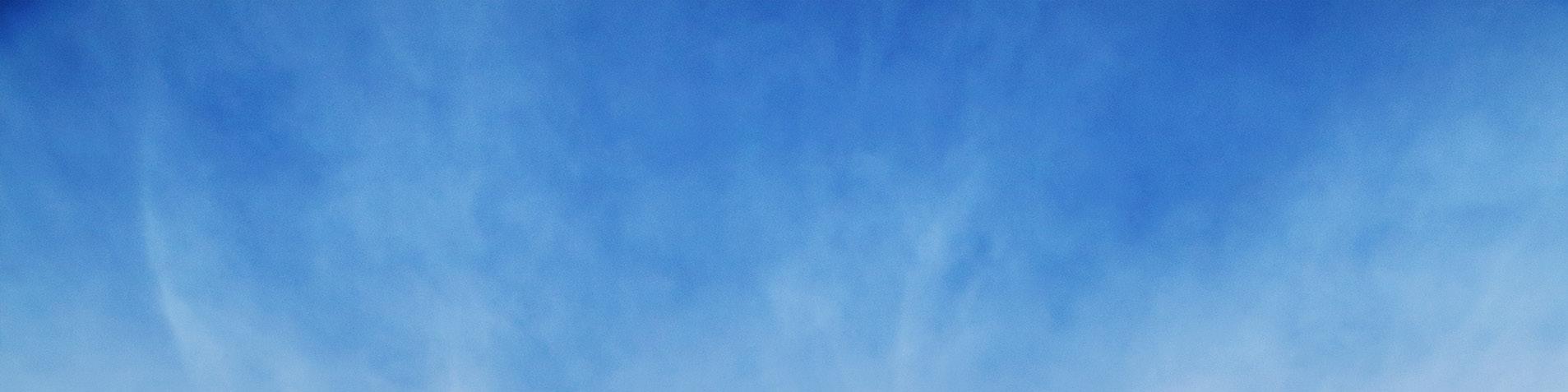
32 minute read
OPERATOR INSPECTIONS DRIVE EQUIPMENT UPTIME
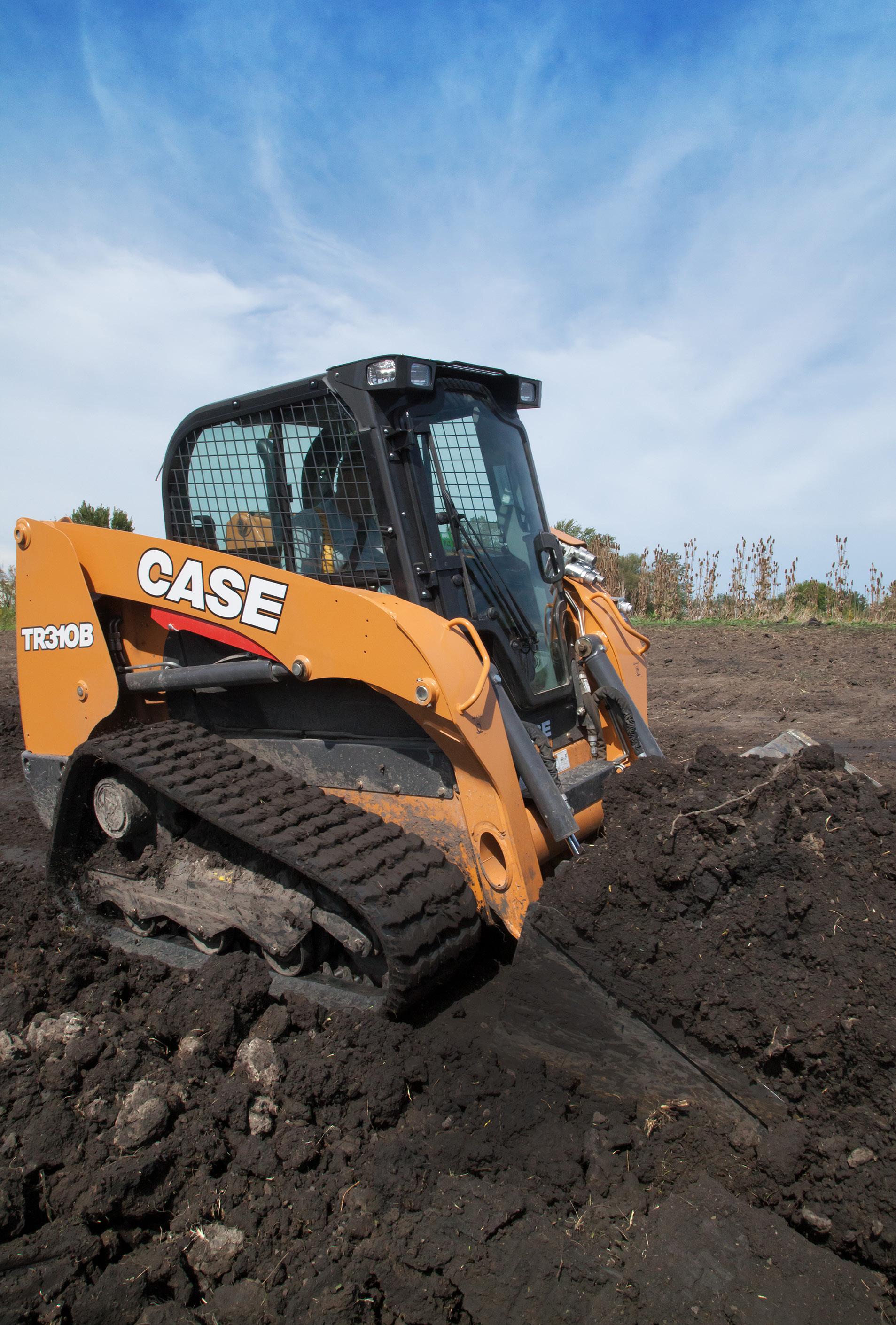
Drive Equipment Uptime
Operators are in the best position to monitor machine health, prevent downtime and maximize efficiency.
RIGHT: Daily service checks are heavily dependent on the type of machine being utilized. Operators need to become familiar with the particular machine they plan to use and develop a routine.
Rubber tires and tracks can easily be damaged during a shift. With compact track loaders, it is important to look for cracks, damage and debris. Also look at rollers and idlers.
The operator plays a critical role in minimizing owning and operating costs. Ted Polzer, director of product and customer support, and Brad Stemper, director of light equipment, Case Construction Equipment, explain how operator inspections can catch potential issues before they become problems, resulting in increased uptime and machine efficiency.
The operator is in the best position to monitor machine health. “He is going to notice the little changes in that machine over time,” says Stemper. The operator can note daily changes, such as if something got damaged yesterday during operation. “Maybe your tracks or tires have a new cut. Maybe there is an oil point that is gathering dust and dirt.”
By developing an inspection routine, the operator’s observations provide critical insight. Let’s take a look at some of the key inspection points.
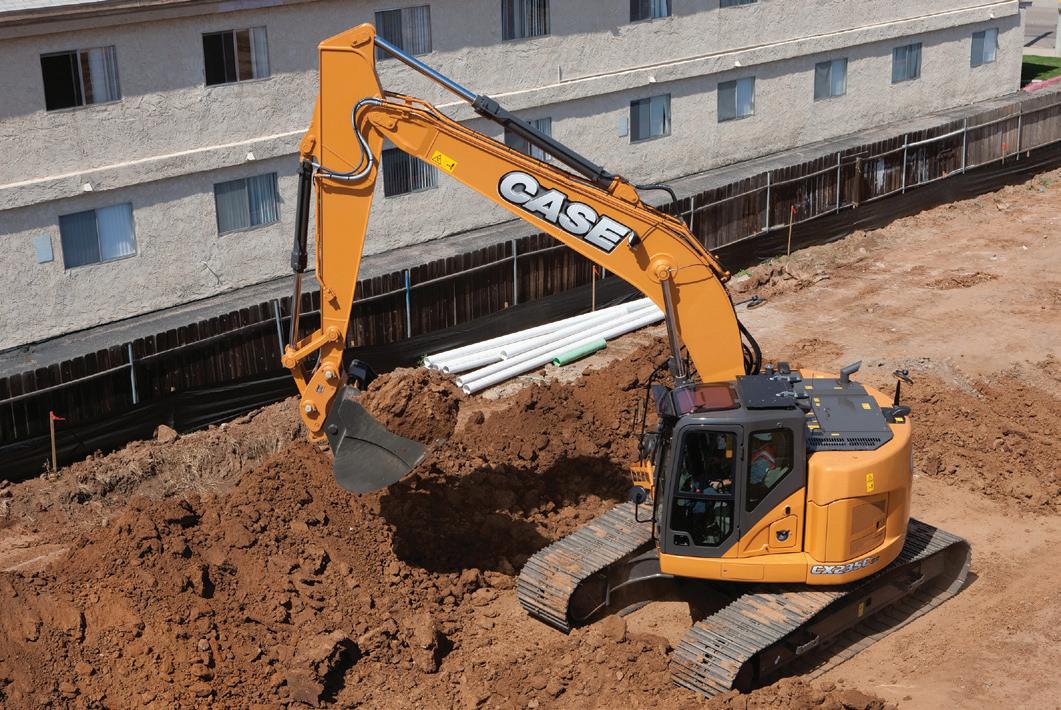
DAILY SERVICE CHECKS
Daily service checks are heavily dependent on the type of machine being utilized. Operators need to become familiar with the particular machine and develop a routine.
For instance, operators need to have a basic understanding of the airflow around the engine compartment and pay attention to ensure debris doesn’t impede airflow around the rear deck or vents.
“You want to keep that radiator cool, and any material that blocks airflow is definitely going to make that machine run hot. You want to be observant of material or debris that might be collecting during your operation day,” says Stemper. “Is it clogging the radiator? There are certain machines that have chaff screens that you want to check.” These make it a little easier to clean out the coolers.
Keep an eye on fluid levels, such as hydraulic or coolant fluids, Stemper advises. Make sure you understand where all of the fluid level checks are located on the particular machine being utilized.
In addition, you need to check filters. “If you do your own maintenance, one of the tips and tricks that I always recommend is mark the date, time and hours that you performed that last filter change so that you know what the life on them is,” says Polzer.
This is important beyond simply tracking hours. “Let’s say you had some dirty fuel that was delivered and may have gotten into a few different machines. At least you know the last time that filter was changed,” says Polzer. It also helps you identify the root cause of the problem, so you are not blindly changing fuel filters that don’t need to be replaced.
Air and fluid filters are not the only concern. “One of the most common areas that is overlooked are cab filters,” Polzer points out. “Engine filters are always the first thing that customers think of and normally those are addressed pretty frequently.” But if it’s a hot day and your AC isn’t performing like it normally does, check to make sure the cab filter is not packed full of debris. While you can blow out the filter to get by, it really isn’t a substitute for replacing the filter with a clean one.
Belts are often out of sight due to protective guards. “It is important to periodically glance [around the guard] to make sure there isn’t debris around the belt. Make sure you don’t have any guard contact with the belt that can cause premature wear,” says Polzer. “Then also inspect the belt itself.” Check for cracks that indicate the belt needs to be changed. “It is cheap insurance to have a spare belt with you on your truck.”
INSPECT TRACKS AND TIRES
Rubber tires and tracks can easily be damaged during a shift. With compact track loaders, it’s important to look for cracks, damage and debris.
“Maybe you have hit something sharp that has stuck through the tread,” says Polzer. “In addition to just the rubber tire and tracks, we also want to be taking a look at rollers and idlers.” But he cautions, “Unless it has an obvious oil leak that is easy to spot, an idler or roller sometimes can be very, very hot, so we recommend that customers don’t actually touch these components after the machine has been running, because it can burn you.”
This is where an affordable temperature gun that is readily available can prove useful. It allows you to identify hot spots, and some of these devices even provide thermal imaging. “We can clearly point out a roller that is extremely hot that needs attention,” says Polzer.
Tires present their own unique set of challenges. “Tire pressure is extremely important with your machines. Underinflated tires can create excessive heat that can lead to shorter life,” Polzer explains. This can prematurely wear the tire tread. “It is extremely important to monitor that every day... You can either do that through the use of an air pressure gauge or you can do a visual on them if you know they’ve been set properly to that jobsite when you first got started.”
MAINTAIN GREASE POINTS
Grease provides the protection necessary to prevent excessive wear and failure between moving components. Uptime is dependent upon grease getting to the proper location and in the proper amount.
“The first thing that any operator should do is open up the operator’s manual and familiarize themselves with the grease points and the frequency for those,” says Stemper. “Some grease points are daily; some are not as frequent.”
The amount of grease is also important. “It’s not simply connecting that grease gun to that point. It’s the appropriate number of grease fill pumps. Not all grease points require you to pump until something comes out of that grease spot,” Stemper elaborates.
Check documentation to make sure critical joints are not missed. “There are often diagrams on the machine and inside the operator’s manual with the grease points and how much those grease points take,” says Stemper.
Make sure not to miss less visible grease points. “Operators can sometimes bypass certain points that might be higher up on the machine if there are not remote grease zerks,” says Stemper.
In joints such as bucket pins that are often operated underground or in wet or underwater conditions, grease helps purge the contaminants and provides a new fluid film for rotating components.
“Making sure you are greasing [all of these] areas is going to make the machine more efficient,” Stemper comments. It also provides a good opportunity to check highly vulnerable areas of the machine for damage such as bulging hoses and dinged or nicked cylinders.
Tire pressure is extremely important. Under-inflated tires can create excessive heat that can lead to shorter life. IDENTIFY LEAKS
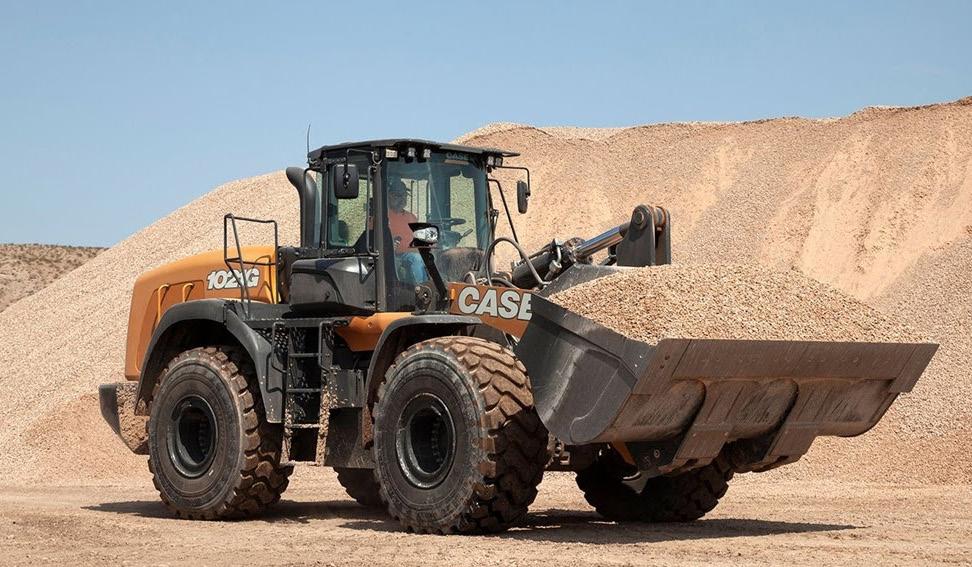
By nature, construction equipment often works in dirty environments, which can make it more of a challenge to identify leaks. “In the morning [after] the machine has been sitting, oftentimes gravity is going to be our friend. If you have a leak, we’re going to start to see that along rollers and seals,” says Polzer. “But primarily one of the things we really try to monitor and pay attention to is looking for accumulations of dirt in certain areas. Any time we have a fitting that is leaking, we start to get oil residue and oil residue attracts dirt, especially in dusty environments.”
Areas where dust and dirt accumulate are clues to potential leaks. “Look up into the [hydraulic cylinder] rod and the gland seal a little bit to see if there is an accumulation of dust and debris,” Polzer advises. “That indication can save you a lot of time and money because we are not yet at a point of failure. We can approach the dealer and say there is a leak that needs to be addressed.” Maybe it is just a loose fitting that needs to be tightened.
A lot of newer machines come with UV reactive dye in the oil. An inexpensive UV flashlight can make the oil glow, which makes leaks easy to find, even in very hard to access areas. For those machines that don’t have UV reactive dye in the oil, it is relatively inexpensive to add it, says Polzer.
Auxiliary hydraulics are another area that require operator diligence. “If you are operating auxiliary hydraulics, it is an absolutely vital spot to pay attention to,” says Stemper. “The best thing to do if you are changing attachments is to carry a rag with you. Leave it in the machine. Make sure it’s a clean rag; the worst thing to do is clean something with a dirty rag. Before you connect those [hydraulic couplings], make sure those ports are clean. You don’t want to introduce any dirt on the hydraulic hose connection or on the machine connection by shoving it in without cleaning it.”
There are other steps you can take to keep attachment connections clean. “When you disconnect the hydraulic hoses on an attachment, don’t hesitate to connect the two halves together,” says Stemper. “That creates a circuit that allows the entire attachment to be protected. It keeps fittings out of the dirt so you have less dirt to clean up. It also allows the pressure to equalize in both lines.”
MONITOR CUTTING EDGES
Teeth and cutting edges provide the ability for a machine to complete the task efficiently. Using teeth and cutting edges that are worn down will result in a loss of fuel efficiency. If the machine is working inefficiently, there is also likely more heat buildup.
“It is important to observe how teeth are wearing,” says Stemper. “Do you have the right teeth on your machine for the application? Some teeth are better designed for harder materials, some are better designed for softer materials. It’s really important to investigate whether you are using the right teeth and the right cutting edge for your application.
“In the end, putting the right tooth on and using it within its normal useful life range gives you that efficiency in operation,” he continues. “You’re going to be more productive in filling the bucket, filling the material, loading the material into a truck by having those newer teeth or sharper edges.”
THE STARTUP
After the operator inspects the machine in the morning, it is good to develop a startup procedure.
“It is a good practice to be able to start a machine and let it warm up a little bit by simply idling,” says Polzer. “Obviously, idling too long is a bad thing. What I like to do is start the machine up and let the machine
go through all of its self checks. As it’s warming up, I validate my lights are working. Then as that machine has been warming up, I look back at the display and make sure we don’t have any warnings on the dash.” Communication is vital. “If you have multiple shifts that are operating, make sure that you have a process for each shift to be able to communicate if there’s anything that has been noticed or going on with that unit,” says Polzer. “Maybe there was an intermittent fault code that had popped up last night, but because it wasn’t on when the operator shut it off, he didn’t alert anybody. That could be really important because that might be leading up to a bigger downtime scenario.” ET
FIND MORE ONLINE
Prevent Premature Dozer Undercarriage Wear - www.ForConstructionPros.com/12118319 Track Chain Tension is Your Key to Cutting Undercarriage Costs - www.ForConstructionPros.com/21001484 How Undercarriage Design Impacts Compact Track Loader Productivity and Performance - www.ForConstructionPros.com/21087402 Inspections and Proper Maintenance Give Dozer Uptime a Push - www.ForConstructionPros.com/20989229
John Deere Anti-vibration Undercarriage System
An anti-vibration undercarriage system is now available on zig-zag bar tracks on the John Deere 333G compact track loaders.
•Includes an isolated undercarriage, bogie rollers, updated grease points, hydrostatic hose protection shield and rubber isolators •Provides a smoother ride for the operator and enables machine to travel at higher speeds while retaining material •Bogie roller system allows for oscillating movement of rollers •Oscillating bogie arm includes only four easy to access grease points •Angled steel shield protects hydrostatic hoses from exposure to debris www.forconstructionpros.com/21614822
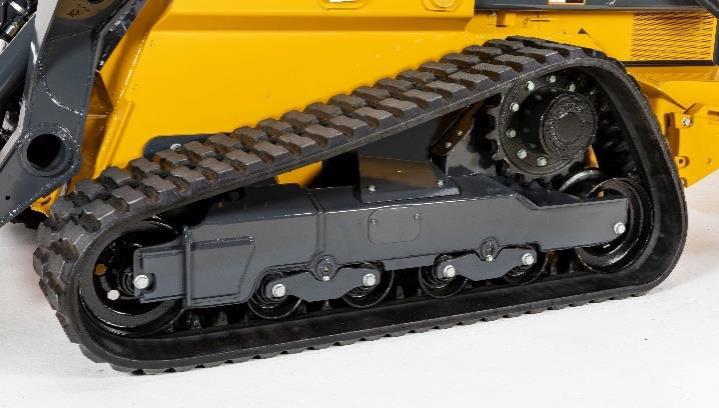
American Eagle Multi-Tank Fuel Trailer
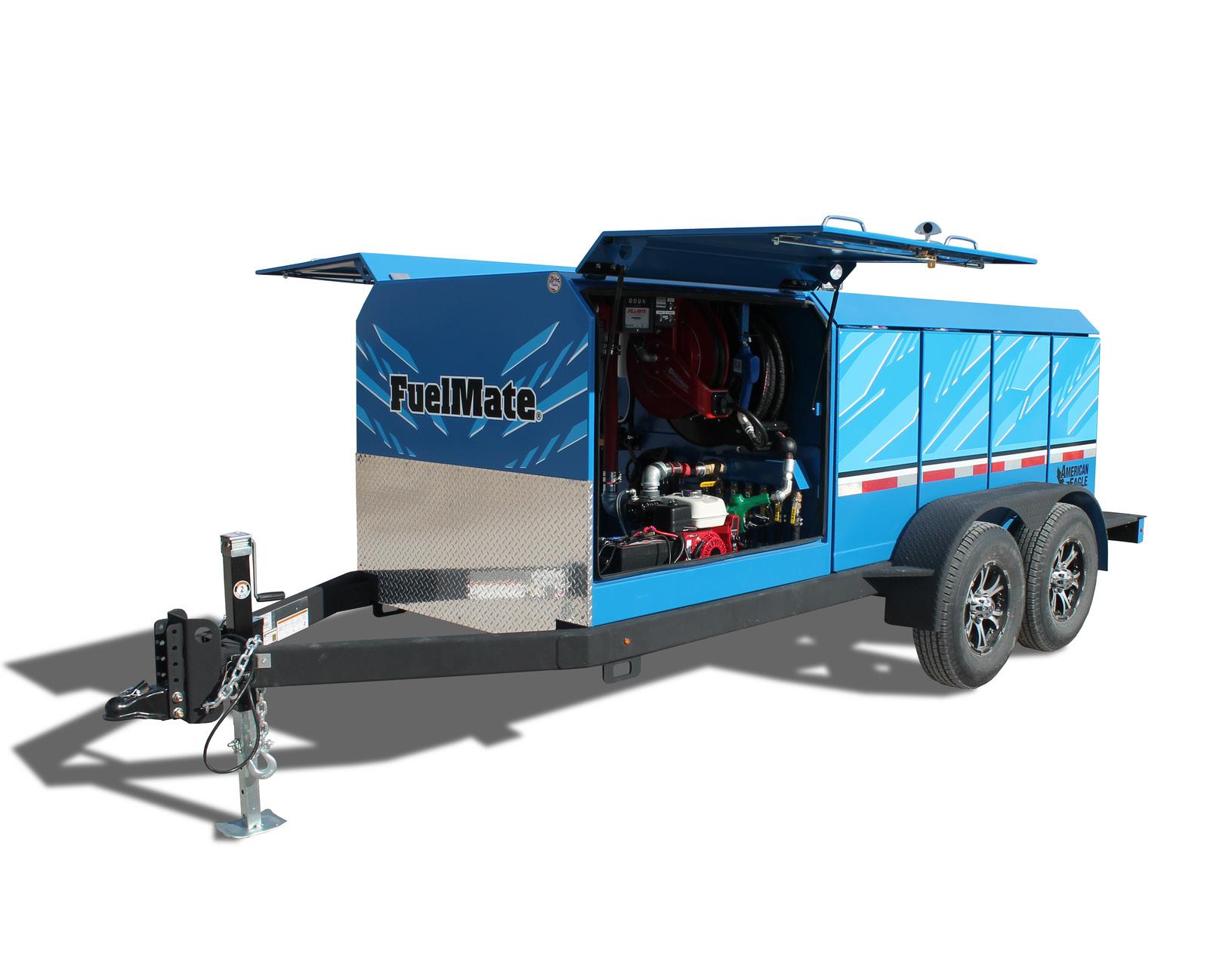
The Multi-Tank Fuel Trailer enables contractors to haul diesel fuel without the need for CDL hazmat certification.
•Equipped with seven 110-gal. internally baffled fuel tanks with sight gauge, vented cap and tank breather •Features one 110-gal. stainless steel DEF tank, work lighting and a drawer system •Spacious, ergonomically useful 54-in. cabinet with two gullwing doors •Tube framing stronger than channel iron •Durable, easy to replace spring leaf •Primer powder coat for enhanced salt spray performance, durability and a premium finish www.forconstructionpros.com/21197776
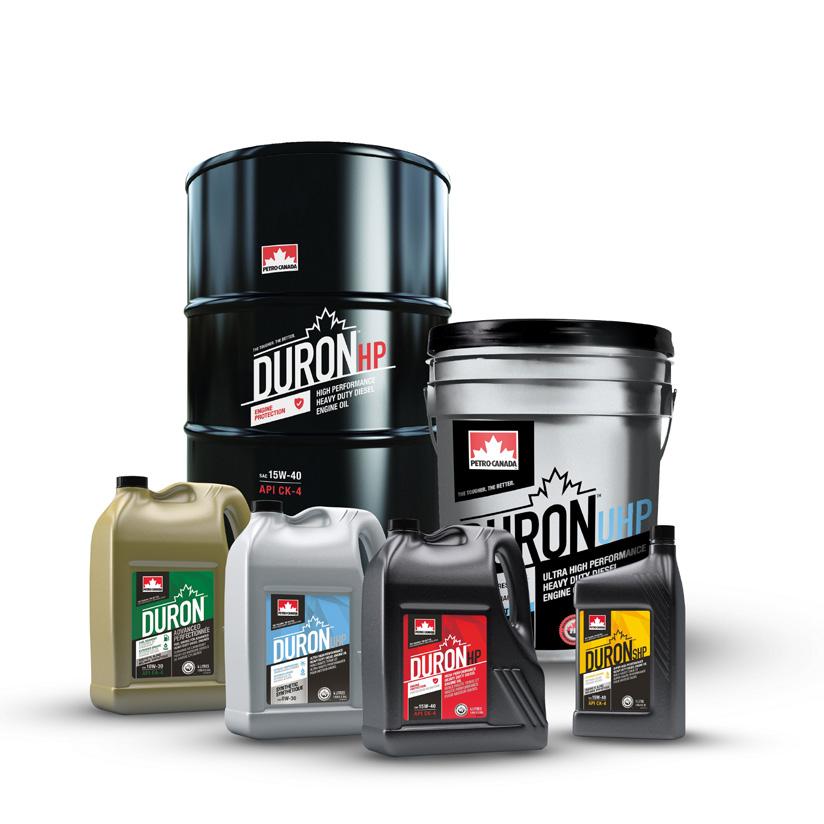
Chevron Delo 600 ADF with OMNIMAX
Delo 600 ADF with OMNIMAX is a heavy-duty engine oil formulated to 0.4% sulfated ash to significantly reduce the rate of DPF clogging and extend DPF service life by up to 2.5 times.
•Enables a 3% fuel economy retention advantage over the life of the equipment •Meets or exceeds API CK-4 and OEM specifications and has demonstrated optimal oxidation stability for the potential to extend engine oil drain intervals •Delivers enhanced valve train wear protection and piston deposit performance •Available in Delo 600 ADF 15W-40 and Delo 600 ADF 10W-30 www.forconstructionpros.com/21127785
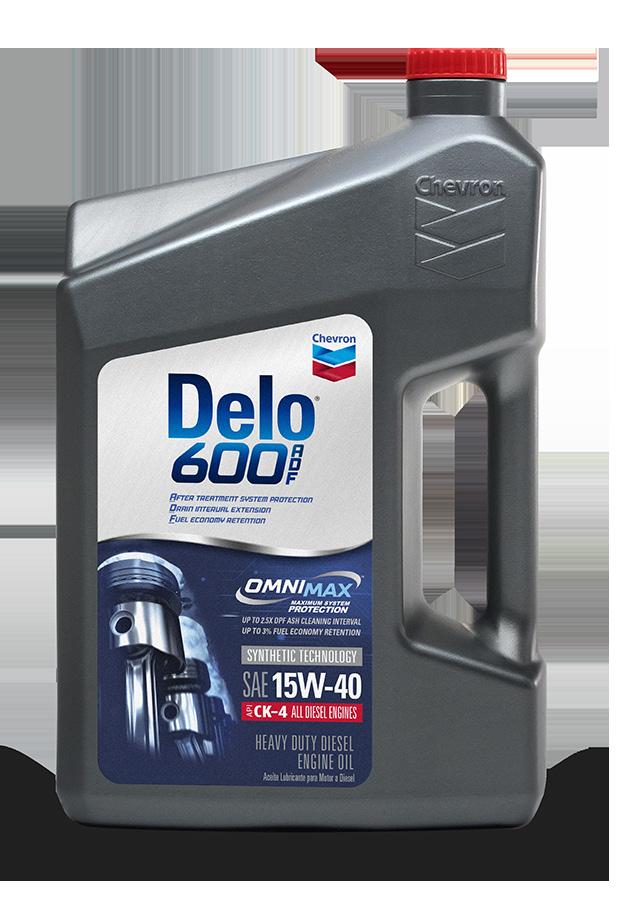
BKT RIDEMAX FL 699 Tire Range
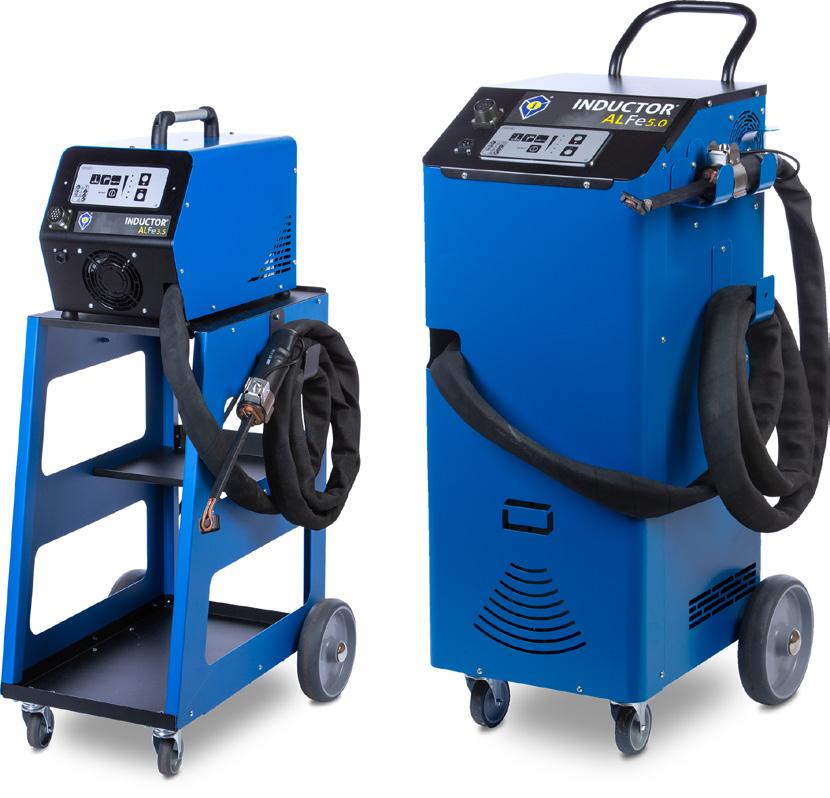
The RIDEMAX FL 699 is available in 24 R 20.5 and a new 525/65 R 20.5 size designed for transport operations with tractors and trailers in industrial and agricultural applications.
•Developed to be stable at high speeds, support heavy loads and reduce rolling resistance •All-steel structure withstands a high load capacity, decreasing the number of transport cycles •Reinforced bead ensures stability even at high speeds and a comfortable ride for safety and control www.forconstructionpros.com/21497147
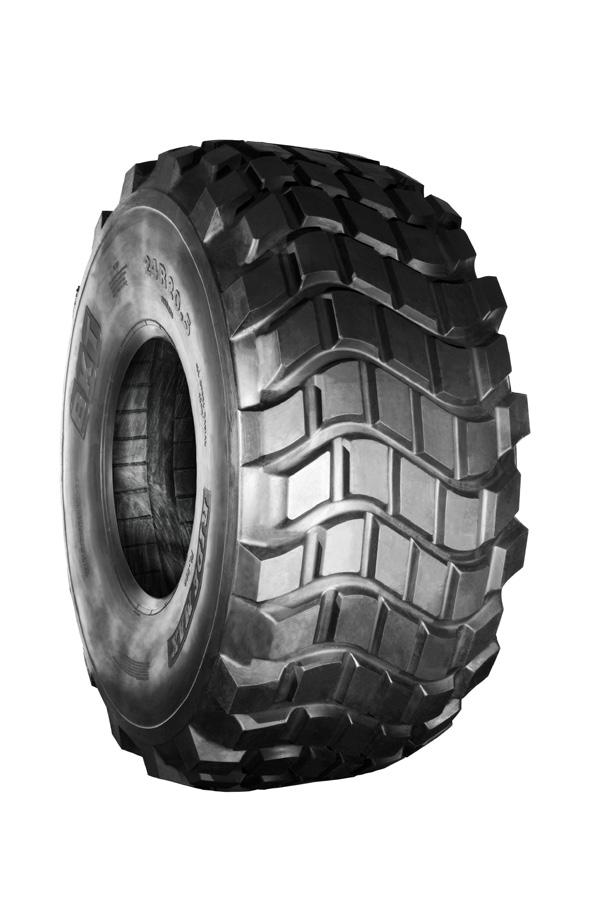
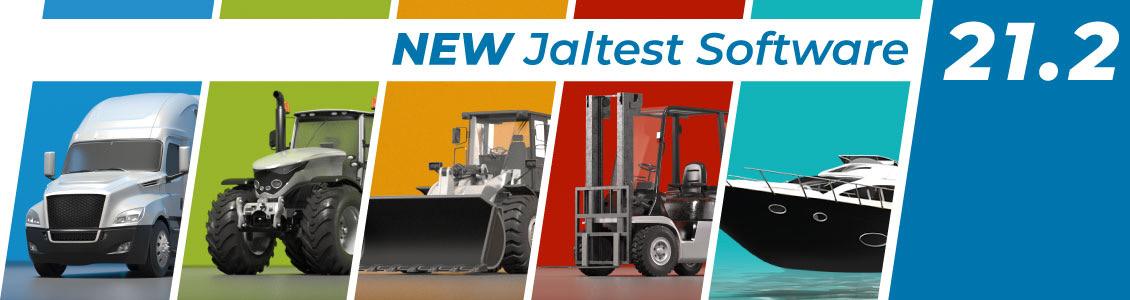
Cojali Jaltest 21.2 Aftermarket Diagnostics Tool
Jaltest 21.2 extends the tool’s coverage and actions on material-handling equipment (MHE), packaging it in a distinct module called Jaltest MHE.
•Covers forklifts, boom lifts, scissor lifts, telescopic handlers, etc. •Available wiring diagrams now include full vehicle wiring with no need to exit diagnostics software •Page index and component search box enables technician to identify cables by color and find parts reference within the same diagnostics screen •Approved compatible tool for the FCA (Fiat Chrysler Automobiles) Secure GateWay for in-app access to FCA-protected vehicles equipped with this SGW module, such as new Ram trucks www.forconstructionpros.com/21533504
Petro-Canada Duron Heavy-duty Engine Oils
DURON heavy-duty diesel engine oils are suited for the toughest conditions and can take vehicles farther between oil drains.
•Meet the category demands of API CK-4 and FA-4 •Extreme durability means drain intervals can be stretched with no compromise on reliability or engine protection •Include high-performance, super highperformance, synthetic and other blends •Capable of extreme temperature performance www.forconstructionpros.com/21772171
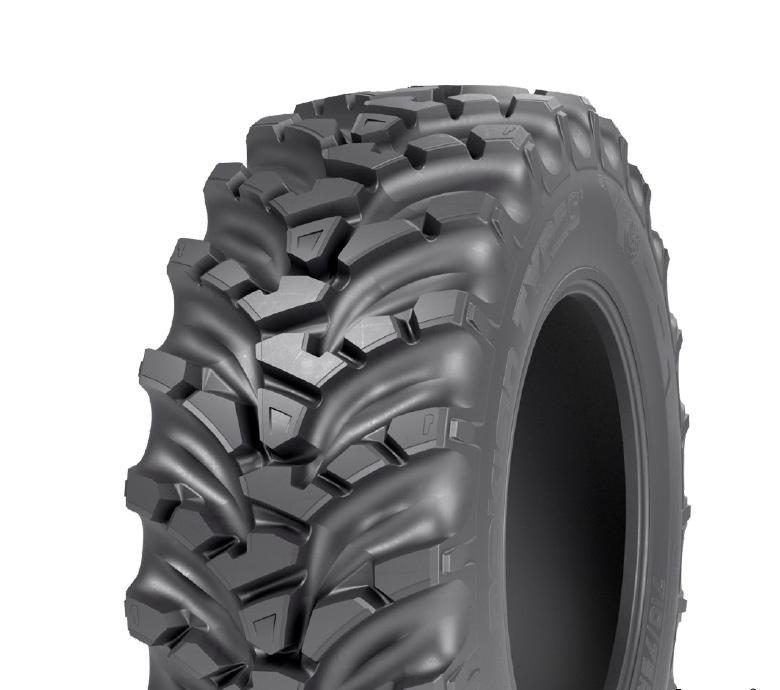
Nokian Ground King Tire
The Ground King tire includes the Hybrilug technology, which combines features of lug and block patterns for allterrain mobility and traction combined with a high level of comfort and precise handling response on the road.
•Incorporates specially aligned pattern elements and more tread compound •High-grade, wear-resistant tread compound offers extended ground contact area to enable more operating hours even in extensive on-road use •High load bearing capacity enables use of heavy work implements and high loads •Self-cleaning abilities www.forconstructionpros.com/21085389
Induction Innovations Inductor ALFe Induction Heaters
ALFe 3.5 and ALFe 5.0 induction heaters are capable of heating aluminum and steel to help release seized parts and panel bond adhesives.
•230V/16A/P1 (ALFe 3.5) or 208V/20A/P3 (ALFe 5.0) •ALFe 3.5 offers a 9-minute duty cycle, while the ALFe 5.0 has a 30-minute duty cycle •LED light indicator •Safety shutoff www.forconstructionpros.com/21108959
You no longer need to make a phone call to reserve equipment from a rental equipment provider. You can now do it 24/7 via a desktop or mobile app. An equipment management system can allow users to share costs across multiple purchase orders.
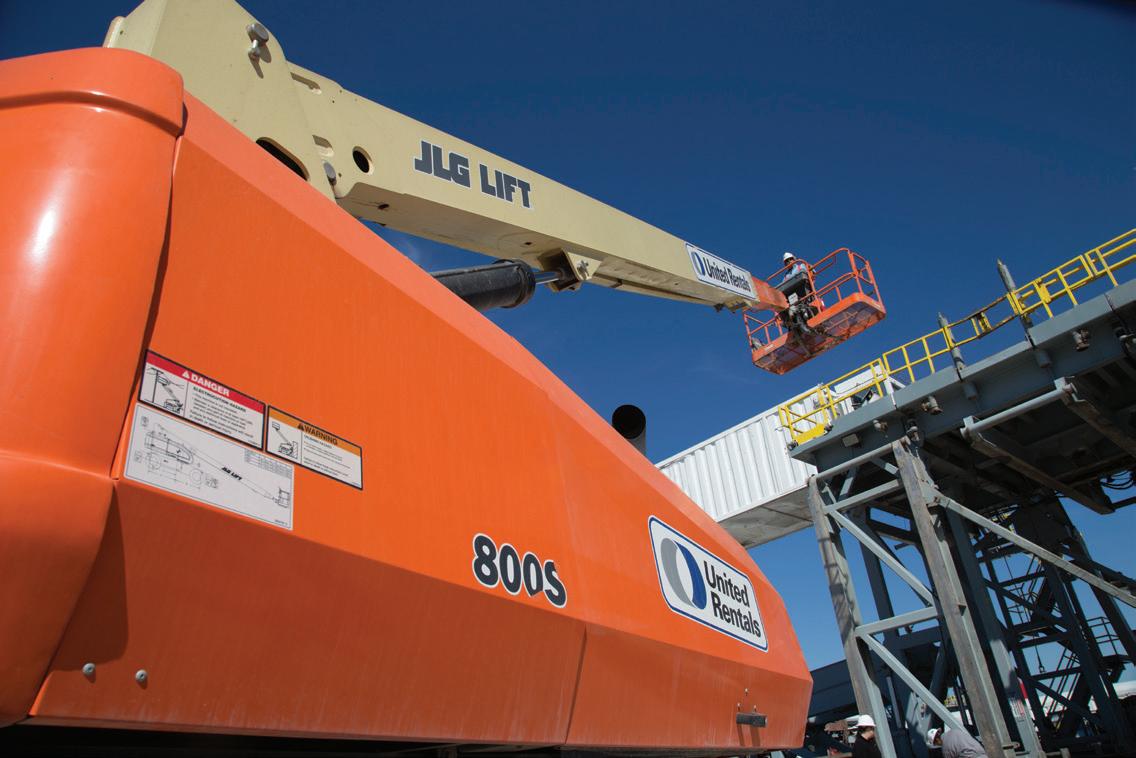
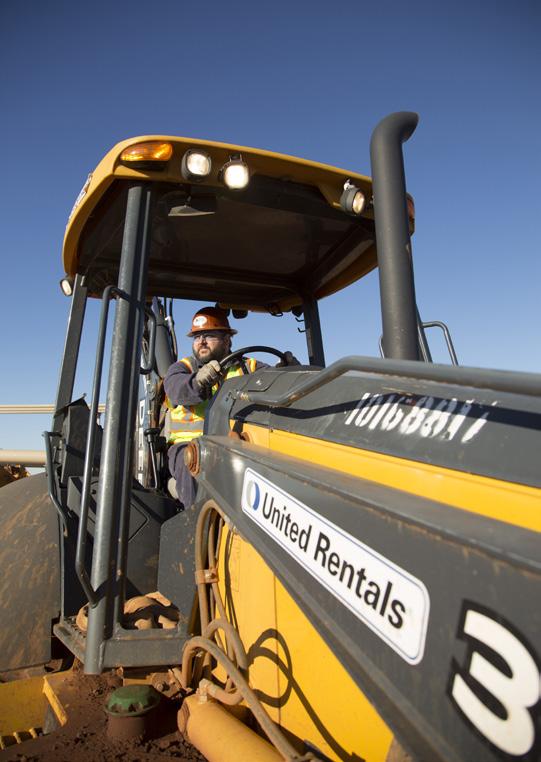
Digital tools can help manage rented and owned fleet all in one place in ways that save time and money.

HARNESS DIGITAL TECHNOLOGY to Manage Rented and Owned Equipment
Digital solutions can help you better manage construction equipment and improve worksite productivity.
Whether you need to rent or return equipment, locate equipment or monitor utilization, digital tools put action and information at your fingertips. Digital technology — including telematics, online self-service tools and fleet management solutions — allow construction teams to find what they need and do what they need, no matter where they are or what device or tool is being used.
Such solutions can help contractors of all sizes to better manage complex projects and address under utilization of equipment such as excavators, loaders, aerial work platforms and more.
“In today’s world, harnessing the power of digital technology to manage construction equipment just makes sense,” says Ty Campbell, director - sales, Managed Services, United Rentals. “There is plenty to worry about on the jobsite and digital tools should be an important part of managing complexity. This approach can help contractors streamline processes, save time and gain greater control so they can deliver better results and have fewer safety incidents. Crews can find and order needed equipment and manage rented and owned assets exactly when and how they want, without wasting a moment and with just a few clicks.”
Here are some ways you can tap digital solutions to manage construction equipment to create more productive worksites and more efficient, profitable companies.
FIND, RENT AND RETURN EQUIPMENT
Construction companies no longer need to make a phone call to reserve equipment from a rental equipment provider. You can now do it 24/7 at your convenience via a desktop or mobile app with a seamless experience, whether you order one forklift twice a year or 100 boom lifts for a single project.
With a few clicks, construction teams can find needed equipment and order and offrent equipment. They can also request a pick-up, track equipment deliveries, adjust rental dates, access leniency windows to reduce rental costs and see the location of all telematics-enabled equipment and assets.
If a maintenance issue arises, you can request service directly from a mobile app and even upload photos to help diagnose the issue. Digital tools are expected to keep evolving, adding capabilities such as saving favorites and providing equipment recommendations based on the type of work being done.
These tools also open the door to alerts that can help manage equipment rentals more easily and effectively. For example, you can receive alerts via email or text message when equipment is due back and potentially save thousands of dollars in late returns.
MANAGE RENTED AND OWNED FLEET
in one place in ways that save time and money. For instance, they can arm you against the significant problem of under utilization.
The longer an asset or piece of equipment sits idle, the more it costs your company, whether it is owned or rented. Many companies don’t regularly track utilization and aren’t aware how much under utilization is costing them. But utilization is easy to track in a fleet management application through desktop or mobile access.
Running utilization reports and leveraging real-time low utilization alerts are smart ways for you to meet your utilization goals and beat industry benchmarks. Some contractors have seen annual rental costs cut by a third by improving utilization.
Another potential money saver is an equipment management system. This type of system can facilitate equipment sharing by letting users share equipment costs across multiple purchase orders.
You can also upload owned equipment to a rental provider’s fleet management solution to take advantage of fleet maintenance tools. These tools include viewing preventive maintenance history and current maintenance status of every piece of equipment, seeing fault codes and managing work orders. Contractors can receive alerts when preventive maintenance is overdue.
“With the right digital tools in the toolbox, it is possible to work smarter and accomplish more in less time with fewer resources. Best-in-class rental platforms accessible by desktop and mobile are making it faster and easier to find, choose, rent and off-rent equipment,” says Campbell.
“Rental providers that offer a digital fleet management solution give contractors even more power, providing visibility into both rented and owned equipment,” he adds. “That visibility can help companies save money by helping boost utilization, eliminate hoarding and reduce duplication.” ET
Article provided by United Rentals, which offers the Total Control cloud-based worksite management solution as well as the United Rentals Mobile App.
IN-LINE FINANCIAL TOOLS Upgrade Contractor’s Forecasting Accuracy
All images courtesy Kitchell
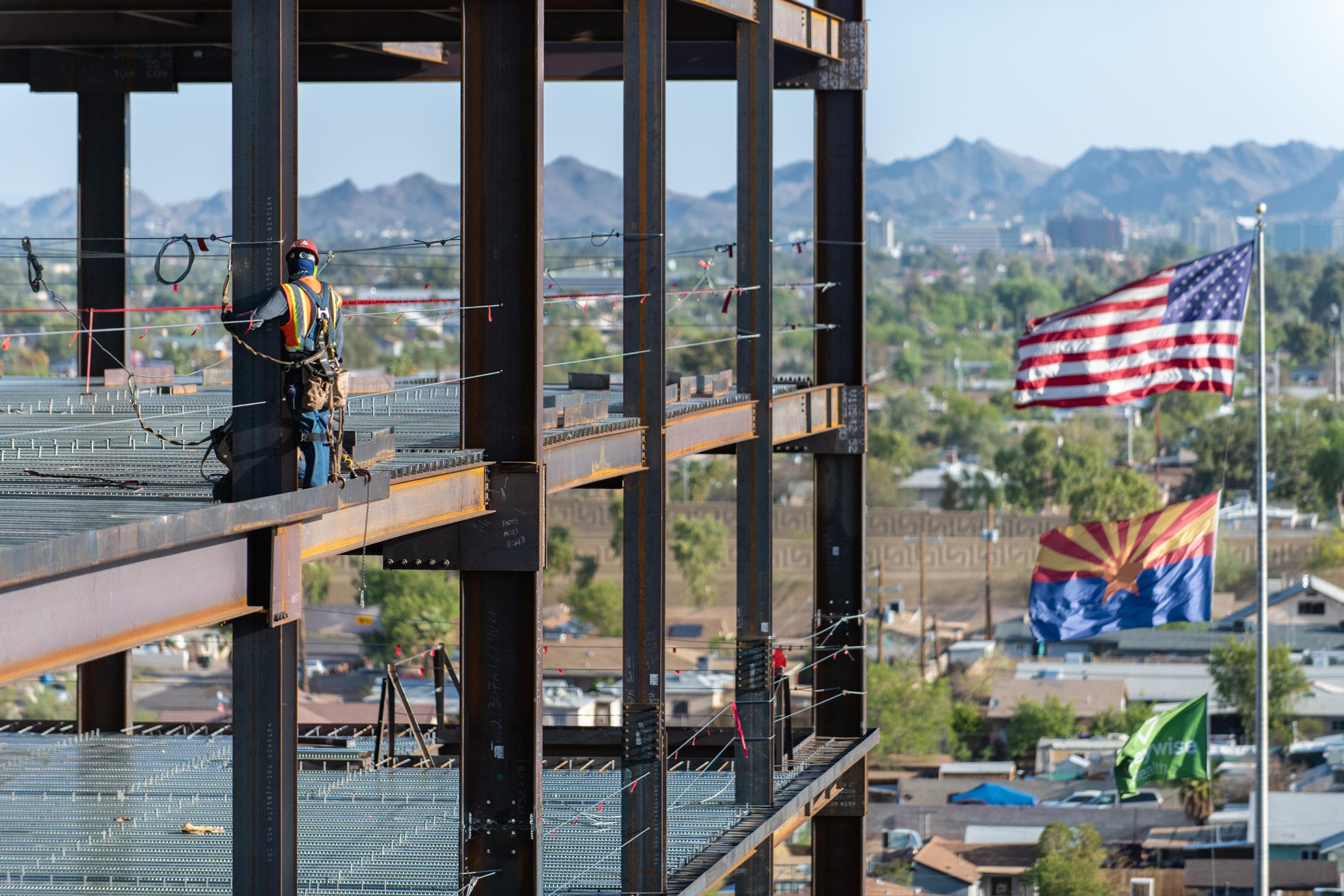
Kitchell’s modeling with safety data has proven that artificial intelligence can predict risk with an accuracy that the company will also apply to construction project financial performance.
To move from reactive to proactive management, Arizona-based commercial general contractor Kitchell invested in Procore’s cloud project management software in 2018. The firm normally works 30 to 50 building projects across the western U.S. ranging in size up to $600 million — more than half of which are complex healthcare and higher education projects — and it wanted to use the terabytes of data each throws off to predict project safety and quality.
Carl McFarland, market sector executive at Kitchell’s Technology & Venture Development group, says Procore’s promise of a coming financial management application was also particularly exciting because the contractor wanted to drive toward more consistent and accurate financial forecasts.
“It was incredible how much time and resources we spent doing forecasts on spreadsheets,” McFarland says. “We had 12 or 15 different versions [of the spreadsheets] across the organization that project managers used. Each month, if you were a project director and you had six project managers, you would have to look at six forecasts in six different formats. There was a lot of inconsistency.”
FORECASTS IN LINE WITH PROJECT MANAGEMENT
The new Procore financial package that emerged, called Monitored Resources, draws on consistent project management data. It brings a uniform level of detail, presented in a uniform format, to financial forecasts that dramatically improves the accuracy of the projections driving Kitchell’s business tactics.
“We’re starting to make our way into advanced forecasting that is really going to help us with projecting future cash flow and is starting to dial in some of our projected revenues,” says McFarland. “That’s a big deal at the senior executive level, where they’re saying, ‘Okay, how much work are we going to put in place? And what do those projected revenues look like?’
“Right now, the project teams are using spreadsheets to forecast those revenues based on the work in place to date, and then taking that information and projecting that out,” he adds.
Procore’s Monitored Resources can improve the accuracy of forecasts by taking into account the current pace and scheduled phases of the project during the forecast period. “Procore is giving us a tool that gives us options for what the distribution curve looks like,” says McFarland. “Those costs are going to be spread out over time in a different way — they’re not just linear. Even if they’re not down to a level of exact precision, the forecast is far more accurate than some of the guesstimating that’s been done with spreadsheets.”
McFarland points to the value of forecast accuracy for both Kitchell and its clients: “Let’s say we’ve just signed a $15 million contract. In the past, we would have to take that schedule of values, put it into a spreadsheet and approximate what we think the billing curve would look like over the 18 to 24 months of the project. With advanced forecasting, we can project that billing curve on a line-item basis, and come to an
even more accurate prediction of the billing the owner can expect to get over time.”
BETTER TACTICAL FORECASTS UNLOCK PREDICTIVE ANALYTICS
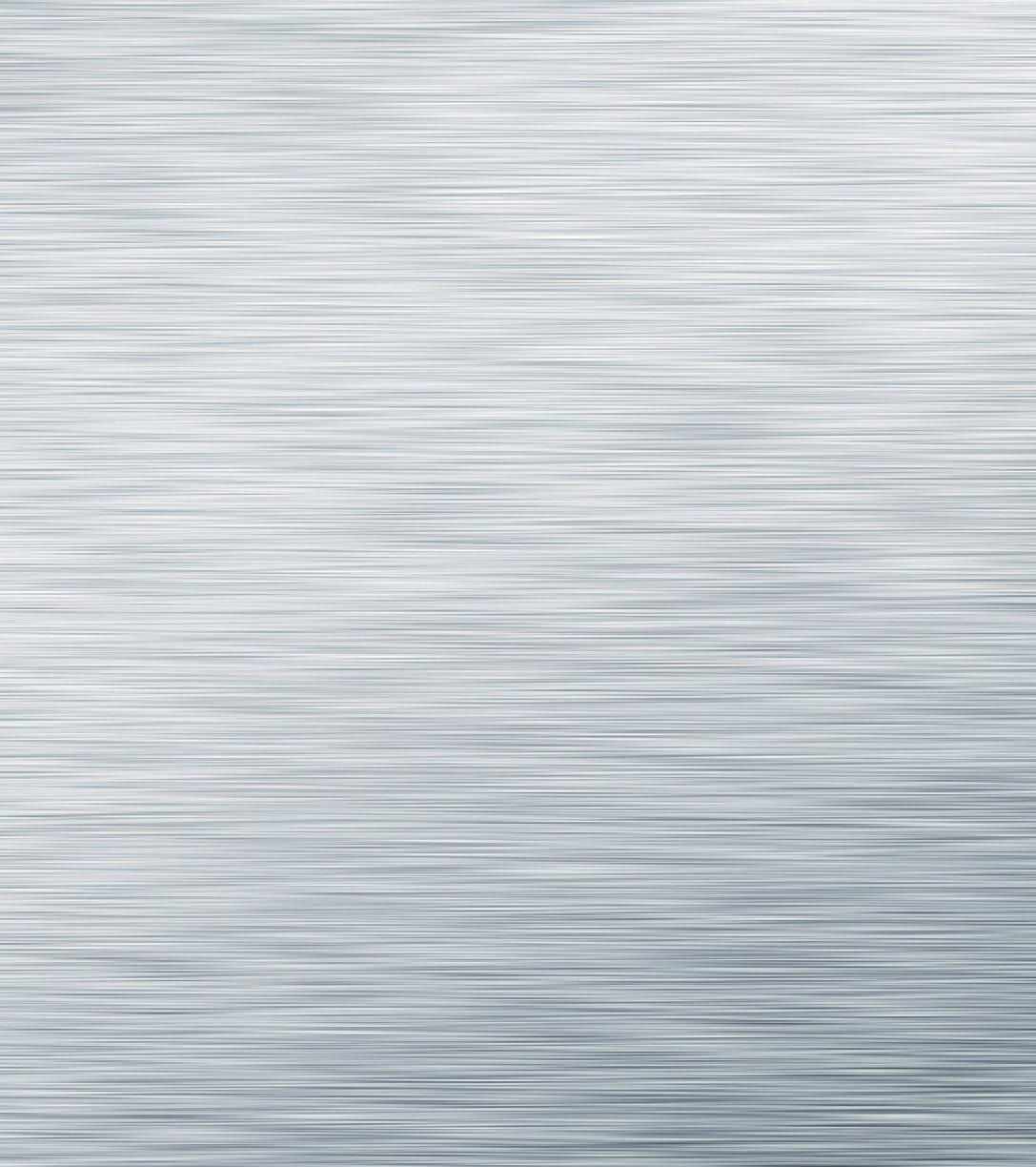
Improved forecasting is pushing a paradigm shift Kitchell is engineering on a much larger scale. McFarland’s operations technologies group keeps in mind an axiom that transparency and consistency promote accountability. And, ultimately, that should lead to accuracy and certainty.
“We’ve seen that in some other areas of the business. That’s really what we’re seeing across the board as we continue to build those forecasting processes that were once done offline into a more structured and formal process right in our budgets.”
Consistently structured financial data in a cloud database offers Kitchell an opportunity to do some 21st Century numbers crunching with potentially huge payoffs.
“We’re layering this structured data with some outside resources that are starting to use predictive analytics to look at huge data sets and learn things that the individual data streams will never say. For example: If you’re X percent through the project with a contingency spend on Y, there is a X percent probability that you’re going to experience fee erosion,” McFarland explains.
“We’re seeing that with safety. We’re finally in the predictive side of safety. I’ve seen some modeling of our data there and it has validated that it does work,” he says. “It’s not going to replace our decision making; it’s simply going to enhance our ability to make smarter decisions.
“That’s why we think it’s important we continue to adopt these new tools — because it will provide us with more structure around our data. And the more organized, clean and accurate the data is, the better position we’re in to be able to predict and leverage it,” he adds.
McFarland believes forecasting certainty is more important than ever for construction firms, especially in the area of financials. “We are faced with having to invest dollars in areas we’ve never had to invest in before. We’re having to invest in technology research and development,” he comments. “Better accuracy should ultimately produce better income results — happier customers — and therefore should produce more free cash flow to invest in the tools necessary to advance the business and better serve our clients.”
McFarland connects the value these tasklevel tools offer with helping make macro changes at the company and even the industry level. “When you can say with certainty, ‘We’re projecting our revenue +/- 1% or +/- 5%, it can free up a certain amount of cash flow to reinvest. As a business, that will advance the company, and that has tremendous value right now — more value than it did even 10 years ago, in my opinion,” he states.
Kitchell, for example, has invested in off-site prefabrication of building components. “It takes less resources, less labor, so it’s helping solve the labor issue. It’s safer, putting fewer people in fall or other types of hazards. Quality is better because you’re indoors, you’re not exposed to climate issues. And technologies are improving visibility to the supply chain,” says McFarland. “I would say online shopping is to retail what off-site prefabrication will be to the construction industry.”
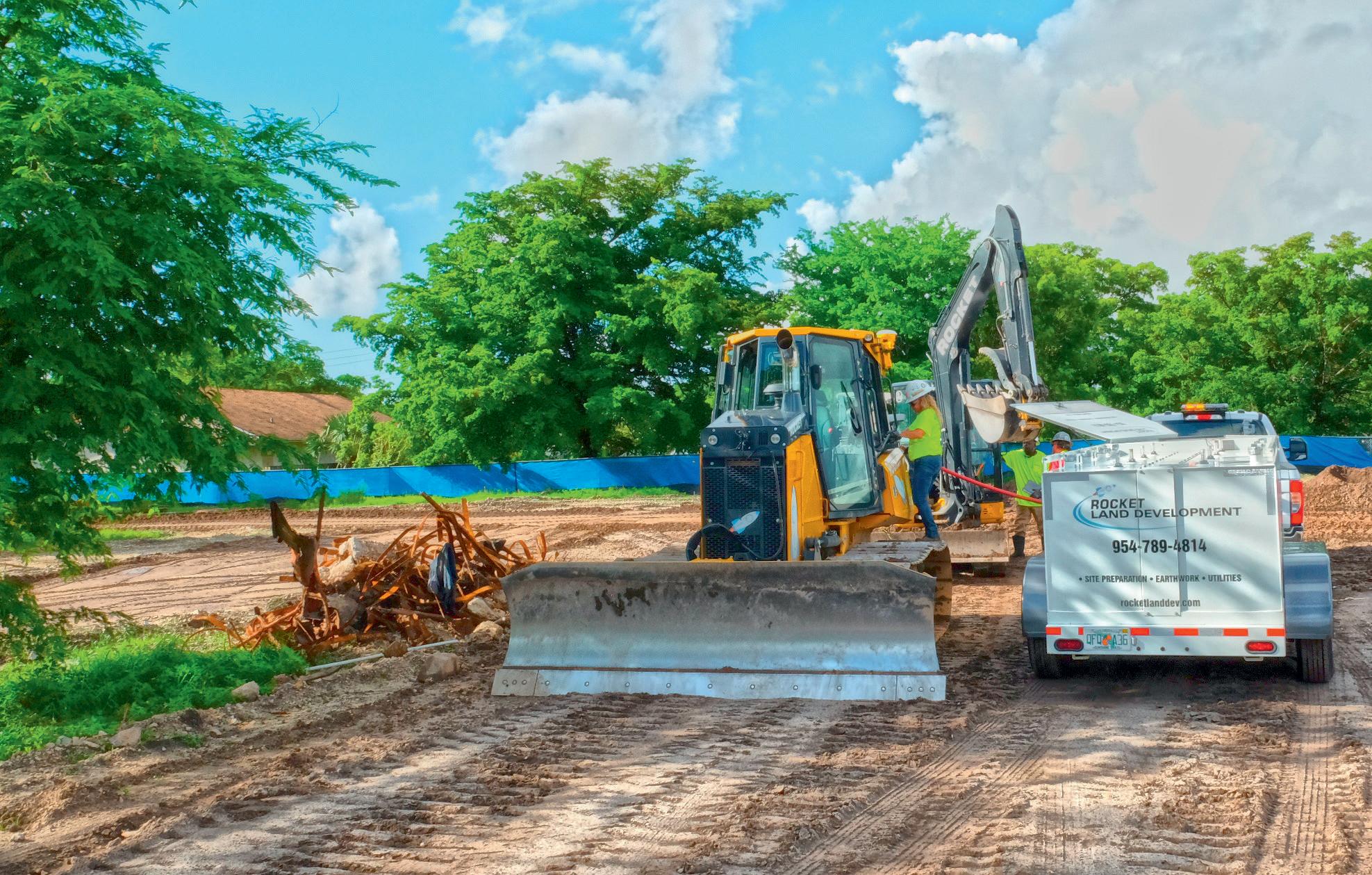
FROM PROJECTIONS TO PARADIGM SHIFT
“General contractors, trade contractors, suppliers — we’re all going to need a better understanding of our overall financial performance to figure out how we’re going to adapt to all of these changes coming to the industry,” says McFarland. And that’s the line he draws between contractors’ financial forecasting and the future of construction.
“I think this era of company leadership is going to have the most difficult and greatest opportunity of any leadership team in the last 100 years, because we’re not going to be able to rely solely on our experience within our businesses to be able to move the next generation forward. We’re going to have to learn to rely on our expertise in organizational change management to adapt to new ways of doing business,” McFarland predicts.
“I think that’s very difficult for us as leaders because we’re all kind of uncomfortable there,” he acknowledges. “For example, few leaders are experts in the digitization of business. They’re not experts in off-site prefabrication, or any of these other things that are disrupting our industry. We don’t have 30 years of experience in these spaces, so we’re relying on the up and coming people and talent outside of our industry to have that expertise.
“I think the vast majority of our time and effort is spent on changing the culture,” he adds, “and getting people to believe that there is a better way and being strategic about it.” ET Kitchell’s Carl McFarland says accuracy in project forecasting can improve margins enough to support process investments such as the company’s stake in a prefab business.
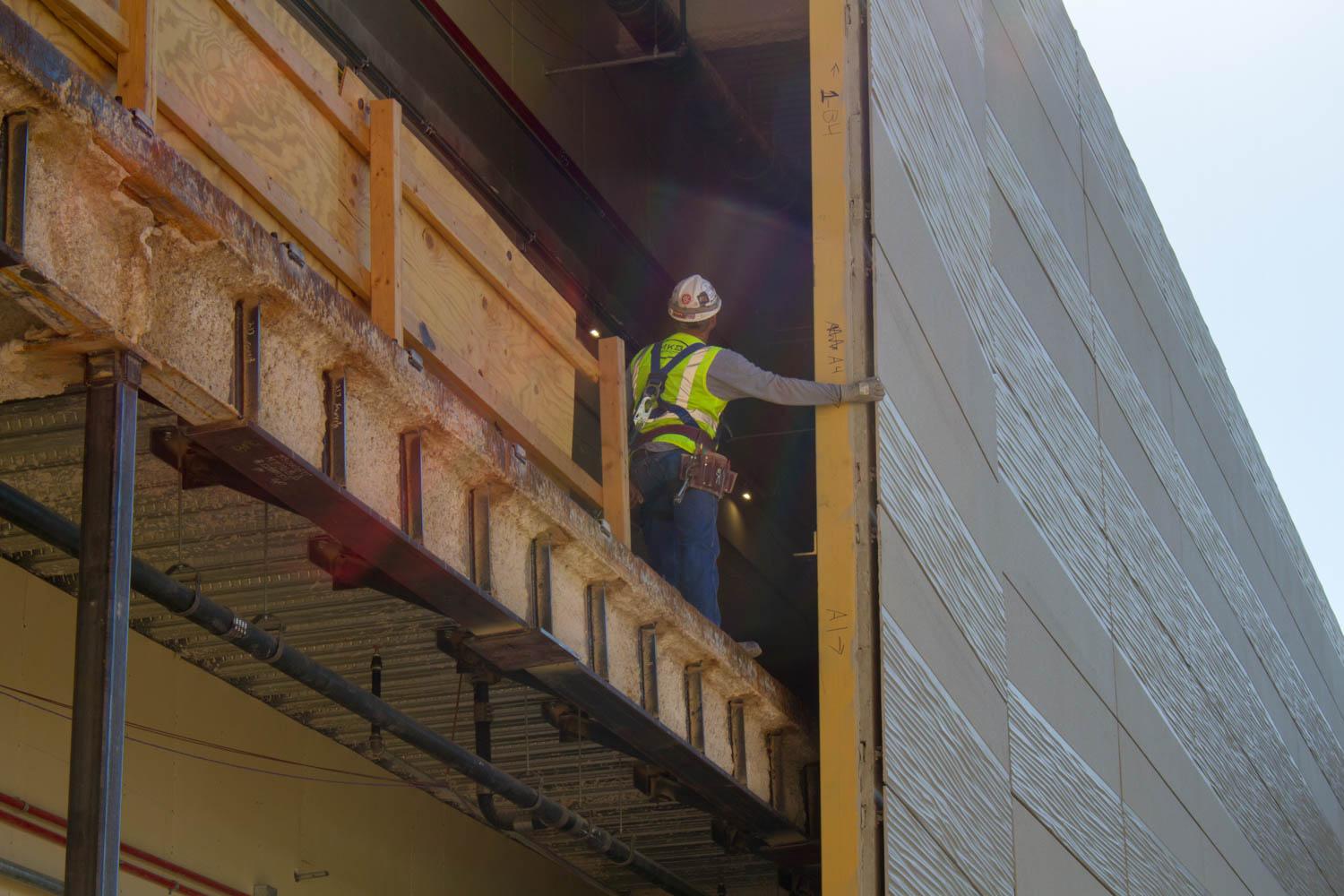
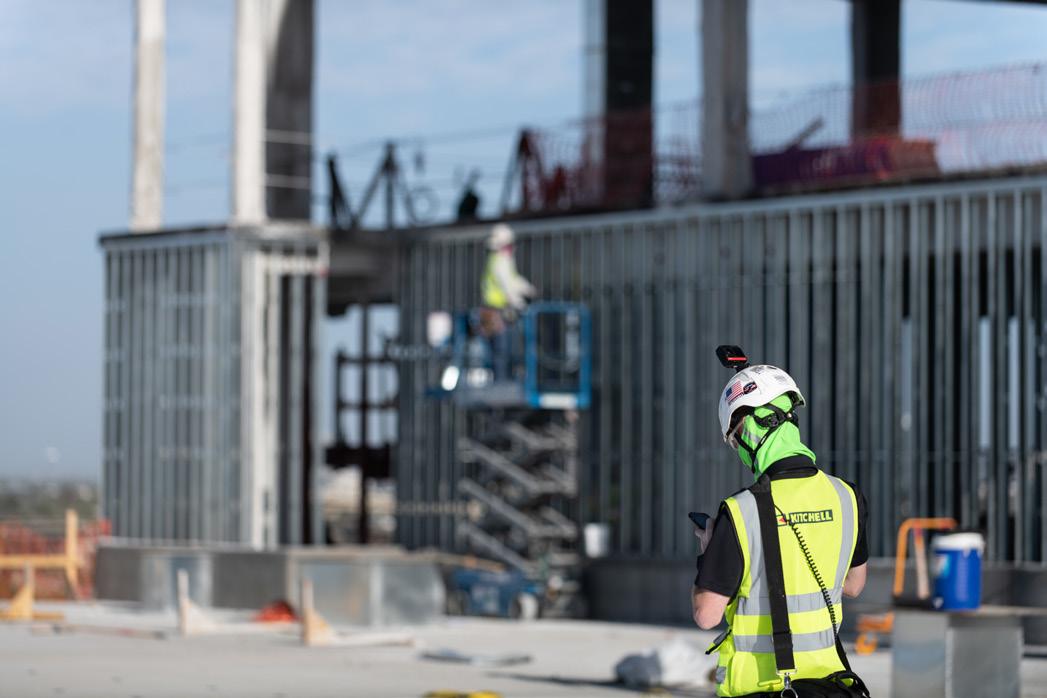
Protect Your Deadlines with the Multi-Tank Trailer
• No CDL/No HAZMAT • 420, 690, & 920 Gallon Capacities • Fast, Mobile Fuel Limits Downtime to Keep
Projects on Track • $1,500 Down. No Payment/Interest for 6
Months
- John, General Superintendent Rocket Land Development
Learn more online at: go.ThunderCreek.com/et1121 Call us at: 866.535.7667
Easy Financing: $1,500 down payment based on our jobsite ready, 690-gallon Multi-Tank Trailer and patented 100-gallon, 2-in-1 DEF system. Subject to approval. Offer valid until Dec. 31, 2021.
Tomorrow’s Digital Dispatcher Will DRIVE PROFITS
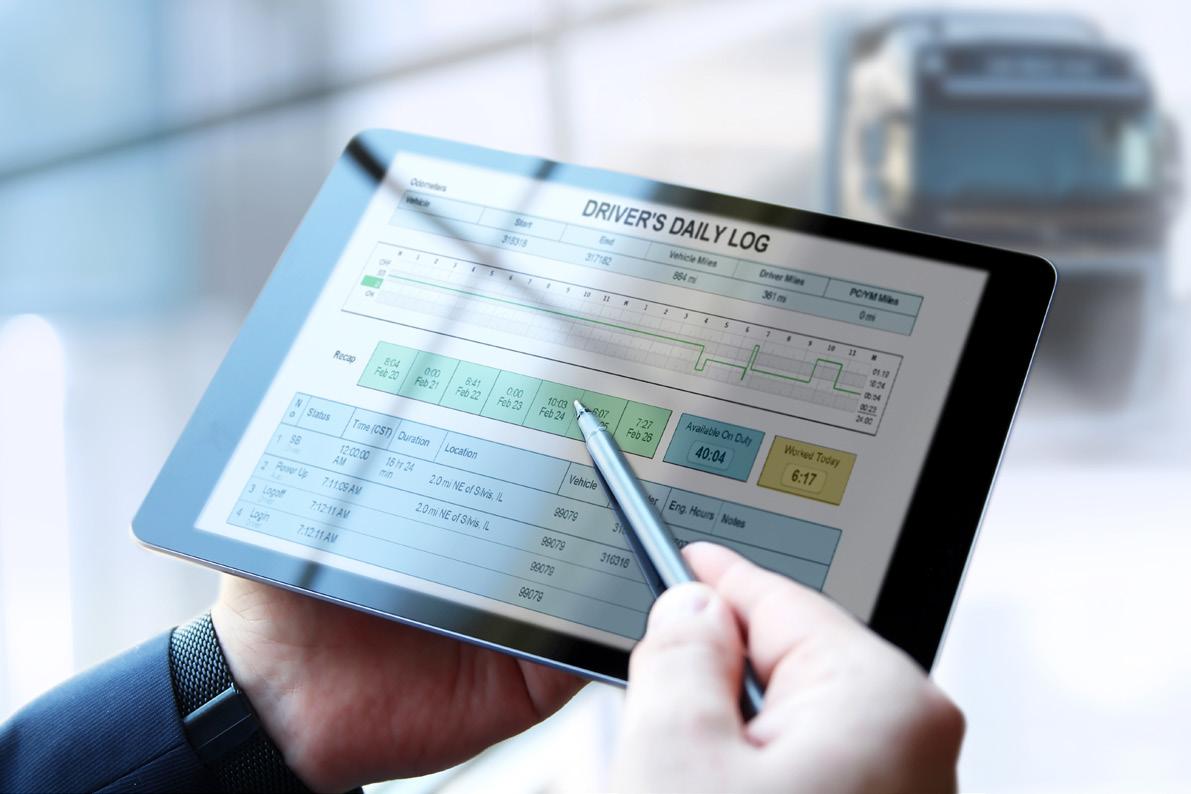
Software will empower dispatchers to increase customer satisfaction.
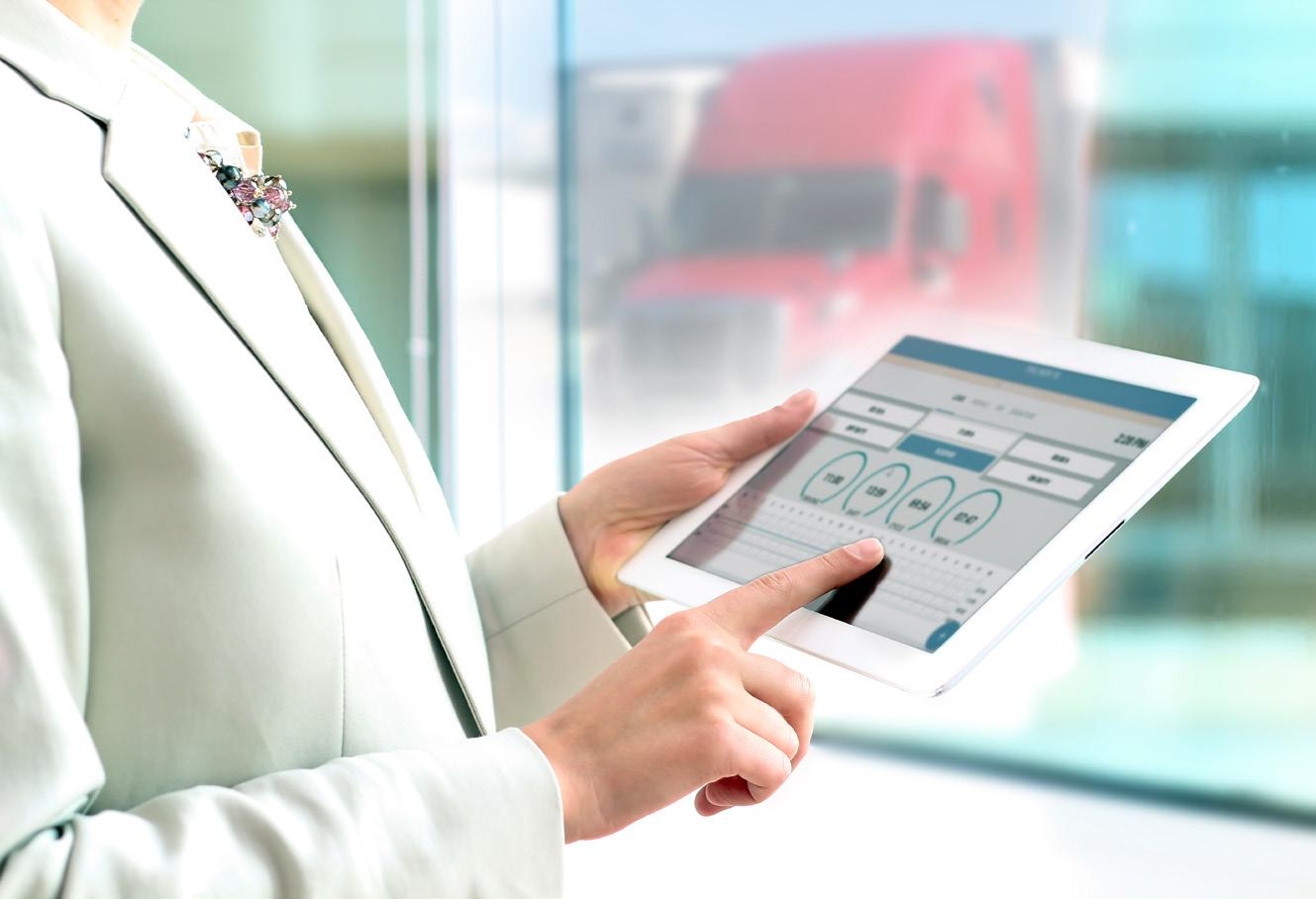
©Saklakova – stock.adobe.com
Changes that have been pioneered in other industries are coming to construction and changing the game. Cloud-based software, GPS tracking and mobile apps all contribute to an ecosystem in which parties are empowered by real-time tracking, multi-modal communications and data integration/connectivity.
The dispatcher role is the cornerstone of a well-run construction logistics operation. Today’s dispatcher spends his or her time fielding calls for orders, finding haulers and chasing down the status of deliveries. These operations have been managed using the same set of tools for generations: pen, paper and phone calls.
Much like the wave of technological advances that have revolutionized banking, manufacturing and retail, there is imminent change for how construction as an industry operates, and how dispatchers perform their jobs. This software-based revolution will empower dispatchers to be more effective, driving increased satisfaction among customers and haulers, and improved profitability for all members of the heavy construction value chain.
The new tech-powered “digital dispatchers” will leverage the power of software platforms, B2B marketplaces and mobile technology. These changes will elevate the dispatcher’s functional role and unlock new business value in construction.
THE EVOLUTION OF DISPATCHING
Effective communication and coordination with truckers is at the core of a dispatcher’s day to day success. Innovations in logistics management — which have been pioneered in other industries by innovators such as Amazon and UPS — have been slow to make their way into the construction dispatcher’s toolbox.
Not only have these innovations transformed the way businesses manage their logistics, they have also raised the bar for our collective expectations of what the delivery experience should be as a society, resulting in higher expectations from end customers in all industries, including construction. These changes were accelerated by the COVID-19 pandemic and related social distancing restrictions. As a result, contractors are asking: “If I can track my pizza from the oven to my door, why can’t I do the same for the thousands of dollars’ worth of materials en route to my construction site?”
Changes that have been pioneered in other industries, including long-haul trucking, are coming to construction and changing the game. Cloudbased software, GPS tracking and mobile applications all contribute to an ecosystem in which parties are empowered by real-time tracking, multi-modal communications and data integration/connectivity. This ecosystem represents a digital platform where multiple industry participants connect and collaborate toward better efficiencies, higher asset utilization and increased profits. The digital dispatcher of the future will play a central role in this ecosystem.
THE ROLE OF THE DIGITAL DISPATCHER
One fundamental impact of this change is that the digital dispatcher will replace the time spent on manual processes and inefficient workflows with new, high-impact activities. They will be part analyst-optimizer, part customer-service-delighter and part business manager, namely working toward: ˜ Optimizing workload distribution across a physical and virtual fleet using a centralized source of trucking and ensuring truckers are working at maximum efficiency; ˜ Delighting customers by providing self-service tools to track and request orders, thereby freeing up time to provide a new level of customer experience; ˜ Managing the logistics business, which includes prevention of wait times, supply and demand forecasting, rate analysis and budgeting.
These capabilities already exist at a basic level in some dispatch operations today. The newly empowered digital dispatcher will bring a fresh focus to these areas and, leveraging the transformative power of technology, use them to drive business value.
In transitioning from today’s dispatcher to the next, companies can expect improved performance across all their business operations through reduced waste/inefficiency and increased asset utilization. Tangible benefits will include increased amounts of material delivered through optimized scheduling and reduced wait time; increased profitability through consistent, predictable freight rates; and improved customer satisfaction through transparency and technologyenabled customer service.
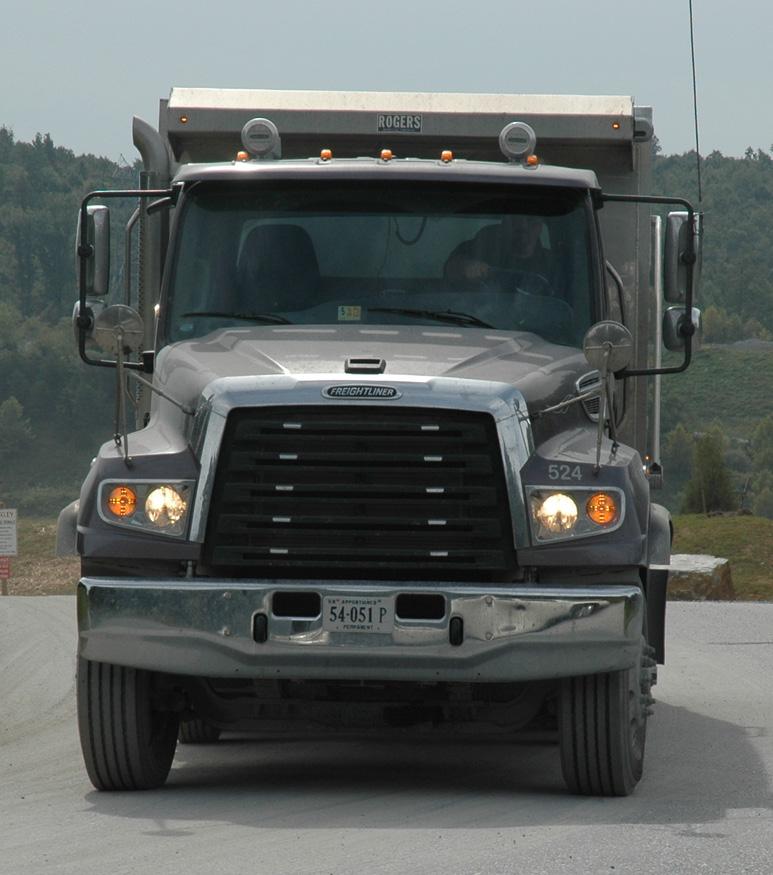
PREPARE FOR THE NEXT WAVE OF DIGITAL DISPATCHING
In order to plan ahead and get set up for success, companies should be armed with the right skills, tools, technologies and organizational support. Dispatchers’ current skills will still be critical, including managing relationships and maintaining market knowledge and industry expertise. Companies that define a clear mandate and utilize fleet management technologies to empower dispatchers to take ownership of their impact on the business will be in the driver’s seat.
Tomorrow’s digital dispatcher will be empowered to leverage technology to dramatically improve efficiencies, reduce waste and enhance the customer experience. You can set a dispatcher up for success by setting the right mandate and preparing your organization to embrace the role of the 21st Century digital dispatcher. ET
Bart Ronan is the CEO of TRUX, a technology company serving the construction industry with logistics management software.
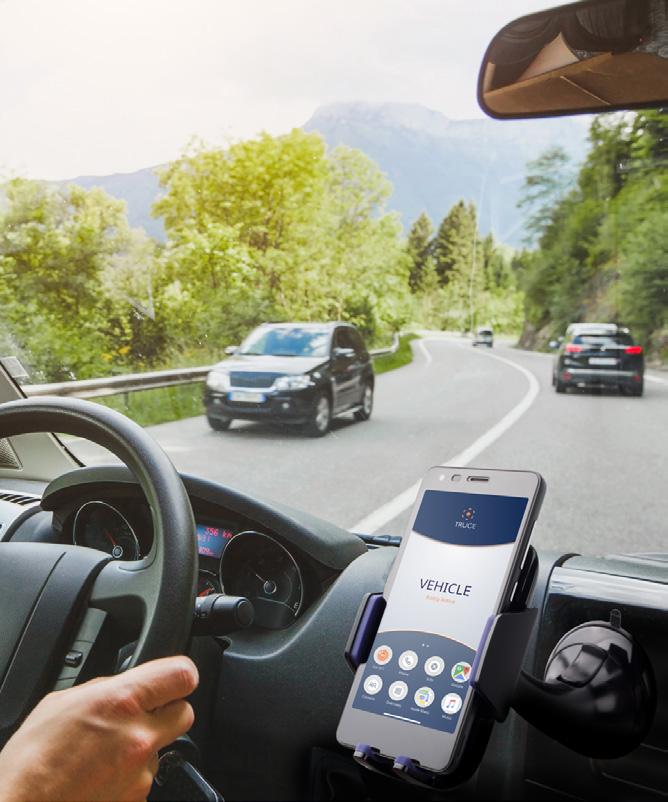
The Contextual Mobile Device Management platform automatically adjusts access to mobile apps and features based on a given work environment and additional contextual indicators.
•Includes a web-based Management Console, mobile app and available Beacon technology that can detect movement or be used to define boundaries •Employer defines how to protect employees based on location or proximity to high-risk areas or equipment, movement including speed, time of day or day of week and user or work group •Apps and functions that help employees are kept front and center, while those seen as distracting are temporarily hidden www.forconstructionpros.com/21295111
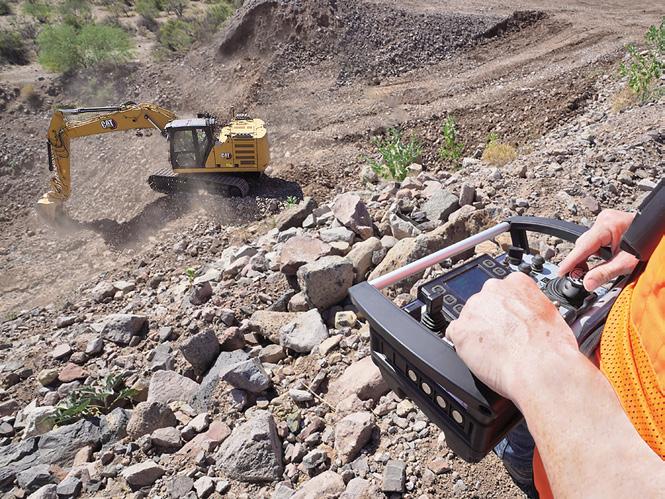
Cat Command for Excavating
Cat Command for Excavating provides remote-control operation for Cat 320, 323, 326, 330, 336 and 340 excavators from the 20- to 40-metric-ton size classes.
•Line-of-sight remote control from up to 437 yds. away or non-line-of-sight remote operating configuration available •Dealer-installed field kit features multiple cameras for non-line-of-site operation from the Command station plus the ability to stream on-site video feeds •Cameras, indicator lights, microphone, wireless receiver and antenna mounted on top of the cab to minimize damage risk •Technology features such as Grade Assist, Swing Assist and E-Fence can be set, activated and deactivated remotely •Excavators can be efficiently switched between remote and manual operation via a ground level switch www.forconstructionpros.com/21603306
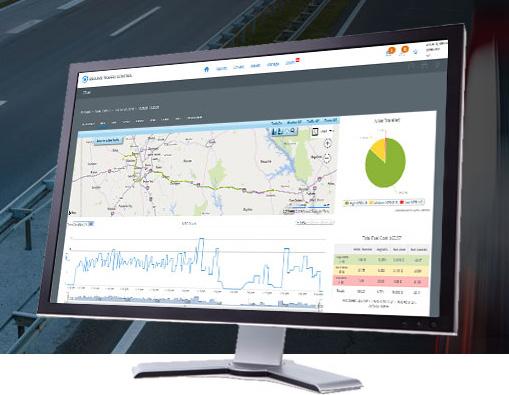
Zonar ZFuel
ZFuel assigns each driver an individualized Driver Efficiency Score to quickly uncover performance areas in need of coaching and monitors improvement over time.
•Normalizes metrics across age of truck and route terrain •Tracks key metrics by truck that impact fuel costs such as speeding and shifting behavior •Flags idle times outside of company policy by individual truck profile •Protects against fuel theft •Quantifies the number and percentage of miles in top gear •Maps cruise control use www.forconstructionpros.com/21772044
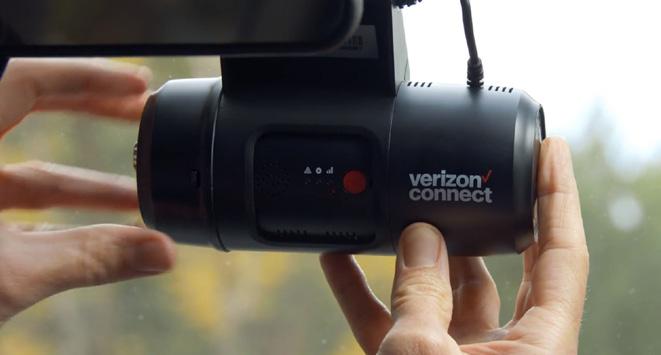
Verizon Connect Integrated Video
Integrated Video is a road facing dashcam that uses AI and machine learning to help categorize harsh driving events.
•Begins recording once engine is turned on and continues until engine is off •Reviews footage based on driver behavior triggers and classifies it as a collision, dangerous, harsh driving or low risk •Video viewable in the Reveal fleet management software on mobile or desktop within minutes of the event or can be downloaded for later use •Identify driver and speed and see vehicle location with GPS tracking •Alerts when a video is available www.forconstructionpros.com/21136272
Geotab GO RUGGED Fleet Tracking Device
This scalable, flexible and customizable off-road fleet solution can capture rich data on equipment position, fuel use, idling and more.
•Delivers accurate intelligence for real results •MyGeotab fleet management platform integrates with AEMP and third-party devices •IP67-rated device with LTE connectivity lets you monitor assets out on the worksite in real time •Manage both off-road and on-road assets together •Open platform and Marketplace offer a variety of third-party solution options www.forconstructionpros.com/21093316
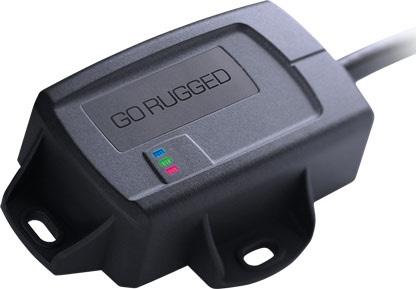
Sensata | Xirgo Connected Fleet Solutions
The newly combined business Sensata | Xirgo offers a range of connected solutions to improve fleet operational efficiencies, reduce costs, unlock new revenue streams and keep people and property safe.
•Include cargo monitoring and tire pressure monitoring solutions •Portfolio of sensors, vehicle and video telematics and asset tracking devices available •Vehicle-area network, cloud solutions and data insight services also offered www.forconstructionpros.com/21771973
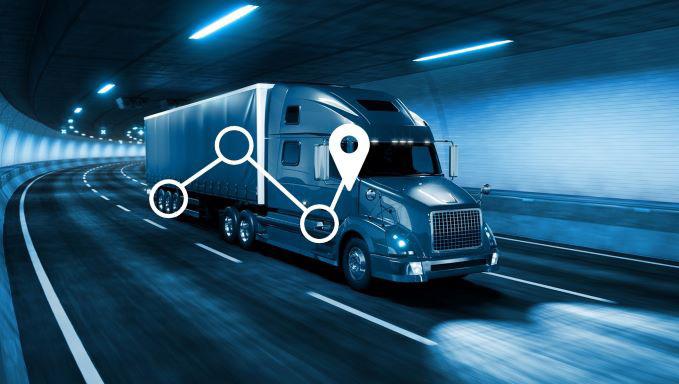
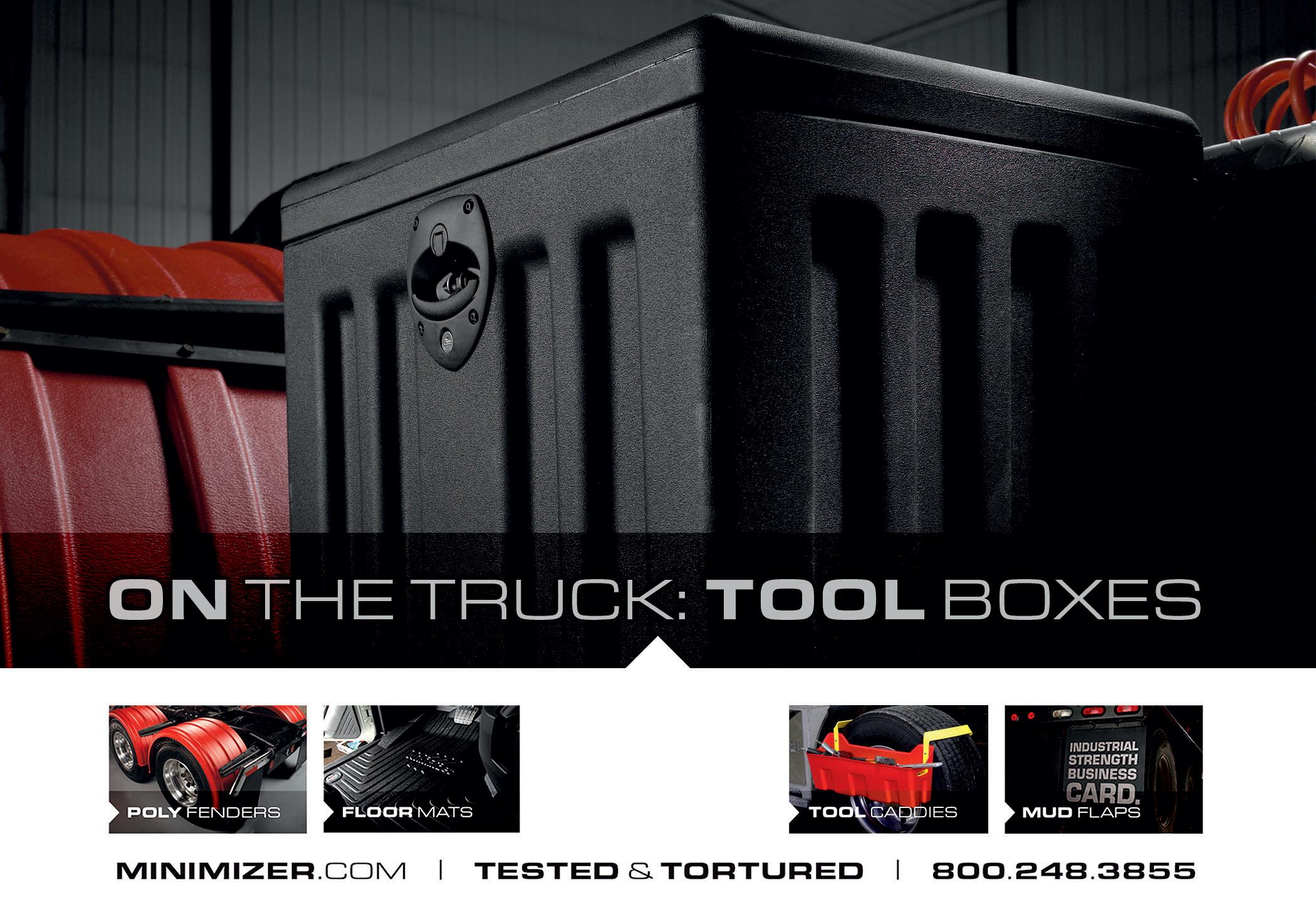