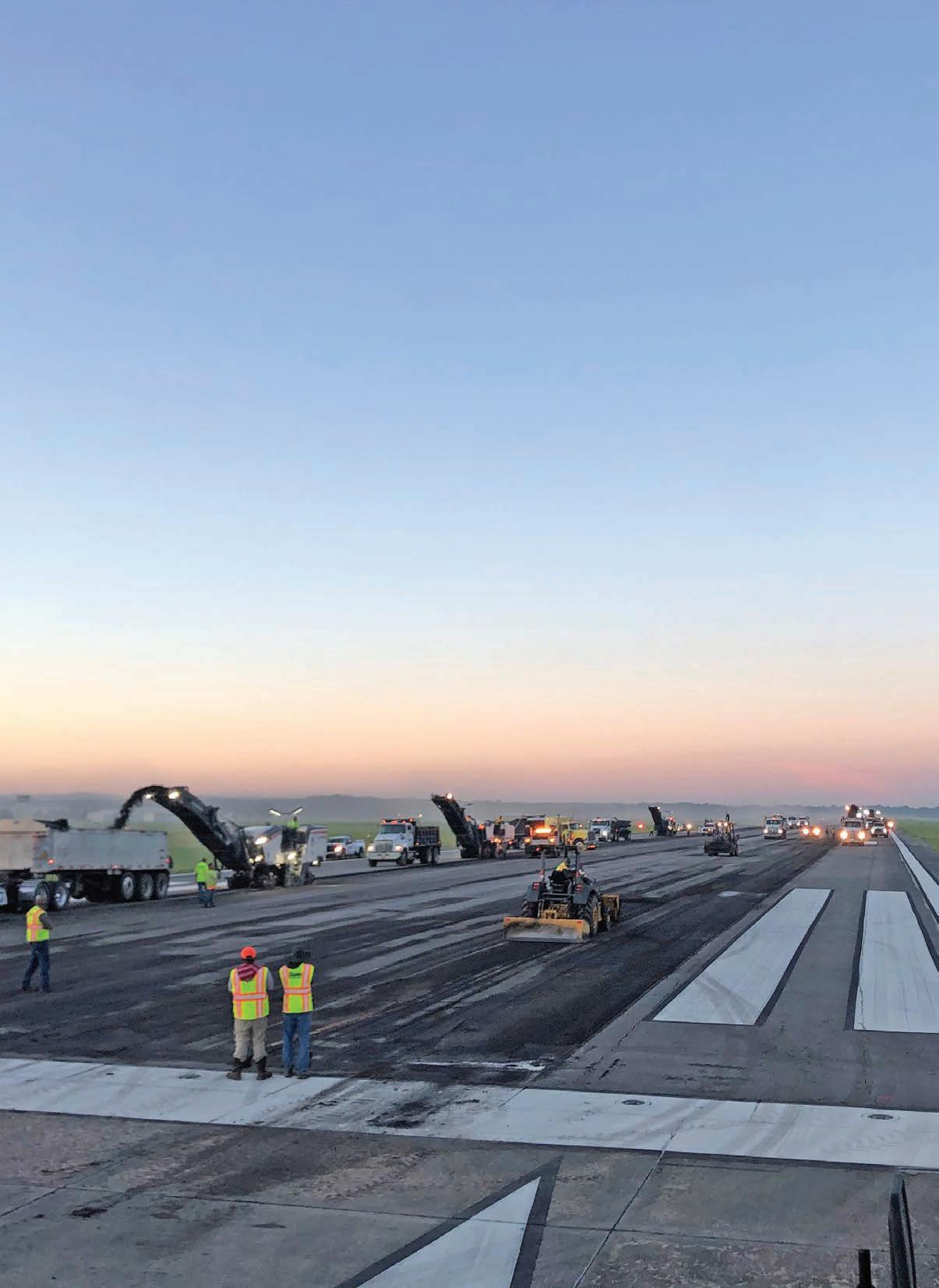
14 minute read
Dunn Roadbuilders coordinates six mills and uses one paver to help reconstruct Key Field airport runway in Meridian, Mississippi
Preparation “Key” to RUNWAY REHABILITATION PROJECT
Dunn Roadbuilders coordinates six mills and uses one paver to help reconstruct Key Field airport runway in Meridian, Mississippi
Runway reconstruction projects are not known for being easy. They require extensive planning, extra coordination and an acceptance of risk for delays that might happen during tight timelines. Dunn Roadbuilders knew all of this heading into the reconstruction of Runway 1-19 on Key Field at Meridian Regional Airport and prepared accordingly.
The town of Meridian's Key Field Airport is home to the longest public runway in the state of Mississippi. It had been 20 years since the runway had been worked on and the Airport Authority knew shutting it down for reconstruction needed to happen, but they needed closure time to be minimized. For two years, the Meridian Airport Authority had been planning the rehabilitation of the runway and they knew they had to get it right.
The runway consists of 8,000 feet of asphalt with 1,000 feet of concrete at each end. Dunn Roadbuilders was hired as the prime contractor on the project. They were tasked with coordinating the extensive work that needed to be done. "The asphalt runway was to be milled, then a stress relief layer was needed to eliminate reflective cracking," Teresa McDonald, project management coordinator at Dunn Roadbuilders says.
Meet The Team
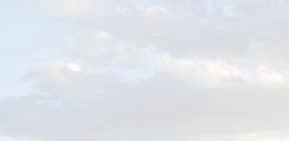
A project of this size needs plenty of help to execute properly. Meridian Airport Authority – Owner Engineering Plus – Engineering Firm Dunn Roadbuilders – Prime Contractor (Asphalt Laydown and Milling) Subcontractors included: • Huey P. Stockstill, LLC – Milling (1 machine) • Mill It Up, LLC – Milling (2 machines) • RJM McQueen Contracting –
Shoulder Material and Stress
Relief Layer • Sunbelt Sealing, Inc. – Joint Repair • Cardinal Grooving, LLC -
Trapezoidal Grooving • Woodall Electric, Inc. –
Electrical / Lighting Adjustments • Gulf Coast Solutions, LLC –
Erosion Control • Hi-Lite Airfield Services, LLC –
Striping / Pavement Marking • APAC – Asphalt Production
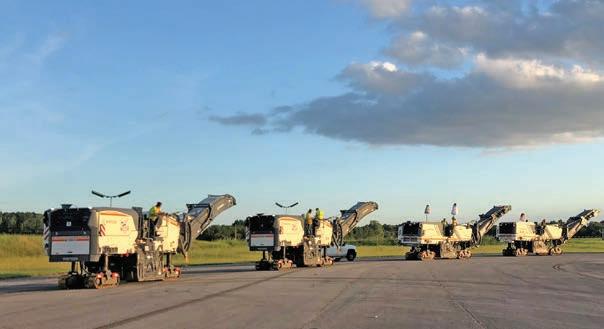
To maximize reconstruction time, Dunn worked with subcontractors to mill in echelon on the project, removing 14,000 tons of material in one night.

"Then asphalt leveling was needed to correct the cross slope. This was followed by an asphalt overlay, shoulder material, runway light adjustments due to the leveling, joint sealant on concrete sections, asphalt grooving and striping."
On August 16th 2021, the runway was closed and work began. For 7 days, 24 hours per day, crews worked and flights resumed as usual on August 24.
MILLING IN ECHELON
In order to maximize their time, Dunn worked with a team of subcontractors to execute the project. Milling of the existing asphalt was done in one shift to expedite the work. There were six milling machines on site, working from 7 p.m. until 8 a.m. the next morning to remove 145,000 square yards of material.
To move this much material in such a short time, Dunn worked with two other milling subcontractors, Huey P. Stockstill, LLC and Mill It Up, LLC, to bring a total of six Wirtgen 220i Milling Machines to the jobsite. "A lot of effort went into pre- planning the project and coordinating milling and trucking," McDonald says. "We ultimately started milling at the center and checked thoroughly to maintain the correct cross slope. A second machine followed behind on the opposite side of the centerline. All of the other machines followed behind and matched the initial first pass cross slope to maintain the correct slope across each side of the 150-ft.wide runway."
Each machine had multiple dump trucks assigned to it and the material was stockpiled on site to improve logistics. In all, almost 600 truckloads of material were removed for a total of 14,000 tons in one night.
“It was very intense work for those 14 hours,” Jason Wooten, vice president of operations at Dunn Roadbuilders adds. “We milled 145,000 square yards and stockpiled it on site to keep our trucks close which allowed our operations to keep moving all night.”
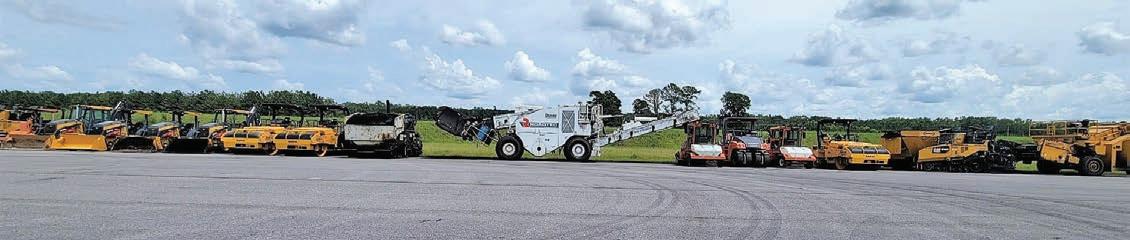

Milling was immediately followed by the stress relief layer, which was performed by another subcontractor, RJM McQueen Contracting.
“The project owners knew there needed to be some repairs done due to cracks in the existing pavement, so we recommended a stress layer,” Wooten says. “That would seal the cracks and after the stress relief layer was performed, it would give relief so the cracks would not reflect through to the new surface. This layer would perform double duty, sealing the cracks and not letting them reflect back to the surface course.”
That was completed Tuesday morning and paving of the leveling course began that night.
“The pavement was 170-ft. wide, but the actual runway was 150-ft. Wide,” Wooten says. “The shoulders on the outside were not at a continuous cross slope so we needed to correct that first and now we have a continuous slope all across the runway.” The leveling course was a FAA P-403 nonpolymer mix.
PAVING BETWEEN RAINDROPS
As with any project, work has to happen around the weather. This is particularly worrisome when your timeline to complete the work is one week. After the stress layer was installed, crews immediately began the process of paving. August 18th, the second day the runway was closed, crews paved 30-ft. of the 150-ft. wide runway.
“We used a 60-ft. contact ski for the centerline with the milling machines and followed that same design on the first pass with the paver,” Wooten says. “That allowed us to achieve smoothness more easily and we did not have any ride disincentives. The contact skis gave us a smooth ride”
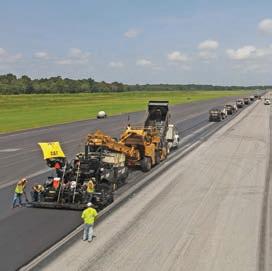
RIGHT RIGHT RIGHT RIGHTValve RIGHTPrice RIGHTNow!Price Now!
Dependable, Economical, Available …
Since 1892, Homestead continues to be the most reliable manufacturer of asphalt valves. With cast iron and ductile iron material options, we offer a complete source of valves for any liquid asphalt application. Our full line of hot-jacketed 2-way shutoff & 3-way diverter valves provide a ready solution to meet your flow requirements. Homestead’s cutting-edge actuation design allows you to easily add actuators to your existing Homestead valves, in-line, without modification. Our fully stocked warehouse of valves and actuators offers you security in knowing that the valve you need is only a phone call away.

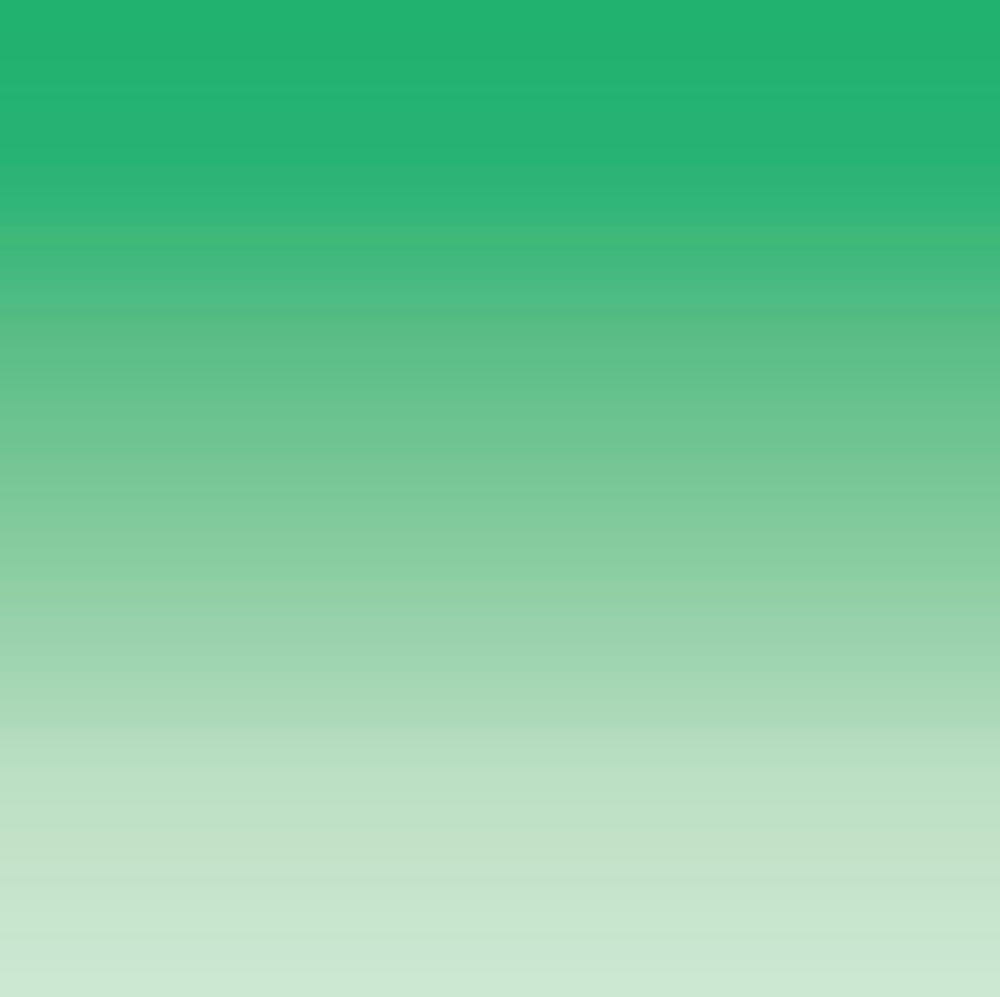
THE ASPHALT VALVE EXPERTS

Valve Types
n Full Port – Standard Port n 2-Way Shutoff and 3-Way Diverter Patterns n 1"-8" Flanged and 1/2"- 4" Threaded n Steam/Hot Oil Jacketed n Transflo Plug n Proportioning Plug
Valve Materials
n Cast Iron – to 450° F n Ductile Iron – to 650° F n High Temperature Seals
Actuator Types
n Pneumatic n Electric n Open-Close n Modulating
®
610-770-1100 asphaltvalves.com
Fax: 610-770-1108 sales@homesteadvalve.com
©2022 Olson Technologies, Inc.
The entire construction team at Dunn was dedicated to working on this project, ensuring the runway was opened on time.

Grant Moves Project Forward
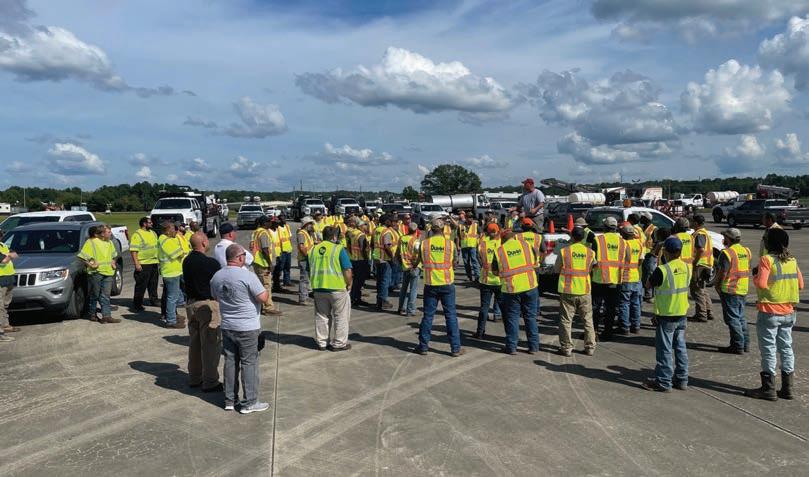
In March, the Federal Aviation Administration announced awards totaling more than $627.7 million in fiscal year 2021 funding for infrastructure and safety projects through its Airport Improvement Program or AIP. These grants are seen as an investment in safety and continued innovation.
In March, it was announced that the U.S. Department of Transportation, on behalf of the Federal Aviation Administration, was awarding grants to 26 facilities across the state of Mississippi and Key Field was one recipient of the funds.
Last paved in 1999, the pavement on the Key Field Runway was in need of repair, but they also wanted to strengthen the runway so it was able to carry heavier loads. After two years of planning, Key Field received a $6.5 million grant to get the work done right away.
“We are excited...to be able to bring the money into the community and hopefully help the economy in the community,” said Meridian Airport Authority president Tom Williams, “but also to keep Key Field as a viable, strong aviation facility for Mississippi.”
The crew encountered challenges however, when rain showers popped up throughout the paving days.
“We had three or four rain delays that cumulatively were 20 to 24 hours," Meridian Airport president Tom Williams says. "We lost a day due to rain because they couldn't pave on a wet surface. The contractor was phenomenal though. They came into this with the right can-do attitude. Everyone has worked together. They coordinated beautifully.”
“Once we got in on Monday, we never left until the work was done the following Tuesday,” Wooten adds. “All we did was stop and wait for the rain to pass, broom and dry the area and start back up.”
Dunn had crews working on the project every hour of the 7-day shut down. They operated two paving crews, one day shift and one night shift, who put down around 2,000 tons each shift using only one paving train for the runway surface course. The highest tonnage in a 24-hour span totaled just over 7,000 tons on Saturday which allowed them to make up time due to rainfall the previous days.
Dunn also made sure they would be able to keep working if any unforeseen breakdowns were to occur.
“We did have backups ready for any breakdowns just in case,” Wooten says. “But reliable and dependable equipment is key to these projects.”


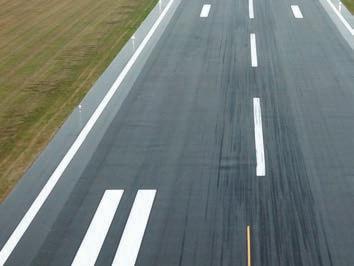
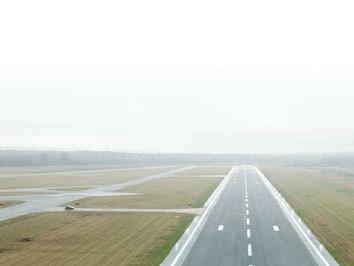

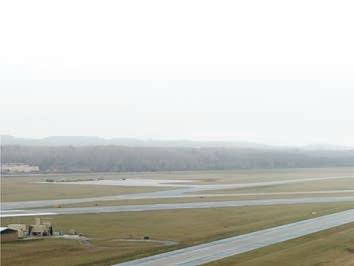
We Have the Equipment to Get Your Job Done! SILOS - PUG MILLS - FIBER FEEDERS Long and Short Term Rentals
Purchase Options Available
Surge Bins Fiber Feeders
USED TO PROCESS FLY ASH CALCIUM CARBONATE CEMENT BAGHOUSE DUST HYDRATED LIME CELLULOSE FIBER
Mineral Filler Silos
EzFloWeighing.com
Contact Us to determine which meets the requirements of your specific application Phone: 952.939.6000
In all, Dunn put down 25,506 tons of asphalt on the runway, finishing the project on time, despite the weather and logistical challenges. The surface course was a standard FAA P-401 Polymer mix supplied by APAC of Meridian.
“APAC was geared up and they gave us their plant for the week because we were running day and night,” Wooten says. “Our whole company was dedicated to this site and there was a lot of coordination. The preparation and coordination with the Meridian Airport Authority, Engineering Plus, suppliers, subcontractors and crews in the beginning is what set the stage for this to be a successful project. I am really proud of our team that worked on this project; hard work, commitment and teamwork made this success possible. It was an honor to be a part of a team that was able to execute such a large project in a very short amount of time.”
For more information on airport paving, visit ForConstructionPros.
com/20999310
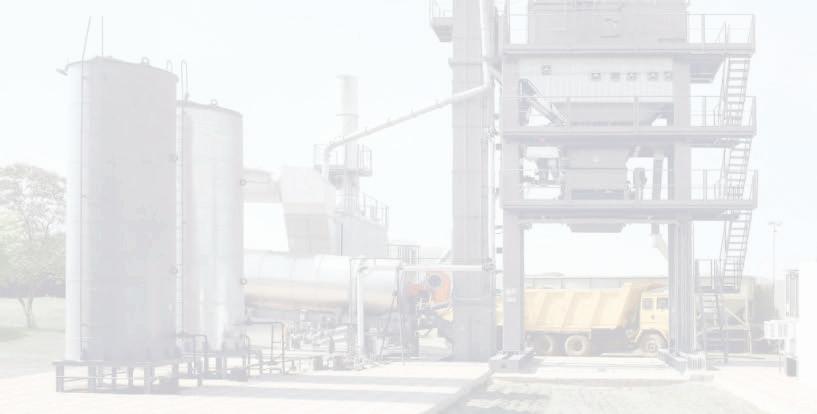


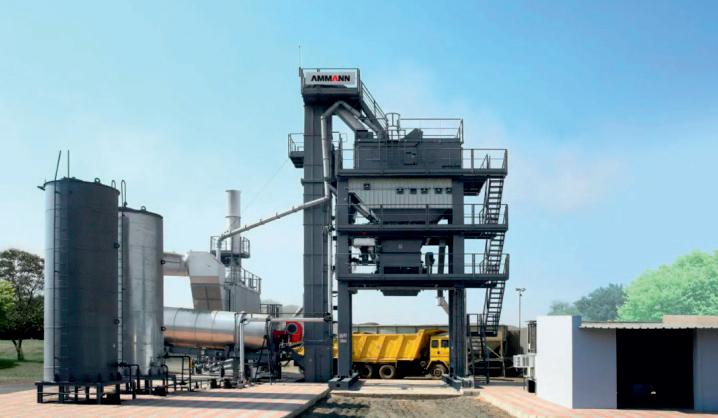
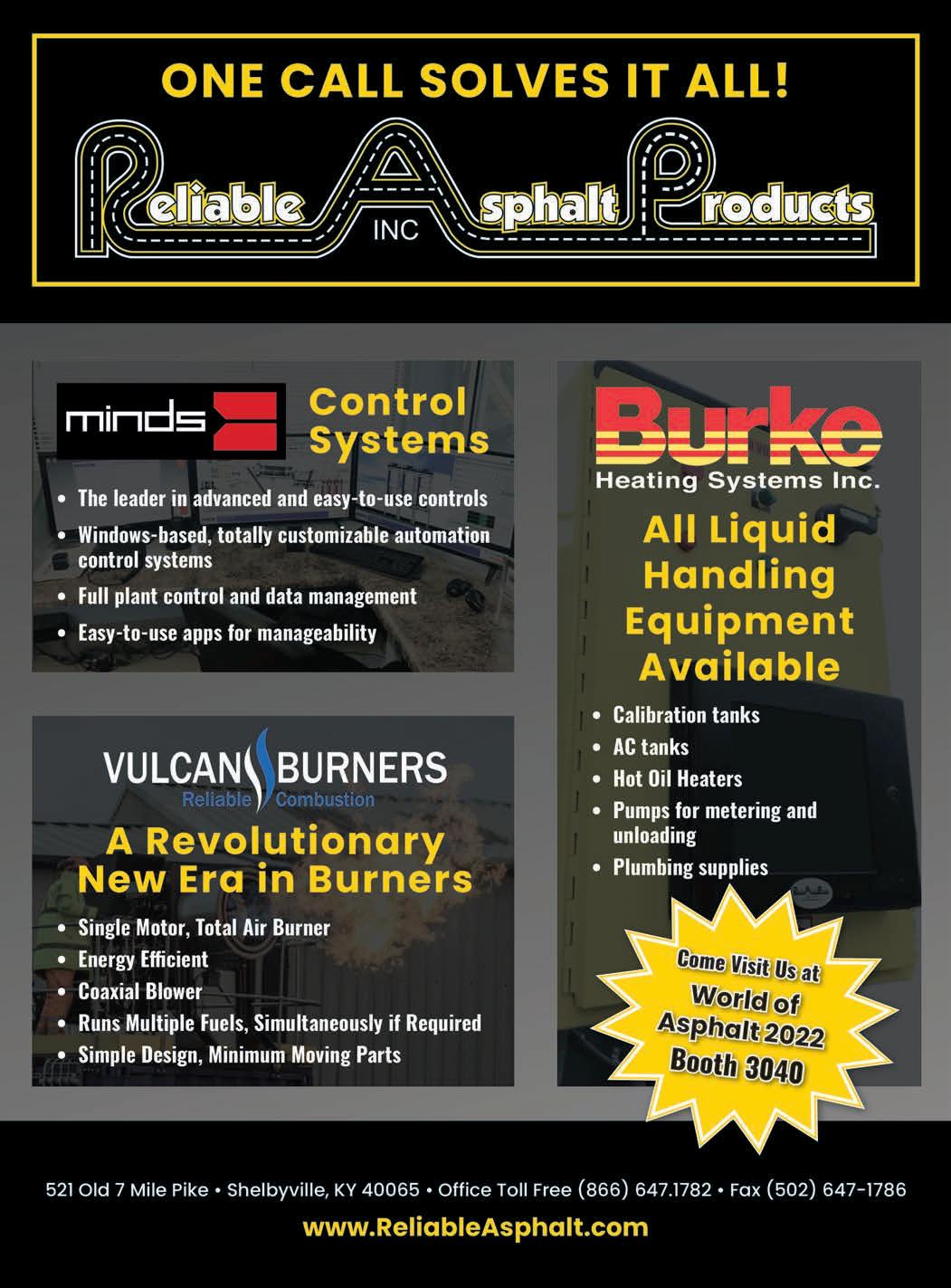
AIin Construction: Beyond Autonomous Machines
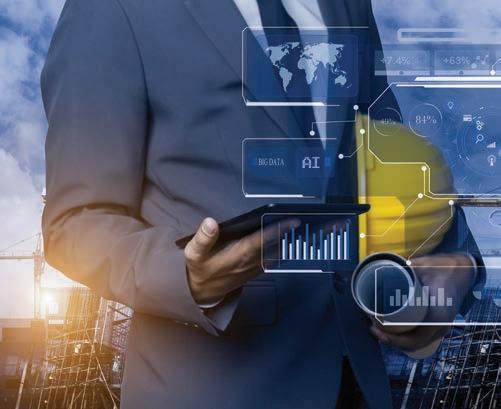
SOMKID/ AdobeStock Artificial intelligence is all around us. Here’s how it is being used today to improve construction change orders, jobsite safety, equipment maintenance and reduce labor demand
AI , short for artificial intelligence, is practically everywhere in our personal lives. Did you ask Siri or Alexa a question today? Did your smart thermostat adjust the temperature in your house as you woke up this morning? Did Netflix recommend a new show when you settled down on the couch? These are all examples of AI in action.
Just as AI is becoming an integral part of our daily routines, it’s turning up more often on the job, too. Your mind may jump first to semi-autonomous machines. That’s a great example of AI in construction, but it’s not the only one. Here are five other ways to incorporate AI into your projects to improve safety, reduce costs and enhance productivity: • Create virtual project duplicates.
Many building information modeling (BIM) systems use AI to convert information from designers, architects and engineers into a virtual duplicate of the site or building under construction. By creating a single design for all project teams to follow, BIM reduces the time and costs associated with changes and rework. It also makes it easier to create timelines, estimate costs and predict building sustainability more accurately. And if modifications do occur, AI can do what other building design programs cannot — update plans in real time. • Monitor site security and safety.
Traditional cameras often use motion sensors to trigger alarms, but debris, stray dogs and even birds can trip them. Integrating cameras with AI lessens the chance of false alarms. AI can recognize a person on camera and alert authorities to investigate, preventing damage and theft of equipment and materials. You can also use facial recognition tools to monitor unsafe behavior on-site. AI can identify hazardous conditions from videos and photos and report them to you, so you can tailor safety briefings or operator training to address any concerns. • Direct traffic in real time. Not only can onboard AI systems alert equipment operators to potential collisions with structures or other equipment, but they can even learn how people move around on-site over time. You can use that information to optimize scheduling and reduce
congestion. Better traffic flow means more efficient operation and fewer accidents that could cause injuries, damage machinery or slow down the work. • Predict maintenance. Rather than scheduled maintenance that requires servicing equipment at set times,
AI-enabled predictive maintenance uses sensors and performance data to determine the most optimal schedule. That means no piece of equipment gets unnecessary servicing or waits until it breaks down to receive upkeep. Avoiding unnecessary maintenance frees those in charge of repairs for other tasks and keeps valuable equipment working, reducing costs and downtime. • Precast components. AI systems can supervise the manufacturing of precast components off-site while your team tends to more important jobs on location. Once completed, precast pieces can be shipped to your site, where experts can install them in the field. Using AI to make better use of your skilled workers is a smart way to deal with labor shortage issues and complete tasks more efficiently.
Clearly, there are plenty of ways to put artificial intelligence to work in construction — these five examples are just the tip of the iceberg. AI is no longer the “future” of work. It’s here today and delivering big advantages in production, safety, cost-efficiency and more.
For more information on AI and road maintenance, visit
ForConstructionPros. com/21103212
Lonnie Fritz is a senior market professional, construction at Caterpillar Inc.
BUILT TO CONNECT
Efficiency and Productivity

Designed with safety and operator comfort in mind, the Shuttle Buggy® SB-3000 material transfer vehicle features adaptive cruise control, bright LED lighting, four-wheel steering for easy transport and groundlevel maintenance access for added convenience. Operators can rely on clear sightlines and the ground operator is safely protected inside the structure of the machine. The Roadtec SB-3000 is the perfect blend of traditional craftsmanship and modern technology.
BUILT TO CONNECT
Connection is at the heart of everything we do
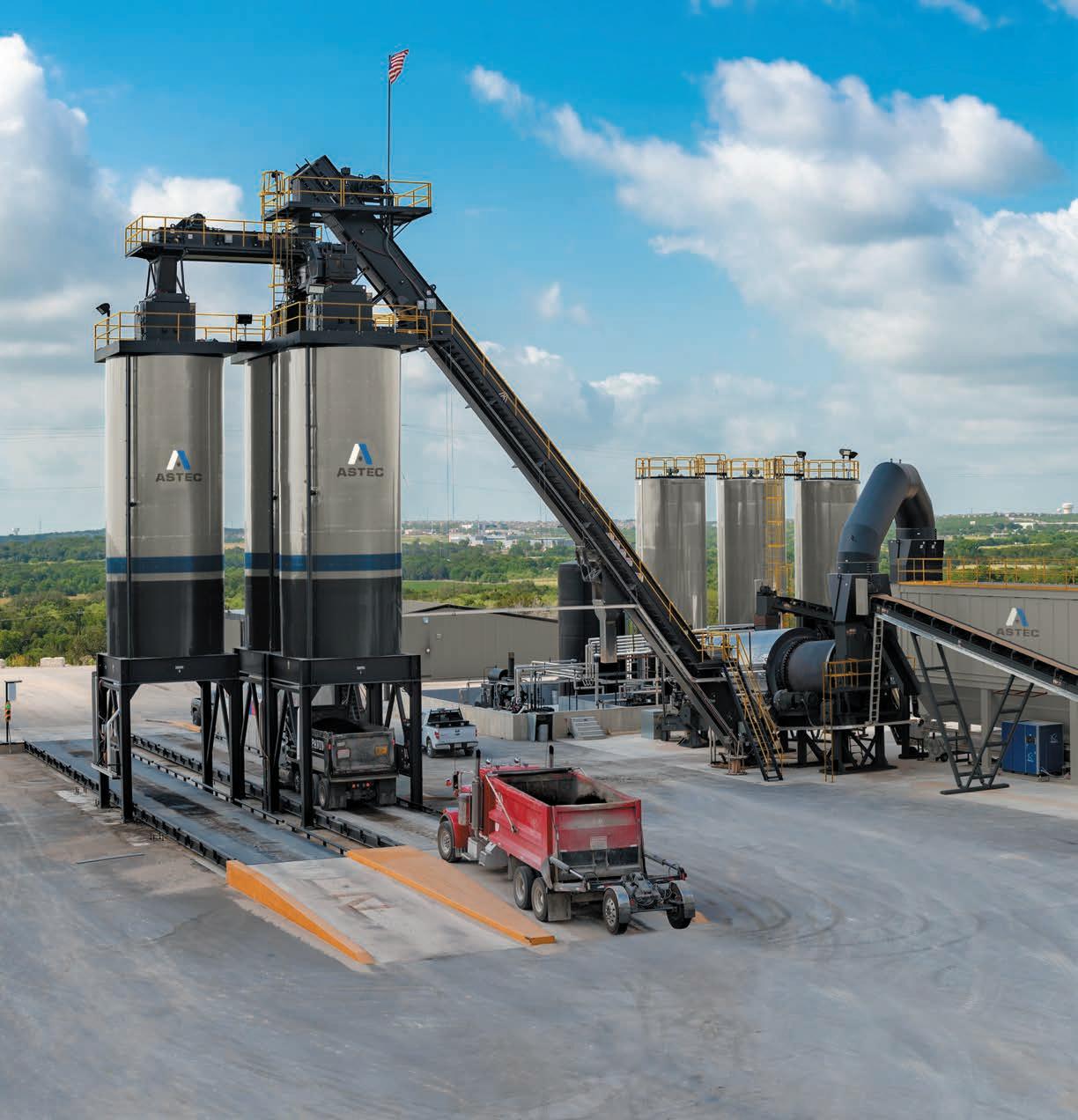
The primary use for asphalt is creating pavement for building the roads that connect goods and services to their markets, people to their communities and families to each other. ASTEC asphalt plants are essential to building and maintaining these vital connections. That’s what drives us to design, manufacture, and sell innovative, efficient, and reliable equipment. And that’s what inspires us to connect to our customers through knowledgeable sales, receptive engineering and responsive parts and service.