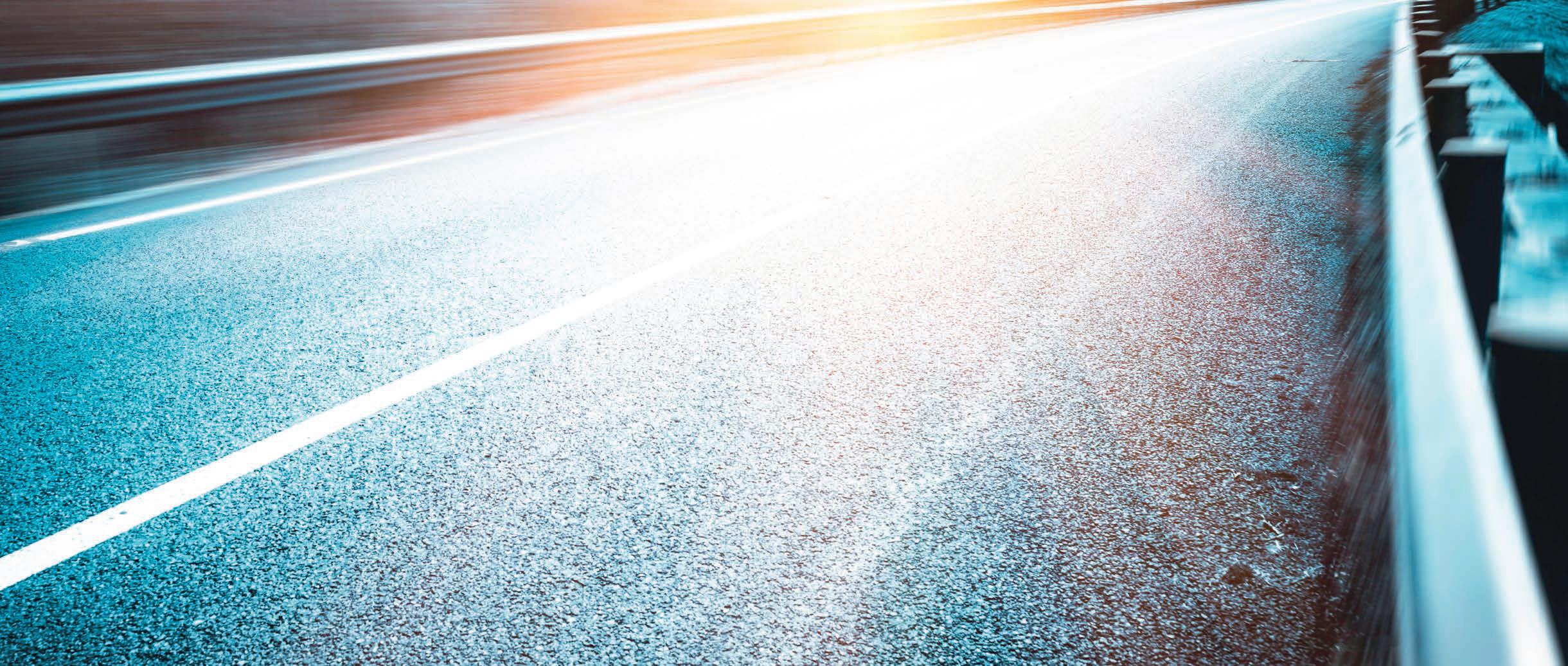
6 minute read
PRODUCTION PRODUCTS
CRUSHERS & SCREENERS
Rock Systems RIP-RAP Screening Plant
Rock Systems Semi-Portable Single Separation
Haver & Boecker Niagara N-Class Vibrating Screen
Haver & Boecker Niagara N-Class Vibrating Screen
The N-Class Vibrating Screen is capable of screening as much as 5,000 tons per hour.
• Ideal for tough jobs, such as scalping and classifying ores, minerals, stones, sand and gravel in aggregates and mining applications
• Dynamically balanced to minimize dynamic loads transferred into the structure and allows multiple screens to be placed side by side in the same building
• Heavy-duty body design handles loads in applications with extreme material sizes up to 2,032 x 1,016 x 1,016 mm
Eagle Crusher 1200-25 CC Crushing Plant
The Eagle Crusher 1200-CC with Pre-Feeder Screen is designed for larger-sized jobs with high volumes of material at- or near-spec.
• Two-deck screen-feed system greatly increases total production as the millings and fines go through the screen to stop wear and tear on the impactor and dramatically increase tonnage
• Available in tri- or quad-axle versions, the two-deck inclined screen produces two cubical spec products
• The plant is also available with a twin-shaft screen option with third reliever deck
Rip-Rap Plant consists of a heavy duty feed hopper constructed of 1-in. thick plate with stiffeners and a 46-in. wide x 20-ft. long vibrating grizzly feeder complete with 14-ft. solid pan impact section and 6-ft. long adjustable grizzly bar section.
• Collecting hopper under the grizzly section constructed of ½-in. thick plate with stiffeners to bypass the fines to an optional side discharge conveyor
• Semi-portable steel fabricated support structure with skid frame and plate steel bulkheads on all sides of structure
• One rust inhibitor prime coat and one finish coat gray paint for all equipment; one finish coat safety
Screen Machine SMI Compact Crushers and Screening Plants
The SMI compact crushers and screening plants are especially suited for use in tight jobsite environments, including urban areas. Models include three tracked jaw crushers from 7" x 16" (10TJ) to 16" x 28" (50TJ); a 3’ x 8’ double-deck tracked screening plant (90TS); and 7" x 16" (10SJ) and 10" x 20" (20SJ) stationary jaw crushers.The 50TJ is capable of processing up to 50 tph, while the 20 and 10 models generate up to 20 and 10 tph, respectively. The 90TS can process up to 90 tons of material per hour. The units can be fed by hand or by a mini-excavator or skid-steer loader. At 26,000 lbs., the 50TJ requires a semi-tractor trailer for transport; all other models can be moved with a heavy-duty pickup truck and transport trailer.
Keestrack R3 Screening and Crushing Plant
Keestrack's R3 plant is available as diesel-hydraulic or fully hybrid "e"-version.
• Production rates up to 250 tph
• Flexible processing of a large variety of raw and recycling materials
• Pre-screening
• High-performance impact crusher 48 ICR 100-00 with 770 x 960 mm inlet opening
• Heavy-duty 920 mm rotor (44-in. diameter)
• Optional 9-ft. x 4-ft. single-deck with reciruclation conveyor after screening unit
Kleemann MOBICAT MC 120 Zi PRO Jaw Crusher
With an output of up to 717 tons per hour, the MOBICAT MC 120 Zi PRO jaw crusher has a feed opening of 48-in. x 32-in. and is equipped with an extra long articulated crusher jaw.
• To ensure the best possible material flow, the continuous feed system (CFS) adapts the conveying speed to the fill level of the crusher
• Should material bridging occur in the jaw crusher, the crusher can be reversed with the aid of the electric crusher drive and in this way the blockage can be cleared in no time
• All components and functions can be controlled conveniently
Superior Industries Portable Sentry HSI Closed Circuit Plant
For material processing can process recycled concrete, reclaimed asphalt and pit run materials into valuable salable products. From a single feed, owners and operators will be able to produce up to four unique products. The closed circuit crushing and screening arrangement includes a 4250 Superior brand Sentry Horizontal Shaft Impactor (HSI). It is fed by a 48 x18 Intrepid Vibrating Grizzly Feeder, which is equipped with interchangeable grizzly cassettes (bars, fingers or punch plates) to accommodate multiple applications. Additionally, a two-deck Anthem Inclined Screen screens up to three material sizes. Returning material is fed back to the HSI via a patent pending recirculating conveyor, which centralizes the feed for full utilization and extended wear life of the crushers blow bars. Onboard, the cross conveyors are universally designed to be interchangeable, which means owners invest in fewer conveyors since they can be mixed and matched throughout the plant. The plant is equipped to accommodate line power but can also be outfitted with a diesel drive genset unit. Its transport weight, dimensions and axle configurations make it permissible for road travel throughout all of North America.
• Process recycled concrete, reclaimed asphalt, and pitrun into valuable products
• Produce up to four unique products from a single feed
• Recirculating conveyor centralizes feed, whichextends life of HSI blow bars
• Rotate universally designed, interchangeable crossconveyors throughout the plant
• Accommodates line power, but can be outfitted with adiesel drive genset unit
Astec PTSC2818VM Portable High Frequency Screen Plant
Equipped with an 8-ft. x 18-ft. top deck and an 8-ft. x 12-ft. bottom deck.
• Patent-pending screen design features externally-mounted vibrators at the ends of the tappets for a more aggressive screening action which creates a higher G-force and reduces heat load from material to motors as compared to single, center-mounted vibrators
• Screen also allows for easier maintenance and adjustments and is equipped with hydraulic operating angle adjustment, a fines collection hopper, top- and bottomdeck discharge chutes and an aggregate spreader
• Similar to other PTSC plants, the 2818VM features a nominal 54-in. x 38-ft. delivery conveyor with hydraulic drive and full-length skirtboards
• Chassis is fitted with manually-operating support legs
Honey Badger RAP Crusher for Recycled Asphalt
From replaceable abrasionresistant steel wear liners to a ½ -inch steel pulverizing hopper, this machine is ready for wear and tear. Included is a two-way valve hydraulic power pack that performs a controlled close of the pulverizing hopper top so that safety is never compromised. It also crushes costs, with an average return on investment reflecting 1/8 the cost of other crushing operations. Here are some of the ways the Honey Badger delivers on cost savings:
• Typical six-month ROI (for a 300,000 ton/season plant)
• Reduced or eliminated crushing costs
• Lower fuel consumption due to reduced RAP moisture
• Minimal material handling
McCloskey J4 Jaw Crusher
McCloskey International has unveiled the new J4 jaw crusher with new features for hard rock applications. Designed to withstand tough conditions, the J4 delivers high production due to its jaw chamber design and material flow. The large 1060mm x 700mm (42-in. x 28-in.) jaw opening accommodates large feed sizes, contributing to production in material processing. The material path is enhanced with the 1064mm x 4247mm (41.9-in. x 167.2-in.) grizzly pan feeder under the hopper that allows for sizing of material with a variety of mesh options. Options of either a short pan feeder to suit the pre-screen or a double deck grizzly pre-screen are available for sizing of material based on the required end product.
A choice of either a two deck or one and a half deck system. The two deck delivers an extra product spec over the mid-size product conveyor. Delivers stockpiling, with wide main and side conveyors for material flow. The angle adjustable 1200mm (48-in.) wide ToughFlex main conveyor has a 3.912m (12-ft. x 10-in.) high stockpile, and with quick release and ground level access, with the belt offering access for maintenance. It’s constructed with a special weave of two fabric plies and an additional binder warp (without the need for steel wire) resulting in reduced belt weight.
JANUARY 30 - FEBRUARY 1, 2024
Henry B. Gonzalez Convention Center - San Antonio, TX
You are invited to the inaugural immersive tradeshow, PAVE/X! And, we are excited to announce that OVER 45 industry-leading manufacturers and suppliers from across the paving and pavement maintenance industry will be in San Antonio for this NEW event.
The event will feature a robust educational program with FIVE TRACKS: a fast-paced demonstration showcase, and unlimited networking opportunities.
Paving, Striping, Sweeping, Sealcoating & Business Management,
We saw a distinct need in the market to evolve what an in-person event could mean to the industry. PAVE/X is already a reflection of that. As such, the experience significantly differs from other trade shows and conferences that serve paving and pavement maintenance contractors. Our goal with this event is to guide contractors towards deeper buyer insights as they make important purchasing decisions by utilizing high-quality curated education, live equipment demonstrations and networking opportunities that connect the right buyers and sellers, while maximizing the entire experience of both attendees and event supporters.
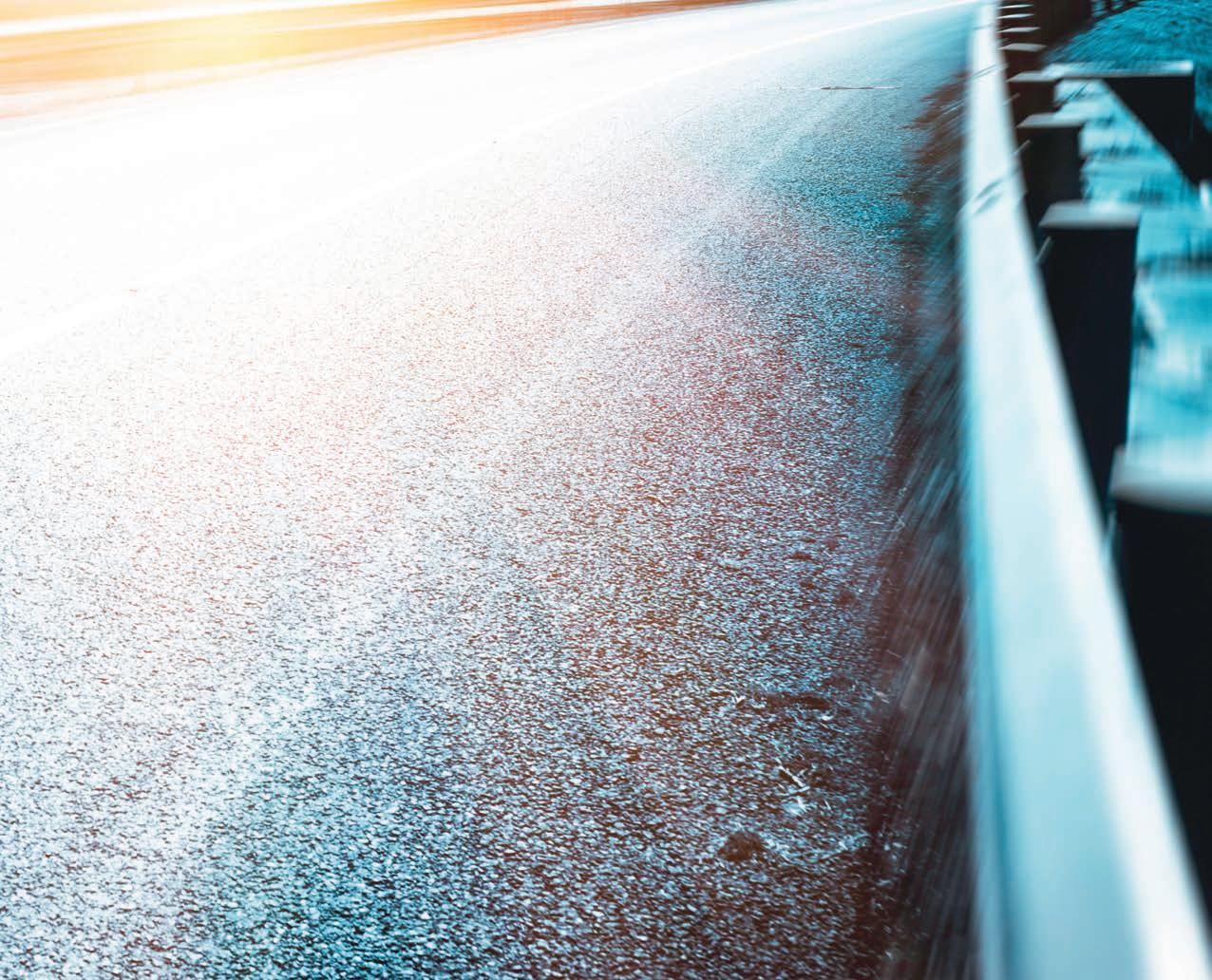
– Amy Schwandt, Chief Revenue Officer, ACBM
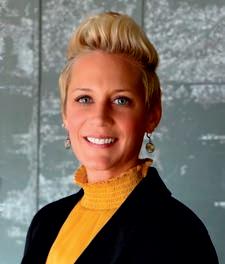
Sponsored by