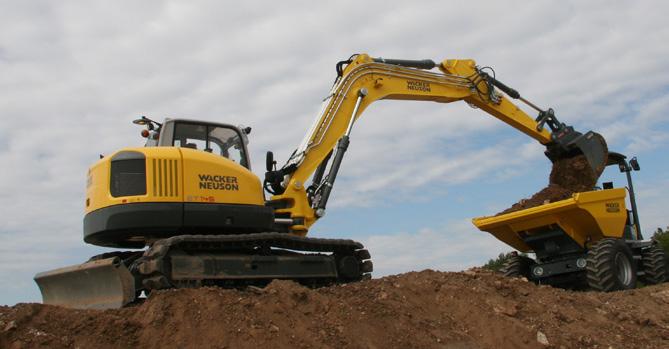
19 minute read
Earthmoving
Wacker Neuson ET145 Excavator
The 32,886-lb. ET145 features a 73.8hp, Tier 4 Final turbocharged engine and optimized powertrain that uses a constant power concept to deliver maximum horsepower and torque regardless of the load.
•127° boom swing •Provides a breakout force of nearly 20,500 lbs. and digging depth of 18 ft. •High-performance hydraulics enable spontaneous actuation of the hydraulic functions and maximum working speed •Spacious cab with intuitive, easy to reach controls, 7-in. high-resolution color display and backup camera •Comes with a solid cast dozer blade and steel, rubber or hybrid track options www.ForConstructionPros.com/12126979
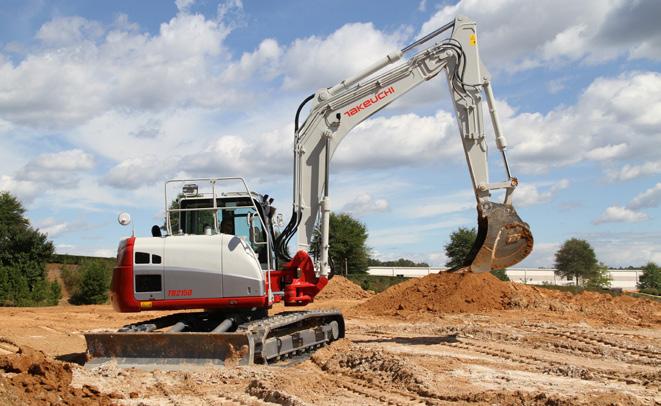
Takeuchi TB2150 Excavator
The 34,646-lb. TB2150 has a maximum digging depth of 18 ft. and maximum bucket breakout force of 22,190 lbs.
•Deutz TCD 3.6-liter, turbocharged, Tier 4 Final-compliant diesel engine offers 114 hp and 339.3 ft.-lbs. of torque •Engine utilizes a DOC+SCR aftertreatment system that requires the use of diesel exhaust fluid but does not need a DPF •Operator station includes an operatorfriendly, automotive-style interior, heated deluxe high-back air suspension seat and 7-in. color multi-information display •Standard Takeuchi Fleet Management telematics system www.ForConstructionPros.com/12273563
LBX Link-Belt 245 X4 Spin Ace
The 56,900-lb. Link-Belt 245 X4 Spin Ace has a dig depth of 21 ft. 10 in. and bucket digging force of 34,600 lbf.
•160-net-hp Isuzu Tier 4 Final diesel engine doesn’t require a DPF •Redesigned hydraulic system reduces cycle times by up to 10% •Speed Priority, Heavy and Applied Power modes •Includes structural improvements to the boom and arm and a robust undercarriage with larger track rollers and thicker plating •Quiet, pressurized, ergonomic cab with 7-in. high-definition LC monitor, RemoteCARE telematics and full-time rear view camera www.ForConstructionPros.com/21013531
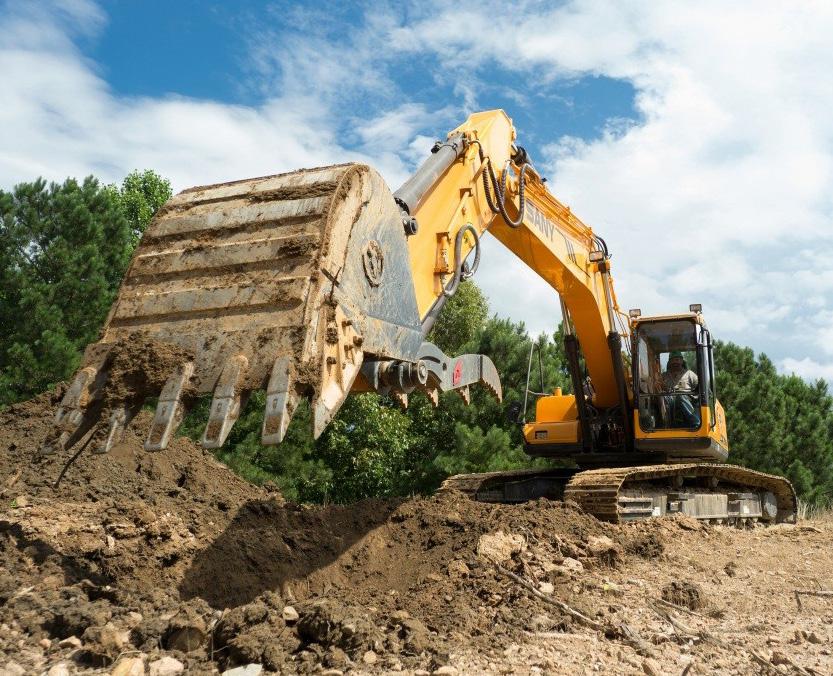
SANY SY215C Excavator
The SY215C excavator is powered by a Cummins Tier 4 Final engine and features two circuits of auxiliary lines down the arm for ready to use hydraulic power.
•Side frame rails standard •Optimized cabin for visibility and operator comfort •SANYLive telematics GPS system keeps track of engine hours, fuel usage, location history, alerts and events www.ForConstructionPros.com/12293819
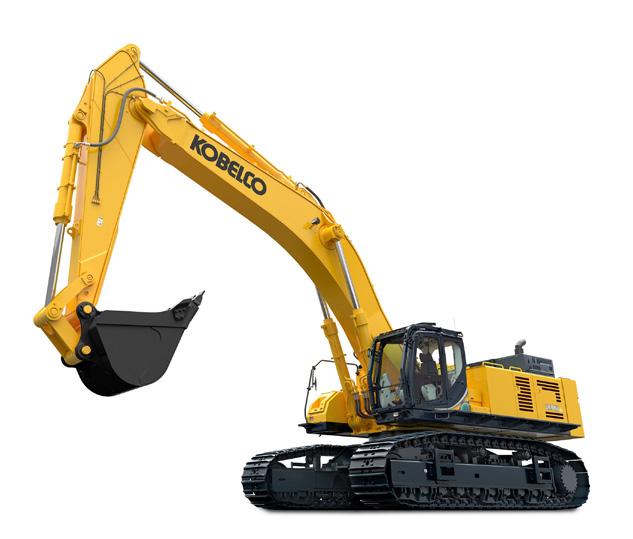
Kobelco SK850LC-10 Excavator
The 185,700-lb. SK850LC-10 excavator delivers a 31-ft. 10-in. maximum digging depth and a bucket digging force of 90,598 lbf. to achieve high work volume.
•Drawbar pull of 146,800 lbf. •510-hp Hino E13C YM-KSDB engine •Boasts a roughly 17% improvement in fuel economy while in ECO-mode •Hydraulic system includes two variable axial piston pumps •Enhanced hydraulic line layout further reduces energy loss for optimal performance www.ForConstructionPros.com/21205488
Hyundai A Series Excavators
The A Series excavator models are powered by Cummins Performance Series Stage V engines offering more than a 10% increase in power and nearly 20% increase in torque while using less fuel.
•HX210A features a 170-hp Cummins B4.5 diesel engine, a standard operating weight of 48,720 lbs. and is equipped with a standard .80-cu.-yd.-capacity bucket •HX85A compact model has a 65-net-hp Yanmar 4TNV98C engine, a 20,390-lb. operating weight with 12-ft. 10-in. two-piece boom, .33-cu.-yd. standard bucket capacity and optional four-way dozer blade •174-net-hp, 54,540-lb. HW250MH wheeled material handler also available www.ForConstructionPros.com/21124109
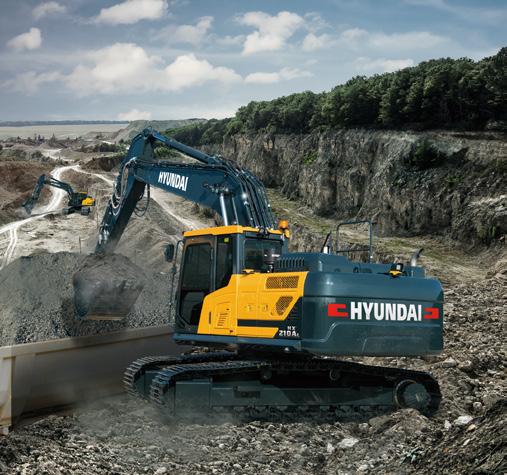
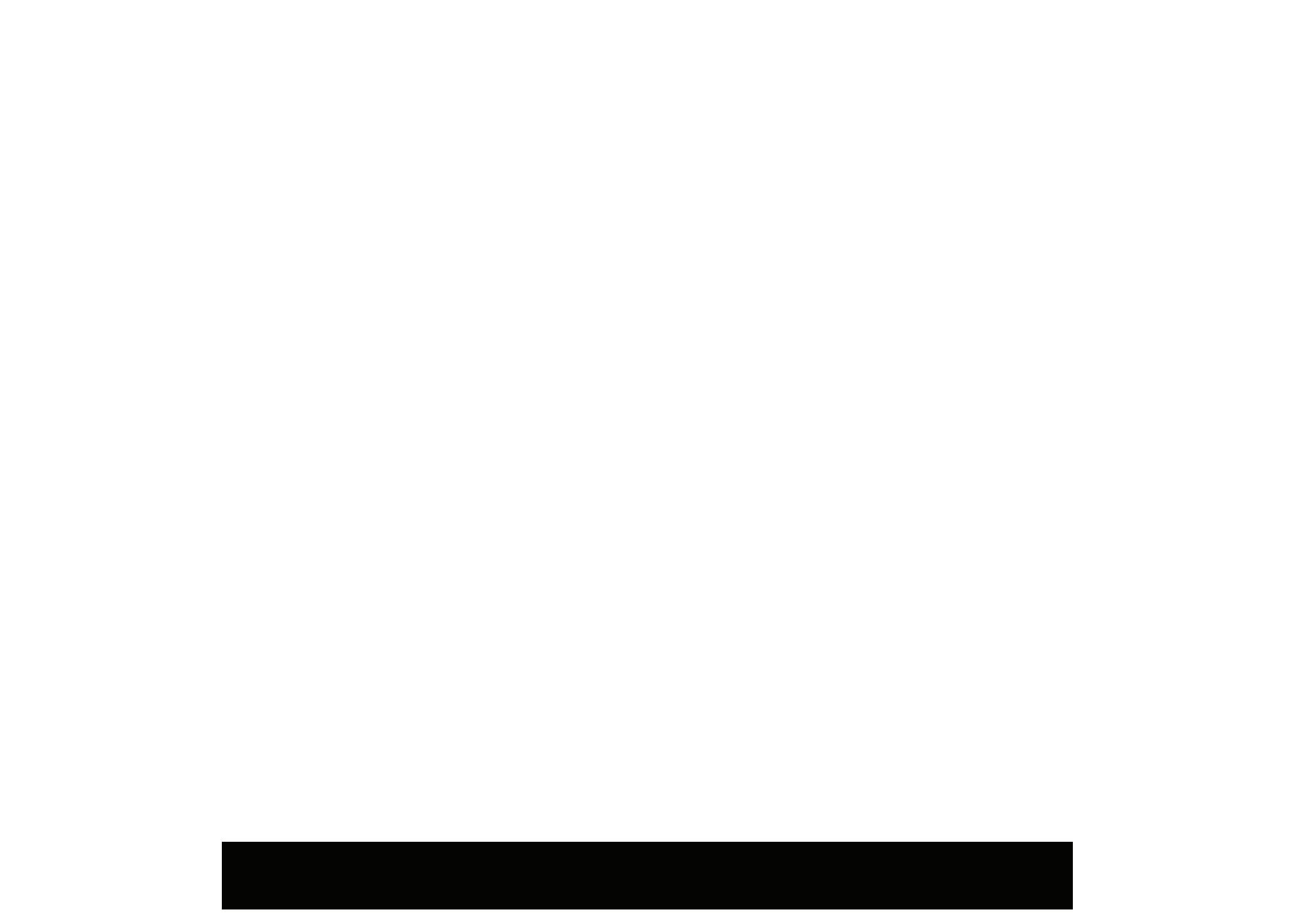
www.venturo.com | 800-226-2238
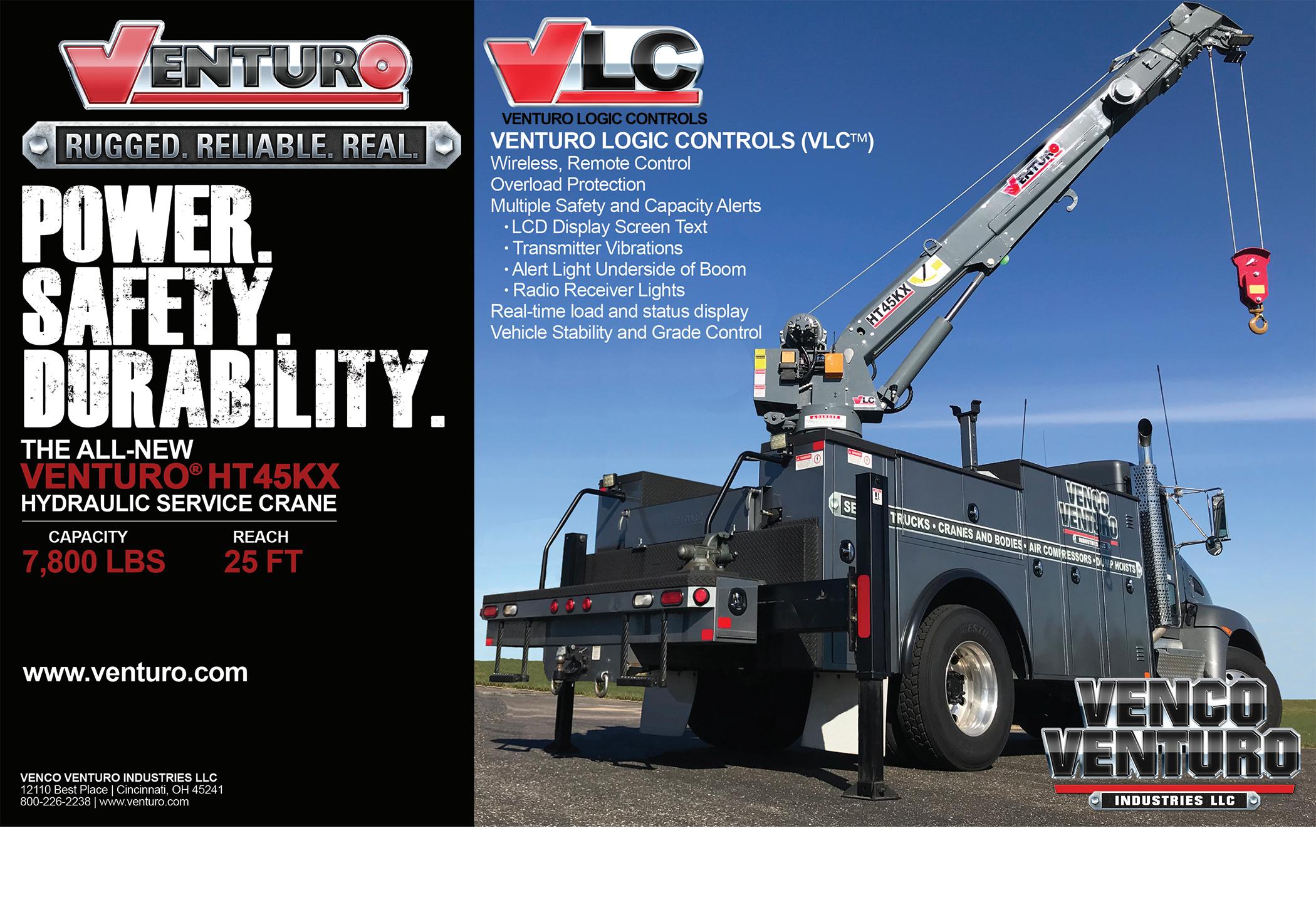
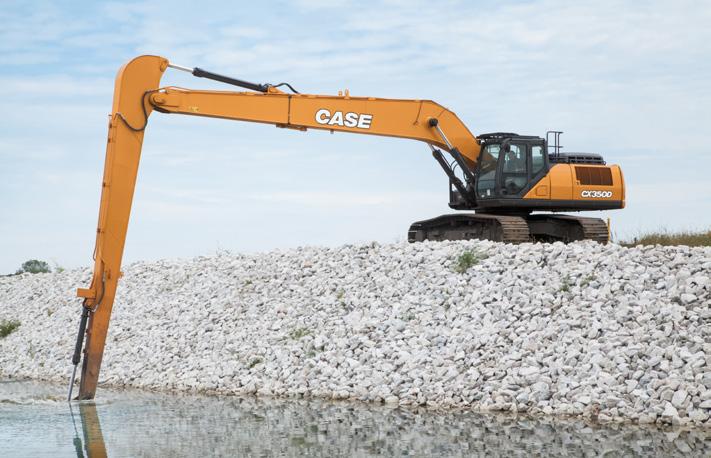
Case CX350D LR Long Reach Excavator
The 88,200-lb. CX350D LR has an elongated boom and arm and additional counterweight for increased digging capabilities in deep or long-distance digging applications.
•268-hp Tier 4 Final diesel engine with lowmaintenance selective catalytic reduction •Maximum dig depth of 46 ft. 3 in. and bucket digging force of 24,500 ft.-lbs. •Includes an electronically controlled pump, larger control valve and multiple advanced sensors •CASE Intelligent Hydraulic System with four integrated control systems •Speed Priority, Heavy and Automatic working modes www.ForConstructionPros.com/21105160
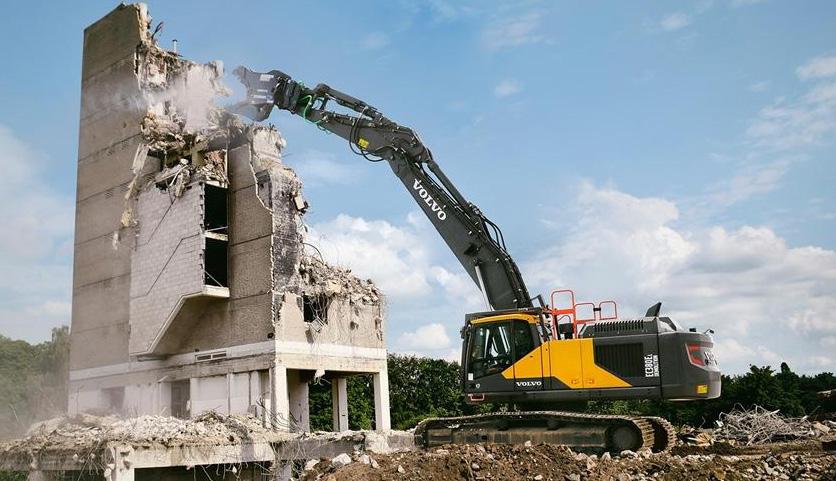
Volvo EC380E Straight Boom Excavator
The 38-ton, 308-gross-hp EC380E Straight Boom excavator features a 23-ft. straight boom and purpose-built arm suited for tough demolition applications.
•Max pin height of 39 ft. 10 in. •44,512-lb. standard breakout force •Includes a heavily reinforced, heavy-duty plate steel main frame with bolt-head protection, heavy-duty (or eXtreme Duty) undercover protection, durable belly guard, full track guard and more •Roof window and front one-piece glass made from high-impact resistant P5A •Dust suppression system with 7.9-gpm lifting pump and four arm-based nozzles www.ForConstructionPros.com/21603154
Bobcat E165 Excavator
The 38,376-lb. E165 has a 131-hp (gross) engine and four selectable power modes to adapt performance to the task.
•20-ft. dig depth and 25,794-lbf. bucket digging force •Smart Power Control matches load to engine rpm, hydraulic pump torque and engine response •Variable Speed Control automatically reduces engine rpm during low workload requirements •Quiet, pressurized cab with seated air suspension seat, premium heat and air conditioning system, 7-in. LCD display panel and standard rear view and side view cameras www.ForConstructionPros.com/21138267
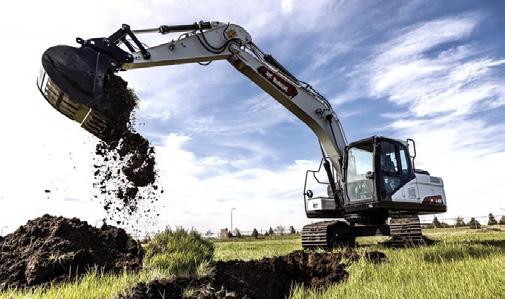
Caterpillar 335 Excavator
Weighing less than 80,000 lbs., the 335 Next Gen excavator with compact tailswing radius provides a 22-ft. 11-in. maximum digging depth.
•Hydraulic power increased by 20% •Includes Cat Payload technology, Lift Assist, Cat Grade with 2D, Cat Grade with Assist and Cat Link telematics •273-hp C7.1 engine •Power, Smart and Eco selectable operating modes with one-touch low idle •Reengineered Deluxe or Premium cab designs www.forconstructionpros.com/21271277
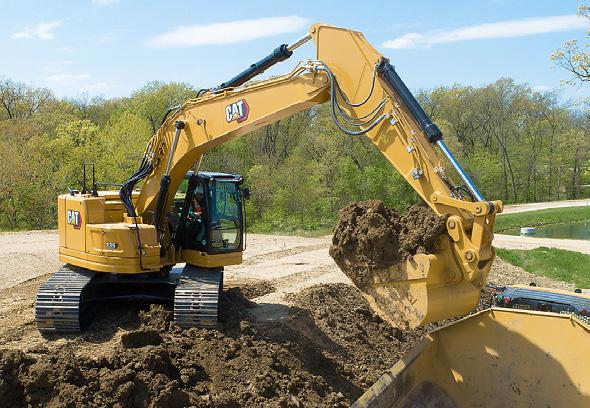
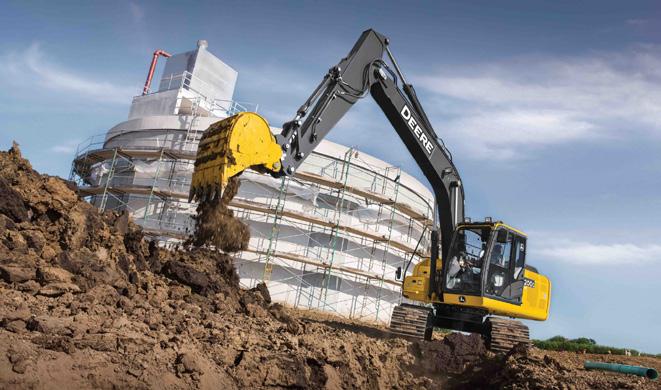
John Deere 200G Excavator
The 200G excavator is powered by a 145hp John Deere PowerTech PSS 4.5-liter, Tier 4 Final engine.
•Adjustable power modes, including ECO and POWER settings, automatically change engine rpm and hydraulic pump calibration based on the job •Hydraulic system efficiencies enable faster swing speed •Double-sealed swing bearing system with enhanced internal grease retention helps to reduce the risk of contamination •Reinforced arm-to-bucket joints maximize front joint durability and reduce maintenance intervals for axial clearance adjustment www.ForConstructionPros.com/21160460
Doosan DX170LC-5 Excavator
The 17-metric-ton DX170LC-5 measures 8 ft. 5 in. wide and falls below the 80,000-lb. GVWR limit for simplified and less expensive transport.
•127-hp Tier 4 diesel engine •Provides a 19-ft. 11-in. maximum digging depth, 28-ft. 10-in. maximum digging reach and 25,794-lbf. bucket breakout force •Four power modes better balance fuel consumption and machine power to working conditions •Digging, breaker, shear and lifting work modes •Standard rear view camera with side view camera available www.forconstructionpros.com/21081845
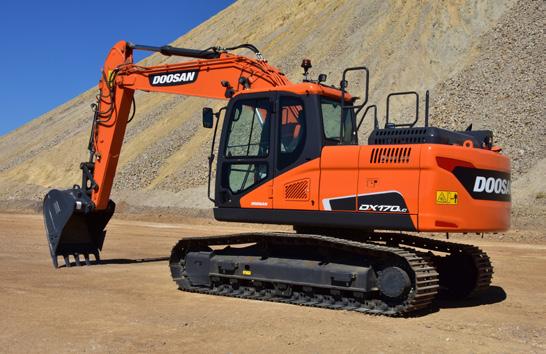
Liebherr R 928 G8 Excavator
The R 928 G8 has a total weight of less than 30 tonnes in various configurations and is characterized by high drawbar pull, enhanced load-bearing capacity and a large bucket.
•Develops higher tear and breakout forces, plus the torque of the superstructure has been increased •Features include an optimized load curve and improved inertia in the rotary drive •Robust X-form undercarriage •Includes a spacious, air conditioned cab with fully retractable front window, pneumatic seat and high-resolution touchscreen www.forconstructionpros.com/21391973
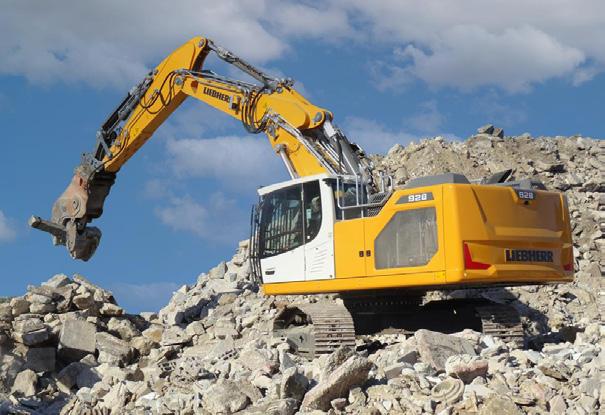
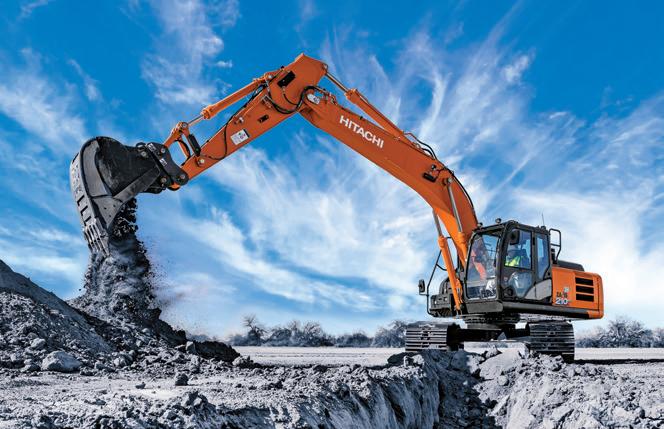
Hitachi ZX210-6 and ZX210LC-6 Utility Class Excavators
The ZX210-6 and ZX210LC-6 feature a 160-net-hp Isuzu 4HKI Tier 4 Final engine that doesn’t require a DPF.
•Offer 45,836- to 48,238-lb. operating weights and maximum digging depths of 20 ft. 3 in. and 21 ft. 11 in. •31,698-lb. bucket digging force (SAE) •HIOS III hydraulic system •Includes High Productivity (HP), Power (P) and Economy (E) work modes, plus programmable attachment modes •Cab includes a multifunction LCD monitor with rotary control, ergonomically placed, low-effort joysticks, fully adjustable high-back sculpted seat, high-efficiency HVAC system and more www.ForConstructionPros.com/21603149
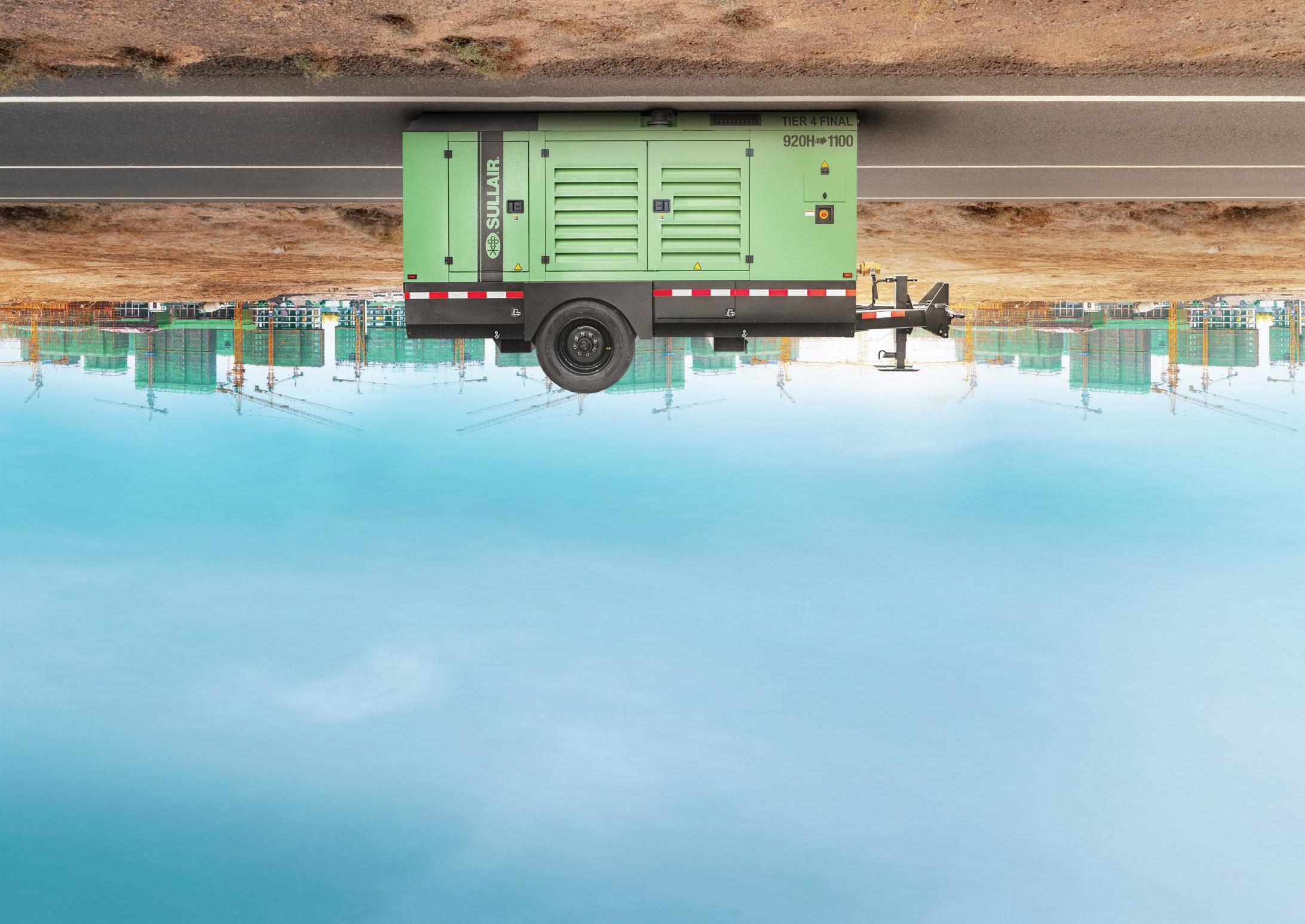
WE’VE TURNED THE WORLD OF PoRTABLE COMPRESSORS UPSIDE DOWN
MANAGING YOUR FLEET JUST GOT A WHOLE LOT SIMPLER.
LEARN MORE AT UpsidedownCompressors.com The Sullair Mid-Range Series features two units that can cover the jobs of up to 9 different compressors. These master-of-all-trades machines bring unmatched versatility to the jobsite to save you time, energy and money.
3 COUNTLESS PRESSURE & FLOW COMBINATIONS 3 TIER 4 FINAL CAT AND PERKINS ENGINE OPTIONS 3 ELECTRONIC SPIRAL VALVE TECHNOLOGY —
A SULLAIR EXCLUSIVE
© 2021 Sullair, LLC. All rights reserved.
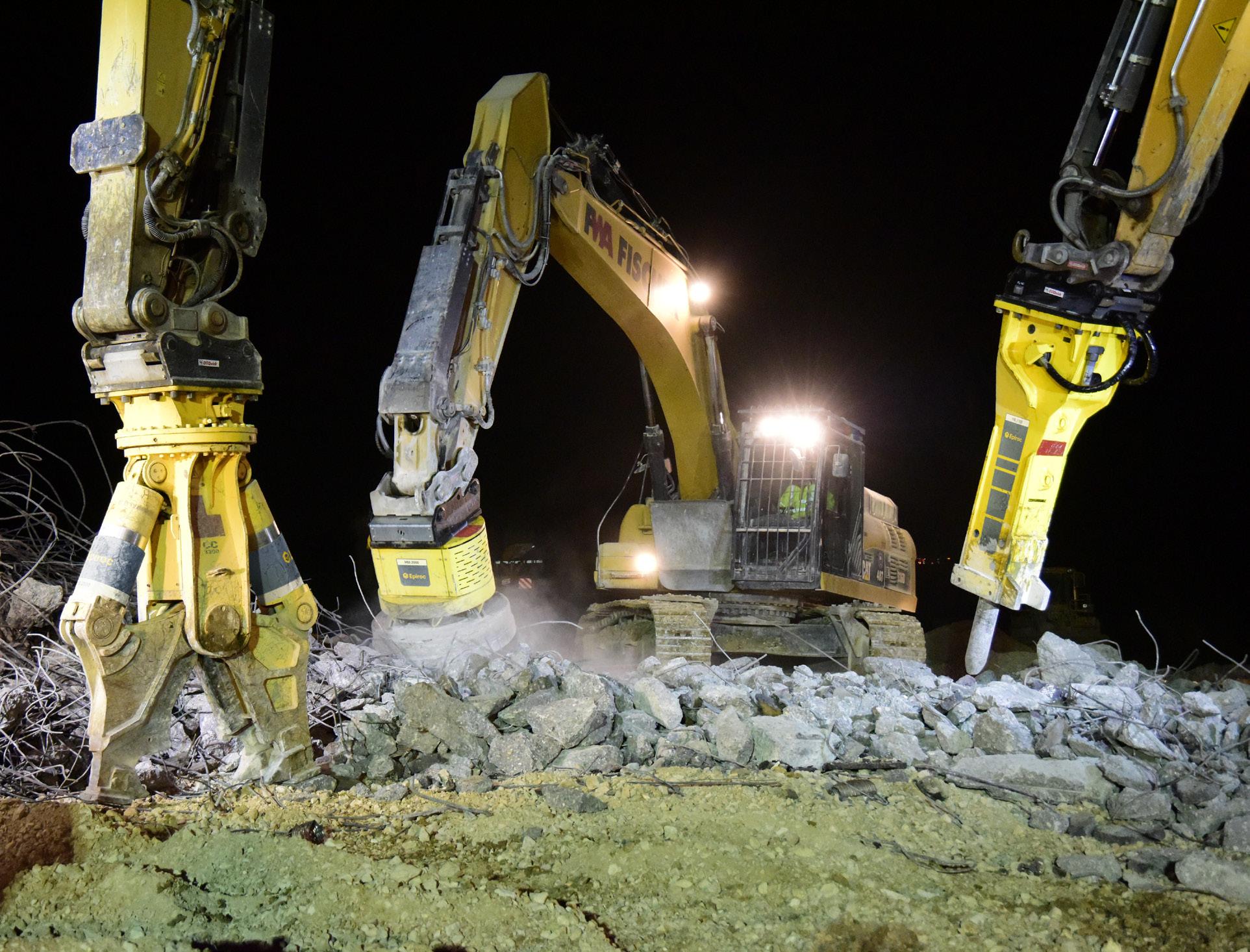
PREVENT Demolition Attachment Breakdown
Delayed maintenance greatly increases the likelihood of catastrophic demolition attachment failure.
Demolition can be a brutal environment, yet attachments that are properly maintained can have a service life measured in decades.
“If you want anything to run at peak performance, you need to constantly maintain and stay on top of it,” says Tom Schwind, business line manager, Epiroc. “Everybody wants to treat their attachment like a bucket. They don’t want to do any maintenance to it.
“The most important thing is to keep up with your preventive maintenance,” he continues. “Be aware of your environment and treat the attachment like it’s a piece of equipment, not just an ancillary bucket or something that you’re going to destroy. The environment for demolition tools and hydraulic breakers is a very tough environment. We don’t need to make it harder.”
Preventive maintenance programs have a proven track record. “I have a customer in Philadelphia that has hammers that go back to the Krupp name in the ’90s,” Schwind notes. “They’re still running every single day. They have an excellent maintenance program.” UNDERSTAND MAINTENANCE DEMANDS OF SPECIFIC TOOLS
It all starts with following the manufacturer’s recommended service intervals. The type of service required depends on the specific attachment. For instance, crushing and concrete pulverizing attachments need periodic inspections for cracks.
“When you’re using any kind of muncher, cracker or shear, a crack presents a real problem. There’s a lot of tertiary forces. You can find a crack, detect it, air arc it out, re-weld it and you’ll be fine,” says Schwind. “You let that go and that little crack becomes the proverbial huge crack. I’ve seen lots of demolition tools literally split in half.” Steel can be worn away quickly in crushing applications.
Some attachments require more attention. “Shears and processors are high-maintenance attachments,” says Greg Smith, marketing communications manager, Okada America. “Hourly, daily, monthly and yearly maintenance intervals are available from the manufacturer and can be found in the operator’s manual and maintenance manuals. It is important that the distributor representative provides this information and discusses the maintenance procedures with the end user and maintenance personnel when delivering the attachment.
“Maintenance intervals are a guideline because the severity of the application and operation may require additional and increased scheduled maintenance,” he adds.
Hydraulic breakers have unique set of maintenance requirements. “Grease and lubrication is the key to hydraulic breaking,” says Schwind. Friction due to lack of lubrication creates heat and will quickly wear out the lower and upper bushings and thrust ring. If the bushings wear out, they will eventually take the seals out. “Now you have an extremely costly repair. If your lower bushing is wearing quickly, my suggestion is to replace that bushing before it gets to 100% wear. You may want to replace it at 85%.”
Bushing wear needs to be constantly monitored. “A lack of grease and neglect — not checking the bushings on the breaker and allowing those to get worn past serviceable limits — will inevitably induce a catastrophic failure,” says Greg Clinton, product service manager, Montabert. Montabert recommends every 40 to 50 hours of breaker operation to remove the tool and inspect. Reseal the breaker anywhere from 350 to 500 hours if the hammer is not leaking.
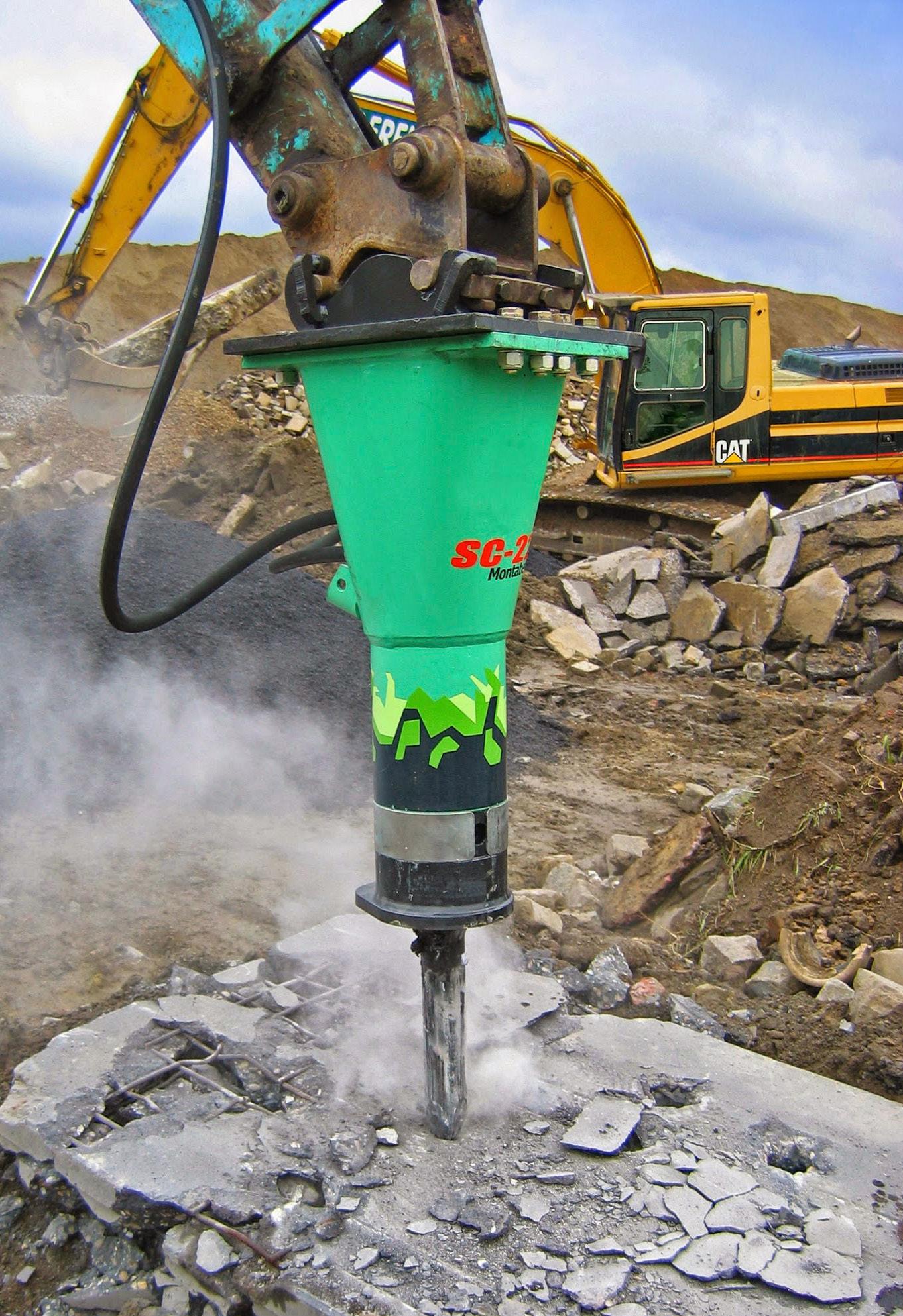
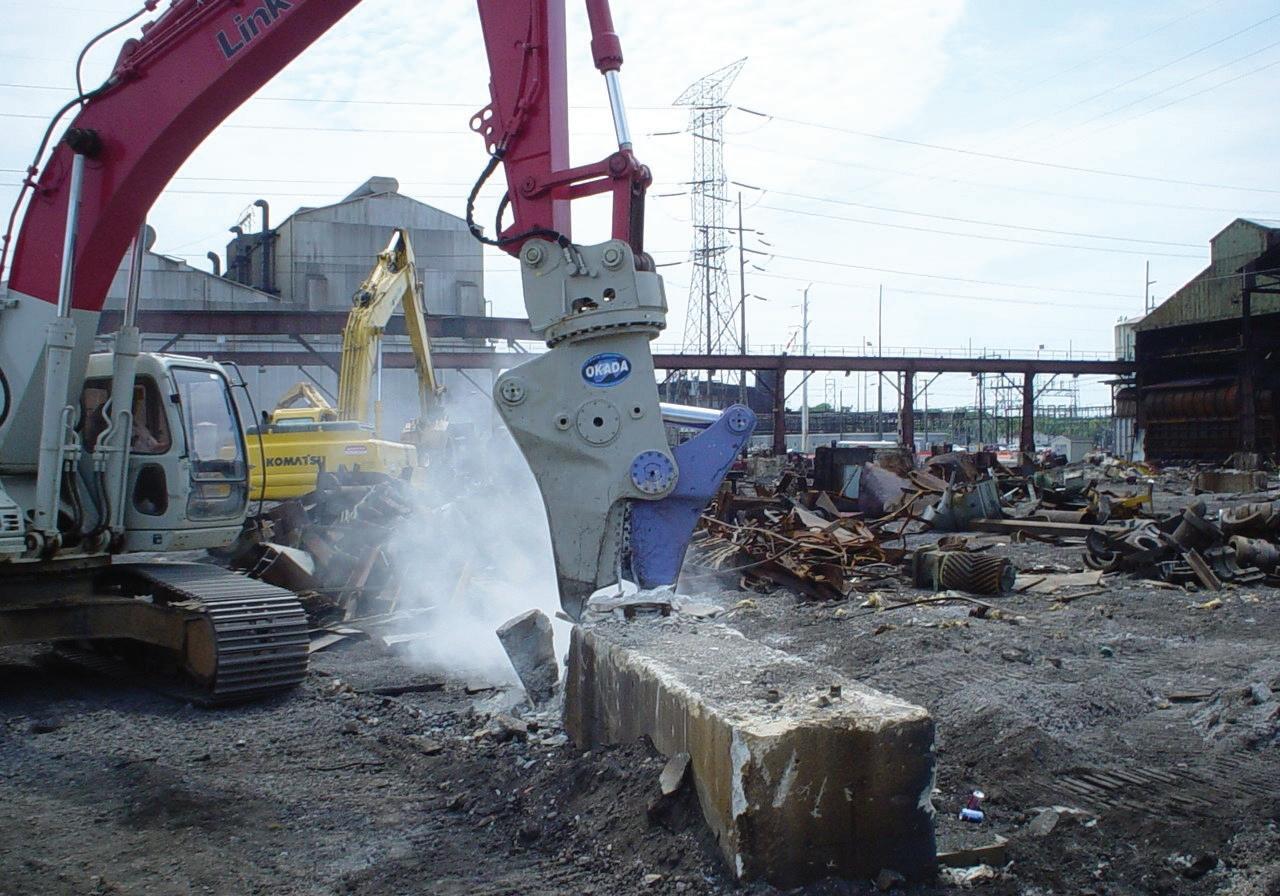
Shears and processors are high-maintenance attachments. Maintenance intervals are a guideline because the severity of the application and operation may require additional and increased scheduled maintenance.
Don’t ignore leaks in the interest of finishing a project. “You can also have a very sudden catastrophic failure with a breaker because the seal goes out and it starts leaking oil,” says Schwind. There is a temptation to keep going to finish a job when a leak first appears. “If a hammer is leaking oil, you need to shut it down immediately because that oil becomes like a lapping compound which results in much more damage. Pushing it may cost you a lot more money in repair or replacement.”
Regular inspections ensure proper hammer operation. “We recommend every 40 to 50 hours of breaker operation to remove the tool and inspect,” says Clinton. Reseal the breaker anywhere from 350 to 500 hours if the hammer is not leaking. “If the hammer is not leaking and your bushings are within spec, run it until your bushings are close to wearing out. Once you get to the 95% wear mark on your bushings, you need to start looking at scheduling it to get resealed.” Take it down, replace the bushings, reseal and inspect. “It pretty much goes on
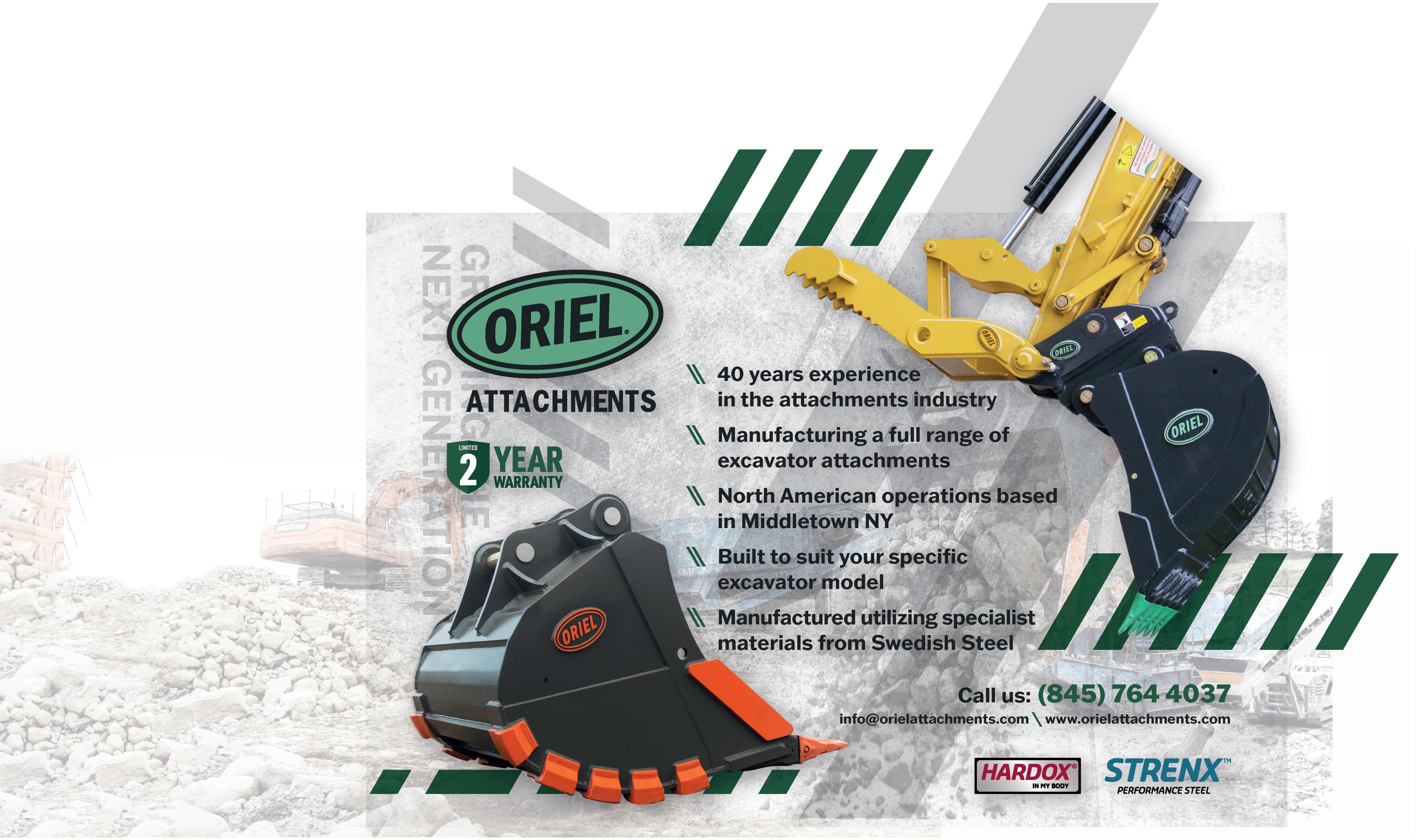
Epiroc
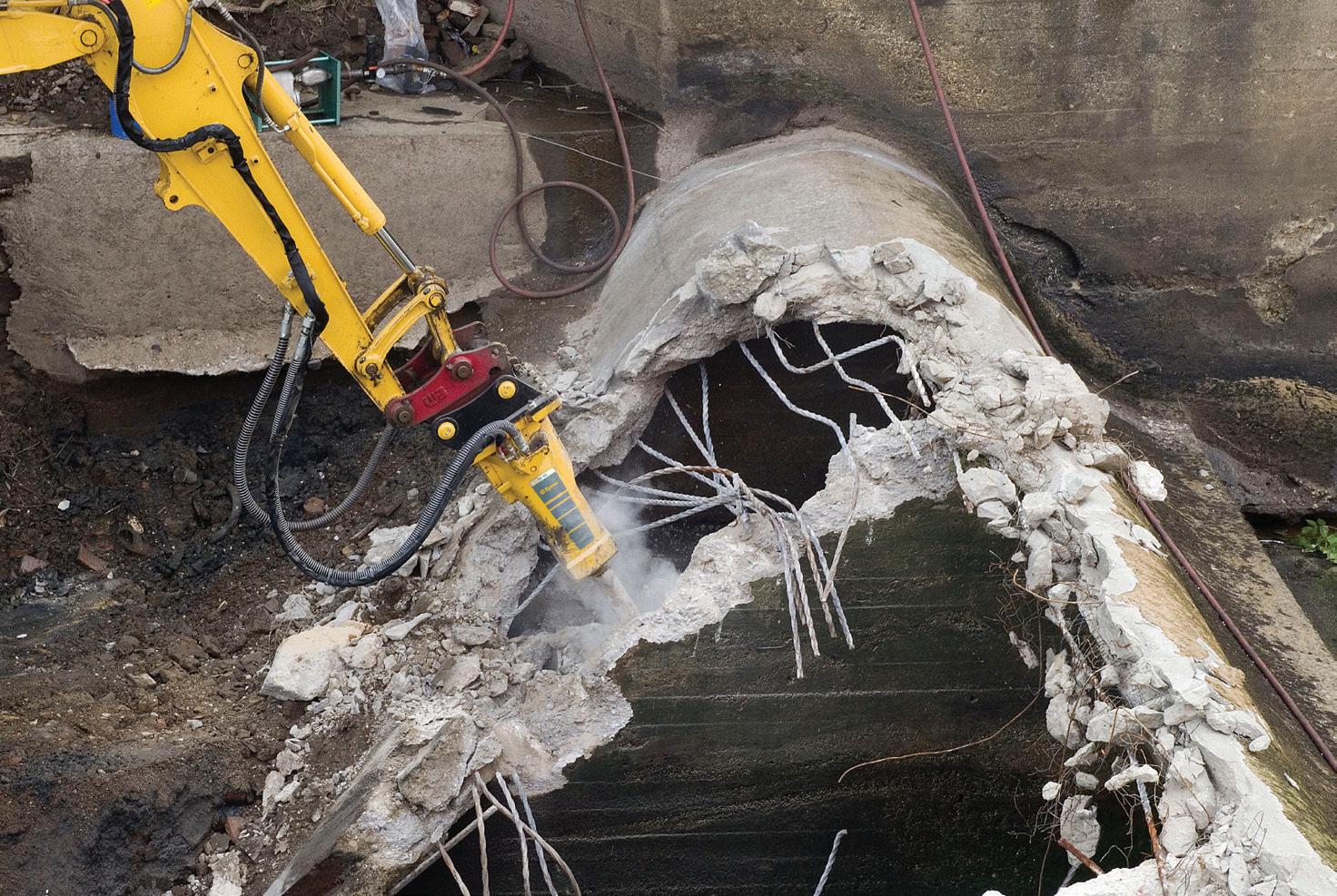
Grease and lubrication are the key to hydraulic breaking. Friction due to lack of lubrication creates heat and will quickly wear out the lower and upper bushings. If the bushings wear out, they will eventually take the seals out.
bushing wear unless you have a catastrophic failure.”
An exception would be a breaker that sits idle for long periods of time. “Even if the bushings are not worn out, if you are not using the hammer every day and it is sitting a lot, I would recommend that you reseal it yearly,” says Clinton.
Autolube systems are recommended for mid-size and larger breakers. “All of [Epiroc’s] medium and heavy breakers come with autolube included in the price. We have what we call the ContiLube system,” says Schwind. “An autolube system will probably get you 10 to 12 hours on our largest hammers, depending upon how you have the setting.”
Montabert recommends autolube systems on all breakers 3,000-ft.-lb. impact class or greater. “Typically, once you get to 3,000 ft.lbs., you cannot put enough grease by hand to the bushings to keep it washed and keep it lubricated,” says Clinton. “Heat will take up a good share of that lubrication. The heat is so great that you just cannot keep up.”
TELEMATICS CHANGES GAME
Tracking hours on most attachments has been a guessing game, but that is changing with telematics.
For example, Epiroc has released HATCON, a telematics system that tracks how long an attachment (not just hammers) operates. Because it works off the vibration of the machine, it allows you to differentiate between when the attachment is operating and when the machine is operating, providing actual service hours for the attachment.
Telematics systems can also be used as training tools. “Hydraulic breakers should not be run for more than 30 seconds,” says Schwind. “If it’s not penetrating, you risk hurting the piston, mushrooming the point, it will not be getting grease. There’s a lot of bad things that can happen in that scenario.” HATCON will let you know if the operator is exceeding that limit. “It’s not a big brother thing; it’s an opportunity for you to help train and work with end users to make them better at what they are doing.”
ENSURE A PROPER MATCH
“Improper sizing of the carrier and attachment is the first mistake companies and end users make,” says Smith. “If the attachment is too small, you may not be able to process the material based on size and type. In these cases, you can experience longer cycle times, premature failure and increased cost of wear items (i.e., blades, knives and teeth). You may
PROPER STORAGE PREVENTS CORROSION
Keep hoses capped if not using an attachment. “When you go to put it back on, clean off the fittings. Take some degreaser and get the dirt and debris away from it,” says Greg Clinton, Montabert.
“In all the manuals, there is proper long-term and proper short-term storage,” says Tom Schwind, Epiroc. Keeping moisture out of the tool is the key focus. Do not have the breaker laying on its back with the point up in the air so water gets invited into it.
“If it is not in use, make sure the mounting cap end is elevated above the front guide bushing so any moisture that does come down and settle on your tool does not migrate up into the bushing area,” says Clinton. “For long-term storage, remove the tool and pack that front guide area and bushings real well with grease. Re-insert the tool. Try to put a bead of grease around the entrance area of the front guide and tool so moisture cannot migrate in, and then cover. You don’t necessarily have to move it indoors, but put a cover over it for long-term storage.
“Moisture is a killer,” he continues. “If your strike piston migrates down out of the cylinder and is exposed, bare metal, moisture and oxygen equates to rust. That will quickly destroy a hammer.”
experience a need for more frequent maintenance intervals and increased repairs to reduce premature failure of structural and major components that may not be covered by the manufacturer’s warranty. Increased downtime can occur, which affects profit and the bottom line.”
The opposite also creates problems. “Using too large an attachment for the carrier can damage carrier brackets, boom and hydraulic components,” says Smith. “In addition, the hydraulic system may not be adequate to achieve the required flow and pressures of the shear or processor, which results in poor performance and increased cycle times.” Stability also becomes an issue.
HOSES ARE THE LIFELINES
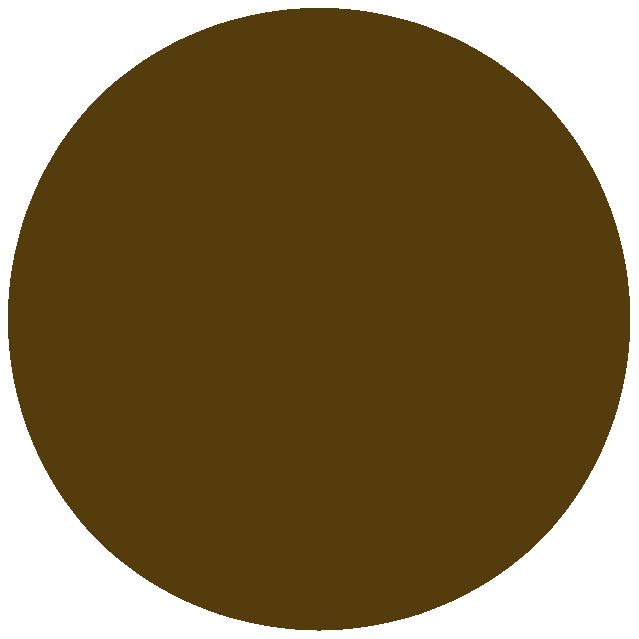
Keep an eye on the condition of hydraulic hoses. “Demolition environments are incredibly demanding. Hose life can be significantly shortened under such applications,” says Keith Zulauf, senior fluid power application engineer, Gates.
“Consider the enemies of the hose to include heat, abrasion and ozone — and each of these is present in demolition environments,” he points out. “Demolition equipment also sees very high duty cycles, quickly oscillating between unloaded and maximum load conditions, which puts additional demand on hydraulic components. Temperature can also be an issue — both the system temperature and the ambient temperature. Gates offers hightemperature hose product solutions for these types of applications.”
As with any hydraulic attachment, the condition of the hoses is critical to reliable performance. “Always be on the lookout for exposed wires, as any damage to the reinforcement can cause instantaneous failure,” says Cindy Cookson, vice president, hydraulics global product line, Gates. “Even if no wire damage is visible, exposed wires can rapidly corrode, and if moisture creeps along the wire path, there could be unseen damage under the cover or in lower wire layers. Also look for any weeping at the hose-coupling interface. If enough oil is present to create a drip, it is time to replace the complete assembly. Finally, look for signs of ozone cracking or weathering. The best place to look for this type of damage is at the exterior parts of the hose bend, which is where that cover is under the most stress, and consequently where this ozone cracking will first appear.”
Hose couplings can become a source of failure. “Proper installation of the hose coupling is critical to assembly performance,” says Zulauf. “Over- or under-torqued thread-end terminations can lead to system fluid losses and contamination, creating fire and safety hazards and necessitating environmental cleanups. Maintenance personnel should receive training in thread-end torque requirements. Torque wrenches should be used for thread-end termination installation. Over-torqued hose assembly thread-end terminations are one of the leading causes of short assembly life, as a result of cracked coupling mechanical seats leading to leaks at the coupling.”
Also ensure that you do not create restrictions when installing quick couplers on the hoses. “If you are going to use a quick coupler, we recommend one that is the same diameter as your hose because you don’t want it to be a neckdown point,” says Schwind. “It can create heat, which is bad for all hydraulic attachments. It can also change the pressure because you are necking it down.”
When utilizing hydraulic quick couplings, Epiroc prefers the screw-on fittings for larger demolition tools. “You can get a positive pipe fit,” says Schwind. “It doesn’t allow any contaminants. When you take it off, you can reverse the male and the female on each line.” When the attachment is removed, the two hose ends can be connected to create a totally closed system. Nothing goes in the dirt, so you don’t let contaminants in.
Schwind adds, “If you are using any quick coupler, make sure you definitely have either an inline filter or your filter is working in your tank to pick up if anything does let go.”
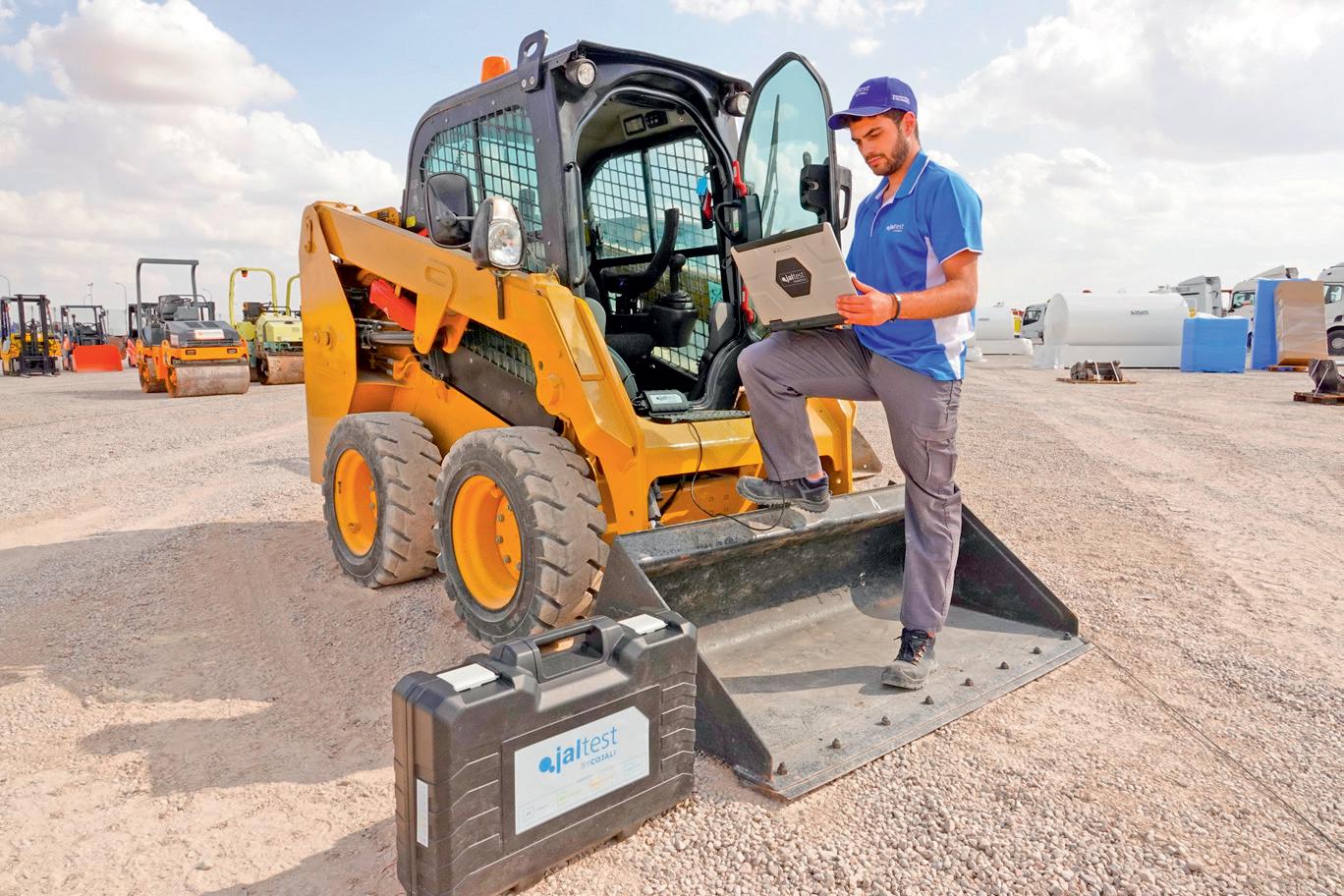
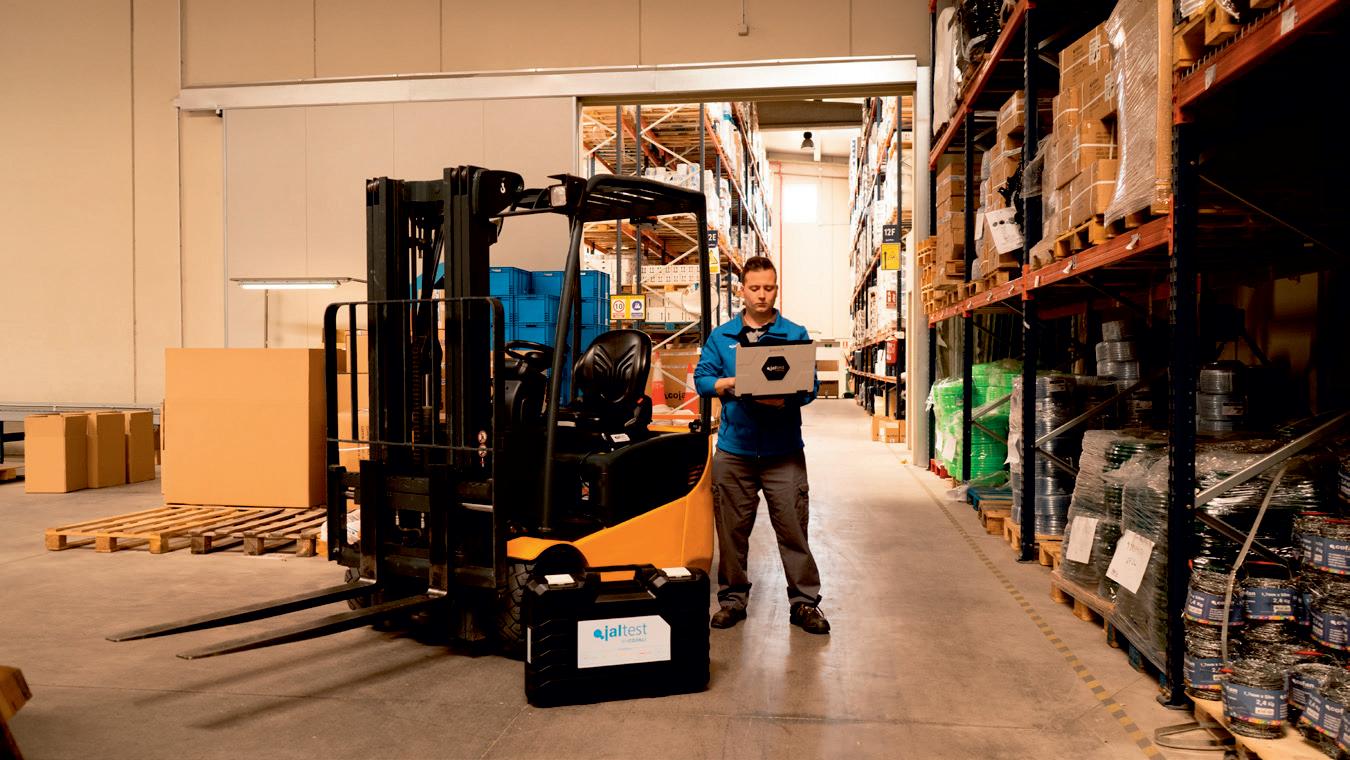
ENSURE CLEANLINESS OF REPLACEMENT HOSES
Take special precautions when fabricating replacement hoses.
“The hose assembly process introduces contamination in a variety of ways: lubricants from the hose manufacturing process; contaminants from the coupling fabrication and plating processes; and debris generated when the hose is cut,” says Zulauf. “Hose cleaning systems like Gates MegaClean and UltraClean can remove assembly contamination before the hose assembly is placed in service. Both systems use pneumatic projectiles to remove contaminants. Cleaning a hose assembly in this manner is quick, easy and effective.”
To minimize the risk of contaminants, always cap a hose immediately after assembly and cleaning. “If you’re wondering why it is so important to minimize contamination, consider the system on which this hose is being installed,” says Zulauf. “Hydraulic pumps are extremely expensive, and their operation is tuned for tight tolerances at the valves and pistons. These are small orifices, and any contamination in the hydraulic fluid can affect their operation, so cleaning the hose assemblies after crimping is essential to minimize downtime and maintenance costs.
“Proper hose routing is the best way to protect a hose assembly from environmental damage,” he continues. “Hoses that are too long can unexpectedly rub against machine elements. Hoses that are too short may require excessive bending at the coupling, which can minimize hose life. Proper routing can also include clamping and/or yoking the hose to the machine to keep the hose in place, although care should be taken to account for hose flexing and hose elongation when pressurized to avoid creating other problems.”
Selecting abrasion-resistant covers and using hose accessories for risky areas can help extend hose life. “Manufacturers such as Gates offer high-abrasion hoses that provide significantly longer life in those applications,” says Zulauf. ET
EQUIPMENT ALWAYS READY TO WORK
SEE YOU AT UTILITY EXPO COME BY OUR BOOTH For a chance to
BOOTH B1545 SEP 28-30
One Platform, One solution:
Diagnostics Technical Info Live Data Calibrations Parameters DPF Regens Resets
WIN $200
Check us Out at www.cojaliusa.com Call us 800 975 1865