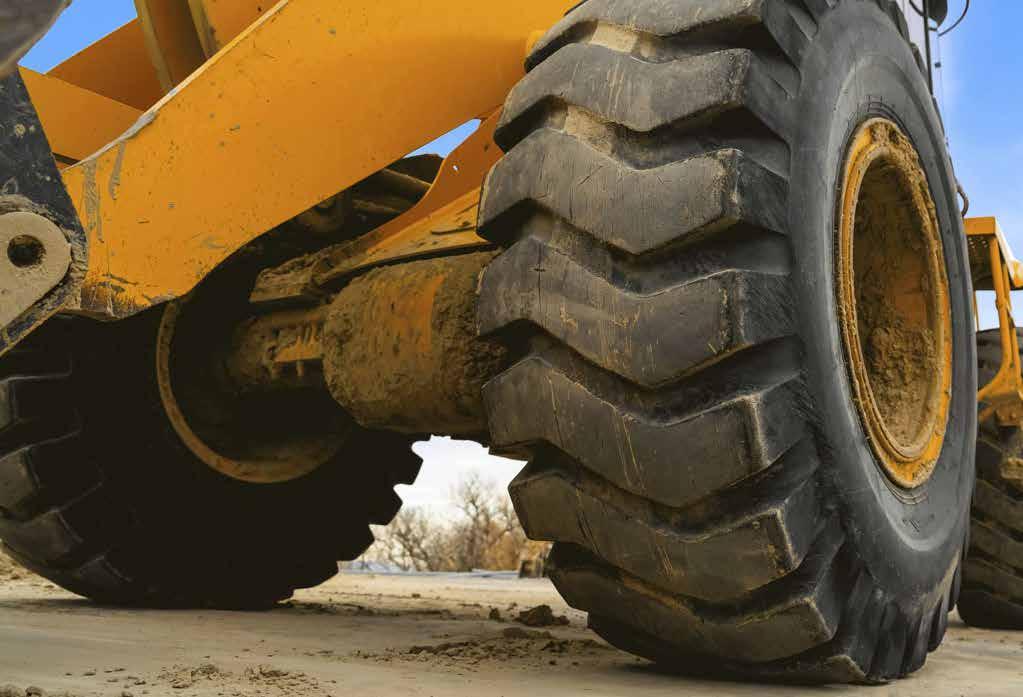
Enhancing mining operation with proper OTR tyres
In mining operation, proper tire selection can mean the difference between unnecessary roadside breakdown and increased profitability. OTR tires, also known as Off-the-road tyres may be the best choice for fleets with frequent or continuous off-road applications to avoid the cost of repairs and maintenance.
The tires are built to support large amounts of weight to guide vehicles through challenging conditions that would leave most other trucks dead in their tracks. Simply put: OTR tyres are designed for vehicles that frequently travel on difficult terrain.
OTR tyres come in three basic construction
Cross-ply
Cross-ply tyres refer to the construction whereby nylon cords are crossed diagonally over each other. These are then layered with thick rubber piles providing tough, rigid sidewalls. Whilst cross-ply tyres are tough and provide a higher resistance against sidewall damage, they also have a higher rolling resistance which can cause the tyres to heat up quickly increasing the air pressure within the tyres.
Radial
As car designs evolved so did tyre technology and a more flexible tyre was developed known as radial tyres. Radial tyres are constructed from cords which have been rubber bonded and placed so they run across the circumference of the tyre. The radial piles are then covered by a casing belt made up of cord or steel which is then covered by the rubber tread. Radial tyres offer greater comfort, water and heat resistance and improved fuel economy.
Bias and belted bias OTR tires are best used for vehicles traveling at slower speeds while radial tires are great for trucks traveling at higher speeds. While these three constructions are the most commonly seen among OTR tires, and used in such as road grading quarry work, construction, and all types of hauling.
Now, let’s look at the individual elements that are added to make up these two tyre construction types.
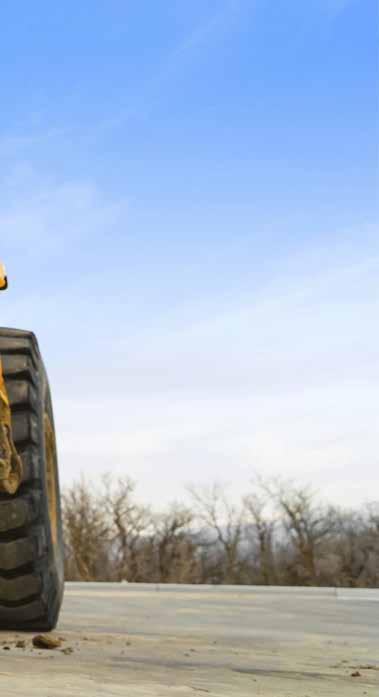
Tread
The tread is the rubber compound which overlays the tyre construction. The tread covers the circumference of the tyre and is the part that makes contact with the road. As such tread patterns are developed for performance in varying driving conditions.
Sidewall
The sidewall is the outer side of the tyre which protects the cord piles. It is made up of rubber compound designed to resist cracking and scuffing. The sidewalls feature information about the tyre such as size, type and brand.
Chafer
The chafer in cross-ply tyres is a lining between the body and the bead (tyre and rim) which prevents them from chafing. In radial tyres the chafer works as added reinforcement strengthening the tyre and converting the forces from the torque.
Inner liner
Found in tubeless tyres, the liner prevents air leaking by covering the inner surface of the tyre.
Bead
The bead is a strong, steel cable loop coated in rubber which sits on the rim of the tyre and keeps the tyre in position.
Ply
The ply is composed of either nylon piles or steel cord and works to confine the pressure within the tyres. The ply absorbs any braking and steering shocks while driving to provide the motorist with a comfortable ride.
Breaker or belt
Breaker or belt refers to the layer of the tyre between the carcass and the tread. In a cross-ply tyre these are referred to as breakers in a radial tyre this layer is referred to as a belt.
Breakers are constructed of steel wire or nylon while belts can be made up of any number of materials although generally they are also made of steel cord wires. The wires are layered between the tread and the ply.
So you see not all tyres are the same, the research design and technology involved in the manufacturing process is what distinguishes one tyre from another. When buying an OTR Tyre. Keep the following in mind: 1. Pattern. It guarantees the good grip on the road and durability. OTR tires with an asymmetric pattern mostly have the good performance. Pay an attention to the tire tread depth, the deeper it is, the better. This would help to make the handling process of the machine easier. 2. Type and size. You should take into account the recommendations of your vehicle producer. Before the purchase make sure you make the right choice and all technical recommendations have been followed. Otherwise you can ask your tire dealer for a professional advice. 3. Material. According to all standards the higher percentage of the natural rubber in the tire is the better its performance. It’s up to natural rubber to guarantee the elasticity and strength of the tires. 4. Brand. The best choice would be an A-brand that has already proved its quality in the field of OTR tires, for example: Yokohama, Michelin,
Bridgestone, GoodYear. 5. Tread depth of the used OTR tires. If you want to save some money and purchase the used OTR tires, pay an attention to the rest tread depth of the pattern and also inspect the tire, there shouldn’t be any damages, few cosmetic damages won’t do any harm.

How to choose the right OTR tyre and reduce on operating costs
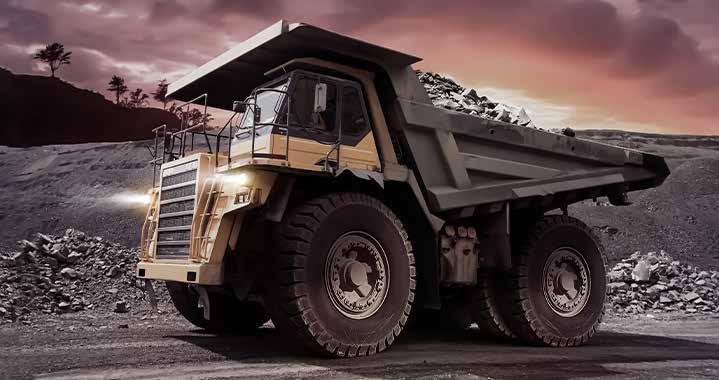
Tyres plays an essential role in keeping your vehicles on the move, no matter what kind of industry you operate in. No matter if you transport raw materials in mining & earthmoving, hauling freight across the country or you handle containers at terminal sites and ports, keeping your fleet up and running is crucial. Downtime is incredibly expensive and, in most cases, easily avoidable. Paying attention to how you use and choose your OTR tyres is one of those easily applicable steps to significantly increase efficiency and reduce your total operation costs.
Choose the right OTR tyre for the application
The most important way of reducing tyre degradation and unnecessary wear is choosing the right OTR tyre for the job, to determine which tyre suits your application best, we need to look at the various construction methods. All tyres are predominantly made of multiple rubber components. The biggest differences among the various OTR tyres is the way the internal steel reinforcements are placed within the tyre. Radial tyres are constructed with a series of steel cords that run across the tread. Radial tyres are mainly developed to be more shock absorbing for uneven surfaces.
Another construction method that also uses steed beads is the bias / diagonal tyre. The beads are placed at an angle of 30 to 40 degrees instead of in a straight manner. For additional strength, plies of nylon are placed at opposing angles to create a crisscross pattern that provides additional strength. The bias / diagonal tyre offers a smoother ride on rough surfaces and can handle heavier loads. That is why the bias / diagonal tyre is commonly used in industries such as mining and earthmoving.
If your machinery operates on smooth surfaces or on sites with a high risk of punctures, the third option is a solid tyre. The solid tyre is, as the name suggest, a tyre made of solid materials so is unaffected by sharp materials that would cause damage to pneumatic tyres. These tyres are perfect for dozers on scrapyards or forklifts.
Calculate tonne kilometer per hour for the perfect fit
The best way to determine which tyre is the perfect fit for your machinery is to calculate it. Of course, rim size is the most important factor to actually choose a tyre that fits, but rim size doesn’t tell you much more than that. The tonne kilometer per hour index indicates what loads your tyre can handle and is determined by the tyre compound and materials used.
OTR Tyre manufacturer Magna Tyres Group has recently published* an article explaining how to use the formula in easy steps, so even those without a degree in mathematics can use it. For your convenience, we will try to summarize it. The main formula is as follows: TKPH = (mean tyre-load) x (average work-shift speed)