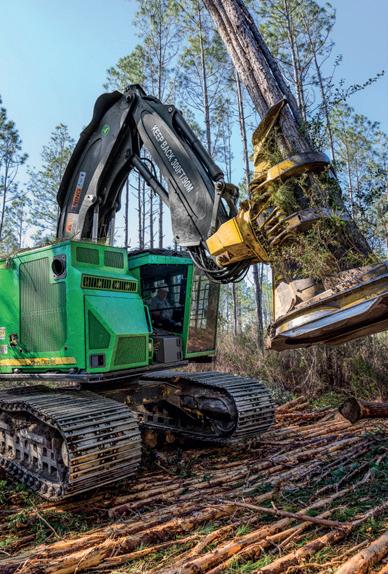
20 minute read
FELLER BUNCHERS
L-Series II Wheeled Feller Bunchers
The L-Series II Wheeled Feller Bunchers were designed based on extensive customer input, resulting in a lineup of machines that improve operation, maintenance, and reliability.
Advertisement
The simplified L-Series II models incorporate several part changes to reduce complexity. Changes to the electrical and hydraulic systems and improvements to component placements enhance the logger experience when servicing the machines. “The two-piece wiring harness makes it easier to work on the machines,” said Wayne Sugg of Sugg Logging. “Wiring is rerouted, so it is not bunched up in the machine, which reduces rubbing wear. The cylinder guards protect the hoses from falling limbs. These changes help make the machine more reliable, which saves time and money on maintenance.”
803M Tracked Feller Buncher
From the L-Series wheeled machines to the 959ML and M-Series Tracked models, the John Deere feller bunchers deliver productive, reliable machine solutions built with loggers’ needs top of mind.
M-Series Tracked Feller Bunchers
Ongoing input from customers has helped to make the 800M- and 900M- Series Feller Bunchers more productive and user-friendly. The spacious operator station was designed by loggers for loggers and includes ergonomically designed controls. Other features include fully adjustable armrests with mounted keypads, a sealed touchpad allowing longer switch life, and floor-to-ceiling front windows to improve visibility. “The guys in the cab, they can see so much better off of the visibility. And that visibility should equate to better productivity… if the guy can see better, he can do a better job,” said Cory Isley of D&J Isley and Sons.
The 800M- and 900M- Series are equipped with a Final Tier 4 engine, increasing overall performance and reliability by minimizing fluid consumption. This latest Final Tier 4 engine meets EPA regulations in emissions without sacrificing power or torque. The optional Rapid Cycle System (RCS) allows for faster, low-effort joystick control of all boom functions. This helps operators of 800M- and 800MH-Series machines to be more productive by combining automated felling head arm cycling with simple boom controls. RCS significantly reduces operator fatigue while increasing efficiency and productivity.
The two-piece wiring harness makes it easier to work on the machines,” “Wiring is rerouted, so it is not bunched up in the machine, which reduces rubbing wear. The cylinder guards protect the hoses from falling limbs. These changes help make the machine more reliable, which saves time
Wayne Sugg, Sugg Logging
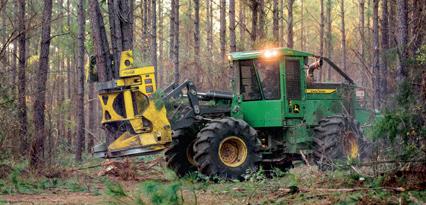
Cory Isley , D&J Isley and Sons
643L-II Wheeled Feller Buncher
John Deere’s goal was to improve the overall user experience based on customer feedback. They made over 1,600 component changes, including more robust electrical harnesses, fittings, hoses, and cylinder guards. And they made subtle changes under the hood, such as improving component placement and dramatically reducing the complexity of the electrical and hydraulic systems
The heavy-duty axles on the 643L-II and 843L-II Wheeled Feller Bunchers provide the operator with the stability and hill-climbing power they need to navigate challenging forest conditions. The higher-ply tire options are available from the factory, increasing tire strength for carrying heavier loads and powering through rugged wood conditions.
New steering sensors enable operators to control articulation speed for frameto-frame contact, cushioning impact during full articulation, and improving operator comfort. Further enhancing operation, the electrohydraulic controls can be configured to personal preferences for the operator. The optional joystick and foot controls deliver smooth, low-effort control to decrease operator fatigue over long shifts.
The TimberMatic™ Maps and TimberManager™ map-based production planning and tracking systems are available for the M-Series Tracked Feller Bunchers and the L-Series II Wheeled Feller Bunchers. Optimizing productivity and efficiency, TimberMatic Maps helps eliminate guesswork for operators related to routes and the location of the timber. TimberManager provides complete visibility to the operation from the land harvested to the machines at work, allowing operators to streamline communication and increase efficiency.
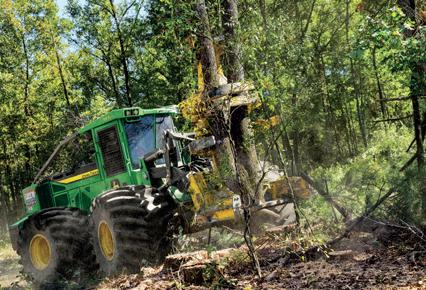
843L-II Wheeled Feller Buncher
REVERSIBLE FANS FOR AUTOMATIC RADIATOR CLEANING | www.cleanfix.org
more Cooling more Power
more Productivity
less Downtime
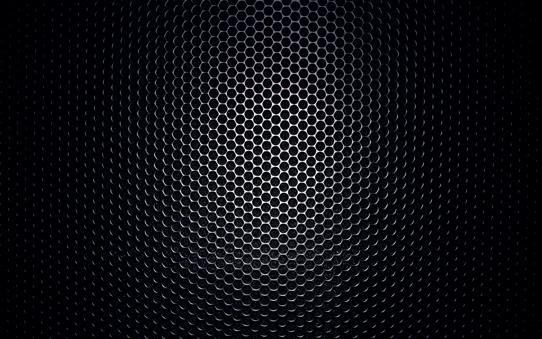
The XT465L-5 sets high industry standards of excellence for Track Feller Bunchers
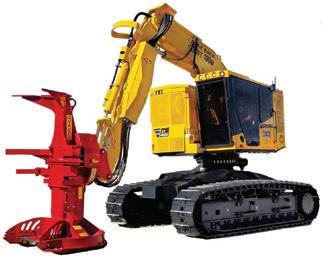
Improved service access, reliability and durability means increased productivity for the Komatsu XT465L-5 feller buncher.
Built for ease of serviceability, a gull-wing style engine hood folds down, providing an elevated service work platform. Four additional service doors provide easy access. The innovative hydraulic tank design features two tanks, requiring 55% less total hydraulic oil.
Operator comfort and convenience are premium with a state-of-the-art cab, which has been relocated to the left of the boom. The design changes provide superior lines of sight to each track. The intuitive IQAN-MD4 digital control system puts machine control at the operator’s fingertips.
The rugged undercarriage significantly increases service life, including rugged, stronger track chain links that resist twist and longer-wear track roller and idler bushings. The new triple labyrinth floating seal housings protect the final drive seals against mud packing.
Fuel consumption is up to 5% lower due to advanced engine and hydraulic system control designs with the 331 peak hp (247 kW) Cummins QSL9 9-liter engine.
Lift capacity at full reach has been significantly increased and the XT465L-5 now readily operates the Quadco 24-inch (610 mm) cutting capacity disc saw heads. Features
Gull-Style Engine Hood
Gull-wing engine hood folds down providing an elevated service platform. Hydraulically-actuated with backup manual hand pump. Robust design provides a secure footing with 500 lbs (227 kg) load capacity. Offers excellent visibility and access to all engine-related components. Provides full access to engine oil filter, air filter, fuel filters, coolant, DEF fluid and hydraulic filters.
Relocated Operator’s Cab - Increased Track Visibility
State-of-the-art cab relocated to the left side. Tracks are now highly visible through the side door and boom side windows • Larger Door window has an
“L-shaped” flat bottom • Engine/pump compartment is set-back; top 2/3 portion is indented rearward
Rugged New Undercarriage
Rugged new Komatsu undercarriage provides longer service life due to: • Heavier 8.5“ track chain links have a thicker bushing strap which is stronger at resisting
“twist” • Track rollers & idler bushings are made of high-density material
• New track sliders have a reduced angle providing 30% lower contact • Final drives use a new triple labyrinth seal to protect from mud-packing • Crawler Box improvements include: • Removeable track guards have larger roller side openings to reduce mud packing
• Additional set of steps has been added to each crawler box
16% Greater Lift Capacity
Increased lift capacity at full reach vs. XT-3 due to improved boom & arm geometry and larger cylinders. Provides better balance between boom lift & arm holding capacity. Broad line of Quadco high speed disc saws available.

Built for ease of serviceability, a gull-wing style engine hood folds down, providing an elevated service work platform
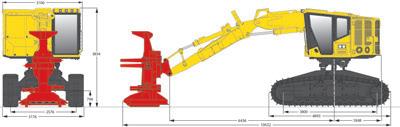
The new operator’s cab has been mounted on the left side for industry and Komatsu commonality.
The layout is ergonomically efficient, spacious and quieter. Its sloped roof line provides excellent headroom above and forward of the seat. • Large quiet ROPS/FOPS/
TOPS/ FOG/OPS /WCB /Oregon
OSHAcertifi ed cab with an adjustable high back operator seat. • High-capacity heater, air conditioner and defroster provide a comfortable operator climate regardless of the season. • IQAN-MD4 control system provides ability to custom tune vehicle response to meet individual operator preferences. The XT-5 is equipped with the latest state-of-the-art IQAN-MD4 Programmable Digital Control System.
Komatsu was “1st in the Forest” with the advanced IQAN-MD4 technology on the XT-3 series machines and continues to be a leader
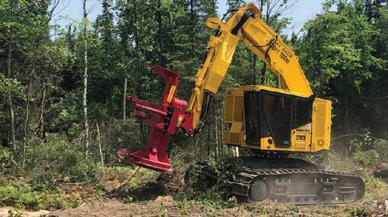
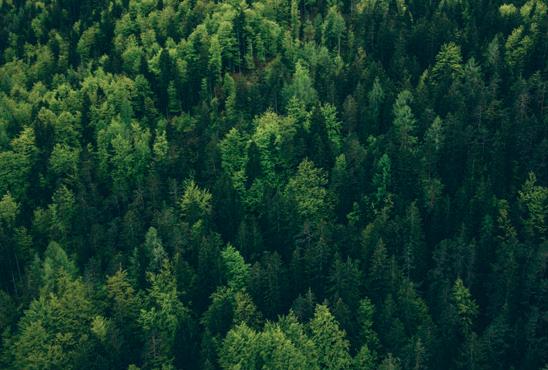
Chippers
Astec Peterson Products Provide Biomass Solutions

The need for innovative and clean energy has skyrocketed in recent years as more sustainable solutions are needed to preserve the environment and its natural resources.
The fast-growing industry of biomass, or bioenergy, has delivered promising results as an environmentally friendly solution for clean power.
The demand for long-term renewable energy has presented forestry producers with an increasingly popular and profitable division of work, and this demand is expected to rise.
Not new to the biomass industry, Astec Peterson forestry products have been utilized in biomass production for over 40 years, playing a leading role in the progression towards clean energy. With these years of experience, Astec forestry machinery is equipped with the most modern and innovative technology for producing biomass, taking the lead towards a more sustainable future.
Biomass Production
Producing biomass to be converted into energy begins with processing plant-based materials that will eventually become fuel to create biomass. Wood waste, forest debris, crops, agricultural waste and stumps are just a few commonly used materials. In addition to producing energy, the process of biomass production also allows for the recycling of organic waste, which also benefits the environment. In order to convert organic material to energy, the chips are burned to create electricity and other forms of power.
Astec drum chippers are a highly efficient tool for processing organic waste into biofuel. The Peterson 4310B drum chipper is designed for high volume biomass producers and accepts a wide variety of feed material, from small brush to large logs up to 24-inches in diameter. This machine provides
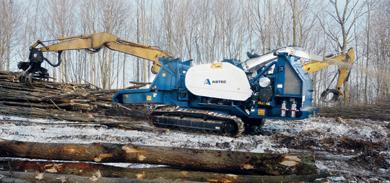
all the elements producers are seeking in biomass production, including precise end-products and high productivity.
The Peterson 4310B Drum Chipper

The 4310B drum chipper is trackmounted, making it especially suited when on-site mobility and frequent moves are required. Additionally, when even more versatility is needed on extreme terrain, Astec offers the 4310B Highwalker model, providing an additional ground clearance of 5-inches for added stability and mobility.
One of the many advantages of the 4310B chipper is that it delivers superior and accurate product sizing. For instance, the grate system easily fractures twigs and small stems; and the solid AR400 steel anvils provide long-life and consistent sizing, essential elements in biomass production. Additionally, the 4310B is designed with an adaptive feed system that adjusts the chipper speed to maintain a consistent speed ratio with the drum, which results in high quality and exact end-products.
In biomass production, consistent end-products are crucial. Fines, like twigs and branches, can cause material blockages in the augers of a biomass plant, making product consistency essential to biomass chip customers. Astec drum chippers feature a secondary screen that processes twigs or branches and heavy-duty adjustable knives that create material with clean-cut edges and more consistent product sizing.
Astec Peterson drum chippers come standard with an end-load spout, but the 4310B is also available with an optional top-load spout, which allows chips to be loaded quickly into a top-load truck for faster and efficient hauling.
The efficiency of Astec equipment allows for low operating costs, an important advantage for producers seeking high profits. The 4310B chipper is highly effective for biomass producers, with many cost savings features, including higher torque rates that deliver fuel efficiency, longer wear parts life that reduces downtime, a chip accelerator that increases load density which lowers transportation costs and the adaptive feed system, which reduces engine load and increases fuel efficiency.
(Below) Astec Peterson 4300 Whole tree WHEELED drum chipper for biomass and microchips
Both machines make chips from ¼” to 1 ¼” (6 to 32mm) and have CAT C18 Tier IV, 755hp (563 kW)
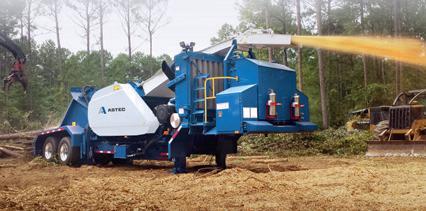
High Production Rates
Biomass processing requires high production rates because of the high fuel consumption needed to create energy and for profitability to the producers. Depending on the wood species, chip length and tree size will determine the exact production rate. The 4310B configured with a six-pocket drum producing 7/8” (mm) length chips will make approximately 80-tons per hour, and with the microchip configuration with a 12-pocket drum set at .25” (6 mm) chips will produce roughly 5-tons per hour.
An additional advantage of the 4310B is its productivity in processing tops, un-merchantable wood and residue from logging for biomass creation. Depending on the configuration, the machine can produce chips from 1/8” to 1 ¼” (3-31 mm).
The high production rates of the 4310B drum chipper make it one of the industry’s leading machines for biomass creation, and Astec is a technology-driven manufacturer committed to providing users with the most innovative and productive equipment on the market. Astec also offers many other valuable machines that are productive for biomass, including horizontal grinders, screening systems and stacking conveyors.
The Future of Energy
As the need for renewable energy sources quickly increases, Astec is a crucial partner to the biomass industry. Astec forestry equipment is leading energy solutions for a cleaner, more sustainable future, with technology at the forefront and innovation as a leading core value.
Astec Peterson 4310B Highwalker
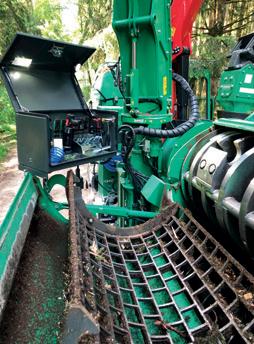
What really counts in a chipper driver’s day-to-day work: Smooth cutter change thanks to swivelling tool box. This necessary cleaning and maintenance tool is located directly on the rotor.
Handling the machine correctly
Requirements for professional chipping work
The shortage of skilled workers is also omnipresent in the forestry sector, and at the same time the pressure is increasing for companies to use woodchippers economically and efficiently. All the more reason for woodchip producers to concentrate on fully utilising the potential of their machinery. Because only those who understand the effect of the individual machine parameters can ultimately achieve the required woodchip quality.
Producing quality woodchips is all about the right machine setup,” explains JENZ product manager Dominik Meden. How this should look depends on which material is to be processed taking into account the required woodchip quality.“A good chipping is the result of the right interplay between feed-in speed, drum speed and defined pre-grip,” explained the Product Manager.
The most important requirements for this are sharp cutters which are correctly adjusted to the counterblade and regular replacement of blunt cutter blades, even during chipping operations.
Changing cutters and blades is quick and easy thanks to the toolbox located directly on the rotor and also additional storage space, which means waiting times during chipping work in the forest can be used productively.
The product manager is also keen to point out an essential feature regarding installation of new chipping blades: “The optimum distance to the counterblade is decisive in order to produce consistently high-quality material. Because it’s the clean cut that produces the quality.
“The chipping size, on the other hand, is defined by the pregrip, not by the screen basket.” In the chipping process the screen basket actually only has the important task of avoiding overlengths. However, a correctlyselected screen basket also makes itself conspicuous in lower fuel consumption. This is logical because the easier the chippings can flow off, the more economical the machine can work.
In addition, smart systems and smartphone-like controls help compensate for the shortage of skilled workers. “In other words, the machine has to offer simple solutions which correspond to the everyday problems of a chipper driver,” said the 33-year-old manager.
This starts with quick readiness for use of the machine and ends with self-regulation of the relevant machine settings. “For example, it is possible for the machine to produce the first chip only a few seconds after reaching the chipping area,” Mr Meden emphasised.
That’s not just good for the driver, but also improves the machine efficiency thanks to
Whether set-up assistants or feed control systems: smart systems and smartphone-like control take the strain off the driver and improve chipping quality
Dominik Meden, Product Manager, JENZ
optimised/shorter setup times. The feed-in speed also has a massive effect on the end product depending on the material to be processed. “During shrub cutting and light wood applications the CFA system takes over selection of the correct feed-in speed, and thus relieves the driver,” explained Mr Meden.
This is because the feed-in speed in this system is regulated by the rotor speed with the aim of achieving optimum wood chip quality. The feed-in speed is adjusted in such a way that reversing is avoided, but the pregrip still remains almost constant. As the rotor speed drops, the feedin speed decreases and, ideally, the motor can permanently maintain its maximum torque.
Unnecessary reversing or stopping of the feed-in at the expense of the drive motor can virtually be avoided, which leads to a uniformly high and machinefriendly utilisation. Those who have a lot of logs to process will benefit from the CFA2 system extension. This is because the feed-in speed is not only controlled by the rotor speed, but also by the opening of the top roller. Dominik Meden made it clear: “The machine effectively recognises what is coming into it. It can react in time to avoid running at full intake speed on 60 cm beech logs, for example.”
In combination with this, care should be taken to ensure a low drum and blower speed when processing logs, otherwise a higher fines content would result.
To sum up, the product manager referred to feeling the machine: “Machine and driver must become one - this is the only way to meet the different requirements in the forestry sector, always react flexibly to orders and keep skilled workers. At the end of the day, that’s what makes a company profitable.”
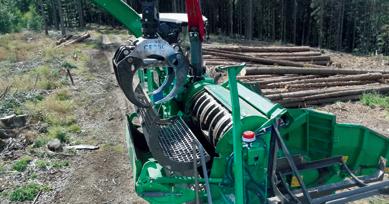
Additional screen basket: A screen basket holder at the rear enables the transport of an additional screen basket. The change is carried out by the driver using a crane and offers more flexibility during order processing
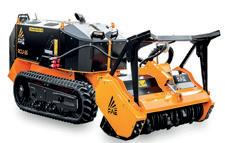
FAE introduces the RCU55: the compact remote controlled tracked carrier
FAE is expanding its product line with the RCU series, a compact and professional, remote controlled tracked carrier that is the result of merging FAE’s extensive experience in designing tracked carriers for the PT series and remote-control systems for the vehicles in our Demining line.
The RCU-55 is designed to work on hard-to-access areas and steeply sloping terrain that requires dedicated equipment to ensure operator safety and operating efficiency. It’s excellent for working in hilly wooded areas, near railroad tracks, power lines, gas and oil pipelines, gardens, roadsides, highways, canals, rivers and lakes.
The new FAE tracked carrier is powered by the Kohler Common Rail electronic fuel injection engine — a compact, powerful and fuel-efficient 56-hp propulsion system that complies with the most stringent emission standards.
The heavy-duty undercarriage features a hydraulic extendable & retractable independent track system and an automatic tensioning system that is built to work in the toughest conditions, thanks to a rubber track structure, oscillating rollers system and triple-flange style idlers. High-tech solutions give the RCU unbeatable traction, enabling it to work on steep slopes up to 55°.
A dual hydrostatic transmission provides better traction and optimal management of the attachment. Electronically controlled piston pumps combined with a dedicated electronic control unit provide an integrated technological system. The result is high performance and reliability that lasts, plus simple and intuitive operation.
The RCU-55 is guided by an ergonomic remote control with a large 3.5” display for superior management of all vehicle and attachment functions and with customizable function keys. A 2.4 GHz transmission frequency ensures reliable communication.
The RCU-55 can be paired with two specialized FAE forestry mulchers. The BL1/RCU mulcher, designed to mulch vegetation up to 5” in diameter. This mulcher features a fixed tooth rotor and Bite Limiter technology that provides higher productivity with even less horsepower due to low power absorption. The PML/RCU is a swinging hammer forestry mulcher ideal for mulching vegetation up to 2” in diameter. The FAE RCU product line will be further expanding in the coming months with the introduction of the RCU-75, FAE’s remote controlled compact tracked carrier that can take on the more demanding jobs.
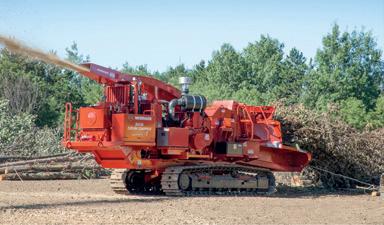
30/36 Track Whole Tree Drum Chipper
Morbark Drum Chippers
Morbark offers a full line of whole tree Drum Chippers in a range of sizes and in several configurations – with cab and loader (WCL) or no cab and loader (NCL), on tracks or tires, diesel or electric powered
Add to these choices a wide variety of available options, and you’ve got the flexibility to customize the perfect chipper for your particular needs. With their rigid structural frame and powerful internal-drive, single-feed-wheel infeed system, Morbark chippers are the best you can get. They can chip small, unmerchantable material, giving you access to more markets – and higher profits. These are just some of the reasons that Morbark is the largest and most respected name in chipping. 50/48x whole tree drum chipper
The Morbark 50/48 whole tree wood chipper is the largest, most productive drum chipper on the market.
The 50/48X was updated to a similar design layout as Morbark’s other industry-leading industrial drum chippers with a sloped infeed, externally adjustable anvil and large work platforms for easy access for routine maintenance.
The reverse pivot yoke produces more down pressure than the conventional style yoke for aggressive feeding of a variety of material.
Morbark’s Advantage 3 Drum produces more consistent chips, while the heat-treated, AR-450 steel drum skin provides longer wear life for lower replacement costs and less downtime. The Advantage 3 drum assembly can come as 10-knives for fuel chip or 20-knives for micro-chip application .

The Morbark 40/36 Whole Tree Drum Chipper is a compact, affordable, productive drum chipper designed with the biomass industry in mind.
Equipped with the same internal drive perfected on Morbark horizontal grinders, along with an extra wide feed opening, the 40/36 aggressively feeds brushy tops and limbs, quickly and effortlessly filling a chip van to maximum legal load capacity.
Morbark’s Advantage 3 Drum produces more consistent chips, while the heat-treated, AR-450 steel drum skin provides longer wear life for lower replacement costs and less downtime. The feed system is more efficient due to a staggered knife configuration and contains fewer moving parts, reducing maintenance.
With low fuel consumption per ton produced, this unit is economical. At 8’6″ (2.59 m) wide this compact unit is easily transportable and requires no permits to move. 30/36 Whole tree drum chipper
The Morbark 30/36 Whole Tree Drum Chipper’s high production rate lowers operating costs by increasing fuel efficiency.
The aggressive live floor feeding system with two strands of durable WHD-120 chain and a large top and bottom feedwheels ensure positive feeding of material, including brushy tops and limbs.
Morbark’s Advantage 3 Drum produces more consistent chips, while the heat-treated, AR-450 steel drum skin provides longer wear life for lower replacement costs and less downtime.
M20r forestry whole tree drum chipper
The hard-working, aggressive M20R Forestry chipper provides optimal performance for in-woods chipping.
Easily filling a 53′ (16.15 m) trailer and sustaining up to four to five loads per day, this hardworking, aggressive chipper is the perfect option for those looking to enter the biomass market with low startup costs.
This machine features the Advantage 3 Drum and electronic flow control to control feed speed from the remote. Tough, abrasionresistant AR-450 steel is used for the drum skin, replaceable belly band, discharge chute and wear strips beneath the bed chain, providing strength and long wear life. 40/36 Whole Tree Microchipper


30/36 Whole tree drum chipper
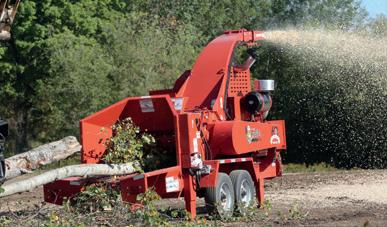