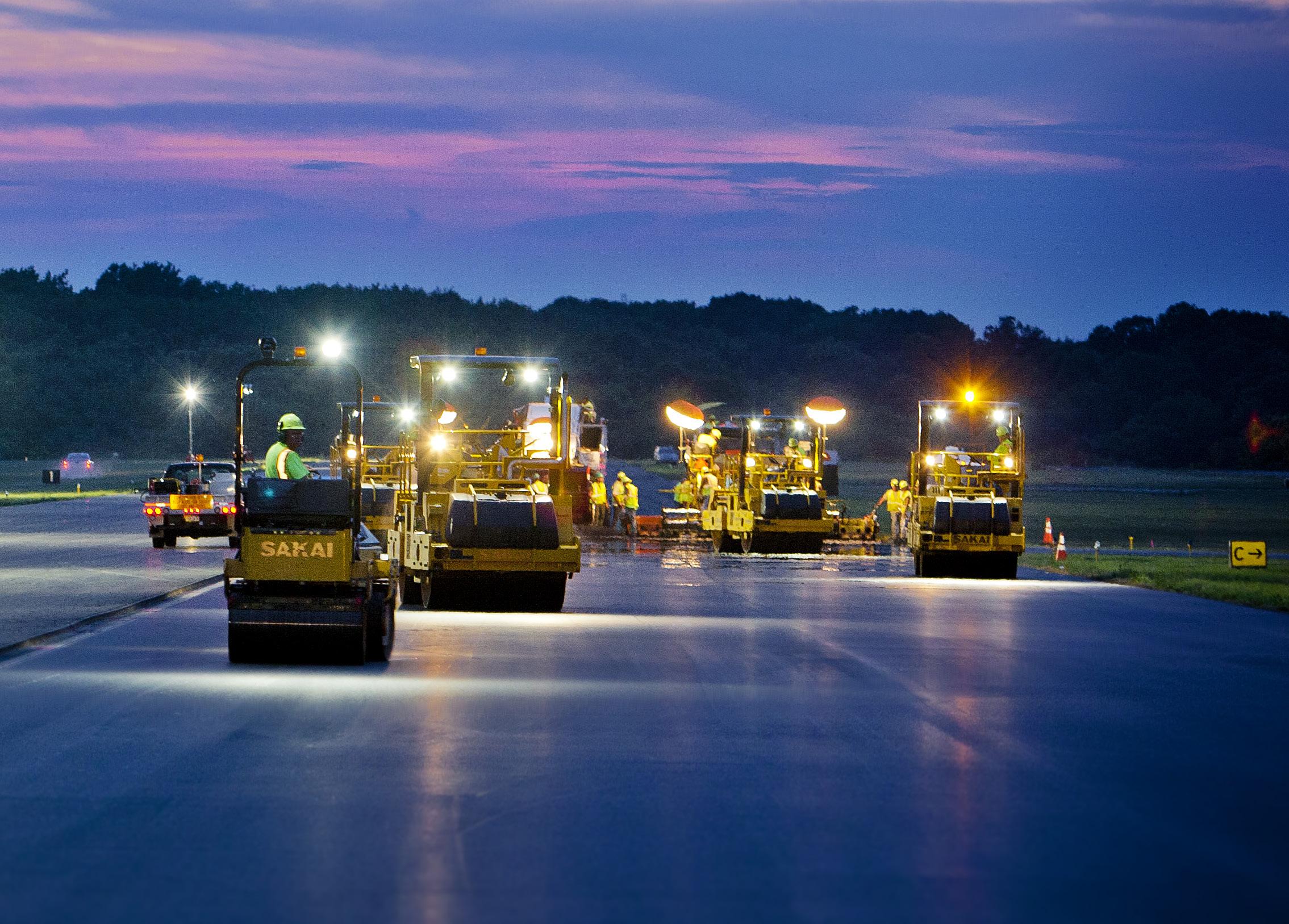
22 minute read
HOW OPERATOR TRAINING IMPACTS COMPACTION PERFORMANCE
Proper performance by your crew on the roller can help maximize mat quality.
Roller operators need to be properly trained to understand the effects of changing amplitude and frequency on a steel drum roller and how these changes affect the ability to reach density, maintain smoothness and a roller’s speed to keep up with the paver.
Agood paving job will have a smooth, dense appearance that looks flat and tight without any gaps between the aggregates at the surface. We all know that appearance doesn’t just happen. There are a lot of factors that affect mat quality.
The paver, asphalt mixture and even the distance from the asphalt plant to the jobsite all play a role in achieving optimum mat density. But the last equipment to touch the pavement is the rollers, and their operators have the greatest influence on smoothness and those all-important density numbers.
“Roller operators need to understand their important role in the paving process, as compaction is the last step in laying down a quality pavement,” says Eric Booth, product training and marketing manager at Sakai. “They need to be observant in order to monitor their machine... watching asphalt temperature, water tank level, DEF tank level, status of the DPF and if any asphalt is being picked up by the drums, etc.
“The plant, milling machine and paver can do everything correct,” he adds, “but if the roller isn’t on the mat at the right time, or not maintained correctly, they could get density issues that lead to early failures and potentially impact any guarantees the contractor may have made.”
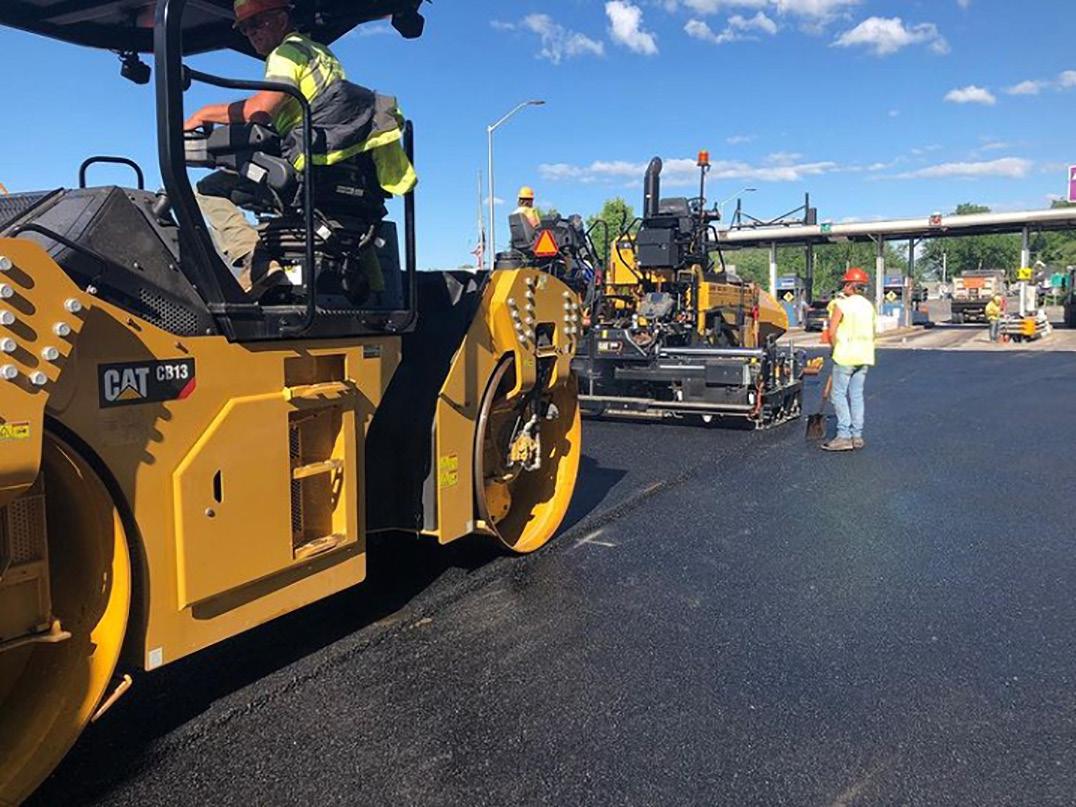
TRAIN FOR SUCCESS
To be successful in today’s competitive paving market, asphalt paver and roller operators must acquire a deep knowledge of the equipment’s features and put this knowledge into practice on the jobsite. With long-time equipment operators retiring at a high rate, the next generation of operators must receive in-depth training on the equipment in order to meet project specifications without costly rework, so companies can maximize equipment ROI.
“Untrained personnel can cause not only bad/inadequate/ undesirable results in the compacted surface, but could also be a danger at the jobsite, potentially causing damage to the equipment or, worse, causing harm to other personnel,” notes Bert Erdmann, product manager compaction and assisted systems, BOMAG Americas. “Untrained roller operators potentially could cause undesirable results or permanently damage the material.”
Over and under compaction of the asphalt are common mistakes operators can make and can adversely impact the final product.
“Under compaction would most likely result in inadequate densities, which could potentially result in fines or rework, depending on what the job specification requires,” Erdmann says. “Over compaction often results in breaking the aggregate,
which would ultimately lead to premature failure.” For example, water can enter the asphalt layer and freezing conditions would cause the mat to fail, which could lead to potholes, etc.
Under compaction means the pavement is more permeable to water infiltration from above or below the pavement. Longterm exposure to water will strip the asphalt cement bonding the aggregates together and cause the pavement to ravel or fall apart.
Over compacting results in pavement that has no internal, interconnected air voids or air space, so when ambient temperatures increase or decrease, there is little or no room for expansion or contraction of the asphalt cement (binder) in the mix. In hot weather, the asphalt cement flushes or bleeds to the surface, which can result in instability of the mix or susceptibility to rutting.
Operators need to know how to properly compact the mat to avoid both. “Roller operators are often ‘on their own’ on the job to work with the quality control personnel who are measuring density using a nuclear or nonnuclear gauge. So, it is important that operators are properly trained to understand the effects of changing amplitude and frequency on a steel drum roller and how these changes affect the ability to reach density, maintain smoothness and roller speed to keep up with the paver,” says Todd Mansell, product application specialist, Caterpillar, Inc.
“Roller operator training is a three-pronged relationship between amplitude, frequency and impacts per foot, or roller speed, on a steel drum roller,” he continues. “Operators should always try to maintain a minimum of 10 impacts per foot to achieve density efficiently, but equally important, to meet or exceed smoothness specifications for IRI.”
Mansell says the simplest calculation is to take the roller frequency setting and divide by 10. For example, if the roller is set on high frequency at 3,800 vpm, then 380 fpm (3,800 / 10 = 380) should be the roller’s maximum ground speed — or 380 / 88 = 4.3 mph. “Most rollers on the market today have a gauge indicating the impacts per foot, so the roller does the calculation for the operator automatically based on the frequency setting,” Mansell notes.
Operators should be trained to understand the relationship between impacts per foot and roller speed as it is critical to maintain smoothness on a job.
TRAIN FOR OPTIMIZED MACHINE USE
Operators should be trained/ given the knowledge to overcome some of the hurdles that can crop up on a project, such as difficult weather conditions, clumpy mixes, extremely thick or thin lifts, joining of hot and cold lanes, etc. This will help ensure the machines are being used to their fullest potential.
Most roller manufacturers, in conjunction with their dealers, offer training for end users of their equipment. That training is available in a variety of forms, including group seminars, hands-on courses or one-on-one training on the jobsite or at the manufacturer’s training grounds.
“Operators not only need to understand these relationships between amplitude, frequency and impacts per foot... they must understand how to change these settings on the roller they are operating,” Mansell advises. “This sounds simple, but all manufacturers have different methods and combinations of how to change amplitude and frequency. Some changes are made by switches at the operator’s station, while other changes are made on the drum itself and, further, a combination of the two. Understanding how to make these changes is not always intuitive if you have not been properly trained.
“It can be very challenging for operators, especially when they are on different rollers from day to day and job to job,” he acknowledges. “All manufacturers offer charts and ‘cheat sheets’ on how to change these roller settings. Ask for these guides and stick them on the roller somewhere obvious for the operator to review, and laminate them to make them weatherproof.”
Don’t forget to teach safety best practices to your operators. According to Erdmann, operators should know: ˜ the functionality and proper use of the controls on the roller, ˜ proper rolling techniques and best practices/commonly applied rolling patterns, ˜ and proper use of water — just enough to keep material from sticking, but not too much so the asphalt mat doesn’t cool down too fast.
TRAIN ON TECHNOLOGY TO SIMPLIFY OPERATIONS
Manufacturers of equipment have been hard at work trying to simplify and standardize many operations, including compaction. The main technologies that are available to help operators achieve optimal compaction are pass count mapping and temperature mapping, often collectively referred to as “intelligent compaction.”
“Intelligent compaction often includes some type of stiffnessmeasuring instrument, most commonly an accelerometer mounted near the drum of the roller to give an indication of material stiffness by measuring the rebound of the steel drum
— Todd Mansell, Caterpillar
The technologies and best practices for the construction of asphalt pavements are constantly changing. Be sure to stay on top of training your operators to ensure your efforts will be successful.
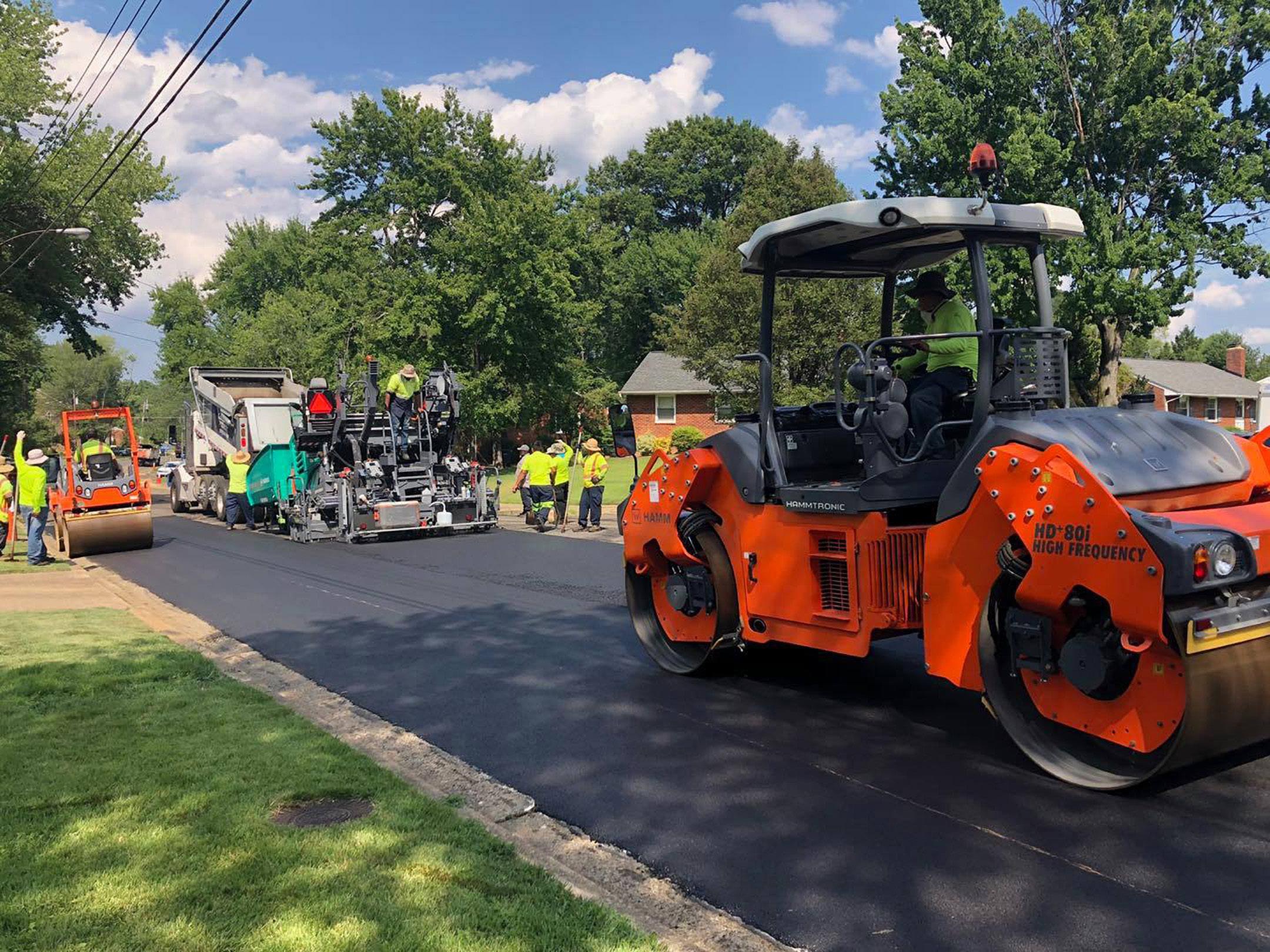
during the compaction process,” Mansell says. “The most valuable and useful tools for operators today are pass count mapping that keeps track of the number and location of roller passes and displays it to the operator in real time during the rolling operation, and the temperature mapping that helps operators stay in the proper temperature range, or zone, for optimal compaction.”
BOMAG ECONOMIZER provides a stiffness gauge to the operator with direct “traffic light-type” feedback of the current status of compaction. More sophisticated systems such as ASPHALT MANAGER take it up a notch by reducing the drum output automatically to prevent over compaction.
“BOMAG’s BOMAP Connect is the next evolution in Intelligent Compaction,” Erdmann says. This subscriptionbased cloud solution connects the BOMAP app with the ability to plan, track and document multiple compaction projects. BOMAP-equipped rollers can effectively “see” each other and the projects and data exchanged with the ability to connect multiple rollers with each other on the jobsite to provide a visual compaction map. “The operator [on the] machine, the supervisor on the jobsite and even your project manager back at the office have instant connection to your job’s compaction status.”
Having visibility like this helps ensure operators have real-time information on their compaction efforts so they can make adjustments accordingly.
“Roller operators are the last ones on the mat, so they normally are first to be blamed if something goes wrong,” says Tim Kowalski, HAMM application support manager at Wirtgen America. “Technology today is much more sophisticated and designed to assist operators with consistency of operations, while also ensuring they are doing the job correctly.”
Intelligent compaction technology has been instrumental in helping contractors understand and better manage density. Manufacturers have worked to make the data visible and easily accessible while the machine is in use.
“Intelligent compaction on HAMM rollers features colorcoded pass mapping,” Kowalski says. “Operators can tell the number of passes they have completed and where they have already been on the mat so they know what areas have already achieved compaction. They can also tell where to stop and start on the mat, which is especially helpful during night work.”
Other technologies are also available to help operators achieve smoothness goals.
“There are a number of technologies to aid the roller operator in getting density, some being more high-tech than others,” Booth says. “Sakai offers an Exact Compact Meter to show the operator which speed gives them the appropriate impacts per foot. Rollers that utilize oscillation can hit density and smoothness in no-vibration areas. Though density is goal No. 1, the compaction crew can’t forget about smoothness or roller efficiencies either. More states are setting smoothness requirements as part of the specifications, and getting density and smoothness in as few passes as possible is important.”
The technologies and best practices for construction of asphalt pavements are constantly changing. Staying on top of training your operators will ensure your efforts will be successful.
“Training should be a never-ending process,” Kowalski emphasizes. “As manufacturers, we want to make sure companies are getting the most out of the equipment. We want to train operators, foremen, superintendents and even the owners on these machines and what they are designed to help with.” ET Untrained roller operators potentially could cause undesirable results or permanently damage the material.
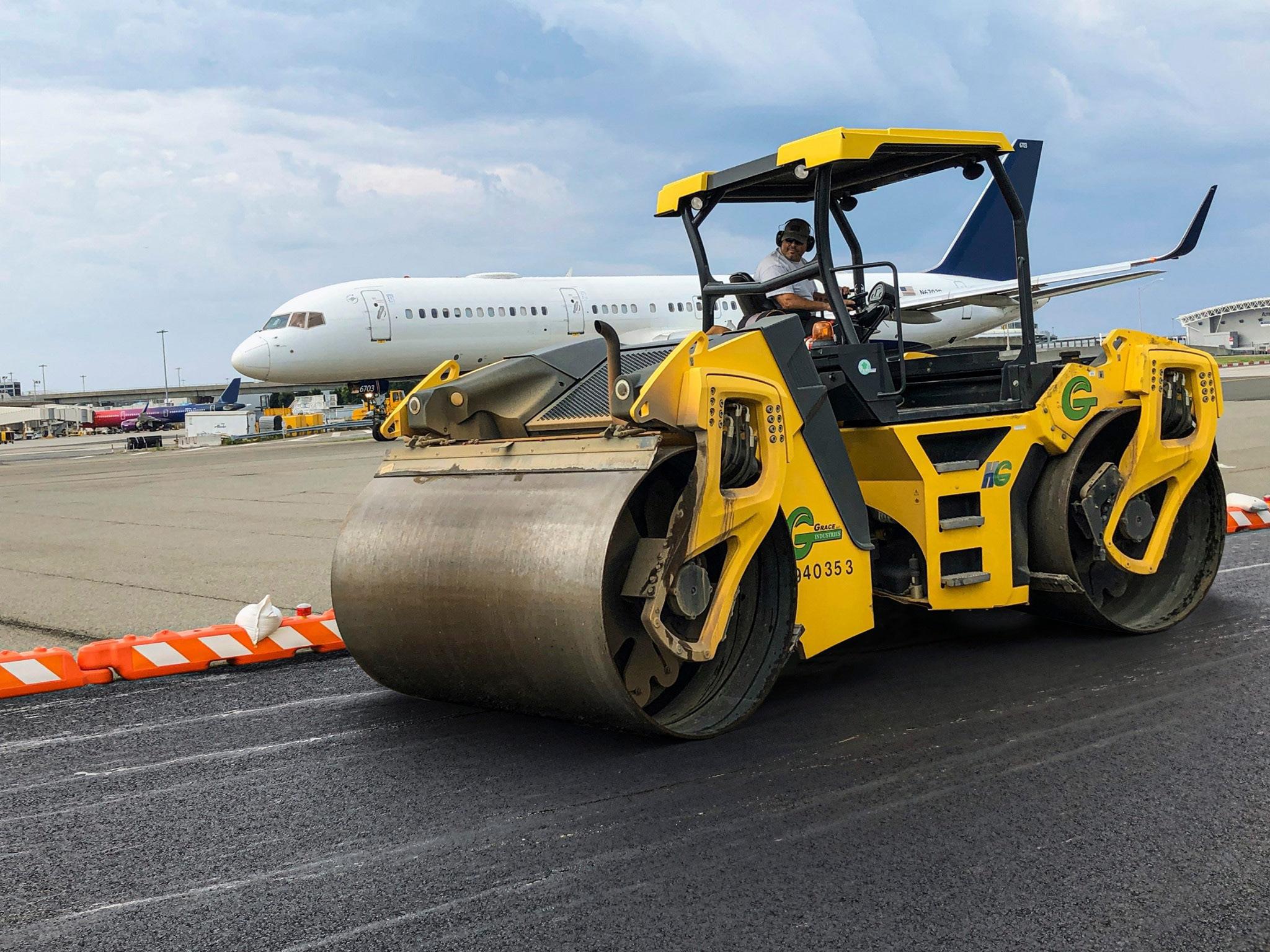
SET THE STAGE
When teaching your operators proper rolling techniques, keep these tips in mind: • Maintain proper speed — Roller speed has one of the greatest influences on mat quality. Driving too slow can over compact the surface; driving too fast can leave gaps and compromise safety if the operator gets too close to the paver.
Using the correct speed will also help to maintain the appropriate impact spacing to prevent washboarding. For most jobs, correct spacing is between 10 and 14 impacts per foot. • Monitor mat temperature — Typically, asphalt comes out of the plant at about 300° F. At that temperature, it is relatively viscous and liquid and is readily compacted. As it cools, the asphalt firms up and compaction becomes increasingly difficult. At about 100° to 150° F, it has cooled enough that the aggregates no longer move. A good operator will understand the temperature range they must work within and adapt accordingly. • Determine when to use vibratory and static modes — Vibratory compaction creates shock waves that compact from the bottom up, while static compaction works from the top down. Most manufacturers will recommend that you roll in vibratory mode right out of the gate. For most jobs, you will use a combination of compaction modes, starting with vibratory compaction and finishing with static. With vibration, you’re getting the desired density, and with static you’re finalizing the compaction. • Select the right amplitude — Generally, amplitude settings are determined by the depth of the lift. Machines with variable amplitudes allow the operator to fine tune the setting to the mix. Lower amplitude settings are recommended for lifts of 2 in. or less; higher amplitude settings should be used for deeper lifts. • Avoid sharp turns or sudden speed changes — Sharp turns can tear the mat and decelerating/accelerating quickly can rip/tear the mat or leave indentations.
Here is a collection of products designed to enhance jobsite efficiency, productivity and/ or safety. For more information, use the URLs shown or visit the New Product Directory at www.ForConstructionPros.com.
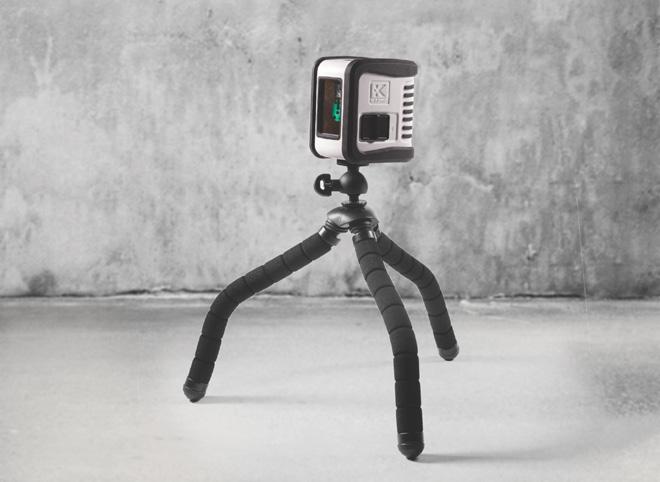
The 842 ProLaser Bambino Cross Laser Level series is based on the heavy-duty 872 Prolaser PLUS Cross Laser Levels and incorporates many of its features.
•Include intersecting horizontal and vertical beams at 90° and feature an indoor laser range of up to 50 ft. •Accuracy of 0.0004”/1” and self-leveling range of +/- 3° •Manual mode for angular layout/marking with a visual “out of level” warning •Mechanical pendulum lock mechanism incorporated in the on-off switch •Flexible omni-set tripod for mounting and attaching levels to most surfaces •Available in red (842S) and green (842GS) versions www.forconstructionpros.com/21722913
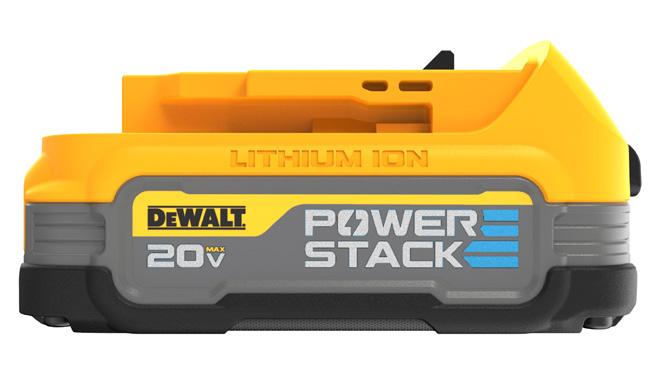
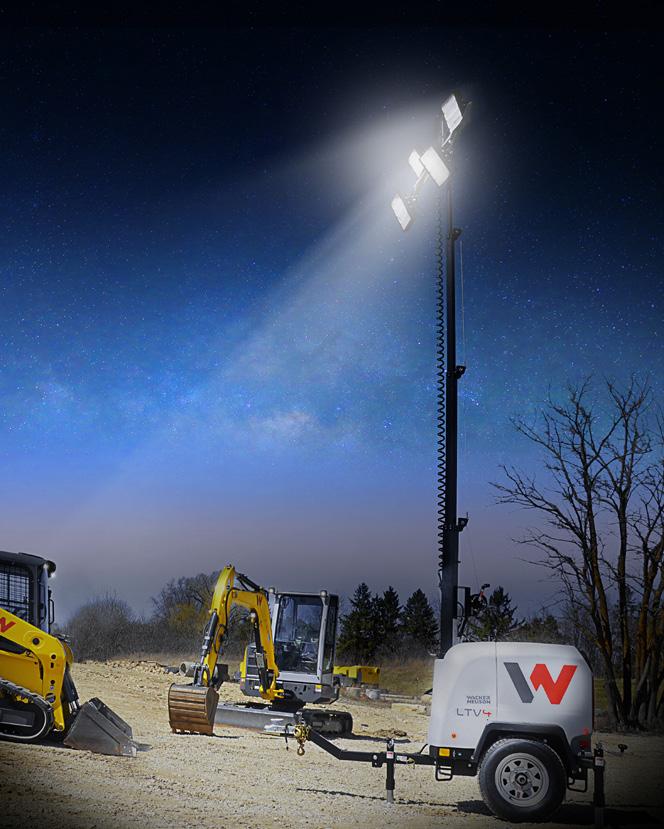
Wacker Neuson LTV4L Compact LED Light Tower Model
The LTV4L is powered by a Kohler engine and features four 300-watt LED lights that offer life expectancy of up to 50,000 hours.
•145-gal. fuel tank enables up to 187 hours of run time (lights only) •Instant on/off operation with no time needed to warm up or cool down •Adjustable vertical mast extends up to 23 ft. and can rotate 360° •LED fixtures can be adjusted by hand to focus light exactly where it is needed •4-kW auxiliary power with 120V 12A duplex GFCI receptacles provide added power for on-site power tools www.forconstructionpros.com/21808653
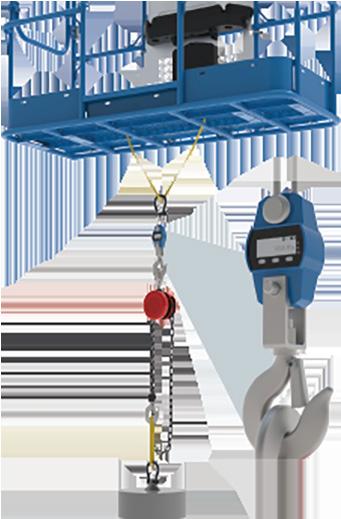
Genie Tool Kit for Load Sense Testing, Calibration
This calibration tool kit includes everything service personnel need to make it easier and faster to do a full load calibration test of most Genie boom lifts equipped with digital Load Sense.
•Provides ability to conduct the full load calibration without putting physical weights in the platform •Testing and calibration can be performed in less than 10 minutes by one person •Zero load calibration can be completed in as little as 30 seconds •Includes approved rigging, scale, chain hoist and instruction manual in a portable carrying case www.forconstructionpros.com/21735052
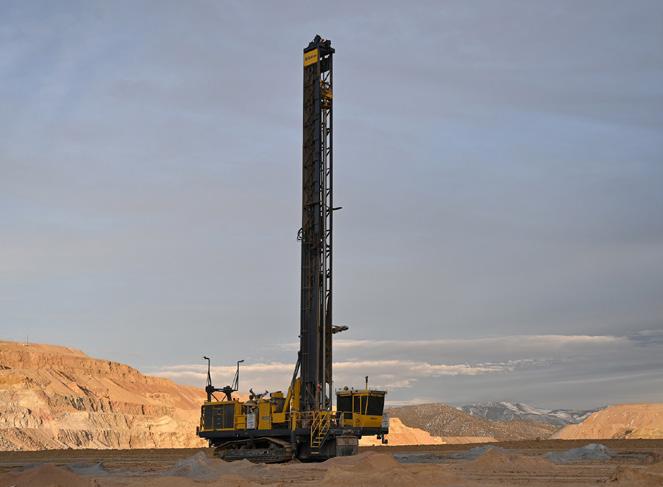
Epiroc Pit Viper 291 Blasthole Drilling Rig
The Pit Viper 291 single-pass drill is designed for larger diameter drilling in soft to medium ground conditions.
•Capable of 11- to 12 1/4-in.-diameter holes with an 85,000-lb. bit load capacity •Offers 80,000 lbs. of pulldown capacity, 35,000 lbf. of pulldown force and 11,000 ft.-lbs. of torque •Rig Control System includes scalable automation features such as optional AutoDrill and AutoLevel and the BenchREMOTE package that allows an off-drill operator to run one or multiple units •Also capable of fully autonomous drilling www.forconstructionpros.com/21722564
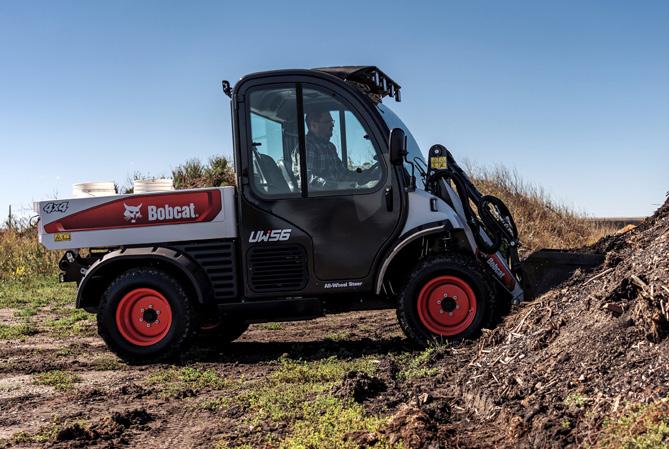
Bobcat UW56 Toolcat Utility Work Machine
The UW56 serves as a pickup, compact tractor, loader and work vehicle in one, plus it can be paired with over 45 different attachment configurations.
•Comes equipped with redesigned allLED lights for optimum visibility and long-term durability even in low-light working conditions •Enhanced drive response system provides smoother acceleration/deceleration and automatically recalls drive response settings •Other updates include improved corrosion protection, an overhead dashboard with integrated 5-in. display and ultra-comfortable cab www.forconstructionpros.com/21809167
DeWalt POWERSTACK 20V MAX Compact Battery
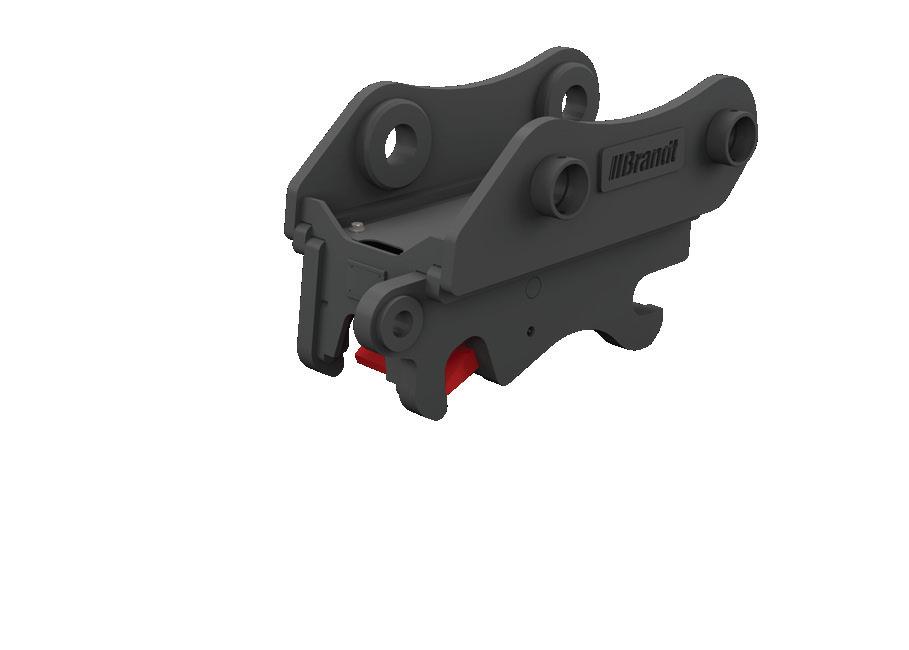
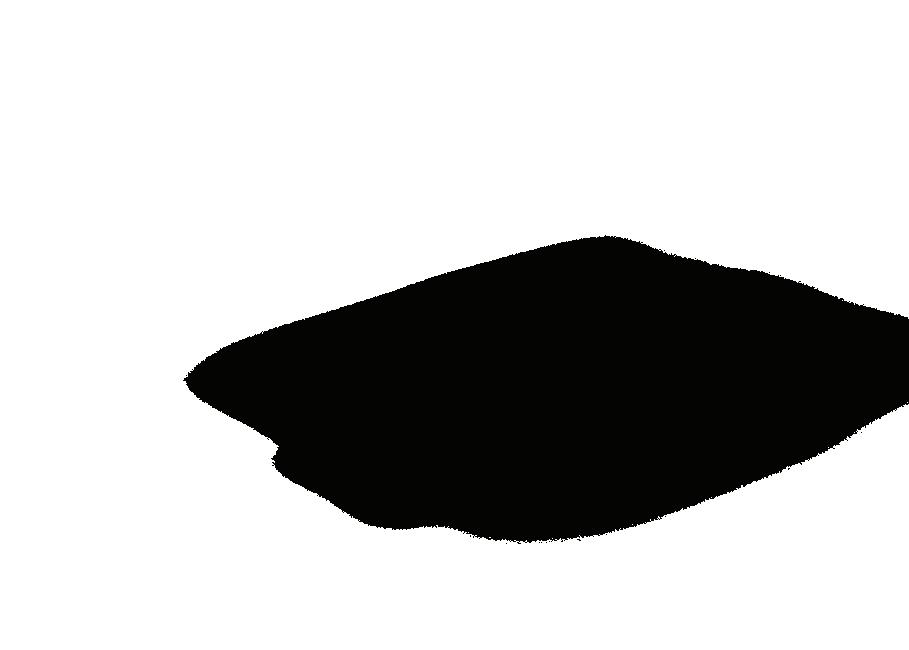
The POWERSTACK 20V MAX Compact Battery is a next-generation lithium-ion battery that is designed to provide 50% more power, enabling broad application capabilities and fast performance with cordless tools.
•25% more compact and 15% lighter than DCB203 battery •Designed to provide tool maneuverability, high precision and reduced fatigue when used in tight workspaces •LED fuel gauge displays battery’s stateof-charge •Durable, non-marring rubber overmold provides impact resistance while helping to protect finished surfaces •Compatible with all 20V MAX tools and chargers in the 20V MAX system www.forconstructionpros.com/21772036
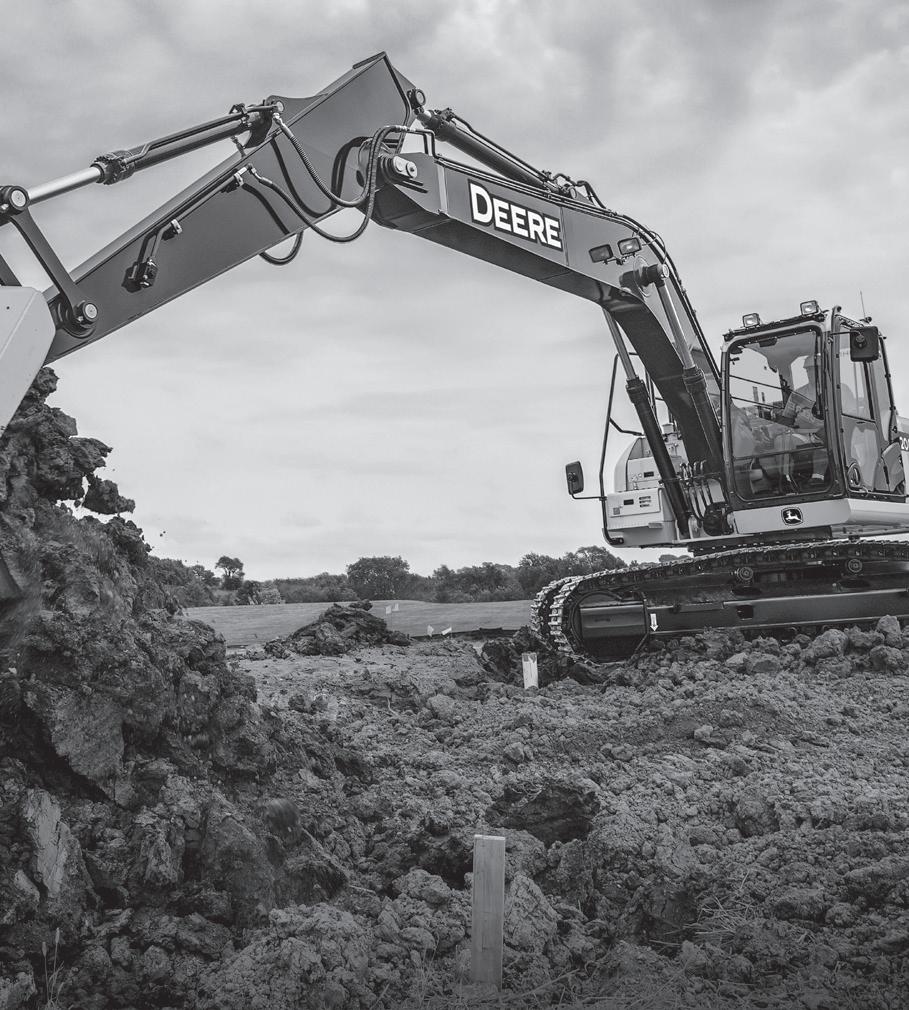
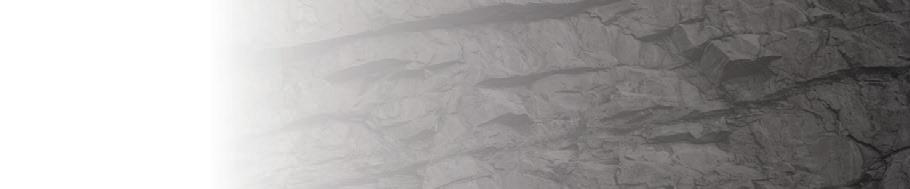
The GPB18V-5C 18V Jobsite Radio with Bluetooth 5.0 and Power Station provides connection to music streaming services or stored songs via a mobile device.
•Four-way speakers with integrated subwoofer create high-quality stereo sound that projects in all directions •Offers USB charging capability for mobile devices plus four 120V AC power outlets can be used to power lights, tools, electronics and more •Protective aluminum and rubber roll cage •Runs on 18V lithium-ion batteries or included 120V AC power cord •Large digital media bay provides secure storage for most mobile devices www.forconstructionpros.com/21627825
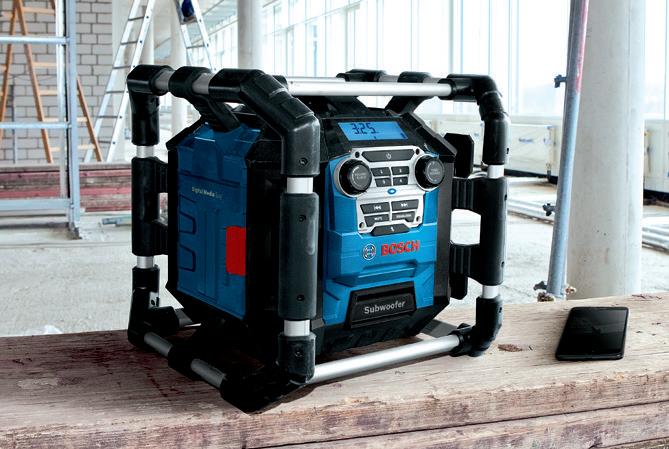
GET A SOLID GRIP ON SAFETY.
Brandt’s new Hard To The Core dedicated pin grabber coupler ensures a safe, positive coupling with your attachment, holding it in the working position at all times. The design utilizes fewer moving parts for superior reliability, all while meeting rigorous ISO 13031, EN 474, and AS 4772 safety standards. And, it delivers faster cycle times than the competition.
That’s Powerful Value. Delivered.
Plan to Navigate the Cost Maze of 2022
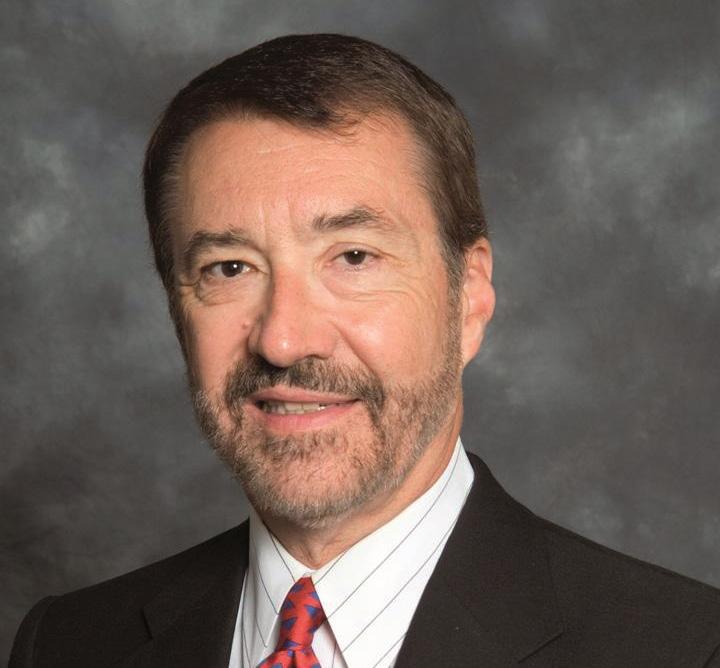
Garry Bartecki is the managing member of GB Financial Services LLP and a consultant to the Independent Equipment Dealers Association. He can be reached at (708) 347-9109 or gbartecki@comcast.net.
@Matthieu – stock.adobe.com
Just when we thought we were out of the weeds, here comes another virus variant (omicron) to stir the pot once more, giving us another major issue to deal with as we enter 2022. Just what we needed!
Unfortunately, the equipment situation is still a mess, as well. There is significant demand but a lack of both new and used units. New unit prices are up 20+% and used units are up 30+%, causing a lot of pent-up demand and deferral of equipment purchases. In short, contractors are deciding to keep their current internal fleets longer, hoping that required parts will be available as needed.
As part of my homework to keep up to date on the industry, I reviewed two major industry reports prepared by Deloitte (CPS firm) and Equipment Watch. The major points I gathered were: ˜ Equipment costs will remain above average for some time to come. So, if you need equipment for your 2022 schedule, be prepared to have to deal with used or rental units. ˜ Technology and related productivity increases will allow companies that embrace it to lower time and costs on jobs, which will become reflected in their bid pricing sooner rather than later.
Another point I noted in the reports is that equipment costs now represent up to 30% of job costs. When I was CFO at the Associated Equipment Distributors, it was running at about 17%. Thinking about it, this could mean: ˜ equipment costs are higher; ˜ more equipment for specific uses is available today compared to 10 to 15 years ago; ˜ or contractors are finding ways to cut costs and improve productivity using the current crop of equipment available to them.
The answer is probably a combination of the three.
PLAN FOR PRODUCTIVITY
In planning for 2022, I would advise you do a quick inventory of what you have and develop a unit by unit list of maintenance required now or sometime during the year. As part of this process, you may want to nail down your parts suppliers and purchase any hard to find parts if they are available. In addition, I would schedule any outside work ASAP to determine whether the dealer or rental company can make your units ready before your construction season starts. On the productivity front, if you want to stay competitive and profitable, you should examine your people, processes and technology to determine if they will provide adequate productivity to remain competitive compared to contractors that have chosen to upgrade their systems to cut the costs and time required to complete a job. The important thing about productivity is it is basically “free” if you can use your existing staff to get work completed with fewer hours compared to what they did in the past (same people and material costs converted into a completed project in less time). Believe me, this is where the industry is heading, meaning changes are required to improve productivity. I can promise that you will have a problem if you are doing things the same way you did seven to 10 years ago. One area where a lot of contractors are suffering is finding adequate workers. Guess what? There are costeffective technology platforms focused on recruiting blue-collar workers that can help. I suggest investigating these platforms then arranging a demo. (Links to several options can be found at www. ForConstructionPros.com/21940892.)
PREPARE FOR INFLATION-RELATED COST INCREASES
The last topic we need to cover is inflation. It is here and it is going be around for some time. Contractors will feel it in material, labor and interest costs. Consequently, it may be prudent to consider converting any floating rate borrowing into a fixed rate note while rates are still low. Last I heard, they are expecting at least two rate increases during 2022.
With inflation raising your costs, your bidding has to take these higher costs into account, which I’m sure it will. But even if it does, you have to manage your margins on a real-time basis to ensure they will provide gross profit dollars in line with your historical gross profit margins.
You do not want to find yourself in a position where you bid based on where you thought your costs would end up and then find out the margin dollars are well below where they should be. In 2022, where costs could materially change throughout the year, you have to know on a daily basis how the “real” cost compares against budget. See what your system can do to provide this information.
Before we close, one quick follow-up: the Employee Retention Credit referred to in a previous column (www.ForConstructionPros. com/21722627) will not be available for Q4 of 2021 unless you are a new company. It’s still available for Q1, Q2 and Q3 if you qualify.
Now, let’s hope that the pandemic is behind us and all of you can get booked up for the entire year. But even if that is the case, material, payroll and funding costs need to be monitored closely.
Make a lot of money in 2022!
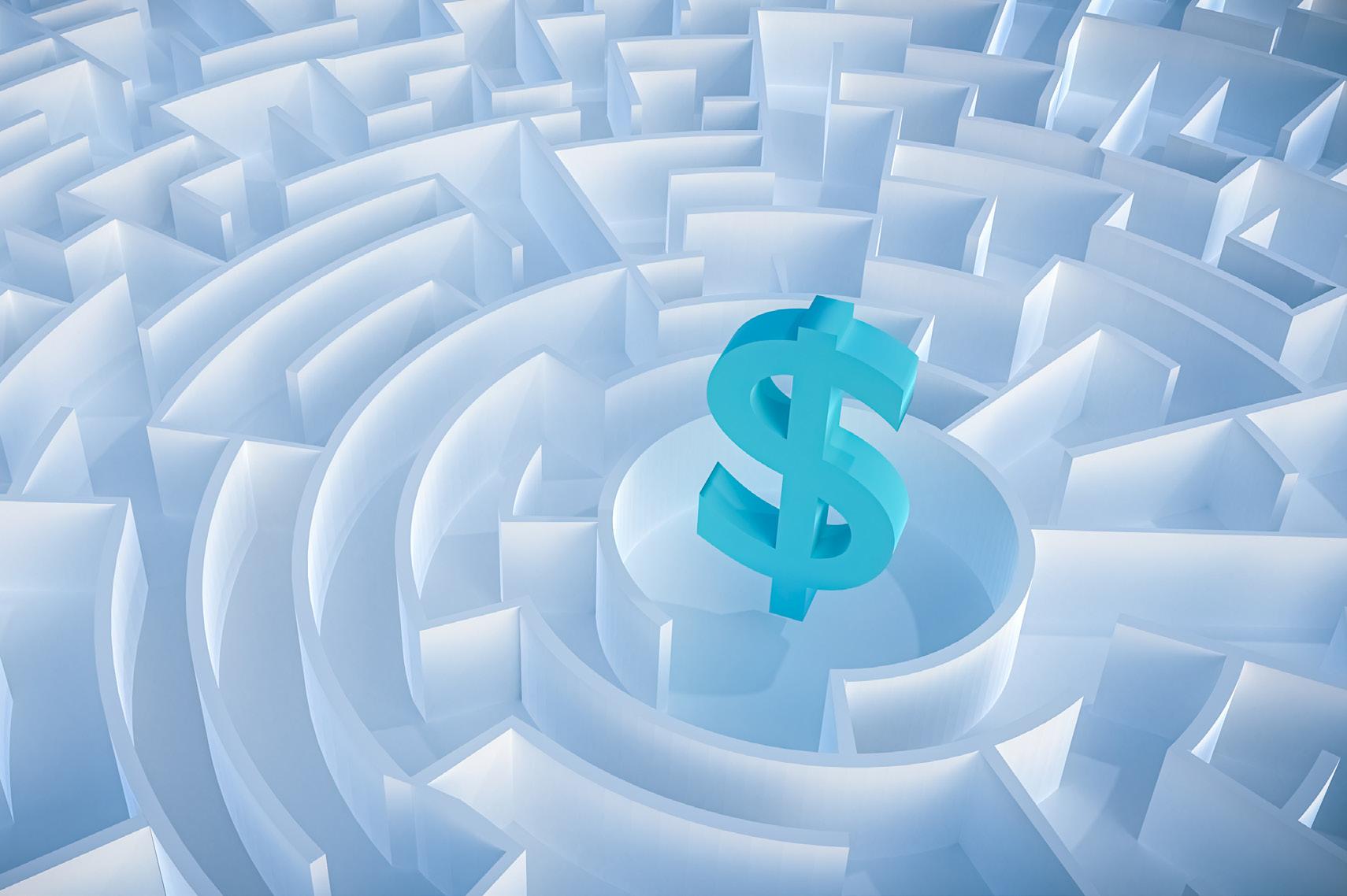
201 N. Main Street, 5th Floor Fort Atkinson, Wisconsin 53538 (800) 538-5544 www.ACBusinessMedia.com
Publication Staff
Publisher SEAN DUNPHY, sdunphy@ACBusinessMedia.com Editor BECKY SCHULTZ, bschultz@ACBusinessMedia.com Senior Field Editor CURT BENNINK, cbennink@ACBusinessMedia.com Contributing Writers GARRY BARTECKI, JESSICA LOMBARDO Art Director DAVE HAGLUND Senior Production Manager CINDY RUSCH Audience Development Manager ANGELA FRANKS Advertising Sales (800) 538-5544
SEAN DUNPHY; NIKKI LAWSON; KRIS FLITCROFT; TADASHI SOMA
ForConstructionPros.com
Editor-in-Chief WAYNE GRAYSON Editor LARRY STEWART
AC Business Media
Chief Executive Officer.............RON SPINK Chief Financial Officer..............JOANN BREUCHEL Chief Digital Officer .................KRIS HEINEMAN Chief Revenue Officer ..............AMY SCHWANDT VP Audience Development........RONDA HUGHES Director, Demand Generation & Education ............................JIM BAGAN Vice President, Operations ......NICK RAETHER Group Content Director............JON MINNICK
Change of Address & Subscriptions
PO Box 3605, Northbrook, IL 60065-3605, Phone: (877) 201-3915 • Fax: (847) 291-4816 circ.EquipmentToday@omeda.com
List Rental
Bart Piccirillo, Sr. Account Manager, Data Axle Phone: (518) 339-4511 bart.piccirillo@data-axle.com
Reprints
Reprints — For reprints and licensing please contact Sean Dunphy at 920-542-1252 sdunphy@acbusinessmedia.com
Published and copyrighted 2022 by AC Business Media Equipment Today makes every effort to report manufacturers’ product news accurately, but is not responsible for validity of news claims. All rights reserved. No part of this publication may be reproduced or transmitted in any form or by any means, electronic or mechanical, including photocopy, recording or any information storage or retrieval system, without written permission from the publisher. SUBSCRIPTION POLICY: Individual subscriptions are available without charge in the U.S. and Canada to management, engineering, supervisory, equipment maintenance and other personnel who have buying influence in the construction equipment industry. Subscribe online at www.ForConstructionPros.com. Publisher reserves the right to reject non-qualified subscribers.
One year subscription to non-qualified individuals: U.S. $50; Canada/Mexico $70; all other countries $100 (payable in U.S. funds, drawn on U.S. bank). Single copies available (prepaid only) $10.00 each (U.S., Canada & Mexico), $15.00 each (International). For change of address or subscription information call (847) 559-7598 or fax (847) 291-4816. Equipment Today (USPS 369-290, ISSN 0891-141X) is published is published 12x with issues of January, February, March, April, May, June, July, August, September, October, November and December by AC Business Media, 201 N. Main Street, 5th Fl., Fort Atkinson, WI 53538. Periodicals postage paid at Fort Atkinson, WI, and additional entry offices. POSTMASTER: Please send change of address to Equipment Today, PO Box 3605, Northbrook, IL 60065-3605. Printed in the USA.
Canada Post PM40612608. Return Undeliverable Canadian Addresses to: Equipment Today, PO Box 25542, London, ON N6C 6B2.
Vol. 58 No. 1 January 2022