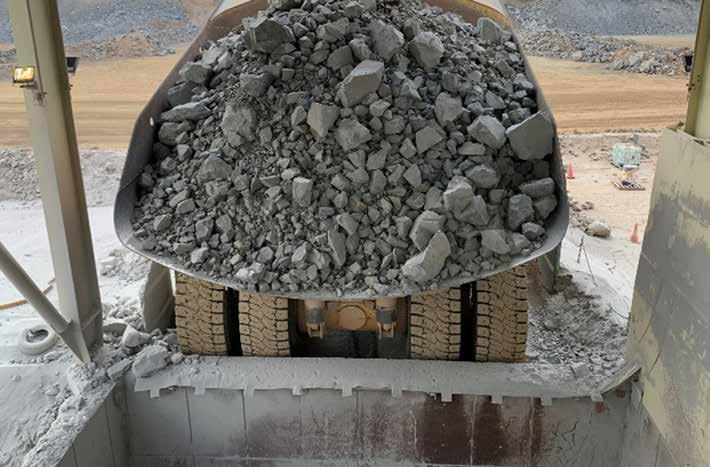
25 minute read
DRC Mining Week
ORICA expands its fragmentation monitoring solution with fragtrack™ crusher
Orica (ASX: ORI), has announced the release of its latest fragmentation monitoring solution enabled by FRAGTrack™ Crusher, an automated pre-crusher fragmentation measurement tool delivering operational continuity in a safe and reliable way.
Advertisement
FRAGTrack™ Crusher camera view. Measurements are captured and processed in real-time during the tipping operation.
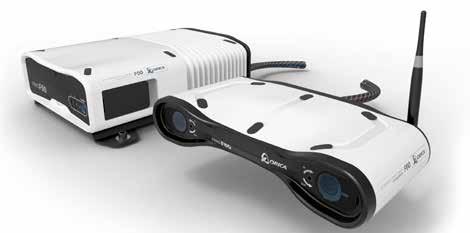
The Orica FRAGTrack™ system (Front) F60 camera houses various measurement sensors used in the determination of PSD samples. (Back) F50 processing unit houses the edge computer processing and communication technologies used by the system. Based on the success of the existing suite of automated post-blast fragmentation monitoring solutions, Orica has developed FRAGTrack™ Crusher to meet growing demand from customers for downstream monitoring and optimisation solutions at every stage of the mining value chain. The technology leverages the latest deep neural network artificial intelligence (AI) framework along with the industry-proven hybrid 2D and 3D particle size distribution (PSD) processing methods to deliver a fully autonomous adaptive fragmentation monitoring solution at the crusher dump pocket, enabling customers to measure material on the truck during the tipping operations.
FRAGTrack™ Crusher provides truck by truck PSD analysis of rock fragments during the dumping operation with unmatched accuracy and without impacting operations or productivity.
The technology delivers constant performance tracking for both the drill and blast operations and the downstream processing functions, driving continuous improvements end-to-end in the mining value chain. When bundled with Orica’s FRAGTrack™ Conveyor technology in a fragmentation monitoring solution, it enables further analysis of the crusher’s performance and the impact of blasting parameters in a production workflow in real-time.
Orica Vice President - Digital Solutions, Raj Mathiravedu, said: ”The full adoption of AI technology into our architecture, coupled with our strategic partnership with Microsoft, allows us to expedite the delivery of capabilities that were not previously possible, and FRAGTrack™ Crusher is an example of how we leverage AI to help deliver intelligence and value to our customers.”
PSD data is provided via a real-time application programming interface (API) and industrial open platform communication unified architecture (OPC UA) protocol to drill and blast software and crusher distributed control systems (DCS), allowing seamless integration into the existing site operation workflows.
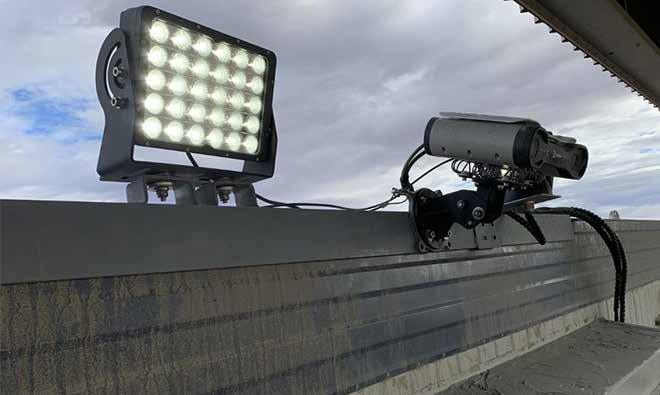
FRAGTrack™ Crusher installation
FRAGTrack™ Crusher has already been gaining traction globally in the mining and quarry markets, where it is being utilised as a critical enabler of blasting optimisation and mine to mill initiatives.
This signals a significant transformation from the subjective nature of existing manual PSD analysis methods while eliminating the safety concerns of onbench photography and the extensive time required to manually process and correlate to relevant data sets, including fleet management data to determine the material’s blast of origin. In the most recent application of FRAGTrack™ Crusher in a Tier I low-cost gold operation in Western Australia, it successfully delivered an automated blasting optimisation workflow on site leveraging PSD as a primary KPI to throughput and overall mill performance.
The project included installation of a FRAGTrack™ Conveyor system post crusher, allowing pre and post crusher PSD to be monitored. When combined with a fragmentation improvement process, the FRAGTrack™ solution enabled a continuous feedback loop that enabled the operation to rapidly optimise blast designs that drive overall project profitability.
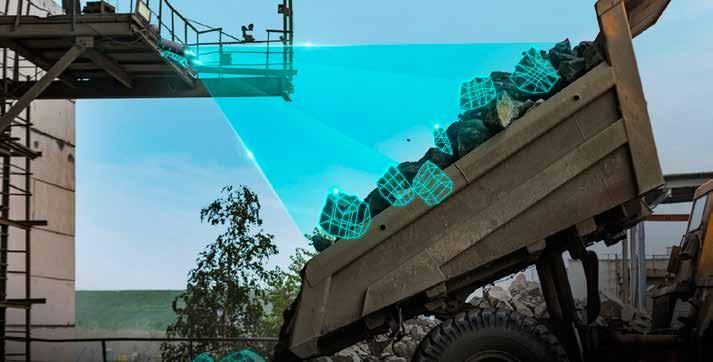
Metso Outotec launches Geminex™, a digital twin for efficient management of variability in mining and metallurgical operations
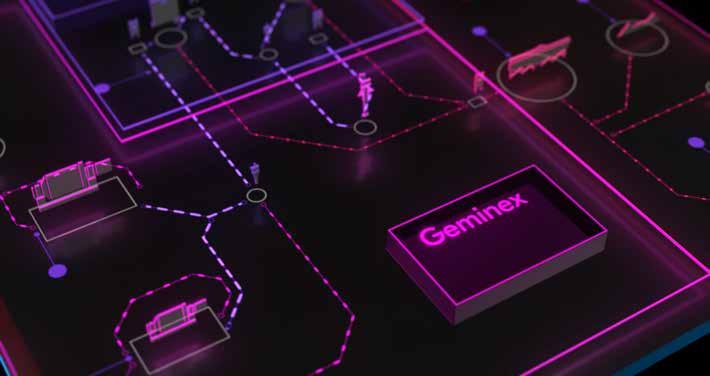
Metso Outotec is launching a science-based digital twin, Metso Outotec Geminex™, for managing variability and optimizing resources. The unique solution simulates and optimizes seamless sustainable operations in minerals, pyro- and hydrometallurgical processes by combining operational data from both internal and external data sources.
“Metso Outotec’s digital twin provides unparalleled benefits to the mining and metallurgical industry. The increasing complexity of ores, the shorter global economic cycles and the faster changes in commodities demand, combined with strict sustainability targets, form an equation that requires a new toolbox to solve these challenges. The innovative GeminexTM digital twin supports our customers in designing and adjusting their processes in an agile manner,” explains Professor Emeritus Kari Heiskanen, Technology Director at Metso Outotec.
With GeminexTM, alternative operational scenarios and parameters can be efficiently simulated and tested based on accurate process models and real data. It provides invaluable information for short- and long-term decision-making and allows operations to use resources in an optimal way while considering both impacts and constraints.
“When the GeminexTM capability is combined with our leading global service, Metso Outotec is able to further support local operators in turning the desired scenarios into real plant performance by offering precisely the right support – from process to technology – to help achieve the results needed today and long into the future. This makes us truly unique,” says Terry Galvin, Vice President, Expert services at Metso Outotec.
The GeminexTM digital twin is part of Metso Outotec’s Planet Positive portfolio.
Market-leading sizing and simulation tools at the core
For simulation and production, Geminex™ utilizes the unique HSC process models that have already more than 20,000 users worldwide. These process models have been successfully implemented in hundreds of minerals and metals processing flowsheet development cases, and the same models are utilized in plant run-time optimization.
“In brief, the Metso Outotec Geminex™ provides a true end-to-end digital solution by enabling enriched decisions leading to optimized performance and resulting in tangible benefits for the customers’ operations,” explains Jari Moilanen, Director for minerals processing digital solutions.
Benefits of the Metso Outotec Geminex™:
• Minimizes carbon footprint • Maximizes efficient use of resources • Simulates the process safely without environmental or financial risks • Enables material traceability • Increases profitability • Quick and easy to implement
More information about GeminexTM is available on our website.
The Role of Mining Vehicle Automation in the Mine of the Future
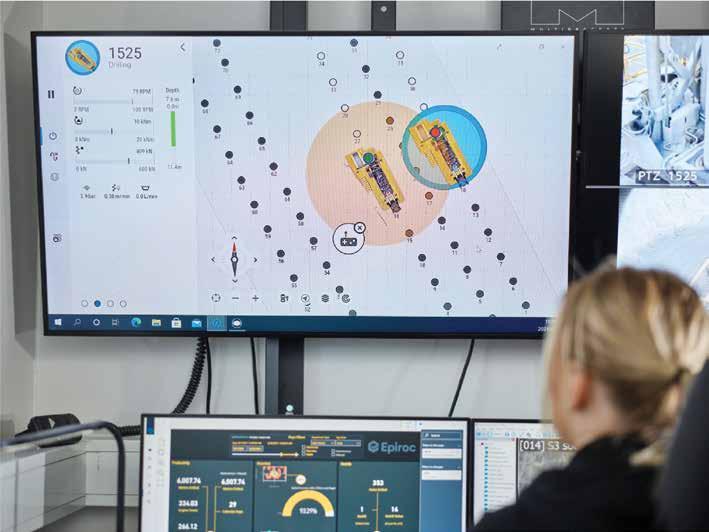
Nick Holland, CEO of Gold Fields, one of the world’s largest gold mining firms, recently outlined many of the challenges faced by gold producers —as well as by miners of most other resources—and discussed the roadmap Gold Fields intends to take to thrive in today’s mining environment. His address took place at the Future Mining Conference 2015 in Sydney Australia, November 4, 2015.
Holland shared that due to challenges in the recent years such as lower grade of ore deposits, significant global price drops, and cost inflation, “shareholder value [has slumped] by 50-80% since 2007.” With pressures on global commodities, today’s mining industry at large mirrors this trend, though Holland’s presentation provided a dramatic window into just how piercing these pressures have been. “The gold mine of the future has to be set up, structured, and managed differently from how it is today if it is to remain relevant and valueadding to all its stakeholders,” Holland concluded.
Of the solutions to the gold mine of the future posed by Holland, three are of particular interest to the automation industry. In his presentation, Holland suggested that in order to remain competitive the mining industry should improve in the following areas: • Embracing digital mining, advanced analytics, and new software technologies • Converting conventional mining practices to mechanization and automation • Cooperating more closely with
OEMs that develop and operate best-of-class technologies and equipment at various levels of automation
Mining automation technologies are becoming more available and affordable for nearly every area of operation, such as: exploration, extraction, transportation of materials, processes automation, software/analytics, etc. In one of these areas, extraction and transportation, automation technology focuses primarily on further mechanizing and introducing remotely controlled vehicles to enhance production and safety. Despite this primary purpose, the software used to direct the efforts of robotic vehicles can also provide a variety of analytic and process benefits.
For example, Mobius command and control software developed by Autonomous Solutions, Inc. (ASI) allows a single operator to control multiple unmanned vehicles. However, as a secondary benefit, Mobius tracks all manned and unmanned vehicles in the mining network, which gives mine administrators access to real-time vehicle locations and enables them to monitor equipment utilization, locate bottlenecks in the production process, and receive notification of maintenance or safety issues.
Mining companies can further combat inflating costs by shifting to unmanned vehicle technologies. Recent numbers released by global mining major Rio Tinto suggest that vehicle automation technologies outperform manned fleets by an average of 12% and can save as much as 500 man hours per year per vehicle by eliminating downtime for shift changes, breaks, and absenteeism.
In addition, automation improves safety and enhances the ability to operate equipment at OEM recommended parameters thus facilitating predictable maintenance schedules and decreasing unscheduled maintenance. Remote operators can control more than one vehicle allowing mines to benefit from economies of scale in their labor force. While Holland suggests a closer relationship with technology and vehicle OEMs that provide automation, mining companies may find this course expensive and restrictive. Closer relationships may involve replacing existing equipment with automationenabled equipment or signing restrictive single-source fleet contracts.
Third party automation companies may be the most affordable and least restrictive option. Third party companies, like ASI, provide aftermarket automation technologies that retrofit to existing equipment, allowing miners to automate their existing fleet, integrate with existing software and infrastructure, and maintain their flexibility to purchase and automate the right vehicle regardless of the manufacturer.
Talk to an automation specialist today, and explore the benefits your mine could experience with ASI’s vehicle automation technologies.
Metso Outotec wins major order for a large iron ore pellet plant in India
Metso Outotec has signed an agreement for the delivery of engineering and key equipment for an iron ore grate kiln pellet plant to Jindal Steel Odisha Limited (JSOL), a wholly owned subsidiary of Jindal Steel & Power Limited (JSPL). The plant is located in the industrial city of Angul, in eastern India. The value of the order is approximately EUR 30 million, and it has been booked in Metals’ Q1/2022 orders received.
Metso Outotec’s scope of delivery consists of engineering and the supply of major equipment, including the traveling grate, rotary kiln, and annular cooler.
The plant will produce six million tons of high-quality iron ore pellets per year. This is Metso Outotec’s second pellet plant order from JSOL in the past 12 months. The first grate kiln pellet plant is currently being installed at the same location by Metso Outotec and JSOL.
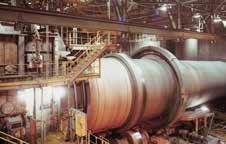
“Metso Outotec and JSPL have a strong history of working together in the field of iron ore pelletizing. We have previously worked with JSPL in 2006 and 2012 for the deliveries of two traveling grate pelletizing plants to Barbil, India. We’re very pleased to be able to supply JSOL with two grate kiln pelletizing plants for their Angul location. Metso Outotec is the only equipment manufacturer to offer both the traveling grate and grate kiln technologies for indurating iron ore pellets; each technology offers unique advantages. With these technologies, JSPL will be a global leader in their ability to efficiently produce of a variety of world-class pellet products,” says Chris Urban, Vice President, Heat Transfer Products at Metso Outotec.
Metso Outotec is the world’s leading supplier of grate kiln pellet plants, with more than 50 installations globally totaling over 130 mtpa of production. The Metso Outotec technology produces superior-quality pellets while minimizing overall plant operational expenses.
Discover more about our pelletizing technologies and the grate kiln system on our website.
SKF West Africa’s lubrication and condition monitoring solutions boost uptime, delivering significant savings for Guinean ore mine

SKF West Africa identified a number of lubrication issues while conducting a paid lubrication audit for a long-standing mining customer in the Republic of Guinea. “Our objective with the audit process was to gain a better understanding of our customer’s existing lubrication and maintenance strategy, their lubricant purchasing and Automatic Lubrication System (ALS) management process as well as their environment protection plan,” explains , Lubrication and CoMo Champion for SKF West Africa, Ouattara Yelli Fatou.
The comprehensive audit done by Hassan Missaoui and Yelli Ouattara was conducted on lubrication management as well as on all lubrication products including lubricant and tools. “We also looked at the mine’s maintenance and condition monitoring (COMO) products and strategies,” affirms Fatou. “In addition to the failure of large slew bearings, gearbox oil was overheating. We also noticed a lack of equipment monitoring devices and recognised that our customer needed assistance with lubrication management in terms of best practices and skills.”
The all-inclusive lubrication solution proposed by SKF included an oil storage room, twelve oil conditioning units (OCUs) and 200 System 24 TLSD series lubricators. According to Fatou the oil storage room will improve oil storage, conditioning, dispersing and oil cleanness levels. The OCUs will help to cool and filter gearbox oil to prevent overheating. “To significantly improve bearing lubrication reliability on critical equipment, we recommended our efficient SKF Automatic Lubrication System, some system 24 TLSD and progressive lubrication system.” These automatics lubrication systems are being fitted to a wide range of equipment on the mine site including a badge loader, a stacker, conveyors, car dumpers, motors and gearboxes.
Preventative maintenance is fundamental to maximising production levels as early detection of potential component issues can prevent catastrophic and costly machine failure and unplanned downtime to allow for repair work. SKF therefore suggested an automated machine monitoring system.
Fatou confirms that the SKF West African team has already completed vibration analysis on critical equipment.
Bi-annual shaft alignment services will also be conducted which will include the alignment of more than twelve conveyors and command equipment (motors, gear boxes, conveyor pulleys). SKF West Africa will offer once-off training on ALS understanding and maintenance to assist their customer in applying best practices for optimum results. “We are also in the process of signing a contract with our local SKF Authorised Distributor, SAREF INTERNATIONAL, for consignment stock of bearings for the mine,” confirms Fatou.
“Our turnkey solutions enable us to assist our customer in minimising equipment breakdowns and increasing machine performance, ultimately delivering significant cost savings. We have further helped the mine to decrease operating expenses by reducing oil and grease consumption. The SKF West Africa team is extremely proud of this project as this was the first lubrication audit to be performed in West Africa and we secured a great outcome! This is also a result of successfull team work with our lubrication management team around SKF,” concludes Fatou.
Thickener Optimisation in mineral processing
Integrated online monitoring simplifies the convoluted process of monitoring data, which is central to precise process control in thickeners, in key measuring points. This results in reduction in costs (mainly of energy and flocculants), reduction in waste volumes sent to tailings dam, as well as increase in safety. Ultimately, improved recovery translates into high profitability.
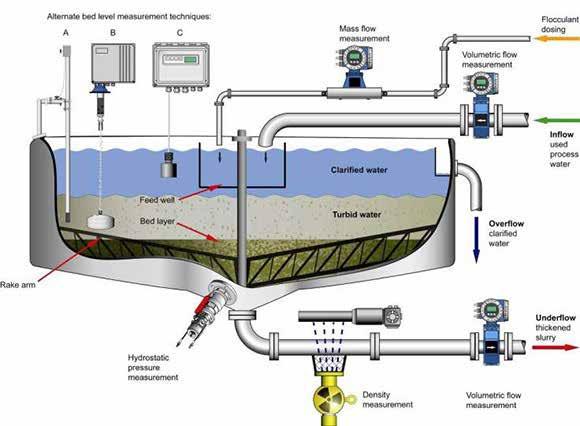
‘Process optimisation’ has become a buzzword in contemporary mineral refining processes, as mine operators are continuously seeking ways of increasing ore recovery as costly effectively, safely and environmentally friendly as possible. Process optimisation is universally regarded as one the established ways of improving physical separation of process water from useful extract or tailings. With reference to thickeners, it has been demonstrated that process optimisation can be attained through accurate measurement of key parameters which enable precise thickener process control.
Ultimately, through process control the following objectives can be met: a continuous and adequate feed, that the overflow is as clean as possible, and that the thickened product has the density required at the time of discharge.
However, for process control to be effective, a number of critical process parameters, which enable the optimisation of thickener efficiency, have to be accurately and reliably monitored. In particular, the following measurements are critical: Rake torque & lift, Bed level, bed mass, Underflow density, underflow rate, Overflow Clarity and Dry solids feed rate.
Integrated online monitoring system
However, the biggest challenge for mine operators is to have all data monitored and controlled to gain an efficient thickening process in plant conditions that are dirty. Hence, suitable monitoring equipment has to be selected and installed. There has been growing evidence in the effectiveness of Endress + Hauser’s online integrated system enabling mine operators achieve precise process control in thickeners.
By examining the common shortcomings or challenges experienced with conventional measurement techniques, one would appreciate better the relevance of online integrated online monitoring as an alternative.
Common challenges with conventional measurement techniques
Wrong measurement of the parameters using conventional techniques can be very costly. Commonly, this surfaces through problems encountered in bed level and bed mass. In the ‘bed level’, which is the interface between the aggregated solid material and process water, incorrect measurements can cause three scenarios - water being drawn out through the underflow, sludge spilling over in the overflow, in addition to incorrect flocculation. These events result in unnecessary expense due to wasted flocculent or reprocessing costs. Lower mass of the bed mass or density of the settled sludge can result in more process water being pumped out of the thickener’s underflow.
Key aspects of the parameters
Key aspects of the six parameters to be measured for process control to be optimised have to be identified.
• Hydraulic rake drives
In hydraulic rake drives, through measure hydraulic pressure, common process problems like insufficient underflow pump rate or blocked discharge outlets can be monitored.
• Bed level
The “bed level”’ is the interface between the aggregated solid material and the process water, which indicates the position of the settled bed. Incorrect measurements in the bed level can lead to water being drawn out through the underflow, sludge spilling over in the overflow or incorrect flocculation. There is unnecessary expense involved in all cases due to wasted flocculent or reprocessing costs. This necessitates monitoring data from all critical measuring points at a concentrator.
• Bed mass
Bed mass is the density of the settled sludge. The rule of the thumb is: The higher the density, the less process water is pumped out of the thickener’s underflow.
Thus, through the optimisation of water content in the underflow, recycling of process water can be maximised, while ensuring that the underflow slurry is sufficiently liquid to be managed by the underflow pump.
In cases where the underflow is to be sent to a tailing dam, negative environmental impact through leaching is reduced. That is why, it is important to report the inventory of settled solids inside the thickener.
• Underflow density
Monitoring underflow density is vital to control the final percentage of solids. Underflow density is central to maintaining operational stability and it prevents tailings from blocking in the thickener discharge outlet.
• Underflow rate
Another aspect that should be monitored is the dry solids mass flow rate of the total tailings slurry is destined for disposal. Furthermore, constant outflow density and volumetric flow measurements can be fed back to the variable speed drive controlling the outflow pump. The data gathered can be used to optimise pump speeds, reduce wasted energy and improve efficiency. Thus, the combination of density and volumetric flow rate provides an integrated mass flow rate which is useful for accounting of mineral recovery as well as waste.
• Overflow Clarity
To ensure clarity of the recovered process water, accurate volumetric measurement of the thickener’s inflow is vital. Essentially, the in-feed flow rate can be controlled based on high clarity of the overflow. So, the clearer the outflow, the faster the inflow feed rate which leads to optimised thickener throughput. When this is combined with the mass flow measurement of the flocculent, precise ratio control of the flocculent dosing is achieved.
• Dry solids feed rate
Through accurate measurement of flocculent mass flow in thickeners, precise dosing pump control is realised. From the measurement, concentrations of overflow solids can be obtained, which allow water to be reused or comply with government regulations if the overflow is to be discharged. For instance, in South Africa, recycled water containing 200 mg/L to 1% solids is generally acceptable. In the end, together with other parameters, measurement reduces flocculant usage, which optimises process costs.
Thus, the combination of density and volumetric flow rate provides an integrated mass flow rate which is useful for accounting of mineral recovery as well as waste.
Endress+Hauser’s integrated online integrated as an alternative
Endress+Hauser’s integrated online package has proved to optimise concentrator efficiency in demanding conditions. The instrumentation for level, pressure and flow comprises: • Prosonic T FMU30 ultrasonic level sensor measures and controls the rake height • Cerabar M monitors the rake torque • Promass F 200 or Dosimass coriolis flow meter doses flocculant in relation to bed mass • Cerabar M PMC51 with retractable cleaning assembly monitors bed mass • Promag 55S and Gammapilot M measures the underflow, slurry density and solids concentration
These instruments allow the measurement of the parameters in the following ways: • Rake torque & lift: generates either a shutdown or the rake lift to lower the torque. • Bed Height: reports the position of the settled bed. This feedback is analyzed and sent back to alter the flocculant gram/tonne solid feed set point. • Bed Mass: Reporting the inventory
of settled solids inside the thickener is done with a pressure transmitter that senses the rising bed mass. • Underflow Density: To control the final percentage of solids, a non- invasive nucleonic density meter is mounted along the underflow outlet pipe work. • Underflow rate: A volumetric in-line flow meter can interact with a density meter and the flow meter presents a dry solids mass flow rate of the total tailings slurry volume that goes to disposal. • Overflow Clarity: For quality assurance and final confirmation of the water clarity, a turbidity sensor monitors the solid particle carry over. • Dry solids feed rate: a pair of nucleonic density and inline flow meter can be installed. This predicts the flocculant dosing based on what dry solids feed is expected to enter as well as reacting to what happens with the bed level and bed mass.
Enormous benefits
Mine operators that have used Endress+Hauser’s integrated online monitoring package bear testament have confirmed benefiting in the following ways: • Underflow density increase from 55% to 60 -66% • Improved compliance with environmental regulations • Better water utilisation • Reduced cyanide to tailings • CTD beach angles increased from zero to ~2 • Significantly enhanced tailings storage capacity • Reduced risk of tank overflow • Cost reduction in flocculent dosing • Precise measurements of slurry underflow rates • Accurate online calculation of solids content • Better water utilisation
Accurate measurement, increased profitability
From the foregoing, accurate measurement of all of these important parameters using an online integrated monitoring allows precise thickener process control which results in significant increases in thickener efficiency. These efficiency gains translate directly into overall refining process cost reductions and increased profitability.
Quarries move with technology as better times beckon
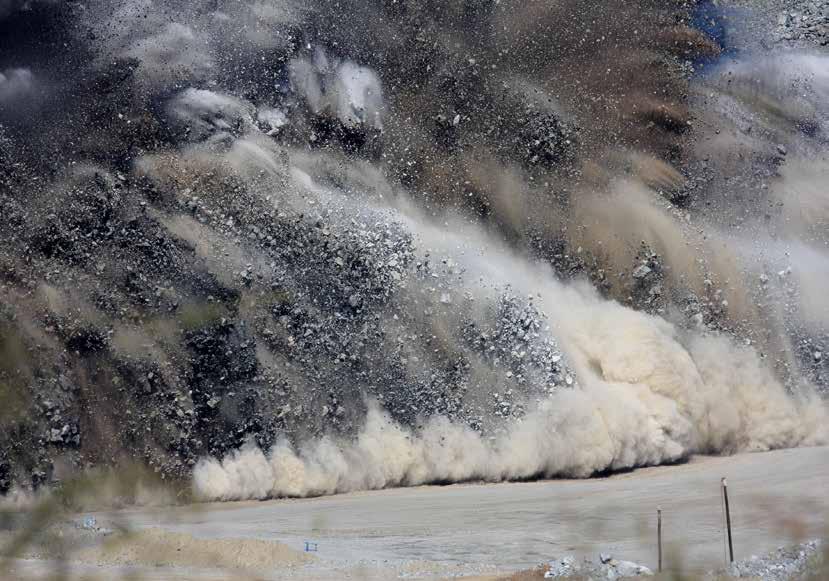
Apositive tone at the recent Institute of Quarrying Southern Africa (IQSA) conference is giving hope that the region’s economy is recovering, according to Tinus Brits, BME’s Global Product Manager – AXXIS™. At the event, Omnia group company BME was showcasing its new AXXIS Silver™ digital initiation system, which was specifically developed with quarrying in mind. Over time, electronic detonation technology has become steadily more popular in the quarrying sector, said Brits. He noted said the presentations at the IQSA event provided an encouraging picture of emerging economic opportunities – especially in road construction, which relies on quarries for aggregate and other building material. As plans were implemented to repair national infrastructure and roll out new projects, contractors were expected to become much busier this year.
“There are definitely improvements in the performance of a range of sectors, and it was exciting to hear that organisation like the South African Roads Agency Limited (SANRAL) had a strong pipeline of projects,” he said. “As quarries position themselves for the growing demand, they are also looking at the efficiencies of their operations – which is where BME makes an important contribution.”
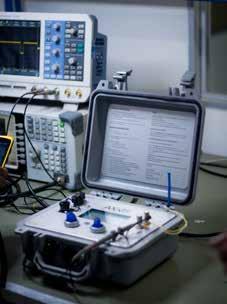
He sees more quarry managers moving toward newer blasting technology, for a couple of key reasons. As quarries age, areas to be blasted can become more challenging, requiring that blasting techniques and equipment become more accurate, flexible and controlled. There is also a cost factor related to energy consumption, where rising electricity prices are incentivising energy-efficiency.
“Quarries want their primary blasted rock to be optimally fragmented, so that their crushers operate as productively and efficiently as possible,” he said. “A presentation at the IQSA conference estimated that the added cost of secondary blasting or breaking of large boulders could reach four times the cost of the initial blast.”
This is where electronic detonators – and the suite of digital tools that accompany this technology – allow quarries to achieve a higher quality of blasts, with better results. Conference visitors showed considerable interest in AXXIS Silver™, he said, which is a slimmeddown version of BME’s flagship initiation system AXXIS Titanium™.
According to Bennie van Nieuwenhuizen, BME’s AXXIS™ quality manager, AXXIS Titanium™ allowed large blasts of up to 20,000 detonators, while AXXIS Silver™ boasted the same high levels of safety but are aimed at smaller operations.
“Our existing customers operating our AXXIS GII™ system are enthusiastic
about moving up to AXXIS Silver™ – and we also received considerable interest from potential customers who would like to see the new system demonstrated and tested on their sites,” said Van Nieuwenhuizen. For those quarries still using non-electric detonation methods, the step to take them to AXXIS Silver™ was easily manageable. “There has been a steady annual conversion rate of quarries from non-electric detonators to electronic detonators, of about 12-14%,” he said. “Within the next five years, it is likely that most quarries will have moved over to electronics.”
AXXIS Silver™ retains all the stringent safety features that has made AXXIS Titanium™ so popular, including an application-specific integrated circuit (ASIC) chip in the BME detonators. Among the added benefits of the ASIC is more internal safety gates against stray current and lightning – which enhances safety levels and allows for inherently safe logging and testing.
“The new system speeds up the blasting process, as the logging, testing and programming is done with one unit and requires only one visit to the blast hole,” he says.
The AXXIS Silver™ initiation system integrates with BME’s Blast Alliance suite of digital tools, including its BLASTMAP blast planning software, XPLOLOG data logger and online dashboard, and the Blasting Guide App for Android devices. This allows customised solutions that can be implemented with speed, accuracy and safety, he said.
“There are also specific advantages for quarries that we have built into AXXIS Silver™, such as the thinner wire which we’ve developed to suit small-diameter waterlogged blastholes,” he said. “This results in a perfectly straight wire down the hole, so you know exactly where the booster is – without compromising on the line strength.”
In addition to being fit for purpose and quick to install, the reduced thickness also translates into a cost benefit for the customer.
Rosond appoints new Operations Director to lead its expansion
Drilling technology solutions provider Rosond of Midrand has appointed Clement Rikhotso as its new Operations Director. This follows Clement initially joining as a project consultant in 2019 to assist Rosond with the onboarding of 27 state-of-theart drill rigs and crew at the Kolomela and Sishen mines of Anglo American’s Kumba Iron Ore in the Northern Cape, as well as its entry into Botswana, where three rigs are currently in operation at Debswana’s Jwaneng diamond mine.
In his new role, Clement is accountable for all the company’s surface exploration drilling activities, in addition to consolidating the company’s mission as the leading mining and geoscientific solutions provider in Southern Africa. Clement’s mining industry career spans 27 years, most of it with the Anglo American and De Beers Group, reflecting his consummate technical and leadership experience in applied project management, drilling, mineral processing, analytical laboratory, mineral resources management (MRM) and engineering geosciences.
He previously served as Executive Director on the boards of four De Beers companies in South Africa, Botswana, and Angola. Clement has been involved with multidisciplinary capital projects across the mining value chain throughout
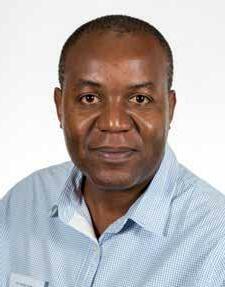
Clement Rikhotso new Operations Director at Rosond
Southern Africa, and as far afield as Canada and Russia, some of which have become profitable mines. He holds a Technical and Financial Appraisal of Mineral Projects Certificate from Imperial College London, a Programme for Management Development (PMD) certificate from GIBS (University of Pretoria), and a BSc Geology Honours (UCT) degree.
“The disciplines of geology and drilling are interrelated. Drilling is carried out to discover new mineral deposits or to evaluate existing mineral resources that are being mined. This is where drilling comes into play as a technique to define these mineral resources,” explains Clement.
“Both disciplines are a keen passion of mine, and I look forward to realising the synergy between the two and application thereof in my new role to ensure our clients’ objectives are met.”
Clement adds that Rosond’s newgeneration automated drill rigs are assisting the mining industry to eliminate injuries and transform to Industry 4.0 as their advanced telemetry systems provide a rich source of data for further machine learning analytics and better business decision-making.
“Although our services are underpinned by traditional drilling, we see ourselves more as an advanced solutions provider to the minerals industry.”
Rosond MD Ricardo Ribeiro says that Clement will play a key role in consolidating the company’s future expansion plans. “We welcome Clement to the Rosond family, and look forward to tapping into his experience and expertise as we continue along our growth path. We have a clear strategy in place that Clement will help us realise as we adapt and evolve.”