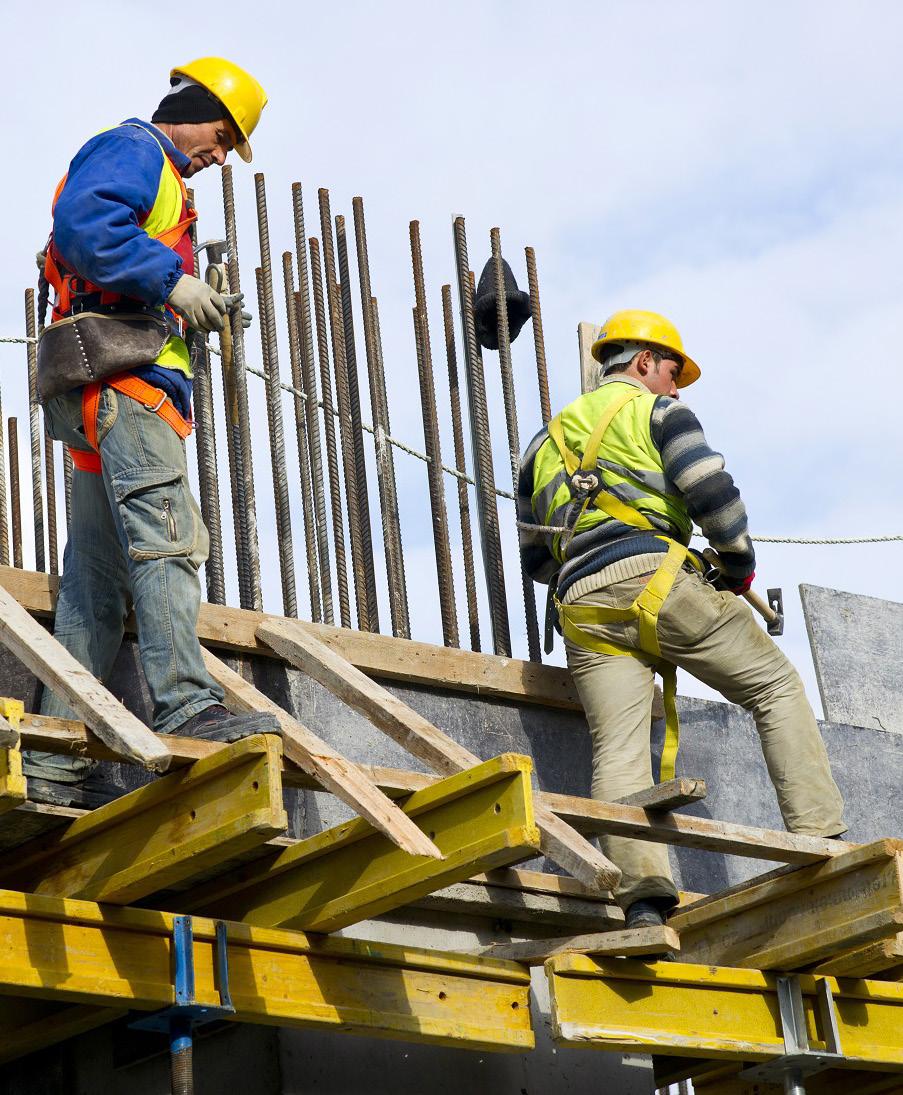
11 minute read
Safety & Compliance
How to Keep Workers SAFE on Construction Sites The construction worksite presents numerous risks for employees, the first and foremost being the risk of falling.
Understand the hazards, their consequences and the measures you can take to create a better working environment on jobsites.
Working in construction is an inherently hazardous activity with a high risk of accidents on site, as well as increasingly complex health and safety risks and hazards off site. This is why knowing the best ways to prevent jobsite hazards will put your business in the optimal position to continue to attract the best workers.
The construction site presents numerous risks for employees, the first and foremost being the risk of falling. According to data from OSHA and the Census of Fatal Occupational Injuries prepared by the U.S. Bureau of Labor Statistics, the top reasons for injuries at work in 2019 included: ˜ Transportation incidents, which increased the most since reporting of this caliber started in 2011 ˜ Falls, slips and trips, which increased by 11% ˜ Exposure to harmful substances or environments, which eventually led to the death of 642 workers, the highest figure since this census began ˜ Fatalities due to fires and explosions, although this is decreasing ˜ Unintentional overdoses due to nonmedical use of drugs or alcohol, which increased for the seventh consecutive year
The worrying aspect of this, of course, is the fact that all but one of the above increased in the most recent year of reporting. Despite what we may perceive to be an overall increase in awareness and regulation in all industries when it comes to worker health and wellbeing, the numbers point to the opposite.
In addition to the top causes of fatalities listed above, it is worth highlighting several other potential risks that can lead to harm or injury: ˜ Lack of communication/ unclear training ˜ Objects that are likely to strike victims — such as falling/flying objects, vehicles or masonry walls — leading to 10.3% of accidents ˜ Electrocution, commonly due to contact with power lines or improper use of equipment, potentially linked to improper training ˜ Being caught between objects because of unsafe access/ egress, unsafe spoil pile placement, failure to inspect a trench and protective systems or no protective systems in place
CONSEQUENCES OF CONSTRUCTION HAZARDS
Knowing the risks and hazards present in a construction environment doesn’t tell the full story from the human or economic point of view. In fact, beyond deaths or physical or mental harm, there is a high toll to pay for businesses that disregard the potential harmful impact of on- and off-site hazards.
The immediate consequence of jobsite accidents is financial. According to a report by ResearchGate, as of 2002, the total costs of fatal and non-fatal injuries were estimated at $11.5 billion, making up 15% of the costs for all private industry. With an average cost of $27,000 per injury, this is a massive consequence of hazards that go unchecked in construction. It is also important to note that the average cost for an injury across all industries is only $15,000 by comparison.
Moreover, employers can incur significant fines if found to be in violation of OSHA standards. Excluding de minimis violations where employers are simply verbally informed of where they are lacking, fines for other violations start from $13,494 and can go up to 10 times that amount for repeated violations.
Another consequence of unsafe or stressful working conditions is more subtle. Mental health repercussions from stress, depression or anxiety are on the rise in the construction industry. Combined with any other type of illness causing employees to miss work, they have the potential to snowball into significant losses for projects.
For workers, beyond the evident impact on personal health and well being, the impact of an accident can be monumental and even lead to the loss of livelihood for an entire family. This is especially true in minority communities, where often the main breadwinner is the injured worker. In addition to the loss of earnings, medical costs can be prohibitive and can have huge impacts depending on the employee’s medical coverage and the severity of injury or illness. HOW TO PREVENT ACCIDENTS AND KEEP WORKERS SAFE
From a regulatory perspective, OSHA (www.osha.gov) imposes regulations for employers to provide a safe workplace. This includes but is not limited to: ˜ Ensuring that construction sites are free of recognized hazards as much as possible ˜ Complying with all standards, rules and regulations issued under the OSH Act ˜ Examining working conditions to ensure they comply with OSHA standards ˜ Providing safe tools and equipment and maintaining them to the best possible standard ˜ Ensuring accurate warnings are in place to highlight potential hazards to workers, including color codes, posters or labels ˜ Having clear operating procedures in place, which are updated as required and communicated clearly to employees ˜ Ensuring that training is given before any work is done on site, and that training is
provided in a language and vocabulary that workers understand ˜ Having a hazard communication program if employees work with hazardous chemicals ˜ Providing medical exams and training
Beyond the OSHA employer guidelines listed, there is the growing importance of ensuring health and well-being are looked after in the realm of mental illness. Employers have a moral duty to ensure working environments are as stress-free as possible, and free of discrimination and abuse of all kinds.
Employers should also remain transparent and honest about hazards and incident reporting. Any accidents or injuries should be discussed openly with employees to ensure all parties take away lessons from what has happened. These discussions may lead to an information exchange that can ensure better practices in the future. ET
Hensel Phelps Keeps Discovering Profitable Uses for DRONES Weekly flights provide the map for daily work planning, safety briefings, progress reports and more.
Hensel Phelps used drone surveying and Propeller’s 3D site surveys to track, map and measure the project to demolish and replace a terminal at Honolulu’s Daniel K. Inouye Airport. The contractor has embraced virtual reality in managing airport projects, and drone data, marshalled by Propeller’s online processing and presentation platform, became the next step in updating construction status digitally and communicating work plans.
“We started using [drone data] in smaller chunks, really identifying areas we knew we were going to be working in,” says Carter Johnson, VDC engineer with the Hensel Phelps Pacific office. “The initial drone flight to map the entire project site before we started demolition was the first time we’d ever flown a jobsite.”
How the software was used evolved throughout the project. “As we were doing demolition, it was used like a progress tracking tool. We also utilized it to track existing
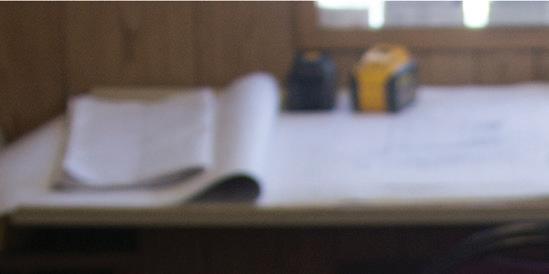
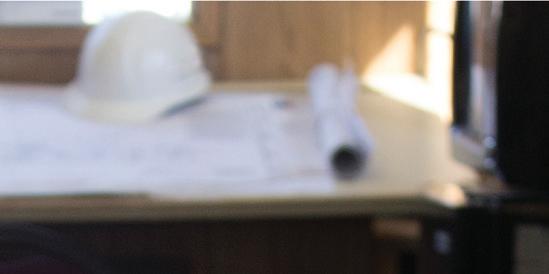
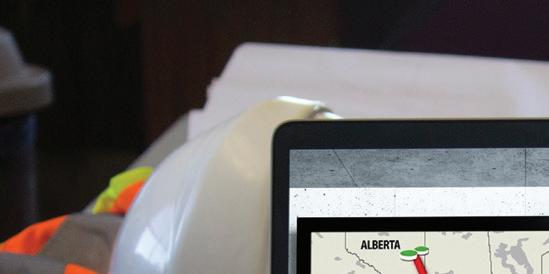
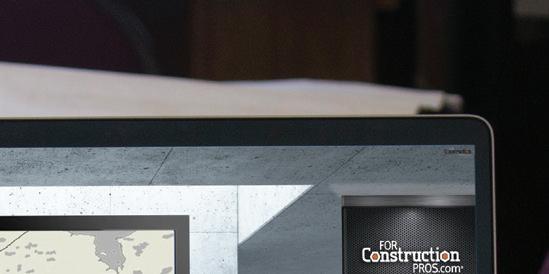

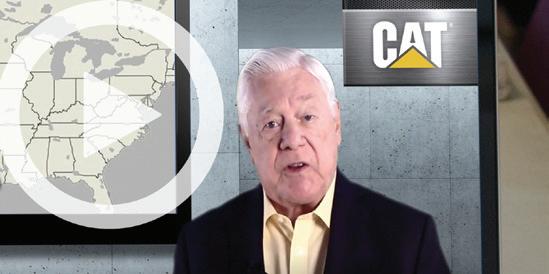


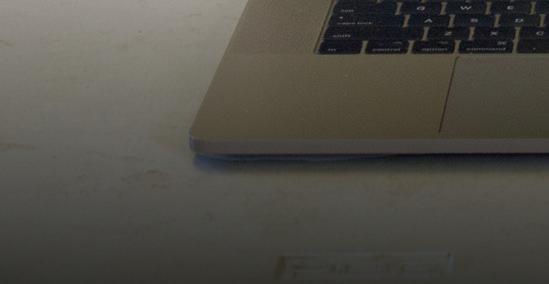
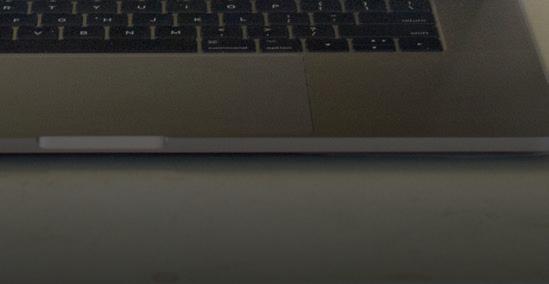

YOUR INDUSTRY NEWS SOURCE
Construction News Tracker is the construction industry’s only regular video newscast, bringing you breaking news, top stories, and product innovations. Watch for updates every other week with construction correspondent Roger Mann.
Brought to you by:
Produced by: structures,” says Johnson. “During demolition, manholes get covered up and other things happen. We can go back to a previous survey and have the northings and eastings from the Propeller survey and drone flight and be able to locate those items.”
DONE RIGHT THE FIRST TIME
By 6:30 a.m. each morning, all the superintendents, field engineers and foremen on site were soon meeting in front of aerial imagery and would go around the room and brief each other on the day’s work. “We can see real time how the site’s changed and the different areas people are going to be working on,” says Brian Holm, Hensel Phelps project superintendent.
The drone imagery keeps people out of hazardous areas of the site, and Hensel Phelps now uses the aerial images to do better safety briefings with up-to-date visuals.
“When I’m going on a job walk, it’s pretty hard to say that you’ve walked every piece,” says Adam Cotton, the contractor’s regional director of safety and health. “With Propeller, it eliminates that risk. You’re seeing what your project is — you’re not having to physically go into situations [or] down in trenches. It gives you that knowledge without stepping foot on site.”
The Inouye Airport job quickly showed the value of inputting layers to Propeller’s online platform in order to overlay utility drawings (existing ones to avoid and new ones to build) on current site images.
“We were able to survey in those positions prior to pavement demolition,” says Johnson. “We had the CAD files with the location of existing utilities, which we were then able to overlay with our excavations.”
The information has become a key element in issuing “dig permits” on complex sites. “It’s part of our Hensel Phelps process that we do dig permits,” says Johnson. “The document for that didn’t normally include a drone image, but it did include a map of the area with utilities. Because we were able to utilize the drone flights in Propeller, we were able to overlay the existing utilities that we shot in along with the new utility installation (plan), with accurate, up-todate drone flights as the background, which really helps communicate with the operators during that stage in the project.”
Operators can double check their location using the landmarks currently visible on the site surface. “Obviously, we still mark them out in the field with spray paint and such, but the overlaid plans give them an added advantage for knowing where work is at,” says Johnson.
OVERCOMING CONFLICTS
Overlaying utilities drawings on site images delivered big benefits by showing significant utility conflicts. A 16-in. water main and the main power feeds for the airport cut through the site in a location that was not indicated on the drawings.
“We used Propeller to identify those impacts,” says Holm. “We had the drone snapshot and overlays of where the existing utilities used to be and where the existing utilities ended up being.”
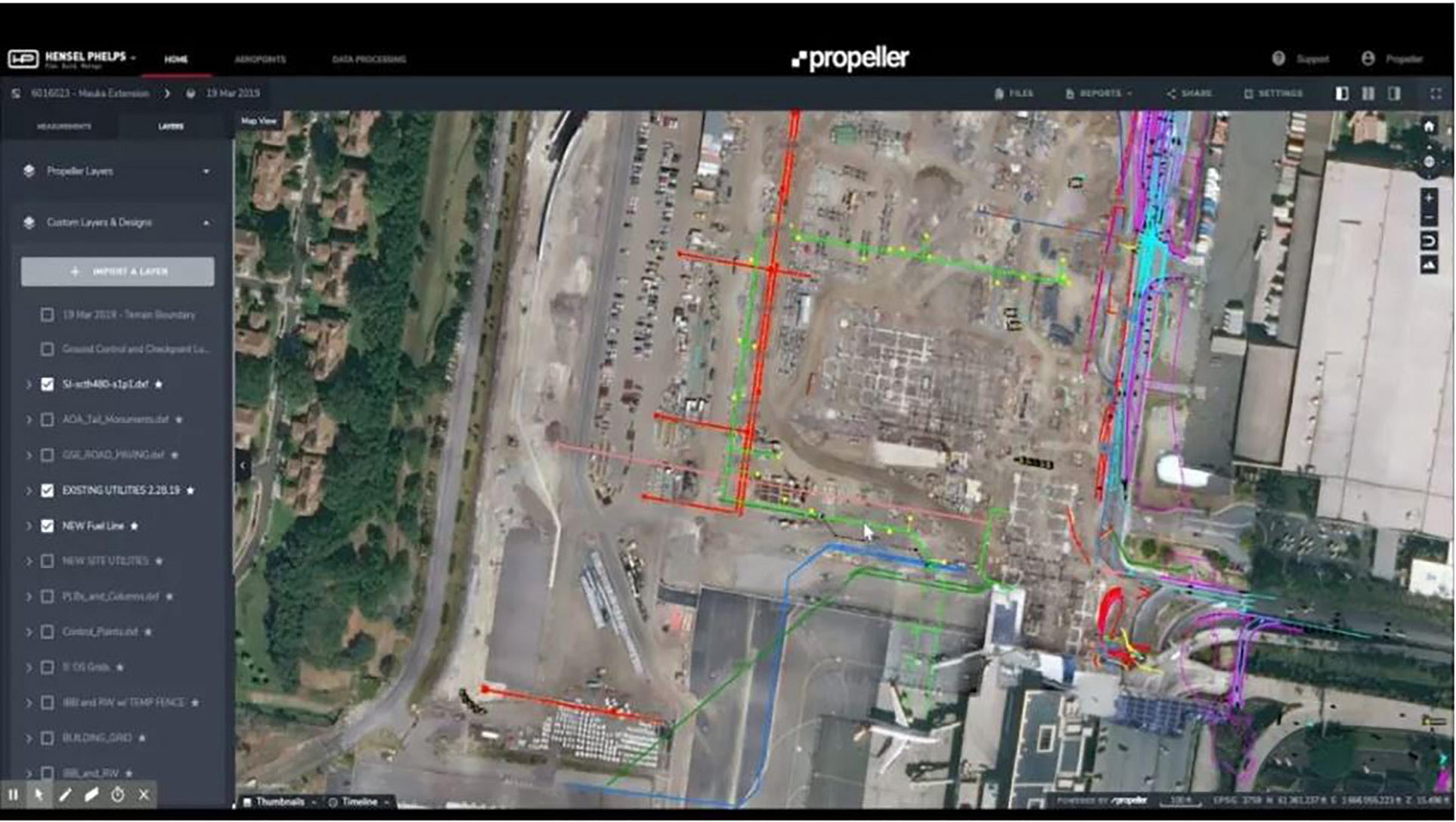
Drone imagery was essential to safely and efficiently communicate those surprises and revise the work. It also proved useful in addressing contract changes.
“If you show the owner — or anybody who isn’t directly involved with all the details associated with the work — a line marked on a drone flight image and say, ‘This is where it said it was supposed to be, but it’s actually over here,’ you don’t have to know a lot about the work for it to make sense,” says Johnson.
WEEKLY FLIGHTS
“We flew just about every single week from when we started the project back in 2018,” says Johnson. “Toward the end of the week, the site started changing and by the next drone flight, [site management] would really be looking to utilize the new images in the meetings so that they could have an accurate representation of the field when they were communicating where the work was going to be.”
Latitude and longitude information in the point cloud that the drones capture extends the value of the data into quality control. “With the drone, you’re able to fly the entire jobsite in an hour or hour and a half, and not only have a complete jobsite image, but also survey locations of everything that drone was able to capture,” says Johnson. “You’re packaging multiple things into one platform.
“The superintendent is able to just overlay the utility CAD file from the contract documents on the current data set from Propeller and see that, ‘Okay, we’re excavating in the area where the new utility is supposed to go. QC all good,’” he adds.
VALUE DISCOVERY CONTINUES
Drone data was uploaded with ground control points after each drone flight. When Hensel Phelps broke ground at Inouye Airport, the vendor’s data processing time was a day or more. Now, it is building 3D maps with the data in under 24 hours. The Propeller platform organizes the data and makes it easy for users to find current and previous images for comparisons. The 3D survey can be simplified to a 2D survey and orthomosaic photo image.
The data available via web browser allowed Johnson and the crew to experiment with downloading point clouds and other ways to present and use the data. “It’s another Hensel Phelps process that we do model coordination. There’s a 3D model for the building for the MEP, the underground utilities, all of that,” Johnson notes.
Hensel Phelps was able to export the point cloud generated from the drone survey, import it into Navisworks and show it to subcontractors during the BIM coordination meeting to provide a picture of what it looks like in 3D in relationship to their 3D model of utilities, as well as in consults on concrete work for footings, etc., Johnson notes.
Hensel Phelps has benefitted from drone data in additional ways, from initial site flights to document existing conditions prior to starting work, to quick stockpile measures, improved communication of site logistics and route planning, recording of unforeseen conditions and more.
“It was hard to see that value until we started using it,” Johnson acknowledges. “Now that we have it, it’s kind of hard to be without it.”
“What we’ve realized is that they [drones] are tools for conveying our plan,” says Holm. “If you understand the value of that tool and how simple it is, and use it to what it’s capable of, it will save you time and money out in the field.” ET
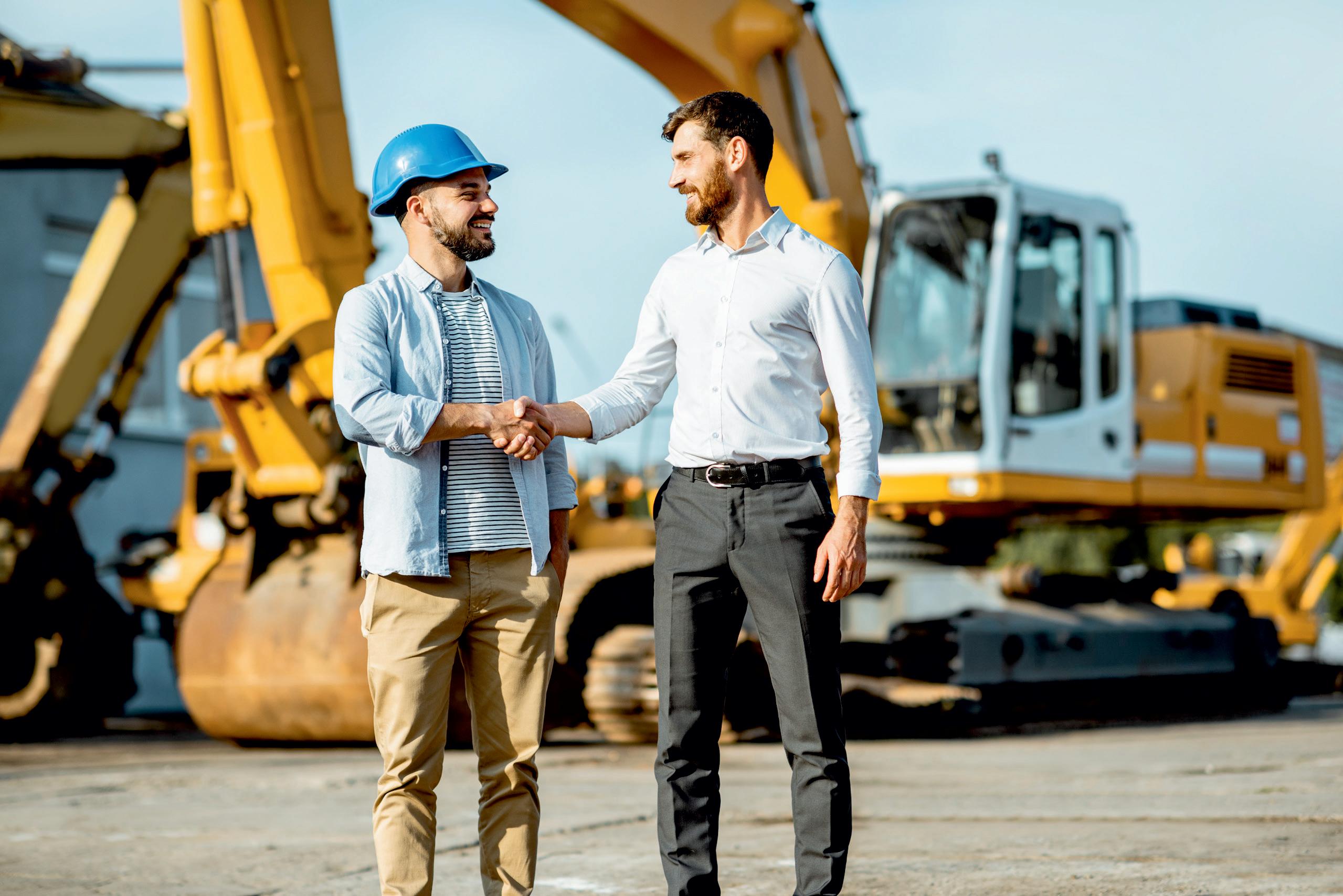