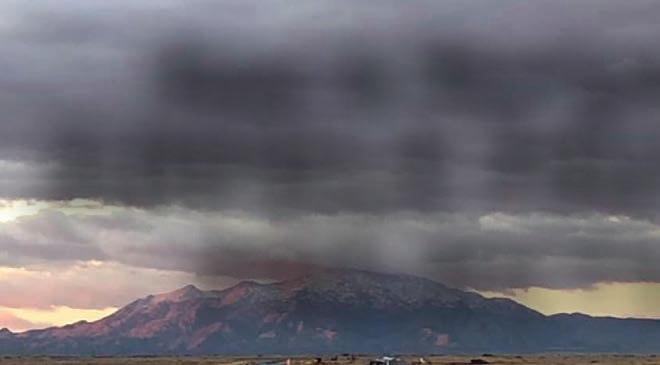
7 minute read
How to Navigate Airfield Paving Projects
Attention to detail and a focus on quality are critical for successful airfield paving
With nearly 85 percent of all airport runways, taxiways, and aprons constructed from asphalt, airfields present a significant opportunity for asphalt contractors willing to tackle the quality demands required to meet stringent airfield pavement specifications. To put the market segment into perspective, U.S. airfields have approximately 460 million square yards of paved surface - or the equivalent of nearly a quarter of surface area of the U.S. Interstate highway system.
But, paving airfields is not for the faint of heart. “Airfields are significantly different from typical road construction,” notes Mark Blow, P.E., senior regional engineer with the Lexington, KY-based Asphalt Institute. He says airfields face much heavier loading than roadways, while being traversed by aircraft with much higher tire pressure than cars and semi trucks. These factors drive the need for higher quality construction materials and tighter construction tolerances.
Paving has to take place quickly and during off peak hours because airports depend on the landing fees that are collected each time a plane takes off or lands. Work must often be scheduled in the short window between the last flight of an evening and the first flight of the next day.
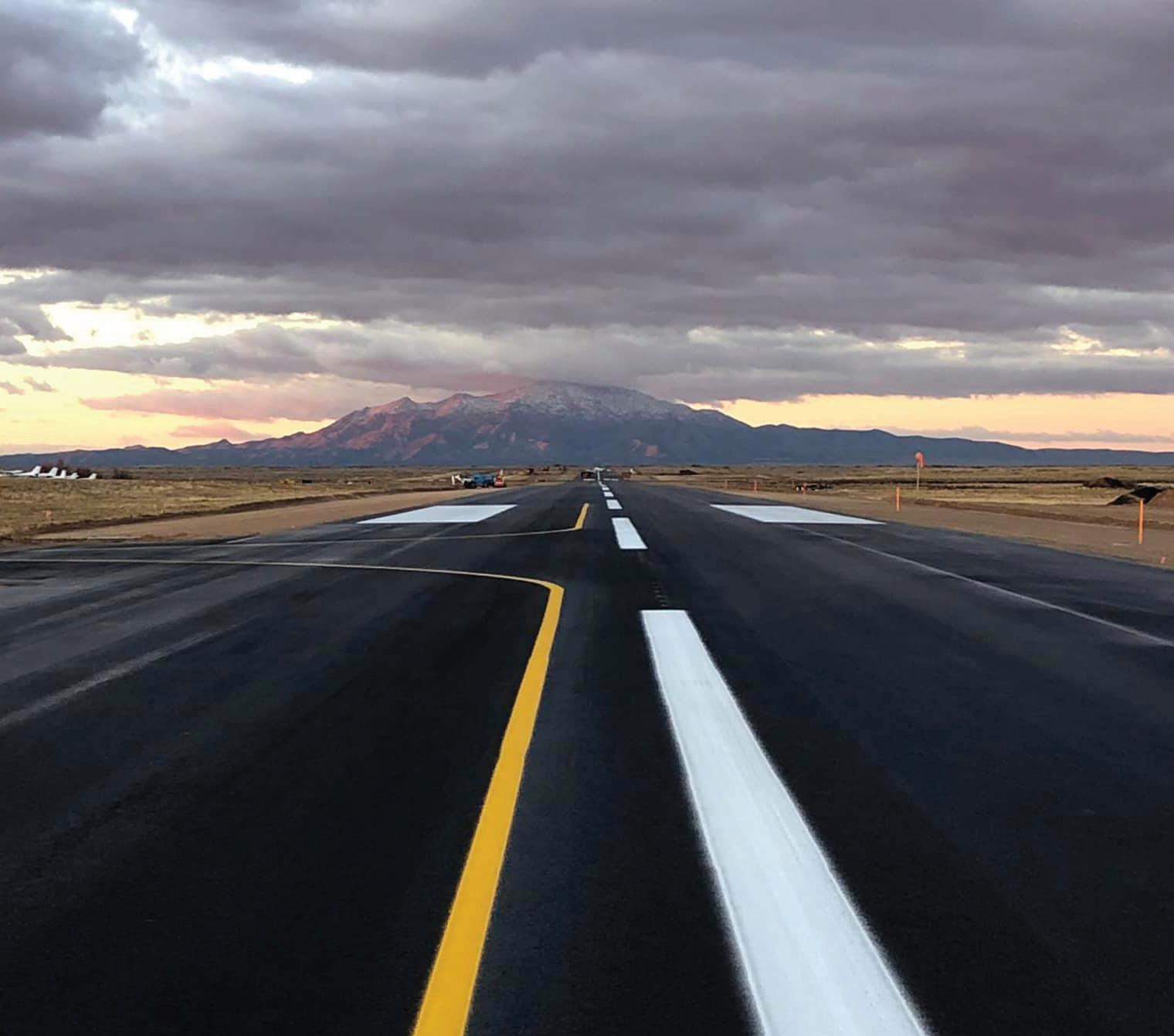
USE QUALITY MATERIALS
Deteriorating pavement conditions are the most likely trigger for airfield pavement projects. “Foreign object debris (FOD) is a huge issue in the airfield world,” Blow says. “It is quite often a parameter that triggers
Deteriorating pavement conditions are the most likely trigger for airfield pavement projects, aimed to help prevent foreign object debris (FOD).
rehabilitation of a runway.” FOD can occur if there is any cracking, raveling or spalls in the pavement. The loose material can be picked up by aircraft engines and cause significant damage.
Once conditions necessitate rehabilitation, airfield projects are typically funded via Federal Aviation Administration (FAA) grants. To receive those funds, which amounted to $3.2 billion in the last year available, paving projects must meet FAA guidelines, with the guiding specification being FAA P-401.
Historically, all airfields had to meet the requirements laid out in P-401. With more recent updates to the specification, however, smaller airfields, such as those with aircraft under 30,000 pounds, may now incorporate state DOT paving specifications for airfield pavements with minimum changes. Midsize airfields, with aircraft from 30,000 to 60,000 pounds, may be allowed to use state specification materials with the appropriate FAA modification of standards. Airfields with larger aircraft must continue to conform to the original specifications.
Contractors should use a quality crushed stone with a focus on proper material gradation. Some airfields are paying increased attention to the aggregate’s LA Abrasion rating to ensure better performance and reduce pavement shoving, which can occur when the asphalt surface course slides over the base course of the pavement.
“You have to use better materials,” Blow says. “You want as long a life of pavement out there as you can get because you don’t want to have to shut down an airfield.”
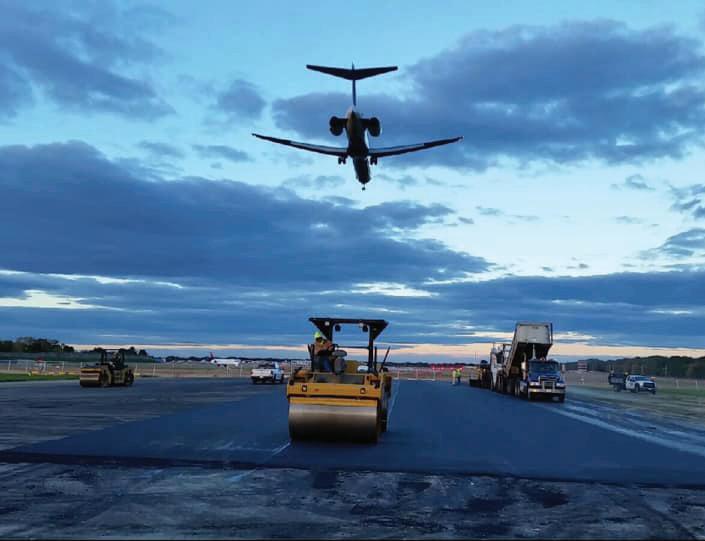
FOCUS ON COMPACTION RATES
One key difference between highway and airfield pavements relates to compaction. The amount of compaction required in airfield pavements is significantly higher, Blow says, and failure to meet compaction requirements includes stiff penalties.
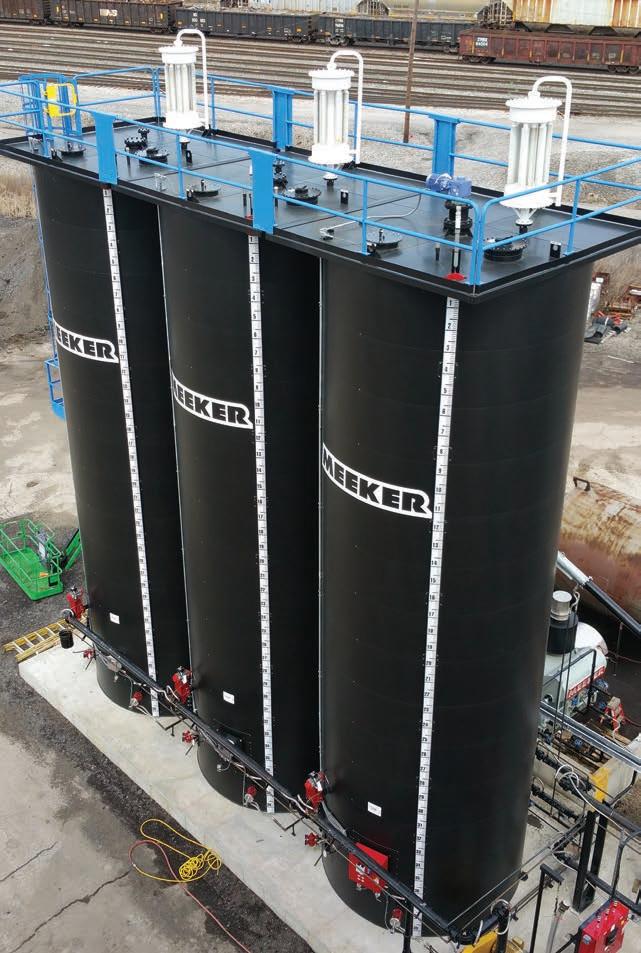
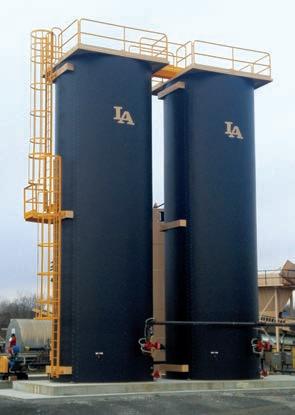
Material density is first tested in the lab to determine the theoretical maximum density, or TMD. Specifications require the contractor to meet the same density as achieved in the lab when the mix was designed. If the average mat density falls below 96 percent, it must be removed and replaced at the contractor’s expense.
“You have to pay attention to what you’re doing,” Blow says. Typically, the pavement will be rolled faster and with more repetitions than a highway pavement. When using unmodified asphalt binder, the use of pneumatic rubber-tired roller may be helpful during intermediate compaction. Proper lift thickness is critical in achieving density in the mat. Paving lift thickness must be no less than three times the nominal maximum aggregate size (NMAS) of the mixture. Four or five times the NMAS is better and will help provide a tighter surface that is more dense and less permeable.
“You just have to have a much tighter operation and pay attention to what
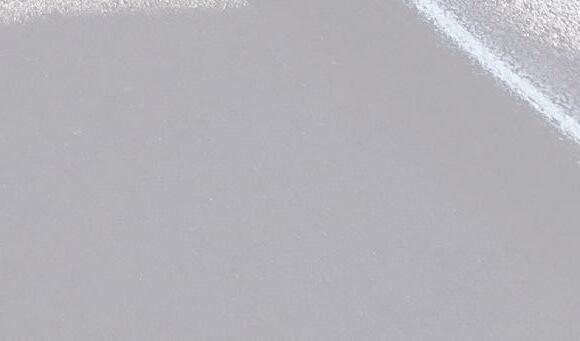
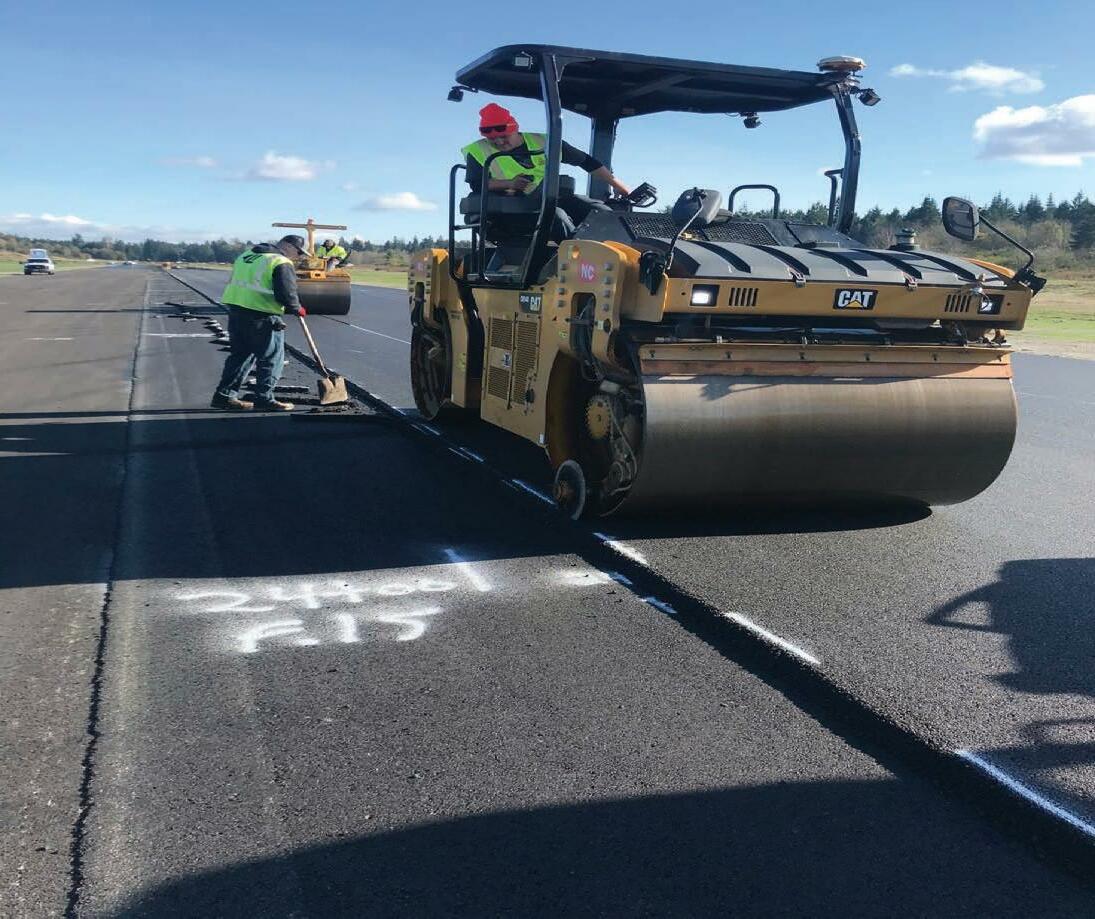
Proper compaction is critical, and subject to stiff penalties. If the average mat density falls below 96 percent, it must be removed and replaced at the contractor’s expense.
Engineered Innovation.
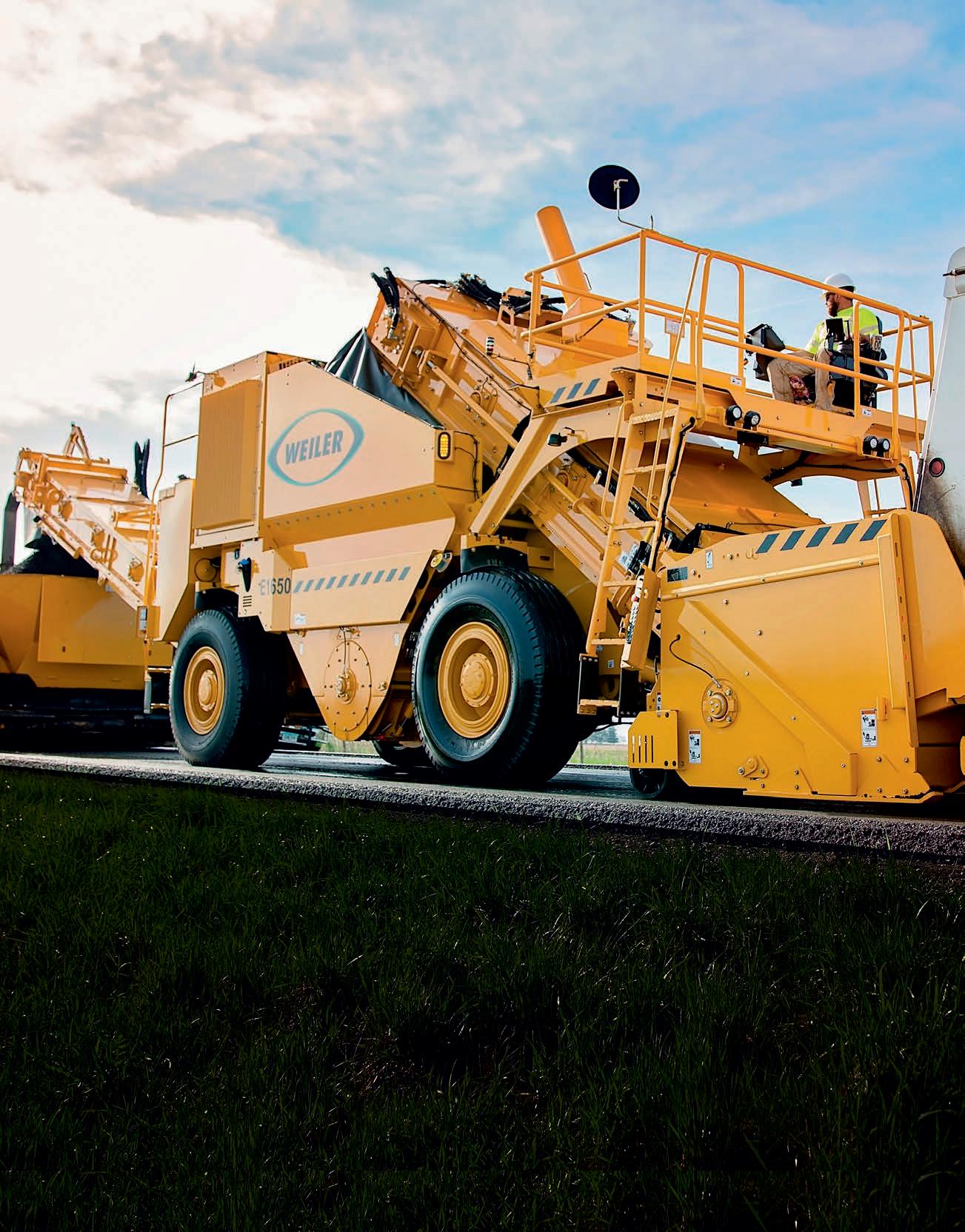
From innovative designs to Caterpillar dealer service and support, Weiler is paving the way to success for contractors across North America. Weiler’s material transfer vehicles, commercial pavers, road wideners, windrow elevators, static split-drum compactors, soil stabilizers, rock drills, tack distributors and front mount screeds are engineered with innovative features to increase productivity while reducing operating costs. Weiler equipment is sold and serviced exclusively at Caterpillar dealers throughout North America.
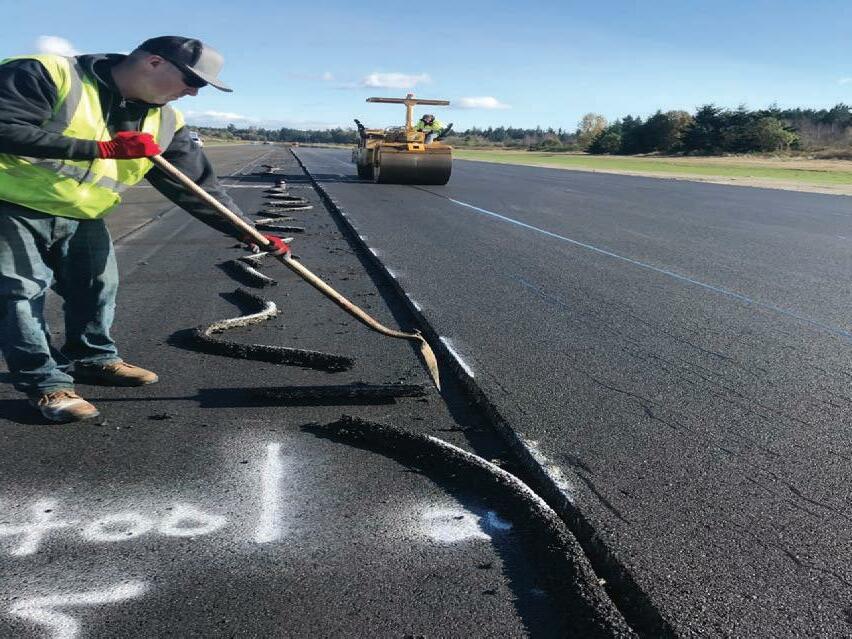
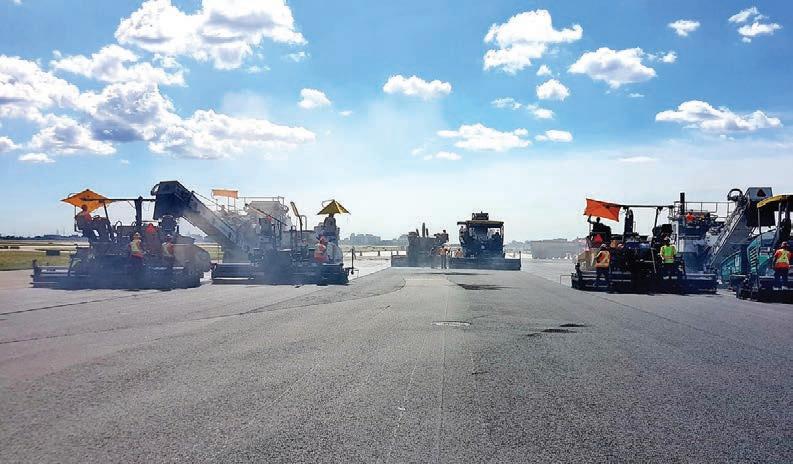
To prevent future FOD concerns, the FAA requires all unconfined longitudinal joints to be cut back 6 inches from an unconfined edge. Many use a cutting wheel attached to the drum of a roller.

you’re doing to get that density,” he advises. Monitoring density throughout the process using a density gauge is essential in meeting specification compliance.
PAY ATTENTION EDGES AND JOINTS
When compacting a first pass of asphalt that is not confined, the roller should overhang the edge of the unconfined material by 4 to 6 inches during compaction. It is very difficult to achieve the specified density at a longitudinal joint. In order to prevent the possibility of a permeable joint, that could eventually lead to future FOD problems, the FAA requires all unconfined longitudinal joints to be cut back 6 inches from the unconfined edge. Many contractors use a cutting wheel attached to the drum of a roller to trim the outside six inches of pavement.
When rolling the first pass on the confined side of a longitudinal joint, the entire drum should be on the hot mat with the roller edge approximately 6 inches to 1 foot from the joint. On the second pass, the hot side can be compacted by overlapping the joint which allows the maximum amount of compactive effort to be focused on the 6 to 12 inches of material directly adjacent to the longitudinal joint.
It is easier to cut back material at paving joints while the mix is warm. It is also critical to cut straight, so Blow recommends using stringline and equipment that is well controlled or with a long wheel base to achieve that cut. Some pieces of equipment, such as a skid steer loader, make it very difficult to achieve the straight, clean cut required for longitudinal airfield joints.
USE A FUEL-RESISTANT MIX WHERE NEEDED
One common trouble spot for airfields can be along aprons or other areas that are subject to fuel spills. Coal tar sealers, which are resistant to fuel denigration, have often been used in these areas. A newer trend, however, is the use of the fuel-resistant asphalt found in the P-404 spec. It incorporates a high percentage of highly modified liquid binder, such as PG 92-28.
“We’re seeing extremely good performance with those products,” Blow says. “It’s an extremely durable mix. In fact, it has applicability beyond fuel spills, with some airports using it on runways and taxiways to prevent ruts due to braking and turning movements of commercial jets.
The Asphalt Institute offers an airfield paving clinic. For more information, visit www.asphaltinstitute.org/training/seminars
Therese Dunphy is an award-winning journalist who has covered the construction materials industry for more than 30 years.
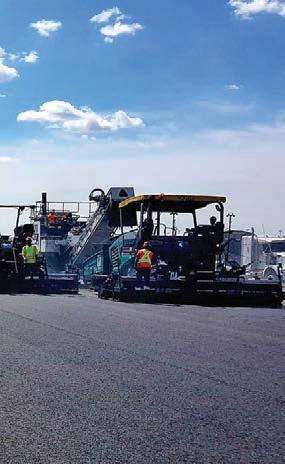
Therese Dunphy is an award-winning journalist who has covered the construction materials industry for more than 30 years.
For more information on airport paving, visit
ForConstructionPros.com/21067061
ASPHALT PLANTS AND COMPONENTS
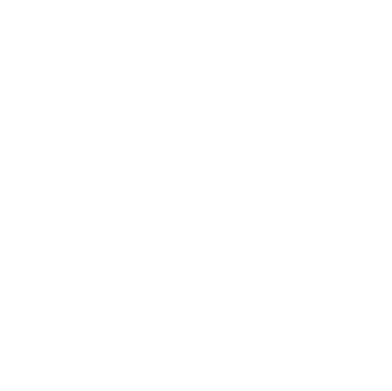
www.tarmacinc.com
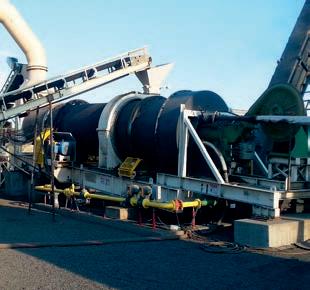